摘要:文章介绍了“液压阀芯”组件中核心零件“阀芯内螺纹轴”的数控车削加工工艺分析与加工路线设计,刀具选择、数控车削程序编制。实际加工及零件检测结果证明,工艺路线方案切实可行,加工程序运行正确,零件质量得到保证。
关键词:阀芯内螺纹轴 数控车削加工 工艺 编程
1 工艺分析与工艺设计
1.1 零件图分析
阀芯内螺纹轴为典型的带有内螺纹孔及外成型面的轴类零件,结构形状较复杂、精度要求高,适合在数控车床上加工。
零件加工的难点在于槽底尺寸为Φ24±0.05的凹槽型面及两侧,以及M27Χ1.5-6G内螺纹的加工。轮廓表面要通过粗车和精车,逐步达到精度要求。特别是凹槽两侧30°斜面、R3及R7圆弧的加工,要注意刀具与工件间的干涉,选择副偏角大的尖形外圆车刀分层车削,从左右两个方向或者需要调头装夹加工,才能逐步达到要求。所以加工过程中零件需要调头安装,或者一次装夹但要分别使用左、右偏刀加工凹槽左侧及右侧形面。
1.2 零件装夹定位分析
第一种方案:用三爪自定心卡盘辅以顶尖,两次装夹。
为避免使用右偏车刀的不便,采用分两次装夹,先夹住零件毛坯左端外圆,依次粗车右端Φ44-0.025圆柱表面至Φ44.5*55及外凹形槽槽底Φ24及两侧面去除余量 (留精车余量0.5-1mm);钻孔Φ20,内孔车刀镗底孔及内切槽刀加工4*Φ32螺纹退刀槽,螺纹车刀车内螺纹M24Χ1.5-6G,再用35°V 型刀片车刀加工Φ24±0.05及左侧的R3和30°锥面 (见图2所示) ;切断零件后调头包铜皮夹住Φ44-0.025外圆表面找正后夹紧(采用一夹一顶),依次车削出左端倒角、Φ 48-0.03外圆,以及中间Φ24±0.05mm凹槽右半部分及R3圆角、R7凸圆弧面、Φ44-0.025圆柱表面。
第二种方案:用三爪自定心卡盘辅以顶尖,一次装夹。
该方案和方案一不同之处是对于零件中间凹槽的加工,分别使用左、右偏刀在同一次安装中先后加工出凹槽的槽底及左侧(R3圆弧、30°斜面)、槽底及凹槽的右侧(R3、R7圆弧)。
另外,也可采用先以切槽刀切除凹槽大部分的余量,但要在槽底及左右两侧留精加工的余量;再用左(右)偏尖形车刀加工出凹槽最终形状及尺寸。其特点是用外圆切槽复合循环(G75)指令编程,加工效率较高。
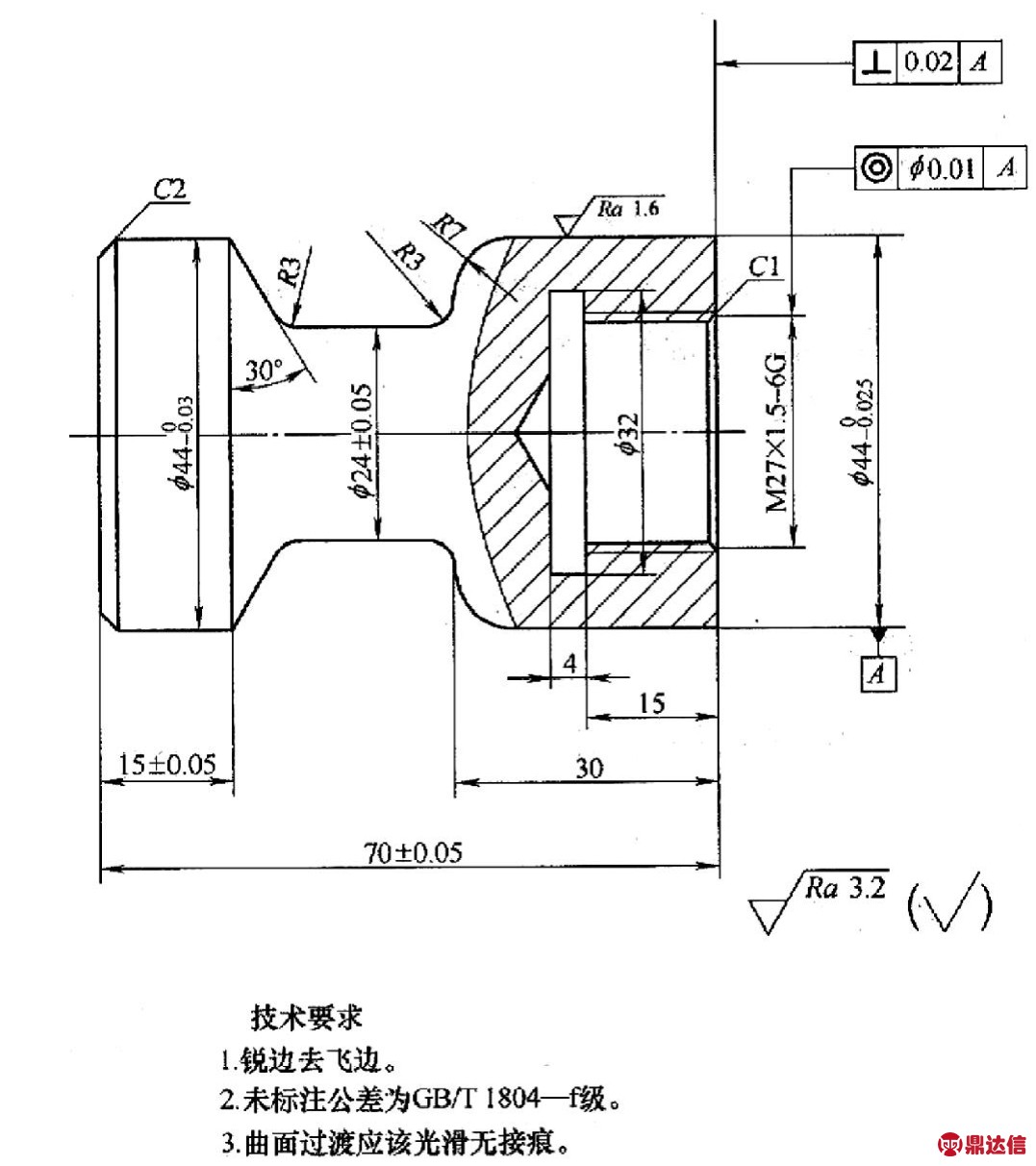
图1 阀芯内螺纹轴
1.3 工艺路线设计
方案一:
(1)如图1示,夹工件毛坯左端外圆;1)用内孔车刀加工出M27x1.5-6G内螺纹底孔,包括孔口倒角C2;换内切槽刀切螺纹退刀槽4xΦ32;粗、精车内螺纹直至与阀芯螺纹轴良好旋合;2)右端用顶尖定位,用35°尖形车刀加工出凹槽底部及左侧,包括Φ25.5、R3圆角及30°角度斜面;注:凹槽中间可以先用切槽刀加工出宽18、深10的槽,见方案三。3)换93°外圆车刀加工右端Φ44外圆表面;4)切断,留1mm余量(长度71mm);
如图3示采用“一夹一顶”安装。
方案二:
熵值法是指用来判断某个指标的离散程度的数学方法。离散程度越大,该指标对综合评价的影响越大。设决策矩阵为表示第j个指标的第i个方案的指标值。计算步骤如下:
(1)用35°左偏尖形车刀加工出凹槽槽底及左侧;
(2)换35°右偏尖形车刀,加工出凹槽槽底及右侧;
(3)移出顶尖,垫铜皮夹Φ44外圆表面,分别加工出内螺纹底孔、螺纹退刀槽、M27x1.5螺纹;
(4)用93°外圆车刀车两端Φ44外圆表面;
(5)加工左端C2倒角,切断;
(6)零件调头,车断面,保证总长。
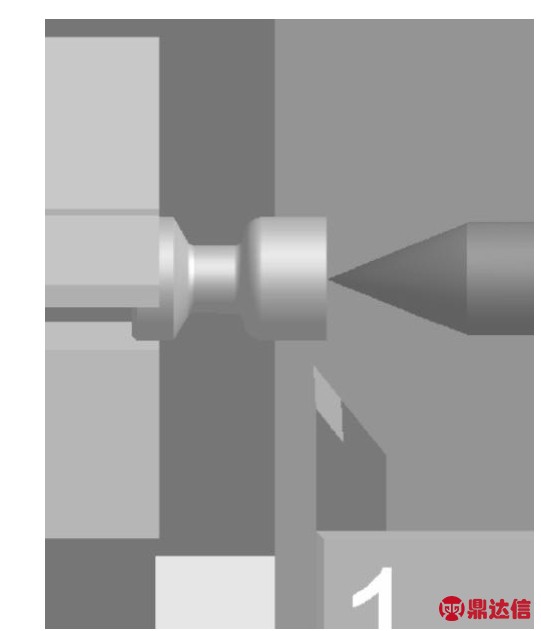
图2
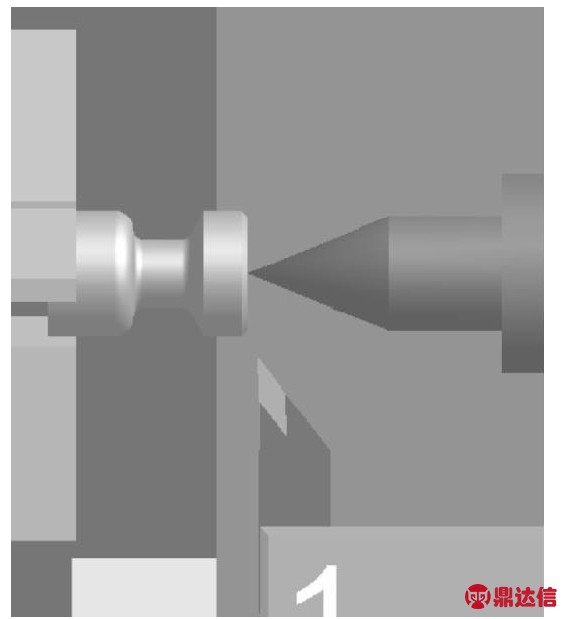
图3
方案三:
同方案一和方案二不同之处是对于零件中间凹槽的加工,方案三采用先以切槽刀切除凹槽大部分的余量,再用左(右)偏尖形车刀加工出凹槽最终形状及尺寸。其特点是用外圆切槽复合循环(G75)指令编程,加工效率较高。
2 加工程序的编制
分两次安装的加工程序如下;
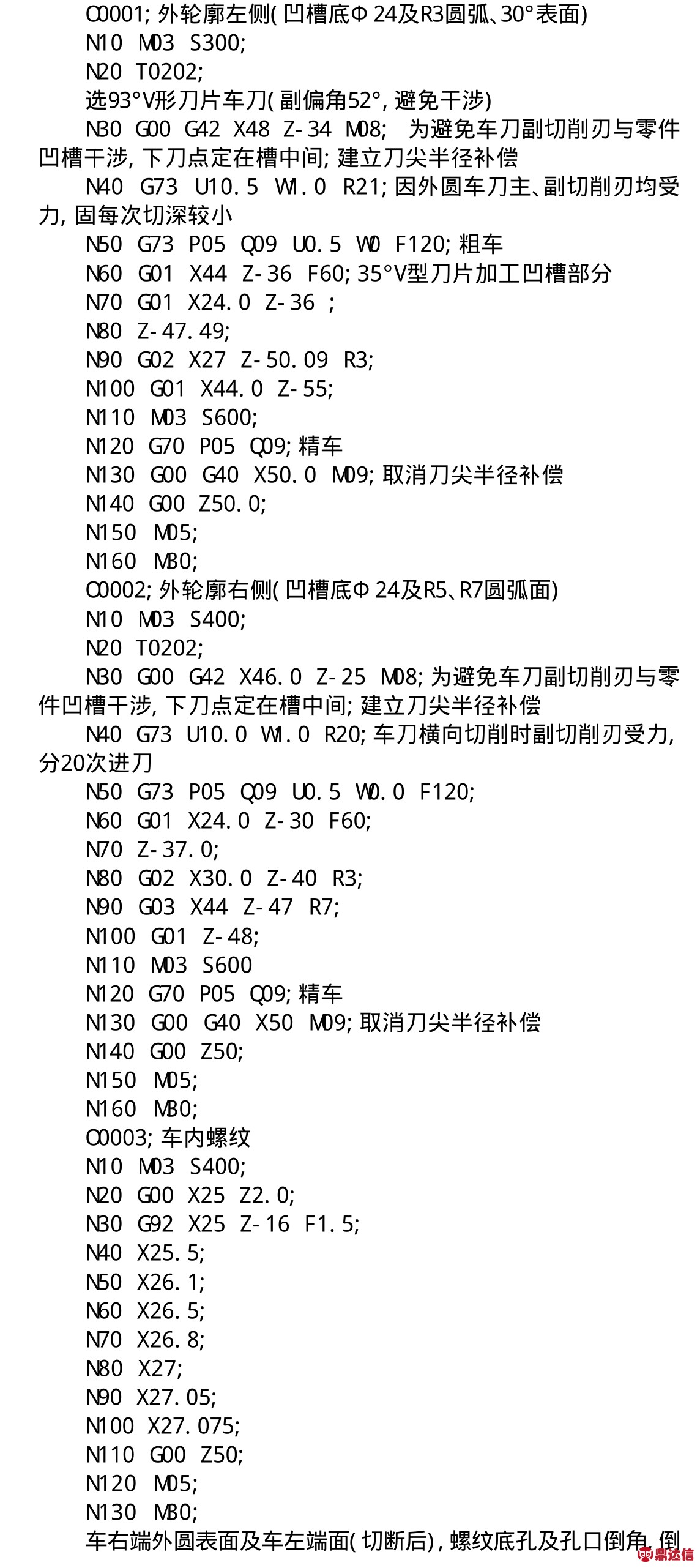
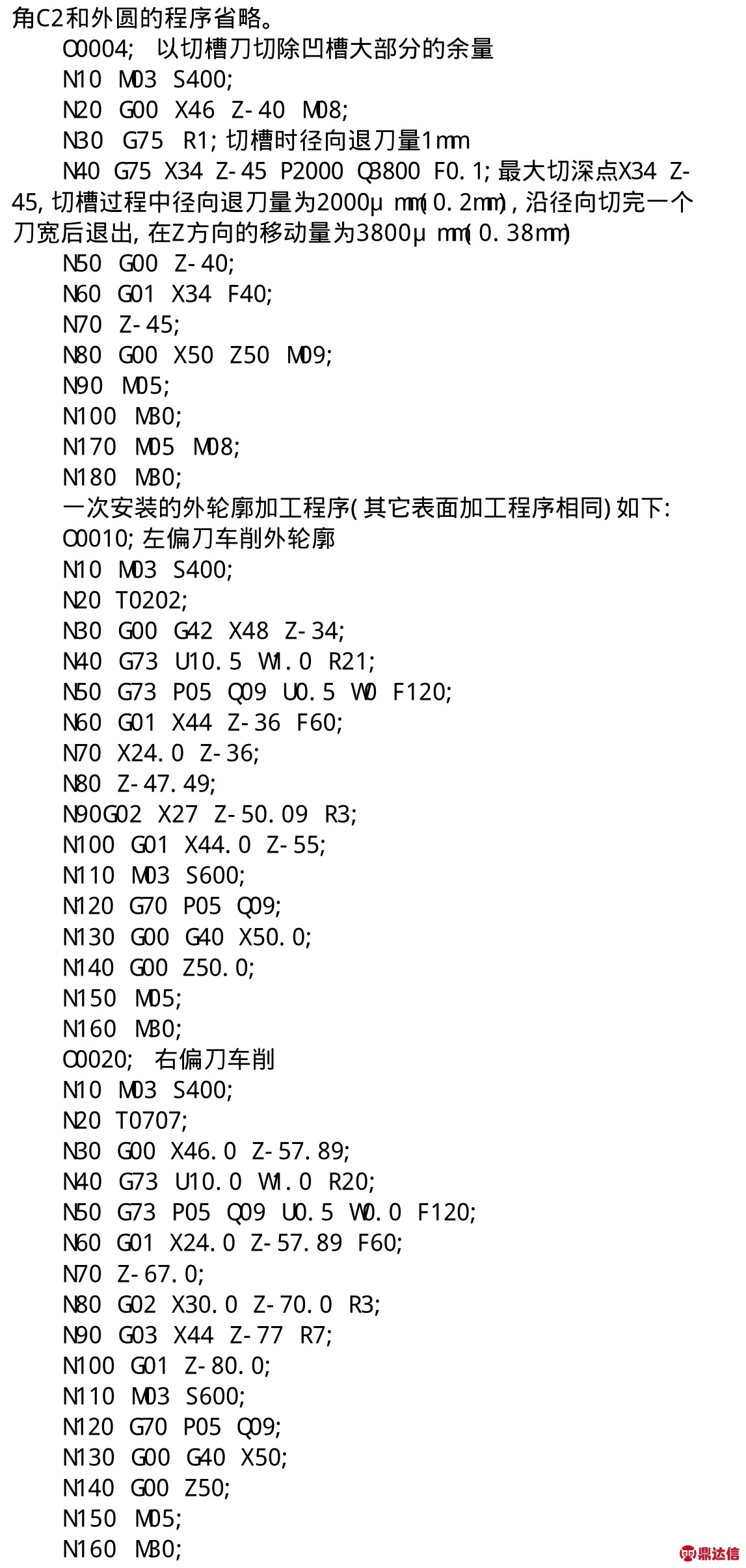
车螺纹底孔及孔口倒角、车内螺纹、车右端外圆表面,以及零件调头用93°外圆车刀加工右端面保证总长,倒角C2及Φ44外圆表面的程序,同前面“分两次安装”。