前言:工业过程控制系统用阀门执行器广泛用于工程中的排水、通风、抽采、洒水等管道中。阀门执行器的控制端盖装在阀门执行器控制端,阀门执行器在爆炸极限工况下使用时,腔内压力会迅速增大,导致端盖损坏。通过对现有阀门执行器控制端盖存在的问题进行分析,改进了阀门执行器端盖的结构设计,建立了新的阀门执行器端盖模型并进行了有限元分析,最终通过计算结果验证了设计的可行性。
1 初始结构有限元分析
1.1 有限元前处理
1.1.1 材料选择
阀门执行器端盖的耐压设计是阀门执行器的核心技术之一。不同场合中使用的阀门执行器环境复杂多变,这对阀门执行器端盖的材料提出了严格的要求。目前主流的阀门执行器端盖材料采取铸铝制造,底部圆孔是玻璃,如图1所示。铸铝的性能参数与铝相似,材料属性如表1所示。
表1 材料属性

1.1.2 建立模型
建立阀门执行器端盖三位模型如图2所示。
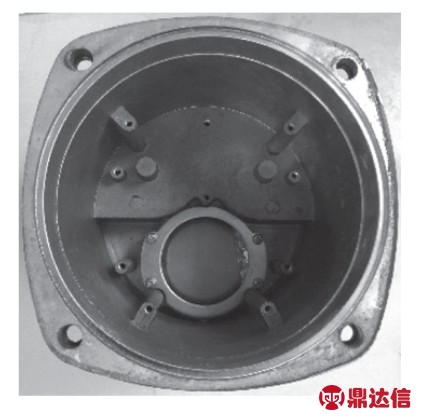
图1 端盖实物图
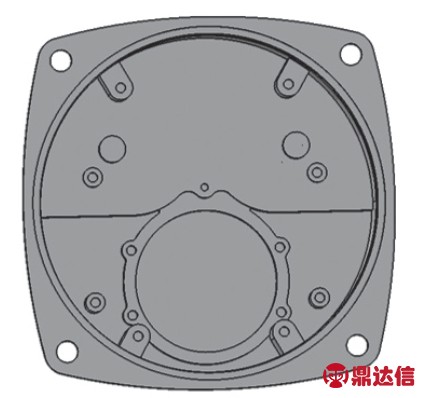
图2 原阀门执行器端盖三维模型
1.1.3 约束条件设置
执行器端盖接触面添加固定约束,爆炸极限工况下阀门执行器端盖最大要承受2.5MPa的压强,因此端盖内表面加载荷2.5Mpa。
1.1.4 网格划分
阀门执行器端盖结构相对简单,采用直接建立单元模型的网格直接生成法,最终得到有限元模型含有31790个节点,16573个网格单元,对网格质量进行检查,纵横比合适。
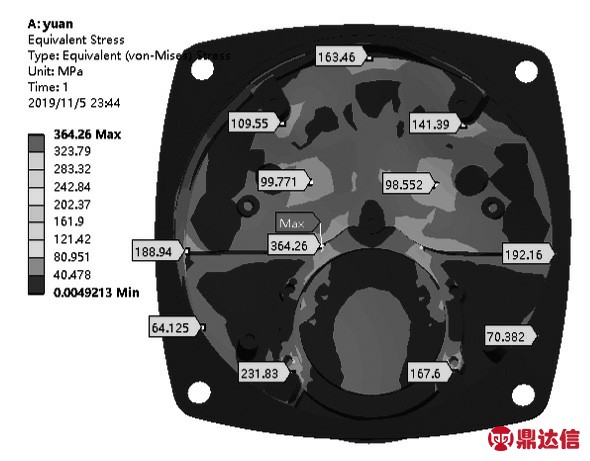
图3 原阀门执行器端盖重点部位应力云图
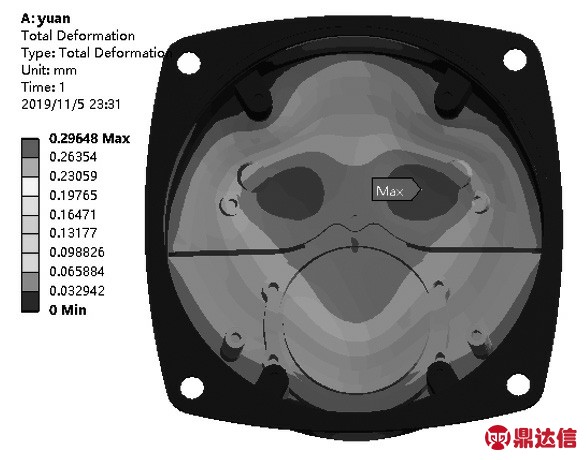
图4 原阀门执行器端盖最大变形处
1.2 有限元分析结果
1.2.1 最大应力
根据仿真结果,阀门执行器端盖在内压2.5MPa的仿真条件下,最大应力为364.26MPa,如图3所示,超出255 MPa,其他应力集中主要发生在端盖内直角的部位。
1.2.2 最大变形量
根据仿真结果,阀门执行器端盖最大变形发生在底部,变形量为296.48µm,结构已近破坏,如图4所示。
1.3 问题分析
根据仿真结果,找出压力集中的位置并分析原因,主要有以下两个方面:
(1)应力集中主要出现在端盖内直角的部位,原因是倒角太小。
(2)底部加强筋设计不合理,导致端盖向外变形,端盖边缘(主要体现为转角处)有一个较大的向外的撕裂应力,最终形成了转角处的应力集中最大。
综合以上分析可知,造成端盖破坏的主要原因是结构设计上存在一定的不合理。同时,此端盖侧壁较厚,而此处没有应力集中现象,可以适当减轻,提高经济效益。
2 改进结构及有限元分析
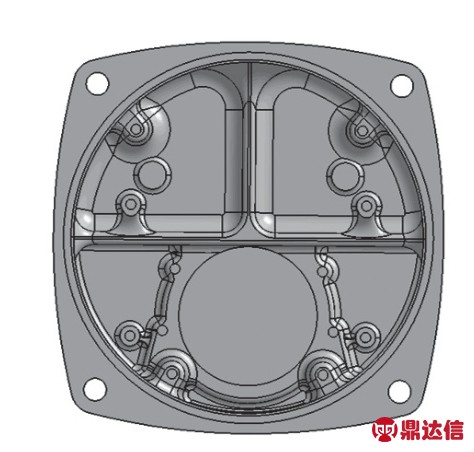
图5 加加强筋优化
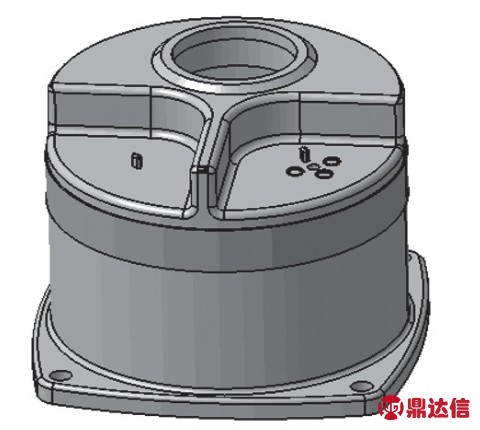
图6 改进后阀门执行器端盖三维模型
2.1 改进结构
如图5所示,在内部相应的位置增加一些加强筋,同时为克服应力集中,进行倒圆角处理,侧壁从原来的3mm减薄为现在的2.5mm,底部从6mm减薄到3mm,质量降低了10%,为了防止压强过大使盖子向外扩张而应力集中,在壳子的外部添加了一个1mm厚20宽的圆环。又考虑到这个环在使用的过程中会慢慢的滑出去,因此在相应的位置弄了两个0.2mm深的凹槽,防止环滑出。
2.2 改进效果
表2 优化前、后端盖重点部位应力对比(单位:MPa)

优化后端盖的三维模型装配如图6所示,设置相同的仿真条件进行有限元分析。从仿真结果可见,优化后的端盖在2.5 MPa压力下超过材料抗拉强度极限200 MPa的区域基本没有。将原始端盖易发生破坏位置的应力值取出,与改进之后端盖的应力值进行对比,优化前、后端盖重点部位应力值对比如表2所示,优化后强度明显提高。
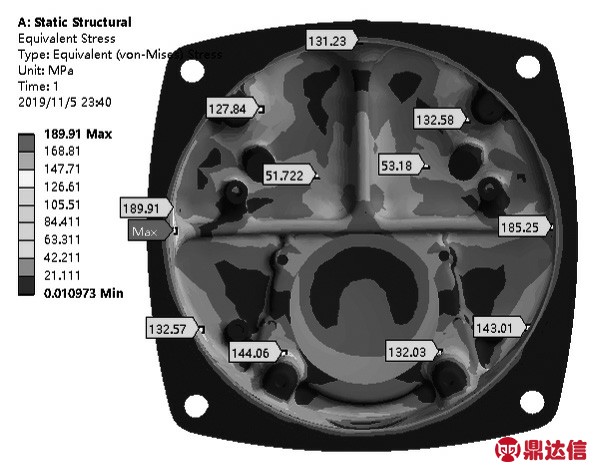
图7 优化后阀门执行器端盖重点部位应力云图
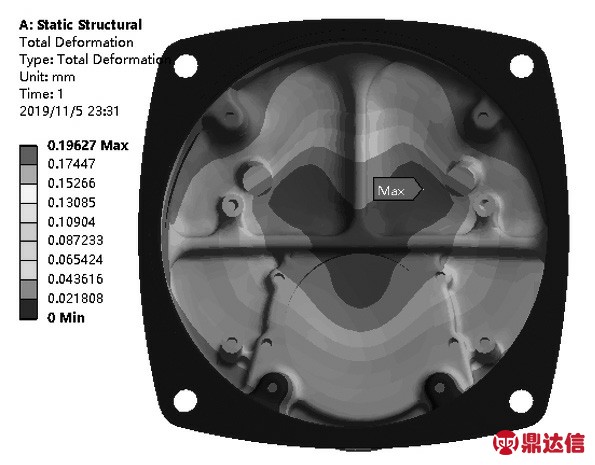
图8 优化后阀门执行器端盖最大变形处
优化后阀门执行器端盖最大应力只是点应力集中,且所受最大应力为189.91MPa,如图7所示。执行器端盖变形量减小,如图8所示,满足设计要求。
3 结论
(1)利用有限元对阀门执行器端盖的破坏形式进行了分析,判断了阀门执行器端盖破坏的原因。
(2)根据得出的结论改进了阀门执行器端盖的结构,并进行了有限元分析,验证了改进设计的可行性。
(3)改进后的阀门执行器端盖抗爆性能满足爆炸极限工况下的设计要求,同时重量减轻接近10%,大量生产可明显降低成本。