摘 要: 滑阀的内泄漏会使阀控缸系统中的油缸活塞产生自行动作,为减小滑阀内泄漏量,在影响滑阀内泄漏的诸多因素中,选择了易于实现且成本较低的方案——增大滑阀阀芯和阀套的搭接量,同时为了弥补死区以及滑阀工作锐边变钝对滑阀性能的影响,基于数字伺服阀,采用分段变增益的流量增益补偿方案对滑阀中位的线性补偿技术进行了研究。经试验表明,降低滑阀内泄漏及滑阀中位线性补偿方案有效的保证了滑阀的低泄漏及空载流量增益的线性特性。
关键词: 低泄漏;死区;补偿
引言
在阀控缸液压系统中使用滑阀换向时,一般采用O形滑阀机能的中位进行油缸制动。可是,由于滑阀存在内泄漏,对油缸制动产生的影响不可忽视,甚至使油缸活塞产生自行动作[1],因此,减少滑阀内泄漏对阀控缸液压系统的发展有较大的工程意义。
在影响滑阀内泄漏的诸多因素中,滑阀阀芯和阀套的搭接量是较为主要的因素之一[2],也是降低滑阀内泄漏量经常采取措施的对象之一,本研究采用增大阀芯和阀套搭接量的方式来降低滑阀的内泄漏量,并基于数字伺服阀,对因增大搭接量而造成的死区及因滑阀的工作锐边变钝导致滑阀工作窗口面积梯度不恒定等现象进行了线性化补偿技术研究,有效的减少了滑阀的内泄漏量,基本消除死区及工作锐边变钝对滑阀性能的影响。
1 低泄漏滑阀非线性特性的形成
阀芯和阀套是滑阀的核心工作部件,按其搭接量的不同可将滑阀区分为正开口滑阀、零开口滑阀和负开口滑阀[3],如图1所示,它们具有不同的流量增益特性。

图1 滑阀工作边搭接示意图
在滑阀的常规使用场合,零开口滑阀才是其制造的追求目标,然而为了补偿阀芯与阀套间隙造成的内泄漏影响,使滑阀的增益具有线性特性,零开口滑阀实际上总具有一个微小的正搭接量[4],因此零开口滑阀在零位附近的内泄漏量可以认为和负开口滑阀一致[5]。其泄漏可通过以下公式计算[6]:
(1)
式中, Q —— 流量
xv —— 阀芯位移
L —— 搭接量
ps —— 供油压力
d —— 阀套内孔孔径
δ —— 阀芯与阀套单边间隙
由公式可知,通过增大阀芯和阀套的搭接量L和减小阀芯和阀套的径向间隙δ均能达到进一步减小滑阀中位的内泄漏量的目的[7],但在具体实现中,为降低机械加工的难度以及滑阀中阀芯和阀套出现卡滞的概率,显然增大阀芯和阀套的搭接量L[8],使滑阀进一步成为负开口滑阀为相对易行的方法。
当阀芯和阀套的搭接量增大到一定值后,滑阀在阀芯和阀套的搭接范围内的工作流量相对于正常流量可以忽略[9],滑阀控制信号在此范围的流量反馈较为迟钝甚至没有反馈,滑阀在采取低泄漏措施后形成工作死区,其空载流量曲线表现非线性,滑阀工作流量可通过如下公式计算得出:

(2)

(3)

(4)
式中, Cd —— 流量系数
ω —— 面积梯度
pL —— 负载压降
p0 —— 回油压力
ρ —— 油液密度
其流量特性曲线如图2所示。

图2 负开口滑阀流量特性曲线
2 增益补偿方案分析
由滑阀工作流量计算公式知,滑阀流量与阀芯位移成比例关系,为了使阀具有较低内泄漏量的同时保有良好的线性流量特性,本研究提出变增益控制方案,即滑阀切换工位工作时,通过控制使滑阀在死区范围的阀芯位移增益大于正常工作区间,对滑阀死区范围较低的流量增益进行补偿,控制方案效果应如图3所示,为了便于说明,对负开口量范围内的流量增益进行了一定的放大处理。
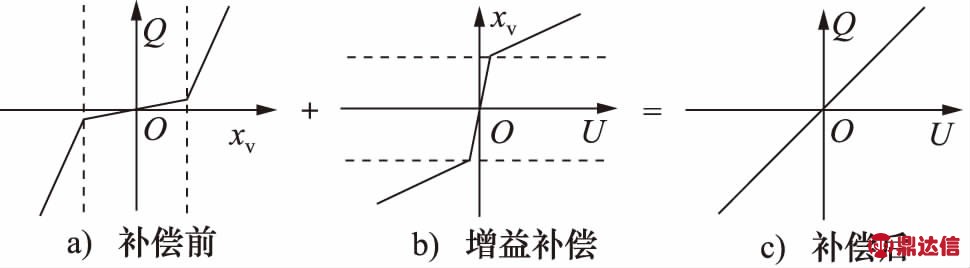
图3 变增益补偿控制效果预期图
基于数字伺服阀对低泄漏滑阀进行多区段增益补偿控制验证,数字伺服阀以永磁同步电机作为电/机转换器,采用丝杠副将电机输出转角转换为直线位移,进而直接驱动滑阀阀芯滑动,最终输出流量,其结构简图如图4所示[10]。
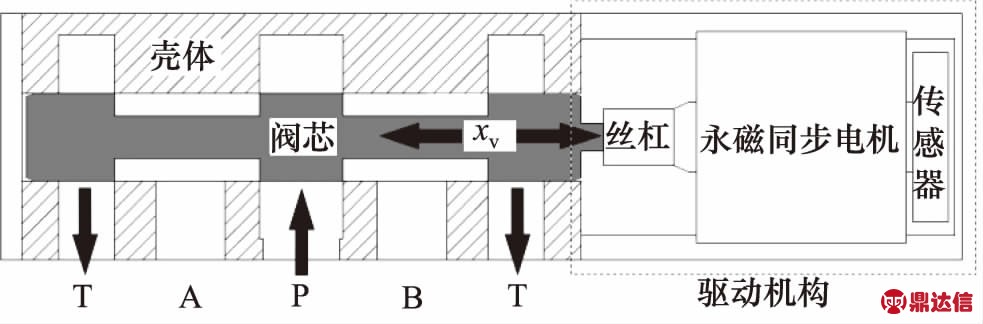
图4 数字伺服阀结构简图
数字伺服阀整阀采用半闭环控制,永磁同步电机采用转动角度闭环控制,其控制原理图如图5所示。

图5 数字伺服阀控制原理简图
永磁同步电机在工作中,其转子旋转角度与指令信号的比值是电机对指令信号的放大倍数。为了实现本研究对滑阀的流量增益补偿,按方案,需为电机设置多个工作区域和切换点,工作区域包括滑阀的死区和2个正常工作区间,不同工作区域按需设置其放大倍数,切换点为阀芯死区的2个边界点。
由零位附近的内泄漏公式知,滑阀泄漏量与阀芯位移并非简单的线性比例关系,为了简化控制,提高其工程应用性,将电机角度与指令信号的关系定义如下:
θ=k1U -U0≤U≤U0
(5)
θ=k1U0+k2(U-U0) U>U0
(6)
θ=-k1U0+k2(U+U0) U<-U0
(7)
式中, θ —— 电机转角
k1 —— 死区转角增益
k2 —— 工作区转角增益
国务院常务会议于日前决定全面清理各类证明事项,更多地消除群众和企业办事烦恼。一是对国务院部门规章和规范性文件等设定的证明事项,可直接取消的要立即停止执行,并抓紧修改或废止规章、文件;二是对法律法规有规定,但可通过法定证照、书面告知承诺、政府部门间核查等涵盖或替代的证明事项,要提请修法,依托信息共享和信用体系予以取消;三是对各地自行设定的证明事项,除地方性法规规定外,最晚应于年底前取消;四是各地区各部门要及时公布取消和保留的证明事项清单,对确需保留的要逐项列明设定依据、办理指南等。清单之外,政府部门、公用事业单位和服务机构不得索要证明。
U —— 指令电压信号
在滑阀的调试过程中,一般以滑阀流量为零时阀芯的位置为液压零位,当滑阀切换不同工位时,阀芯沿其轴线向不同的方向滑动,但受机械加工水平等因素的影响,滑阀并不像理想中的情况,其4个节流窗口并不完全匹配及对称,也就是说,阀芯沿不同方向滑动,需要脱离死区进入正常工作区间时,其通过死区的位移不同,这就需要在进行变增益控制时,增加分段分别控制。因此上述公式改变为:

(8)

(9)
θ=k1U 0≤U≤U0
(10)
θ=k1U0+k2(U-U0) U>U0
(11)
式中, k′1, k1 —— 对应死区转角增益
k′2, k2 —— 对应工作区转角增益
为保证滑阀的相关性能,滑阀中阀芯和阀套的工作边均需保持锐边,但受机械加工水平的影响,或在长期使用后,其工作变不再尖锐[11],此时,为了保证滑阀的压力增益等相关性能,亦可通过控制方法对其进行补偿[12]。阀芯工作锐边因机加水平或长期使用后,其工作变不再尖锐,其形状各异,其影响直接体现在滑阀的空载流量曲线中,为简化模型,可在空载流量曲线中采用斜边近似贴近,如图6所示。
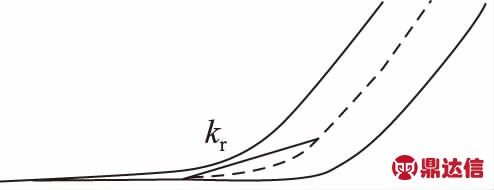
图6 阀芯钝化工作边近似补偿图
电机角度与指令信号的关系式如下:
U<-U0
(12)


(13)

(14)

(15)


(16)

U>U0
(17)
式中, kr —— 工作锐边钝化区域转角增益
工作锐边钝化后死区与工作区的分界电压值
3 试验验证
为验证线性补偿方案的效果,对同一型号的2台数字伺服阀采用了不同的配磨参数,其配磨参数如表1所示。
表1 试验数字伺服阀阀芯阀套配磨参数统计表 mm
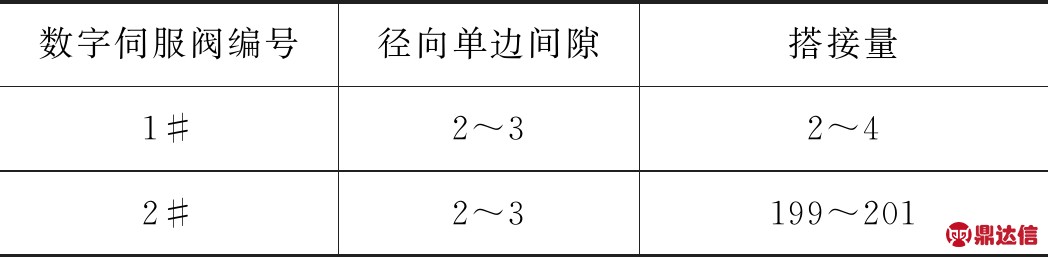
其中2#滑阀工作边在配磨时未刻意保持锐边。
其他试验相关参数如下:
① 工作介质:10号航空液压油;
② 阀芯直径:d0=20 mm;
③ 供油压力:ps=10 MPa;
④ 负载压降:pL=0;
⑤ 回油压力:po=0.5 MPa;
⑥ 丝杠导程:ph=3 mm。
3.1 内泄漏试验验证
O形滑阀机能处于中位时,介质通过A、B油口的内泄漏是造成油缸制动失效甚至自走的主要原因,因此,本研究主要对滑阀处于中位时介质通过A、B油口的泄漏量进行了测试。测试原理图简图如图7所示。
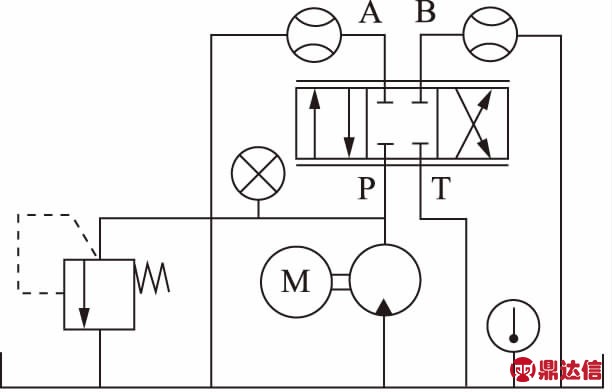
图7 滑阀中位内泄漏量测试原理简图
2#滑阀因其泄漏量过小,在图7基础上,将介质由A、B油路直接引出,采用量杯测量,测量时间1 min,测试结果如表2所示。
表2 内泄漏测试结果统计表 mL/min
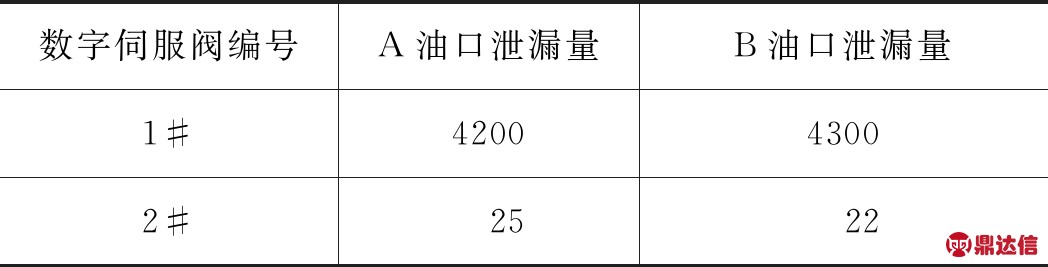
由表2数据得知,增大阀芯阀套搭肩量有效降低了滑阀中位的内泄漏量。
3.2 滑阀中位线性补偿试验验证
流量增益补偿相关参数的确定均在大搭接量滑阀实测空载曲线基础上确定。为了更方便的测量和补偿,在死区和正常工作区域之间定义过渡区域,该区域包括死区泄漏量较大的区域及因工作边变钝等因素引起的泄漏量增大的区域,其具体确定如图8所示。
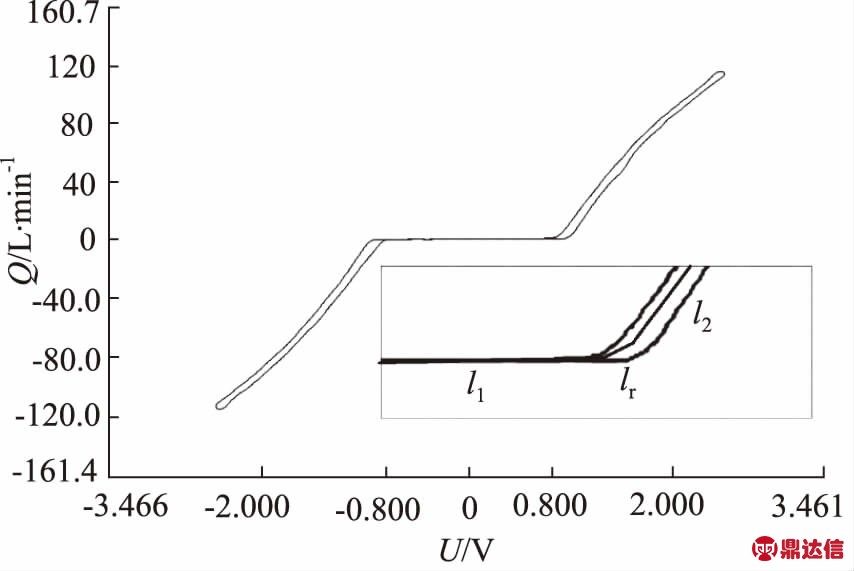
图8 2#未采取线性补偿空载流量曲线
图8为2#滑阀未采取线性补偿的空载流量曲线,可通过对原始图进行放大测量,读取并计算滑阀在死区的流量增益正常工作区流量增益
以及死区与正常工作区过渡区域的流量增益
因试验工装孔道的影响,在接受较大的指令信号时流量曲线发生一定程度的弯曲,在获取滑阀正常工作区的流量增益时,可对弯曲段进行有选择的忽略。流量曲线不同增益曲线交汇点处的指令信号值即为不同工作区域的分界点,即U0和
的值。
增益补偿的相关参数初步确定应符合如下关系:

在实际的调试过程中,考虑电机响应等相关因素,并根据实测曲线调整参数,最终确定补偿的相关参数如表3所示。
表3 增益补偿参数统计表
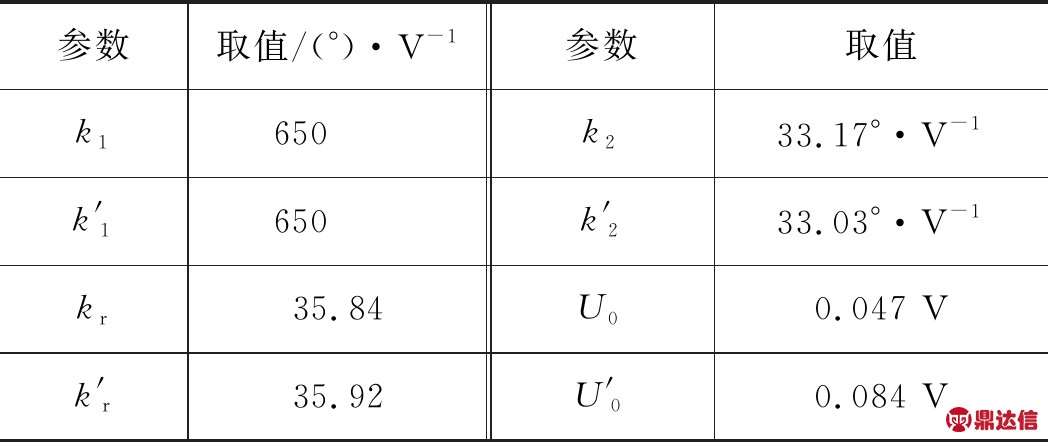
图9为2#滑阀采取线性补偿后的空载流量曲线,图6和图7的绘制压力均为10 MPa,指令信号均为峰峰值为5 V的正弦电压信号,通过对比可知,本研究基于数字伺服阀的大搭接量量滑阀线性补偿技术可以较好的跨越死区,并保证滑阀的线性流量特性。
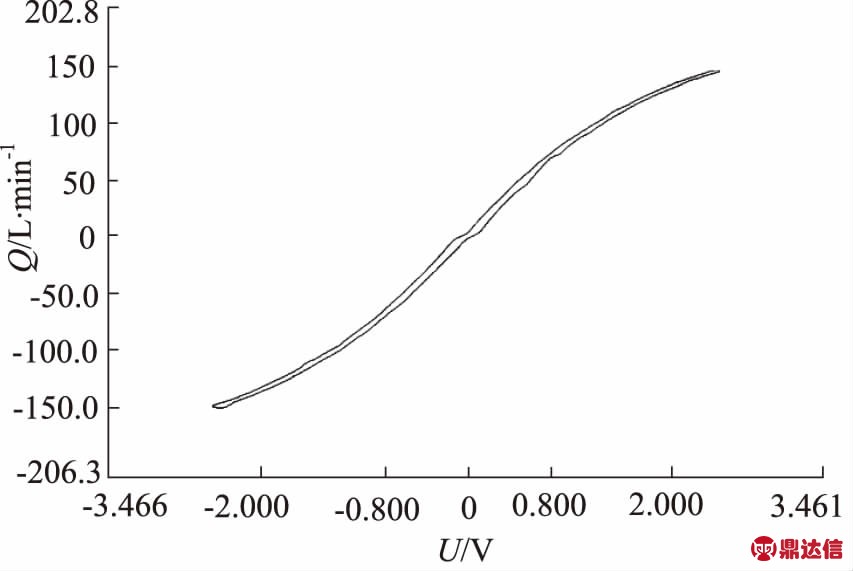
图9 2#采取线性补偿后的空载流量曲线
4 结论
本研究针对滑阀内泄漏造成阀控缸液压系统油缸的自走现象,提出了一种增大滑阀中阀芯和阀套搭接量的低泄漏滑阀方案,并进一步提出了采用多区间流量增益补偿技术方案以确保滑阀空载流量的线性特性,最后通过试验比对验证了其可行性。该方案使阀兼具了良好的线性流量特性和低内泄漏量,为解决阀控缸液压系统的油缸自走提供了一种解决思路。