摘要:针对某气控先导式电磁阀的气控副阀在装配试验和性能试验过程中吸合响应时间存在明显差异的问题,建立气控副阀和试验系统的等效电路模型,并进行了理论计算和仿真分析,最终得出:性能试验过程中气控副阀响应时间与装配试验存在差异的原因是,在性能试验过程中测试电压补偿方式不当。通过对比研究试验系统等效电路模型,提出了一种测试电压补偿方法,采用新方法后,气控副阀在性能试验过程中的吸合响应时间与装配试验一致,差异性得以消除。
关键词:气控副阀;响应时间;Ansoft;电压补偿
1 引言
现代航天飞行器中,为提高姿轨控动力系统的动态响应速度,要求姿轨控发动机具有快响应的能力。姿轨控发动机通常由电磁阀和推力室组成,其中,通过电磁阀的开启/关闭控制推进剂的通路/断路,对应着发动机的开机/关机。想要实现发动机的快响应,就需要缩短电磁阀开启/关闭响应时间[1]。目前国内外的快响应姿轨控发动机中,往往使用气控先导式电磁阀(以下简称电磁阀)。而在试验过程中,如何获得最真实的电磁阀响应性能,将直接影响着姿轨控发动机的控制方式与控制精度[2]。
2 气控先导式电磁阀简介
图1为气控先导式电磁阀的工作原理示意图,电磁阀由副阀、主阀两部分组成:副阀部分可视为一个两位三通阀,主阀部分可视为一个两位两通阀。当副阀接通电信号打开后,控制气从气源出发沿白色箭头通路进入R、Y主阀,驱动两路主阀打开,将推进剂送入推力室,此时发动机开机工作;当副阀断开电信号关闭后,控制气沿白色箭头通路被切断,R、Y主阀的剩余控制气排出,控制气压力下降至一定值时,主阀复位关闭,电磁阀断路。电磁阀的动态响应性能主要决定于副阀的响应特性。
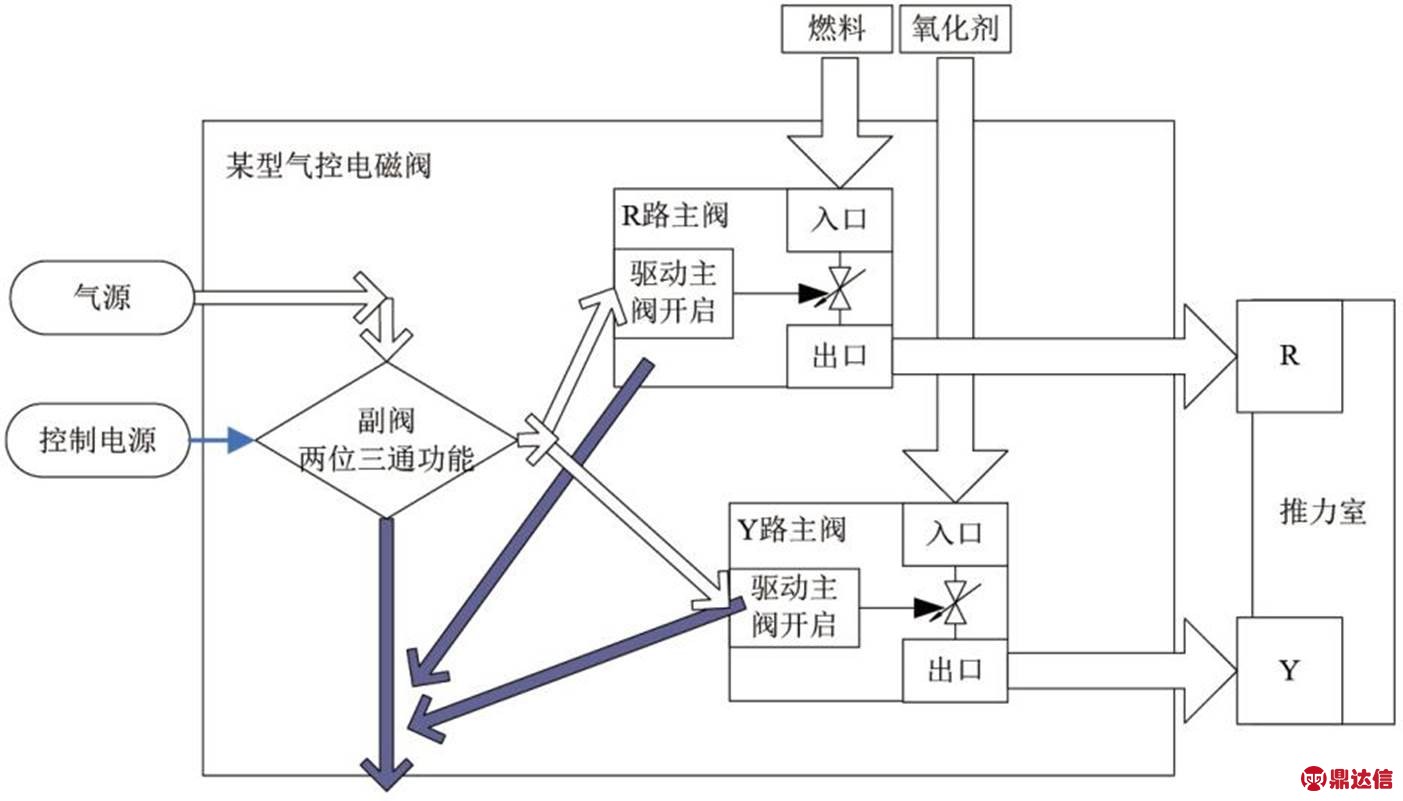
图1 气控先导式电磁阀工作原理示意图
电磁阀副阀的典型响应曲线如图2所示,其中横轴代表时间,纵轴代表线圈内电流。当t=0时,在线圈两端接通驱动电压,此时线圈内电流开始上升;当t=t0时,电流升到触动电流I1时,衔铁上的电磁吸力克服衔铁上的启动反力,衔铁开始运动,线圈内电流受衔铁运动产生的反电动势影响,电流开始下降;当时间到达t1时,衔铁运动到位,副阀此时完全打开;线圈内电流继续增加,直至达到最大电流Im。
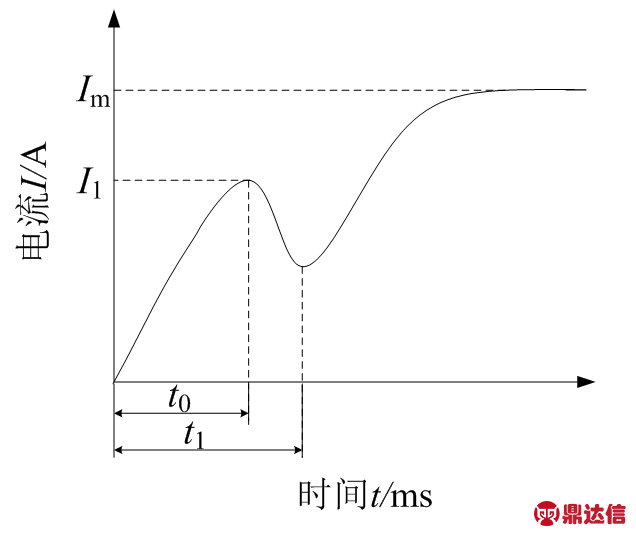
图2 电磁阀副阀典型响应曲线[3]
图2中所示的t1时间为副阀的开启响应时间,当副阀的技术状态确认后,该值应为一确定值,不会随试验系统而变化。而本文发现了同一台副阀在不同试验系统中的响应时间存在差异性,并针对该现象进行研究。对副阀在额定工作状态下的动态特性,和在整阀性能试验中的动态响应特性,进行对比分析与理论计算,并最终将差异性的原因归结到电磁阀性能试验过程中电压补偿方法不当。
为解决该问题,通过对比试验系统的等效电路模型,提出了一种新的测试电压补偿方法,使副阀在电磁阀性能试验中的触动时间、吸合时间与副阀额定工作状态一致,电磁阀测试所得到的整阀响应性能也与实际额定工况一致,消除了试验系统不同带来的差异性,提高了电磁阀性能试验结果的可信度。
3 副阀响应时间差异性分析
3.1 概述

图3 性能试验电磁阀性能曲线
电磁阀副阀在装配试验阶段和性能试验阶段,均会测试副阀的动态响应特性。其中,装配试验阶段的试验结果为副阀在额定工况下的响应。电磁阀性能试验过程中,副阀线圈的电流如图3中曲线所示,根据副阀工作原理,当线圈两端施加电压后,线圈电流缓慢上升,当电流达到触动电流i触动时,衔铁开始运动,此时时间t触动=4.5ms,即为副阀衔铁开始运动时间;线圈电流在反电动势作用下开始降低,当时间到达吸合时间t吸合=5.5ms时,衔铁运动到位;衔铁运动时间t衔铁运动即为t吸合-t触动=1ms。副阀衔铁运动到位后,主阀开启,t主阀运动为主阀固有性能,为0.5ms。
复查在装配试验阶段,副阀的响应特性,衔铁吸合时间为6ms,副阀在电磁阀性能试验中的响应时间较额定工作状态快0.5ms。
3.2 副阀响应特性分析
副阀在额定状态中与副阀在电磁阀性能试验状态中的性能参数如表1所示。
表1 电磁阀副阀在不同试验条件下性能参数对比
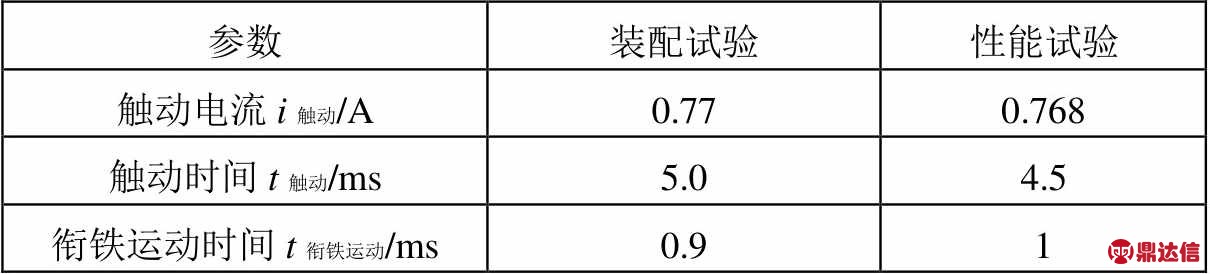
参数装配试验性能试验 触动电流i触动/A0.770.768 触动时间t触动/ms5.04.5 衔铁运动时间t衔铁运动/ms0.91
两次试验过程中,副阀触动电流基本相同,均为0.77A,可知副阀的工作载荷无变化[4];衔铁运动时间基本相同,为1ms,可知衔铁及其附属零部件的惯量、阻尼未发生变化[5];两者在触动时间上存在较大差别,分别为5.0ms和4.5ms。经初步分析,影响触动时间的因素有触动电流大小和触动电流上升速率(参考图3中辅助箭头K斜率),因两次试验中触动电流相同,则造成触动时间差异性的因素为触动电流上升速率。
4 副阀工作特性分析
4.1 副阀响应时间计算
影响触动电流上升速率的因素有线圈两端电压,线圈整个回路电阻、电感等。对比副阀额定状态测试系统与电磁阀整阀性能试验系统的等效电路,如图4所示,其中,副阀线圈等效为1个电阻和1个电感串联[6],采集控制盒等效为开关S、驱动电路MOS管内阻Rmos和采样电阻内阻R采样;装配试验过程中驱动电压为额定电压27V,在性能试验过程中,为了补偿测试电缆线阻Rwire,将驱动电压补偿到29.5V以保证线圈最大电流一致。
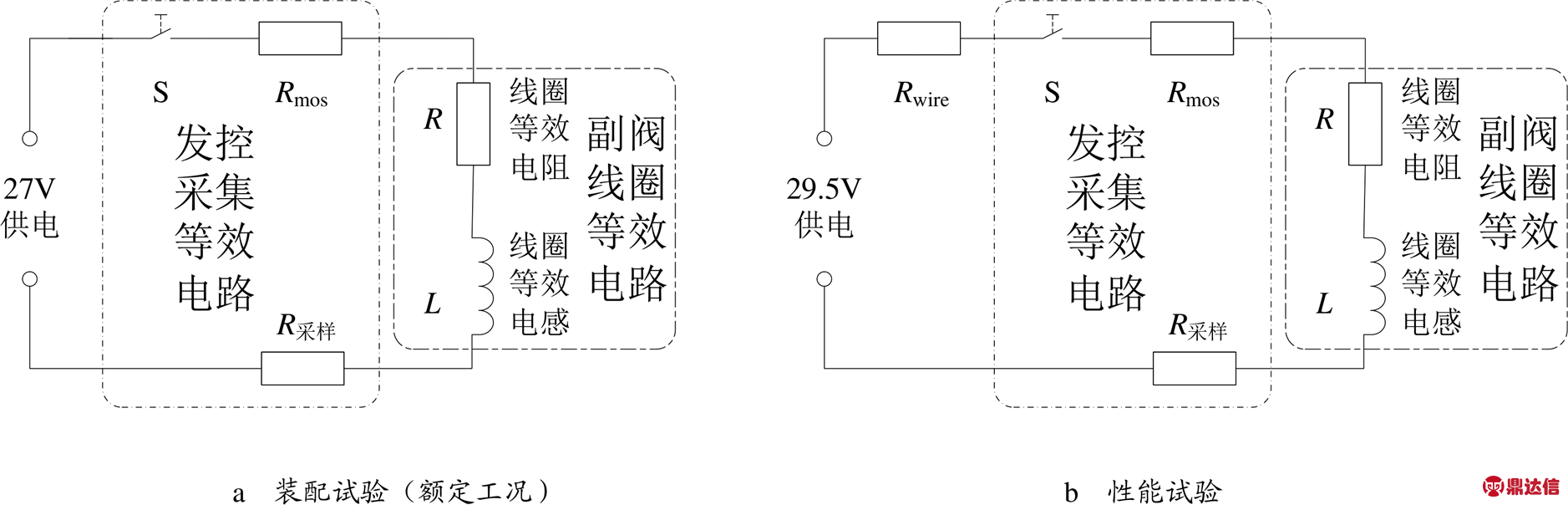
图4 试验系统等效电路图
对于装配试验状态的等效电路,电感内无初始电流,当开关S关闭时,根据基尔霍夫电压定律(Kirchhoff Voltage Law),对于通过线圈电流i(t)有[7]:
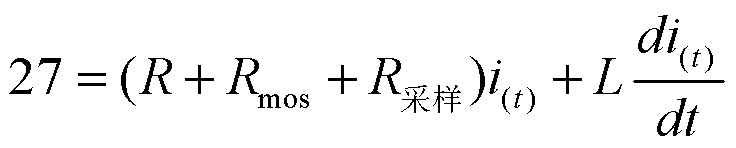
式中,R为线圈等效电阻,Rmos为驱动电路MOS管内阻,R采样为采样电阻,L为线圈等效电感。
乒乓球俱乐部是一个注重以人为本,以群众性活动为本的乒乓球爱好者聚集地。政府机构通过加强对俱乐部之间的管理,能够加强他们之间协调、沟通,使得乒乓球俱乐部成为联系众多乒乓球爱好者的纽带。同时,乒乓球俱乐部也是全民健身活动中的重要基层组织,是支持全民健身活动的基础。一方面,要进行良好的宣传,推动有条件的企事业单位、学校、机关成立乒乓球俱乐部,让乒乓球运动在当地全民健身活动中能够开花结果;另一方面,要积极发展会员,把俱乐部建设成有组织性的群众性体育团体,不但要吸收那些球技较好的运动者,也要吸引初学者,把所有热爱乒乓球运动的人都吸纳进来,从而为全面健身活动提供有力的支撑。
仿真结果总体与试验结果接近,虽然仿真结果中两次试验的驱动电压参数不相同,但衔铁的吸合运动时间相同,均为0.8ms,说明衔铁的吸合运动时间受补偿电压的影响较低。
根据土地质量地球化学评价规范中的相关要求[9],结合土壤环境质量农用地土壤污染风险管控标准中的风险筛选值[4],基于本区土壤理化指标pH值,对As、Cd、Cr、Hg、Ni、Cu、Pb、Zn八项环境指标指标,进行分级统计(表7)。土壤重金属元素含量特征分述如下。
图10(a)(b)分别给出了动态初始压溃应力和动态应变硬化参数随泡沫铝相对密度的变化。我们采用如下幂函数形式分别进行拟合:
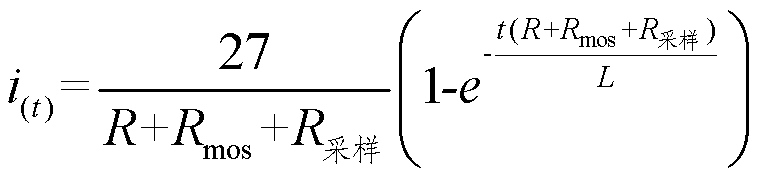
求解t:
(3)
同样方法得到性能试验时线圈电流i(t′),并求解t′:

式中,Rwire为线缆电阻,其余参数与式(1)中相同。
求解该线性非其次微分方程,得到:
公式中各参数的实测值为:线圈电感L=0.12H,线圈电阻R=19Ω,R采样=0.2Ω,Rwire=1.8Ω,为简化计算,Rmos忽略不计[8]。
取触动电流i(t)为0.77A时,带入式(3),计算电磁阀触动时间t触动=4.97ms;
取触动电流i(t′)为0.77A时,带入式(4),计算电磁阀触动时间t′触动=4.54ms。
计算结果与试验结果较接近,通过对比式(4)与式(3),性能试验触动时间较装配试验(额定状态)快0.42ms的原因是:性能试验为排除线缆电阻Rwire的分压影响,将驱动电压提高至29.5V,虽然保证了流经线圈的最大电流与额定状态一致,但2.5V补偿电压大幅度提高了试验系统电路中回路电流i(t′)对一阶零状态响应的时间特性,表现为触动时间与装配试验状态相比快0.42ms。
二是基于生产效率人工智能技术应用。近年来,重庆已经建立了数十个数字内容资源库,在2018年及更长时间,企业会着手数据资源的挖掘和应用,会带动人工智能技术在数字出版领域的应用,通过挖掘相关内容资源,实现内容快速生成和聚合,人工智能技术在城市文化传播、传统文化传承等领域将得到广泛应用,对提升数字出版业创新能力和经济效益具有重要支撑作用。
西汉思想家、政治家、哲学家董仲舒有句名言:“仁人者正其道不谋其利,修其理不急其功。”(《春秋繁露·对胶西王》)意思是,贤明之士,应当遵循正道,不应急于取利;应当恪守理性,不应急于求成。反言之,急于取利者,多走邪道;急于求成者,多悖理性。然而,在董仲舒死了2120年之后,某些地方官员却不懂这个道理,偏要“急功近利”。
4.2 副阀性能仿真
由于该电磁铁为轴对称结构,所以选择轴对称求解类型,建立电磁铁的二维轴对称模型(Z轴旋转)[9],如图5所示。其中,衔铁沿Z轴运动,初始气隙0.3mm,即初始位置为0,运动行程为沿Z轴方向0.3mm;设置衔铁重量为8g,阻尼为0.02N·s/m;开启反力根据理论计算,设为-50N。
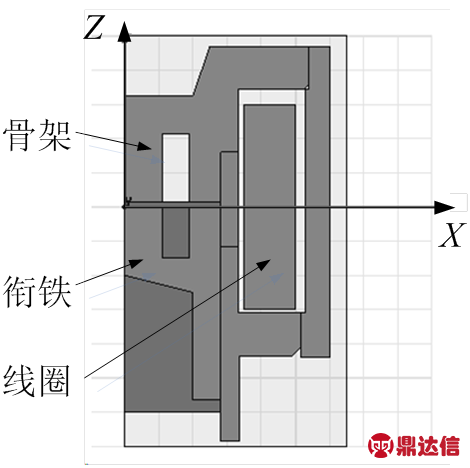
图5 副阀二维瞬态仿真模型
定义材料后,定义激励源和边界条件,设置激励方式为电压激励,初始电流设置为0A,电感设置为实测值0.12H,线圈匝数设定为500匝。分别对图3所示两种副阀测试状态进行仿真,其中,装配试验仿真时将电阻设置为19.2Ω、驱动电压设置为27V,仿真结果如图6所示;液流试验仿真时将电阻设置为21Ω、驱动电压设置为29.5V,仿真结果如图7所示。
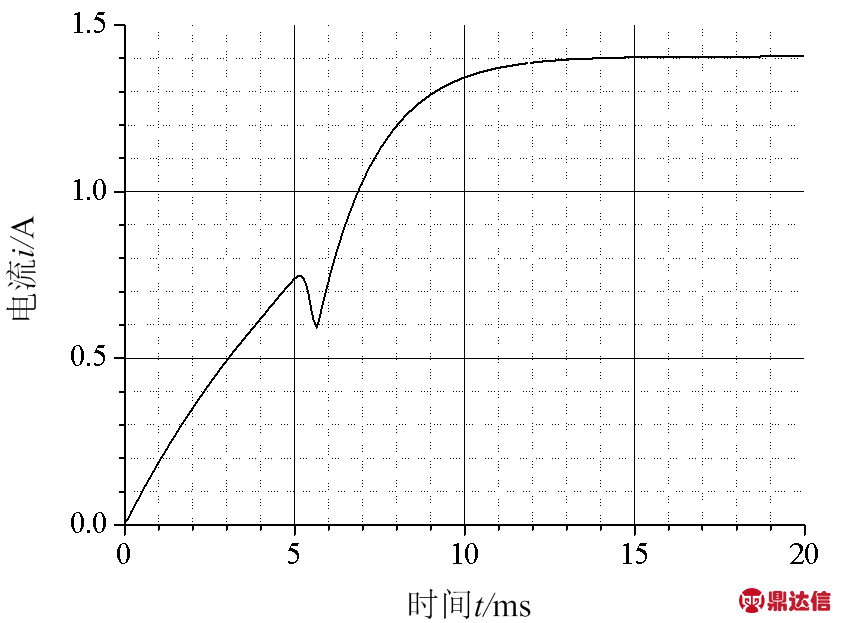
图6 装配试验副阀性能仿真
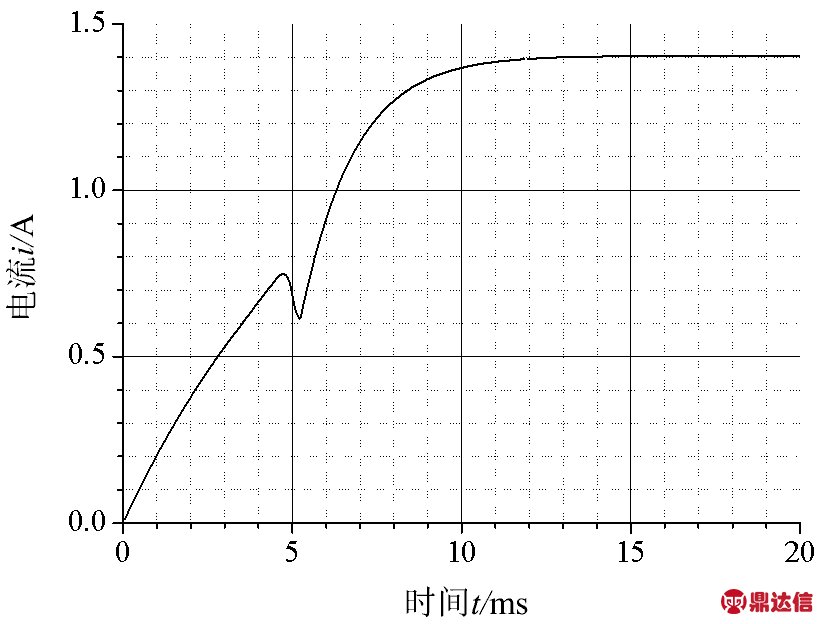
图7 液流试验副阀性能仿真
两次试验中触动电流仿真结果均为0.75A;装配试验的吸合时间仿真结果为5.15ms,液流试验的吸合时间仿真结果为4.6ms;两次试验中衔铁运动时间的仿真结果相同,均为0.8ms。
本文针对RBC的特点,考虑风险因素之间的影响,提出基于ANP和证据融合理论的风险评估模型,对RBC的风险等级进行评估。
为补偿液流试验系统中的线缆电阻Rwire分压,将驱动电压提高至29.5V,虽然可以保证副阀线圈内最大电流与额定状态一致,但却使副阀的响应特性偏离额定工作状态,据此可判断计算线缆电阻分压法的电压补偿方法不能准确反映出电磁阀整阀的响应特性。
仿真结果中触动时间与计算结果、试验实测值均较接近,衔铁运动时间也与试验实测的0.9ms基本相同,并且根据仿真结果,衔铁的运动时间受到补偿电压的影响较小,可忽略,在电压补偿计算中,不需考虑衔铁运动时间。
为了让性能试验中电磁阀的响应时间与电磁阀装配试验(额定工况)尽可能接近,需重新考虑对导线电阻Rwire的补偿方案。想要达到的补偿目标为:副阀衔铁的吸合时间、触动时间尽可能接近额定工作状态,以获得电磁阀整阀的额定响应时间。
5 电压补偿计算及验证
令式(3)、式(4)的触动时间相等,将式(4)中的29.5V电压设为未知量Ux,令t=t′,联立式(3)、式(4),求解Ux:
2.4 两组患者成功排卵和妊娠情况比较 观察组患者成功排卵和妊娠率分别为75.68%(28/37)、72.97%(27/37),对照组患者分别为51.35%(19/37)、45.95%(17/37),差异有统计学意义(χ2=4.723,P=0.000;χ2=5.606,P=0.000)。
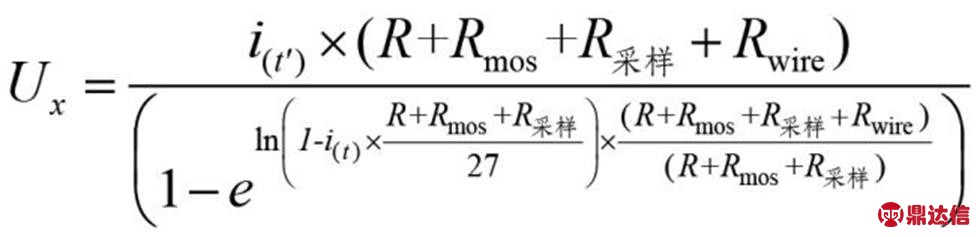
其中,副阀的触动电流相同,结合实测结果取i(t′)=i(t)=0.77A,解得Ux=27.9V,将Ux带入仿真模型,求解副阀线圈电流曲线如图8中曲线 “27.9V补偿”,将图6、图7曲线合成到图8,分别为“额定测试”曲线与“29.5V补偿”曲线。
图8 对比额定状态与两种补偿方式中副阀线圈电流i(t)仿真结果
其中,“27.9V补偿”曲线与“额定测试”曲线在副阀整个动态响应范围内重合,说明27.9V补偿电压时,衔铁的吸合、触动特性与额定状态一致;在7ms时,额定测试状态的电流曲线与27.9V补偿状态的电流曲线才产生分离,并最终达到最大电流1.33A,衔铁在6ms时已完成动作,此后的电流变化不影响副阀的响应特性。
老黄听是听到了她的话,可袁安这小子的龙虎爪已不可思议地直奔他胁下了。匠作的快泥刀、捕快的疯横刀也停不下来。
关停井复产或是长停井恢复,对老油田并非全新话题,但在新时期应该有全新的考虑。关停井的生产恢复,不应仅仅局限在一两口井的重新开井上,而应立足于某个区块、某个油藏的角度,以大修、压裂、补孔等油藏治理手段以及产能建设,带动长停井恢复,实现老油田局部富集区域的二次开发。也就是说,停井复产要作为一场大兵团协同作战的战役去打,才能发挥事半功倍的效果。
调整计算,将线圈两端电压改为27.9V,重新进行液流试验,其副阀线圈电流如图9所示,其中,触动时间t触动由原来的4.5ms变为5ms,衔铁运动时间t衔铁运动仍为1ms,此时副阀的工作曲线与装配状态相同,副阀工作状态与任务书装配要求的额定状态一致。
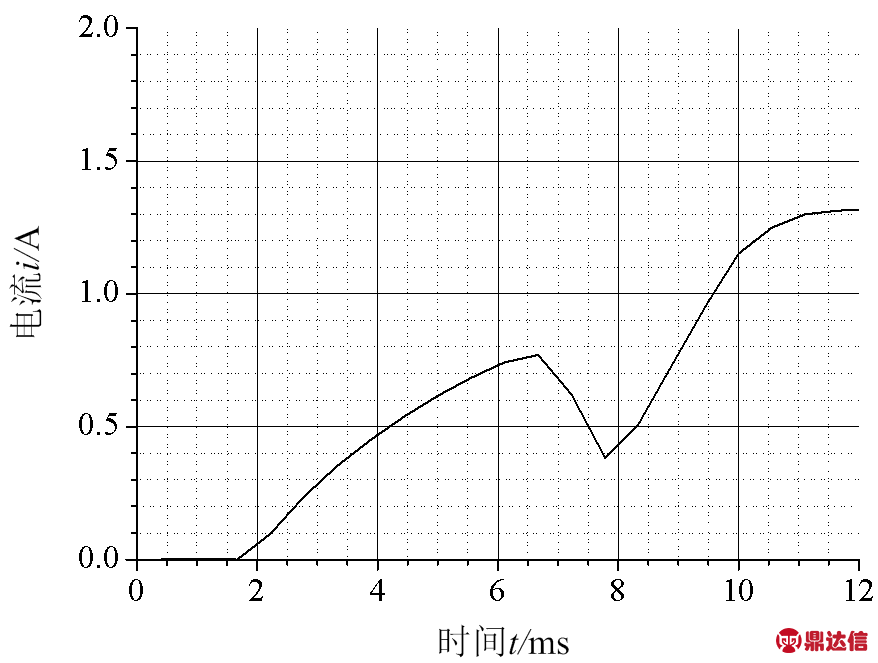
图9 调整计算后副阀触动时间t触动
6 结束语
本文分析了一种气控先导式电磁阀的副阀在额定工作状态与性能试验中响应时间存在差异性的原因是,补偿线阻分压时,将驱动电压设置较高,导致性能试验中副阀响应时间相较额定工作状态快0.5ms。经理论分析与计算,研究出一种新的电压补偿计算方法,按新方法计算出的驱动电压由原来的29.5V降低至27.9V,调整试验系统驱动电压后,重新进行电磁阀性能试验,副阀的响应时间与额定工作状态一致。对于该类型的副阀,后续液流试验或类似试验过程中,为获得与额定工况一样的响应特性,可采用本文的驱动电压补偿算法。