摘要:为研究普通合金9Mn2V和钨基粉末硬质合金两种材料磨杆的动静态特性,对其性能进行评价,基于有限元仿真对两种材料磨杆进行了动静态性能研究,并与模态试验结果进行了对比分析;两种材料磨杆理论分析值与试验数据间的误差在8%以内,证明了所建立有限元模型很好的反映了实际结构以及仿真所得结论:钨基合金磨杆比9Mn2V磨杆具有更好的静刚度和动态性能,即钨基硬质合金能够显著提高磨杆性能的有效性。
关键词:磨削中心;模态试验;动静态特性
0 引言
精密数控内螺纹磨削技术是加工高精密滚珠丝杠螺母和转向器螺母的重要保证,在内螺纹磨削加工过程中,磨杆作为磨削工件的主要施力部位,承受很大的力和力矩,且其长径比较大,刚性不足,极易产生颤振,在这种情况下,不仅加工效率低下,砂轮损耗过大,而且加工出来的工件也会因表面粗糙度值过大,尺寸精度难以保证[1-2]。因此,磨削刀杆动静态性能的研究与提高则尤为重要。
近年来,国内学者一直致力于刀杆动静态性能的研究,并取得了很多成果。程宏伟等[3]人根据深孔镗削加工过程中产生振颤的机理,建立了减振镗杆的动力学模型,优化减振系统的参数,得到具有良好的减振性能的减振系统;范文冲等[4]人运用ANSYS软件对一种模拟刀杆的部分尺寸作了优化设计,使其在满足强度、刚度和固有频率的约束条件下,达到重量最轻;郭大庆等[5]人对基于PMAC-PC控制下的精密磨床,通过不同转速下电主轴振动信号的傅立叶谱,分析了磨杆对陶瓷轴承电主轴单元动态性能的影响;于英华等[6]人设计了泡沫铝复合结构内圆磨杆并对其静、动态性能进行有限元分析。
从刀杆的研究现状看出,提高刀杆动静态性能的方法主要分为两种,一种是给刀杆加外置的阻尼器或者采用复合材料,另一种就是采用硬质合金;刀杆的动静态性能研究主要集中在镗刀杆上,而对磨杆方面的研究相对较少,这主要是因为磨杆的尺寸一般较小且转速较高,导致磨杆的性能提高相对于镗刀杆要难一些。本文研究对象为精密内螺纹磨床用硬质合金磨杆,使用ANSYS有限元软件对两种不同合金材料磨杆进行动静态性能分析,并采用模态试验方法对磨杆进行了测试,所得结果与仿真数据进行了对比性研究。
1 磨杆有限元模型的建立
本文研究对象是某型号内螺纹磨削加工中心用磨杆,主要用来磨削滚珠丝杠螺母和转向器螺母等。分析的磨杆有两种:一种为厂家正在使用的磨杆,其材料为9Mn2V,这是一种综合力学性能比碳素工具钢好的低合金工具钢,具有较高的硬度和耐磨性,被广大磨床生产厂家广泛使用;另外一种为试验磨杆,其材料为钨基粉末合金,这种合金是由粉末冶金烧结而成,其成分是90%以上的钨和10%以下的软金属,密度大,硬度大于40HRC,通常其抗拉强度大于981MPa[7]。两种磨杆的实物如图1所示。
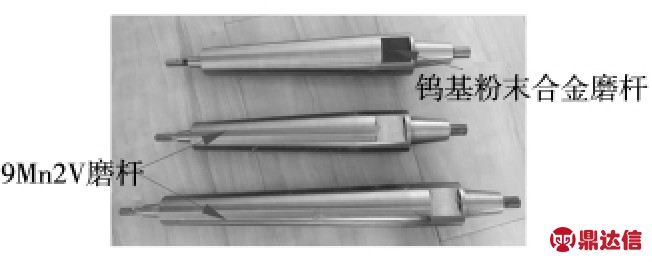
图1 磨杆实物图
将Solidworks建立好的三维模型导入ANSYS有限元软件前,在不改变模型特性的基础上,须简化磨杆的倒角、圆角以及螺纹等影响不大的因素[8],采用Solid45三维实体单元对磨杆进行6级精度,智能控制网格划分,设置磨杆的材料属性,如表1所示,得到磨杆的有限元网格模型如图2所示。
表1 磨杆材料属性
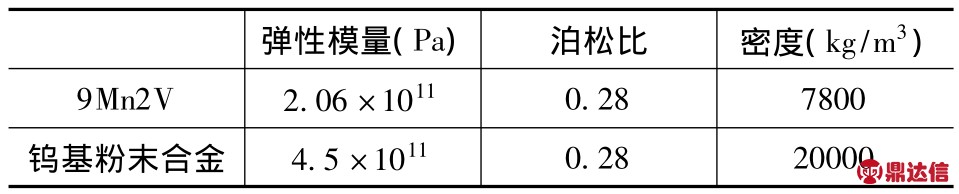
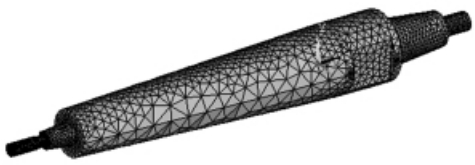
图2 磨杆有限元划分网格模型
2 磨杆动静态特性有限元分析
2.1 磨杆静力分析
螺母磨床磨削过程中,作用在螺母与内磨砂轮之间的力称为磨削力。它可分解为砂轮切线方向的切向力Ft,砂轮和螺母接触面法线方向的法向力Fn以及横向进给方向的轴向力Fa,磨杆磨削示意图如图3所示。磨杆的振动通常产生在径向和切向两个方向,径向力和切向力对径向位移影响较大,轴向力和切向力的扭矩对磨杆的径向位移影响均较小,,所以对磨杆静力分析时只考虑径向力和切向力对其弯曲程度的影响。由切向力估算公式:
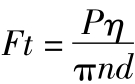
其中:P—电机的功率kW;
η—电机的传动效率;
n—砂轮的转速r/s;
d—砂轮的直径mm。
根据法向力与切向力 Fn/Ft之比 1.5 ~4[9],即可得到磨削力的法向力Fn。
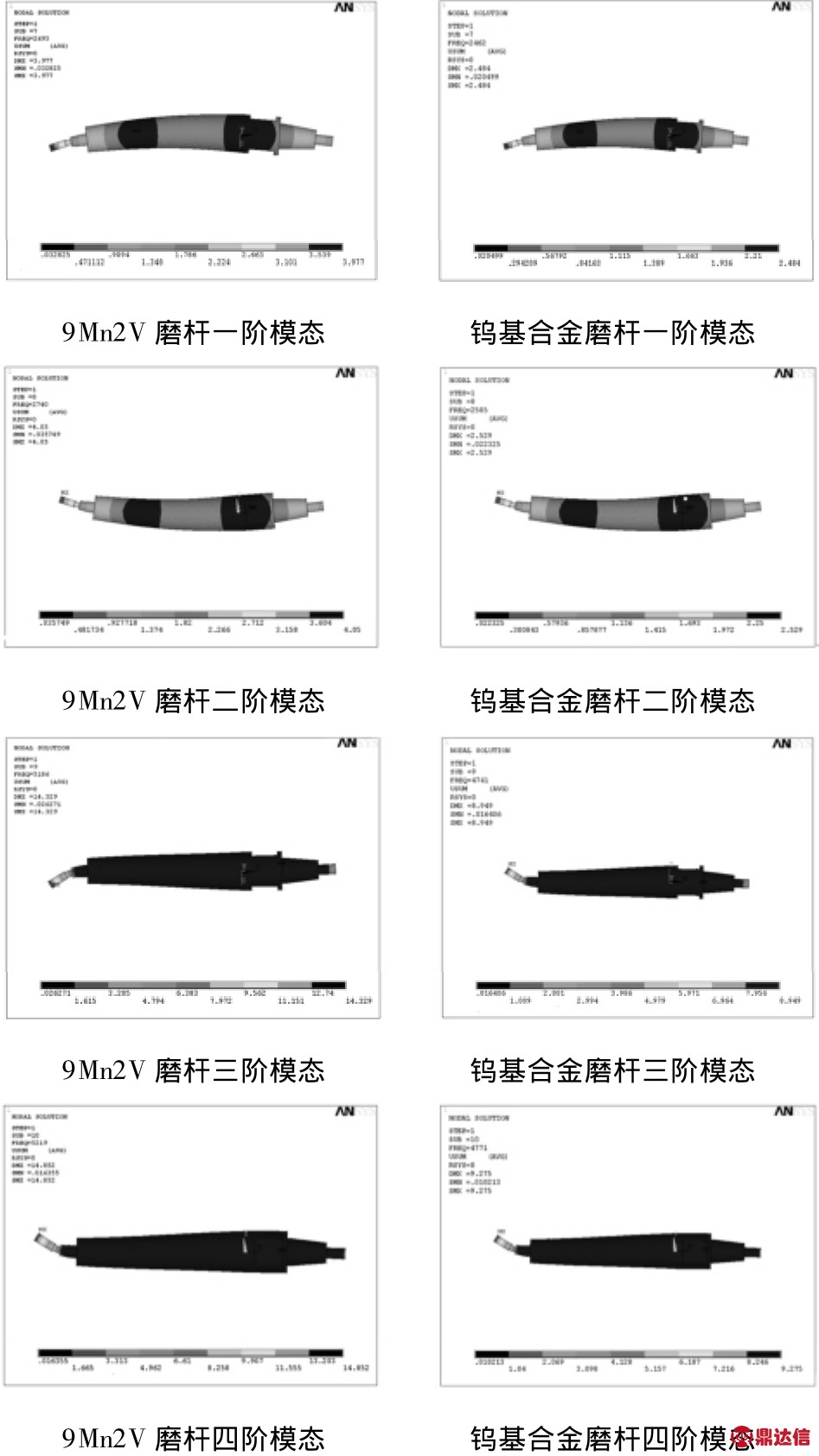
图3 磨杆磨削示意图
磨杆回转轴由交流伺服电机通过联轴节驱动高精度消隙蜗轮蜗杆副回转、角度编码器反馈元件位置实现闭环控制。电机额定功率Pe=1.7kW,转速n=3000r/min,即工作频率为50Hz,极对数p=3,根据经验公式得出Ft=270N,Fn=810N(取电机的传动效率 η 为1,Fn/Ft为3)。
装夹在磨床上的磨杆相当于一悬臂梁结构,一端固定,砂轮通过螺母紧固在磨杆另外一端,砂轮承受工件的反作用力,故静力分析时载荷类型为:
约束分析:限制除磨杆转动方向外的其余五个方向的自由度,与磨杆实际运行情况相吻合;
载荷施加:在磨杆有限元模型安装砂轮处中心节点2189的Z向施加270N的切向力,Y向施加810N的法向力。
磨杆静刚度分析结果如图4和图5所示。
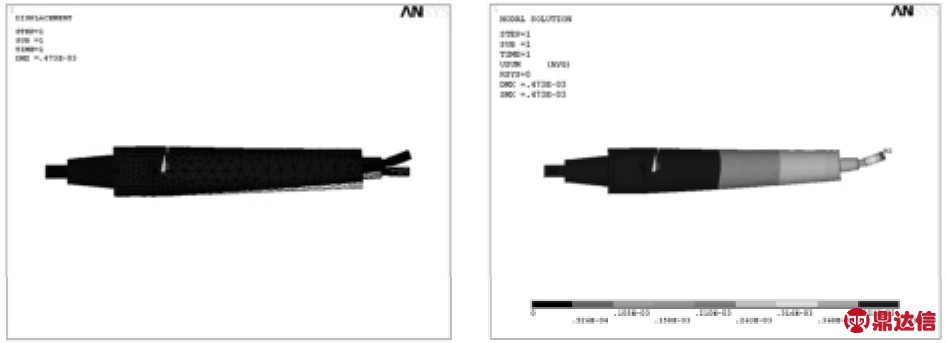
图4 9Mn2V磨杆静应变图
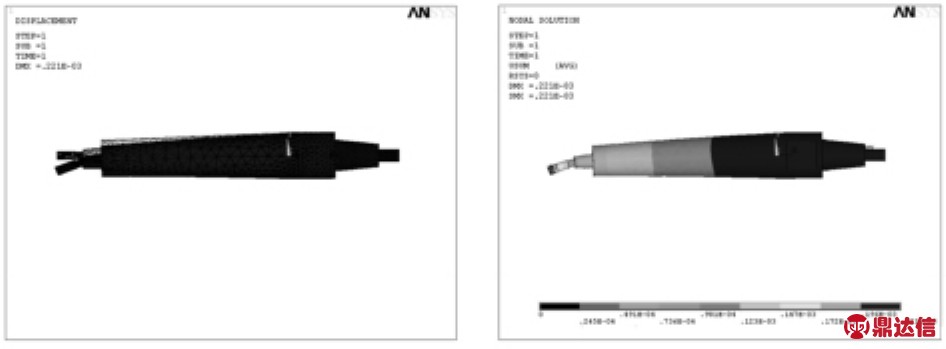
图5 钨基粉末合金磨杆静应变图
由图4可以看出整个9Mn2V磨杆的最大变形处是在外伸端砂轮安装部分,其最大变形量为0.473×10-3m;图5显示采用新型材料钨基粉末合金后磨杆的变形量为 0.221×10-3m,其变形量与原材料9Mn2V相比降低了53.3%,可见钨基粉末合金磨杆的静刚度比9Mn2V材料磨杆的静刚度要好,这主要是因为钨基粉末合金的弹性模量较高。
2.2 磨杆模态分析
采用Block Lanczos方法对自由状态下两种材料磨杆进行模态分析。提取的两种材料磨杆模型前四阶模态的固有频率及相应振型如表2和图6所示。
表2 磨杆模态分析结果
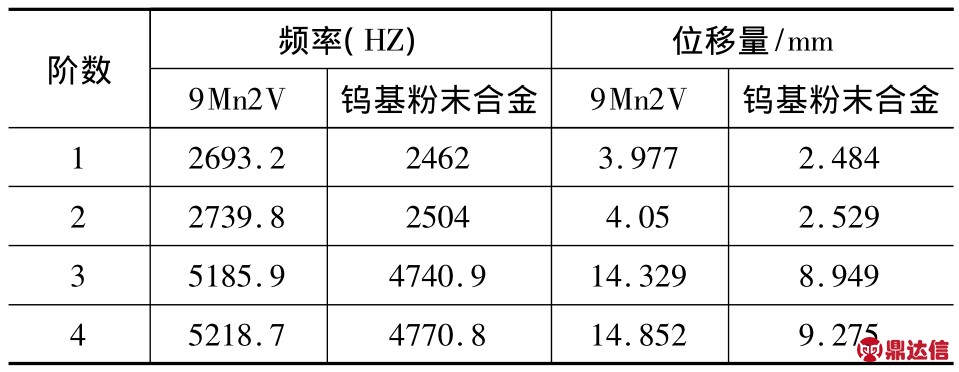
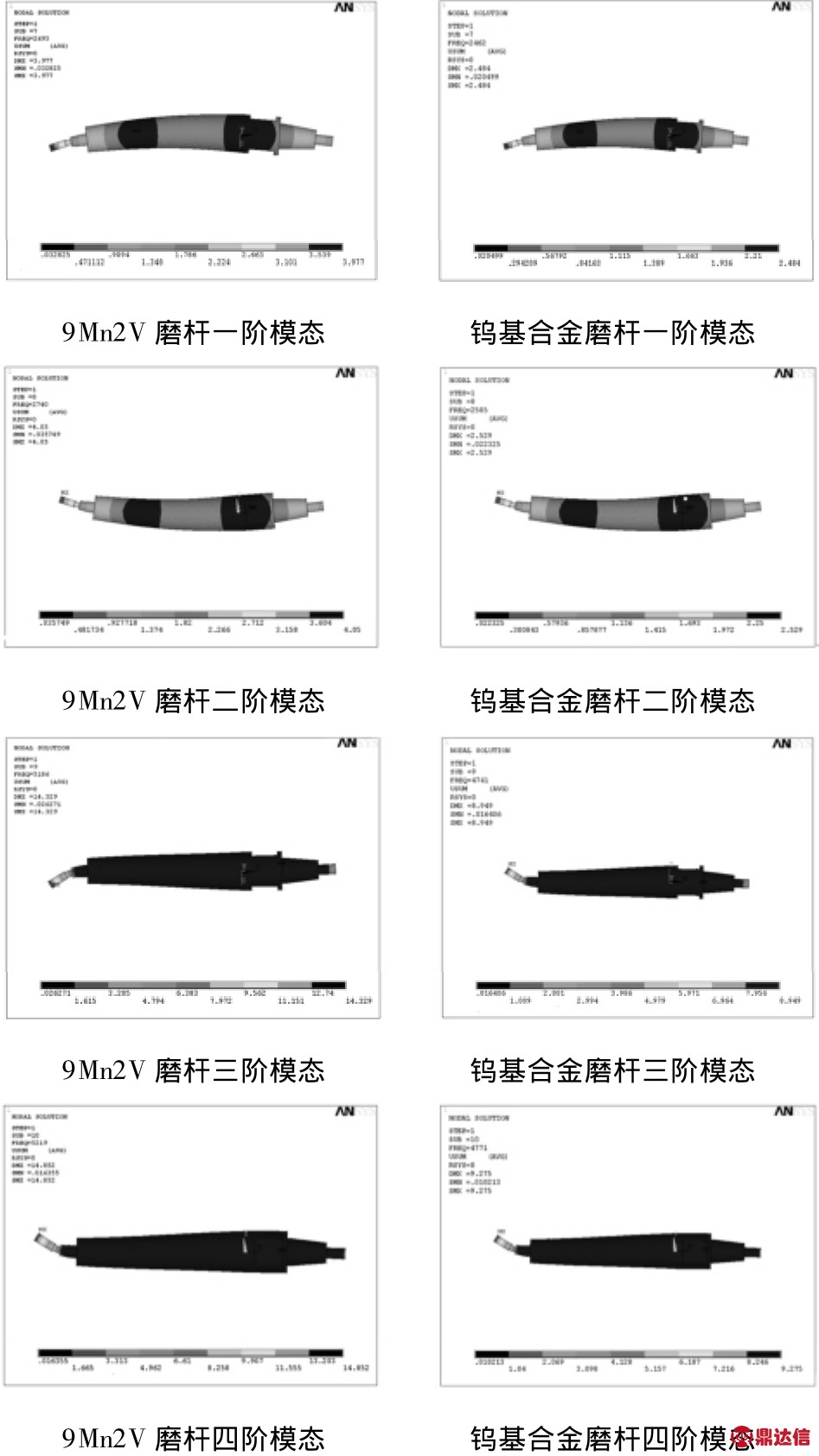
图6 磨杆前四阶模态阵型图
根据表2可以看出自由状态下,钨基粉末合金磨杆的前四阶固有频率均小于9Mn2V磨杆的前四阶固有频率,但钨基粉末合金磨杆的前四阶的最大相对位移量与9Mn2V磨杆的前四阶的最大相对位移量相比均降低了37.55%左右。从图6可以看出两种材料的磨杆一阶,二阶振型均表现为磨杆绕轴线一定角度的摆动,从三、四阶阵型图可以看出磨杆整体的摆动幅度并不大,主要表现为其端部安装砂轮处轴的摆动,主要是由于此处直径小,易产生振动所致。
综上所述,两种材料磨杆相比,9Mn2V磨杆具有更高的临界转速,更能远离共振点,但钨基粉末合金磨杆的最大变形量更小,具有更好的动态性能。对比表明两种材料磨杆各有优劣,在两种材料磨杆都能避开工作频率50Hz的前提下,应优先选择钨基粉末合金磨杆,该材料磨杆更能起到减振的效果,延长磨杆的使用寿命,降低生产成本和减少资源浪费。
3 磨杆模态试验
本试验采用自由支撑形式。自由支撑要求具有自由边界条件,这意味着试件与外界环境之间不存在任何连接,但是实际中是不可能达到完全自由的约束状态的,所以试验时,为了与自由边界条件近似,自由支撑时经常采用橡皮绳、弹簧或者气垫等将试件支撑起来[10],如图7所示。自由支承方式的悬挂点应该尽可能选在所分析的模态节点附近[11]。
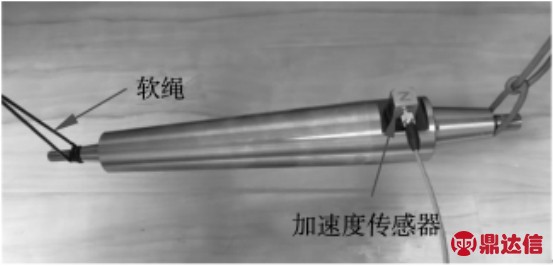
图7 磨杆自由支撑
3.1 测试系统组成
磨杆模态试验试验装置如图7和图8所示。试验仪器只要包括:数据采系统P8012及其配套的数据处理软件;脉冲锤和加速度传感器等。
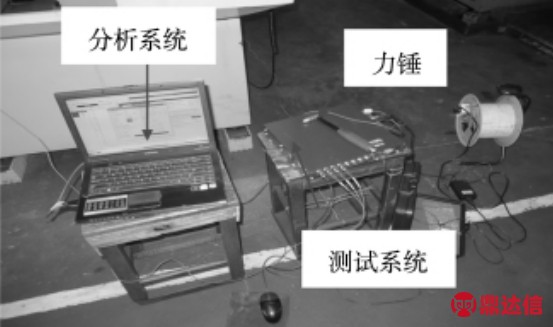
图8 磨杆模态试验试验装置
3.2 磨杆试验测点布置
磨杆结构较为简单,外表面为圆柱型。其振动通常产生在径向和切向两个方向,本文将单向加速度传感器粘贴于磨杆的径向进行单点拾振。在磨杆上均匀选取5个激振点,每个激振点敲击3次,求平均值。
3.3 试验结果分析
(1)两种材料磨杆自由状态下的试验结果如图9和图10所示。
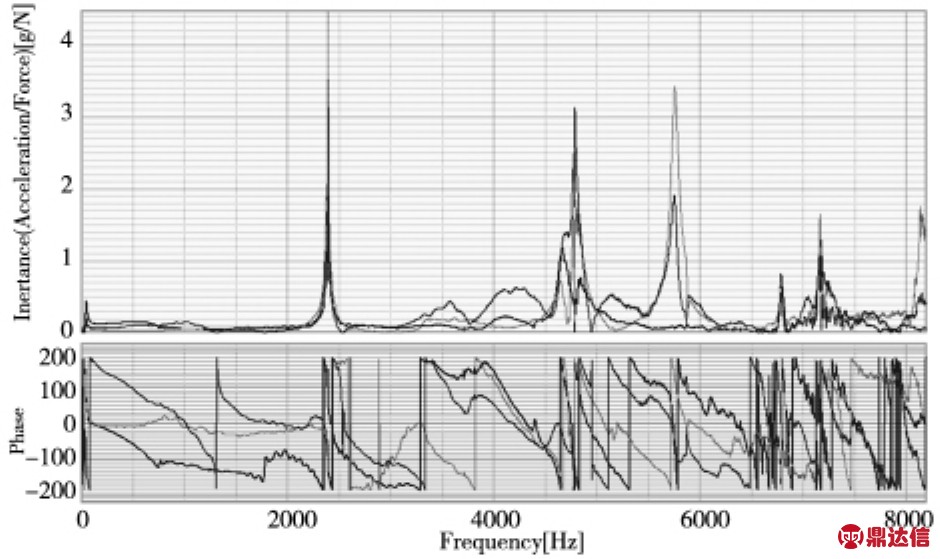
图9 9Mn2V磨杆频谱图
表3 9Mn2V磨杆前四阶固有频率对比(Hz)
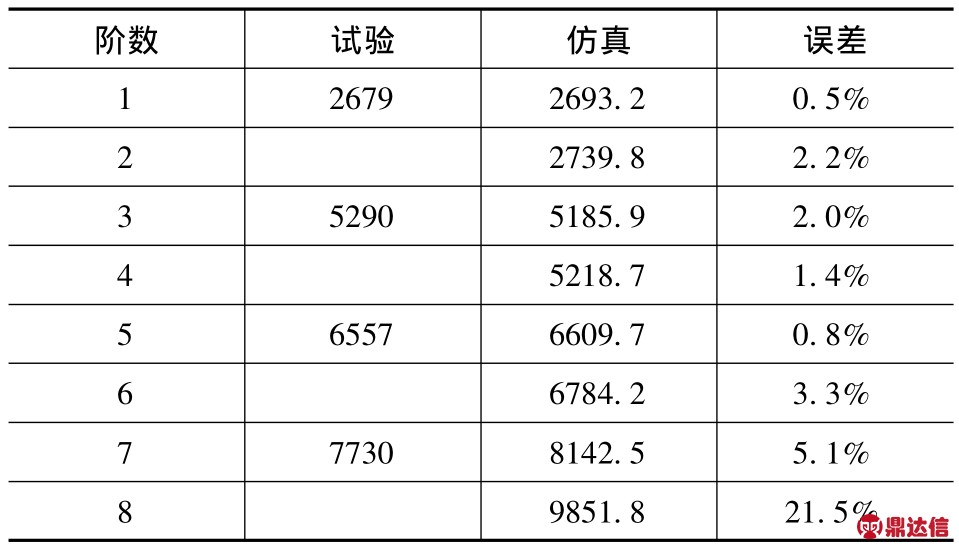
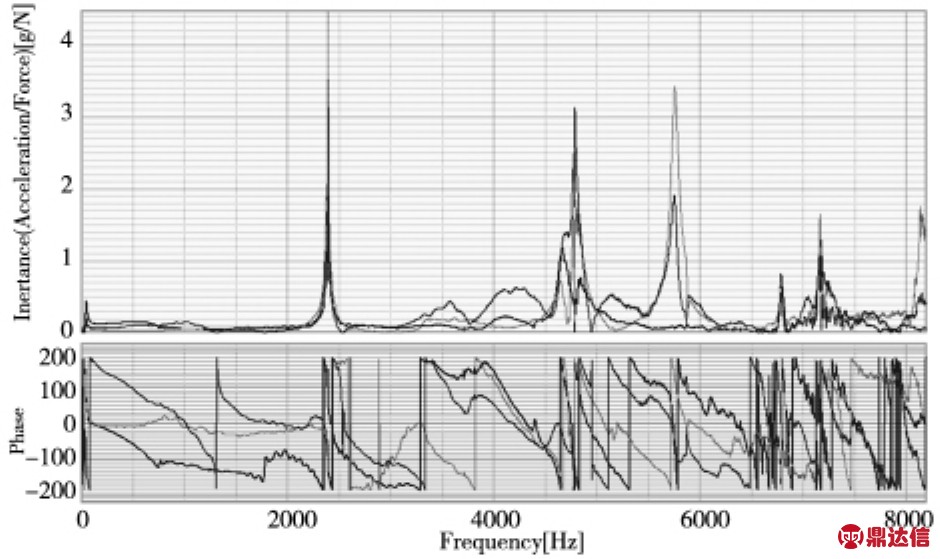
图10 钨基合金磨杆频谱图
表4 钨基合金磨杆前四阶固有频率对比(Hz)
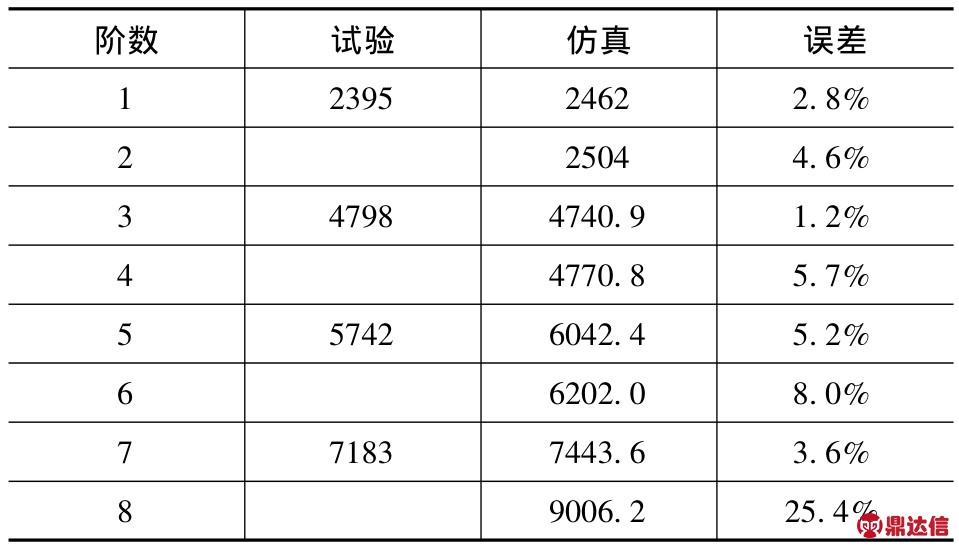
从表3和表4的仿真结果可以看出自由约束状态下,磨杆振型中相互正交的两阶固有频率值十分接近,原因是在无约束的自由状态下磨杆产生了重根,故每相邻两阶固有频率均对应磨杆模态试验的同一个相近的结果,根据磨杆仿真和试验结果可知:
①有限元仿真得出来的模态分析结果与试验测得数据误差很小,9Mn2V磨杆前六阶的误差均在5%以内,第七、八阶的误差稍大;钨基粉末合金磨杆前七阶的误差均小于8%,第八阶误差稍大,但两种材料磨杆前八阶的误差均在允许范围内。这说明两种材料磨杆仿真结果和试验结果是相吻合的,建立的磨杆有限元模型以及对模型的简化处理是合理的,有限元模型很好的反映了实际机械结构。
②由于有限元模型是对连续弹体-磨杆的离散化逼近,采用的是近似线性的材料特性和有限元模型,加之建模时采取的一些简化处理,所以仿真结果和试验结果存在一定的误差,且模态阶数越低,理论分析值与试验测定值越接近,误差越小;越往高阶部分两者分析结果相差越远,误差越大。
4 结束语
本文基于ANSYS有限元分析对9Mn2V和钨基粉末合金两种材料磨杆进行了动静态特性分析以及模态试验。并对两种磨杆进行了对比评价。
有限元静力分析表明钨基合金磨杆的变形量与9Mn2V相比降低了53.3%,钨基粉末合金磨杆具有更好的静刚度;磨杆在约束状态下和自由状态下的模态分析结果表明9Mn2V磨杆比钨基粉末合金磨杆具有更高的固有频率,即更高的临界转速,但其各阶的最大振动变形量均大于钨基粉末合金磨杆,钨基合金磨杆的动态性能更好一些。
磨杆自由状态下模态试验数据与有限元仿真结果相比误差很小,9Mn2V磨杆前六阶的误差均在5%以内,钨基粉末合金磨杆前七阶的误差均小于8%,两种材料磨杆仿真结果和试验结果相吻合,说明本文建立的磨杆有限元模型和对模型进行的简化是合理正确的,有限元模型很好的反映了实际机械结构,并验证了有限元分析结果的正确性。