摘 要:根据高速盘用户不同的要求,对高速盘端盖成型工艺特点进行分析研究,给出两种不同的工艺方案:模具冲压成型工艺与专机旋压成型工艺。针对不同的成型工艺分别介绍模具结构及模具冲压注意的问题、专机旋压成型机结构及专机旋压过程、注意事项。两种方案工艺特点与用户要求相适应,使生产工艺成本最优,具有很好的推广价值。
关键词:预弯;卷圆;模具冲压成型;旋压装置
0 引 言
高速电缆盘的规格很多,根据不同厂家要求外径多达10种,但主要有630 mm与710 mm两种;板厚为2.5~6.0 mm,但主要为5 mm与6 mm。用户技术标准与批量要求主要分两种:国外用户批量大、品种集中、技术要求高,国内用户批量小、品种多、技术要求比国外低。高速电缆盘生产制造中最繁琐的工作是制作端盖,图1所示为高速电缆盘的端盖,端盖主体由圆形板料周边卷圆而成。根据高速盘用户不同的要求,对高速盘端盖成型工艺特点进行分析研究,给出两种不同的工艺及装备方案,使工艺成本降到最低。
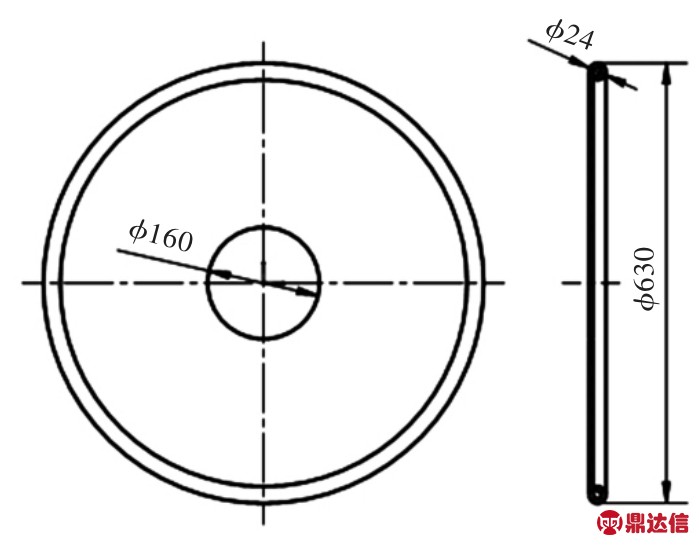
图1 端盖零件图
1 成型分析及工装改进
1.1 成型工艺分析及工序图设计
高速电缆盘的端盖由2.5~6.0 mm的圆形钢板周边卷圆而成。由于卷圆是由圆盘径向卷入,径向缩小使变形区材料增多,相对普通卷圆板料变形更剧烈,且板料易产生失稳变形。经分析,解决变形力过大及板料失稳是该制件卷圆成功的关键。经研究,有两种工艺方法可解决上述问题:模具冲压成型工艺和专机旋压成型工艺。
1)模具冲压成型工艺可把卷圆工作分开完成,工艺如图2所示:模具落料冲孔→模具翻边→车床倒圆角→模具卷圆。其中模具翻边、模具卷圆工序共同完成卷圆工作。模具翻边工序完成两项任务:a. 完成90°的卷圆工作量;b.把扇形平板料变成立体环形料,使板料形状按有利于卷圆布置。模具卷圆工序只完成180°的卷圆工作量。这样使两工序变形程度都降低,变形力变小,板料抗失稳能力增强[1]。
2)专机旋压成型工艺的特点相当于把卷圆工序分多次完成,工艺如图3所示,预弯可使卷圆时不易失稳。旋压卷圆过程是板料逐渐变形的过程,变形区较小,另外旋压过程会产生热量,材料的塑性提高,可以达到解决变形力过大及板料失稳的要求[2]。
1.2 模具冲压成型工艺注意的问题
产品在试生产过程中易出现如下问题:产品底平面不平、卷圆处板料端头有直线端、产品径向及轴向跳动超差且不稳定。分析原因:初始压料力不够,底板在翻边时产生翘曲变形;翻边板料端头有尖角且局部硬化,使周边卷边料端与模具圆角接触不良,料端变形不充分;模具凸、凹模块翻边间隙与倒圆角不均,造成翻边高度不齐。采取的措施:模具翻边时采用氮气缸压料,布置的氮气缸初始压力按翻边压力28%~35%选取[3];产品翻边后在车床上倒圆角(如图2),保证卷圆时板件端头同时导入且与模具卷边模块R角贴合,另外切除端头冲裁硬化部分减薄端头材料厚度;凸模拼块与凹模拼块分别使用同一块材料加工,粗加工时成型圆角整体车削,分块热处理后重新研合组成一体进行精车,保证成型圆角统一、翻边间隙均匀。
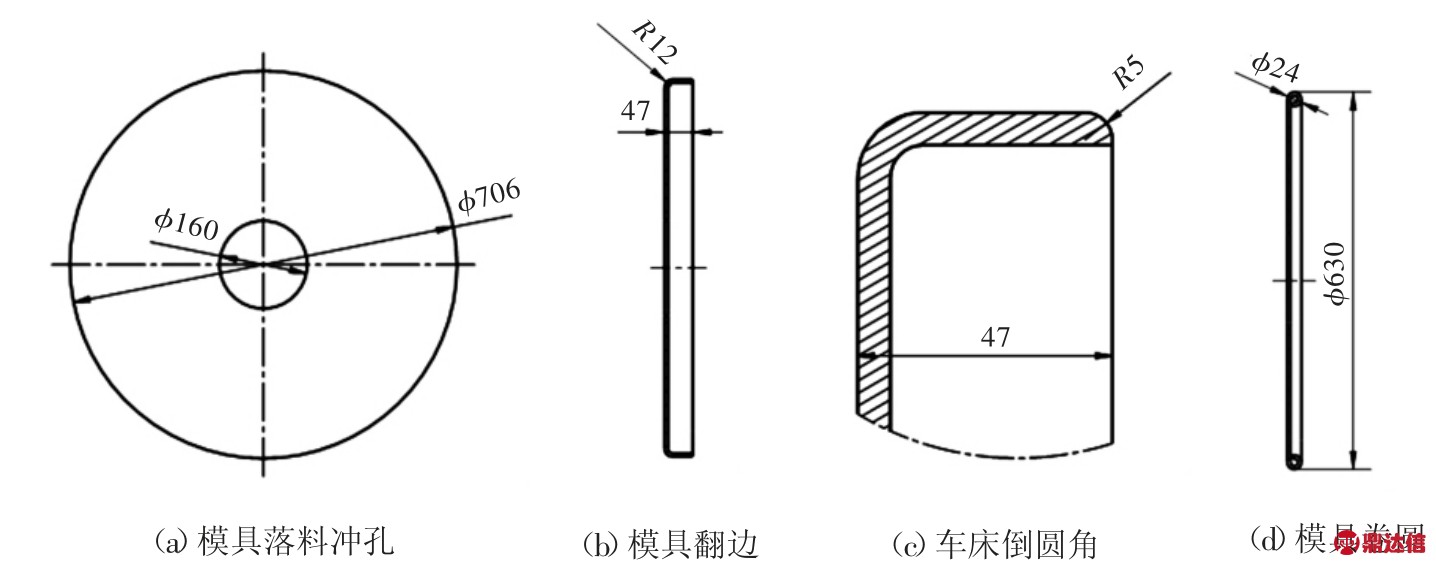
图2 模具冲压成型工艺
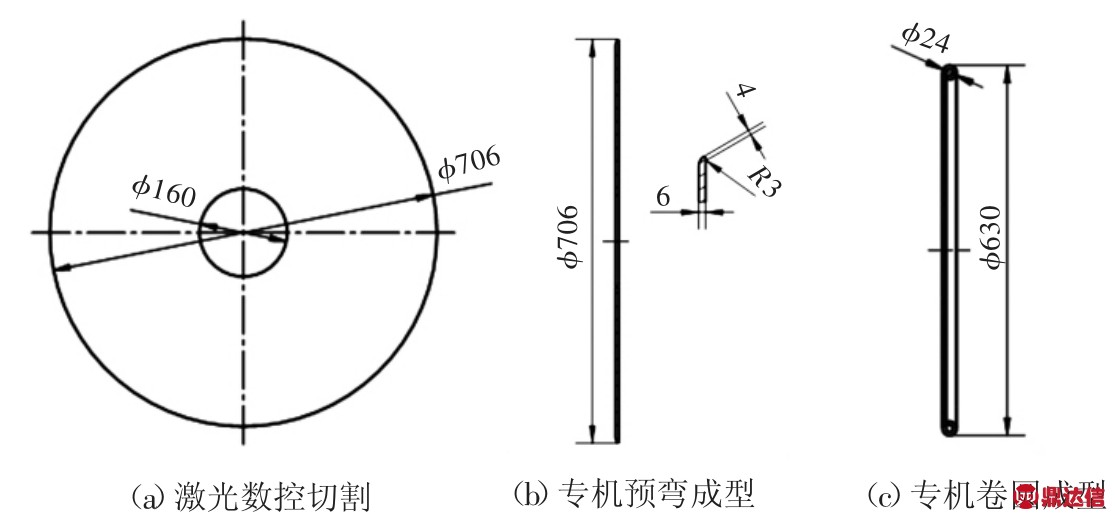
图3 专机旋压成型工艺
1.3 模具结构设计
落料冲孔模结构简单,翻边模具与卷圆模具结构类似,该冲压成型工艺主要难点在于第二工序翻边成型,模具结构如图4所示[4]。
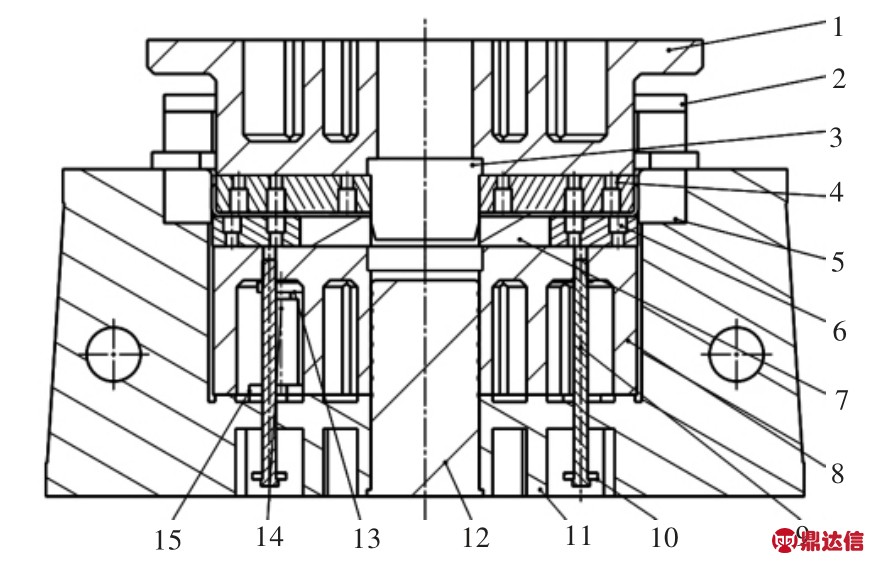
图4 翻边模具结构图
1.上模板2.定位机构3.定位销4.凸模块5.凹模块6.顶料板芯7.顶料板拼块8.顶料板基体9.卸料螺钉10.垫板11.下模板12.导柱13.缸托14.氮缸15.缸垫
1)为保证翻边凸、凹模位置精度,上下模板选用φ60的滑动导柱与导套进行导向;2)板料采用周边粗定位及中间圆孔精定位相结合的定位方式,保证制件稳定;3)压料采用氮气缸,保证工序件翻边时处于受控状态;4)为保证制件精度及模具调整维修方便,凸、凹模采用镶拼式结构。具体形式见图5[5];5)为保证模具有足够的强度与刚度,上下模板采用铸件。
1.4 专机旋压成型工艺注意的问题
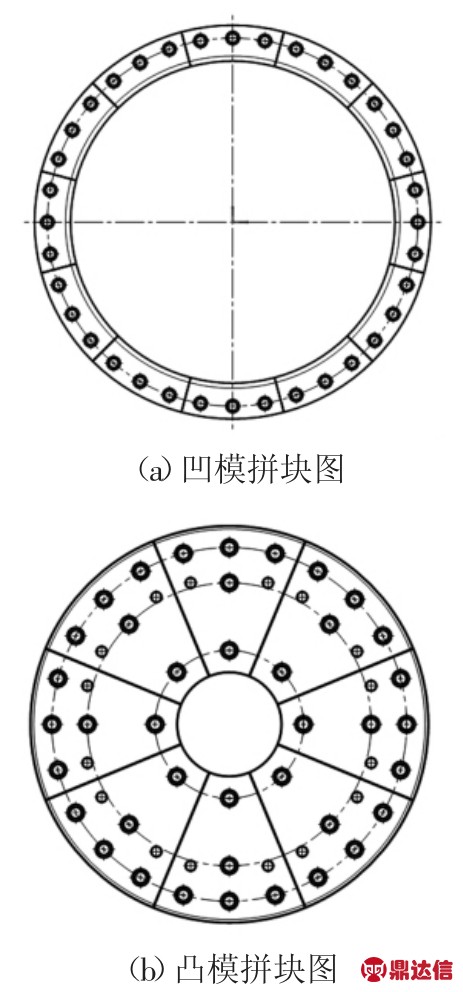
图5 翻边模块图
专机旋压成型工艺主要难点在于预弯工序,预弯不良会使产品卷圆后不规则,主要表现为产品底平面不平、产品径向及轴向跳动超差且不稳定。分析原因:初始压料力不够,底板在预弯时产生翘曲变形;预弯变形区过大且不到位,造成预弯区回弹。采取的措施:专机结构如图6所示,主体采用高强度框架结构[6],压料动力采用大油缸1压料,可根据板料大小更换从动压盘2-4,保证未变形区处于受控状态;对预弯凸、凹模圆角进行回弹修正,使板料端头处凸、凹模间隙小于料厚,预弯后达到图3所示效果,板料端头厚度减薄30%。为保证凸、凹模寿命,建议采用高速钢材料[7]。
1.5 专机旋压成型工艺过程
1)预弯实施过程:打开卷边推进油缸4,使滑块3-4、成型轴3-1、成型轮3-2移出工作位置,将板料工序件放入定位托盘5-1,松开L形导板上的螺栓,调整滑座10-1位置使定轮组件10-3与活动轮组件10-4与板料工序件位置适合,并拧紧螺栓压紧滑座10-1,打开压紧油缸1,从动压盘2-4伸出压紧工件,开动电动机使工件旋转,手工搬动预弯手柄11,活动轮组合10-4绕转轴10-5转动,活动轮组合10-4上的活动轮下移,使旋转的工序件边沿压入定轮,板料在两轮中变形完成预弯。
2)卷圆实施过程:松开L形导板上的螺栓,调整滑座10-1位置使定轮组件10-3与活动轮组合10-4移出工作位置并紧固螺栓,将预弯后的工序件放入定位托盘5-1,打开压紧油缸1,从动压盘2-4伸出压紧工件,开动电动机使工件旋转,操纵卷圆油缸使滑块3-4带动成型轮3-2、成型轴3-1前移,成型轮3-2前移过程中在工序件作用下绕成型轴3-1转动以完成卷圆工作。
该专机卷边机构与预弯机构均可往复移动,使该专机适用于不同直径的产品;该专机电动机为减速电动机,速度可调[8],适用于不同板厚的产品。该专机结构简单,易制造,使用方便,易调整,成本低。
2 结 语
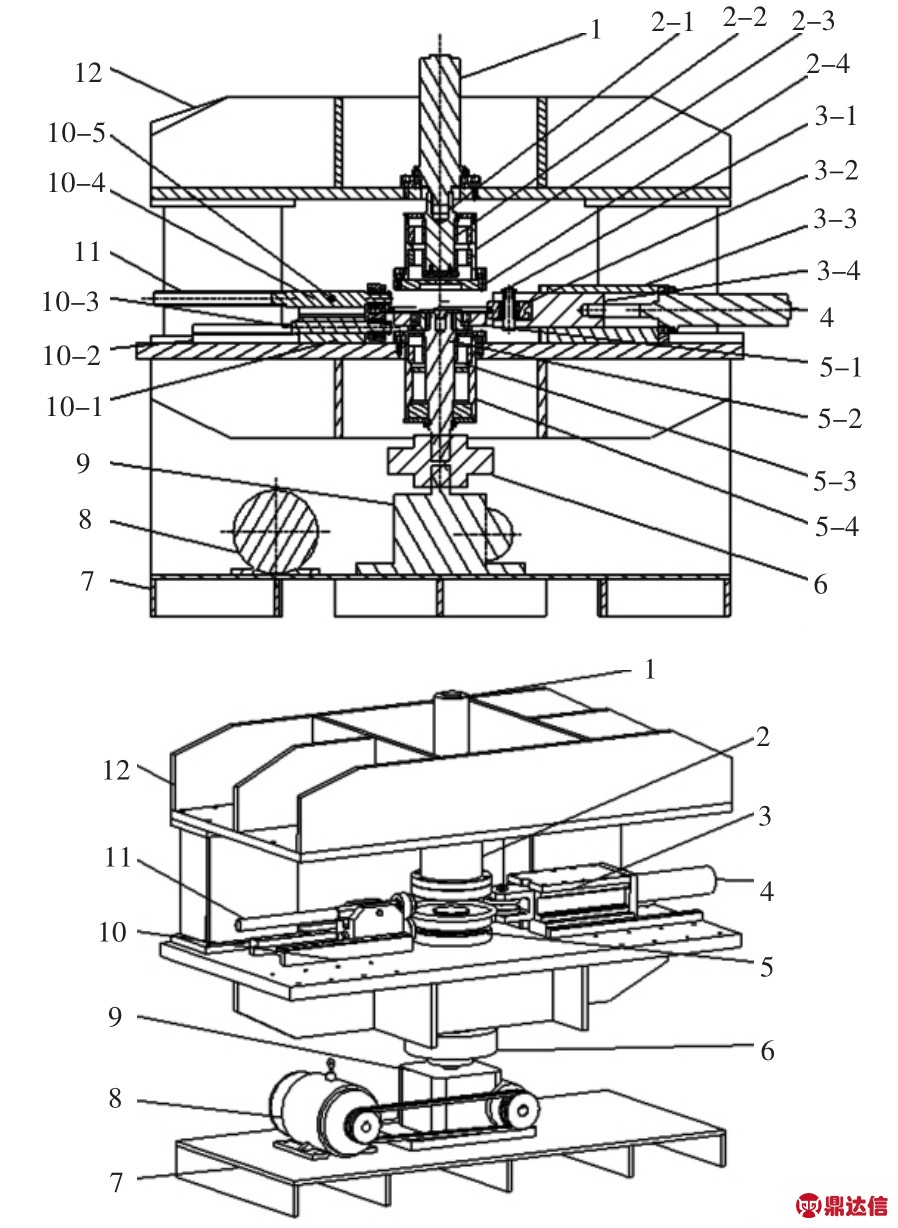
图6 专机结构图及轴测图
1.压紧油缸2.压紧从动机构2-1.第一主轴2-2.第一推力轴承2-3.第一主套2-4.压盘3.卷边机构3-1.成型轴3-2.成型轮3-3.导轨组件3-4.滑块4.卷边推进油缸5.工件定位托盘5-1.定位托盘5-2.第二主轴5-3.第二推力轴承5-4.第二主套6.联轴器7.机架下层8.减速电动机9.减速机10.预弯机构10-1.滑座10-2.L形导板10-3.定轮组合10-4.活动轮组合10-5.转轴11.预弯手柄12.机架上层
1)模具冲压成型工艺。优化后的模具结构及成型工艺可保证产品直线尺寸精度达到0.2 mm以内,端面径向跳动与轴向跳动达到0.3 mm以内,形状面差小于0.3 mm,产品批次稳定,完全达到出口要求。模具操作简单方便、生产效率高,适合大批量生产。
2)专机旋压成型工艺。优化后的专机结构及成型工艺可保证产品直线尺寸精度达到0.3 mm以内,端面径向跳动与轴向跳动达到0.5 mm以内,形状面差小于0.5 mm,卷圆外观质量优,完全达到国内要求。专机操作需有一定的技巧,生产效率低,适合多规格产品小批量生产。