摘 要:为提高设计工艺的车间生产可执行性,在分析典型机械加工车间制造资源状态信息的基础上,针对非线性工艺规划的资源优化配置这一多目标优化问题,通过合理假设和定义,结合对制造资源状态的定量分析,建立了以最短加工时间、最低加工成本和最优制造资源状态为目标的非线性工艺规划资源优化配置模型。利用染色体分层编码遗传算法求解模型,实现了最优工艺路线和资源配置方案的同时生成。给出了工程应用案例,验证了所建立的非线性工艺规划资源优化配置模型的有效性及求解方法的可用性。
关键词:制造资源状态;非线性工艺规划;资源优化配置;多目标优化;遗传算法
0 引言
关于制造资源,广义概念认为它是企业完成产品整个生命周期所有生产活动的物理元素的总称,狭义概念认为它是加工一个零件所需要的物质元素[1]。随着环境的变化,新的制造模式不断出现,很多学者针对不同环境、不同目的的制造资源建模开展研究,制造资源模型已经从面向单一信息化应用系统发展到面向不同信息化应用系统,支持产品全生命周期应用[2-3]。
工艺规划设计作为联系产品设计和制造的纽带,是资源与任务相结合的过程。目前机械加工企业利用计算机辅助工艺规划(Computer Aided Process Planning, CAPP)系统开展工艺规划设计时大都基于自身的制造资源环境,并假定制造资源是静态、无限的,任何时间都是空闲的,因此工艺设计时主要考虑制造资源的技术实现能力,习惯选择精度高、效率高的资源,为每个零件生成单一、固定的工艺路线。然而,车间制造资源是有限且动态变化的,传统的车间生产调度往往在工艺规划设计之后执行,自然受到设计工艺的约束。工艺规划设计时对制造资源状态信息考虑的不足,降低了工艺路线在实际生产中的可执行性。为了充分利用现有的制造资源提高车间生产调度的灵活性,工艺规划与车间调度的集成很有必要,国内外对此开展了广泛的研究,提出的集成模型大致可归纳为非线性工艺规划、闭环式工艺规划和分布式工艺规划三类[4-5]。其中,非线性工艺规划是实现集成的基本模型,现有研究大都在其基础上进行改进。非线性工艺规划包含多种可能的加工方案,是任何全部或者部分具有可替代项的工艺规划的统称,而可替代项可以是整个加工工艺、加工序列或者加工设备。由于企业中同一类型或者同一型号的设备往往不唯一,非线性工艺规划产生的柔性工艺路线以及工艺路线中的工序会带来不同的可用制造资源选择。
工艺规划设计中的制造资源优化配置是个经典问题,研究较多且比较深入,如果制造资源优化配置时考虑状态的约束,则可大大提高工艺路线的实际生产可执行性,因此需要对状态信息进行量化分析。状态信息是制造资源信息的重要组成部分,然而受使用目的不同、制造资源多样性、状态信息采集手段的多样性、信息的异构性以及分析处理方法的差异性等众多因素制约,目前有关制造资源状态信息建模的研究较少,大都围绕信息内容的形式化描述和表达方法展开[6-10]。因此,针对状态信息,难以对其进行精确的定量计算和分析,通常采用定量和定性相结合的方法,如层次分析法、灰色关联法、人工神经网络等[11-14]。具体到非线性工艺规划的资源优化配置,尽管已有少量研究考虑到了制造资源状态约束[11-13],但其本质与传统的工艺规划制造资源优化配置研究区别不大,仍是在制造资源能力的约束下,重点针对工艺规划设计阶段以及关键工序的制造资源进行选择。鉴于非线性工艺规划模型是为实现工艺规划与生产调度的集成而提出,在进行制造资源优化配置时除了考虑制造资源状态约束外,还应考虑工艺路线和制造资源配置方案对生产调度的影响,然而现有研究对此考虑不足。
本文针对现有非线性工艺规划资源优化配置研究的不足,在相关研究的基础上首先讨论了工艺规划设计阶段制造资源配置所受的能力约束和状态约束,分析了典型机械加工车间的制造资源状态信息;然后通过一系列假设和定义,结合对制造资源状态的量化分析和相关优化目标,建立了非线性工艺规划资源优化配置模型,并利用染色体分层编码遗传算法求解模型。最后结合具体工程应用,验证了所建立的非线性工艺规划资源优化配置模型的有效性及求解方法的可用性。
1 机械加工车间制造资源状态信息
非线性工艺规划的制造资源优化配置不仅要考虑制造资源能力约束,还要考虑制造资源状态约束。关于制造资源能力和制造资源状态,目前尚无统一的区分标准。在传统的工艺规划制造资源配置研究中,通常认为制造资源能力反映了制造资源胜任某项任务的技术条件(可加工尺寸范围、可加工重量范围、可加工材料、可加工特征、加工精度、加工表面粗糙度等),在时间域上相对稳定;制造资源状态信息主要反映制造资源运行过程中的使用状况,是制造资源的动态属性[15]。然而,也有研究将制造资源状态视为能力的组成内容[16],因为制造资源的能力会随着状态的变化而变化,制造资源状态反映了能力在特定时间内是否可用。因此,具体的制造资源能力和状态区分应根据使用目的和要求来决定。本文将制造资源能力视作制造资源的静态属性,重点研究制造资源状态对非线性工艺规划设计的影响,因此需要对影响制造资源配置的状态信息进行分析。
为改变毛坯的形状、尺寸和表面质量等特性,获得合格的机械产品零件,工件往往会在不同的机床设备、生产线、车间乃至企业间加工流转,因此本文采用广义的制造资源概念,围绕制造资源的操作权限和合作层次展开,将制造资源划分为车间层、生产单元层、设备层三层。具体到机械产品零件的加工制造过程,只有加工设备和相应的工艺装备结合并相互作用才能产生所需的加工生产能力,然而工艺装备中的大多数刀具、夹具、量具等往往并非为某一台加工设备专用,而是按照加工任务需求在车间合理分配。因此,加工设备是工艺生产能力的实现主体,本文在进行非线性工艺规划资源优化配置研究时仅讨论加工设备资源。
车间层制造资源状态信息主要是使车间管理人员从宏观上了解车间运行状况,包括车间运行起止时间、故障生产单元或加工设备、加工设备故障停机时间统计、订单完成情况等。
生产单元由功能相似的一组机床组成,或者由一组按照产品生产流程组合、可完成一种或几种产品加工的不同功能机床组成。为提高车间制造资源的利用率,生产单元中的加工设备可以独立工作,而将车间内不属于任何生产单元的加工设备视为共同组成的一个特殊的生产单元。生产单元层的制造资源状态信息主要包括生产单元的工作起止时间、无故障工作时间、故障停机时间、生产零件数、计划工作时间、闲置加工设备和故障加工设备等。
设备层的制造资源状态信息最详尽,主要包括制造资源的使用状态信息、生产任务执行信息和性能状态信息。使用状态信息包括开启、闲置、维修、封存、保养等;生产任务执行信息包括加工任务序列以及相应的计划工作时间、正常工作时间、生产任务执行中的故障时间、加工完成的总零件数、总合格零件数等;性能状态信息包括生产任务执行过程中加工设备的主轴转速、主轴负载、机床温度、运动轴进给速度等。
2 非线性工艺规划资源优化配置模型
2.1 模型假设
非线性工艺规划生成工艺的过程可分为技术分析和资源配置两个阶段[17]。在技术分析阶段,仅根据产品的设计要求,讨论加工技术的可行性和所需要的加工能力,不涉及制造资源和时间的可用性。在资源配置阶段,非线性工艺规划的制造资源备选问题主要包括:①为产品设计多条符合技术要求的工艺路线,工艺路线的多样性带来了制造资源选择的多样性;②在工艺路线确定的条件下,每一工序有多种制造资源的选择可能。因此,非线性工艺规划的制造资源优化配置问题最终落脚在一个共性问题,即一种加工方法对应多个可选制造资源时,如何选择最优的制造资源。
结合本文引言对现有非线性工艺规划资源配置问题的分析,非线性工艺规划的资源优化配置不仅需要考虑制造资源状态的约束,还需要考虑资源配置对生产调度的影响,因此本文在研究非线性工艺规划的资源优化配置问题时进行以下假设:
(1)每个加工设备在同一时刻只能处理一道工序。
(2)同一个零件的不同工序不能同时被加工。
(3)当一个零件的一道工序完成后,如果需要运送到下一台加工设备处理下一道工序,则运输时间忽略不计。
(4)进行工艺设计的零件之间相互独立,没有优先级差别。
(5)加工设备的准备时间与工序顺序没有关系,工序的加工时间包含加工设备的准备时间。
(6)一批零件完成工艺设计后同时投放到车间,各零件的柔性工艺路线涉及的加工设备能力足够并可用,且从同一时刻开始。
2.2 模型的数学表达
根据非线性工艺规划的特点和研究假设,首先进行以下定义:
定义1 设CAPP系统进行N个零件(可以存在相同零件)的工艺设计,其中零件i有Li条可选工艺路线,Gi表示零件i的可行工艺路线的集合,Gi={Gi1,Gi2,…,Gij,…,GiLi},i=1,2,…,N,j=1,2,…,Li。
定义2 设零件i的可行工艺路线Gij的工序数目为Uij,用oijk表示可行工艺路线Gij中的第k个工序,Gij={oij1,oij2,…,oijk,…,oijUij},k=1,2,…,Uij。
定义3 设车间共有U个加工设备,它们组成了工艺规划进行资源配置的车间加工设备资源集合DEV,DEV={M1,M2,…,Ml,…,MU},l=1,2,…,U。
定义4 设Rijk表示零件i的可行工艺路线Gij中第k个工序的备选加工设备资源集合,用mijk表示备选加工设备资源集合中加工设备的数目,Rijk={MDev1,MDev2,…,MDevg,…,MDevmijk},其中g=1,2,…,mijk,Devg∈[1,U]。
定义5 设Mw是工序oijk执行所选用的加工设备,Tijkw表示工序oijk在可选加工设备Mw上的加工时间,表示该工序的开始加工时间点,其中Mw∈Rijk,w∈[1,U]。
定义6 设Cijkw表示工序oijk在其执行加工设备Mw上的单位时间加工成本。
传统的工艺规划设计优化问题通常将加工时间、质量、成本作为主要的优化目标,且已有大量文献对其进行研究,本文在此首先选取最小化加工时间和最低加工成本作为资源配置的优化目标,相应的资源优化配置模型表达如下:
(1)零件在加工设备上的完工时间T最小:

(1)

由于同一个零件的不同工序不能同时被加工,存在约束



由于每个加工设备在同一时刻只能处理一道工序,还存在约束



(2)零件的总加工成本C最小:
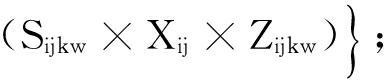

(2)
式中:;
,
;


如果给定零件的工艺路线选择、资源配置方案以及生产调度规则或方法,则上述两个优化目标均可定量计算。然而,车间制造资源状态的优劣难以准确评判,为此本文提出加工设备综合状态评价值的概念。基于本文对典型机械加工车间制造资源状态信息的分析,加工设备综合状态评价值指综合考虑加工设备自身详细状态DS、加工设备所属生产单元层状态CS、加工设备所属车间层状态FS所得到的加工设备状态量化评价值。如果要对一批零件加工选用的全部加工设备综合状态进行评价,则需首先获得单台加工设备的综合状态评价值。基于前述假设和定义,用Sijkw表示工序oijk选用的加工设备Mw的综合状态评价值。借鉴现有研究,本文通过基于层次分析法的二级模糊综合评判方法[18] 计算获得Sijkw。求解Sijkw时,一级评价为总目标(加工设备综合状态最优),二级评价为DS,CS,FS三个指标,各指标包含的评价因素及值的计算公式如表1所示,相关状态参数可由车间生产管理的相关信息化应用系统采集获得。
表1 加工设备状态综合评价所使用的指标及其评价因素
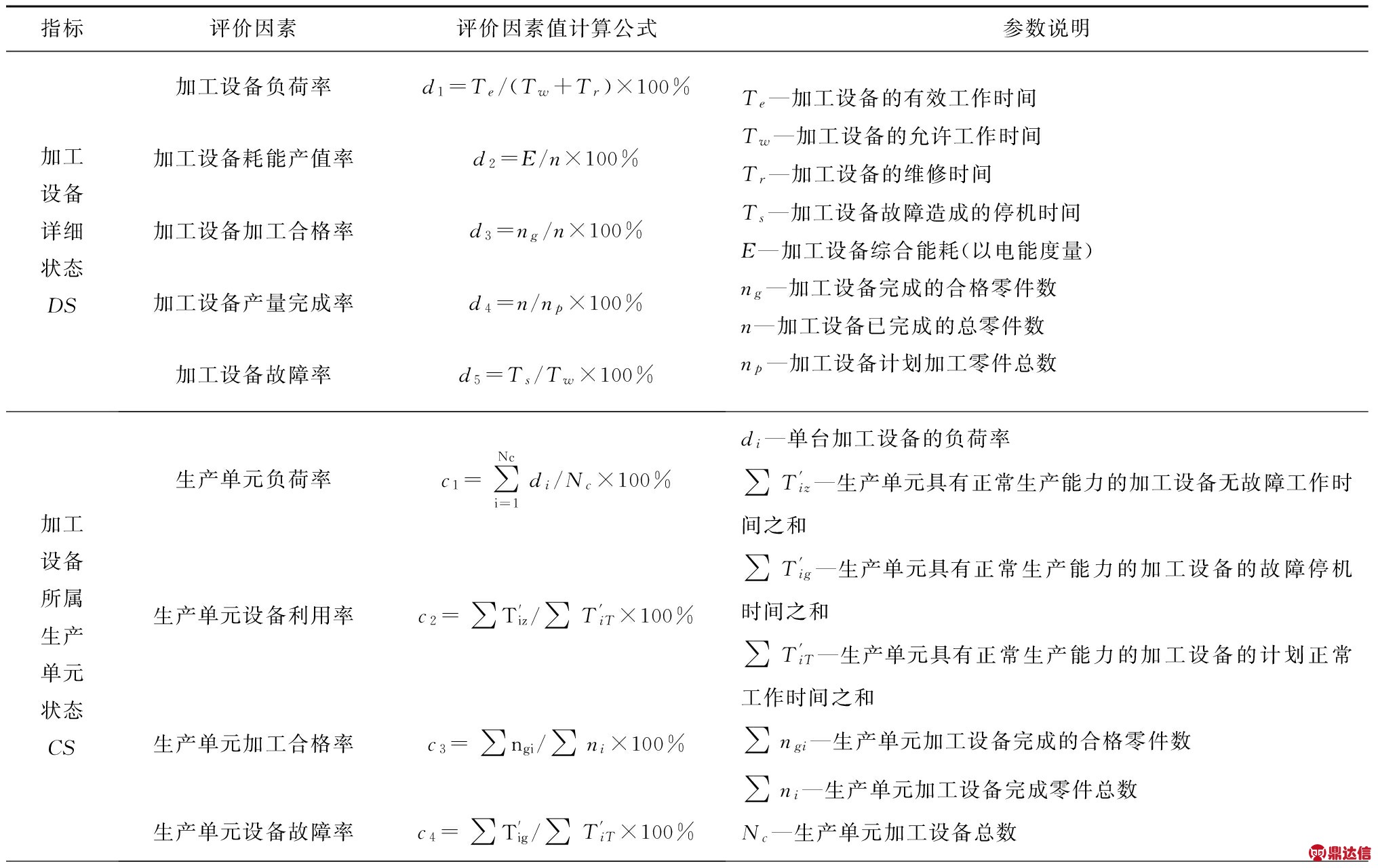
续表1
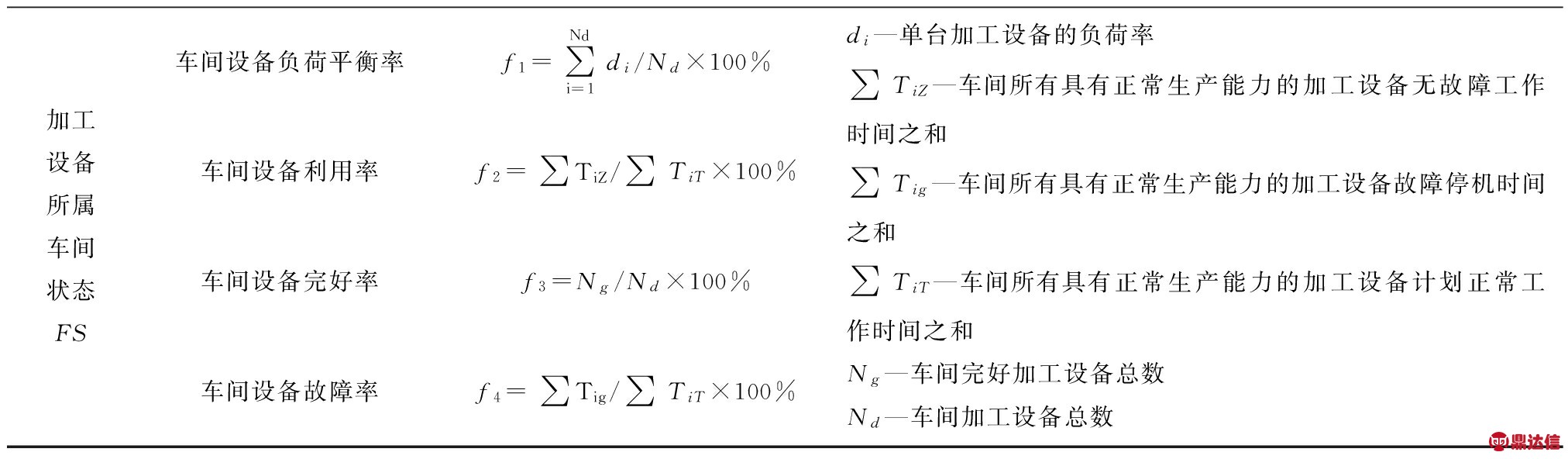
模糊性语言所表达的不确定评价信息通常采用模糊数进行描述,模糊数的形式有很多种,本文采用常用的三角模糊数对模糊语言集进行转化。表1中各指标评价因素的三角模糊数论域以及与其对应的隶属函数可基于车间历史监控和生产数据统计获得。单台加工设备综合状态评价值Sijkw详细的计算过程可参考文献[18],此处不再赘述,计算得到的Sijkw∈[0,1]。
通过对加工设备状态进行量化分析,将车间各加工设备的状态作为约束条件,本文建立的资源优化配置模型的另一优化目标为零件加工使用的加工设备综合状态评价值S最高,即

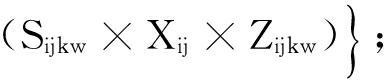
(3)


多目标优化问题通常转化为单目标优化问题求解,本文采用常用的线性加权和法(即根据各目标的重要性赋予相应的权重系数,然后对其进行线性组合)将建立的非线性工艺规划资源优化配置模型转化为单目标优化模型。然而,不同目标的取值范围和量纲常常不同,因此在加权求和之前须先对各优化目标做统一量纲处理。设Tend为本批零件的车间生产完成周期,Call为相应的加工成本限额,则转化后的单目标优化模型为:
。
s.t.


(4)
式中β1,β2和β3为加工时间、成本、加工设备状态三个单目标函数的权值,可通过专家打分法、德尔菲法或层次分析法等方法确定。
3 非线性工艺规划资源优化配置模型的求解
多目标优化问题往往不存在唯一的全局最优解,求解是寻求Pareto解集的过程。借鉴生命科学与信息科学的发展而形成的智能优化算法(进化算法、粒子群算法、蚁群算法等)通过模拟生物进化和群体动物活动等生命特征,运用迭代计算实现对多目标优化问题的求解,而非单纯地从数学的推导演化中寻求Pareto最优解,因此越来越广泛地应用于多目标优化问题的求解。针对建立的非线性工艺规划资源优化配置模型,本文利用染色体分层编码遗传算法[19]对模型进行求解。
3.1 遗传算法设计
3.1.1 基因编码的设计
由式(4)可知,T,C,S各单目标函数的取值是非线性工艺规划资源优化配置模型的决策变量,它们直接构成了模型的解空间。根据式(1)~式(3),T,C,S由零件加工工艺路线、工序工时、工序所选加工设备的属性信息(静态的单位时间加工成本、动态的综合状态评价值)决定,因此非线性工艺规划资源优化配置模型的解空间与零件加工工艺路线、工序工时、加工设备信息组成的搜索空间存在映射关系。
采用遗传算法求解非线性工艺规划资源优化配置模型时,将零件加工工艺路线、工序工时、加工设备的单位时间加工成本以及综合状态评价值这些搜索空间信息编码记录在基因上,组成种群个体的染色体,个体基因型到个体表现型的变换就是获得解空间中可行解的过程。采用基于工序的编码方法,染色体上的每个基因代表一道工序。将搜索空间的信息进行分层处理,则每个染色体基因所包含的工序相关信息表示为(p,g,m,t,c,s),其中:p表示零件序号;g表示零件可选工艺路线的序号;m为加工设备的唯一标识号;t表示工序加工时间;c表示加工设备的单位时间加工成本;s表示加工设备的综合状态评价值。任一加工设备除用自身唯一的标识号标记外,还可以用唯一的(x,y,z)编码表达,其中:x表示加工设备对应的可选车间序号,y表示加工设备隶属的生产单元在所选车间的生产单元序号,z表示加工设备在所属生产单元的序号。以x,y和z为控制码可访问各层状态信息,计算各状态相关评价因素的值后,采用基于层次分析法的二级模糊综合评判方法即可得到各加工设备的综合状态评价值。
种群个体的染色体能表达N个零件选择的工艺路线及其工序内容,故染色体应由Xij×Uij个形如(p,g,m,t,c,s)的基因组成,其中
,且
Xij=1。
假设零件i选择的工艺路线在零件可选工艺路线集合中的序号为l,其包含的工序数为Uil,则在染色体中同时满足p=i和g=l的基因应出现Uil次,从左向右扫描染色体,第k次出现同时满足p=i和g=l的基因即表示零件i的第k道工序。鉴于不同零件不同工艺路线的工序数目可能存在不同,为方便遗传算法的交叉、变异操作,将种群个体的染色体长度统一化。对于N个零件,设工序数目最多的工艺路线有Umax道工序,即Umax=max{Uij},i∈[1,N],j∈[1,Li],当染色体的编码长度达不到N×Umax时,给染色体编码最后补(0,0,0,0,0,0),直至染色体长度为N×Umax。以表2所示的零件可选工艺路线为例,假设它们涉及的加工设备的车间组织结构及相关属性如图1所示,则种群中某个体的染色体编码设计以及加工设备综合状态评价值这一重要基因信息的获取方法如图2所示。
表2 三个零件的可选工艺路线
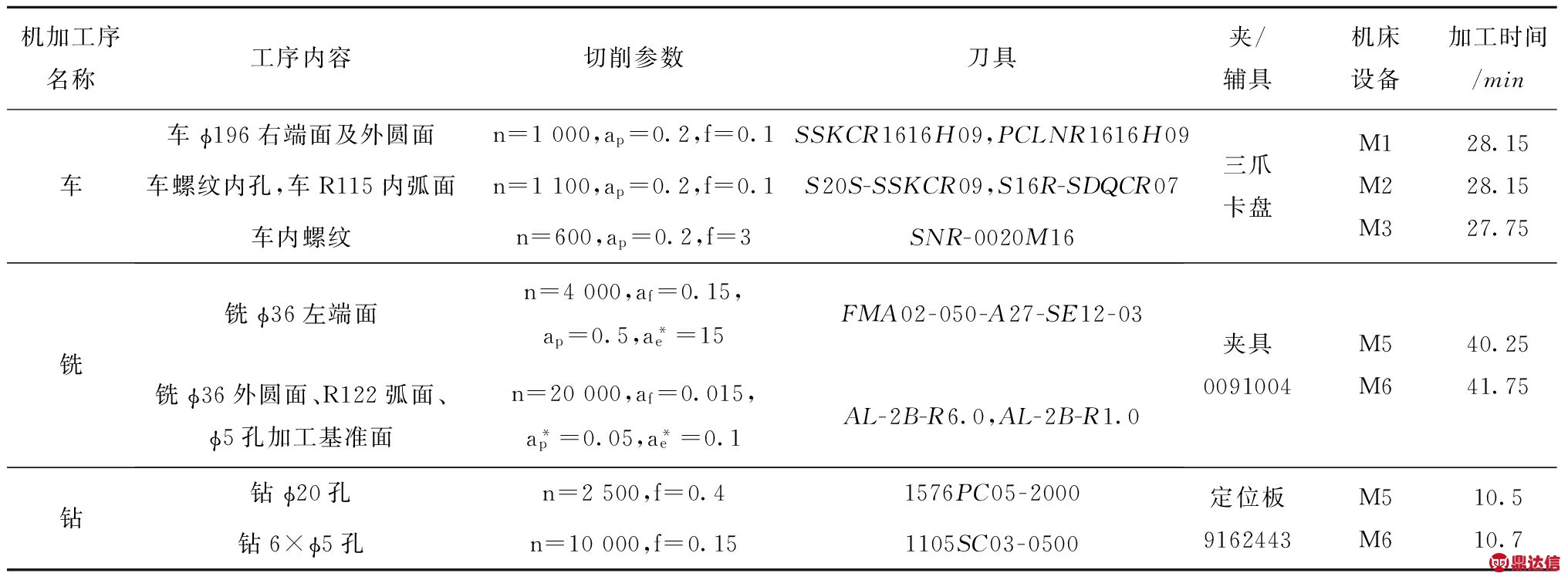
3.1.2 基因解码
解码计算一批零件在加工设备上的完工时间T,需要提取染色体基因零件层、生产设备层和工序加工时间层的信息(即p,m,t的值)。基于模型假设,本文在不改变加工设备上零件加工顺序的生产调度规则的前提下求解T,步骤如下:
步骤1 提取染色体基因信息,获取相应的零件加工工序序列、加工设备序列和加工时间序列,确定每一个零件加工使用的加工设备集合和每一台加工设备加工的零件工序集合及工序顺序。
步骤2 得到零件加工工序序列中每个工序的可行开始加工时间,默认前一工序的结束时间就是后一工序的开始时间,首工序的开始时间为0。
步骤3 获取加工工序序列中首工序的可行开始加工时间ta和加工设备,检查当前工序执行之前加工设备的忙碌时间区域(如果无,则记为0),获得各忙碌时间区域的结束值,进而得到其中的最大值TB。将ta与TB进行比较,如果TB≥ta,则当前工序的实际开始时间tf≠ta,tf=TB;否则tf=ta。然后更新加工工序序列中剩余工序的可行开始加工时间和执行当前工序的加工设备忙碌时间,并记录当前工序的实际开始时间和结束时间。同理,循环分析直至加工工序序列的最后一个工序。
步骤4 得到每个零件每个工序的开始加工时间和结束加工时间集合后,一批零件在加工设备上的完工时间T等于各零件最后一道工序结束加工时间的最大值。
解码计算一批零件的总加工成本C,需要提取染色体基因工序加工时间层和单位时间加工成本层
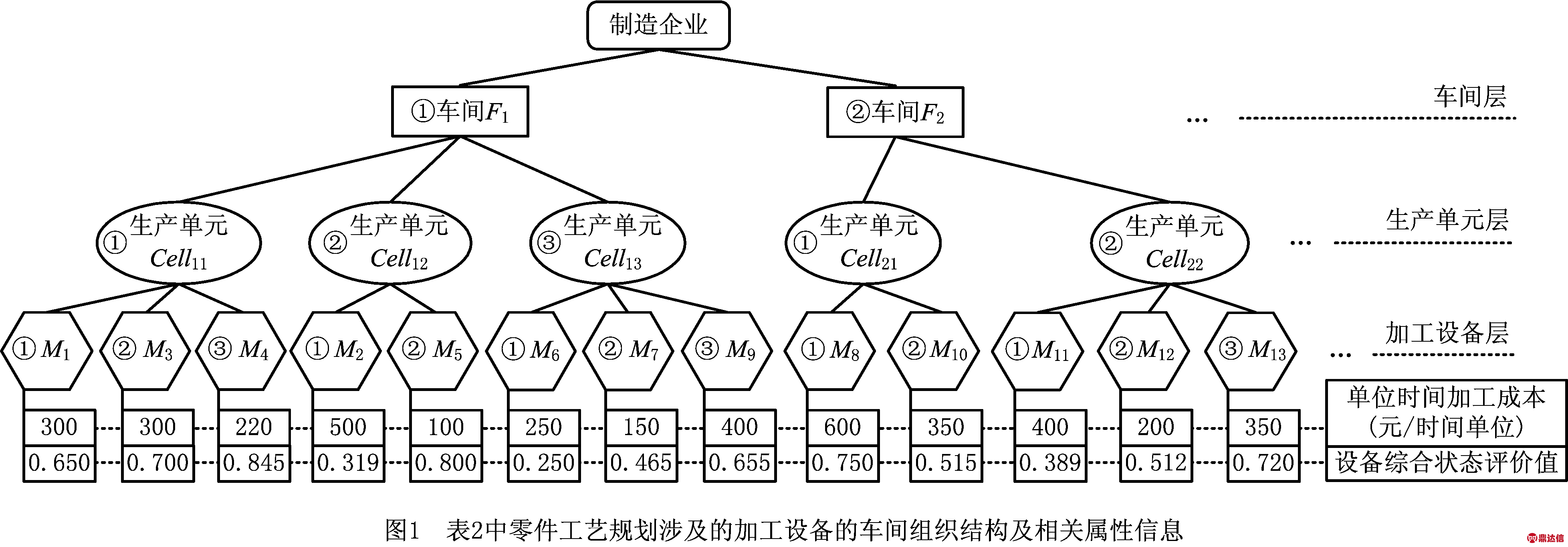
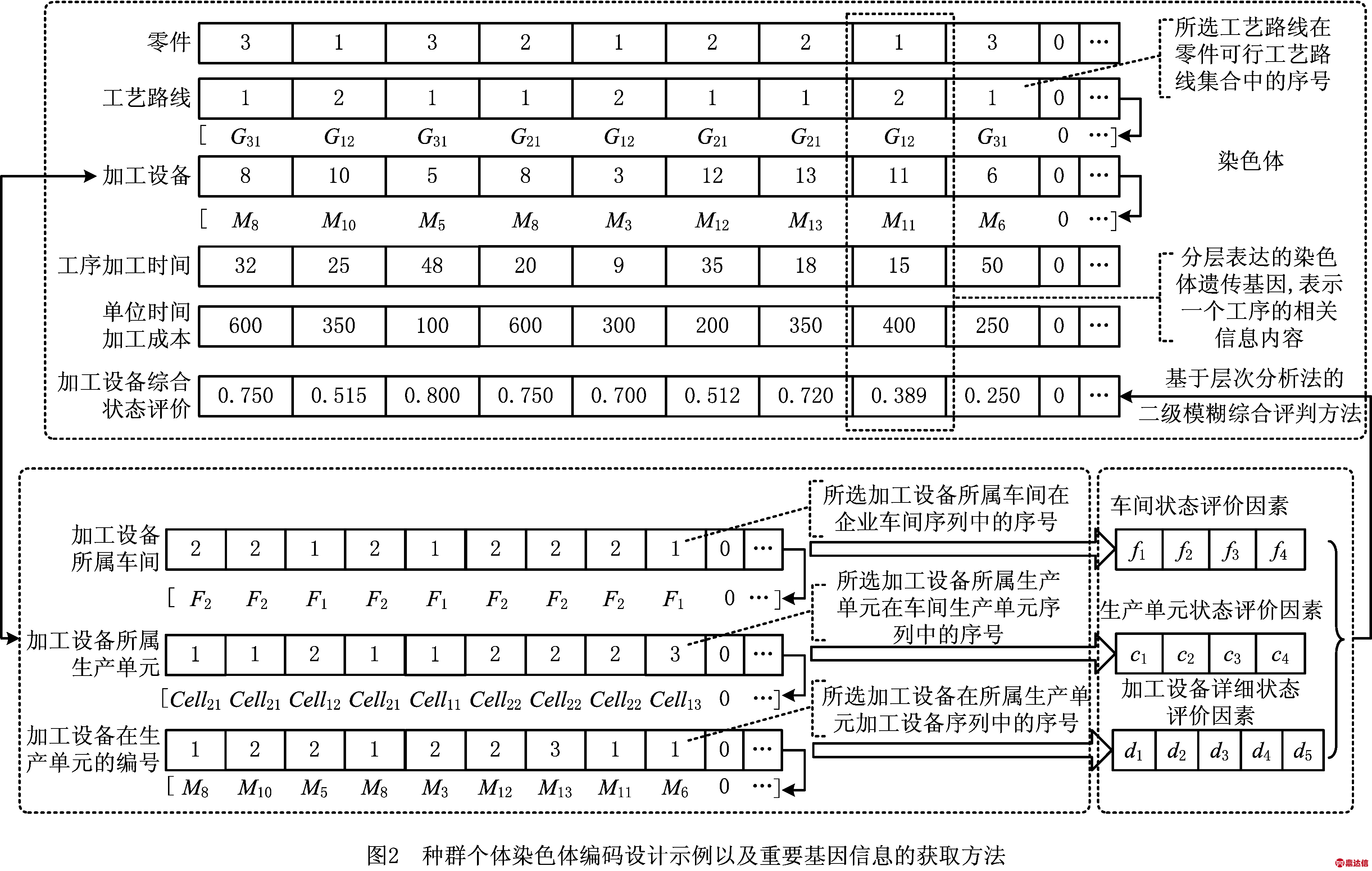
的信息,即t和c的值。tici,其中ti和ci分别为染色体上基因i记录的工序加工时间和工序执行加工设备的单位时间加工成本。
解码计算一批零件加工所用的全部加工设备的综合状态评价值S,需要提取染色体基因加工设备综合状态评价层的信息,即s的值。si,其中:si为染色体上基因i记录的工序执行加工设备的综合状态评价值,其求解过程在第2章中已经说明;L为染色体上非零基因的数目。
获得式(4)中变量T,C和S的值后,便可进一步评价种群个体的适应度。
3.1.3 种群初始化
从每个零件的加工设计任务中随机选择一条工艺路线,再从所选工艺路线随机选出一道工序,然后从该工序对应的可选加工设备集合中随机选择一个加工设备,从而获得一道工序的基因表达(p,g,m,t,c,s)。因为工艺路线中工序存在先后顺序的约束,所以需要对获得的染色体进行遗传基因顺序的调整,以保证染色体的有效性,具体的约束顺序调整过程可参考文献[20]。
3.1.4 适应度函数
适应度函数用于评价染色体个体,本文直接选用非线性工艺规划资源优化配置模型的目标函数(式(4))作为遗传算法的适应度函数。
3.1.5 选择、交叉、变异操作
对于选择操作,本文选用比例选择和最优个体保存策略。第G代种群中个体被选中并遗传到第G+1代群体的概率与该个体的适应度大小成正比。首先经过比例选择,将第G代群体中的一些优良个体复制到G+1代群体,实现第G+1代种群的初始化。然而,比例选择后形成的种群经过交叉、变异操作后,适应度好的个体可能会被破坏,从而影响遗传算法的收敛性。为此,采用最优个体保存策略,如果初始化后的第G+1代种群经交叉、变异操作后得到的最佳个体A的适应度比总的迄今为止最好个体B的适应度高,则将A作为新的迄今为止最好的个体,即B=A;否则将B放入第G+1代种群,并将第G+1代种群的个体数目加1。
对于交叉操作,当两个染色体中的基因发生交叉互换时,基因信息的层次关系和内容也要作对应的交换,本文采用文献[21]的交叉算法进行交叉操作。
变异操作是为了使遗传算法具有局部随机搜索的能力,同时生成新个体以保持种群的多样性。针对染色体遗传基因信息分层表达的特点,本文设计了相应的变异操作,具体的操作流程如图3所示。具体的遗传算法计算步骤在此不再赘述。
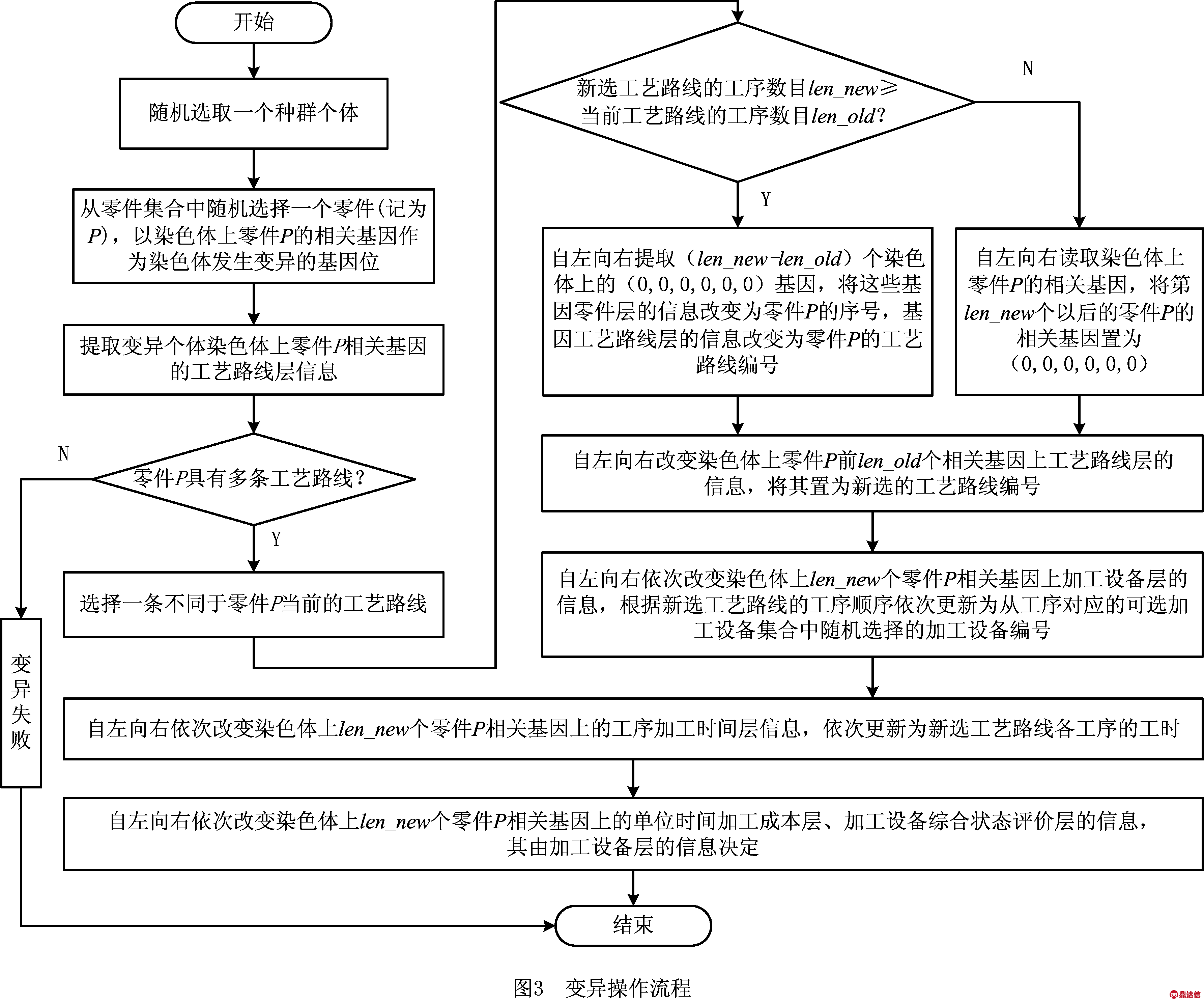
3.2 模型求解算例
以研究依托的某重点军工制造企业的某个订单任务为例,该订单包括两个零件(记为P001,P002),其形状结构、主要尺寸和精度要求如图4所示。下放订单至机加车间生产的约束条件为最长完工时间Tend=90 min,加工成本限额Call=160 元。工艺部门对P001,P002进行非线性工艺规划设计时,涉及的机床设备的规格、参数以及进行资源优化配置所需的属性信息已获知或求出,如表3所示。零件P001和P002的材料为7A04-T6规格的铝合金,其中加工P001的毛坯为直径200 mm、长80 mm的圆柱形棒料,加工P002的毛坯为直径85 mm、长95 mm的圆柱形棒料。针对两零件设计的工艺路线的主要机械加工工序如表4~表7所示。限于篇幅,表4~表7中的切削参数是各工序内容精加工阶段的切削参数,且表4注释中对切削参数的符号说明适用于表5~表7。根据以往的设计和生产经验,P001倾向于选择工艺路线1,对应的机床设备为M3→M5→M5;P002倾向选择工艺路线2,对应的机床设备为M1→M1→M4→M4。按照不改变加工设备上零件加工顺序的生产调度规则可以得到订单的完工时间为78.5 min,加工成本为107.77 元,全部加工设备的综合状态评价值为0.806 0。
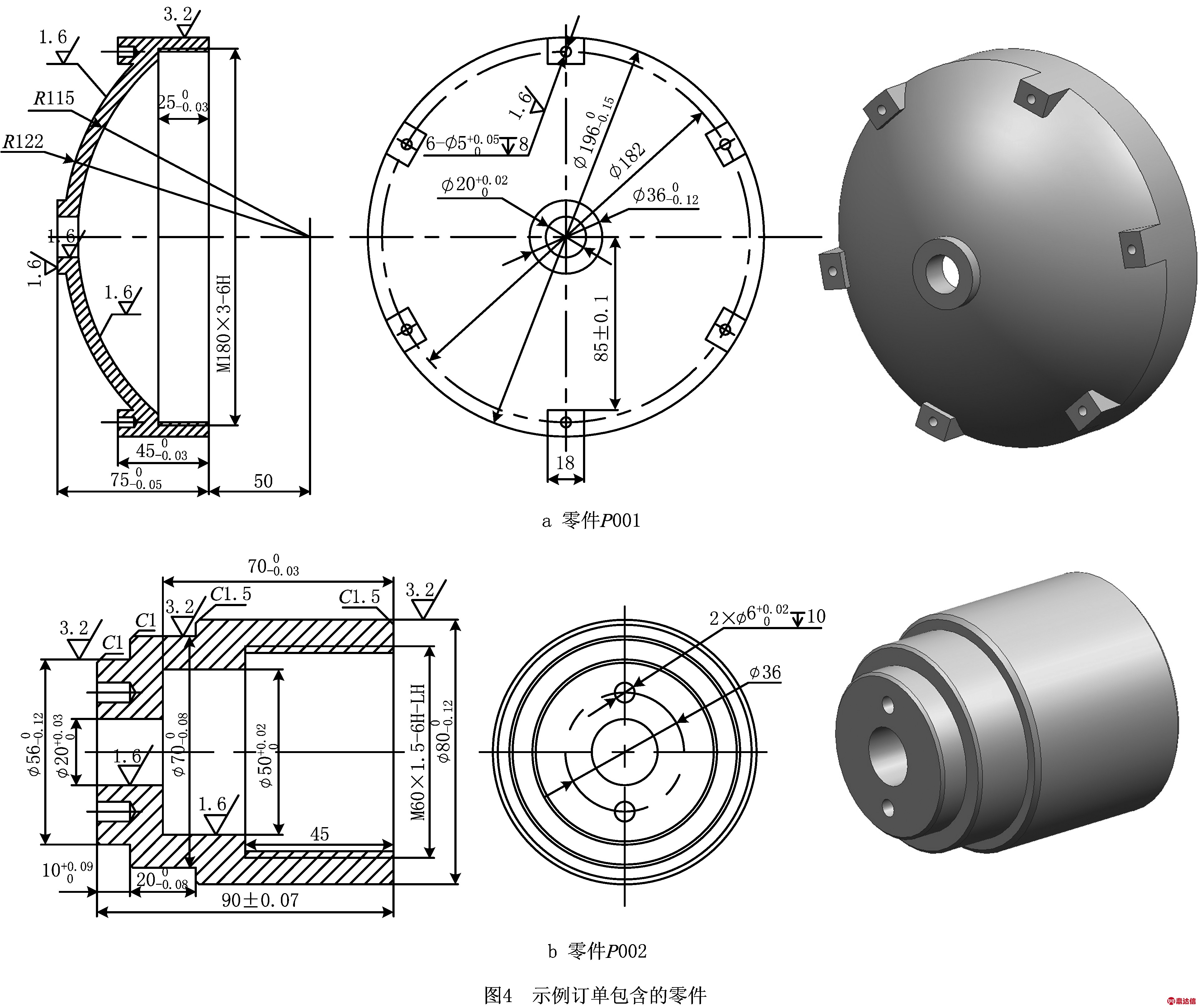
表3 工艺规划所用机床设备的相关信息
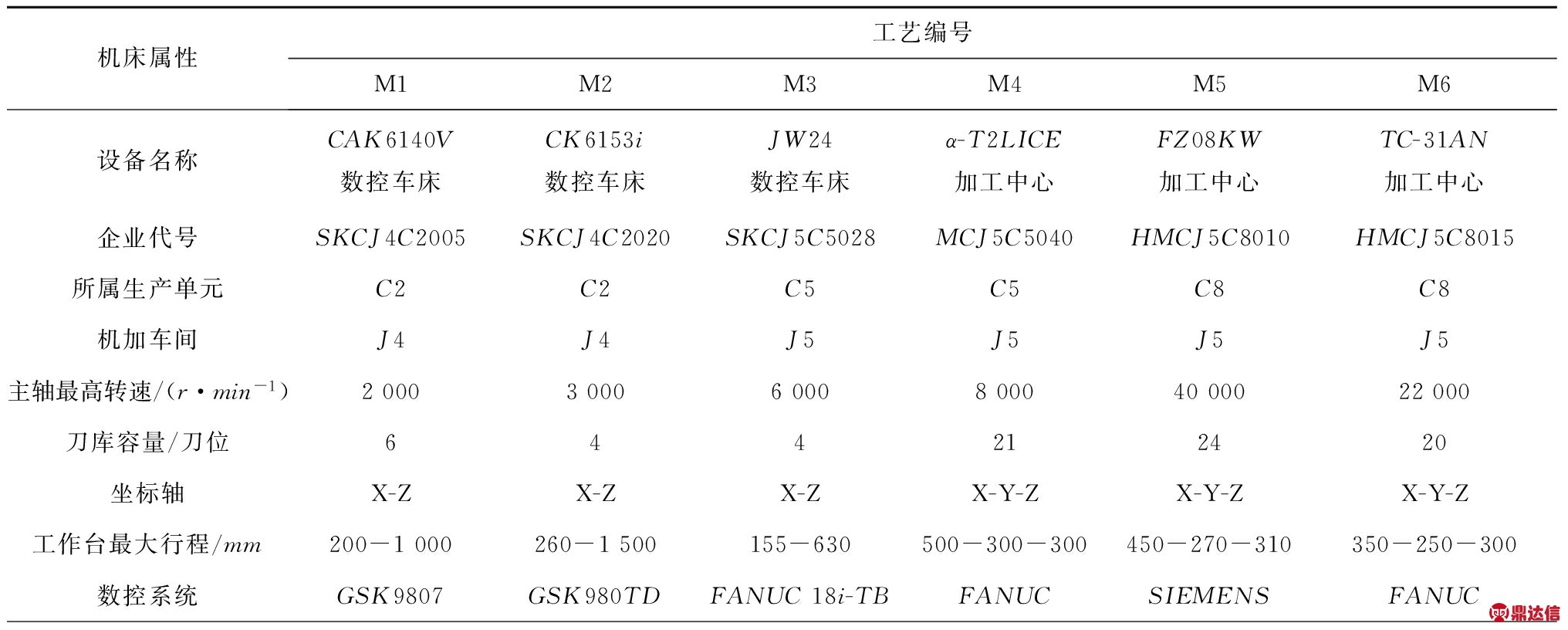
续表3

表4 零件P001工艺路线1的主要机械加工工序
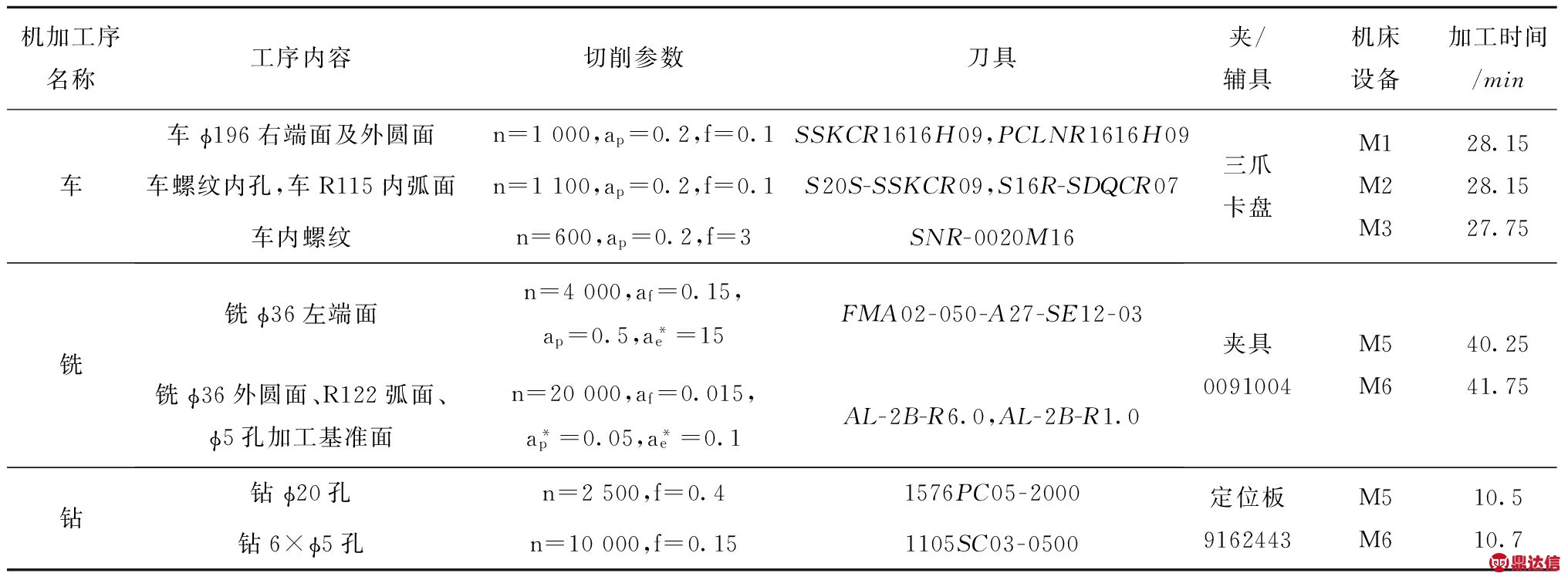
注:n表示主轴转速,单位r/min;ap表示切削/铣削深度,单位mm;f表示车削/铣削的进给速度,单位mm/r;af表示铣刀每齿进给量,单位mm/齿;ae表示铣削宽度,单位mm;表示最大铣削深度,单位mm;
表示最大铣削宽度,单位mm。
表5 零件P001工艺路线2的主要机械加工工序
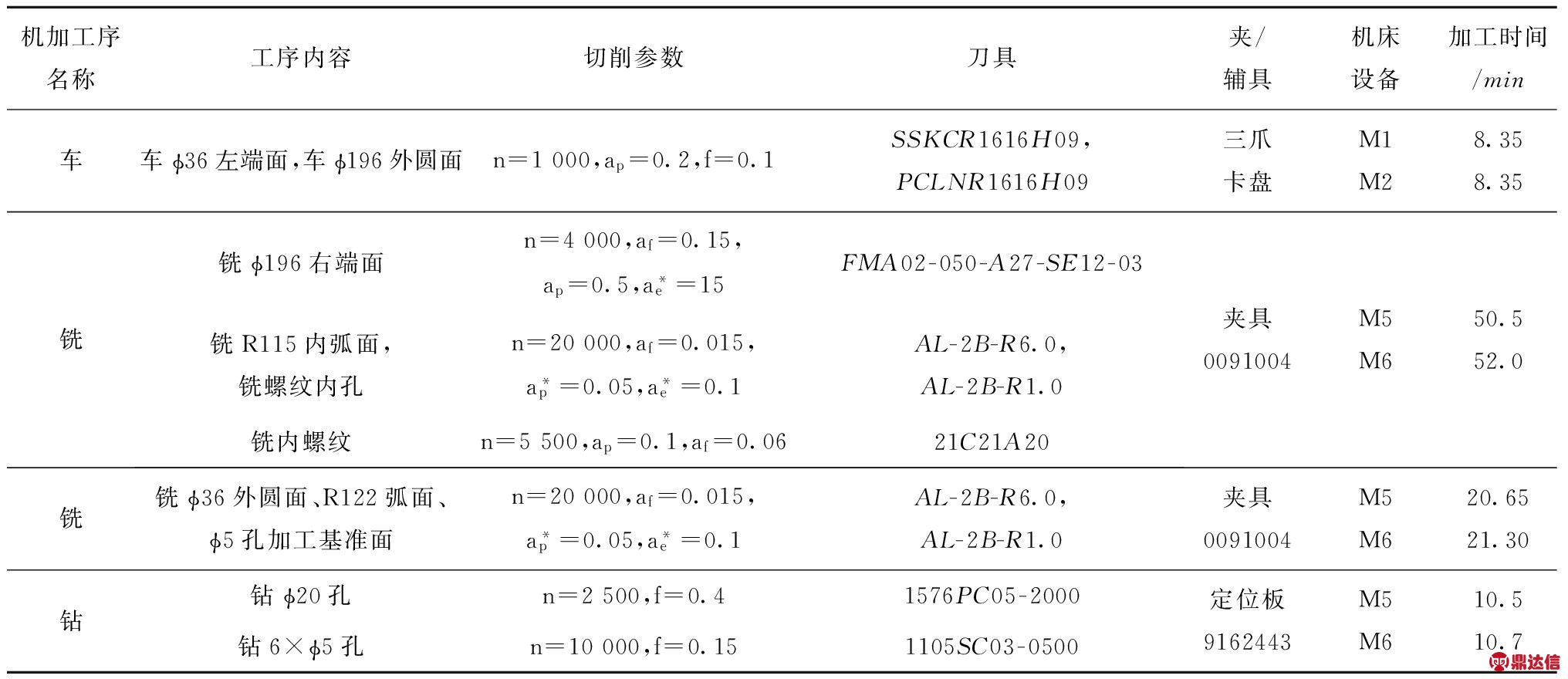
表6 零件P002工艺路线1的主要机械加工工序
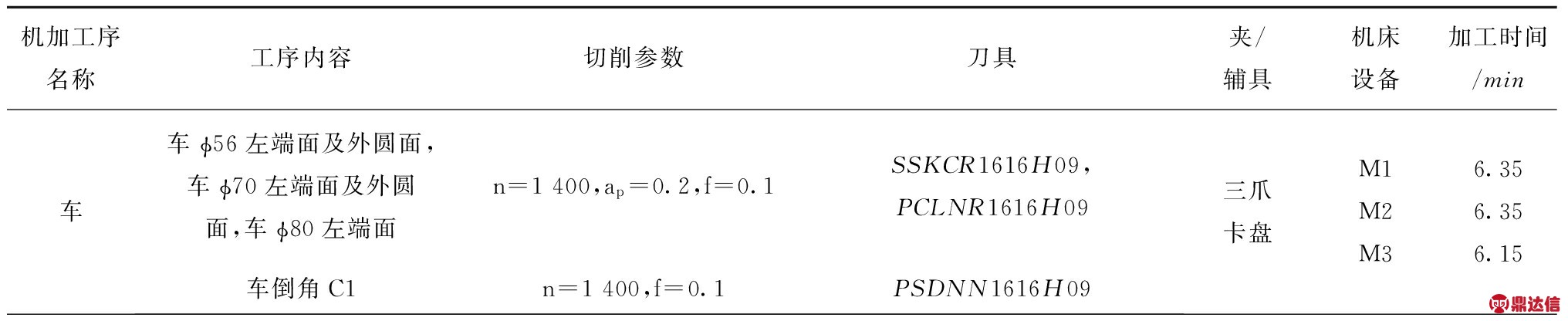
续表6
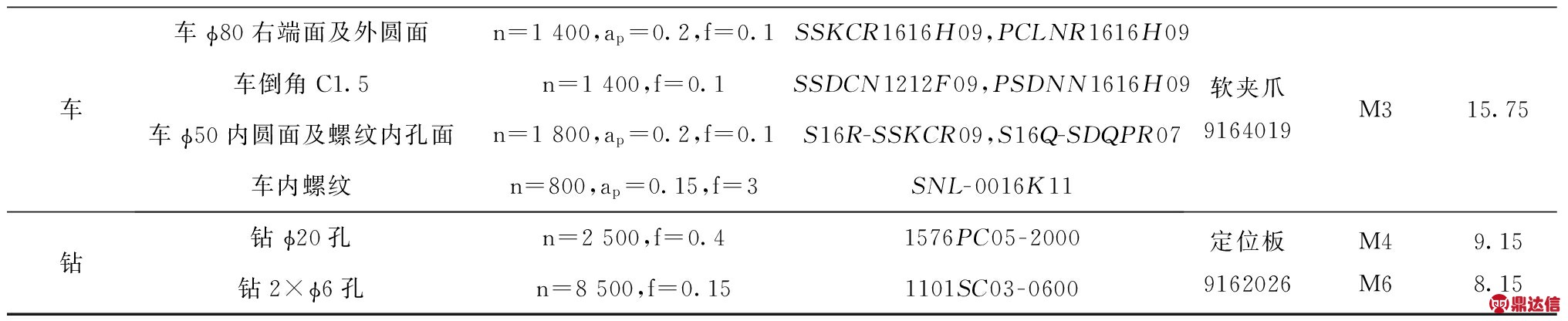
表7 零件P002工艺路线2的主要机械加工工序

利用遗传算法求解非线性工艺规划资源优化配置模型时,由式(4)可知计算个体适应度需要先确定各目标权重。为此,企业采用层次分析法计算影响因子的权重,判断矩阵的标度准则参照1~9级标度[18],评审小组由3人组成,包括企业高层管理者、车间生产管理者、高级工艺设计师,由他们对加工时间、加工成本、加工设备状态三者之间的相对重要程度进行两两比较,建立的判断矩阵分别为。然后利用方根法求解得到各判断矩阵的最大特征根及其对应的权重向量:λ1max=3.019,w1=[0.443 0.388 0.169];λ2max=3.018,w2=[0.239 0.137 0.625];λ3max=3.010,w3=[0.192 0.174 0.634]。为避免判断矩阵偏离一致性过大,还需计算其一致性指标,因为判断矩阵的维度D=3,所以一致性判断的计算公式为
,其中λmax为判断矩阵的最大特征根,IR=0.58,当Rc<0.1时,认为判断矩阵的一致性可以接受,否则需要对判断矩阵进行修正[22]。将R1,R2和R3的最大特征根λ1max,λ2max,λ3max分别代入一致性判断的计算公式,得到Rc的值分别为0.016,0.016,0.009,均小于0.1,故R1,R2,R3的一致性可以接受。最后,计算各评审成员评判各目标权重的算术平均值,得到式(4)中各目标的权重为β1=(0.443+0.239+0.192)/3=0.291,β2=(0.388+0.137+0.174)/3=0.233,β3=(0.169+0.625+0.634)/3=0.476。
遗传算法进化循环代数取300,初始种群个体取50,交叉概率取0.85,变异概率取0.1,算法执行20次条件下求得的最优解个体染色体编码为(1,1,3,27.75,45,0.820)-(2,1,3,6.15,45,0.820)-(1,1,6,41.75,60,0.912)-(2,1,3,15.75,45,0.820)-(2,1,4,9.15,70,0.934)-(1,1,6,10.7,60,0.912)-(0,0,0,0,0,0)-(0,0,0,0,0,0)和(1,1,3,27.75,45,0.820)-(2,1,3,6.15,45,0.820)-(1,1,6,41.75,60,0.912)-(1,1,6,10.7,60,0.912)-(2,1,3,15.75,45,0.820)-(2,1,4,9.15,70,0.934)-(0,0,0,0,0,0)-(0,0,0,0,0,0)。分别解码两个最优个体的染色体基因,得到相同的P001,P002最优工艺路线选择和主要机械加工工序的加工设备选择信息,如表8所示,加工设备的工艺编号意义参考表3。将求解得到的信息与根据以往经验选择的工艺路线和加工设备相比,尽管加工时间有所延长,但降低了加工成本,而且加工设备的综合状态较好,说明加工设备的负荷更为合理,从而降低了加工过程出现故障的概率。
表8 最优个体染色体基因解码得到的信息

4 应用案例
本研究依托的某重点军工制造企业通过实施“千台数控机床增效专项计划”以及后续的一系列数字化工程项目,已经拥有较好的数字化、信息化应用基础,能够对企业加工设备状态信息进行有效采集和存储。针对兵器装备质量和可靠性要求高以及生产多品种、小批量、交付期要求准时的特点,通过协同企业各部门的业务流程,结合提出的非线性工艺规划资源优化配置模型和求解方法,采用Java语言和Ajax、网络数据库等技术开发了基于浏览器/服务器(Browser/Server, B/S)模式的制造资源优化配置系统。本文第3章源于实际应用的算例,其机械加工设备优化配置结果在系统平台中如图5所示。实践应用表明,产品设计工艺的车间生产可执行性和车间生产调度控制的灵活性都得到了提高。
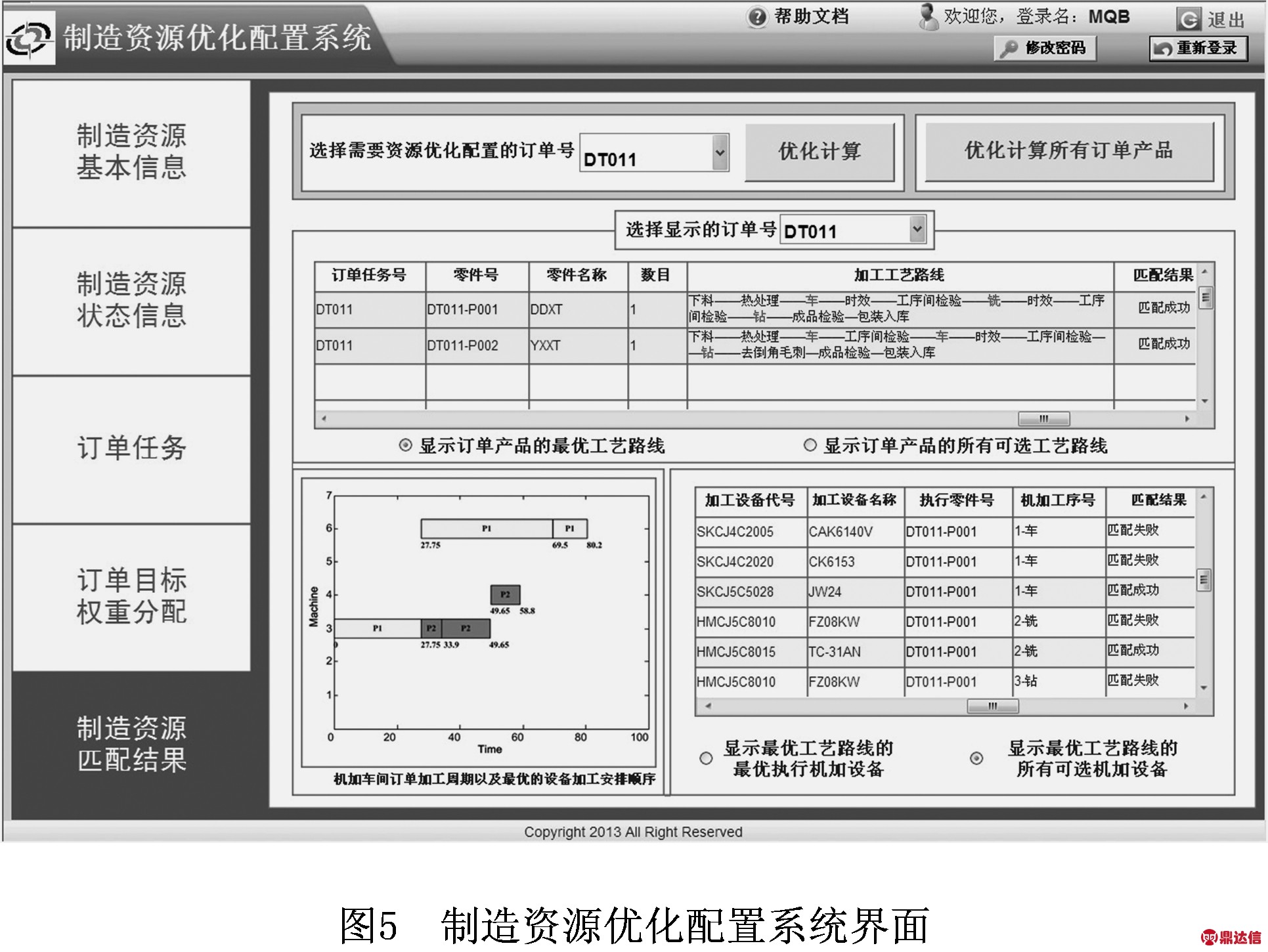
5 结束语
本文分析了典型机械加工车间的制造资源状态信息,借鉴现有的工艺规划资源优化配置研究,利用基于层次分析法的二级模糊综合评判方法实现了加工设备状态的量化分析。在此基础上,进一步考虑非线性工艺规划产生的柔性工艺路线和制造资源配置对生产调度的影响,针对如何从非线性工艺规划生成的众多可选工艺路线中选择较优的工艺路线和制造资源,通过相关假设和定义,建立了以加工时间、加工成本、加工设备资源状态为优化目标的非线性工艺规划资源优化配置模型。最后,通过设计遗传编码、解码和算子操作,利用染色体分层编码遗传算法,实现了非线性工艺规划资源优化配置问题的求解,给出了工程应用案例,验证了所提模型的有效性和求解方法的可用性。
在本文基础上,后续将进一步开展制造资源状态的建模研究,以便对制造资源状态进行更加全面地描述和量化分析;另外,本文建立的非线性工艺规划资源优化配置模型随着零件、可选工艺路线或可选制造资源的增加,其优化解的搜索空间也随之扩大,因此有必要开展更加高效的求解算法研究。