摘要:针对油气井日益苛刻的环境,基于特殊螺纹密封机制,提出一种由锥面对锥面和柱面对球面组合的双主密封螺纹接头结构。采用有限元法对比分析双主密封、锥面对锥面密封、柱面对球面密封3种主密封结构在上扣、拉伸、压缩、拉伸和内压、拉伸和内外压5种工况下,密封面接触应力、接触长度的变化情况,得到3种主密封结构的密封能力随载荷的变化规律。分析结果表明,与单主密封接头相比,该双主密封接头在不同载荷下锥面和柱面上的接触应力分布更均匀,接触长度更长且接触应力峰值更小。全尺寸试验结果表明,该双主密封接头的密封性能达到了使用要求。
关键词:特殊螺纹;接触应力;密封结构;密封性能;全尺寸试验
油套管柱由成百上千根石油专用管材通过螺纹连接在一起,并长期承受复合载荷的考验。油套管最薄弱的部分就是螺纹连接处,螺纹的质量直接影响到油气井的寿命[1-2]。随着石油开采技术的进步,国内外出现了不少超深井、高压气井的开发,特殊螺纹接头已得到广泛使用[3]。特殊螺纹通常采用金属对金属密封结构来实现其优良的密封性能,目前关于金属对金属密封结构密封性能的研究较多。2010年,王建东等[4]对锥面/锥面密封和弧面/锥面密封2种密封结构进行了对比研究,获得了一种新的密封准则。2011年,孔华等人[5]对锥面/锥面密封结构进行了分析研究,获得了锥面接触应力分布规律。2015年,FEN等[6]对变锥面及弧面/锥面2种密封结构的密封性能进行了对比研究,获得了2种密封型面密封性能的规律。2016年,朱鹏等人[7]对球面/柱面密封结构进行了分析研究,得到不同工况下密封面接触应力及等效应力的分布规律。同年,许红林等[8]对球面/锥面密封结构进行了研究,提出了改善球面密封性能的措施。以上研究均集中在单主密封结构上,对双主密封结构密封性能的研究很少。根据油气田现场调研,在超深井、高压气井中,组合主密封螺纹接头应用较多。因此,深入开展组合主密封结构的研究是十分必要的。
本文作者基于特殊螺纹密封机制,提出了一种由锥面对锥面和柱面对球面组合的双主密封结构。利用有限元方法,对比分析了双主密封螺纹接头、锥面对锥面密封接头、柱面对球面密封接头在不同工况下密封性能的变化规律,最后通过全尺寸试验验证了该双主密封螺纹接头的气密封性能,研究内容为组合主密封螺纹接头的设计及应用提供了参考。
1 理论模型
流体通过间隙时产生的局部阻力取决于间隙的截面积和泄漏路径的长度[9],可表示为
ΔR∝Δl/S
(1)
式中:ΔR为局部阻力;S为间隙的截面积;Δl为泄漏路径的最小长度。
接触面上的接触应力越大,间隙的截面积就越小,若二者成比例变化,则有[9]:
ΔR∝ptΔl
(2)
式中:pt为接触应力。
泄漏阻力相当于沿泄漏路径累积的接触应力,当气体或液体通过间隙时,产生的阻力[9]为
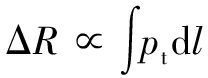
(3)
要提高密封结构的密封能力,必须要增加密封面的临界泄漏阻力,即提高密封面的接触应力,使泄漏路径的面积较小和增加密封面的接触面积,使泄漏路径较长。若单纯增加接触应力,易导致密封面应力超过材料的屈服极限,造成塑性破坏或应力腐蚀;若单纯增加接触面积,则接触应力会减小,复合载荷下难以保证可靠的密封效果。因此,不论选择何种密封形式,要保证接触应力和接触面积的平衡,同时保证密封面的加工质量,才能取得比较好的密封效果。
2 结构设计
目前国内外特殊螺纹接头产品的种类较多,由于设计思想不同,使得主密封结构的类型也各不相同,常见的主密封类型主要有锥面对锥面密封、球面对锥面密封、球面对柱面密封、柱面对柱面密封等结构[10],如图1所示。
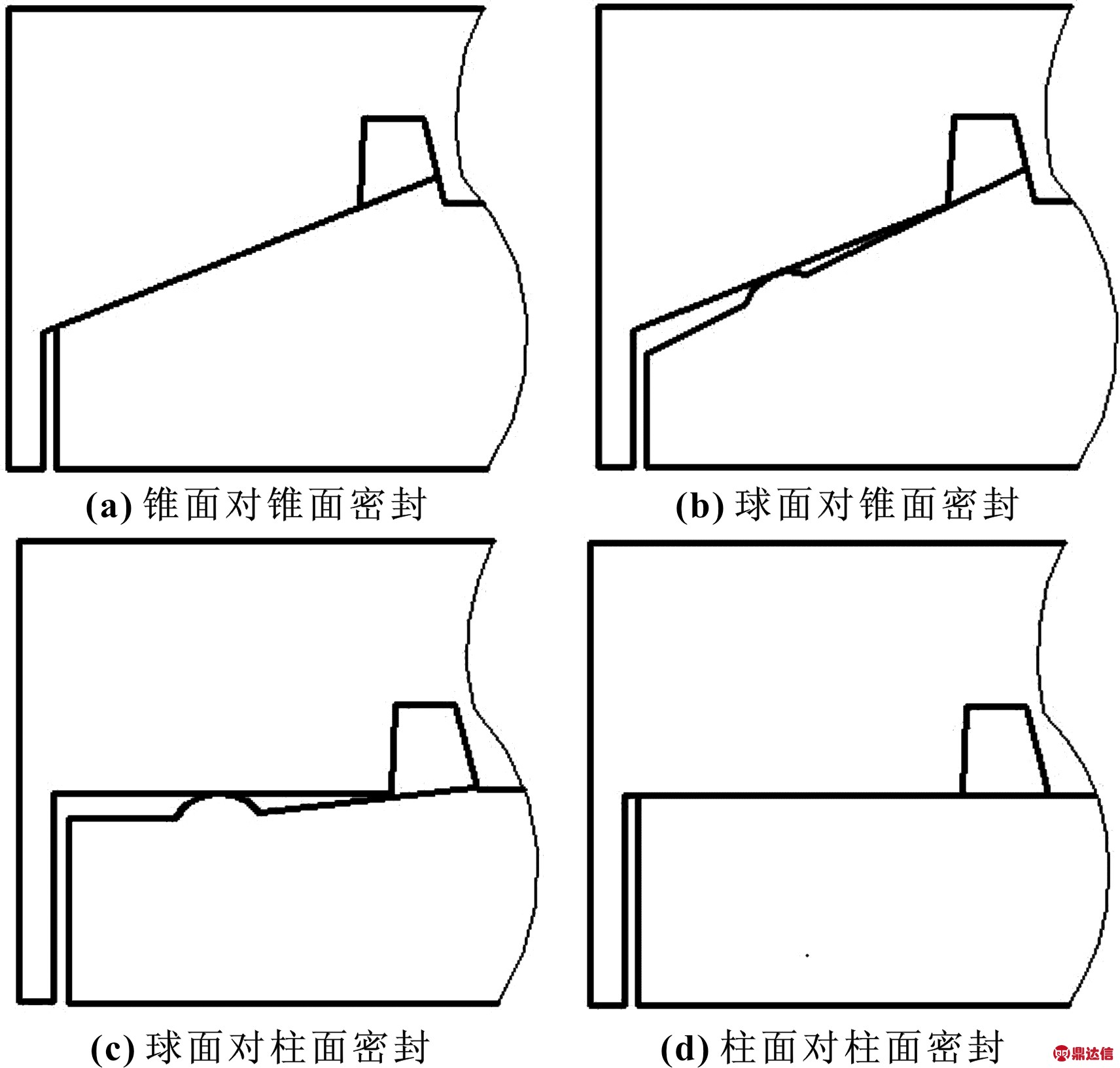
图1 常见的主密封结构形式
Fig 1 Common forms of main sealing structure (a) conical surface to conical surface sealing;(b) spherical surface to conical surface sealing;(c) spherical surface to cylindrical surface sealing;(d)cylindrical surface to cylindrical surface sealing
锥面对锥面密封结构具有较长的泄漏路径,在相同的接触应力下,有更好的密封效果,但锥面加工难度较大。球面对锥面密封结构要求内外螺纹具有较大的拧紧力,使球面产生较大的变形量,才能保证密封面具有足够的接触应力[11]。球面对柱面密封结构接触应力较大,对轴向拉伸载荷不敏感,但接触面积小。柱面对柱面密封结构接触面积大,对轴向载荷不敏感。常规的气密封螺纹接头,通常采用单级金属密封结构,这类密封结构的不足之处是接头在井下会承受各种复合载荷的作用,单级密封一旦受损或发生较大的塑性变形,接头的密封能力会明显降低,甚至失效。为增强接头在复合载荷下的密封性能,设计了一种新型的螺纹接头,该接头主密封结构采用锥面对锥面和柱面对球面的组合密封形式,扭矩台肩采用-15°逆向台肩,螺纹采用-5°承载面的改进型偏梯形螺纹,设计方案如图2所示。
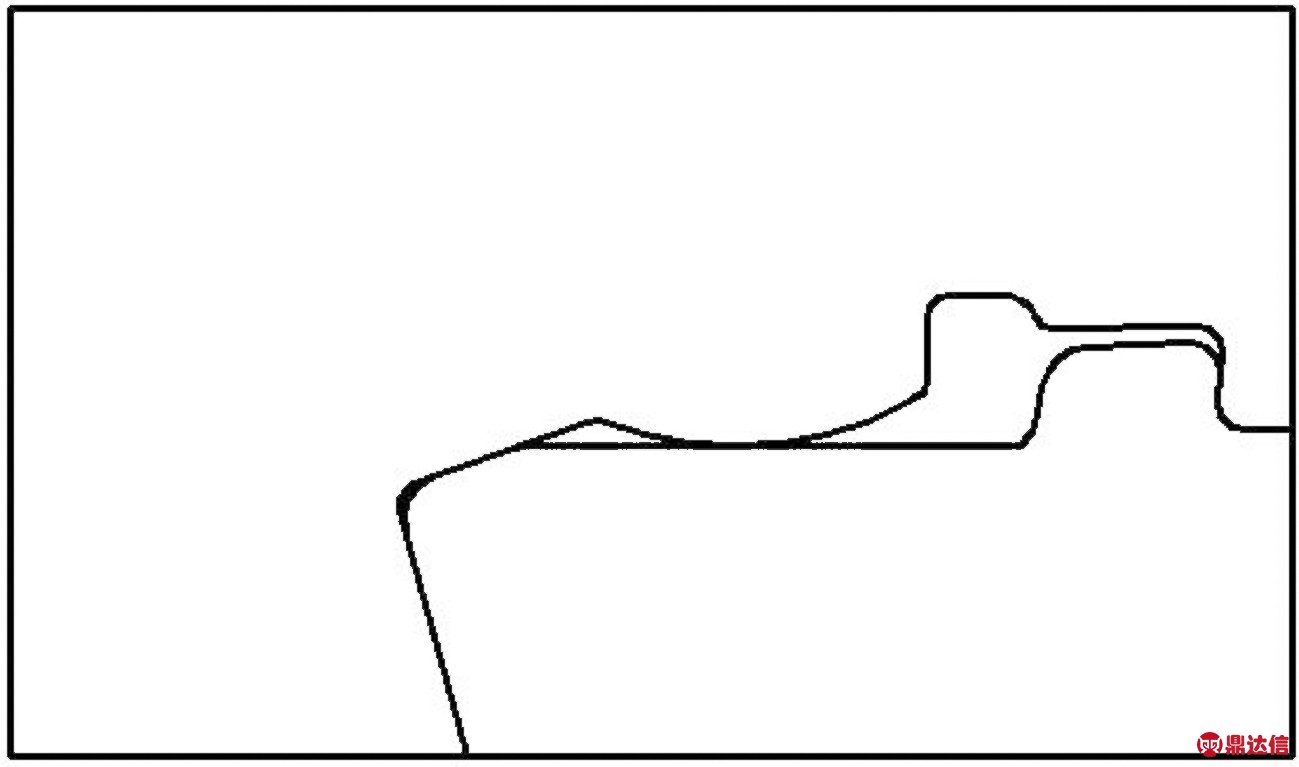
图2 设计的特殊螺纹密封结构形式
Fig 2 The designed sealing structure form of premium connection
3 有限元建模
3.1 模型简化
接头管体规格为φ88.9 mm×6.45 mm,螺纹为-5°承载面的改进型偏梯形螺纹,因该螺纹螺旋升角较小,忽略螺旋升角对计算结果的影响,把接头简化为轴对称结构[12]。采用二维轴对称模型来对接头进行有限元建模,考虑到圣维南效应,为保证计算精度,建模时所取的管体长度为2倍管体小端至螺纹消失点的距离。采用控制变量的思想,保证双主密封螺纹接头主密封结构的尺寸参数分别与对应的单锥面对锥面密封及单柱面对球面密封的结构参数相同,双主密封接头建模图如图3所示。

图3 双主密封接头几何建模图
Fig 3 Geometric model of double primary sealing connection
采用CAX4I四节点双线性轴对称四边形单元对模型进行网格划分,并对螺纹连接部分、密封面及扭矩台肩进行网格细化。双主密封接头局部网格划分如图4所示。
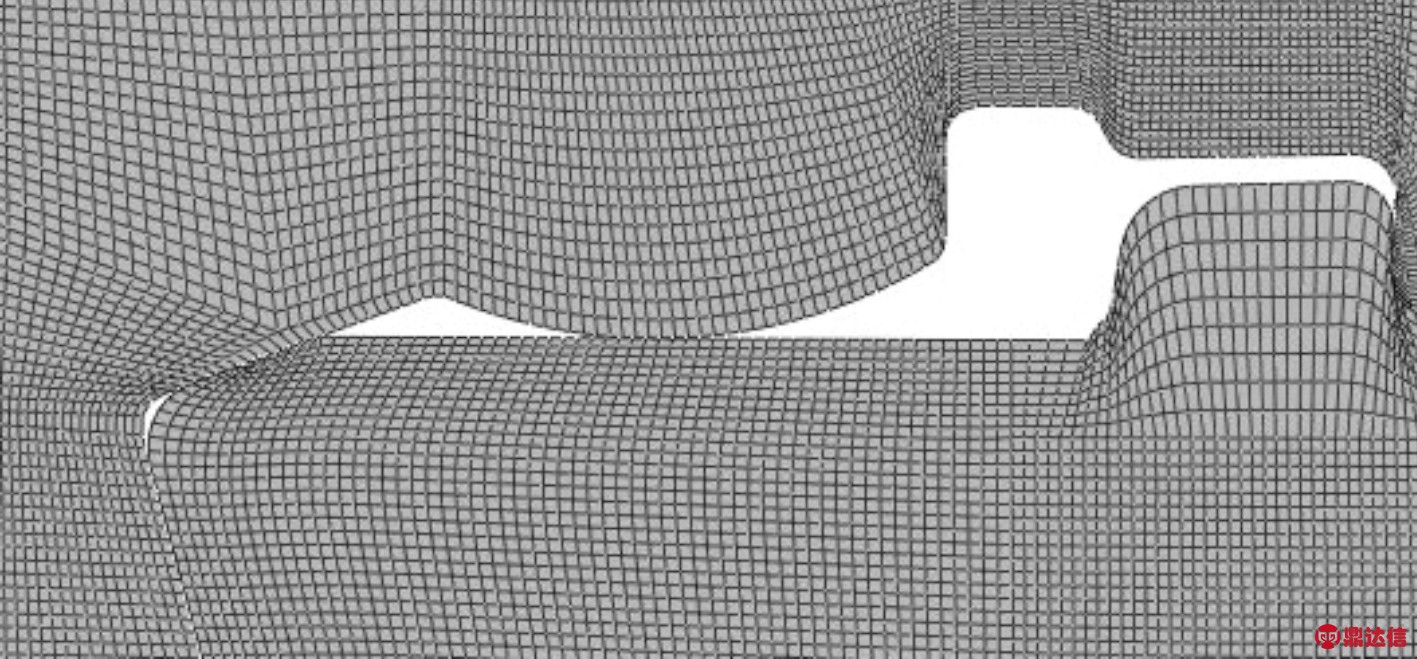
图4 局部网格划分
Fig 4 Local mesh partition
3.2 材料力学性能
接头采用2Cr13材料进行加工,并经过热处理,处理到API L80钢级。对随炉处理的样件实测其屈服强度、抗拉强度及延伸率,结果如表1所示。2Cr13为合金钢,查《机械设计手册》可知,弹性模量为206 GPa,泊松比为0.3[13]。密封面接触时采用库伦摩擦模型,摩擦因数与螺纹脂有关,一般取0.02[14]。
表1 材料力学性能
Table 1 Mechanical properties of materials

3.3 边界条件
根据接箍的对称性,接箍中面的轴向位移为0,因此在接箍对称中面的各结点上施加轴向位移约束,径向方向自由。接头上扣状态通过施加过盈量来模拟,轴向力转化为均布载荷施加在管体大端,计算公式为
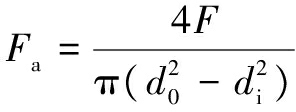
(4)
式中:Fa为轴向应力;F为轴向力;d0为管体外径;di为管体内径。
螺纹接头在井下会承受复杂的工况,不同工况载荷的不同,对接头密封性能会产生不同的影响。考虑上扣、上扣+轴向拉伸载荷、上扣+轴向压缩载荷、上扣+轴向拉伸载荷+内压、上扣+轴向拉伸载荷+内压+外压5种工况,具体的加载情况如表2所示。
表2 加载工况
Table 2 Loading modes
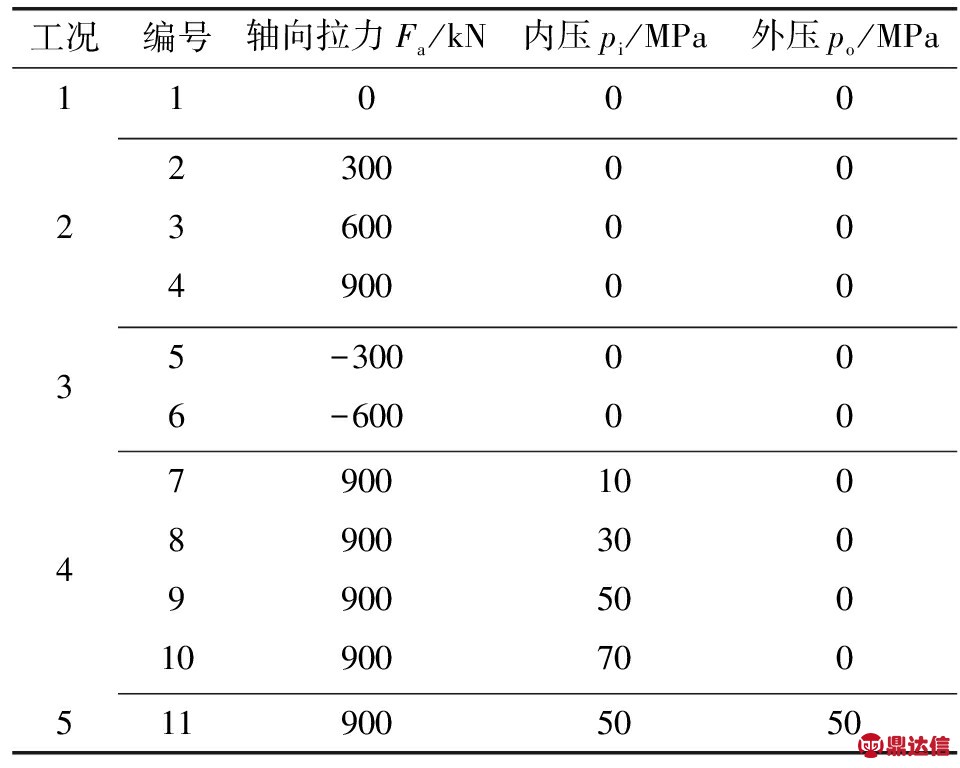
4 有限元结果及分析
4.1 上扣分析
采用施加过盈量来模拟接头上扣后的状态,螺纹上扣一圈至台肩面接触,螺纹过盈量为0.132 3 mm,锥面对锥面密封结构过盈量为0.10 mm,柱面对球面密封结构过盈量为0.08 mm,台肩过盈量为0.03 mm。上扣后不同密封结构的螺纹接头Mises应力云图如图5所示,主密封结构锥面接触应力分布曲线如图6所示,柱面接触应力分布曲线如图7所示。
由图5可知,上扣后不同密封型面接头的Mises应力最大值均出现在台肩和密封面的过渡段,双主密封接头的Mises应力最大值为649 MPa,低于单主密封接头台肩过渡段的Mises应力,表明双主密封接头台肩更不易发生屈服失效。从图6、7可知,双主密封结构锥面接触长度为1.4 mm,大于单主密封锥面的接触长度(1.28 mm),并且双主密封结构锥面最大接触应力(490 MPa)只有单主密封锥面最大接触应力(656 MPa)的74.7%。双主密封柱面接触应力最大值为776 MPa,小于单主密封柱面的最大接触应力971 MPa,而且双主密封柱面接触应力分布更加均匀。
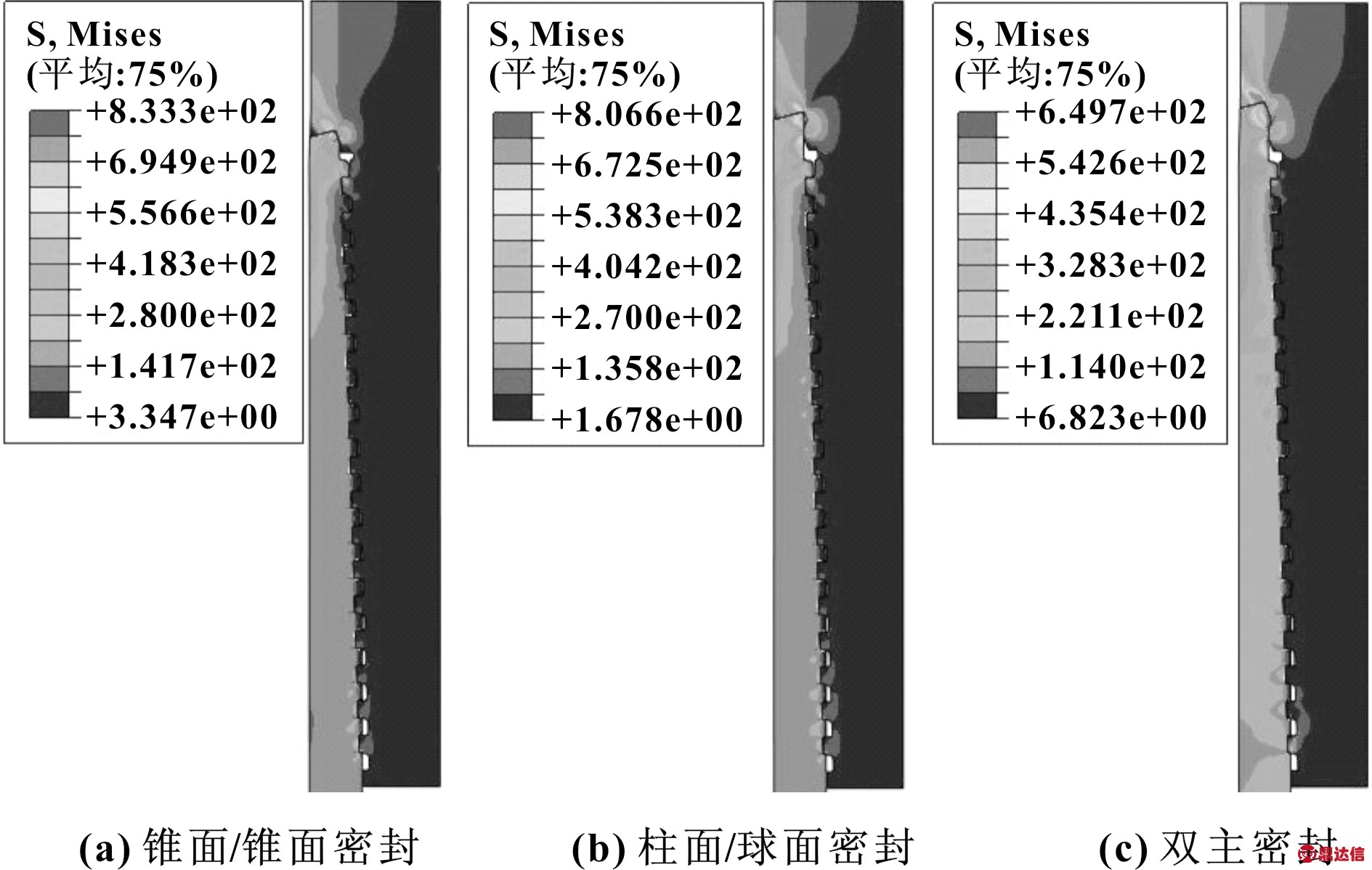
图5 上扣后Mises应力分布
Fig 5 Distribution of Mises stress after make-up (a) conical surface to conical surface sealing;(b) cylindrical surface to spherical surface sealing;(c) double primary sealing
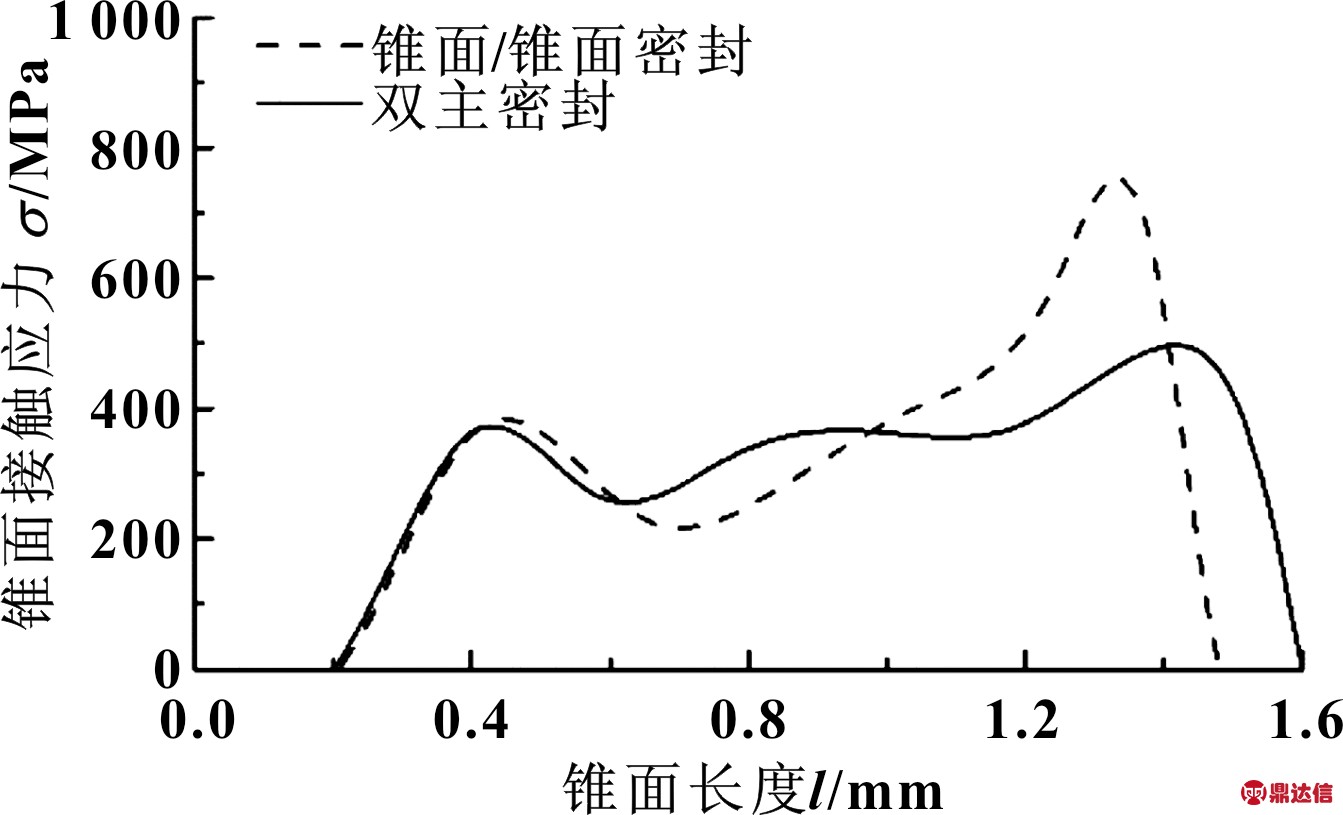
图6 上扣后锥面接触应力分布
Fig 6 Distribution of contact stress on conical surface after make-up
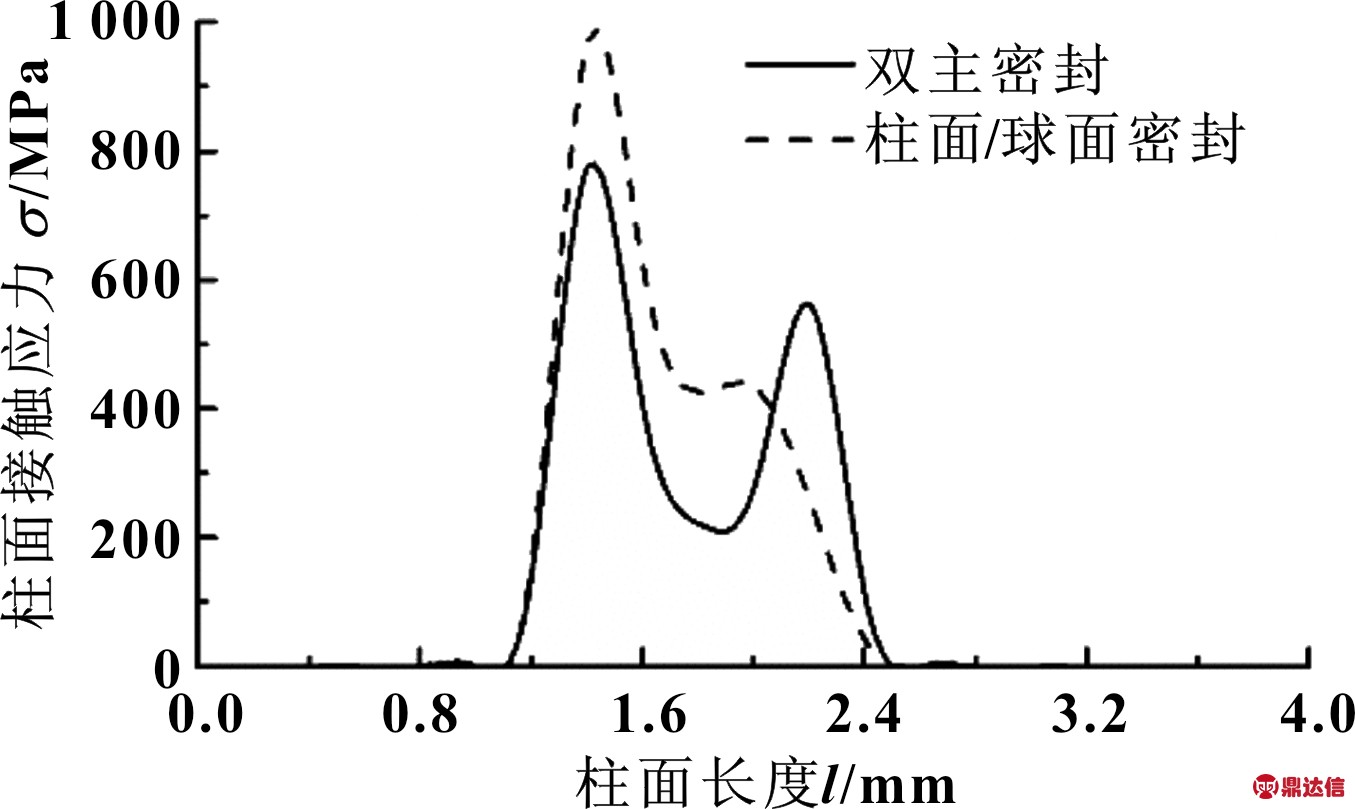
图7 上扣后柱面接触应力分布
Fig 7 Distribution of contact stress on cylindrical surface after make-up
4.2 轴向拉伸载荷下密封性能分析
特殊螺纹接头在井下服役时,会承受较大的拉伸载荷,增加了螺纹接头泄漏的可能性。接头上扣后,沿轴向对3种密封型面的接头分别施加工况2中的300、600、900 kN 3种拉伸载荷,得到了不同主密封结构密封面接触应力分布曲线,如图8、9所示。
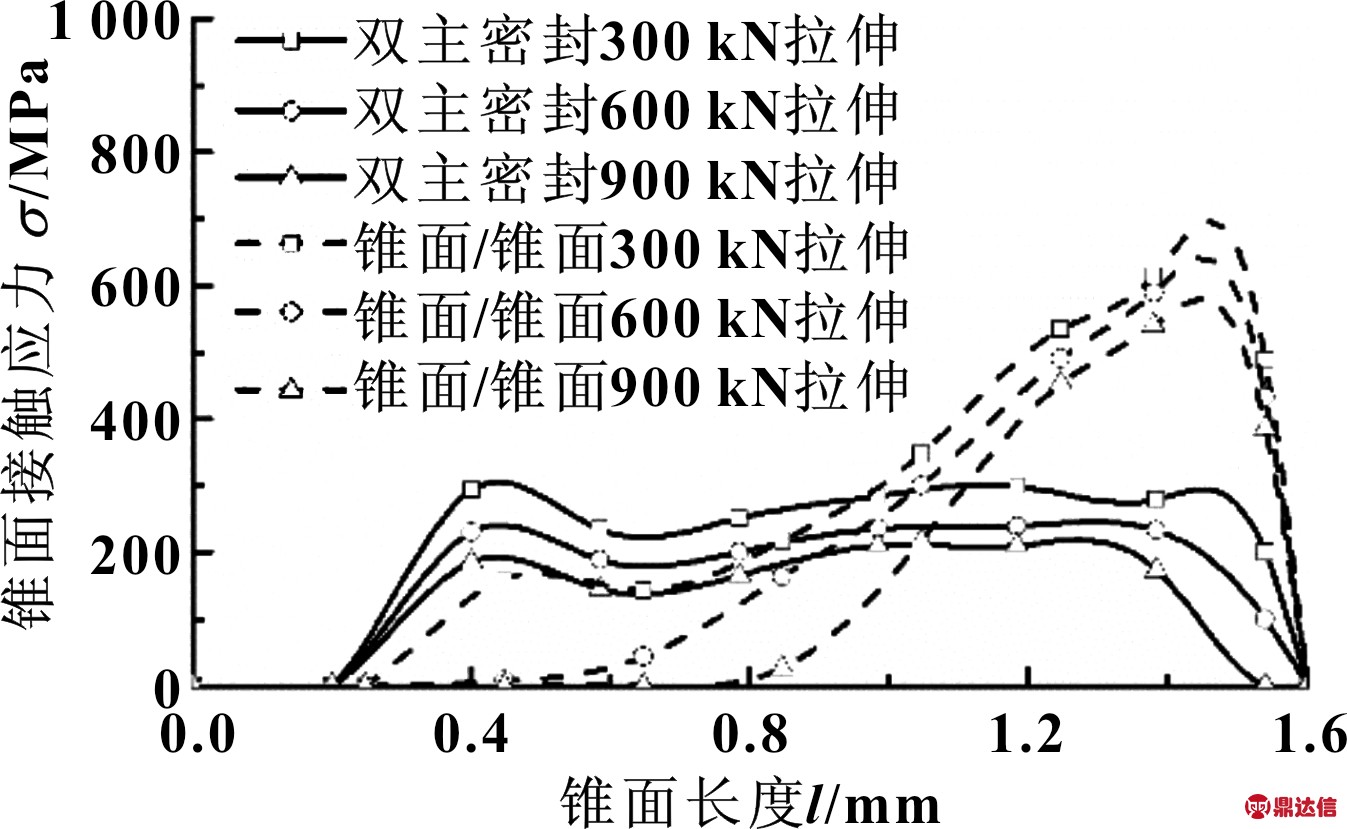
图8 拉伸载荷下锥面接触应力分布
Fig 8 Distribution of contact stress on conical surface under tensile load
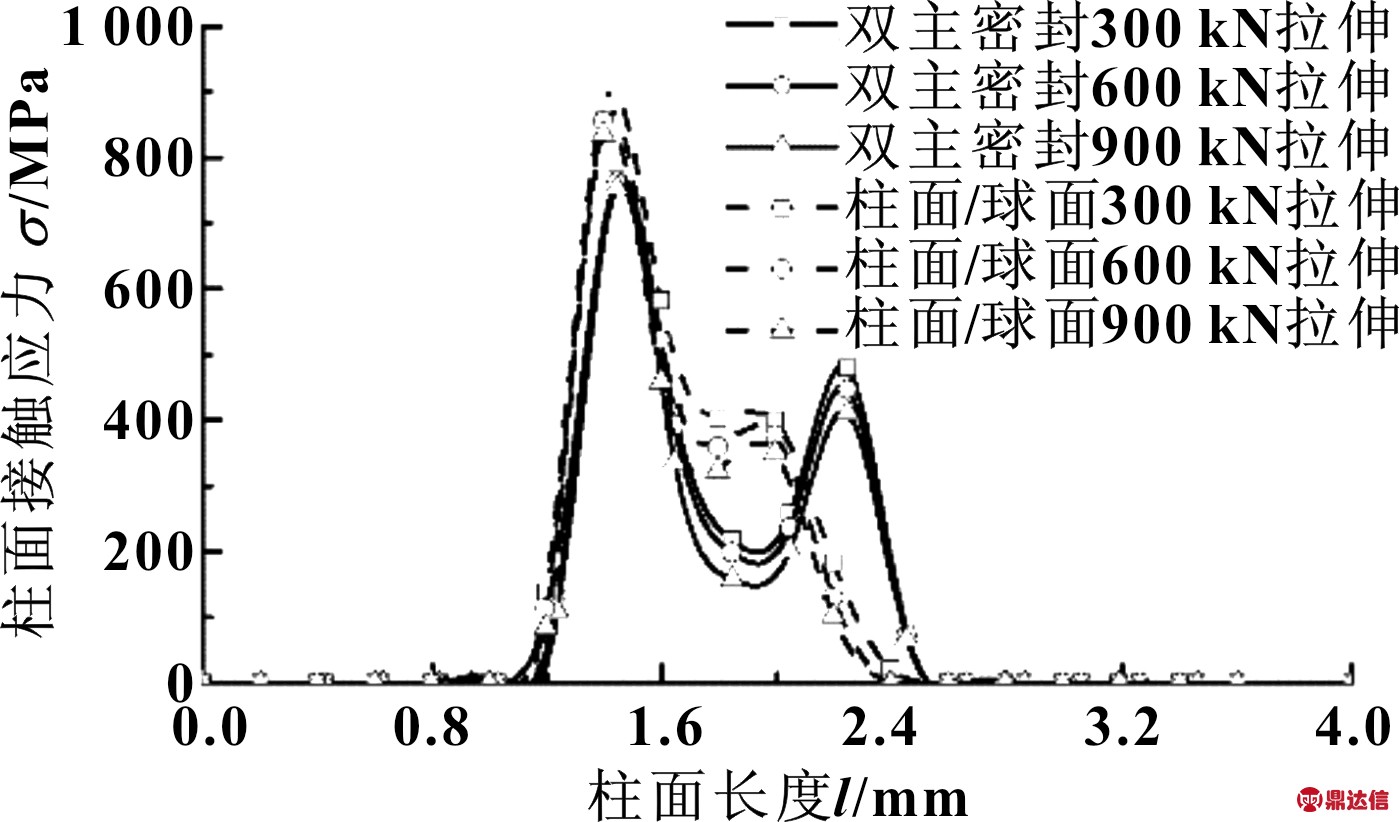
图9 拉伸载荷下柱面接触应力分布
Fig 9 Distribution of contact stress on cylindrical surface under tensile load
由图8可知,单、双主密封结构锥面接触应力和接触长度均随轴向拉伸载荷的增加而减小,但单主密封锥面接触长度减小更快。在900 kN轴向拉力下,单主密封锥面接触长度仅是双主密封锥面的57%,密封可靠性较低。
由图9可知,单、双主密封结构柱面接触应力及接触长度随轴向拉力增加而略有减小。在900 kN轴向拉力下,双主密封柱面接触长度为1.2 mm,是单主密封柱面的接触长度(1.0 mm)的1.2倍,且双主密封柱面最大接触应力比单主密封柱面小,因此双主密封柱面出现黏扣的可能性更低,密封性能更好。
4.3 轴向压缩载荷下密封性能分析
按照工况3的要求,对3种接头分别施加300、600 kN的轴向压缩载荷,得到了不同密封结构密封面上接触应力及接触长度分布曲线,如图10、11所示。
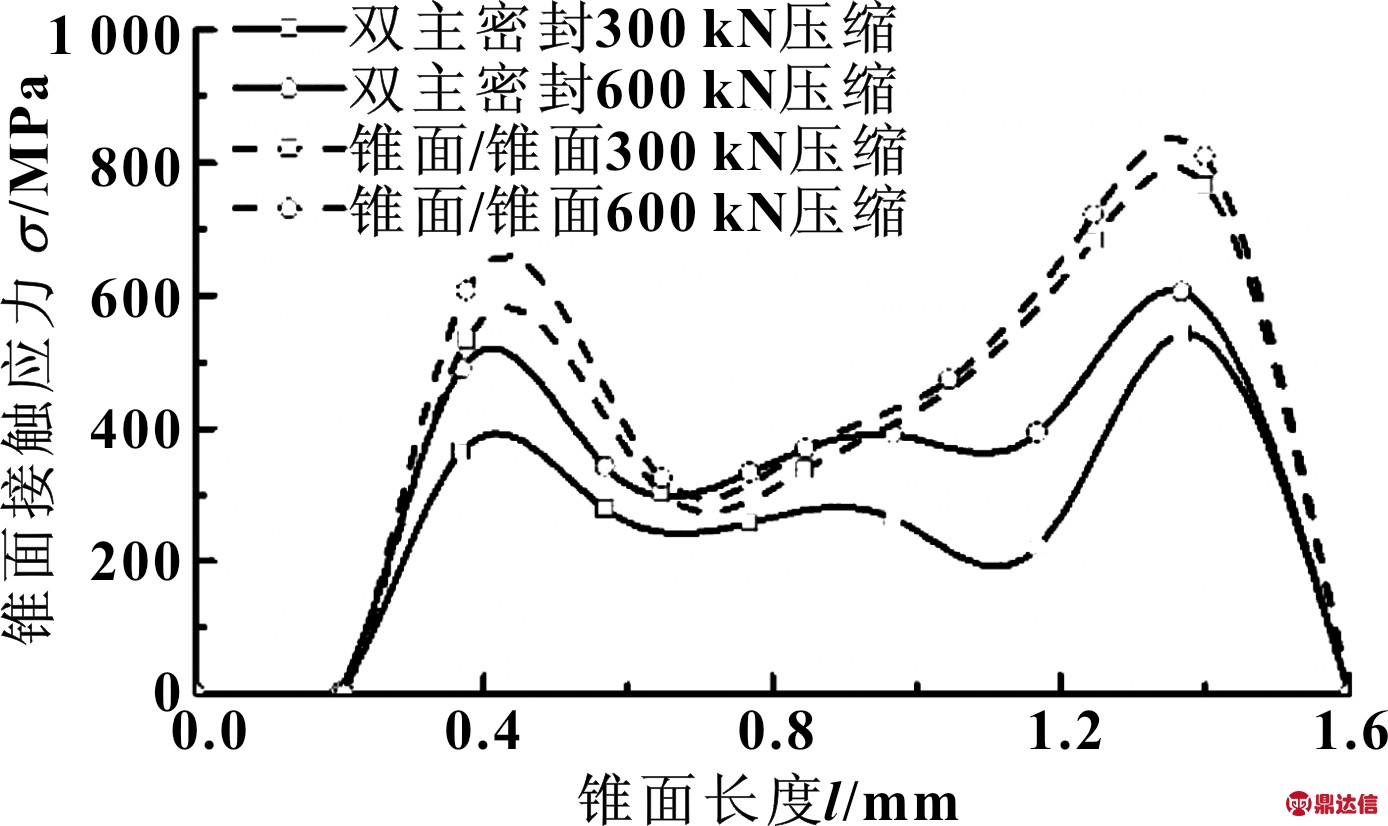
图10 压缩载荷下锥面接触应力分布
Fig 10 Distribution of contact stress on conical surface under compressive load
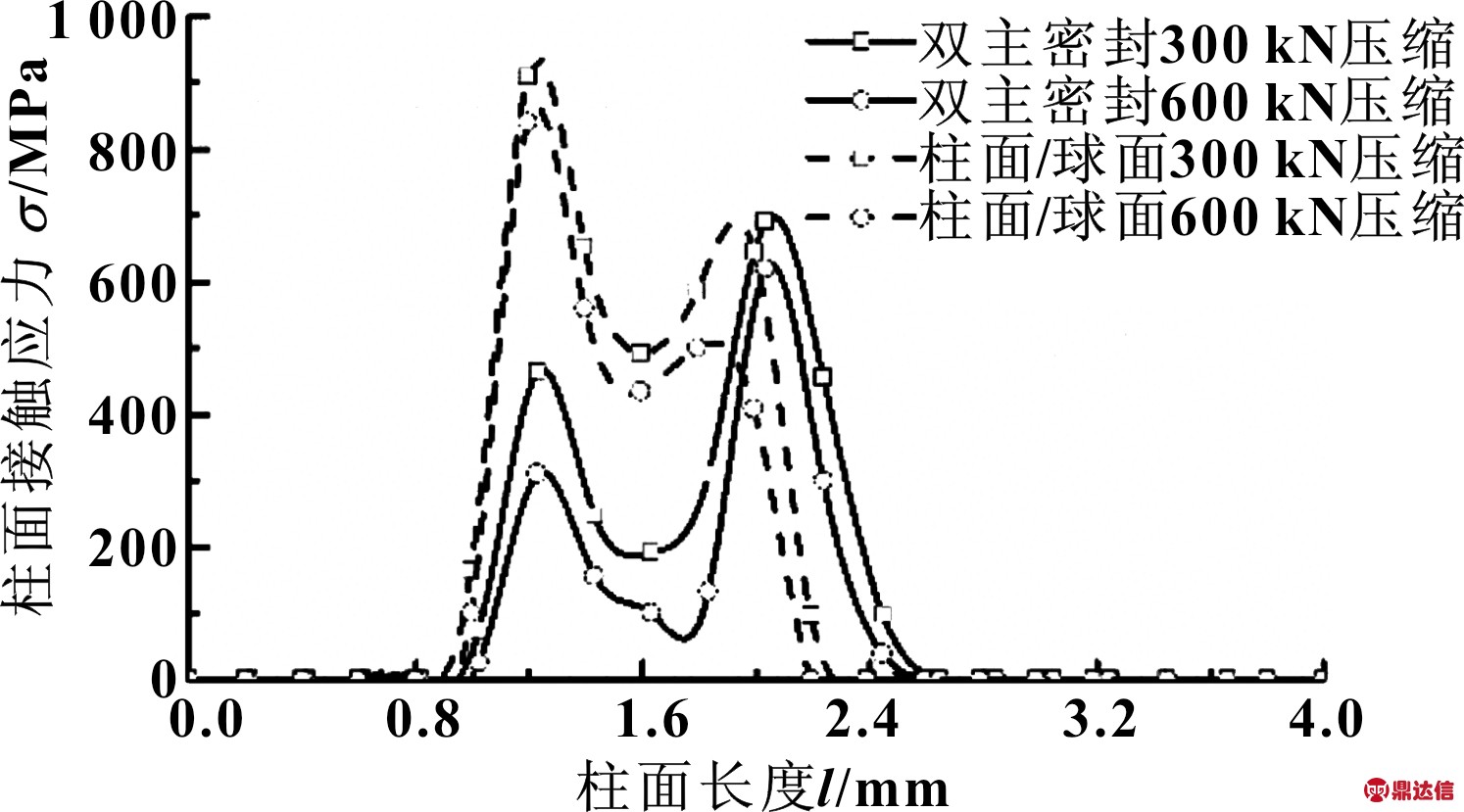
图11 压缩载荷下柱面接触应力分布
Fig 11 Distribution of contact stress on cylindrical surface under compressive load
由图10可知,单、双主密封锥面接触应力均随着轴向压缩载荷的增加而增大,且锥面接触应力最大值均出现在远离台肩的密封面收尾位置。在600 kN压缩载荷下,单主密封锥面的最大接触应力为810 MPa,超出了材料的屈服极限,密封面易产生屈服失效,而双主密封锥面最大接触应力为605 MPa,密封面并未屈服失效。
由图11可知,单、双主密封柱面接触应力和接触长度随轴向压缩载荷的增加而减小。在承受压缩载荷时,单、双主密封柱面的接触应力均随着与锥面距离的增加,先急剧增加,后快速下降,接着又快速增加,最后下降到0,应力曲线出现2个明显的波峰。在600 kN压缩载荷下,双主密封柱面接触长度为1.4 mm,大于单主密封柱面的接触长度(1.0 mm),双主密封柱面最大接触应力(620 MPa)只有单主密封柱面最大接触应力(840 MPa)的74%,因此双主密封柱面接触应力分布更加均匀,发生黏扣可能性也较低。
4.4 轴向拉伸和内压作用下密封性能分析
根据工况4的要求,对3种接头施加900 kN的轴向拉力,然后在接头内表面分别施加10、30、50、70 MPa的压力,得到了不同密封结构密封面的接触应力分布曲线,如图12、13所示。
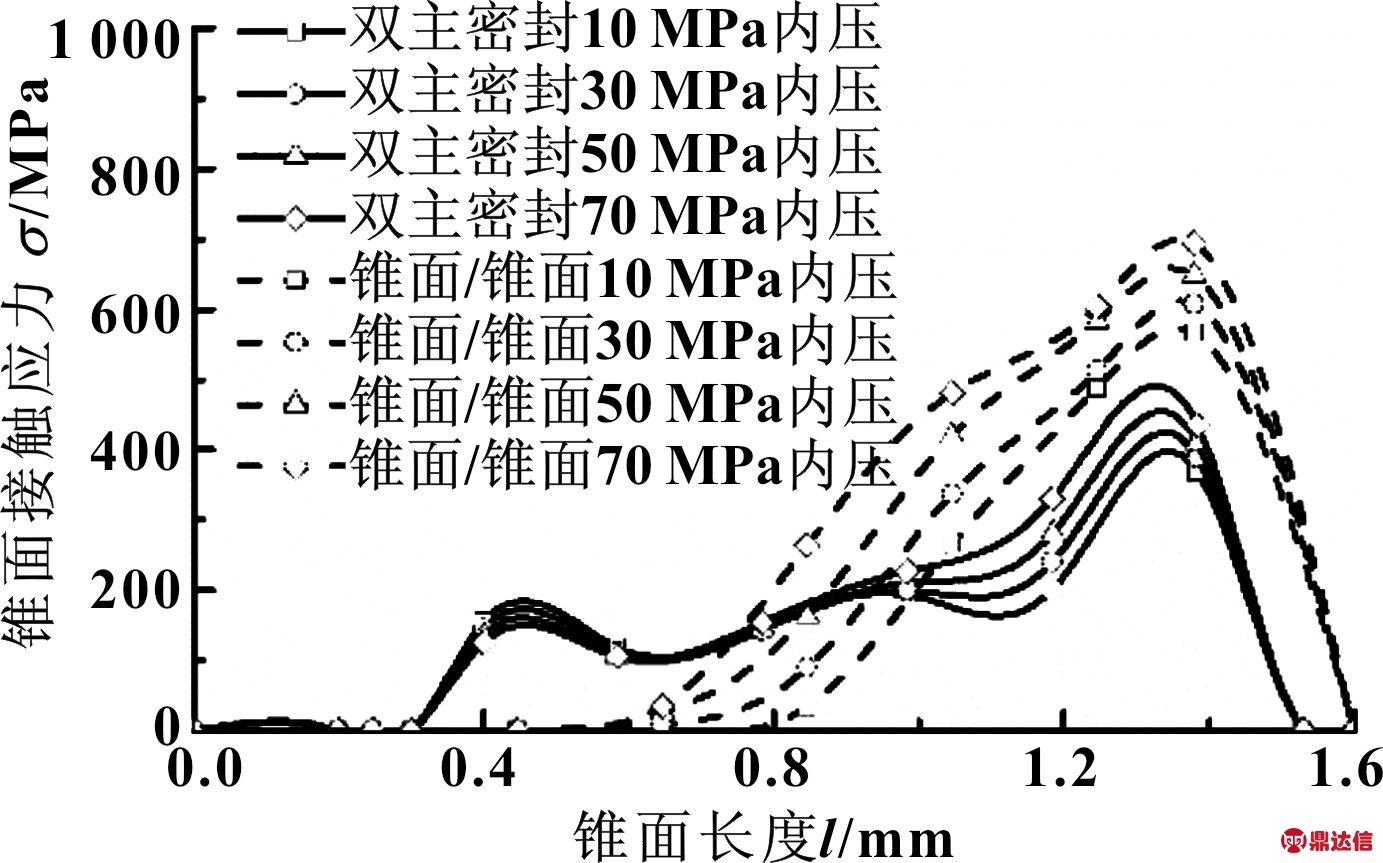
图12 拉伸载荷和内压作用下锥面接触应力分布
Fig 12 Distribution of contact stress on conical surface under tensile load and internal pressure
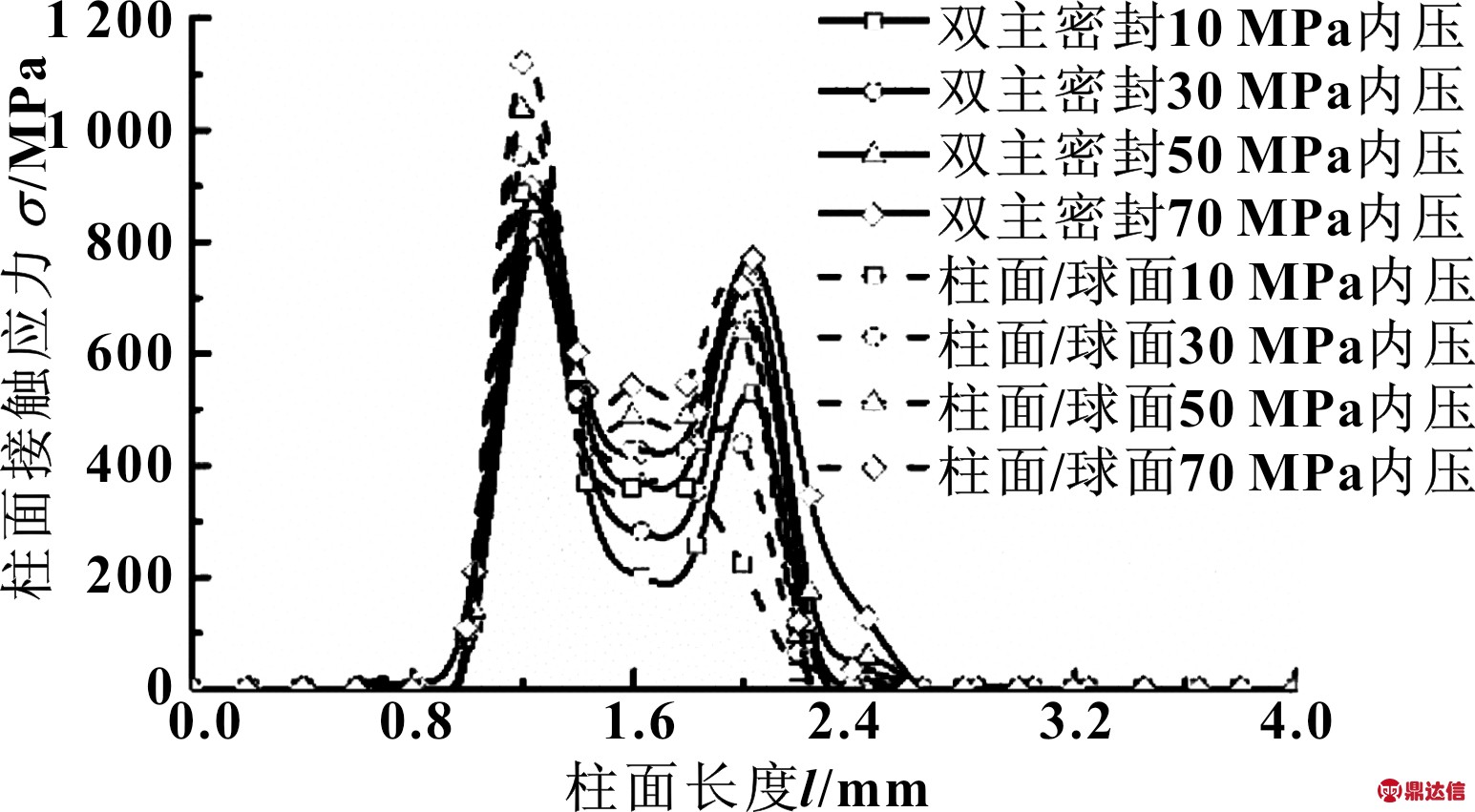
图13 拉伸载荷和内压作用下柱面接触应力分布
Fig 13 Distribution of contact stress on cylindrical surface under tensile load and internal pressure
由图12、13可知,单、双主密封结构锥面及柱面上接触应力和接触长度均随内压的增加而增大。在70 MPa高压下,双主密封锥面接触长度为1.2 mm,大于单主密封锥面的接触长度(0.95 mm),且最大接触应力为434 MPa,并未超过材料的屈服极限,而单锥面密封锥面上最大的接触应力为693 MPa,密封面较易发生黏结。在70 MPa高压下,双主密封柱面的接触应力峰值为900 MPa,低于单主密封柱面的接触应力峰值1 120 MPa。因此,双主密封接头在轴向拉伸和内压载荷共同作用下的密封性能是优于单主密封接头的。
4.5 轴向拉伸和内外压作用下密封性能分析
根据工况5的要求,对接头施加900 kN轴向拉伸载荷,同时对管体施加50 MPa的内压和外压,得到的不同密封结构密封面接触应力数据,将工况5得到的数据和工况4—9得到的数据按照锥面和柱面分别绘制到两张曲线图中,如图14、15所示。

图14 复合载荷下锥面接触应力分布
Fig 14 Distribution of contact stress on conical surface under compound load
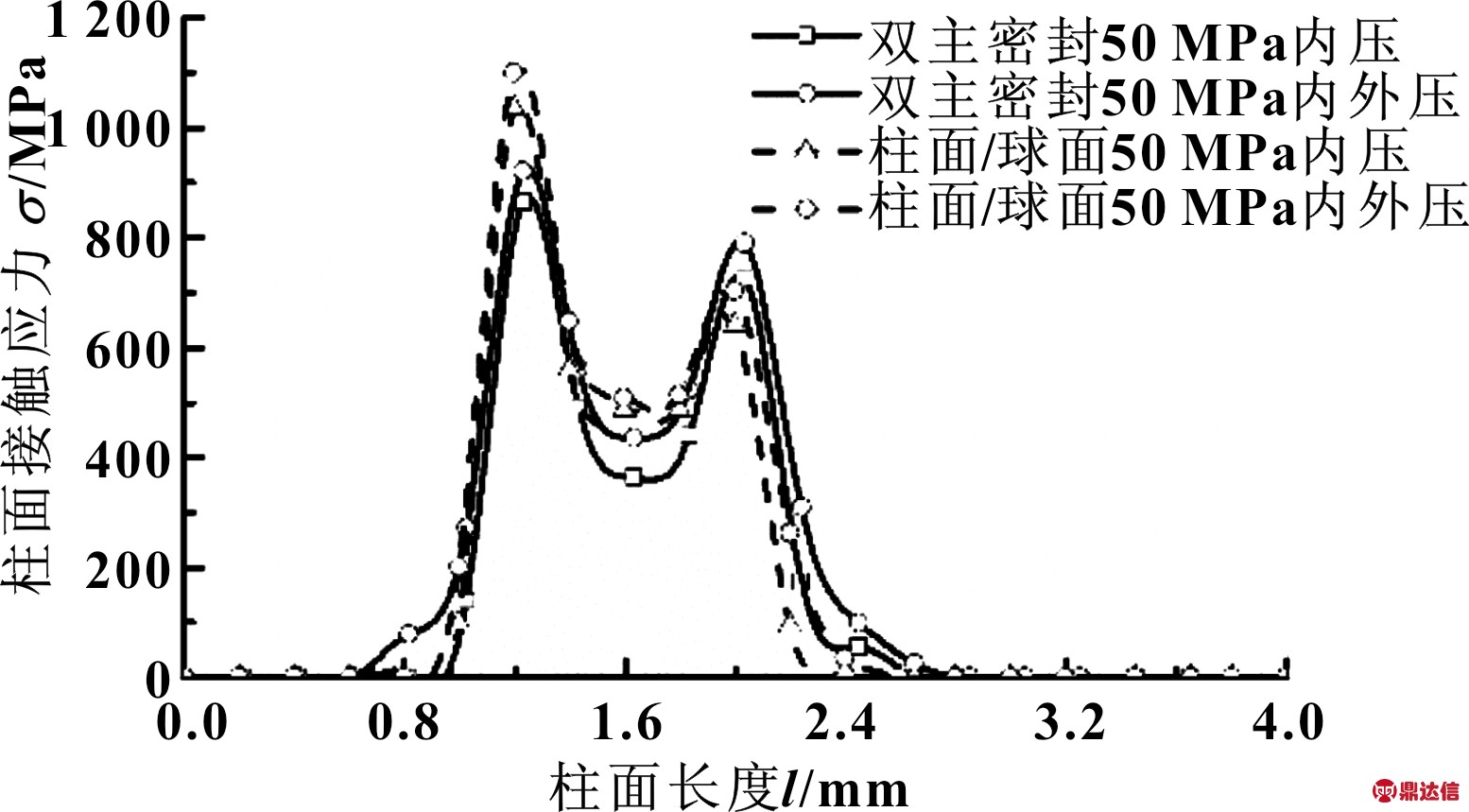
图15 复合载荷下柱面接触应力分布
Fig 15 Distribution of contact stress on cylindrical surface under compound load
由图14、15可知,单、双主密封接头锥面及柱面在外压作用下,密封面的接触应力和接触长度也在增大。在900 kN轴向拉力和50 MPa内外压复合载荷下,双主密封锥面接触接触长度(1.38 mm)约为单主密封锥面接触长度(1.16 mm)的1.2倍,其最大接触应力为450 MPa,远小于单主密封锥面接触应力峰值(698 MPa)。在该复合工况下,双主密封柱面接触应力极值为921 MPa,低于单主密封柱面接触应力1 100 MPa,其接触长度为1.8 mm,是单主密封柱面接触长度(1.4 mm)的1.29倍。综合来看,双主密封接头在轴向拉伸和内外压复合载荷下密封长度更长,应力峰值也较低,在保证优良密封性能的同时,发生黏扣的可能性也较低。
5 全尺寸试验
利用专用数控机床加工出了这种双主密封螺纹接头,随机选择3根试样进行气密封试验,试件的选择严格按照API RP 5C5标准[15]进行。
试验项目主要有螺纹参数检测、几何尺寸测量、上卸扣试验、气密封试验。将接头在液压大钳上进行10次循环上卸扣,然后依照API RP 5C5标准[15],对接头进行气密封试验。
试验结果表明,该接头密封面未出现黏结现象,同时气密封能力达到了API RP 5C5标准的要求,最大试验压力达到72 MPa。图16为试验后公接头试件的照片。目前该种双主密封螺纹接头处于研发试验阶段,技术成熟后将投入到油气井中使用。

图16 试验后试样形貌
Fig 16 The morphology of samples after testing
6 结论
(1)提出了一种新型的主密封结构——锥面对锥面和柱面对球面的组合密封。通过有限元分析可知,轴向拉伸载荷会显著降低主密封锥面的密封性能,对主密封柱面影响不明显;轴向压缩载荷在一定程度上可以提高主密封锥面的密封性能,会降低主密封柱面的密封性能;内压和外压在一定程度上可以增强密封面的密封效果,但是要防止密封面屈服失效。
(2)与单主密封结构相比,双主密封结构在上扣、轴向拉伸、轴向压缩、轴向拉伸+内压、轴向拉伸+内外压5种工况下,密封面的接触应力分布更加均匀,接触长度更长,且接触应力峰值较小,密封面不易产生黏接失效。综合来看,该双密封结构的密封性能优于单锥面对锥面密封和单柱面对球面密封结构。
(3)实物试验较好地验证了有限元分析的结论,证明该双主密封接头具有良好的抗黏扣性及气密封性能。