摘要:针对滚珠丝杠螺母内螺旋滚道型面参数较难测量的问题,展开对丝杠螺母内管道型面参数的自动化检测方法研究。在分析了测试要求后,提出了三种检测方案,分别是光谱共焦法、双频激光干涉法和改进型激光三角法。通过对三种检测方法的研究,分别进行验证性实验的设计,以及试验方案的验证,和误差的分析;最终从检测效果、可行性、经济性等方面对三种检测方法进行比较,结果表明最优秀的检测方案为激光三角法。
关键词:滚珠丝杠螺母;滚道型面;检测方法
0 引言
滚珠丝杠副是由丝杠、螺母、滚珠以及滚珠返向器等零件组成的机械部件,其作用是将旋转运动转换成直线运动或将直线运动转换成旋转运动[1]。滚珠丝杠副具有传动效率高、定位精度高、摩擦阻力小、使用寿命长、同步性能好等特点,广泛应用于精密数控机床、高精度机器人、精密测量仪器和各种工业自动化设备等的直线驱动执行单元中[2]。在滚珠丝杠副中,丝杠和螺母表面被加工成凹圆弧形成螺纹滚道,滚道之间放入滚珠形成滚动摩擦,滚珠在螺母内沿着螺旋滚道滚动并通过返向器构成循环,带动螺母沿丝杠轴向运动,构成滚动螺旋副。滚道的法向截形有两种:单圆弧截形和双圆弧截形。本文主要针对的是双圆弧滚珠丝杠副螺母内滚道型面检测方法的研究。
由于丝杠螺母的内径尺寸有限,普通传感器由于尺寸限制不能直接扫描测量螺母滚道,这是测量螺母内滚道型面最困难的地方。对此国内工厂多采用沿其法向截面剖开并投影的方法,但该方法破坏了螺母的整体结构,检测效率低,样品数量较少,不符合现代高精度、高效率、自动化的检测要求。对于接触式测量方法,何东明设计“内卡钳”式双测球螺母中径测量仪[3],杨凤岐采用光学卧式投影仪[4];对于非接触式测量方法,Zhimin RAO通过工业影像扫描获得螺纹参数[5],但是测量效率低,对环境要求高,成本高,不适合工厂采用。
本文针对螺母内滚道型面的检测方法进行研究,主要研究内容如下:①光谱共焦的检测方法的研究;②双频激光干涉的检测方法的研究;③激光三角的检测方法的研究;这三种方法都具有自动化、高速度、高精度测量的优点。最终从检测效果、可行性、经济性等方面对三种检测方法进行比较,选出最合适的检测方法。
1 螺母内滚道型面检测方法的研究
本文以双圆弧滚道截形的滚珠螺母作为研究对象,图1为双圆弧滚道的几何参数。
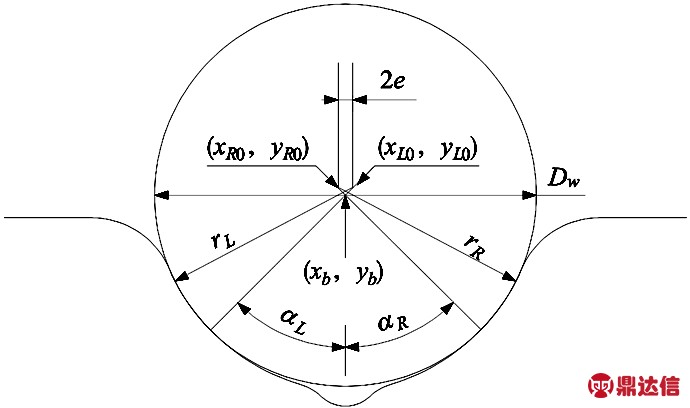
图1 双圆弧滚道几何参数
图1中,(xLO,yLO)和为rL左圆弧圆心与半径;(xRO,yRO)和rR为右圆弧圆心与半径;(xb,yb)为滚珠球心坐标,αL和αR为左右圆弧接触角;e为偏心距。
在测量过程中,获得螺母内滚道型面的轮廓图;通过对轮廓图的分割、拟合,获得左右圆弧圆心与半径。因此,左右圆弧半径的拟合结果误差成为评价测量效果的重要标准。
1.1 光谱共焦的检测方法
1.1.1 光谱共焦方案的设计
光谱共焦传感器具有体积小、测量精度高、对环境要求低和抗干扰能力强等优点,常用工件轮廓测量、角度测量和透明物体的厚度测量[6]。本方案可以采用德国米铱的DT IFS2402型光谱共焦微型探头采集滚珠螺母内滚道轮廓的高度值数据。
测量系统主要由内置白色LED光源的IFC2451型控制器、IFS 2402/90-10型径向测量的光谱共焦位移传感器和相关接线组成。传感器发出的激光光线到达螺母内滚道表面后,部门漫反射回来的光线被传感器所接收,再通过光纤传回传感器控制器,分析处理后得到位移值,控制器将计算结果输出到电脑上,图2为测量系统配置图。
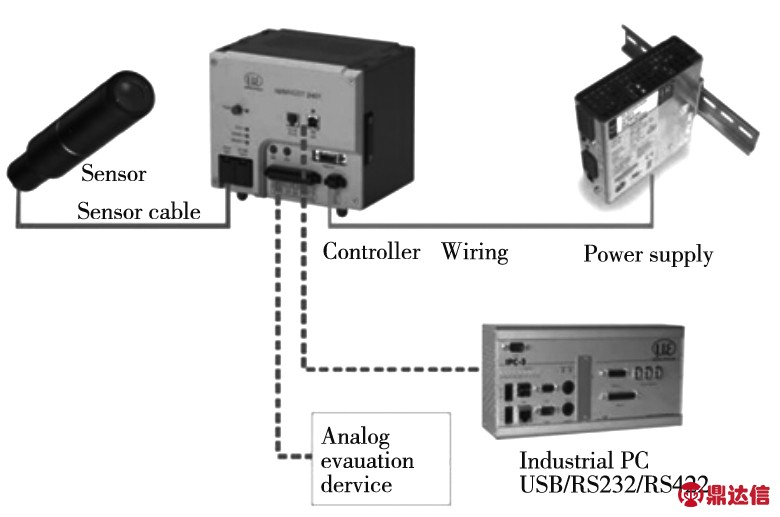
图2 测量系统配置图
1.1.2 光谱共焦法的实验验证
图3为滚珠螺母内滚道检测验证试验台示意图,实验台主要由测量组件、运动组件和支撑组件组成。其中测量组件主要包括光栅尺和光谱共焦位移传感器;运动组件包括手动平移台、电动平移台和电动旋转台;支撑组件包括定制光学平台、平移台底座、支撑块、定制转接板、三爪卡盘和传感器夹具等。实验台实物图如图4所示。
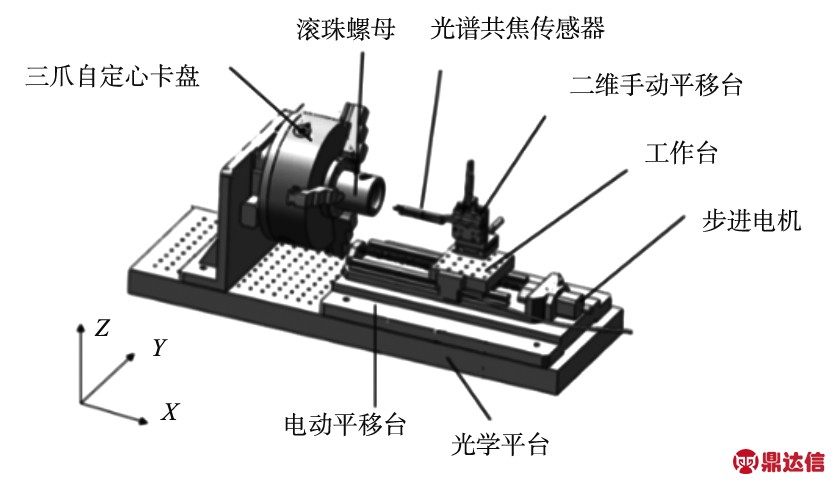
图3 采用光谱共焦传感器的螺母内轮廓检测系统示意图
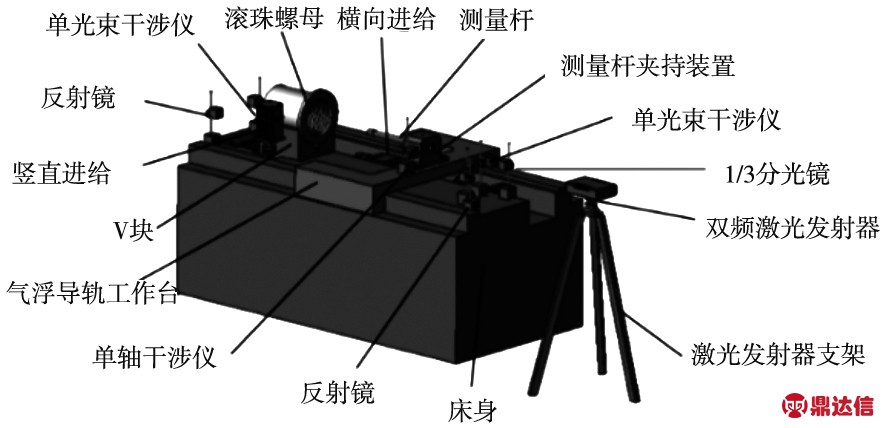
图4 实验台实物图
对获得的滚道螺纹轮廓数据截取滚道左右圆弧部分进行最小二乘拟合,左右圆弧轮廓部分约为60°,获得左右圆弧的圆心和半径。数据处理后结果如表1~表3所示。
表1 两个待测螺母的参数
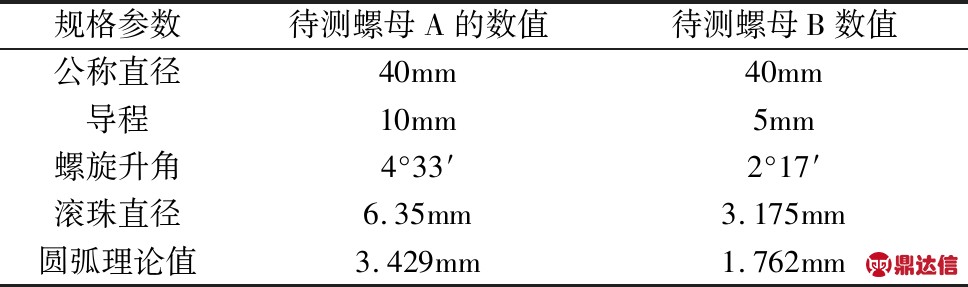
表2 拟合后螺母滚道左圆弧参数表

表3 拟合后螺母滚道左圆弧参数表

从表中可知,拟合后的圆弧半径和圆弧半径理论值存在较大误差,且数值波动较大,准确度较低。拟合精度叫低主要是因为传感器难以采集完整的轮廓数据,且实验装置很难将传感器调整到沿着螺母轴向界面扫描。因此难以选用该型号传感器测量。
1.2 双频激光干涉的检测方法
1.2.1 双频激光干涉方案的设计
激光干涉测量法作为一种非接触式测量方法,具有测量速度快、精度高、灵敏度高的优点,广泛应用于位移、平行度、速度等测量[7]。其中双频激光干涉仪测量系统结构相对复杂,但是它有较强的抗干扰能力,更容易实现高分辨率,适用于滚珠螺母内滚道检测[8]。
根据激光干涉原理,利用其测距功能并结合滚珠丝杠副螺母内滚道的特征,设计出以下利用激光干涉法测量螺母内滚道的方案,图5为方案的示意图。

图5 激光干涉法测量螺母内滚道方案示意图
采用一个单轴干涉仪A测量螺母的位移,其测量镜组为一面反射镜,安装在螺母运动平台上,相比较光栅尺具有精度更高,安装简单的优势,在本方案中,不需要单独为其提供光源,可以利用分光镜从双频激光发生器发出的光源中分出一部分即可。另外采用“单光束干涉仪B+探头B”和“单光束干涉仪C+探头C”,分别从两端伸入检测螺母内滚道的轮廓(探头B和C安装于测量杆内)。该方案完整的光路图,如图6所示。
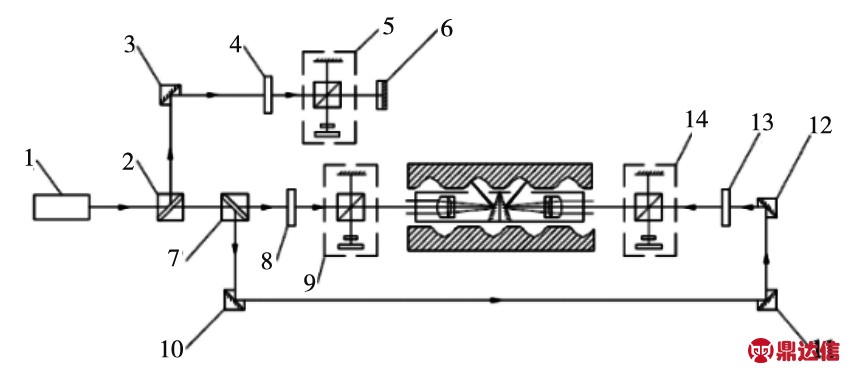
1.双频激光发生器 2.1/3分光镜 3.直角反射镜 4.1/4波片 5.单轴激光干涉仪 6.平面反射镜 7.1/2分光镜 8.1/4波片 9.单光束激光干涉仪 10.直角反射镜 11.直角反射镜 12.直角反射镜 13.1/4波片 14.单光束激光干涉仪
图6 激光干涉测量螺母滚道光路图
该测量方案设计的试验台主要由测量床身,进给系统和测量系统组成。测量时,先使用螺母夹持装置V块固定螺母,测量杆安装于气浮导轨工作台上,由滚珠丝杠副驱动从而实现横向进给,由双频激光发生器发射出的激光经过干涉仪到达反光镜,经过漫反射后返回的激光到达干涉仪,当测量杆运动时,由干涉仪可测得螺母内滚道的圆弧与反光镜中心的相对位移。测量时,通过进给系统调整V型块支撑平台竖直高度。图7为试验台总体结构图。
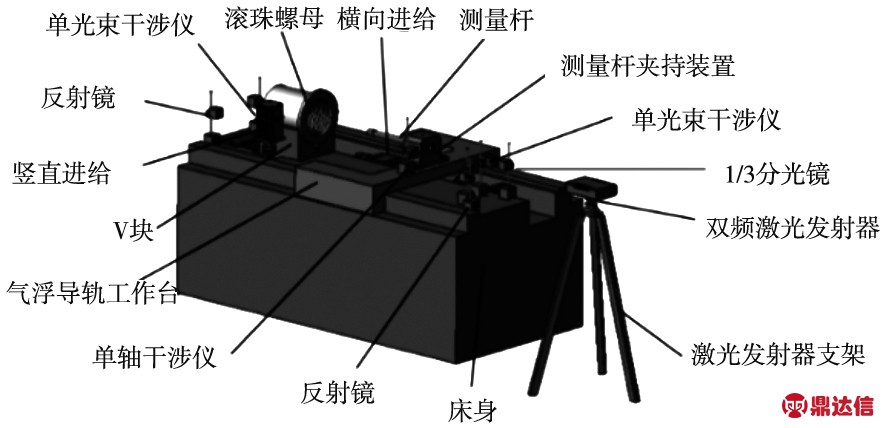
图7 激光干涉法试验台结构示意图
1.2.2 双频激光干涉方案误差分析
根据双频激光的性能,测量方案的主要技术指标分析如表4所示。
表4 激光干涉方案主要技术指标
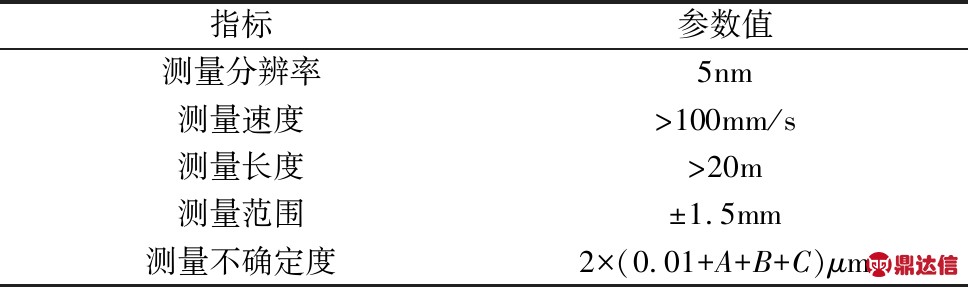
测量分辨率、速度和长度由双频激光光源本身所决定,测量范围主要由光程差决定,图8为激光在螺母滚道处的示意图,r12为光线1和光线2的光程差,r23为光线2和光线3的光程差,r13为光线1和光线3的光程差。
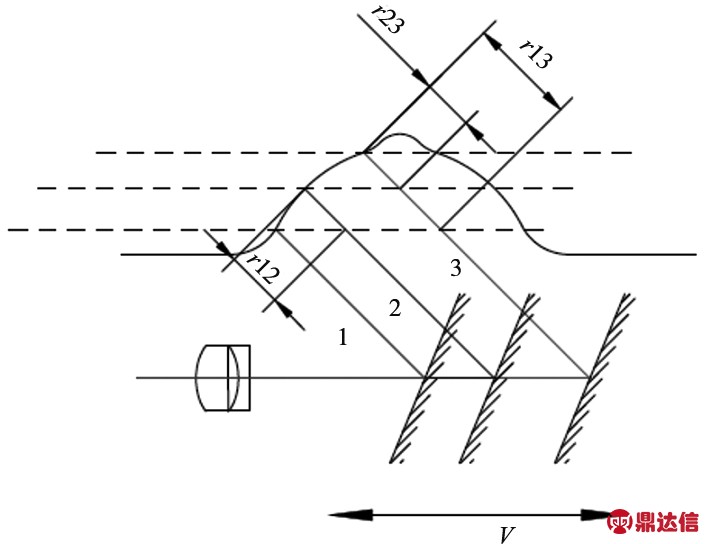
图8 激光在螺母滚道处的示意图
实际探头处为一束激光经过缩束器再由反射镜沿135°反射至螺母滚道上,呈圆锥形,示意图中简化了光束,以线条表示,由单光束干涉仪物镜设计可知,根据测量范围可以设计合适的焦距,但是焦距的增大会伴随着光斑的增大,影响分辨率和精度,进行精密测量时一般要求光斑不超过100μm。利用ZEMAX仿真出的结果在焦点前后移动1.5mm以内的距离,光斑都不会超过100μm,所以可以测量滚道深度在3mm以内的滚珠螺母。
测量不确定度主要由仪器误差、阿贝误差、余弦误差以及环境误差等几部分组成,上表中仪器制造误差为0.01μm。
A为阿贝误差,它是由于测量轴和运动轴不重合,而且被测对象产生倾斜而造成的误差,如图9所示。假设测量轴和运动轴间距为H,被测对象的倾斜角为θ,则阿贝误差为:
A=H×tanθ
(1)
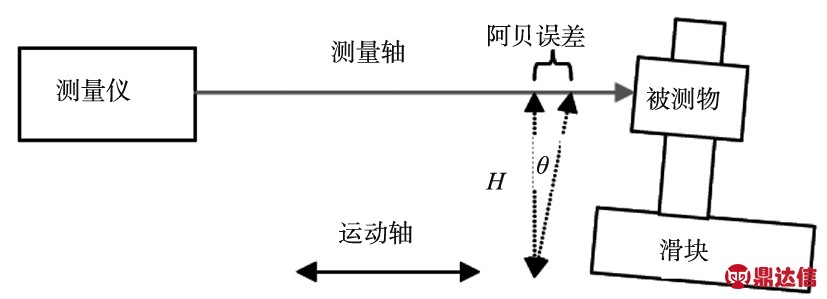
图9 阿贝误差示意图
本方案中H很小,假设为10mm,测头和被测对象产生相对夹角θ为0.01mrad,则阿贝误差为:
A=0.01m×tan0.01mrad=0.1μm
(2)
B为余弦误差,它是由于测量轴与运动轴存在夹角β而造成的误差,如图10所示。
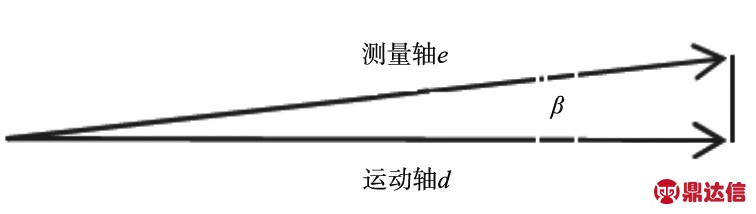
图10 余弦误差示意图
运动轴和测量轴的关系为:
d=e×cosβ
(3)
因此余弦误差为:

(4)
它是一个和测量距离d成正比的误差,假设d=0.5m,而夹角β=0.2mrad,则余弦误差为:

(5)
C为环境误差,主要是由温度变化引起的:
C=0.96×d×T
(6)
其中,0.96是温度变化对波长的影响系数;d为干涉仪到被测物之间的距离,单位m;T为环境温度变化量,单位为℃。
温度变化若能控制在0.2℃以内,测量距离d=0.5m,则该项误差为:
C=0.96×0.5×0.2=0.096μm
(7)
综上所述,则系统测量不确定度为:(0.01+0.1+0.05+0.096)×2=0.512μm
1.3 激光三角的检测方法
1.3.1 激光三角方案的设计
通过激光位移传感器发射聚焦的一束激光,在被测物体表面形成光斑,漫反射的光线被传感器接收透镜接收,然后由内置的光点探测器计算出传感器发射口与被测物体表面的距离[9]。激光三角法由于具有超高的再现性、超高的精度、超快的速度,广泛应用于精密零件测量领域[10]。激光三角方案的设计采用日本某公司生产的LK-H050型号聚焦光点型激光位移传感器。由于待测滚珠丝杠副螺母内径是 20~63mm尺寸级,而LK-H050型号传感器尺寸是70×70×35mm尺寸级,无法直接将传感器深入螺母内部扫描。为了解决此技术问题,可在光路中添加一块高反射率的三棱镜,在保证测量原理不变的情况下,可以成功测量内螺纹孔径的尺寸。改进光路后的激光三角法测量螺母内滚道的示意图,如图11所示。
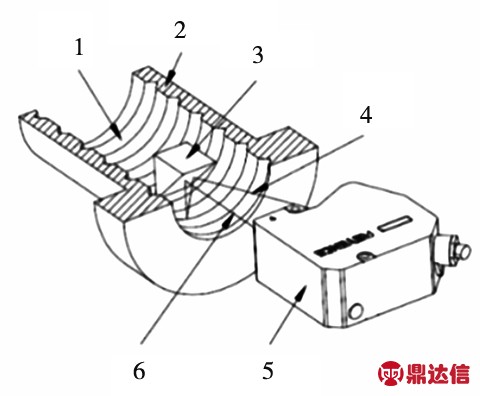
1.双圆弧滚道 2.待测螺母(剖视) 3.高反射率的三棱镜 4.接收光线 5.激光三角传感器 6.入射光线
图11 改进光路的激光三角法测量螺母内滚道
1.3.2 激光三角的实验验证
由于本实验和光谱共焦验证试验所需的运动和约束一致,且保持同一测量平台有利于更直观的发现不同传感器的测量效果,所以依然通过在原来试验台重新设计传感器工装和改写测量程序实现,如图12所示。
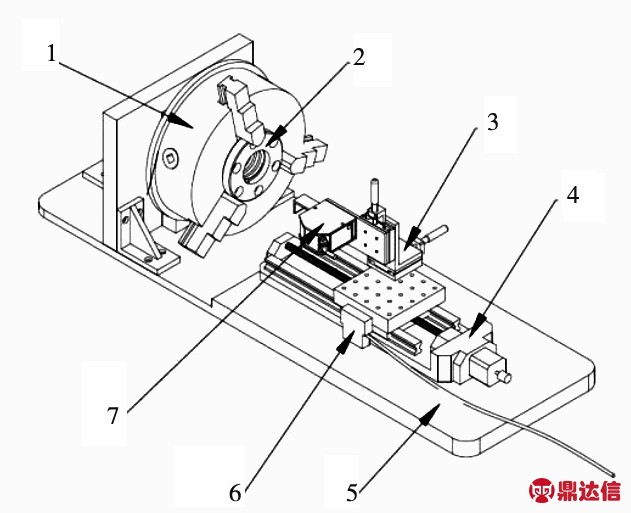
1.三爪卡盘 2.待测螺母 3.二维手动平移台 4.电动平移台 5.底座 6.贴片式光栅尺 7.激光三角传感器
(a) 试验台三维图
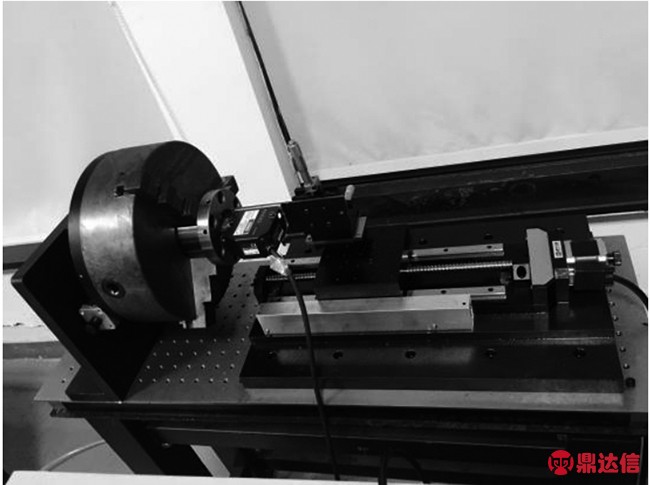
(b) 试验台实物图
图12 试验台三维模型图与实物图
在检测前,先用酒精擦拭干净滚道,避免油污或灰尘对测量的影响,接着将螺母装夹在三爪卡盘上,工控机指令驱动步进电机转动,使电动平移台以2mm/s的速度沿着X轴方向运动,此时X轴方向的位移由光栅尺采集,滚珠丝杠螺母内滚道的齿形表面的相对位移由激光三角传感器获得,将这两组数据保存至程序里,利用最小二乘法进行曲线拟合,便可实现对螺母内滚道轮廓的测量。
选用某厂生产的双圆弧型滚珠丝杠所配合的螺母进行测量,其规格:内径为42.4mm,导程为10mm,滚珠直径5.953mm,滚道圆弧大小未知。将测量系统采集的轮廓数据表格导入MATLAB计算,得到滚道圆弧参数和滚珠圆心坐标的计算结果,表5为滚道圆弧半径及滚珠圆心坐标。
表5 滚道圆弧半径及滚珠圆心坐标
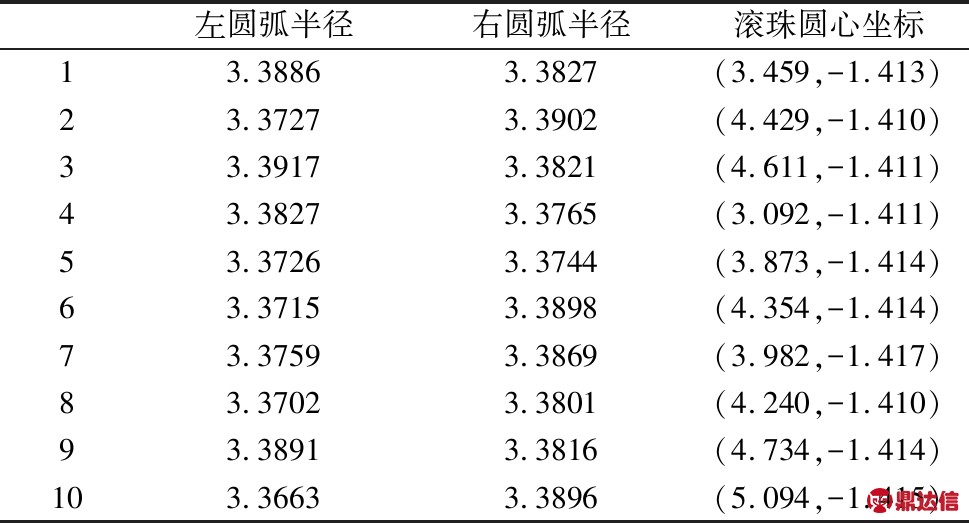
由上可知,滚珠圆心坐标是依据所拟合的左右圆弧坐标和半径计算获得,故左右圆弧的半径和坐标会直接影响滚珠圆心坐标的计算结果,同时,左右圆弧的检测也是螺母内滚道检测的重要内容,图13为本次试验测量的螺母滚道左右圆弧半径的变化趋势图。
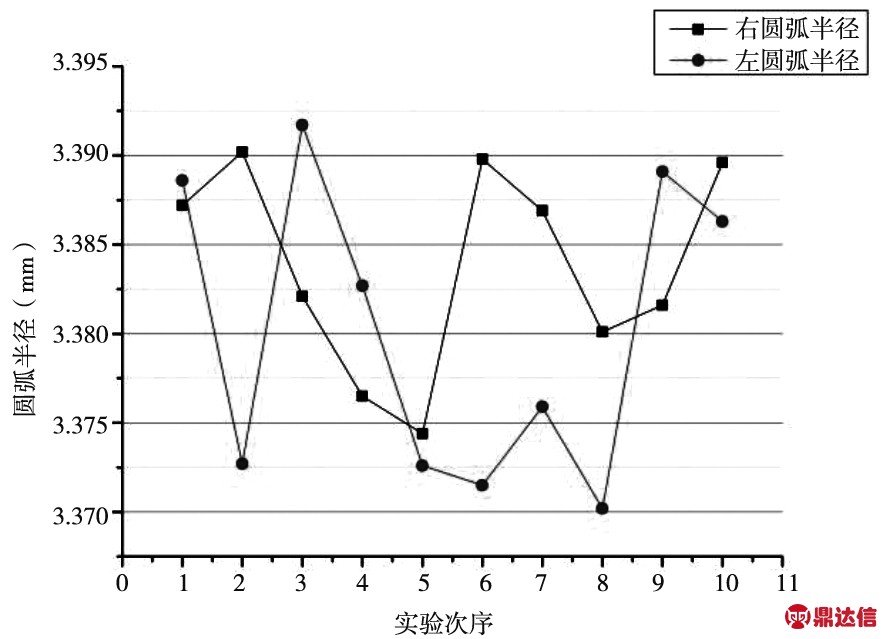
图13 左右圆弧半径测量结果变动趋势
计算出左右圆弧的标准差分别是:
SL=7.96×103;SR=5.43×103
可以看出,测量结果存在波动,但数据的完整性是很好的,其余的误差例如波动较大、同轴度不好、偏心误差等都可以通过设计机械结构和算法进行改善。该验证试验基本证明了激光三角法测量螺母内滚道型面的可行性与优越性,具有自动化快速测量的优点,同时具有非常高的测量精度。
2 结论
根据测量要求设计基于激光的非接触式滚珠螺母测量方法,分别是光谱共焦法、双频激光干涉法和改进型激光三角法。激光干涉法由于存在加工周期长、设计复杂、成本太高的缺点,且难以做验证试验,所以用于技术储备;光谱共焦法和激光三角法经过试验验证,都具有自动化快速测量的优越性,但是激光三角精度明显更高,达到了5μm,符合现代化工厂测量的需求;因此激光三角法更适用于圆弧滚道的测量。