摘 要: 依据QC/T35—2015《汽车与挂车气压控制装置技术要求及台架试验方法》和企业测试要求,基于工控机、PCI高速数据采集卡,电气比例阀,气控电磁阀等研发复合式干燥器的专用在线检测装置,能够完成复合式干燥器的切断压力、回座压差、开启压力、关闭压力、动态关闭压力的在线检测。系统气压测量范围为0~1.6 MPa,气压测量准确度为0.1%,数据采集频率为1 000 Hz;上位机部分使用LabVIEW编程,能够实现检测流程的自动化和测试数据管理功能。对测试系统进行大量重复性实验表明该检测系统能够准确高效地检测复合式干燥器的性能且测试系统稳定,满足企业测试要求。
关键词: 自动化; 在线检测; 汽车制动部件; 计算机控制
0 引 言
复合式干燥器主要用于车载空压机压缩空气的清洁干燥以及整车制动系统供气管路的保护。复合式干燥器通过分子筛干燥筒实现压缩空气的清洁和干燥,避免不洁净空气对汽车制动回路造成腐蚀,导致制动性能的下降或失效;复合干燥器通过内部分流机构把供气管路分成四路,结合单向调压阀实现四路供气回路的保护,各回路可独立工作,其中任何一个回路失效时,其他供气回路都能正常工作,确保汽车制动系统的安全。
2013年,水电局在部党组的正确领导下,认真贯彻落实党的十八大和十八届三中全会精神,按照中央加快水利改革发展决定提出的“大力发展农村水电”,“在保护生态和农民利益前提下,加快水能资源开发利用”的要求,积极转变发展方式,全力推进民生水电、平安水电、绿色水电、和谐水电建设,中央投资30.8亿元,比2012年增加了108%,协调国家农发行出台了农村水电信贷支持政策,全年完成投资240亿元,新增装机200多万kW,总装机超过6 800万kW,年发电量2 000多亿kWh,很好地完成了各项工作任务。
目前我国对于空气干燥器检测技术的研究主要还集中在传统干燥器的性能检测上[1-2],原有的空气干燥器只有过滤功能,新型的复合式干燥器在此基础上增添了保护功能,国内目前有万安、瑞丽、东科等企业生产复合式干燥器,但厂家对于复合式干燥器的检测仍处于用压力表检测的阶段,检测效率低、检测精度差,且国内对于集合分路和安全保护功能的复合式干燥器的检测尚没有相关文献研究;而国外的检测设备如威柏科等公司研发的检测台虽检测精度高、检测技术全面,但价格昂贵、维护成本高且技术对外保密,不符合我国厂商的实际情况。作为一个新产品,复合式干燥器在量产过程中,需要对产品的密封性、压力控制特性进行在线检测,确保生产质量。因此通过研究复合式干燥器的工作原理,设计复合式干燥器在线检测系统,有重要的现实意义。
1 复合式干燥器测试需求分析
1.1 复合式干燥器工作原理
复合式干燥器的内部结构如图1所示。
来自空压机的压缩空气经1口进入A腔,干燥后的空气经F腔后一部分气体经单向阀H后直接由22口输出到其他几条回路;同时一部分气体进入O腔。当出气口22的气压达到输入口的开启压力时,气压克服弹簧的力,打开阀门T,推动排气活塞W,A腔的杂质从排气口3排出。在排气的瞬间单向阀H关闭,气压就会返回来,通过回流孔与节流孔冲干燥筒。在回流的同时当膜片K上边的压力降到关闭压力时,回流结束。排气活塞W有调压的作用,在压力过高的情况下,W将打开阀门B进行排气。输出口22气压降低到关闭压力时,阀门T和B关闭,干燥器再次向输出口供气。由22口的气体到达输出口的a腔。当气压达到设置的开启压力时,气压克服弹簧力打开各腔阀门B进入21、22、23、24回路。如果供气过程中供气回路失效,4条回路的空气将从失效回路中泄漏,直到气压降到其动态关闭压力,弹簧力使阀门B关闭[3-4],保证了汽车在一条管路失效的情况下,其他管路仍有一定的气压进行控制。提高了汽车行驶的安全性。
绵羊、山羊、牛非胃肠道给药可用于治疗革兰氏阳性菌和革兰氏阴性菌引起的呼吸道感染,肌注林可霉素-大观霉素还可用于治疗绵羊的恶性腐蹄病,Venning(1990)等报道按1 ml/10 kg林可霉素-大观霉素(每ml含有50 mg林可霉素和100 mg大观霉素)肌注给药治疗绵羊的恶性腐蹄病,其治愈率为92.5%,效果优于肌注青霉素-链霉素。
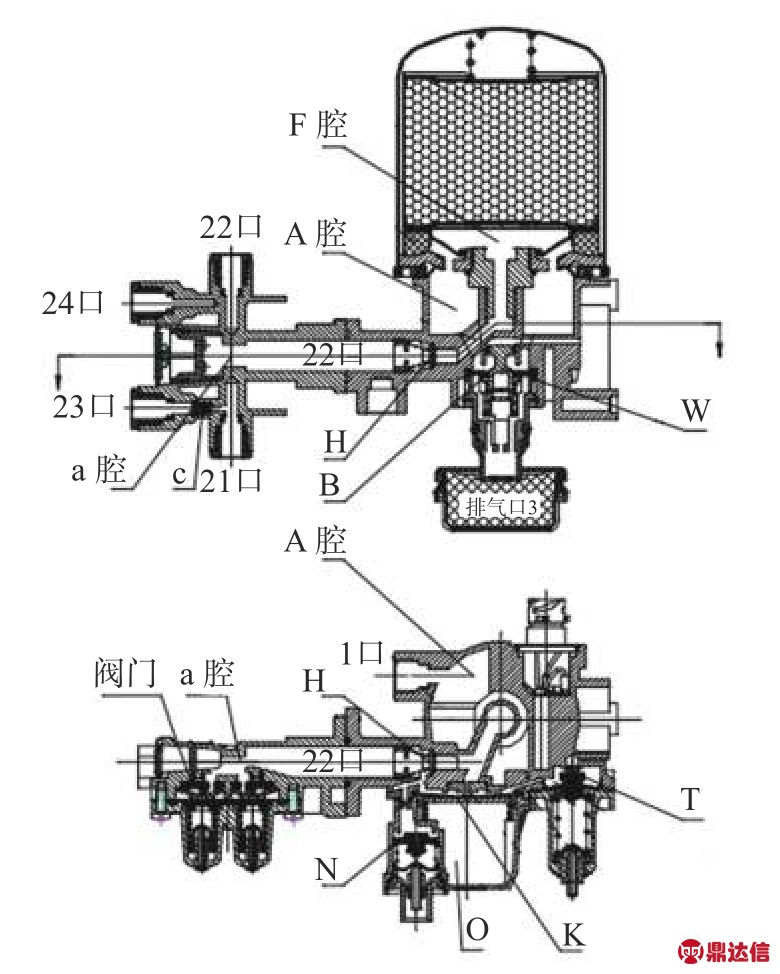
图1 复合式干燥器结构图
其中根据国内主流厂家要求及查阅相关技术参数,性能测试项目:切断压力不大于 1 050 kPa、回座压差小于150 kPa、开启压力大于690 kPa、关闭压力大于 200 kPa 及动态关闭压力大于 550 kPa[5-6],这些技术指标决定了复合式干燥器的控制压力特性性能。
1.2 需求分析
通过分析复合式干燥器的内部结构和工作原理,得出密封的膜片和阀座以及外壳壳体均存在泄漏的可能性,在正常工作中阀体可能因为泄漏而失去足够的气压驱动制动阀工作,根据汽车行业标准QC/T 37—2011 规定:在常温,工作气压下,5 min 内密封性指数不大于20 kPa,视为产品合格。通过状态转换参数将行业标准的5 min转化为10 s,提高检测效率[4]。
鼻内镜下严重外伤性歪鼻畸形肋软骨整形及同期鼻中隔偏曲矫正一例(何川 秦喜昕 吴晓平 杨俊慧)5∶389
通过分析复合式干燥器的内部结构和工作原理可知,其内部输入口部分的自动调压功能、分配给用于反吹的气体体积及反吹时所花费的时间,输出口的开启压力、关闭压力及动态关闭压力对于其整体性能的实现至关重要[5-6]。参考上述相关要求,设计一个模拟拥有充放气及快速排气功能的系统,其中产品压力特性中切断压力需达到1 050 kPa,为保证气源稳定性,供气气压范围设定为0~1.6 MPa,采用气液增压器和电气比例阀实现气压的精准控制,厂家要求选用测量准确度为0.1%的气压传感器测量气压,采用测量准确度为0.1%的差压传感器测量密封性[7],为实现进出气口气压、时间等数据的采集,设计一个数据实时采集与控制系统,具备模拟量输入(AI)、模拟量输出(AO)、数字量输入(DI)、数字量输出(DO)等功能,系统采样频率设置为1 000 Hz,满足高速采集的要求。复合式干燥器在线检测系统的指标如表1所示。
表1 复合式干燥器在线检测系统技术要求
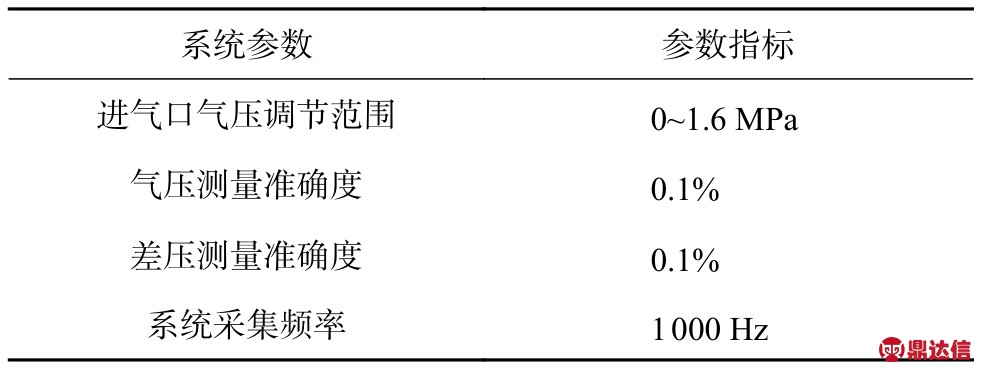
系统参数 参数指标进气口气压调节范围 0~1.6 MPa气压测量准确度 0.1%差压测量准确度 0.1%系统采集频率 1 000 Hz
2 在线检测系统设计
在线检测系统需满足快速、安全、可靠的能力,因此本系统设计包括了检测气路设计与检测方法设计,数据采集系统设计及系统快速装夹设计。本系统包括硬件部分和软件部分,硬件部分由工控机、高速数据采集卡、供电系统、电磁阀、电气比例阀、气压传感器及工装夹具组成。软件部分采用Lab-VIEW平台编写,负责数据采集后的数据处理、人机交互及各硬件部分的协调与控制。
2.1 检测气路设计与检测方法设计
对复合式干燥器工作原理及系统总体结构进行分析,系统由气压传感器、差压传感器、电气比例阀、电磁阀、气控阀、手动球阀、储气罐、消音器、平衡阀、针阀及夹具工装组成。系统气路原理图如图2所示,进气口和输出口安装有量程0~1.6 MPa,准确度为0.1% 的气压传感器,实现实时监控气压功能;电磁阀控制系统气源通断及测试管路;电气比例阀实现对气压的精确调控;气控阀的管路口径较大,能瞬间通过大量的气体,用于模拟行车过程中管路突然爆裂;针阀通过调节其本身的旋钮增加或减少气体的充放速度。
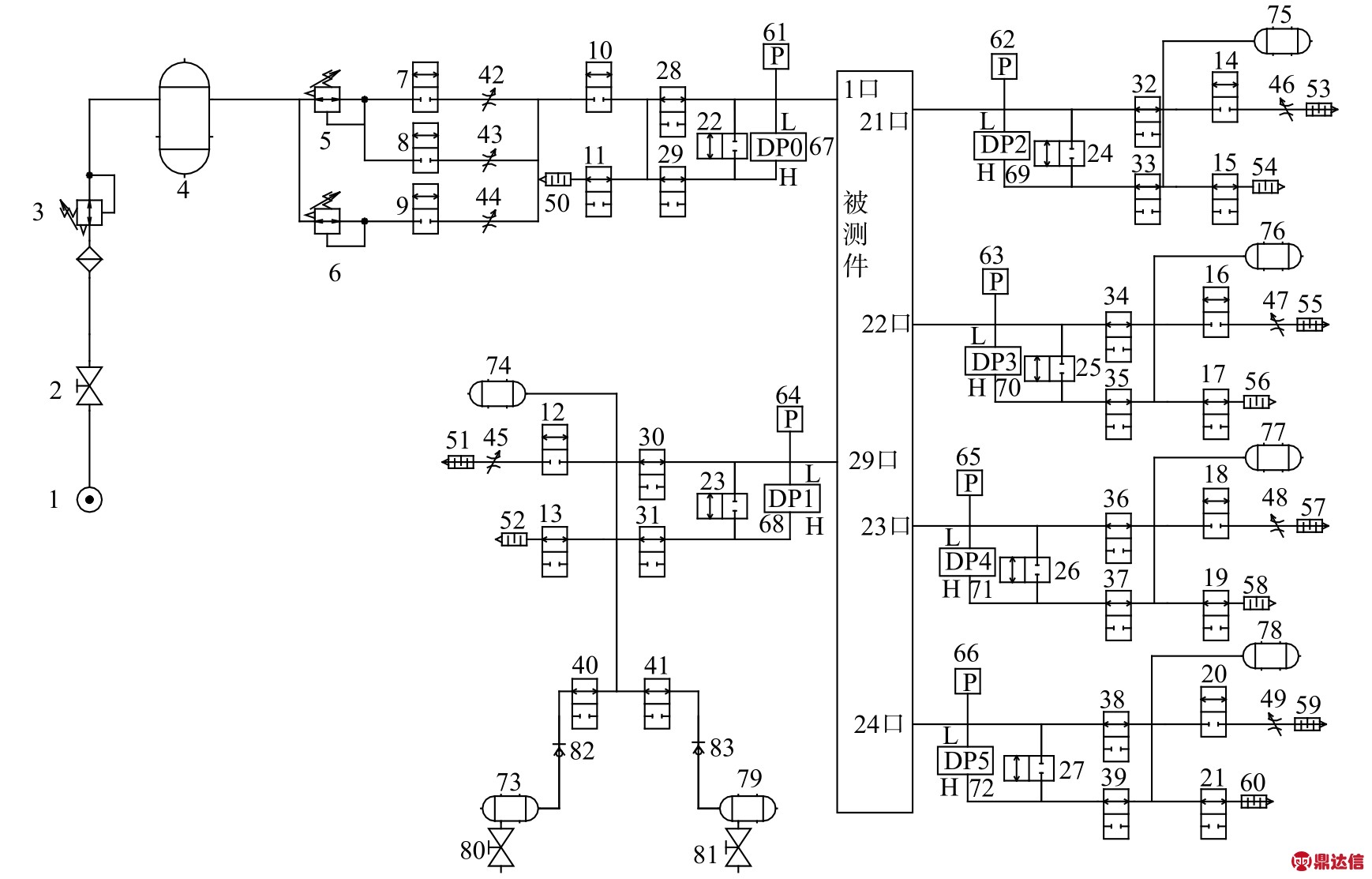
图2 系统气路原理图
1.气源; 2.手动球阀; 3.过滤减压阀; 4.20 L 储气罐; 5~6.电气比例阀; 7~10.进气电磁阀; 11~21 排气电磁阀; 22~27.平衡阀;28~41.气控阀; 42~49.针阀; 50~60.消声器; 61~66.气压传感器; 67~72.差压传感器; 73、79.40 L 储气罐; 74~78.1 L 储气罐;80、81.手动球阀; 82~83.单向阀。
压力特性测试主要分为输入口压力特性测试及输出口压力特性测试。输入口部分压力特性测试测量切断压力时,打开进气电磁阀10,平衡阀22~27,气控阀32~39,进气电磁阀7~9,对产品进行充气,待气压传感器64检测到29口气压突然降低时,获取64的示值,并且记录时间,此时64的示值就是待测件的切断压力,从29口排出的气体进入设备选择的负载腔,随后负载腔开始对产品进行反吹,待检测到产品29口压力趋于稳定时,记录此时29口的压力与时间,用切断压力减去29口测得的示值,即为压降。压降乘以设备选择的负载腔除以101 kPa即为复合式干燥器的再生容积,用此时测得的时间减去测得切断压力时的时间得到待测件的回流时间。随后待检测到1口压力回升时记录此时29口的压力,用切断压力减去29口的压力得到回座压差。
输出口压力特性测试时首先测量输出口部分的开启压力,打开进气电磁阀10,平衡阀22~27,气控阀30~39,进气电磁阀7、8以及储气罐73和79,随后以一定速率充气,之后测量21口开启压力时22、23、24口的平衡阀打开,待检测到21口的压力突然变大时,记录此时气压传感器62的示值,得到21口的开启压力,同理可测得22、23、24口的开启压力。
其次测量关闭压力及动态关闭压力,测量时打开进气电磁阀10,平衡阀22~27,气控阀28~31,进气电磁阀7、8以及储气罐73和79,以一定速率充气。测量关闭压力时,打开21口排气电磁阀14,产品开始以一定速率排气,阀门关闭,其他3个输出口压力趋于稳定时传感器62的示值为21口关闭压力,另外3个输出口关闭压力测试方法同21口;测量动态关闭压力时,充气完成后关闭1口与29口的进气电磁阀10,平衡阀22、23,气控阀28~31及29口排气电磁阀12进行快速排气,待输出口压力输出趋于稳定时的压力即为动态关闭压力。
整体密封性测试和输出口密封性测试选用差压检漏法,在基准腔将测试分为充气、平衡、测量、排气4个过程,通过1口的差压传感器67测得整体密封性指数,通过29口的差压传感器68测得输出口部分密封性指数,通过21~24口的差压传感器测得输出口单向阀密封性指数。
2.2 数据采集系统设计
图3为数据采集系统设计。系统共有12路AI输入,2路AO输出,7路DI输入及30路DO输出,选用研华的PCI-1711U与PCI-1730U,PCI-1711U具备 16通道单端 A/D输出,12 bit A/D转换,最高采样频率达 100 kHz[8-10],PCI-1730U具备 32路隔离数字量输入/输出,满足测试系统需求。
当前阶段,共识算法呈现出百花齐放的态势,例如2-hop[10],限制51%攻击者在拥有51%以上算力的同时还需要拥有51%以上的权益。目前燃烧证明(PoB)、活跃证明(PoA)等共识机制成为了新研究方向。另外,存在共识算法在PoW基础上添加了Ghost协议,将无用的挖矿算力转换为解决有效问题。这些算法大多是PoW、PoS或者传统一致性算法的改进或混合,《区块链共识算法发展现状与展望》[3]一文将当前的共识协议进行总结并对其脉络进行梳理,指出了共识协议的发展方向。
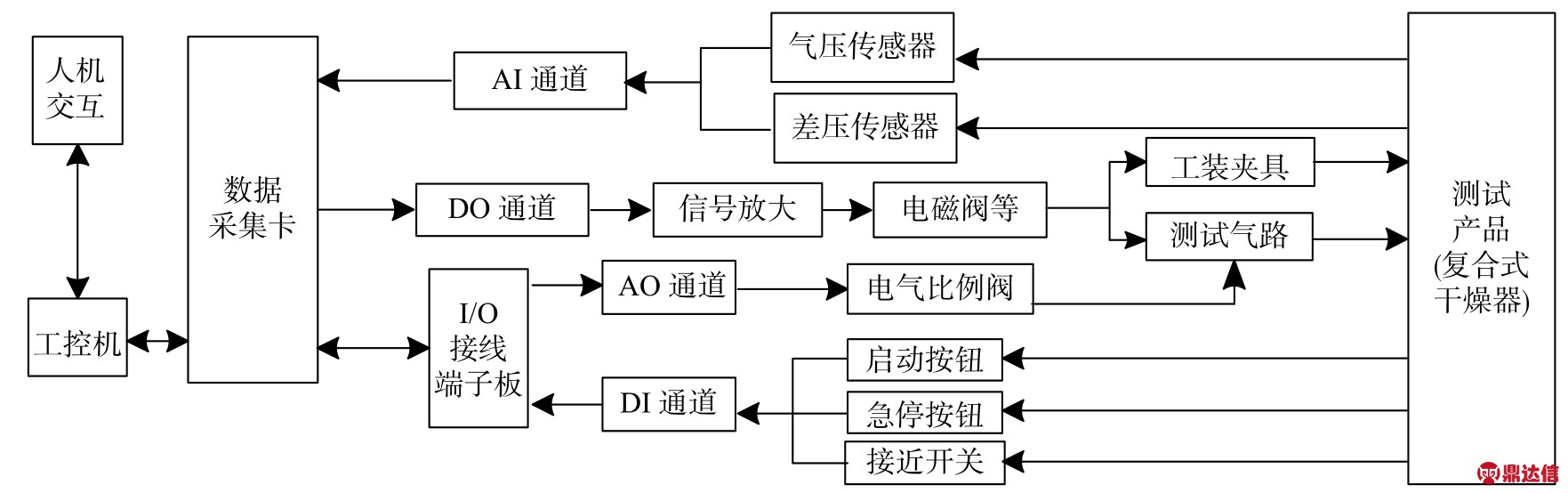
图3 数据采集系统设计
2.3 系统快速装夹设计
本测试系统旨在用于工业生产线上的快速测试,应满足快速装夹的功能,系统快速装夹的机械工装由如图4所示。被测件直接放置在工装的产品座上,产品座是固定不动的,待测件上侧和右侧分别有带封堵堵头的气液增压缸和侧封气缸,待测件左侧由带有封堵堵头左侧工装进行密封。开始测试时,侧封气缸及下压气缸实现横向和纵向向待测件压紧,配备磁性开关来调整侧封气缸及下压气缸的限位,实现对待测件的快速装夹,同时本系统带有安全光栅可实现实时保护的功能,从而使系统工作高效、安全、可靠。
师:同学们,今天我们要到云贵高原的大山深处,去欣赏一曲悲壮的生命之歌。下面请同学们读课文《生命的壮歌》,并请你在书上做上适当的标记和必要的记录,读完后请在小组内谈谈你的阅读感受。(学生读完)
3 测试数据分析
3.1 密封性数据分析
利用所设计的检测系统对某型号复合式干燥器的性能进行测试,在常温,工作气压为1.6 MPa的条件下进行试验,在软件界面参数设置成功后按下启动按钮,对复合式干燥器的密封特性及压力特性进行自动化检测,密封性检测首先检测的是整体密封性,依据相关行业标准及厂家相关技术指标,密封性测试需求在测试时不得大于0.6 kPa,测得的密封性曲线如图5所示,测得密封性指数如表2所示,在 10 s内,1 口的差压值不大于 0.2 kPa,标准差为0.009 kPa,产品合格且一致性较好。
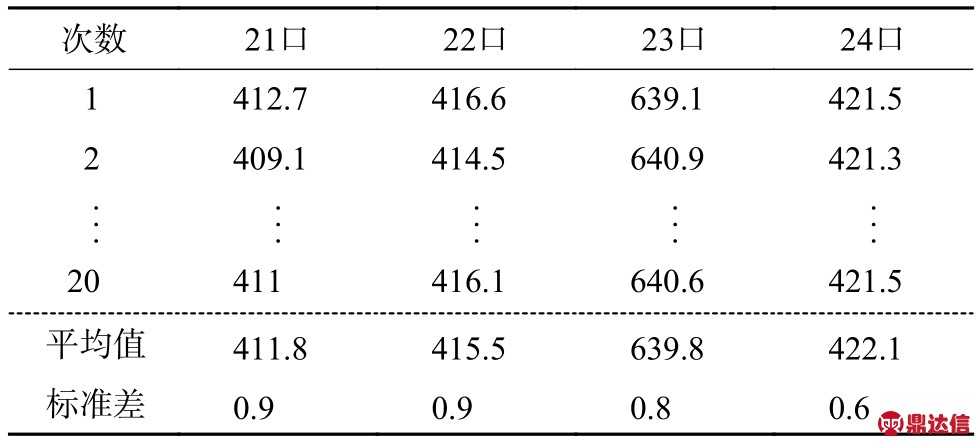
图4 机械工装夹具图
1.气液增压缸; 2.侧封气缸; 3.待测件; 4.封堵堵头; 5.固定底座;6 夹具底板; 7.螺丝刀。
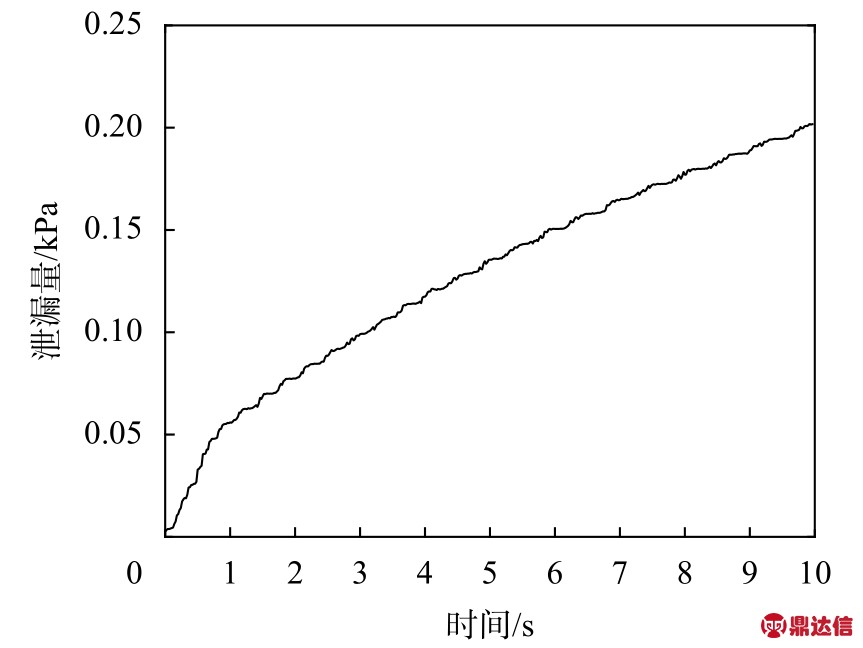
图5 1口整体密封性测试曲线
整体密封性测试完后进行输出口部分密封性检测,测试结果见表3,在10 s内输出口差压值不大于 0.025 kPa,标准差为0.011 kPa,产品合格且一致性较好。
输出口整体密封性测试后进行输出口单向密封性测试,测试结果见表4,10 s内 21、22、23、24 口差压值均不大于0.11 kPa,标准差分别为0.013,0.007,0.012,0.007 kPa,产品合格且一致性较好。
表2 整体密封性测试结果 kPa

序号 结果1 0.201 2 0.201......20 0.190平均值 0.199标准差 0.009
表3 输出口整体密封性测试结果 kPa
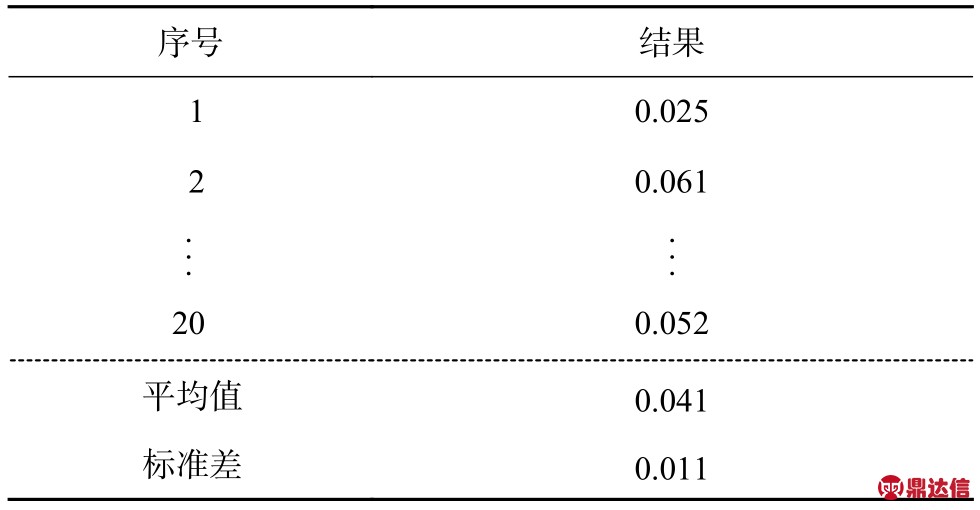
序号 结果1 0.025 2 0.061......20 0.052平均值 0.041标准差 0.011
表4 输出口单向密封性测试结果 kPa
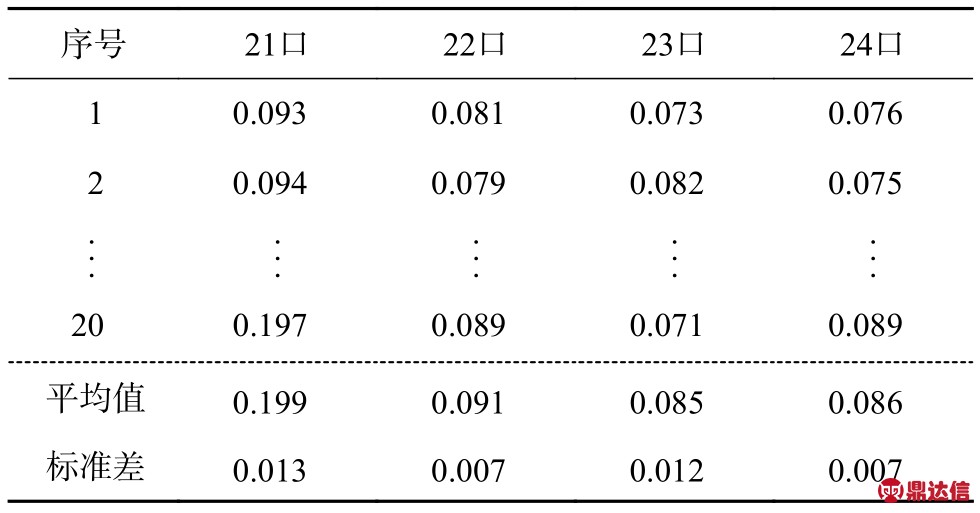
?
3.2 压力特性分析
首先对待测件进行切断压力、回流时间、再生容积的检测,实测曲线如图6所示,结果参照表5。

图6 切断压力气压变化曲线
表5 切断压力测试结果 kPa
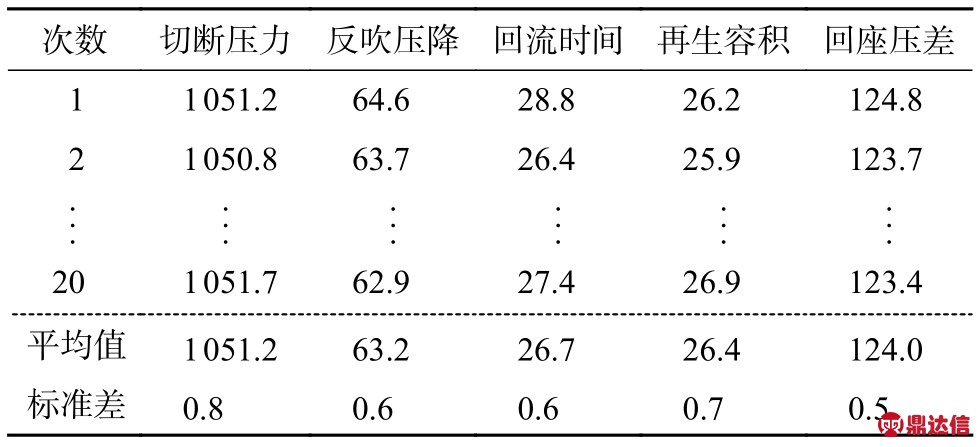
?
由图6及表5可知,切断压力的测试均值为1 051.2 kPa,回座压差的测试均值为124 kPa,产品合格。切断压力等压力特性分析完成后系统自动进行开启压力的测试,图7为开启压力测试曲线,表6为开启压力的测试结果。
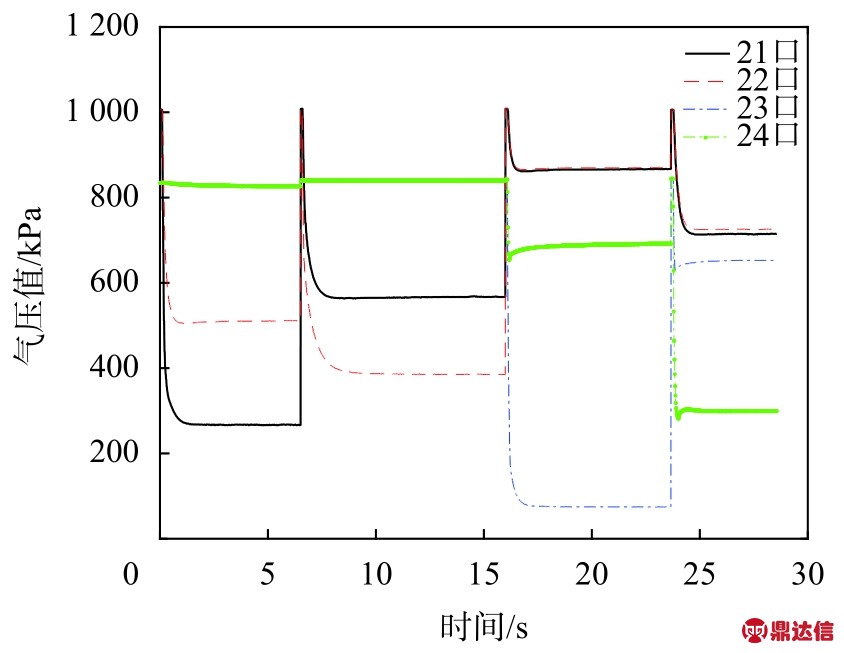
图7 开启压力测试曲线
表6 开启压力测试结果 kPa
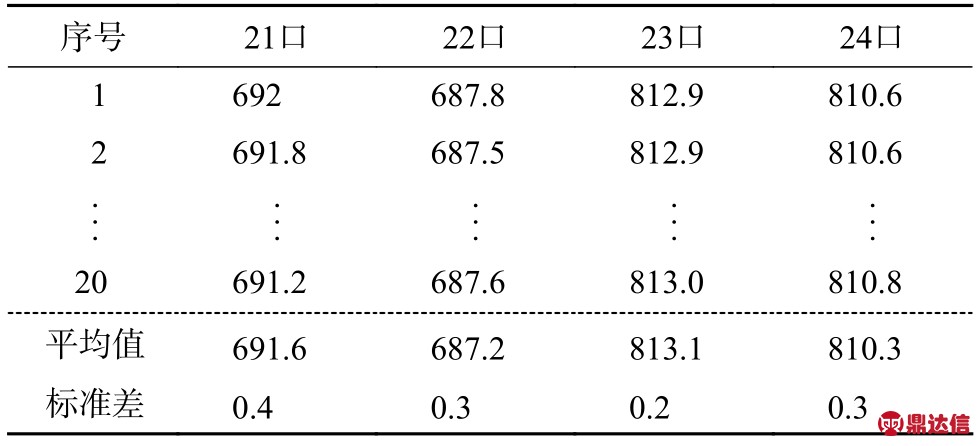
序号 21口 22口 23口 24口1 692 687.8 812.9 810.6 2 691.8 687.5 812.9 810.6...............20 691.2 687.6 813.0 810.8平均值 691.6 687.2 813.1 810.3标准差 0.4 0.3 0.2 0.3
由图7及表6可知,21、22、23、24口开启压力值的测试均值分别为691.6,687.2,813.1,810.3 kPa,产品合格,开启压力测试完成后系统自动选择测量关闭压力,关闭压力是在输入口关闭气源输入的情况下其它输出口所能保持的压力值,输出口的压力要求为不小于200 kPa,测试曲线如图8所示,测试结果如表7所示。
由图8及表7可知,21、22、23、24口关闭压力值的测试均值分别为411.8,415.5,639.8,422.1 kPa,产品合格,关闭压力测试结束后系统自动选择测量动态关闭压力,动态关闭压力的测试曲线和测试结果如图9和表8所示。
Dochy等人和Gijbels等人都就问题导向式学习(PBL)有效性的元分析得出了研究结果。这些结果也显示了PBL在技能上的影响是积极的,而它在知识上的影响则是负面的。综合结果表明了问题导向式学习整体上具有负面影响。Gijbels等人在衡量问题导向式学习效果时建议认真考虑评估方式。
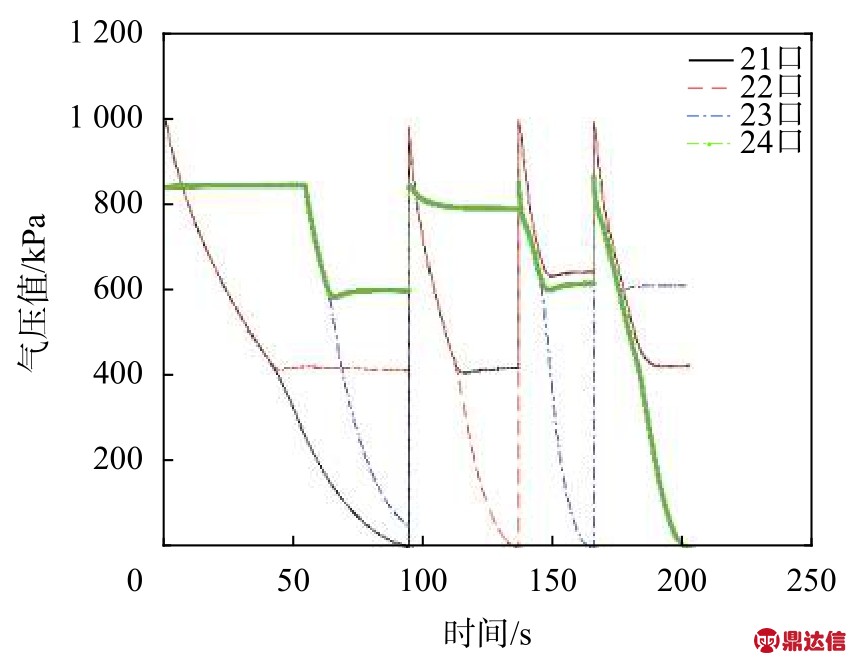
图8 关闭压力测试曲线
表7 关闭压力测试结果 kPa
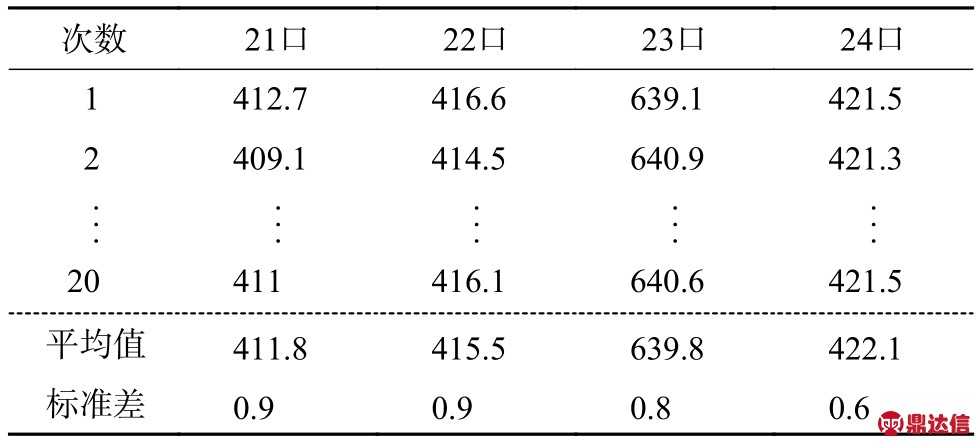
?
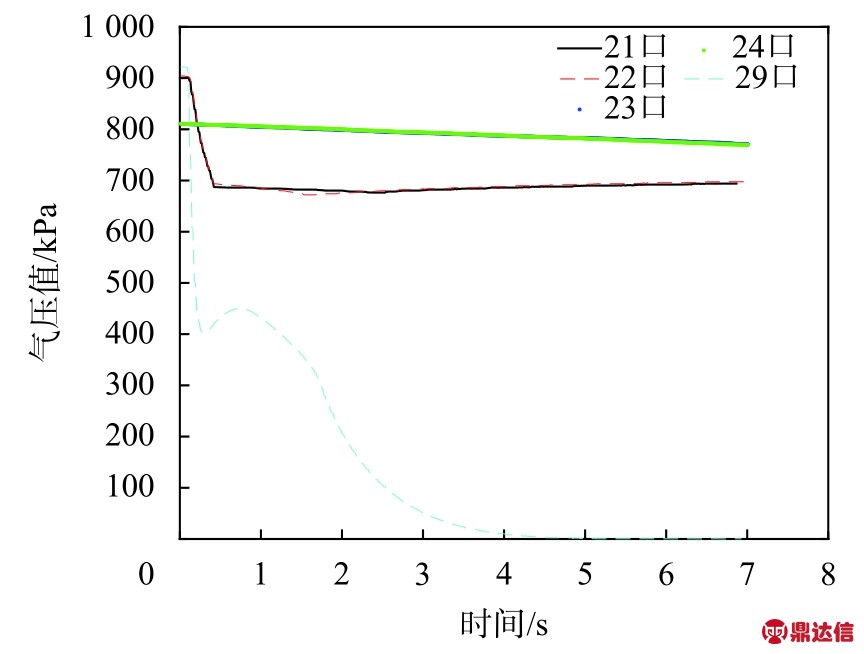
图9 动态关闭压力的测试曲线
表8 动态关闭压力的测试结果 kPa
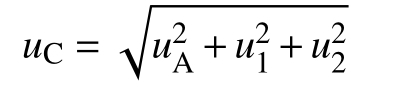
次数 21口 22口 23口 24口1 695.7 696.3 792.5 790.1 2 694.6 694.4 789.4 788.3...............20 695.6 696.1 792.7 789.1平均值 695.1 696.3 792.0 789.1标准差 0.6 0.5 0.7 0.7
由图9及表8可知,21口、22口、23口、24口动态关闭压力的测试均值分别为695.1,696.3,792.0,789.1 kPa,产品合格。
4 检测系统不确定度分析
根据JJF1059—2012《测量不确定度评定与表示》中不确定度的定义及评定要求,对检测系统进行不确定度评定。测量系统的不确定度主要由测量重复性误差、数据采集卡和气压传感器的测量误差引起的。测量重复性引起的不确定度分量uA用A类方法评定;气压传感器引起的测量不确定度u1与数据采集卡引起的测量不确定度u2采用B类评定[11]。
气压传感器与差压传感器的准确度为0.1%,在量程内引起的最大误差为1.60 kPa 与 0.006 kPa,属于均匀分布。数据采集卡的误差是由量化误差、偏移误差和增益误差组成,通过计算得出量化误差为2.44 mV对气压和差压造成的不确定度u2影响分别为0.623 kPa及 0.004 kPa。系统合成不确定度为:
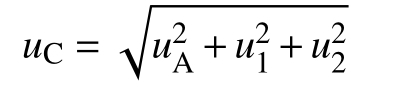
根据上述公式计算出uC,结果如表9所示。密封性合成不确定度最大为0.008 kPa,压力特性最大合成标准不确定度为1.729 kPa。由此可知设备重复性较好。
根据学生的操作过程,评价如下:要素1,能执行探究方案中规定的大部分步骤,动作不够规范,如不会稀释溶液,量取根的长度误差较大等,故给1分;要素2,能准确地描述实验现象,记录实验数据,故给2分;要素3,未重复收集数据,故给1分;要素4,处理数据时删除了个别出入较大的数据,故给1分。得分5分(总分10分)。
表9 合成标准不确定度表 kPa
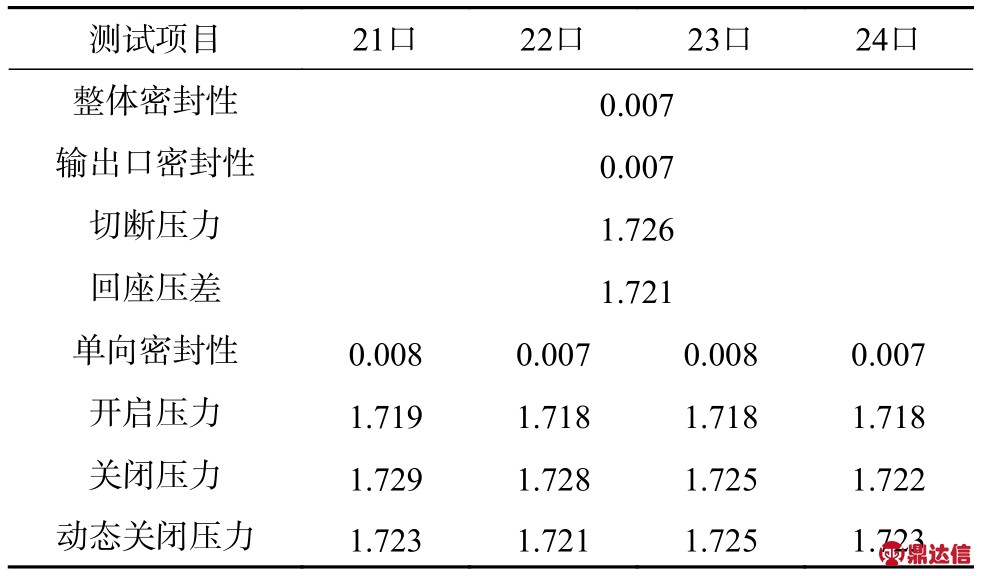
测试项目 21口 22口 23口 24口整体密封性 0.007输出口密封性 0.007切断压力 1.726回座压差 1.721单向密封性 0.008 0.007 0.008 0.007开启压力 1.719 1.718 1.718 1.718关闭压力 1.729 1.728 1.725 1.722动态关闭压力 1.723 1.721 1.725 1.723
5 结束语
在分析复合式干燥器工作原理的基础上,根据汽车制动行业的标准及与工业生产需求相结合设计了复合式干燥器在线检测系统,完成系统结构设计,检测气路设计,系统快速装夹设计及系统软件设计。采用不确定度分析方法得出密封性合成不确定度为0.008 kPa,压力特性合成标准不确定度为1.729 kPa。实验结果表明,复合式干燥器在线检测系统运行平稳,检测数据有效可靠,满足汽车行业标准气制动部件的检测要求及工业上在线检测的要求。