[摘要]主要针对内螺纹的精密磨削加工技术,从砂轮截形设计、磨杆研究、砂轮修整以及磨削工艺等几个方面对现有内螺纹磨削加工技术的研究成果进行介绍,分析了磨削的砂轮截形设计解析法和计算机辅助设计法的优缺点;简述了减小内螺纹磨杆振颤和提高内螺纹磨削砂轮修整精度的方法;介绍了内螺纹加工过程中对刀、工艺参数、超声振动辅助磨削和磨削过程中磨削力等方面的研究;总结了内螺纹磨削加工技术的发展现状,并展望了内螺纹磨削加工技术的未来发展方向。
关键词:内螺纹磨削;砂轮截形设计;砂轮磨杆;砂轮修整;磨削工艺
内螺纹在航空航天、国防、汽车、机床装备、微电子等行业中具有广泛的应用,按照用途分类可分为连接内螺纹和传动内螺纹。连接内螺纹作为一种可拆的固定连接零件,具有结构简单、连接可靠、装拆方便等优点;传动内螺纹作为一种基于螺旋副将主动件的回转运动变为从动件的直线运动的传动零件,具有工作连续、传动平稳、承载能力大、传动精度高等优点,已被广泛应用于传动机构中,如滚珠丝杠、滚柱丝杠、蜗轮蜗杆等。
内螺纹的广泛应用对其制造提出了巨大加工需求,机械加工中各种内螺纹的加工占到孔加工工作量的50%,并且随着相关行业的发展,内螺纹的尺寸范围越来越大,加工精度要求也越来越高,同时因为内螺纹的加工空间是半封闭的,这对内螺纹的加工提出了更高的要求。目前针对内螺纹的主要加工方式有铣削、挤压、车削、攻丝、磨削、旋风切削、挤压攻丝和振动攻丝等[1–2]。其中对于经热处理后的高硬度螺纹面或硬脆材料螺纹面的高精度加工,磨削是目前唯一行之有效的加工方式。
本文主要针对内螺纹的精密磨削加工技术,从砂轮截形设计、磨杆研究、砂轮修整以及磨削工艺4 个方面对现有内螺纹磨削加工技术的研究成果进行介绍分析。
面向内螺纹磨削的砂轮截形设计研究
内螺纹加工属于成形磨削加工的范畴。内螺纹的实际轮廓是由砂轮的形状和轨迹决定的,因此对于磨削来说,砂轮截形的设计将直接影响内螺纹的加工精度[3–4]。国内外各科研单位很早就开展了对于螺纹面加工工具的设计方法研究。目前针对其截形设计的方法主要有图解法、解析法和计算机辅助设计法3 种。其中图解法是通过作图法来直观得到工具截形,虽然求解效率较低,但易于实现,适用于螺旋曲面复杂导致其难以或不能用数学方程表示的情况。图解法的求解精度主要取决于描述理想的螺旋面剖面和初始工具表面的点数。增加点数会提高求解精度,但同时也会降低图解法的应用可能性[5]。相对图解法,解析法是通过求取工具与螺纹面的接触线来获得工具的截形,因此具有更高的求解精度[6]。但对于由复杂曲线段组成的复杂螺旋面,用解析法求解难度较大。计算机辅助设计法由此产生,其基于计算机技术以求解工具截形,因此具有更好的适用性。本文将主要介绍后两种方法。
解析法求解精度高且应用最为广泛。西安交通大学的林其骏[7]在1979年就提出了在已知螺旋面端面截形来求螺旋面工具截形的计算方式,方便了计算机程序的编制,并分析了工具截形的曲率问题。1982年,吴序堂[8]提出在计算加工螺旋面工件的铣刀、砂轮截形时,常用的方法为先给出工件螺旋面的方程式,对螺旋面及其加工原理、加工工具和工件之间啮合原理、工具回转面与工件螺旋面的接触条件式进行分析求解,建立工具与工件螺旋面的相对位置坐标系,最后通过坐标变换来求取工具截形。这种方法是已知确定的螺旋面截形方程来求解砂轮截形,但是对于复杂螺旋面截形,能得到的只有一系列离散的点。为解决这个问题,1984年卜啸华等[9]提出用三次样条光顺函数拟合由离散点先得到螺旋面截形的方程,由此解决了离散点工件廓形的工具计算问题。具体方法是:已知工件某个截面上一系列离散点的坐标,先拟合这些离散点得到曲线,再根据这个拟合曲线的方程建立螺旋面的方程,最后计算工具的截形。这种方法的缺点就是运算过程太复杂,计算结果误差比较大。1990年,吴序堂等[10]提出了一种系列离散点各点处的导数求解方法,在不用对离散点进行拟合的情况下求出各点处的一阶导数,这种方法不用先通过对离散点拟合曲线求解螺旋面方程式求解工具截形,而是直接计算工具截形,减少了工作量,而且砂轮截形求解精度也显著提高了;以前提出的对于已知螺纹截面离散点坐标来求解砂轮截形的方法,在加工精度要求不高的情况下可以使用,但对于加工精度要求比较高的情况已经不适用。张光辉等[11]提出了在已知螺旋面轴向截形或者端面截形的离散点时,推导成形工具与螺旋面的接触条件式,用累积三次参数样条法求解每个离散点处的斜率问题,这一方法不仅简化了运算过程,也提高了运算精度,并且用累计样条参数法和双圆弧样条法对求得的砂轮截形数据点进行了光顺处理,光顺处理的砂轮三维效果如图1所示[11],获得了可用于数控加工的CNC 代码,可用于提高加工精度。
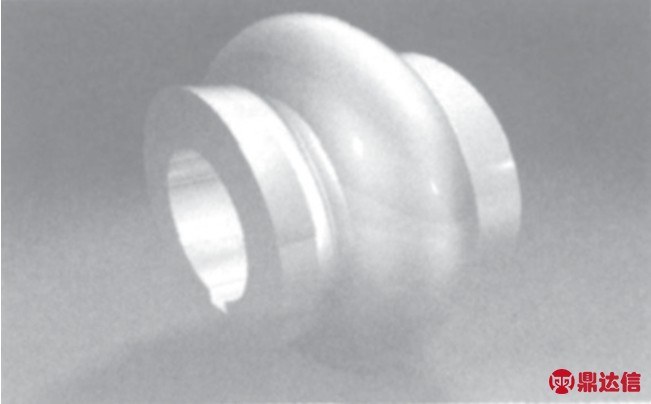
图1 光顺处理效果图
Fig.1 Renderings of smooth treatment
前边提到的解析法主要是通过工具和螺旋面工件的啮合原理,推导出工具和螺旋面之间的接触线,进而由接触线求得工具截形。但是对于工具截形具有奇异点的情况,由于工具表面奇异点的法向量不能确定,这时采用解析法不太适用。对于此问题韩国的Nguyen 等[12]提出了一种采用砂轮表面的相切方程和接触方程的求解方法,研究了砂轮一般表面和砂轮锐边在螺旋槽加工过程中发挥的作用,提出了对工具截形有奇异点情况的精确计算方法。
范东风[13]和赵万镒[14]等将前边提到的砂轮截形解析法应用在滚珠丝杠螺母滚道的加工中。加工时采用倾角成形磨削加工(使砂轮磨杆与螺母轴线之间的夹角等于螺母的螺旋升角,螺母绕其轴线做旋转运动,而砂轮沿螺母轴线做直线运动)。由于砂轮轴线与工件轴线之间存在安装角度时砂轮磨杆容易与磨削滚道面发生干涉,如图2所示[15],使砂轮不能越过这一位置完成整个内螺纹的磨削加工,这样就限制了可以加工螺母的长度,使大长径比的螺母磨削加工变得非常困难。日本北海道大学的Kagiwada 等[16]针对长径内螺纹提出了一种基于通用砂轮截形的磨削方法,采用标准砂轮截形,通过对砂轮轴倾斜角度进行优化,选择最优的倾斜角度来加工螺纹滚道,最佳倾斜角度只和砂轮廓形和滚道截形的符合。但是其优化安装角度过程中,只考虑了砂轮的截形,没有考虑螺旋面的截形,不可避免砂轮会对已加工表面过切,使得到的螺纹截形不是目标螺纹滚道截形。对此问题,范东风[13]、Kagiwada[16]、姜洪奎[17]、和Harada[18]等提出了针对大导程内螺纹在改变砂轮安装角的同时,改变砂轮的截形,对螺母滚道进行磨削加工。以螺旋面法向截形为已知条件,根据齿轮啮合原理推导砂轮截形公式,并对理论模型进行数值计算,求解砂轮截形。
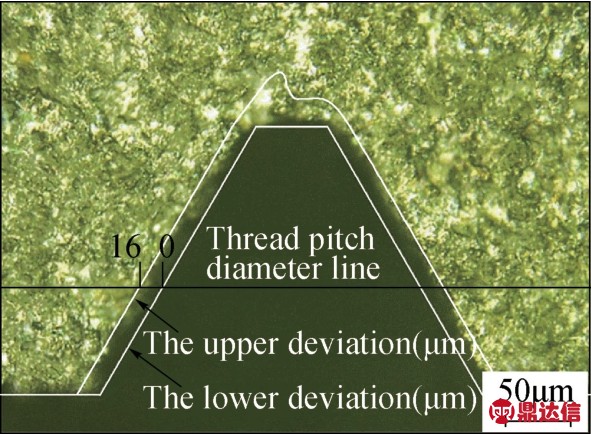
图2 螺母滚道干涉示意图
Fig.2 Schematic diagram of nut raceway interference
莫斯科国立工业大学的Volkov等[19]提出了一种不倾斜砂轮轴线来加工内螺纹的数学模型,解决了砂轮截形弧线部分的计算问题,模拟砂轮磨削某一齿廓的过程来确定加工螺纹表面,通过对模拟磨削过程所得到的曲面与所要求曲面进行比较,对加工误差进行了评定。大连理工大学的Gao 等[20]也提出一种平行轴磨削方法,如图3所示,砂轮轴和工件轴平行,偏心距离为e,砂轮绕自身轴线高速旋转,轮的进给运动是沿螺旋线进行的:一方面砂轮轴绕工件轴作匀速圆周运动;另一方面,砂轮轴沿轴向作匀速直线运动,在硬脆材料上加工了微小内螺纹,并建立了一个数学模型来预测螺纹齿形误差,通过研究砂轮直径与螺纹中径的比值和砂轮截形角度与螺纹齿形误差的变化关系,提供砂轮参数的合理范围,如砂轮截面角度的变化范围,砂轮直径与螺纹中径的比值的变化范围。对于尺寸为M2 内螺纹的加工,采用砂轮参数为:砂轮直径1.5mm,砂轮磨杆直径0.9mm,砂轮截形角度56°,加工的螺纹精度能达到H4 级,如图4所示[20]。
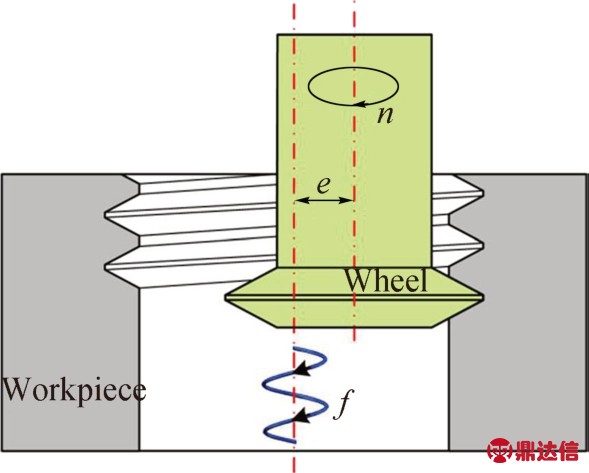
图3 平行轴内螺纹磨削示意图
Fig.3 Schematic diagram of parallel axis internal thread grinding
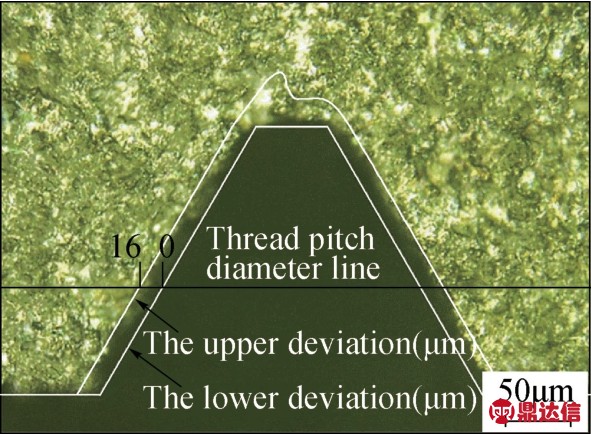
图4 M2内螺纹廓形的测量
Fig.4 Measurement of single thread profile of M2 internal thread
由于与螺旋面成形磨削理论相同,成形铣削技术中铣刀廓形的设计方法与成形砂轮廓形设计方法相似,因此铣刀廓形的确定方法也是可以借鉴的。高明明等[21]根据无瞬心包络铣削原理,建立了工具与工件的相对位置及坐标系的变换,并基于啮合位置的接触点的相对速度与该点的公法线垂直这一啮合条件建立了啮合条件方程式。李成松[22]从成形铣削原理展开研究,建立铣刀与工件的相对位置坐标系,同成形磨削原理类似,通过建立工具与工件接触线条件式,并利用数值分析方法求解条件式,得到铣刀轴向截形。丁伟等[23]也是利用已知的螺旋面方程,由共轭原理计算工具截形,提出了对于端截面、轴截面、偏轴截面、法截面等各种螺旋型面的数学模型,为复杂螺旋面螺杆外、内(旋风)铣削加工提供了工具设计的数学模型。
以上提到的工具截形计算方法主要是基于啮合原理求得接触条件式,并利用数值分析方法求解得到工具截形。随着计算机技术的发展,许多学者进行了计算机辅助工具截形设计研究。Kang 等[24–25]提出利用微分几何和运动学原理,建立了广义螺旋槽加工模型,并利用CAD 方法对该问题进行了分析。Ivanov 等[26]针对解析法的非线性方程不易求解和图解法工作量大、精度低的问题提出了基于CAD 的通用成形砂轮轮廓建立模型。应用计算机辅助设计不仅极大地简化了运算过程,并且提高了运算精度。但是大部分的计算机辅助设计方法只是针对解析法的全部或者计算机化,后来又有学者提出和解析法完全不同的计算机辅助设计方法。如郑州大学的马田军等[27]通过研究螺旋面加工机理,借助于SolidWorks 三维建模软件,通过应用布尔运算方法求取工具截形,用螺旋面工件来反求工具截形。应用布尔运算解决截形设计问题的还有匈牙利的Hegedüs 等[28]也提出应用布尔运算方法,用工件表面减去砂轮表面来确定生成的工具轮廓,如图5所示。
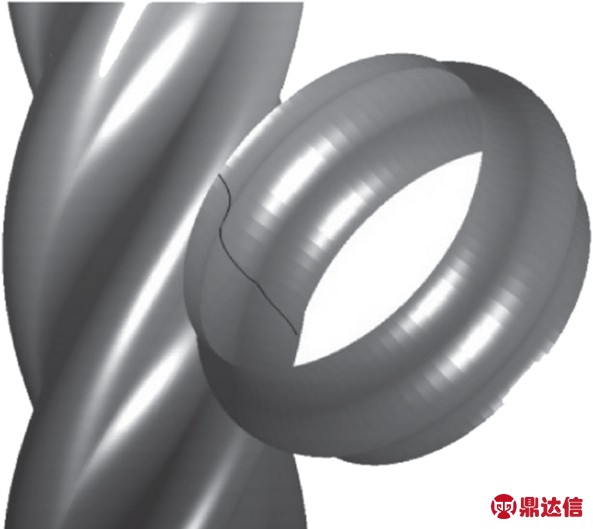
图5 布尔运算法计算砂轮截形
Fig.5 Calculation of wheel truncation by Boolean operation
由于需要进行多次体布尔运算,运算量非常大,计算机运行时间长,占用内存大,对设备的要求非常高,因此在此基础上进行改进,提出了薄片法来求工具截形。薄片法主要是将螺旋面工件切成薄片,让每一薄片绕工具轴线回转包络工具毛坯,通过多次面布尔运算和体布尔运算最终求的工具截形面布尔运算相对于体布尔运算量小,薄片法具有精度高、占用内存小、运算量小、运算快的特点。为了进一步减小运算量又提出了半径法来求加工螺旋面用成形砂轮截形,该方法只用做一次体与体的布尔运算,利用CAD 的方法获得多个截面的交线,通过求得交线上到砂轮轴线距离最短的点,求得工具截形。与半径法类似的有况雨春等[29]提出的基于MATLAB 对砂轮截形进行设计的数值方法。通过坐标变换将砂轮坐标系和工件坐标系统一,将工件和砂轮离散,找到砂轮和工件相交线上到砂轮轴距离最小的点集,应用编程仿真得到更加精确直观的砂轮截形,如图6所示[29],图中黑线为螺旋面与砂轮接触线。
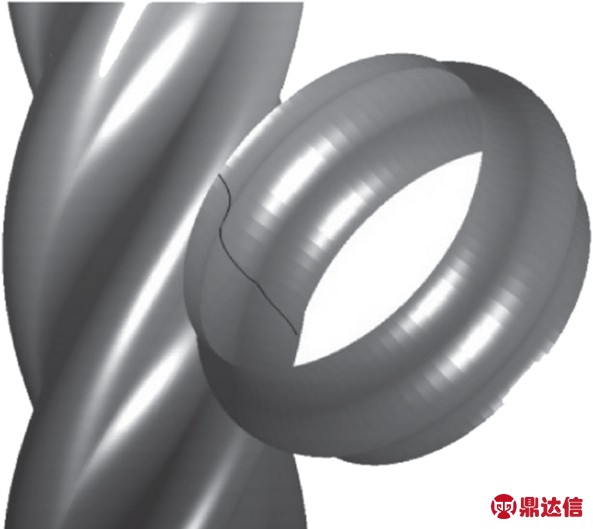
图6 砂轮与螺旋面的接触状态仿真图
Fig.6 Simulation diagram of contact state between grinding wheel and spiral plane
综上所述,面向内螺纹磨削砂轮截形的设计研究从最开始的图解法,发展到后来用数值法求解砂轮截形,既减小了工作量又提高了设计精度,后来随着计算机技术的发展,通过计算机辅助方式发展出了精度更高设计结果更直观的设计方式,进一步应用计算机进行砂轮截形辅助设计是未来的发展趋势。
普京总统2018年3月1日发表国情咨文,提出要大力发展人工智能等先进技术,将基础设施建设与无人驾驶、海上和空中导航系统相结合;利用人工智能组织物流;到2024年向公民开放“数字世界的所有可能性”;提供在线教育、远程医疗、商务,以及数字空间广域的人工智能化的现代服务。在最短的时间完成人工智能的立法。
内螺纹磨削用砂轮磨杆研究
在进行大长径比内螺纹磨削时,砂轮磨杆呈细长悬臂状态,由于磨削时砂轮的转速一般较高,极易发生由砂轮磨杆弱刚度特性引起的颤振问题。磨杆的振动问题有以下4 个缺点: (1)振动会使加工表面产生振纹,影响加工精度;(2)振动使机床主轴受交变载荷,降低机床寿命;(3)振动加剧砂轮磨损;(4)为避免振动可采用的方法是采用小切削深度的方法,但是这会降低加工效率,因此研究砂轮磨杆结构来减小振动对内螺纹磨削非常重要。以瑞典、美国、日本为首的加工制造业比较发达国家一直致力于减振砂轮磨杆/刀杆的研制工作,总的来说,减振砂轮磨杆/刀杆的研究和发展是比较缓慢的。到目前为止,世界上只有少数几个国家的厂商可以生产出减振效果较好的磨杆。国内外研究者主要是在材料和结构两方面进行了探索。
一种方法是通过采用特性较好的新型材料来改善磨杆性能。主要通过这些材料的硬度和强度来提高磨杆的静刚度,并且选择密度较小的材料来减小刀杆的质量,提高刀杆的固有频率,提高磨杆动刚度。新型材料主要包括Ti 合金、硬质合金和新型陶瓷等。实际生产应用中有用硬质合金代替钢材来作为磨杆的制作材料,由于硬质合金和钢相比具有弹性模量高的特点,所以由硬质合金加工的刀具静态刚度比较好,但由于硬质合金密度大,导致硬质合金制造的磨杆动态性能不好。因为陶瓷具有弹性模量高、密度低的特点,再配合上金属又具有高韧性的特点,有学者提出可以将陶瓷和金属结合起来制作磨杆。燕山大学的王军等[30–31]提出了一种金属–陶瓷复合结构的磨杆,如图7所示[31],这种磨杆的静刚度较传统钢材的磨杆提高了10%~30%,动刚度较传统磨杆也有了很大提升。此外,国内外还有一些研究者提出了应用铝合金材料的磨杆,铝合金相对于其他工业金属具有较小的密度,可以有效地减轻磨杆的整体质量,当磨杆在进行加工时产生的回转惯性力也随之减小,在高速旋转的刀杆中惯性力较小,可以很好地适应高频振动环境下的工作。其中比较典型的铝合金刀杆是瑞典Sandvik 公司生产的Coromant 型铣刀等产品。辽宁工程技术大学的于英华等[32]提出了一种泡沫铝复合结构内圆磨杆,分析发现此磨杆静态和动态性能优于20MnVB 材料的磨杆。

图7 金属–陶瓷复合结构磨杆示意图
Fig.7 Schematic diagram of grinding rod of metal–ceramic composite structure
另一种方法是通过设计磨杆结构在磨杆中增加阻尼器,阻尼器在运动过程中对磨杆产生阻碍作用,可以有效消耗振动能量,使磨杆振动减小。中北大学的张恒明[33]采用将铣刀杆前段加工成空心的方法,在空腔中填充上阻尼颗粒,铣刀在转动时,颗粒之间相互碰撞,将铣刀杆的振动吸收,达到减振的效果。西华大学的郭佳等[34]、哈尔滨理工大学的韩东[35]、北京航空航天大学的杨毅青等[36]都采用类似的方式,通过将铣刀杆加工成中空的结构,在空腔中加入阻尼件来达到减振的目的。另外还有通过用磁流变材料、压电材料等来加工镗杆,通过改变磁场或者电场的方式主动改变刀杆的固有频率或主动生成振动来抑制镗杆振动。采用阻尼器的方法进行减振的磨杆或者镗杆可以达到良好的减振效果,但是其缺点是结构较为复杂,阻尼器多种多样,并且磨杆直径比较小,在磨杆中加阻尼器难度较大。
综上所述,国内外有关旋转式减振工具杆的研究主要集中于镗杆,而减振砂轮磨杆研究目前还较少,其原因是砂轮磨杆尺寸小而转速高,相对镗刀杆来说减振设计难度大,综合减振措施难以实现。一般对于回转运动的磨杆来说,新型材料的特性往往无法满足多方要求,通常只能改善动态或静态一方面性能。如果磨杆应用材料比较脆硬,那么磨杆具有较高的静刚度,在高速振动中,其动态响应位移将会很大,动态性能较差。相反,如果材料具有一定弹性,可以有效地消耗振动产生的能量,其动态响应位移将会减小,但其静刚度也将会减小,无法满足低速时的性能要求。因此通过改变磨杆的结构,将不同的材料特性结合起来,才能使磨杆具有较好的减振效果。
内螺纹磨削中砂轮修整方法研究
对于内螺纹成形磨削来说,砂轮截形的精度严重影响加工螺纹精度。当内螺纹的牙形尺寸较小时,成形砂轮特别是影响螺纹内角尖端圆弧半径的砂轮顶角部分在磨削加工过程中极易发生磨损,使砂轮极易失效,加工精度很难保证。大连理工大学的Gao 等[20]采用金属基细磨粒金刚石砂轮进行了长径比为1.5、行程为3mm 的内螺纹磨削加工,结果表明在加工30mm 螺纹后,内螺纹齿形精度已严重丧失,如图8所示[20]。所以在内螺纹加工过程中需要对砂轮进行多次重复修整,加工效率极低,有时甚至无法完成磨削加工,因此内螺纹磨削砂轮修整问题需要进行研究。
目前,砂轮的修整方式主要有车削修整法、滚压修整法、磨削修整法、激光修整法、电火花修整法、超声修整法及复合修整法等。大部分学者对不同砂轮的修整都主要集中在平面磨削领域,但是对于微齿内螺纹螺旋面磨削用成形砂轮的修整研究比较少。上海工程技术大学的朱欢欢等[37]对滚珠丝杠成形砂轮修整工艺原理进行研究,采用金刚石滚轮修整砂轮,分析了影响修整效果比较明显的修整深度、修整速比和光修时间3 个修整工艺参数对修整效果的影响,用金刚石滚轮与砂轮的干涉角作为综合修整参数来分析修整状况,通过试验研究了干涉角对修整结果的影响。但是这一方法需要预先将修整轮加工成目标砂轮截型,由于金刚石滚轮也会磨损,所以这种修整方法过程比较复杂且修整精度不高。山东大学的姜洪奎等[17]在大导程滚珠丝杠副螺母加工的研究中通过数值计算方法得到了螺纹磨削的砂轮截形参数,并进一步得到了靠模板的截形,设计了砂轮修整器,如图9所示[17],通过修整器用金刚石笔来进行成形砂轮的修整。但是这种修整器不具备可调性,并且要受到靠模的廓形精度、安装精度以及操作条件等的影响。陕西理工学院的赵永强等[38]提出了对于螺杆加工用成形砂轮精密修整的CNC 系统,首先通过数值计算得到砂轮截形参数,再由截形参数精确控制CNC 系统,如图10所示[38],应用数控方法对成形砂轮精密修整,这种修整法修整参数可调,工作可靠,修整精度高。航天一院的董超等[39]利用金刚石碟轮对螺纹成形磨削用的陶瓷CBN 成形砂轮进行修整,选用砂轮和碟轮的修整速比、砂轮轴向进给速度、碟轮修整进给量3 个修整参数进行正交试验设计,以螺纹环槽表面质量好坏、螺纹齿形角误差及螺纹形状轮廓完整性作为评价指标确定最优修整参数组合。哈尔滨工业大学的Guo 等[40]采用电火花修整方法对V 型砂轮进行修整,得到尖角半径22.5μm,角度为120.03°的V 型砂轮,加工得到的WC 表面V 型微结构底角圆角为55μm。
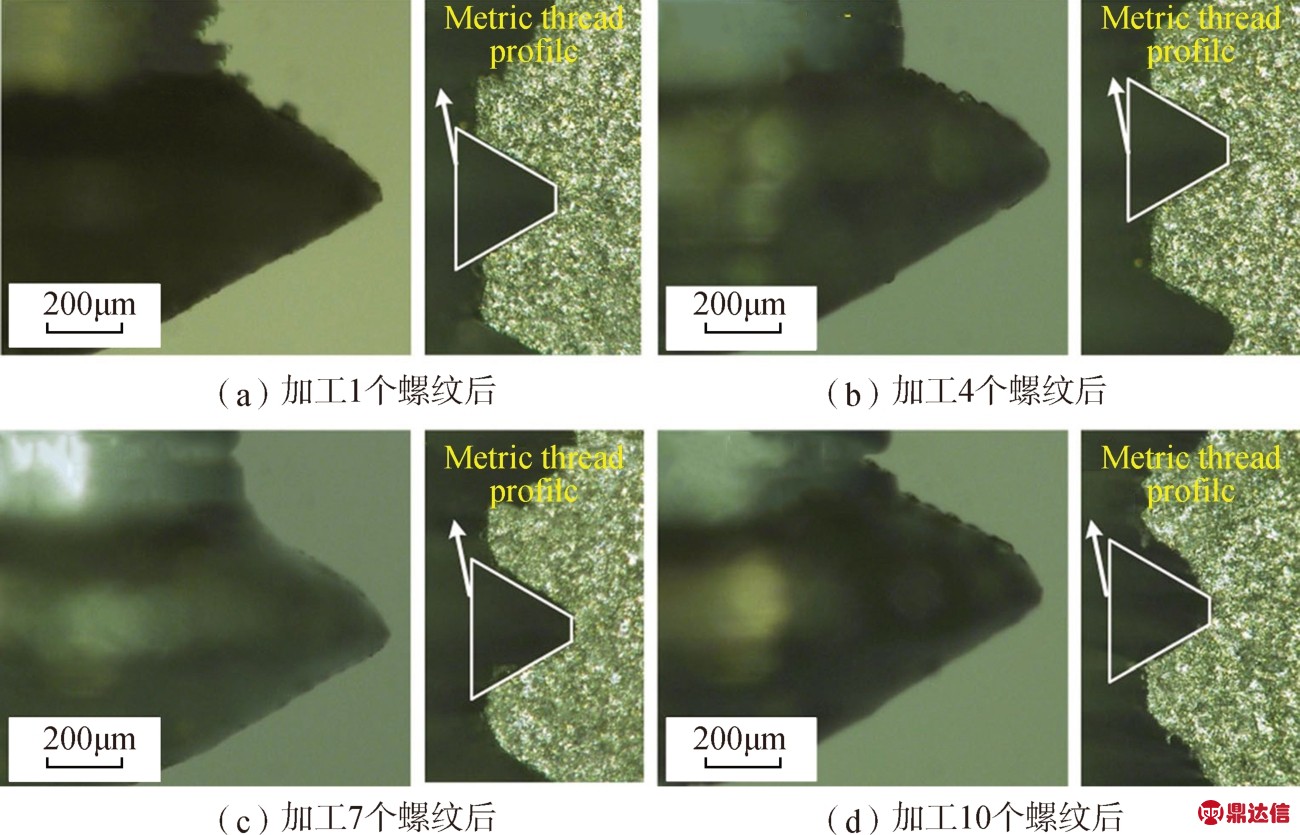
图8 砂轮磨损状况对螺纹轮廓的影响
Fig.8 Influence of grinding wheel wear condition on thread profile
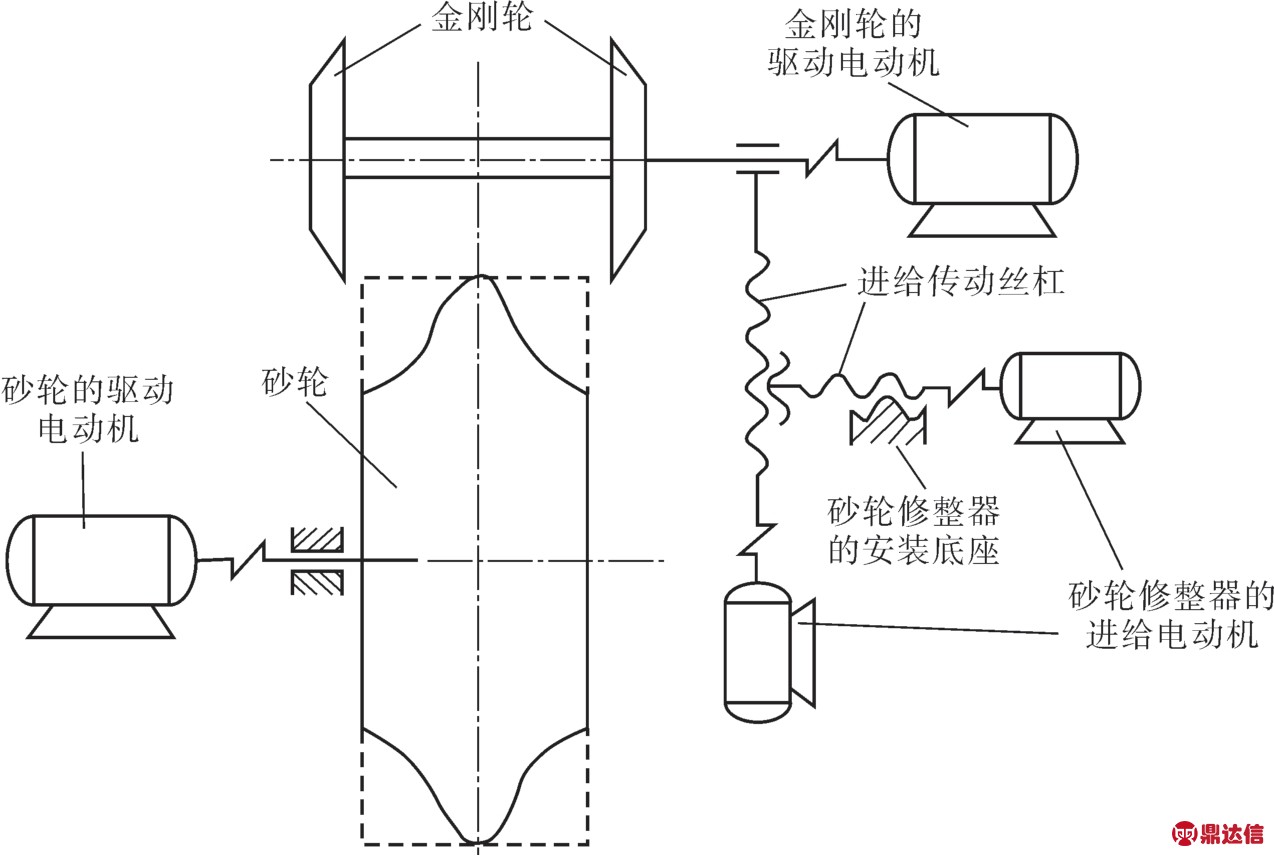
图9 修整器模型
Fig.9 Dresser model
综上所述,内螺纹磨削用的成形砂轮磨损严重,因此对于螺纹磨削用成形砂轮的修整非常重要,比较常用的修整方法为单点金刚石笔车削修整、滚轮磨削修整等传统的修整方法,应用电火花、激光、超声及复合修整方法的研究还比较少,这可能是未来螺纹磨削成形砂轮修整的发展方向。
内螺纹精密磨削加工工艺研究
内螺纹在进行精密磨削加工之前有一个重要环节,即对刀。对刀误差是影响螺纹加工精度的一个重要因素。内螺纹加工对刀不同于外螺纹,因为内螺纹的加工是在一个半封闭的环境中,采用接触式对刀方式比较困难。国内南京理工大学的张传剑等[41–42]提出了一种非接触式自动对刀技术,对刀重复精度达到0.002mm,应用这种对刀方式提高了内螺纹磨削过程中的对刀精度,减小了对刀误差,提高了对刀效率。
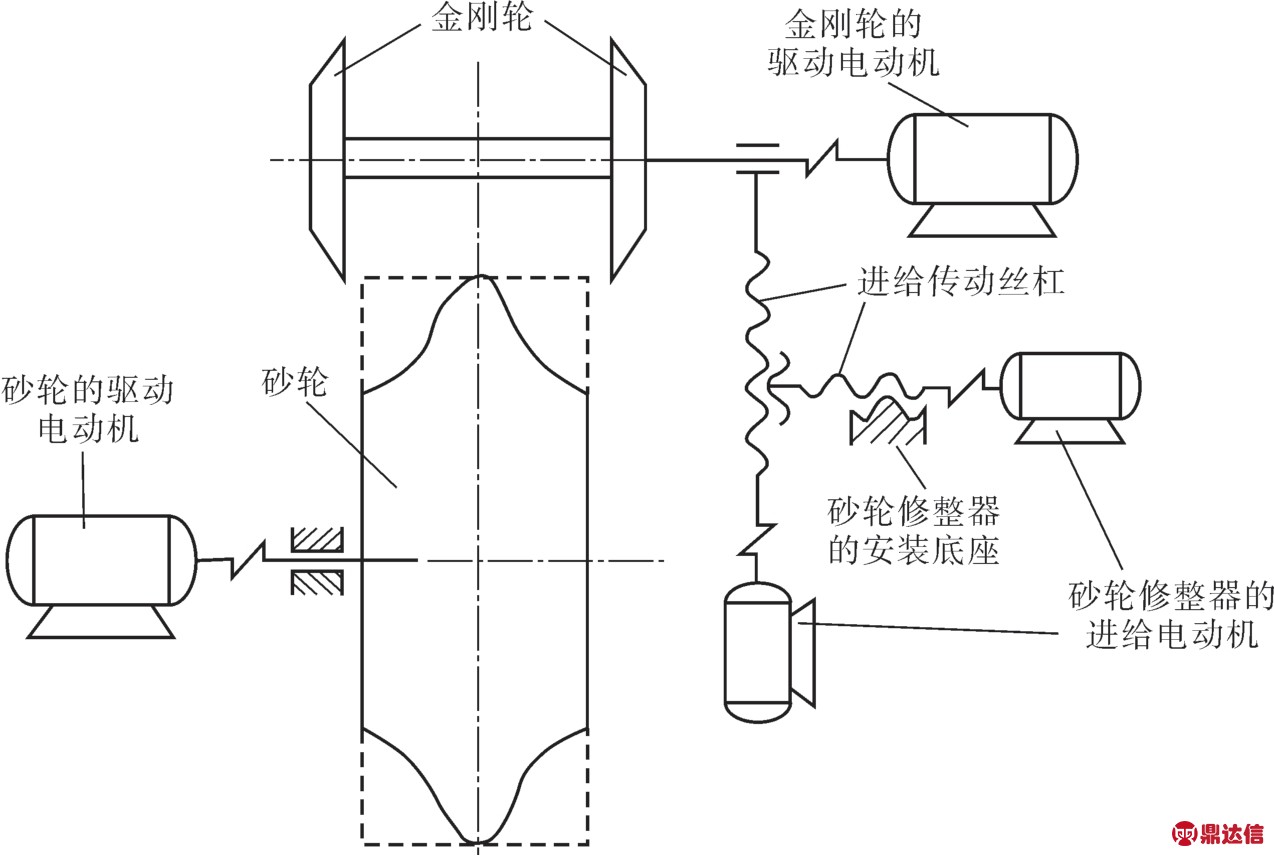
图10 CNC修整器示意图
Fig.10 Schematic diagram of CNC dresser
对于内螺纹的磨削工艺研究主要关注砂轮转速、磨削进给量以及工件转速或轴向进给速度2 个试验参数对螺纹加工结果(齿形误差和表面质量)的影响。Gao 等[20]通过用设计好的砂轮采用平行轴磨削的方式在SiCp/Al 上加工螺纹直径为2mm的内螺纹,通过试验发现,当砂轮转速越大,轴向进给速度越低时,加工的内螺纹表面质量越好,并且最终加工精度能达到H4。董超[43]通过对砂轮线速度、磨削进给速度、工件转速3 个试验参数进行正交试验设计和对试验结果分析,找到了砂轮的线速度、磨削进给速度、工件转速3 个工艺参数的最优值。
除了传统的磨削加工内螺纹试验,也有学者进行了超声振动辅助磨削内螺纹试验。河南职业技术学院的Feng 等[44]提出了用超声振动辅助加工内螺纹,根据超声纵扭振动的特点,分析了单粒磨粒在常规磨削和超声纵扭振动辅助磨削条件下的运动轨迹,如图11所示[44]。通过试验研究了加工参数对两种金刚石砂轮磨削力、孔表面质量、螺纹轮廓精度和磨损状况的影响。结果表明超声辅助振动可以降低磨削力,而磨削力主要由进给率控制,主轴转速和超声振幅对磨削力的影响较小。采用适当振幅的超声辅助振动磨削可以减小砂轮的磨损,延长其使用寿命,提高螺纹的精度和合格率,这一试验证明了超声振动辅助加工内螺纹的可行性。
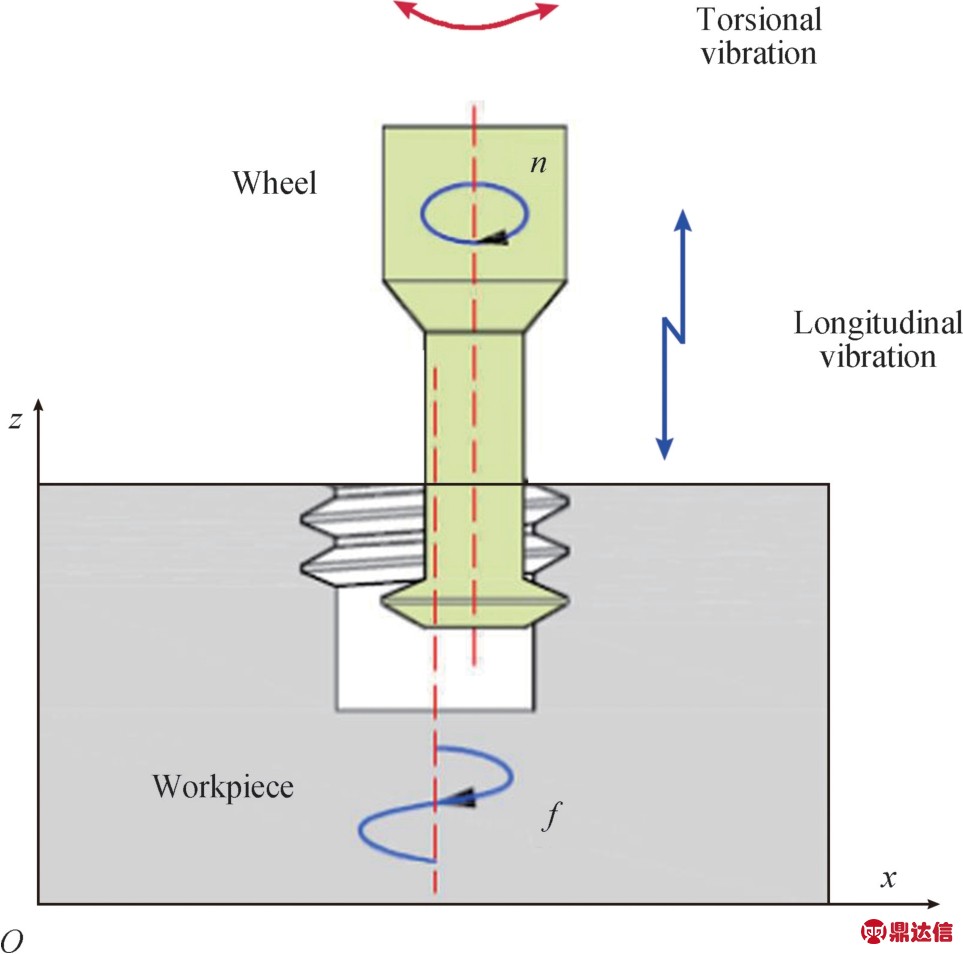
图11 超声振动辅助加工内螺纹示意图
Fig.11 Schematic diagram of ultrasonic vibration assisted machining of internal thread
磨削力来自于砂轮与工件接触表面的弹性变形、塑性变形和磨屑去除过程。同时,磨粒及黏结剂与工件之间的摩擦也会对磨削力产生影响。山东大学Wang 等[45]在单磨粒磨削模型的基础上,考虑内螺纹磨削过程中磨粒动态接触弧长和磨粒几何特性,建立了动态数值磨粒模型,并研究了内螺纹磨削过程中磨削力和动态接触弧长的变化特性。但模型从均匀磨粒出发,没有考虑磨削力的不均匀性和磨粒的重叠问题,并且对于内螺纹磨削没有考虑螺旋角。北京工业大学的Fang 等[46]提出了考虑螺纹螺旋角和颗粒重叠效应的内螺纹磨削力模型,并通过试验对模型进行了验证,但模型中默认磨粒大小是均匀的,忽略了磨粒高度的不均匀性。近年来,虽然众多研究人员研究了各种工艺的磨削力,并建立了相应的磨削力公式,但对于内螺纹磨削过程的磨削力研究还有待进一步完善。
结论
(1)在内螺纹磨削加工中,目前主要采用解析法和计算机辅助设计两种方法。解析法是由已知的螺旋面截形方程或者复杂截形的一系列离散点,经过坐标变换求得工件与砂轮之间的接触线,进而求得砂轮截形。计算机辅助设计分两种,一种是将解析法部分或全部程序化来求解砂轮截形;另一种是应用三维仿真软件,采用布尔算法,直观地得到砂轮截形。
(2)在进行大长径比内螺纹磨削时,砂轮磨杆呈细长悬臂状态,极易发生由砂轮磨杆弱刚度特性引起的颤振问题,严重影响加工精度和加工效率。相对切削加工过程中的减振工具,对于砂轮磨杆的相关研究还较少,且研究主要集中在磨杆结构以及新材料利用等方面。
(3)对于内螺纹磨削砂轮磨损严重情况,目前内螺纹磨削砂轮的修整主要采用磨削修整法和车削修整法两种方法,结合CNC 技术进行修整,可以更精确地控制修整参数,修整精度更高。
(4)国内外对与内螺纹磨削工艺的研究较少,内螺纹磨削工艺主要从内螺纹对刀、工艺参数研究、超声振动辅助磨削和磨削过程中磨削力预测模型等方面进行了研究,为以后内螺纹磨削工艺研究方案拟定提供了参考。