【摘 要】大规格内螺纹铣削修复工艺可以对螺纹的坍塌、撕裂、弯曲变形等严重问题进行修复。论文对内螺纹铣削修复工艺进行介绍,并针对修复后的螺纹孔进行螺纹副抗挤压强度计算,验证大规格内螺纹小面积铣削对螺纹强度的影响。
【关键词】大规格内螺纹;螺纹铣削修复;螺纹挤压强度
1 引言
大型制造企业机械生产装置中,多数设备筒体端部采用埋头螺柱结构。这类装置基本属于重型设备,一般采用全寿期零部件,出现问题时,零件更换困难、代价大[1]。同时由于这类设备的特殊性与重要性,往往会设置较多的预防性维修项目或由于生产工艺的需要对其进行拆装,在对其维修和操作过程中,为了不妨碍生产、设备检修或改造工作,需要将埋头螺柱取出。倘若对筒体端部内螺纹孔保护不好,会造成内螺纹孔损坏或腐蚀,影响埋头螺柱的回装。
对于一般的缺陷,例如,起扣螺纹损伤、毛刺、双螺纹等,一般采用手工修复或丝锥修复往往即可达到继续使用的要求,但对于局部螺纹的坍塌、撕裂、弯曲变形等问题,需要使用类似扩孔攻丝、螺纹铣削、钢丝螺套等烦琐的手段进行修复处理。对比目前较为流行的几类修复方式,内螺纹铣削机能够较好地修复内螺纹局部缺陷,本文将对螺纹铣削机的具体工艺进行初步探讨和分析[2]。
2 实际螺纹铣削修复工艺模拟
本部分内容对内螺纹铣削修复工艺流程进行简单介绍。
2.1 准备工作
缺陷确认判断:首先使用内窥镜对内螺纹缺陷位置进行判断,确认属于局部缺陷,且需要对缺陷螺纹进行整体铣削,同时对该螺纹的其他螺纹段进行检查确认,保证存在一段完好的螺纹作为定心组件定位的位置。
定位孔确认:对缺陷螺纹孔两侧的内螺纹孔位置及状况进行检查,确认环境条件符合精度要求,避免因表面异物等原因影响定位精度。
2.2 定位
定位螺纹孔:将基板、压板、定位组件等零部件组装完成,固定定位装置,同时安装定位环筒组件。此步骤需要中心缺陷孔的定位精度,从根本上保证螺纹修复的精度,如图1所示。
定位缺陷位置:用测量尺测量定位待铣螺纹的深度并将测量数值锁定,通过内窥镜观察,确定待铣螺纹段的轴向起始和终止位置,在定位环筒上做好标记以确定铣削机的铣削范围。
2.3 安装走刀组件及内窥装置
本装置走刀组件使用偏心式,因此,初始位置需要将铣刀片通过偏心筒组件偏到最小位置;同时走刀组件内螺纹轴向位置进行粗定位,此步骤主要依靠上一步骤测量尺进行。调整完成安装走刀装置至缺陷螺纹孔,并安装内窥装置,同时使用内窥镜对铣刀和缺陷位置进行确认,做精定位调整,如图2所示。
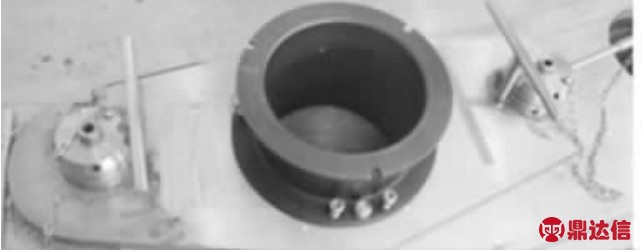
图1 定位装置
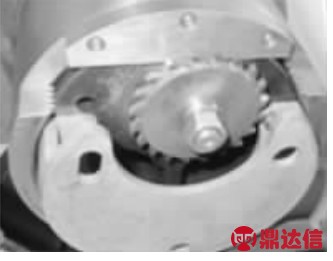
图2 偏心铣刀
2.4 缺陷铣削
铣削工艺动力采用气动方式,通过气压设置驱动气动马达实现,能很好地控制铣削过程中的力矩,在轴向进给方式中使用人工控制偏心装置进给,通过旋转标尺进行进给量的控制,整个过程使用内窥装置进行过程视频控制,如图3所示。
2.5 检测
铣削完成,首先使用内窥装置进行铣削效果检测,确认缺陷螺纹已经铣削完成,且无毛刺,过度平滑;随后拆除走刀组件及定位环筒,对缺陷螺纹孔进行整体清洁检查,最终使用通规进行检测,确认内螺纹的可用性,如图4所示。
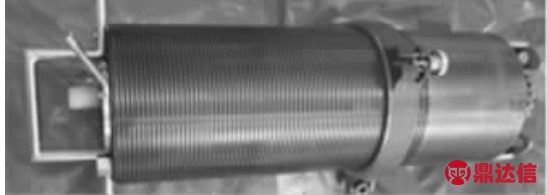
图3 铣削装置
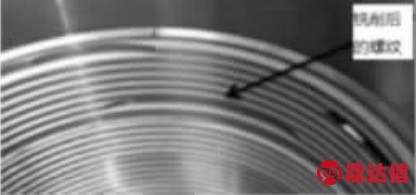
图4 铣削后的螺纹
3 力学计算及分析
工业上氨合成塔处于高温、高压、氢介质环境,外筒温度小于200℃,选材考虑机械强度、焊接性能和冷热加工性。筒体,内筒直接与介质接触,要求防腐蚀好、耐高压、耐高温、强度高、韧性好,可选用15MnVR。上端盖,需要具有耐氢腐蚀的性能材料,且应使平盖厚度尽量减小些,选用强度较好的20MnMoNb即可,上端法兰及下端的球形封头须锻造和冲压,要求强度好、耐腐蚀的材料,可选用18MnMoNbR。
在此,依据氨合成塔的筒体压力来评估,设计压力:24.6MPa,筒体内环直径:2 180.5mm,设计温度:300℃,设备质量:筒体140t;设备上盖29t,塔体主螺栓尺寸参数:M134mm×6mm×1044mm;数量:32个;材质:螺栓ASTMSA193GRADEB16、螺母SA194GRADEB16。为使条件更为苛刻,对于顶盖,采用平顶盖模拟计算[3],相应计算如表1所示。
表1 螺纹挤压强度计算
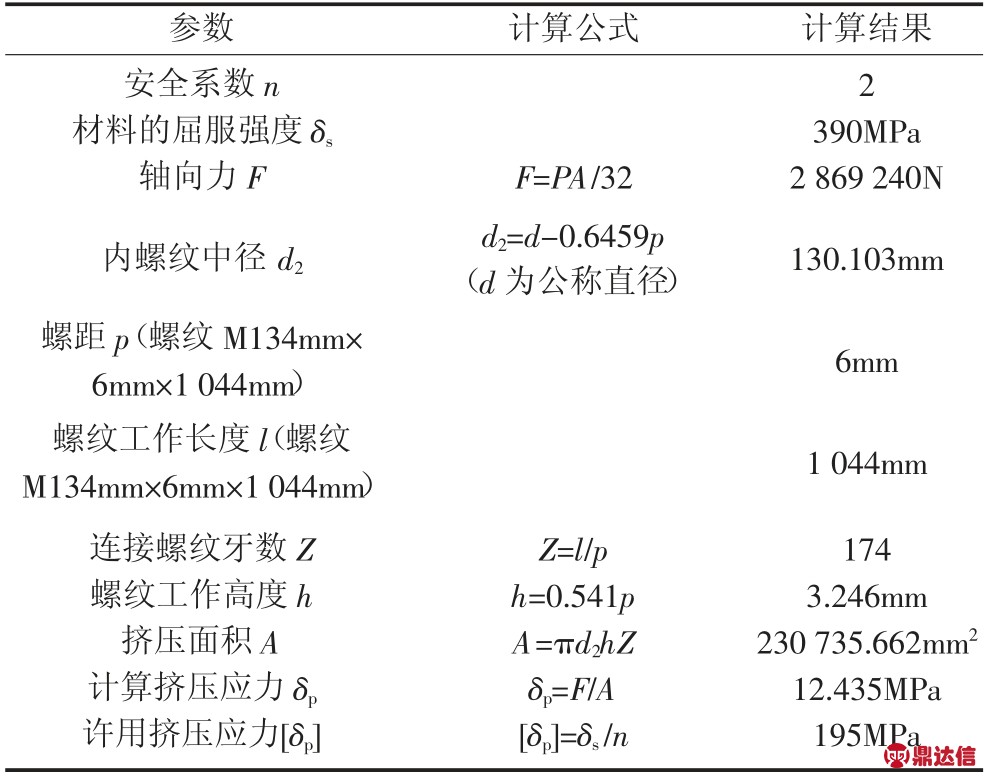
从以上抗挤压强度分析计算来看,完整的螺纹副的计算挤压应力远远小于许用挤压应力,当有螺纹牙损坏时,剩余螺纹牙数Z的极限值为:Z=174δp/195=11,即剩余11个螺纹牙时,那么实际挤压应力超过了许用挤压应力,螺纹将不可用。而在实际使用中,螺纹牙出现小面积损伤,通过铣削修复完全不会影响整个螺纹的使用[4]。
4 结论
针对内螺纹局部的坍塌、撕裂、弯曲变形缺陷,内螺纹铣削工艺能够快速便捷的完成相关修复工作,从时间、人力以及设备本身等各项成本中优势明显,对于原螺纹孔的功能、强度等方面影响微小,有良好的实用价值,但后续需要对可调式定位装置、偏心进给量以及内窥功能进行持续优化设计,以满足不同规格的内螺纹的工作状况。