摘要:设计了一种盖子的双层脱螺纹机构及其模具,盖子中心孔内分上、下两层设置梯形内螺纹、细牙内螺纹特征。模具布局1 模1 腔,两板式单次开模。模架使用一种非标改装模架,无推板机构;为保证上、下螺纹型芯的同轴度,模架导向机构使用一种特殊的单导柱,在定模板、动模板上都设有配套双导套的单导柱导向机构。模腔的浇注采用潜伏式浇口以实现自动脱废料。针对上层梯形螺纹的脱模,采用油缸驱动齿条从而驱动内螺纹型芯转动,并由螺纹导向套进行转动控制的脱模方式。针对下层细牙螺纹的脱模,采用电机驱动螺纹型芯转动以实现螺纹脱模的方式。脱螺纹机构结构设置合理,动作可靠,成型效果良好,可为同类塑件的注塑生产提供有益借鉴,降低潜在设计风险。
关键词:注塑模具;螺纹抽芯;脱模;机构设计;模具设计
螺纹联接是塑件零件之间联接的一种重要方式,塑件设计中,所使用的塑料制品螺纹的类型有:①标准螺纹,主要为三角形截面螺纹(V 形螺纹),这类螺纹装拆简便、快速,广泛用于联接与紧固,螺纹联接强度低,螺纹牙尖部分难于充满成型,小螺距(<0.7 mm)螺纹不宜模塑成型。②方形螺纹,主要用于管件制品之间的高强度联接。③梯形螺纹,主要用于泵壳等的高强度联接,成型较方形螺纹容易。④锯齿形螺纹,这种螺纹具有方形螺纹的联接效率和V 形螺纹的强度,沿轴向有较高的应力,用于单向受力及软质瓶口联接,应用面较窄。⑤圆弧形螺纹(瓶口螺纹),由玻璃瓶口螺纹移植而来,螺纹根部不产生应力集中,旋出旋入十分方便,其成型时可采用强制脱模。螺纹的脱模是带螺纹塑件模具结构设计中的难点,针对不同类型的螺纹,进行模具设计时,其脱模方式的选择及脱模机构的设计须区别对待 [1–3]。
塑件螺纹模塑成型时,有内、外螺纹之分。对外螺纹而言,脱模机构设计相对较为简单,可以通过型腔、型芯分型面设置而实现上、下开模,或者通过滑块前、后开模来自然脱模[4],或者旋转抽芯脱模[5]。而对内螺纹而言,如果孔内仅有单一内螺纹,且成型精度一般,可以采用旋转螺纹型芯的方式来脱模,对应的脱模机构有马达驱动螺纹型芯式[6–9]、齿轮齿条驱动螺纹型芯式[10–11]以及蜗杆模板驱动螺纹型芯式等机构[12–13]。若内螺纹成型精度要求高,有两种特殊的脱模方式,其一是采用螺纹型芯分块差速抽芯机构[14–15],其二是将螺纹型芯劈分成四个内收分块,然后采用分步顺序抽芯方式[16]。
而对于塑件上同一轴心孔内,当其上、下层都设置有内螺纹,且上、下层螺纹为两种不同类型的内螺纹时,在孔内同轴的两个反向方向须设置两个不同类型的螺纹型芯来脱模;不同类型螺纹型芯的抽芯,则须结合螺纹的类型,设计不同的旋转驱动机构来进行驱动。笔者以带上、下层不同类型内螺纹特征的螺纹盖塑件为例,论述其脱模机构的设计思路和方法,为同类塑件的模具设计提供参考。
1 塑件特征
螺纹盖塑件结构如图1 所示。
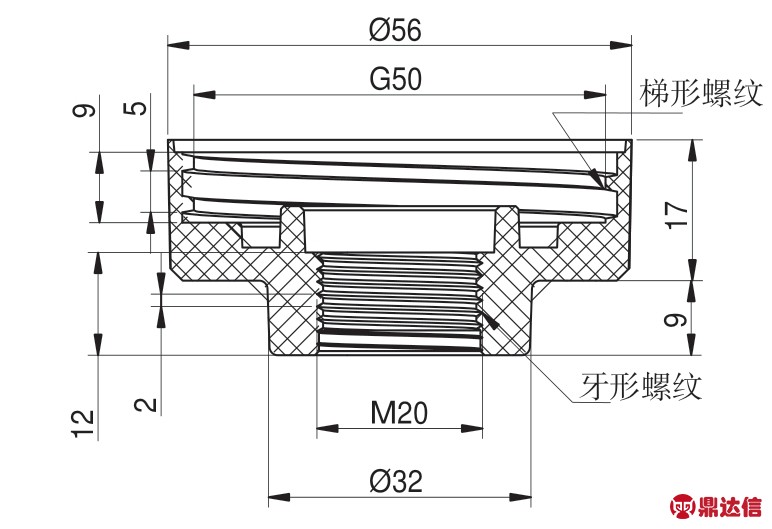
图1 塑件结构
塑件为圆台双层盖子,上层盖子的外径56 mm,下层盖子的外径32 mm。上层盖子的内环中,设置有梯形管螺纹G50,螺纹深度9 mm,螺纹节距5 mm。下层盖子内环中,设置有普通细牙螺纹M20,螺纹深度12 mm,螺纹节距2 mm。中间为Ø23 mm 的通孔。塑件材质选用改性塑料合金——聚碳酸酯(PC)/丙烯腈–丁二烯–苯乙烯塑料(ABS),其收缩率0.45%。塑件产量要求5 万个。塑件成型精度MT5 级。
2 模塑成型处理
塑料螺纹注射成型一般用于螺纹外径大于3 mm、配合长度短(<30 mm)、精度低的螺纹,其成型方法包括有3 种,分别为:①采用螺纹型芯(螺纹型环)成型;②瓣合成型;③整体型芯(型环)成型,成型后可强制脱模(一般用于软质塑料成型)[17]。显然,本塑件的成型适用第①种方式来进行成型。
模塑成型前,对塑件结构进行如下的前处理:
①对螺纹节距和螺纹配合长度进行了修改,即上、下层螺纹节距≥0.75 mm,螺纹配合长度≤12 mm,这样可使两螺纹都满足充填饱满、便于脱模及旋合性良好的成型要求。
②在螺纹的配合长度小于1.5 倍螺纹直径的基础上,设计螺纹型芯时,为保证旋合性良好,上、下层螺纹中径上的配合间隙分别增大0.2 mm 和0.15 mm。
③针对螺纹的第一圈易损伤问题,上、下层螺纹的入口处分别设置深度2 mm 和3 mm 的入口槽。
④为保证螺纹型芯的顺利脱出,上、下层螺纹的底端延长圆柱面深度分别为1 mm 和6 mm。非螺纹部分内、外壁的脱模斜度分别为:上层盖内壁的拔模锥度α ≥2°,下层盖内壁的拔模锥度α ≤ 1.5°。
3 分型及脱模设计
3.1 分型面的选择
塑件在模具的布局设计如图2 所示。
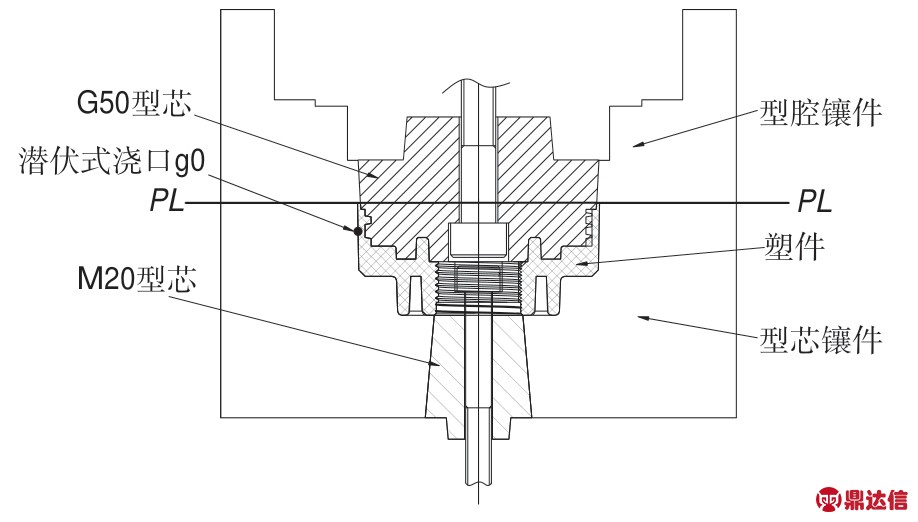
图2 分型及螺纹型芯设置
从螺纹结构特点看,梯形管螺纹G50 旋转脱模时的转动圈数少,较为容易脱模,因此需要的脱模机构组成零件相对较少;而M20 螺纹的转动圈数多,包紧力相对较大,不容易脱模,故其脱螺纹机构组成零件相对较为复杂一些。考虑到动模一侧有利于多零件的安装以及模具开模后塑件必须留于动模一侧,因此,为了便于上、下内螺纹的脱模机构的设计,同时为了使塑件脱模后在分型面所在平面的外径最大,选择了图2 中所示的分型线PL。
另外,考虑到塑件自动化生产的需要,注塑的自动脱模应包括流道废料的脱模和塑件本身的脱模,因图2 中塑件的上、下型芯都需要设置螺纹型芯活动机构,故模腔的浇注只能采用侧浇口形式,若考虑到浇口的自动剪除,则图2 中浇口g0 应用潜伏式浇口较为合适。
3.2 塑件脱模
采用上述分型及对应的成型螺纹型芯后,塑件可以按以下步骤实现脱模:①G50 型芯先旋转抽芯;②PL 面打开;③M20 螺纹型芯旋转抽芯,依靠旋转螺纹所产生的轴向推力将塑件从型芯镶件上推出而脱模。
4 模具结构设计
4.1 模架的选用
本塑件的脱模只需要一次开模即可,因而,模架选用两板模比较合适,具体的模架结构如图3 所示。
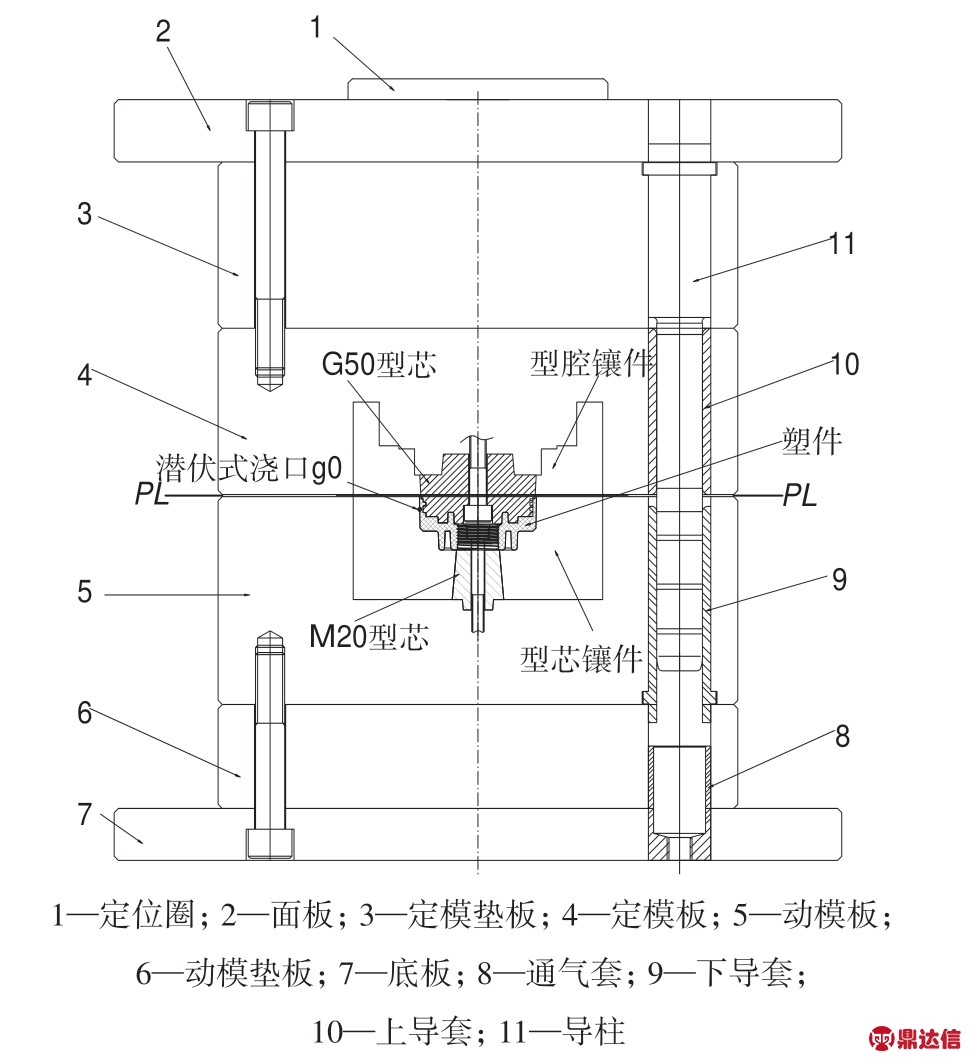
图3 模架结构
模架中,G50 型芯需要设置旋转抽芯机构,因而其定模需要增加一块结构板即定模垫板3,同样,动模需要增加一块结构板即动模垫板6。模架不设置专门的顶出板机构。考虑到G50 螺纹型芯和M20 螺纹型芯同轴要求,模架的导向机构由导柱11、上导套10、下导套9 组成。设置通气套8,一则保护导柱11,另一则便于导柱11 插入下导套9 时排气。模架依照PL 单次分型打开。
4.2 模具机构布置
模具采用两板模结构方式,布局为一模一腔,如图4 所示。图5 为模具成型件的设置(其为图4的A-A 剖面)。对应于塑件的脱模需要,定模一侧需要布置G50 型芯驱动机构,动模一侧需要布置M20 型芯驱动机构来实施塑件螺纹的脱模。
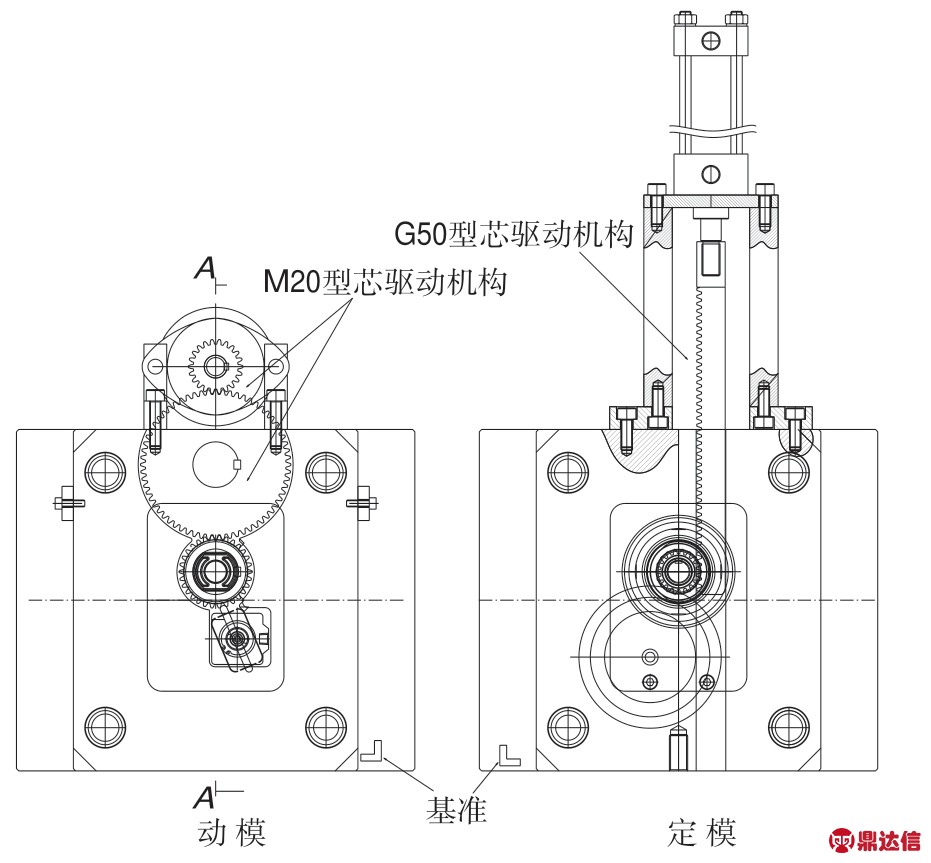
图4 模具布局
(1)浇注系统。
采用潜伏浇口以实现自动脱废料的方式,流道采用Ø6 mm 圆形流道,将浇口衬套12 设置于定模板4 上,以缩短浇注系统的流道长度。采用定位螺丝对浇口衬套12 进行定位和紧固,以防止其工作时转动。浇口的开设位置偏离模具的中心,为偏心设置方式。
(2)冷却系统。
采用水冷方式,在型腔镶件29、型芯镶件30 上各采用一条Ø8 mm 的环绕型水道对其进行冷却。
(3)排气系统。
采用镶件间隙排气方式进行排气,排气间隙δ ≤ 0.02 mm。
(4)导向系统。
模具为两板模结构,因而其导向机构较为简单,即采用四副导柱11/下导套9 导向机构即可实现模具模板开闭的导向功能。
(5)顶出系统。
塑件流道废料的顶出由件13~件18 所构成的顶出机构顶出。
4.3 脱模机构设计
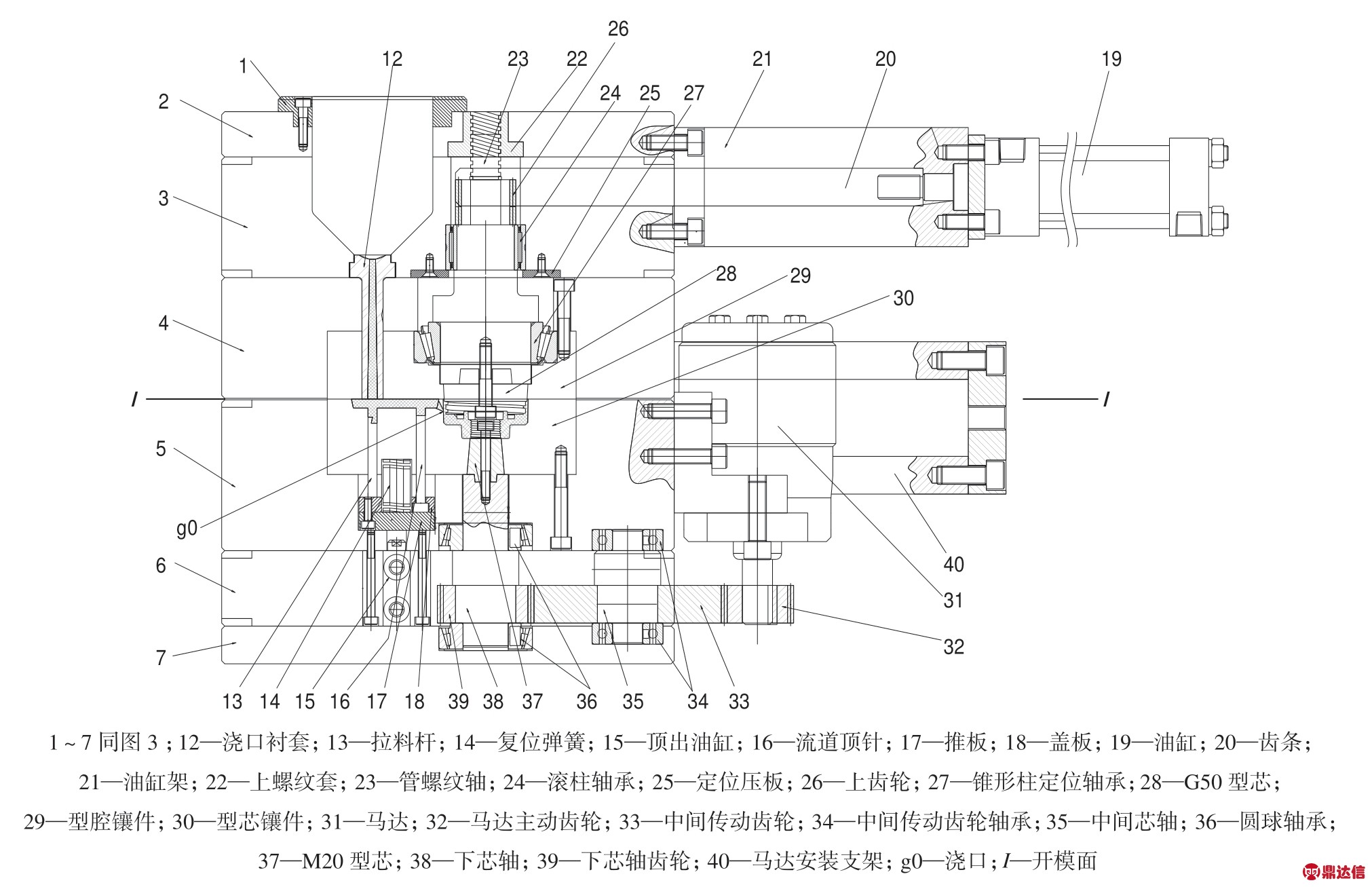
图5 模具成型件设置
塑件在模具模腔内的完全脱模分为四个步骤,涉及到两个螺纹脱模机构的设计。具体的四个脱模步骤分别为:①塑件上半部分的G50 螺纹先脱模;②塑件从型腔镶件29 上脱出;③流道废料与塑件脱离;④塑件下半部分从型芯镶件30 的螺纹中旋转脱出。
从塑件的脱模过程设计中可以看出,塑件的脱模过程为:①注塑完毕,油缸内螺纹G50 先脱螺纹;②模具打开,型腔镶件29 与塑件分离;③顶出油缸15 驱动拉料杆13 将流道废料从型芯镶件30 顶出,实现流道废料与塑件分离;④马达31 驱动M20 型芯37 旋转以实现M20 螺纹脱模,同时将塑件从型芯镶件30 上脱出,从而实现整个塑件的脱模。因而,本模具的两个脱模机构G50 内螺纹脱模机和M20内螺纹脱模机构的设计显得尤为重要,其结构设计如下所示。
(1) G50 管螺纹脱模机构。
G50 管螺纹脱模组件包括件19~件28。G50型芯28 通过螺钉紧固安装于管螺纹轴23 上,管螺纹轴23 的尾端设计有与G50 同节距的梯形螺纹,并与上螺纹套22 通过梯形螺旋副联接,即上螺纹套22 给管螺纹轴23 提供螺纹旋转导向,并且,管螺纹轴23 的转动与止动由上螺纹套22 进行控制。管螺纹轴23 通过滚柱轴承24、锥形柱定位轴承27 安装于模具定模内;上螺纹套22 安装于模具面板2 上;油缸19 通过带动齿条20,从而带动上齿轮26 及管螺纹轴 23,G50 型芯 28 转动,完成塑件上 G50 梯形螺纹的脱模。
(2) M20 细牙螺纹脱模机构。
M20 细牙螺纹脱螺纹组件包括件31~件40。M20 型芯37 通过螺钉安装于下芯轴38 上,M20 型芯37 无转动定位控制要求;下芯轴38 通过一对圆球轴承36 安装于模具动模上;马达31 通过中间传动齿轮33、下芯轴齿轮39、下芯轴38 带动M20 型芯37 转动完成塑件M20 螺纹脱模,并将塑件从型芯镶件30 上推出。
5 模具工作原理
实际工作时,结合图5,模具的工作原理如下所示。
①型腔脱螺纹。模具注塑完毕,开模前,油缸19 动作,带动G50 型芯28 完成塑件G50 螺纹部分的螺纹脱模。
②流道废料顶出。顶出油缸15 动作,通过拉料杆13 及流道顶针16 将流道废料顶出,顶出后,由复位弹簧14 顶回复位。
③型芯脱螺纹。模具在注塑机动模板的带动下,模具在 I–I 面处开模,型腔打开,马达 31 动作,带动M20 型芯37 转动,将塑件从型芯镶件30 旋出,完成塑件的全部脱模。
④复位。复位时,马达31 无须动作,模具在I–I面处闭合,油缸19动作,带动G50型芯28转动复位,模具完全闭合,等待下一个注塑循环的开始。
6 结语
针对带上下不同类型内螺纹的螺纹盖塑件自动化注塑生产要求,设计了两种脱螺纹机构。在塑件上层管螺纹的脱螺纹机构中,采用油缸先驱动齿条、再由齿条驱动螺纹型芯转动的方式,达到对塑件上层管螺纹脱模的目的,为保证螺纹抽芯时,塑件内管螺纹不变形,螺纹型芯的转动设置有相应的梯形螺纹导套进行导向和旋转控制。针对塑件下层细牙内螺纹的脱螺纹机构,采用直接由电机驱动中间传动齿轮的方式驱动螺纹型芯旋转而实施脱螺纹,塑件的完全脱模也依靠螺纹型芯的旋出而实现。模腔的浇注采用潜伏式浇口浇注,流道废料由油缸驱动的拉料杆和顶针直接顶出以实现废料与塑件的自动分离以及废料的自动脱模。模具结构设计合理,机构运动安全可靠,能有效地保证塑件的成型质量,实现了塑件的零缺陷自动化模塑生产。