摘要:为深入研究梯形螺纹振动辅助冷挤压机床的加工过程,延长挤压丝锥寿命以及提高梯形内螺纹质量,本文建立了一套基于虚拟仪器的专用在线监测系统。研究了不同挤压工艺参数下加工过程中的振动、声发射、扭矩以及温度信号,并通过对信号的分析处理,揭示了不同工艺参数与加工过程信号之间的内在联系。研究结果表明,随着主轴转速和润滑油黏度系数的提高,振动、声发射信号的均方根值不断提高,振动、声发射信号频率由低频向高频移动,扭矩和温度也不断提高。激振频率的最优值在18 Hz左右。
关键词:梯形螺纹;振动冷挤压;监测系统;挤压参数
螺纹连接类零件作为最重要的连接和结构件之一,已经广泛应用于重载、高速等条件下的船舶制造、航空航天等工业领域中[1-5]。目前,振动辅助冷挤压加工成形的梯形螺纹具有更高的表面硬度和强度、更高的螺纹表面质量、更低的生产成本以及更高的生产效率,由此保证了重要结构螺纹连接件的机械性能及其疲劳寿命[6-8]。
梯形螺纹振动辅助冷挤压专用机床的核心激振装置是一种基于扭矩平衡状态下的新型机械式激振装置。该激振装置将振动引入梯形螺纹的冷挤压过程中,这种加工方式解决了传统冷挤压加工中的一系列问题,如:挤压扭矩过大、挤压区温度较高、挤压丝锥易断裂、挤压螺纹质量较差和工件使用寿命过短。
本文通过分析加工过程中采集到的多传感器信号,探究主轴转速、激振频率以及润滑油这3个加工工艺参数对信号的影响规律,从一个侧面揭示了振动辅助冷挤压的机理,为加工参数优化以及机床的性能改进提供试验依据。
1 试验材料与方法
梯形螺纹冷挤压工艺试验在南京航空航天大学机电学院研制的振动辅助冷挤压专用机床上进行,机床见图1。该机床在低频振动的辅助下,使用专用的梯形挤压丝锥对预制好底孔的工件进行一次挤压成形加工。
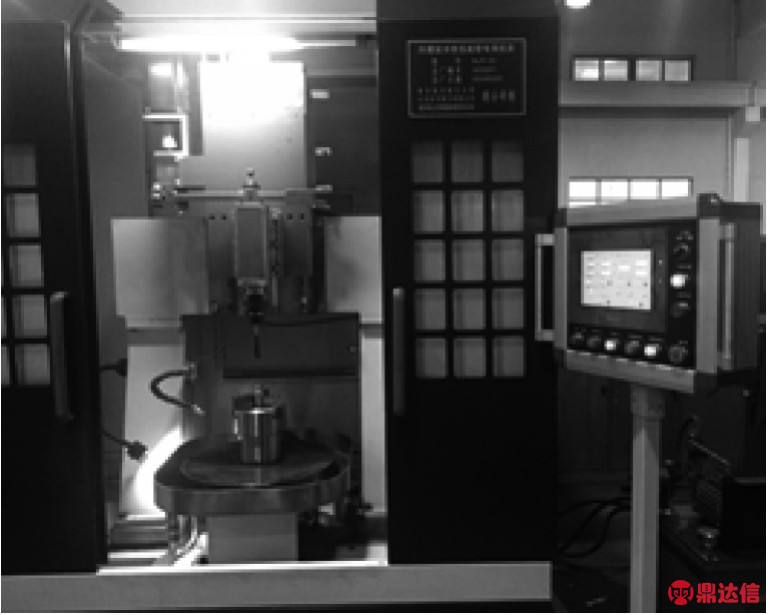
图1 振动辅助冷挤压机床
Fig.1 Vibration-assisted cold extrusion machine
刀具采用圆锥式棱齿结构的Tr14×2×170梯形挤压丝锥,丝锥材料为HSS高速钢,表面进行氮化铝钛处理,挤压丝锥见图2。

图2 梯形挤压丝锥
Fig.2 Trapezoidal extrusion tap
它是一种梯形内螺纹用外径及齿形渐进式挤压丝锥,这种结构可以有效减小挤压过程中的扭矩,避免丝锥折断,同时可以提高工件的加工精度与加工效率。
试验材料采用316L不锈钢,取该材料进行室温25℃下的拉伸试验,得该材料的抗拉强度为663.36 MPa,屈服强度为352.97 MPa,伸长率为48.16%。工件实物及梯形螺纹局部细节见图3。
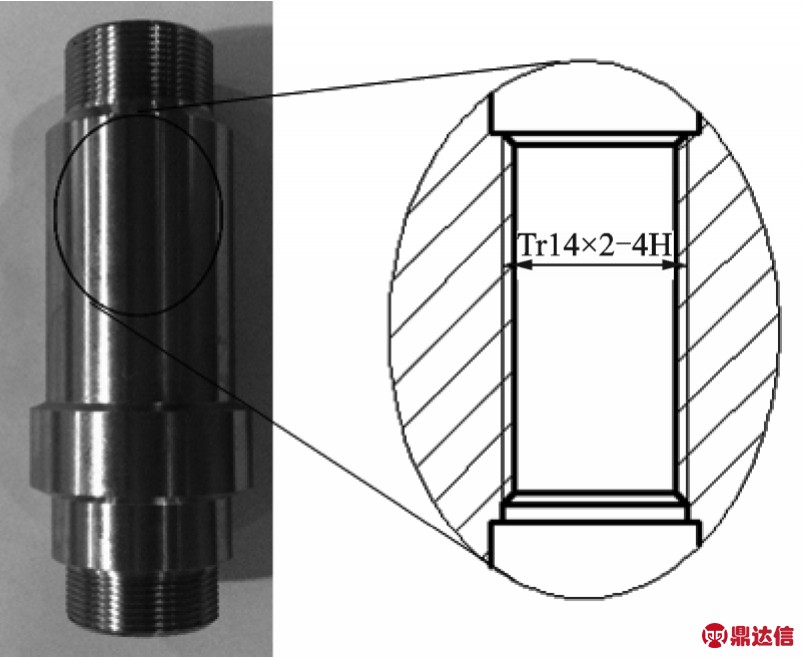
图3 工件实物图
Fig.3 Workpiece physical map
润滑油在梯形螺纹振动辅助冷挤压加工过程中,通过喷嘴用油泵直接加压喷射到挤压丝锥与工件的接触位置,主要起润滑、辅助冷却的作用。本试验采用10#,20#,30#机油和聚二甲基硅氧烷润滑油(Polydimethylsiloxane,PDMS),其黏度系数见表1。
表1 润滑油40℃时的运动黏度
Tab.1 Kinematic viscosity of lubricating oil at 40℃mm2/s
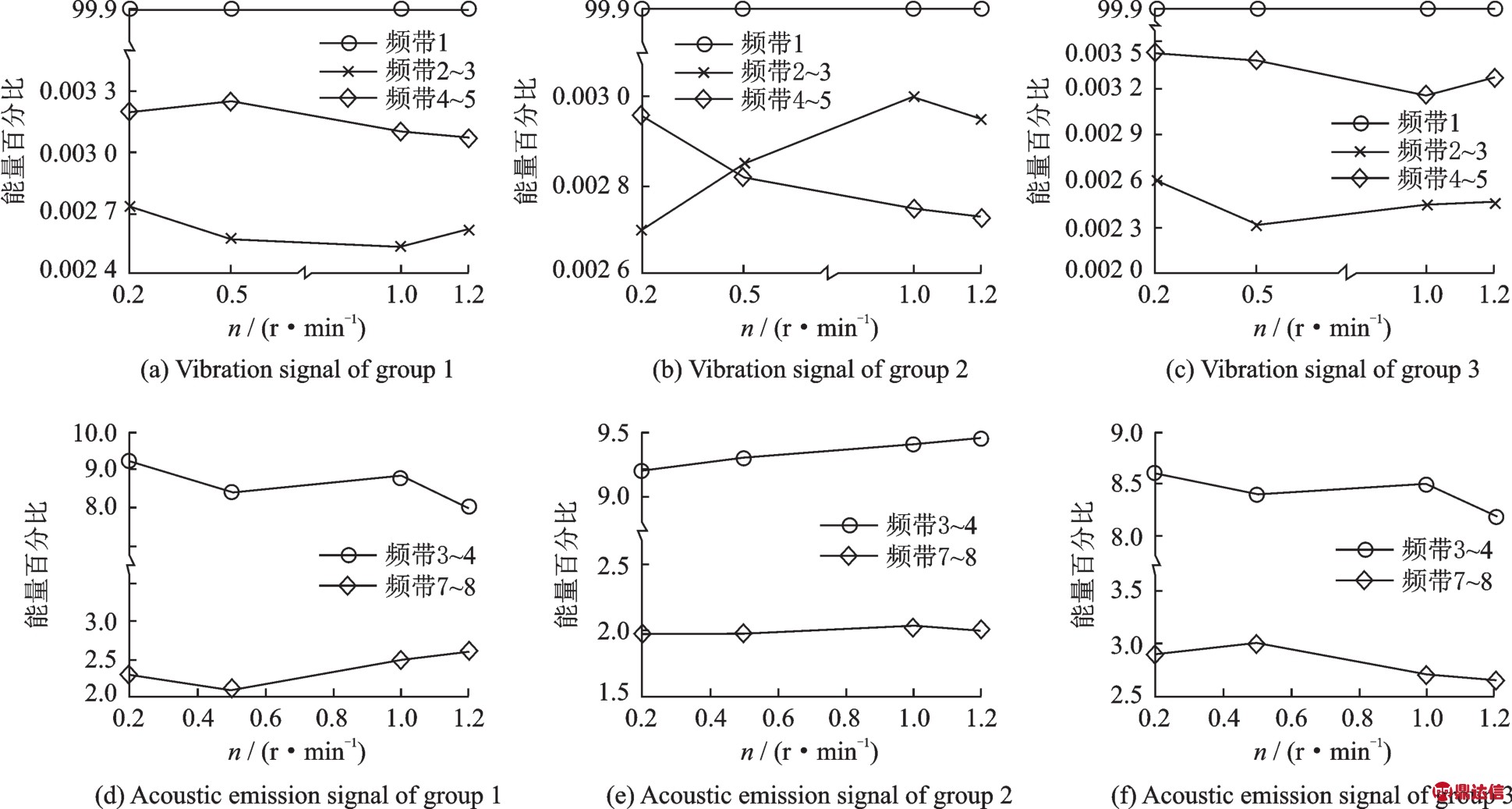
为了探究不同工艺参数对信号的影响,采用单因素法进行试验设计。试验设计见表2,其中:n为主轴转速,f为激振频率,L为润滑液类型。试验分为4组,每组4个试验,共可获得16组数据。
表2 试验参数
Tab.2 Test parameters
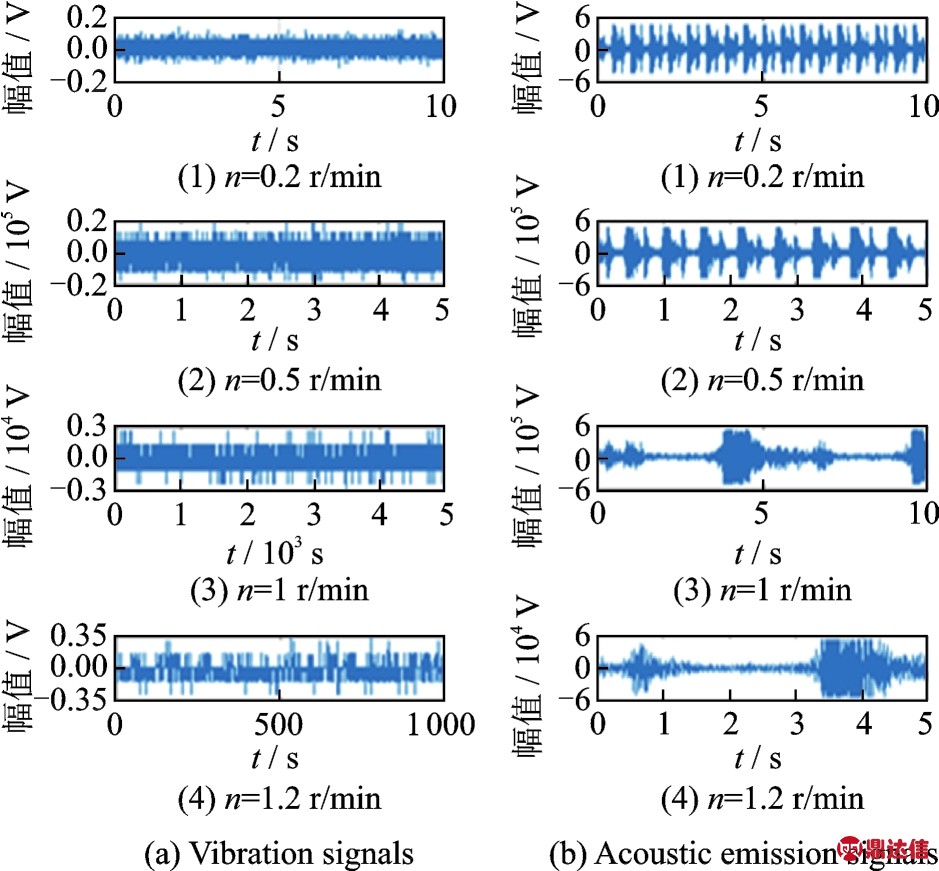
2 在线监测系统
图4为该机床的在线监测系统工作流程图,它是一个以在线分析和工艺试验研究为目标,以提供具有实时性、准确性和多样性的加工过程信息为核心任务,运用多传感器信号采集技术、计算机技术并配以LabVIEW和MATLAB专业软件,组成的一个从信号采集、预处理、特征分析到数据处理及存贮的完整系统,从而实现了对梯形螺纹加工过程的在线监测[9]。
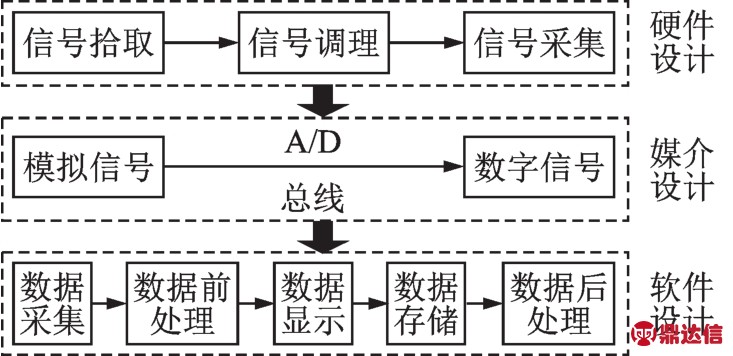
图4 在线监测系统工作流程图
Fig.4 online monitoring system workflow
在线监测系统工作过程实物如图5所示,由电阻应变式扭矩传感器、红外式温度、压电式加速度传感器以及声发射传感器将加工过程中的扭矩、温度、振动和声音等物理参数转化为模拟电压信号,再通过前置放大器进行放大滤波,经过数据采集卡、二次仪表转化为数字信号,然后输入到计算机利用LabVIEW软件进行数据的显示、处理及存储。
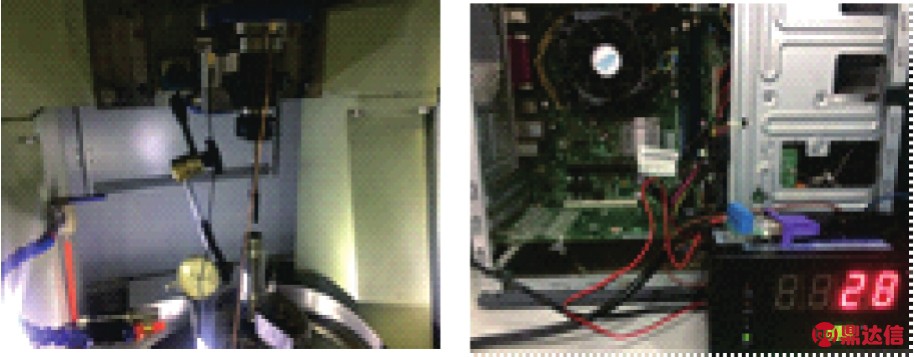
图5 在线监测系统工作实物图
Fig.5 online monitoring system work physical map
3 试验结果与分析讨论
3.1 振动、声发射信号的时域特征分析
第1组试验的振动和声发射信号的时域波形见图6。由图6可以看出,(1)振动、声发射信号具有周期性,这是由于在周期性扭转振动辅助的作用下,刀具的挤压作用也是往复的,这就造成振动的冲击具有了周期性。(2)在丝锥脱离工件时,声发射信号的幅值较低。由此可知,冷挤压过程产生的声发射信号主要由断续挤压过程中丝锥挤压工件材料变形造成。(3)在激振频率和润滑液类型一定的情况下,随着主轴转速的提高,振动、声发射信号的振幅也随之升高。
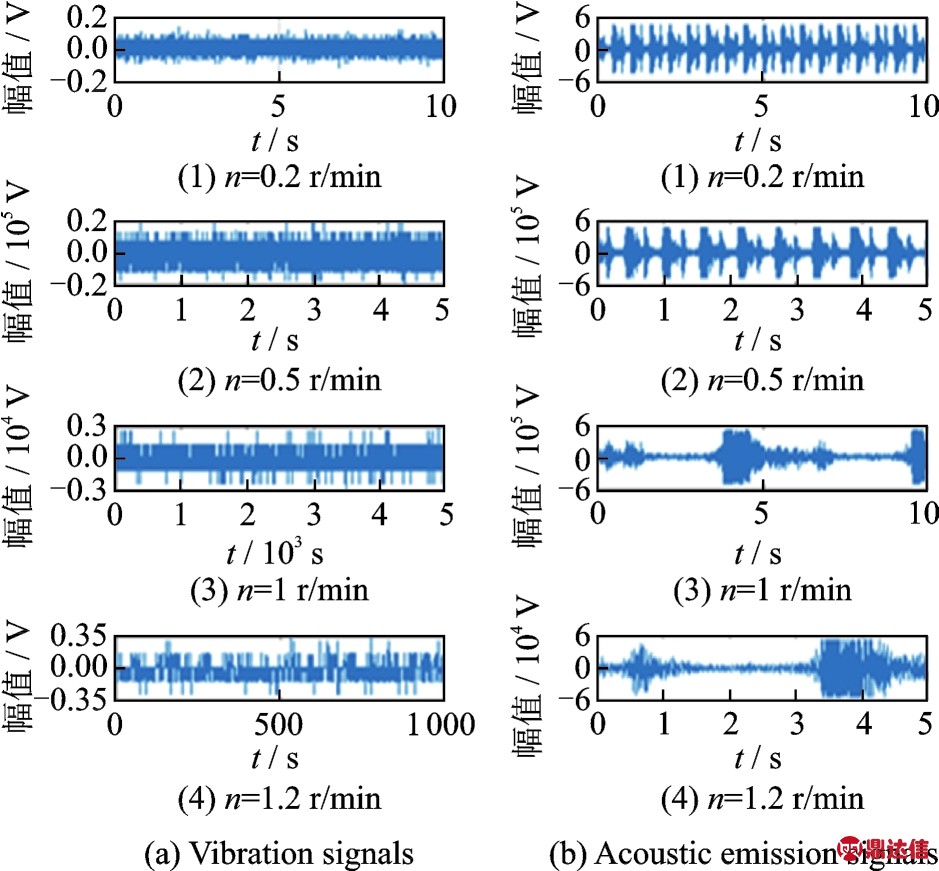
图6 振动、声发射信号的时域波形图
Fig.6 Time-domain waveform of vibration and acoustic emission signal
均方根值是表征信号强度的一种有效参数,因此在对振动、声发射信号的时域研究中,将其作为信号的时域特征进行计算和分析[10]。图7是4组试验的振动、声发射信号的均方根值。由图7可知,(1)随着主轴转速的提高,振动、声发射信号的均方根都呈增大趋势。究其原因主要是:一方面,当主轴转速提高,而激振频率不变,那么每次切入、切出的时间变短,就意味着挤压丝锥对工件的冲击强度变大,工件材料的变形速率增大。另一方面,挤压区温度随着主轴转速的提高而升高,致使润滑油黏度变小,不易在挤压丝锥与工件接触面形成适当的油膜,使得两者的摩擦加剧。(2)随着激振频率的提高,振动、声发射信号的均方根都呈增大趋势。究其原因是:(1)当激振频率提高,而主轴转速不变时,意味着单位时间内切入切出的次数增加,使得信号中的动态成分变大。(2)挤压丝锥每一次切入切出的时间变短,使得润滑油不能充分地流入挤压丝锥与工件的接触面,导致挤压区不能始终处于边界摩擦状态,其结果是两者的摩擦加剧。
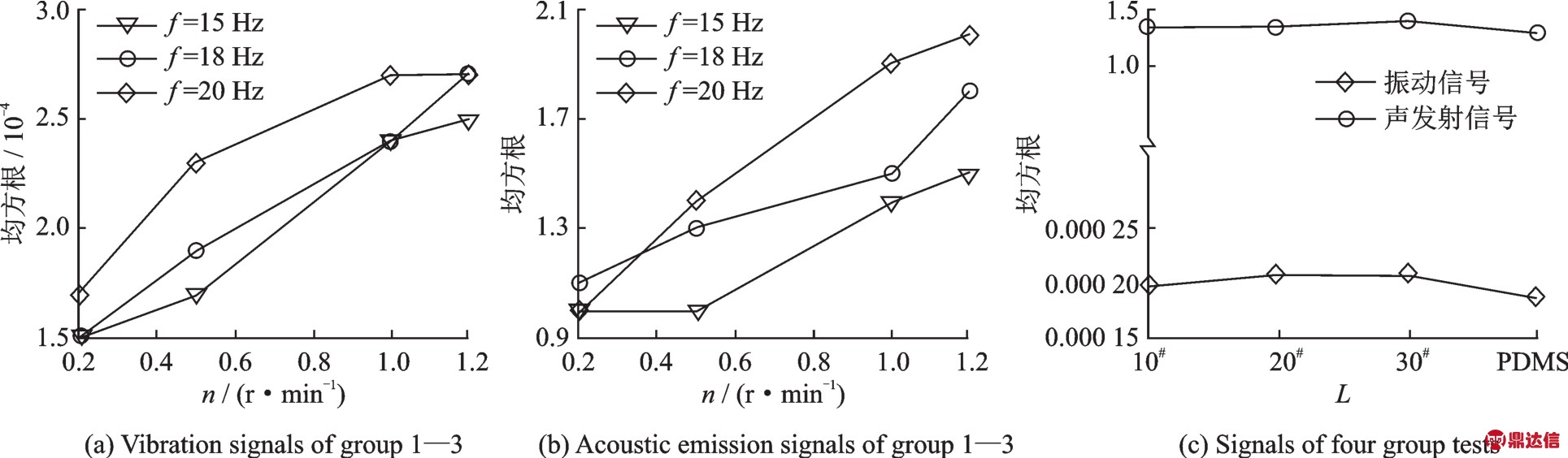
图7 4组试验振动、声发射信号的均方根值
Fig.7 RMS value of vibration and acoustic emission signal of four group tests
(3)主轴转速和激振频率不变时,随着润滑油黏度系数的提高,振动、声发射信号的均方根都有较为微弱的增大趋势。究其原因主要是:(1)当挤压温度较低时,黏度系数越高的润滑油,在挤压丝锥与工件间形成的油膜越厚。厚油膜在压力作用下,不利于挤压丝锥对工件的充分挤压,使工件表面容易咬焊、粘着,使得两者的摩擦加剧,而流体薄油膜润滑有助于降低摩擦阻力。(2)当挤压温度较高时,致使润滑油变薄,不同黏度系数的润滑油的挤压过程都处于边界摩擦状态,这就使得在温度较高时,信号的均方根基本没有差别。此外,在梯形螺纹的挤压过程中,高温度比低温度的持续时间长,信号均方根值随黏度系数的提高而升高,但是影响较为微弱。
通过上述讨论可知,工艺参数对振动、声发射信号的均方根值的影响基本相同。主轴转速和激振频率对其影响较大,而润滑油类型对其影响相对较小。总的来说,两者信号的均方根值与挤压丝锥的切入切出次数、每次切入切出的时间以及丝锥与工件间的摩擦状态有关。
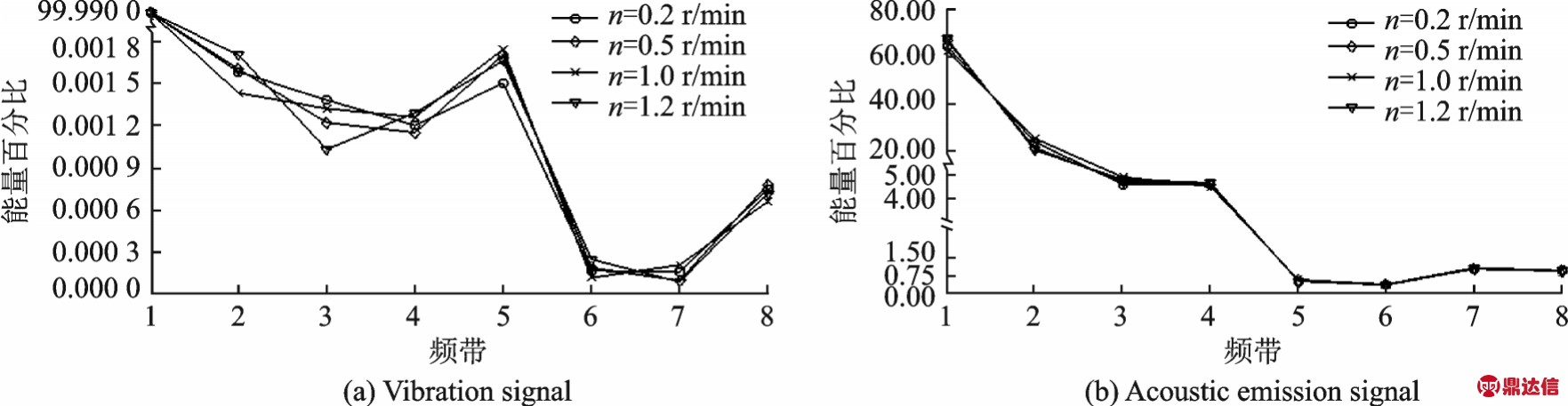
图8 振动、声发射信号的小波包能量分布
Fig.8 Wavelet packet energy distribution of vibration and acoustic emission signal
3.2 振动、声发射信号的小波包能量分析
对第1组试验的振动、声发射信号进行小波包分解。因为振动信号的主要信息分布频率范围是0~20 kHz,所以选择8层小波包分解,得到256个小波包系数序列。每个频带的频宽为1.95 kHz,因此选择前16个小波包系数进行研究,对应的频率宽度为31.28 kHz。而声发射信号的主要信息分布频率范围是100~500 kHz[11],所以选择4层小波包分解,得到16个小波包系数序列。每个频带的频宽为31.25 kHz,对应的频率总宽度为500.10 kHz。为了更清晰地表达出信号的能量分布,对特征矢量进行降维处理,由16维降为8维,即每两个频带能量相加组成一个新的频带,小波包能量分布见图8。
由图 8可知,(1)频带 1(0~3.91 kHz),频带 2~3(3.91~11.72 kHz) 和 频 带 4~5(11.72~19.54 kHz)是振动信号小波包能量的主要集中区域,频带6~8超出 20 kHz的范围,故不予考虑。(2)频带 3~4(125.0~250.0 kHz)和频带 7~8(375.1~500.1 kHz)是声发射信号小波包能量的主要集中区域,频带1~2低于100 kHz的范围,频带5~6能量变化与7~8类似,故不予考虑。振动、声发射信号小波包能量集中的频带的频谱见图9。其他组试验的振动、声发射信号均具有相同的特征规律。
为了清楚地揭示振动、声发射信号的小波包能量与主轴转速和激振频率的内在联系,将前3组试验的振动、声发射信号小波包能量集中的频带单独取出作图分析,结果见图10。
由图10可以看出,对于振动信号而言:(1)频带1(0~3.91 kHz)属于低频带,其能量占比达到了99%以上,主轴转速的改变并不能对其产生什么影响。(2)频带2~3(3.91~11.72 kHz)属于中低频带,其能量占比在15 Hz的激振频率下,随主轴转速的提高先降低后升高,转折点为1 r/min;在18 Hz的激振频率下,随主轴转速的提高而逐渐减低;在20 Hz的激振频率下,随主轴转速的提高也是先降低后升高,转折点降为0.5 r/min。这表明,一方面,主轴转速增加,即工件材料的变形速率增加,导致挤压丝锥与工件间的摩擦力增大,使得振动信号能量向高频移动,表现为中低频能量逐渐降低;另一方面,随激振频率的增加,即挤压丝锥脱离工件的次数增加,改善了挤压丝锥与工件间的摩擦状况,使得振动信号能量又向低频移动,表现为中低频能量发生回升现象。(3)频带 4~5(11.72~19.54 kHz)属于中高频带,而振动信息主要包含在中低频带。因此,在试验中并不能表现出明显的特征。(4)当主轴转速不变时,随着激振频率的升高,中低频带2~3的能量曲线先升后降,而中高频带4~5的能量曲线先降后升。这说明在15~20 Hz频率范围内,振动能量先向低频移动,而后向高频移动。究其原因主要是,随激振频率的增加,即挤压丝锥脱离工件的次数增加,改善了挤压丝锥与工件间的摩擦状况,使得振动信号能量向低频移动。但当激振频率到达一定的界限时继续增加,使得挤压丝锥切入切出工件时间变短,润滑油不能充分流入两者之间,导致摩擦状况恶化,摩擦力增大,致使振动信号能量又向高频移动。在这两个原因的共同作用下,使得该曲线出现转折点,该转折点的激振频率在18 Hz左右,会随着主轴转速的改变而有所移动。
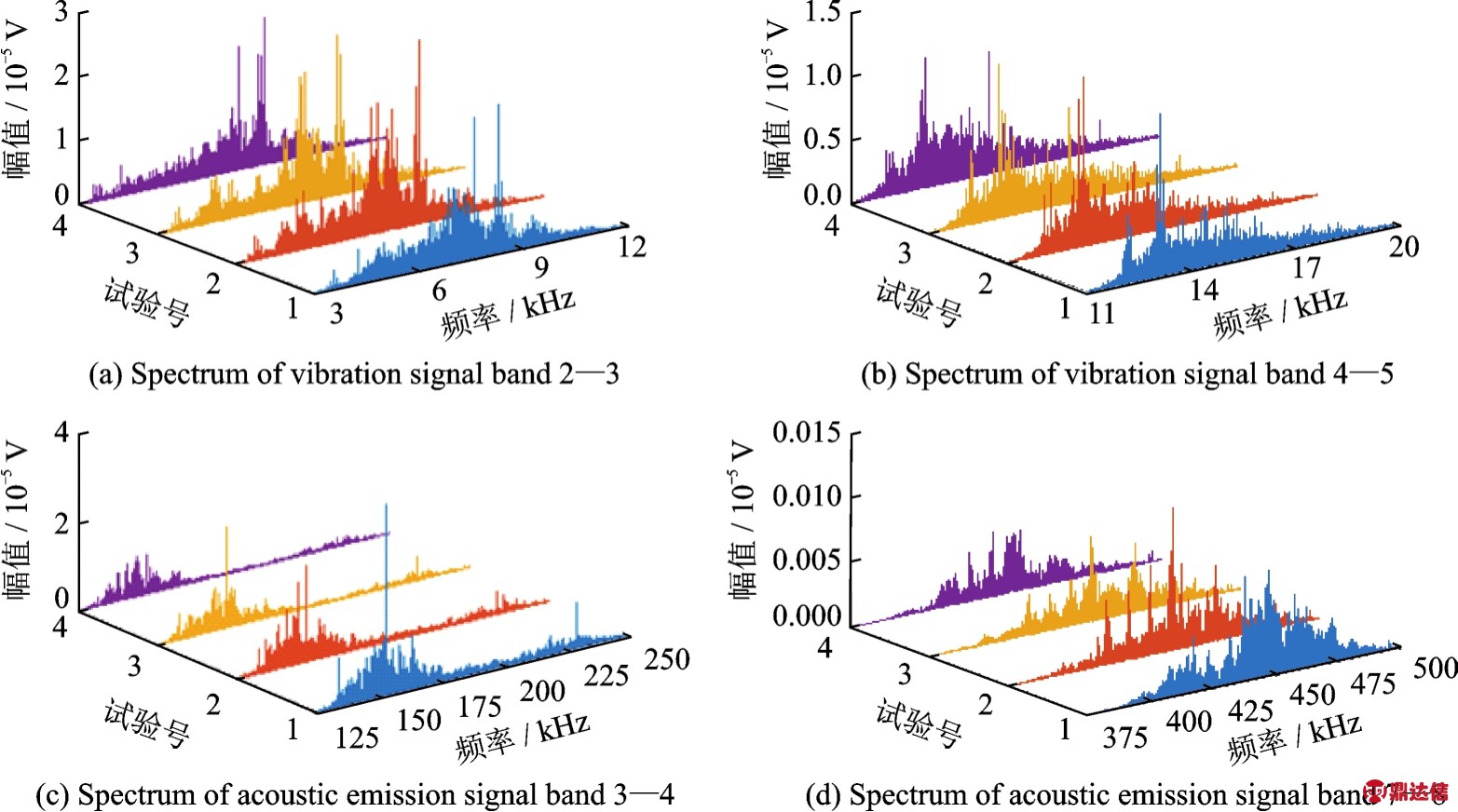
图9 振动、声发射信号小波包能量集中频带的频谱
Fig.9 Wavelet packet energy concentration band spectrum of vibration and acoustic emission signal
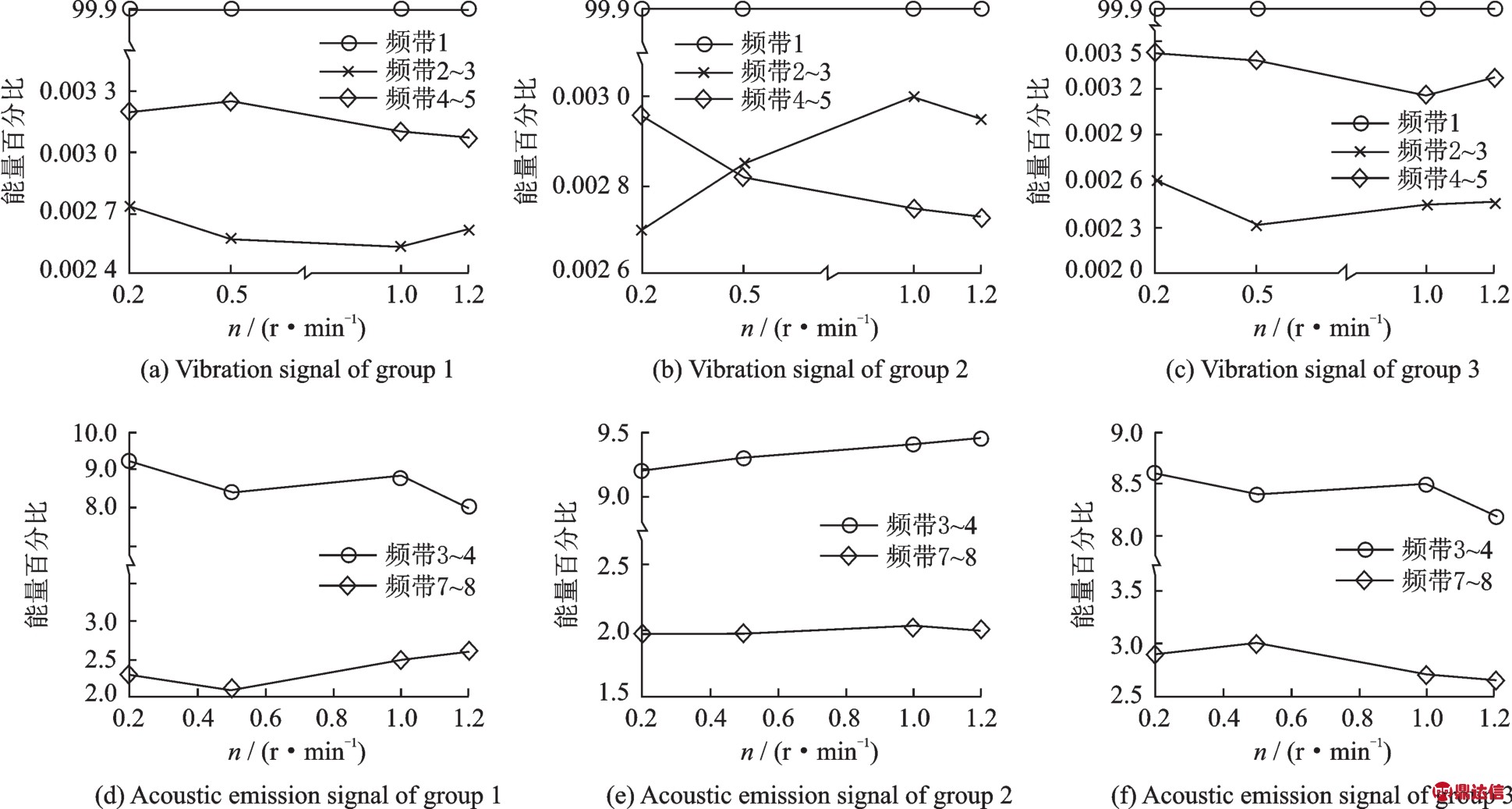
图10 前3组试验的振动、声发射信号小波包能量集中频带的能量分布
Fig.10 Wavelet packet energy concentrated band energy distribution of vibration and acoustic emission signals of group 1—3
对于声发射信号而言:(1)频带 3~4(125~250 kHz)属于中频带 ,频带 7~8(375.1~500.1 kHz)属于高频带,其小波包能量百分比随主轴转速的提高并不能呈现明显的增加或减少趋势。究其原因,声发射信号不仅反映挤压丝锥和工件间的摩擦状态以及工件材料的变形速率,还受到激振装置、主轴箱以及电动机等多方面的因素影响,故声发射信号能量曲线不能呈现明显的规律性。(2)当主轴转速不变时,随着激振频率的升高,声发射信号能量与振动信号能量变化趋势相似,即随激振频率的增加,声发射能量先向低频移动,而后向高频移动。造成这种现象的原因也与振动信号相同,这里不再赘述。
图11是第4组试验的振动、声发射信号的主要频带能量分布。由图11可知,随着润滑液黏度系数的增长,振动信号的频带2~3的能量逐渐减少,而频带4~5的能量逐渐增加;声发射信号的频带3~4的能量逐渐减少,而频带7~8的能量逐渐增加。这说明,厚油膜不利于挤压丝锥对工件的充分挤压,使得摩擦加剧,而流体薄油膜润滑有助于降低摩擦阻力。因此,随着润滑液黏度系数的增长,振动、声发射信号的能量都向着高频移动。
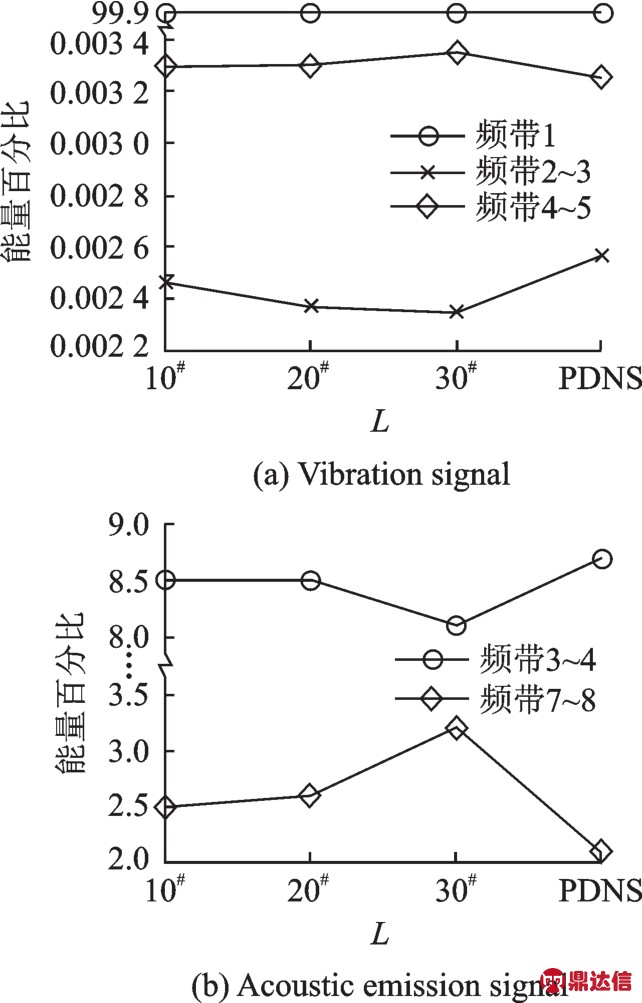
图11 第4组试验振动、声发射信号的主频带的能量分布
Fig.11 Energy concentrated band energy distribution of vibration and acoustic emission signals of group 4
综上所述,振动和声发射信号在不同频带内能量分布的变化反映出挤压丝锥与工件间的摩擦状态的变化,能量向低频移动说明摩擦减弱,能量向高频移动说明摩擦增强。此外,工艺参数对振动、声发射信号的能量分布影响规律为:激振频率对二者影响均最为显著;主轴转速对振动信号影响较小,对声发射信号几乎无影响;润滑油类型对二者均有一定的影响。这一规律反映出上述工艺参数对挤压丝锥与摩擦状态影响程度的不同。
3.3 扭矩信号分析
第3组试验中的试验号1的扭矩原始信号时域波形见图12。采用最小二乘法对其进行拟合,即寻找一条曲线使在误差平方和最小的准则下与所有数据点最为接近[12],拟合结果见图13。把扭矩的最大值作为扭矩信号分析的特征值。
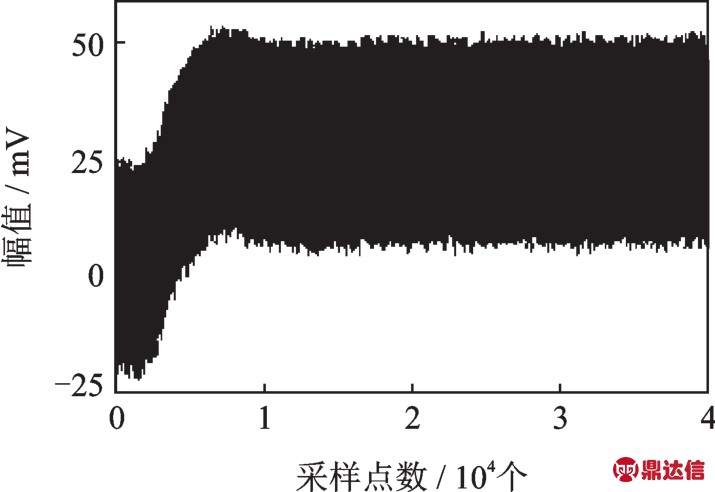
图12 扭矩信号时域波形
Fig.12 Time domain waveform of torque signal
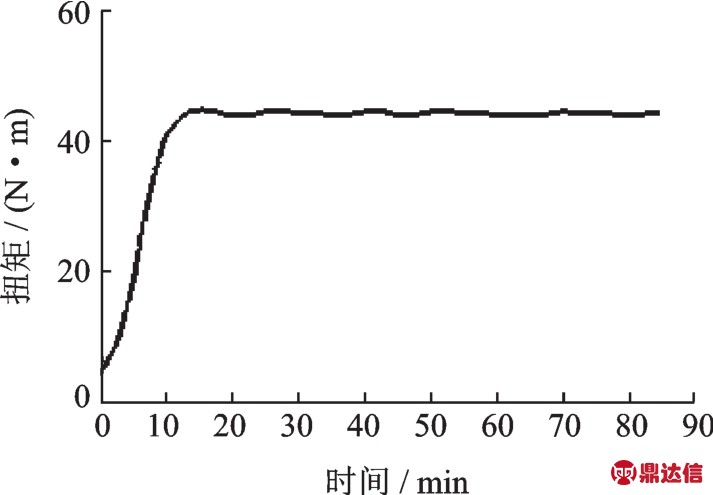
图13 扭矩信号的拟合结果
Fig.13 Torque signal fitting results
图14 是4组试验的扭矩信号的特征值分布。由图14可知,(1)随着主轴转速的提高,挤压扭矩不断增大。这是因为随着主轴转速的提高,工件挤压变形速率加快,引起挤压扭矩升高。(2)随着激振频率的升高,挤压扭矩有一个先升后降的过程。这是因为当激振频率较低时,丝锥与工件接触时间较长,金属材料的屈服强度增大,所需的挤压扭矩也会增大。当激振频率较高时,丝锥切入切出工件的时间变短,使得润滑油不易进入接触位置,导致两者间的磨损加剧,引起挤压扭矩升高。(3)随着润滑油黏度系数的升高,挤压扭矩不断升高。这与振动、声发射的原因类似,这里不再赘述。
3.4 温度信号分析
第2组试验中的试验号1的温度曲线见图15,如图15可将温度曲线分为3个阶段:(1)室温阶段:在加工开始后的一段时间内(约为总加工时间的前1/20),温度一直保持室温不变,这是因为红外温度传感器的测点为工件外部,故温度的传导需要一定的时间。(2)温度上升阶段:该阶段温度持续急剧上升,而且随着主轴转速的提高,上升速度不断加快。但该阶段的时间占比大致不变,约占总加工时间的1/4。(3)温度稳定阶段:当温度上升到一定值后,开始在某一温度上下进行微弱的波动。把第(3)阶段的温度均值作为温度信号分析的特征值。
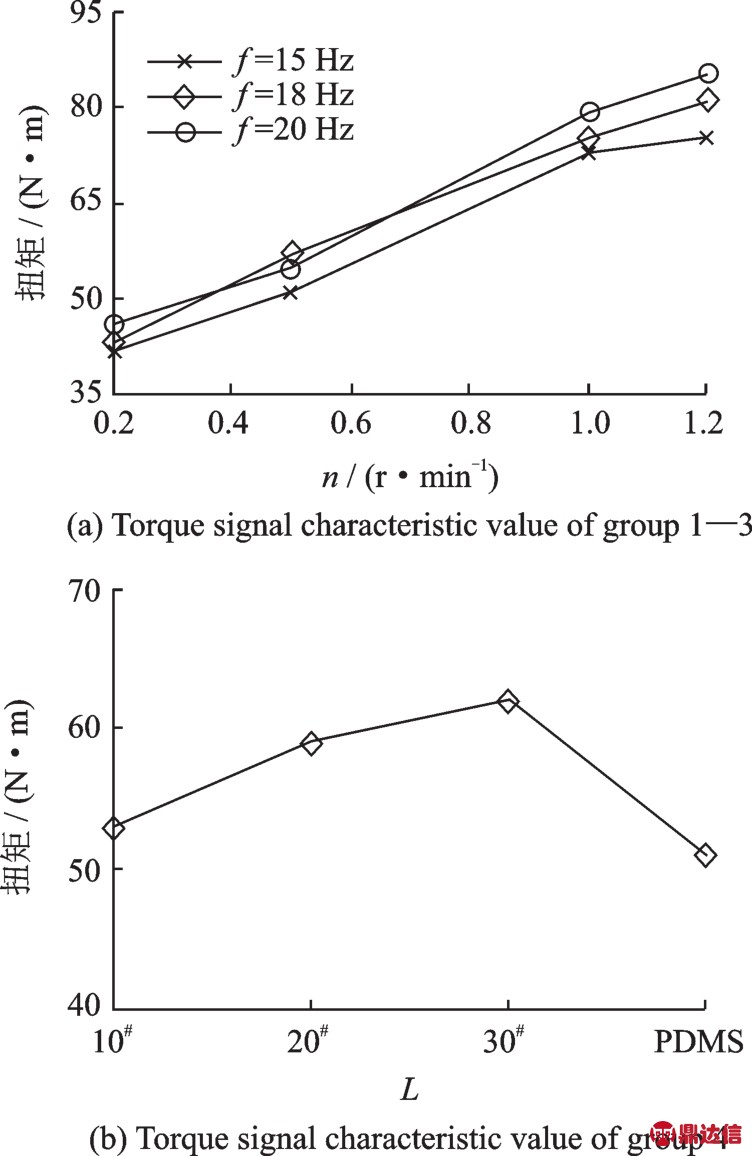
图14 4组试验的扭矩信号特征值
Fig.14 Torque signal characteristic value of four group tests
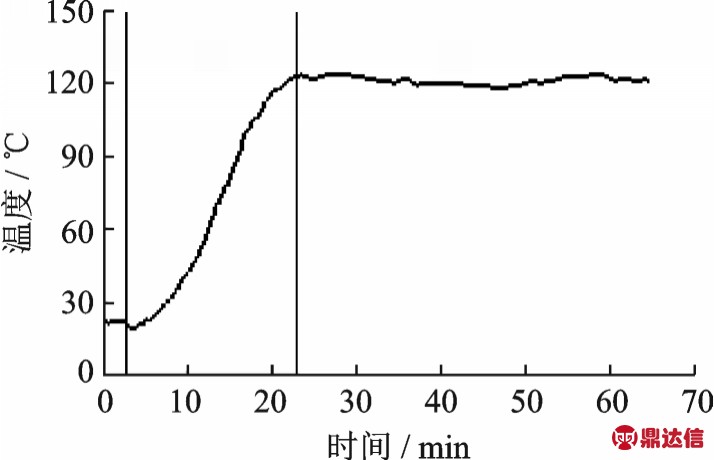
图15 第2组试验中的试验号1的温度曲线
Fig.15 Temperature curve of test No.1 in group 2
图16 是4组试验的温度信号的特征值分布。由图16可知,不同工艺参数下温度的变化趋势和扭矩基本相同,其原因也类似,这里不再赘述。
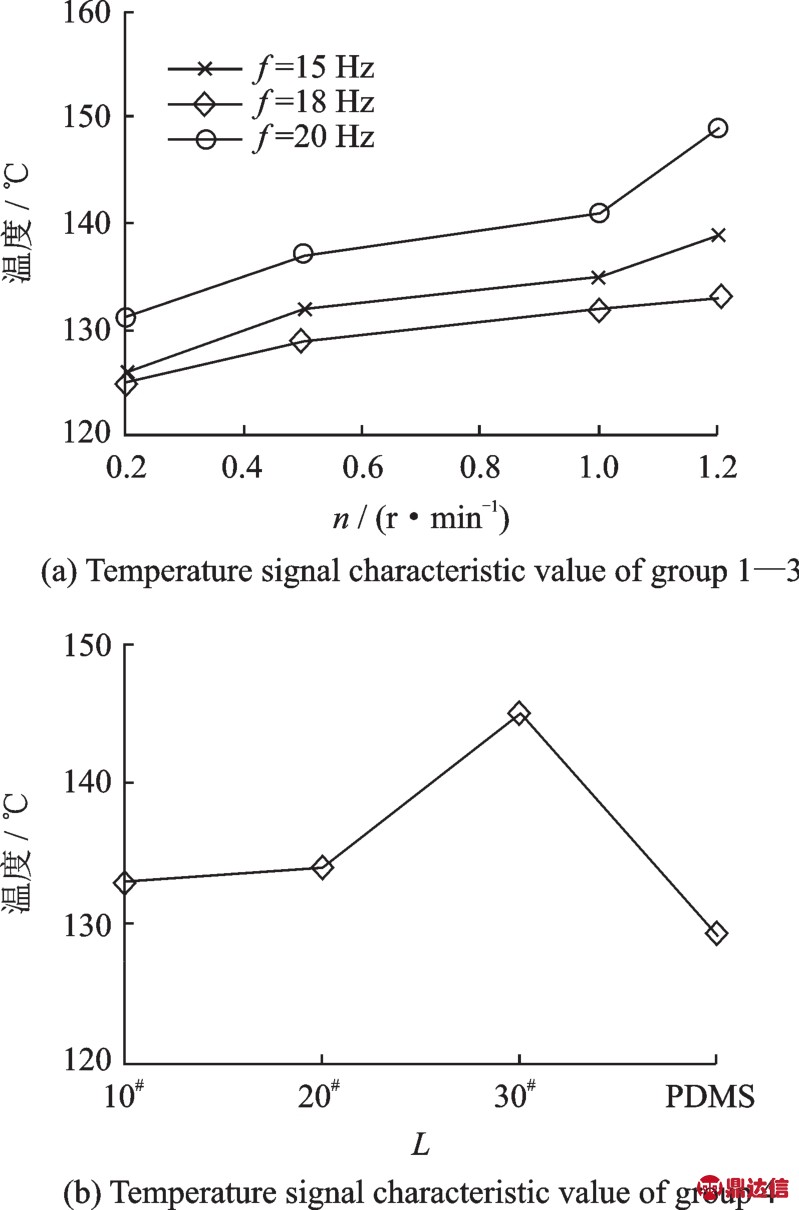
图16 4组试验的温度信号特征值
Fig.16 Temperature signal characteristic value of four group tests
4 结 论
本文结合传感器信号特征,分析了主轴转速、激振频率以及润滑油类型这3个挤压工艺参数的影响。得出:(1)随着主轴转速的提高,振动、扭矩和温度都有着不同程度的提高,但主轴转速又直接影响工件的加工效率,所以应权衡两方面因素选取主轴转速。(2)随着激振频率的提高,振动、扭矩以及温度均先降低后升高,对于316L不锈钢材料的加工,该转折频率位于18 Hz左右。(3)当挤压温度较低时,黏度系数较小的润滑油更有利于改善挤压区的摩擦状态,当挤压温度较高时,该影响不明显。