摘 要:探针作为五轴数控工具磨床重要的测量器件,用来触测刀具工件表面相关参数。为提高五轴磨床测量系统自动化程度以及减少由于测量需要重复装夹工件导致的安装误差,在基于PMAC开放式的控制平台上,开发探针测量功能。以测量工件夹持长度为例,分析自动测量系统原理,研究利用PMAC控制卡程序跳转机制实现探针功能。编写G31代码以及下位机PLC探针程序实现自动探针测量功能。同时探讨了探针补偿值的测量问题,以提高测量精度和响应的快速性。
关键词:PMAC;测量;探针;PLC;补偿值
0 引言
PMAC作为世界上最灵活和强大的运动控制器之一,具有开放性好、联动调节能力强、控制精度高、动态响应快等优点,被用在多轴机床等诸多领域。PMAC可以处理机床控制所需要的任何任务,每秒数千次切换在不同的任务之间。且由于其开放性明显优于德国SIMENS8系列和日本的FANUC6MB等数控系统,所以在多轴机床的自主研发中是被首选的强大运动控制器。
目前,在复杂高精度刀具加工工艺中,五轴联动数控磨床是唯一高效的方法[1]。随着制造技术发展以及降低成本、节省生产时间,测头为主要测量仪器的测量系统越来越多在机床中使用。
本次课题搭建的基于PMAC五轴数控磨床以探针为测量工具,根基于PMAC独特的开放性及快速响应性,开发出自动化探针测量系统。通过对工件自动找正位置、测量工件尺寸、检测加工后工件质量等一系列自动化测量方式,提高机床的可利用时间,大大提高机床单击的生产加工效率[2]。
1 基于PMAC五轴磨床探针应用系统
此课题搭建的五轴工具磨床数控系统是采用“IPC+PMAC运动控制卡”上、下位机的结构配置的开放式数控系统[3]。结合磨床的机械结构特点以及参数要求,数控系统硬件构成如图1所示。
五轴磨床数控系统是一个高精度的闭环反馈系统,反馈信号通过光栅尺获取。光栅尺动态性能好,测量各工作台位置时,无需借助任何中间机械传动元件,它可以检测出机械传递误差并在控制回路中给予修正。
通常情况下磨床加工完成后,需要拆卸工件通过三坐标测量仪或其它测量工具进行单独测量,确定其合格后方可进行下一道工序。其缺点也明显,会浪费较多的时间,最重要的是拆卸后再次安装会造成安装误差等一系列不可控的随机误差[4]。
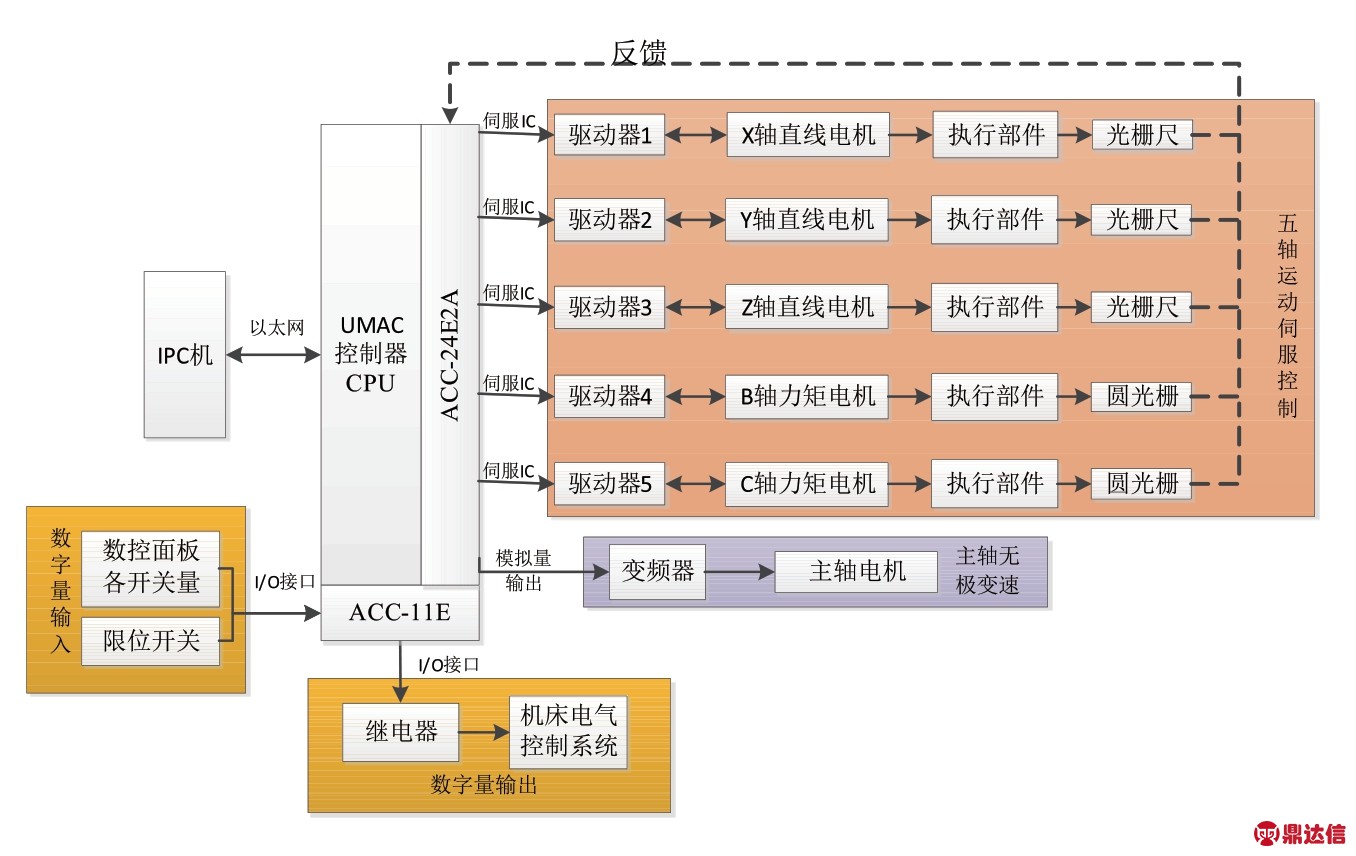
图1 基于PMAC五轴数控磨床系统硬件
为提高五轴工具磨床测量系统的自动化程度及测量精准度,基于PMAC的五轴数控磨床搭配了在线测头系统。如图2所示。基于PMAC控制卡的开放式控制平台,编写G31宏程序作为探针启动程序,并搭配相应PLC构成探针测量内部程序。加工前可测量工件原始尺寸,加工后也可测量相关加工参数,确定是否合格,避免拆卸,消除由于拆卸安装工件造成误差,简化测量流程,提高磨床加工效率及测量精准度[5]。
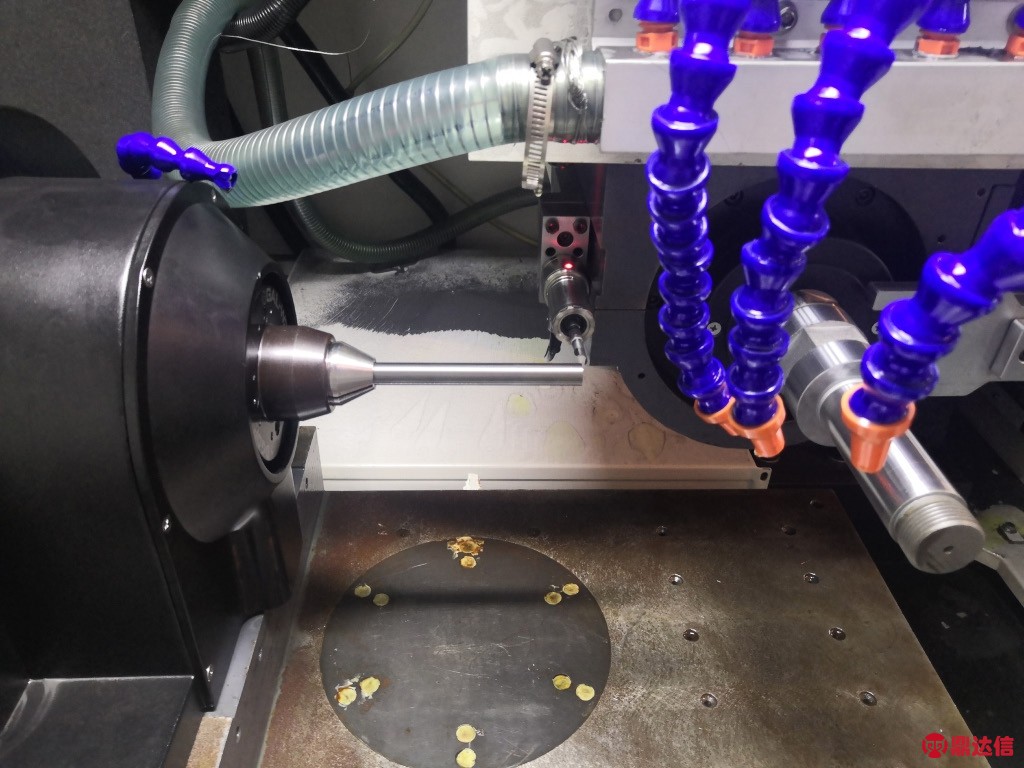
图2 探针测量系统实物图
2 探针测量原理及应用
2.1 探针结构及测量原理
本系统的测量系统的硬件探针为先锋的TP300型电缆通讯触发式三维测头。此测头的组成部分包括:测针一只(可以是红宝石也可以是金属)、φ16mm直柄、通讯电缆LA04-06、配套工具,如图3所示。测头的技术参数如表1所示。
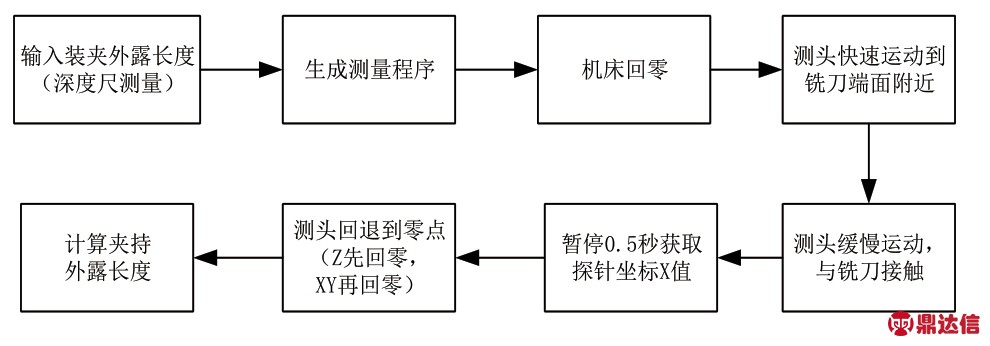
图3 探针组成图
探针测头被触发后,探针自带Led红灯亮起,表示被触碰,并通过通讯线缆发送信号给PMAC控制器,作为运动程序中的触发信号进行相应的逻辑操作。PMAC控制器带有ACC-11E板卡作为IO信号板,可以接收和发送开关量信号。探针与PMAC控制器接线图如图4所示。
表1 测头参数
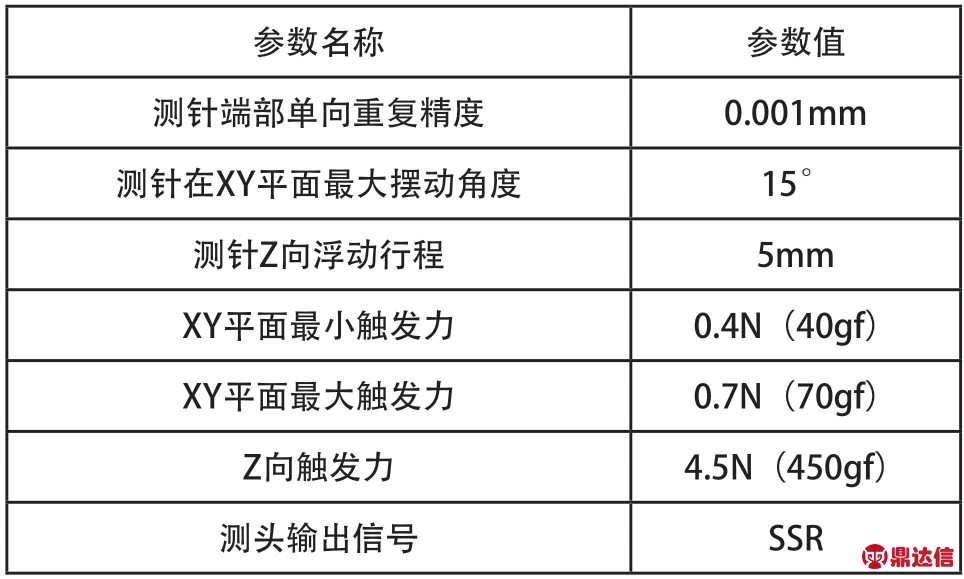
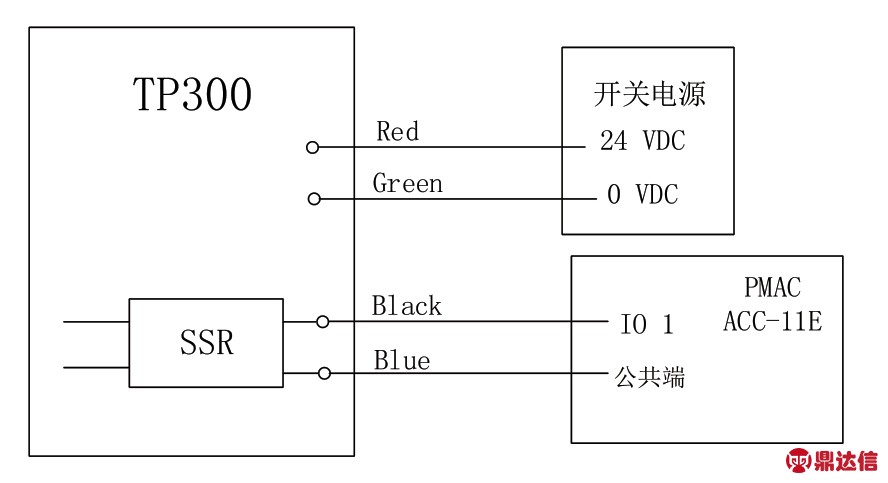
图4 探针测量系统接线图
2.2 探针程序逻辑设计
基于参数化测量的思想,根据被加工件立铣刀设计参数、机床参数和测头参数自动生成测量程序,通过探头与立铣刀的接触,在线测量立铣刀的主要几何参数,包括加工前的参数测量和加工完成后的参数测量。加工前的测量参数用于生产加工铣刀的数控程序,加工完成后的参数测量,用于对比实际加工结果与设计参数,检测加工品质[6]。
在PMAC控制器中,在运动程序遇到带一个值的字母G时,它把命令作为是一个CALL(调用)运动程序10N0,其中N是G后的值的百位数的数字。无百位的值(数学术语为取模100)控制的是跳转到程序10N0的哪个行标签。这个值乘以1000来指定行标签的数值。当遇到一个Return语句,它会跳回到调用程序。例如,G17将导致直接跳转至PROG1000的N17000;G117将导致程序直接跳转到PROG1010的N17000;G973.1会导致跳至PROG1090的N73100。
PMAC中的G代码,除了诸如G01、G02等常见标准G代码有直接命令可以实现外,其余均需要在G代码对应的运动程序中自行编写[7]。
在五轴数控磨床中通过G31启动探针测试的功能。需要测量的内容包括:夹持外露长度、A轴分度位置、螺旋角等。以测量夹持外露长度为例,测量流程如图5所示。
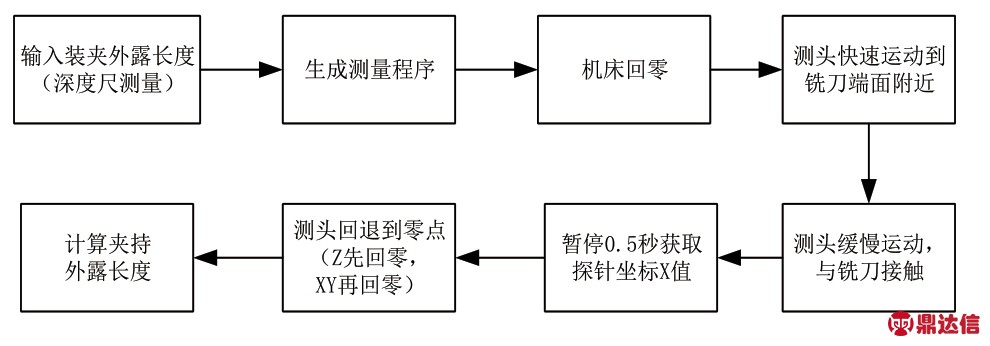
图5 探针自动化测量系统流程图
运动程序部分如下:
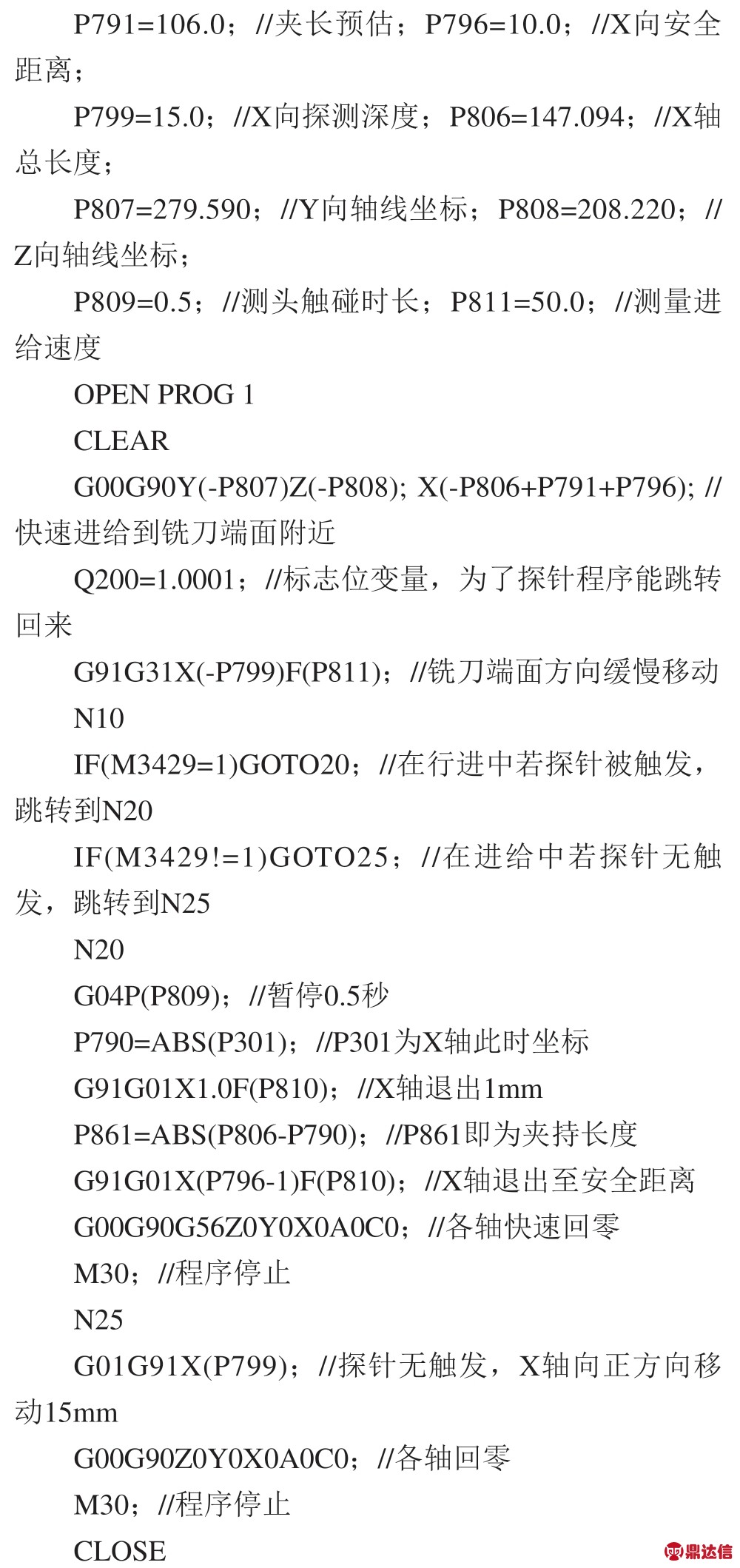
通过上述流程图以及运动程序可知,G31的作用为触发探针功能,并以直线进给运动方式向目标点运动,在探针被触发时,程序立即停止,并记录各轴坐标值用以计算。跳转回原程序后随即关闭探针功能,跳回至原运动程序G31代码的下一行继续执行后续程序[8]。G31的功能逻辑图如图6所示。
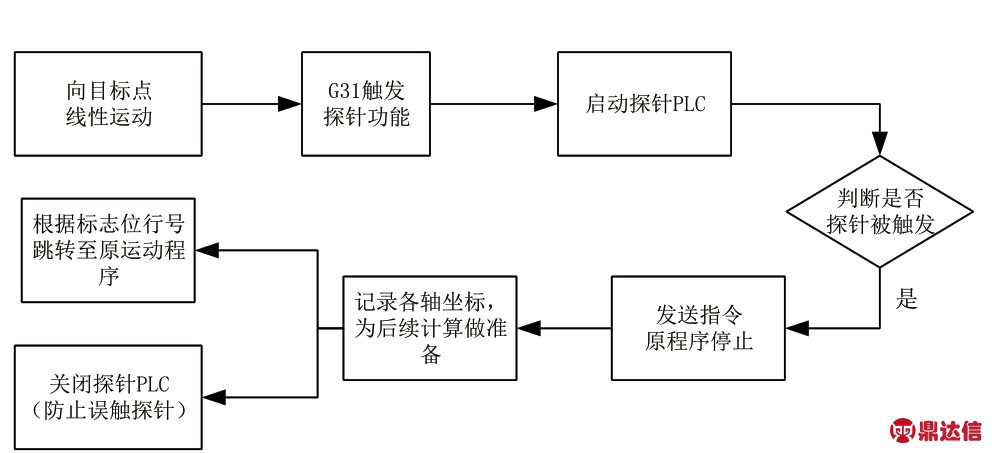
图6 下位机探针功能G31流程图
G31代码为:
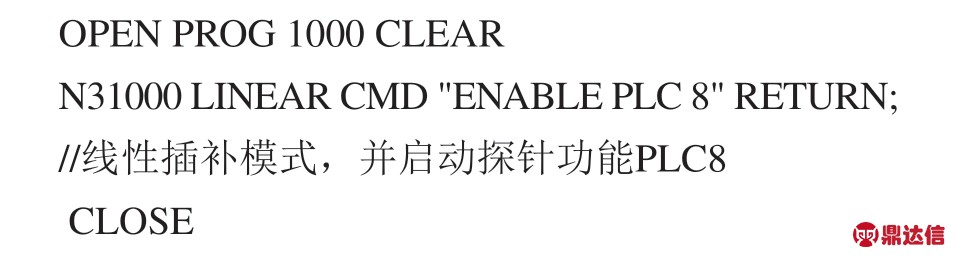
PLC 8程序部分代码如下:
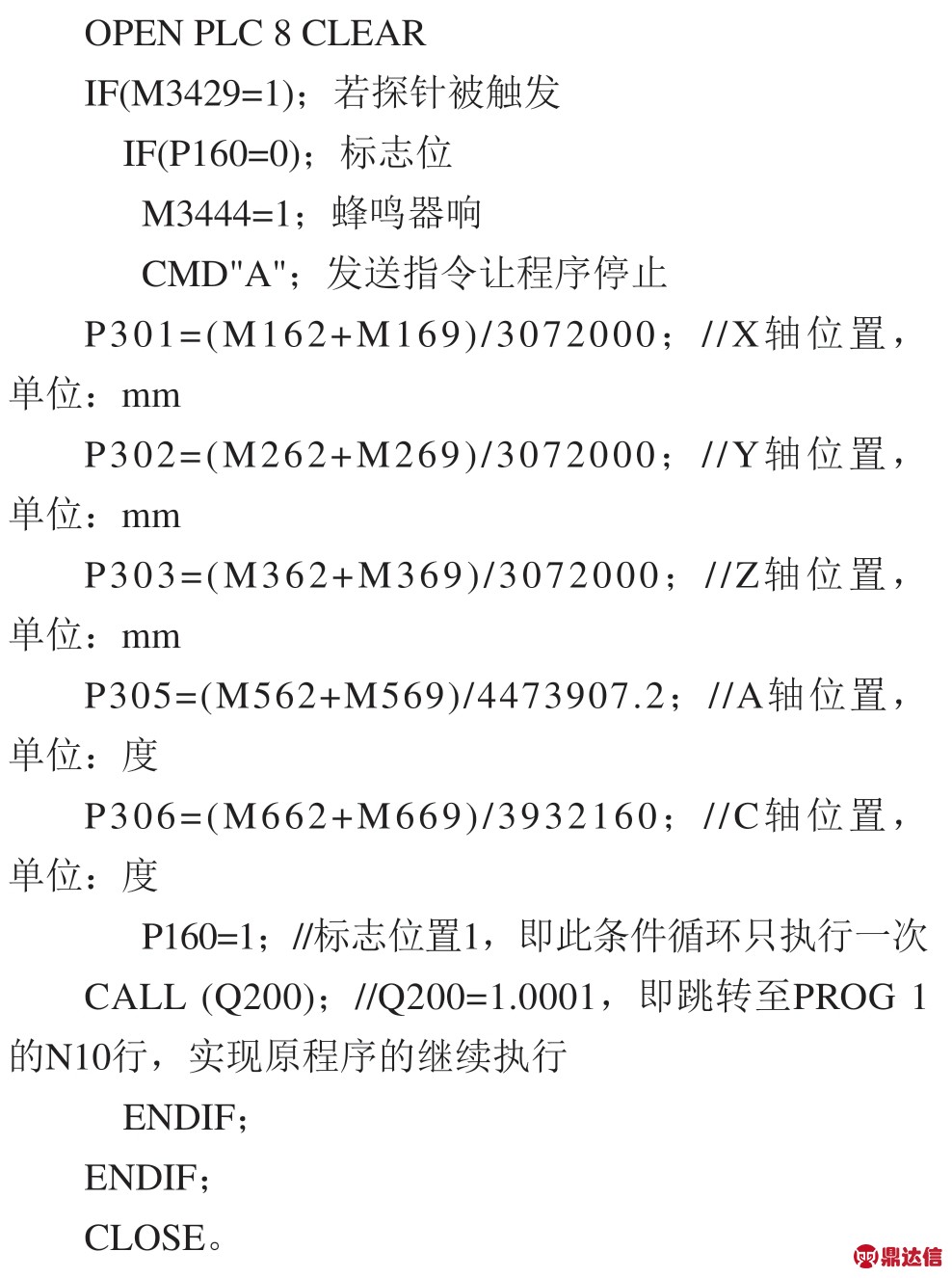
2.3 探针预行程补偿
由于在探针触发后到PLC指令发出程序停止命令,再至电机减速停止,都需要反应时间,导致X轴会继续移动,从而测量的不准确。需要测试这个时间内的X轴移动的距离,并作为补偿添加至运动程序中[9]。
在测量探针预行程实验中,采用万用表通断法测试。继续以测量工件刀具夹持长度为例,测试方法如下:在数控磨床中,使用手动模式将探针靠近被测工件。将探针测头更换为金属材质,万用表拨至通断模式,红黑两支万用表表笔分别搭在工件和探针测头上。使用数控磨床手轮模式,将X轴缓慢靠近被测工件,直到万用表蜂鸣器响起,X轴停止移动,并记录此时X轴坐标。再通过2.2所述自动化测量方法测试夹持长度,并记录X轴坐标。将其差值即为补偿值并在程序计算夹持,从而提高测量精度。
3 测量实验及结果
通过2.2的流程及程序实现自动化测量工件夹持长度的测量,在PID调试及定位精度补偿良好的的情况下,通过不同速度做多次探针触碰测量实验,记录每次触发时X轴坐标。并通过2.3论述的万用表通断法,在手轮模式下极慢的速度移动X轴,记录X轴的坐标值为基准值,试验得出此时X轴坐标值为-105.572mm。
基准值与自动化测量程序得到的X坐标值之差即为预行程补偿值。
结果如表2所示。
表2 不同速度下多次测量的X轴坐标对比
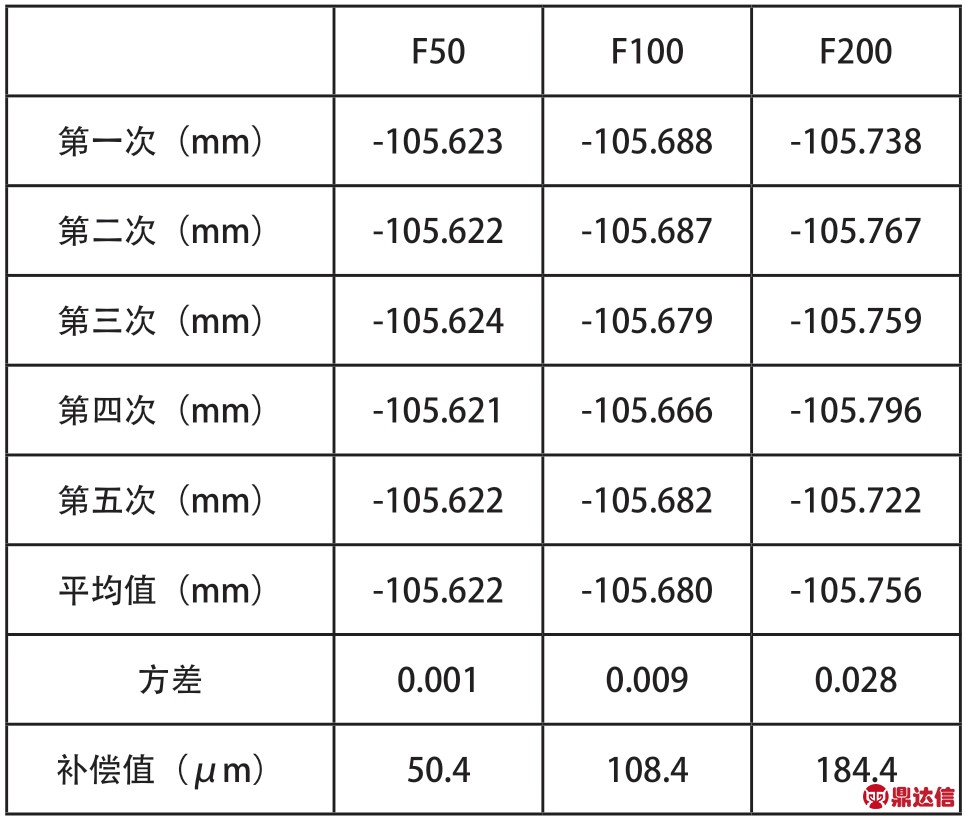
通过实验表明,触发测量时的进给速度越快,X轴坐标值绝对值越大,是由于电机惯性及系统响应有关。X轴从零点出发向负方向运动,在探针触发后到PLC指令发出程序停止命令,再至电机减速停止,都需要反应时间,导致X轴会继续向负方向移动。
由表2可得,速度较慢情况下,测量数据方差小,自动化测量系统稳定、准确。
通过2.3论述的万用表通断预行程补偿法,相比于F100与F200,F50的速度下补偿值最小且稳定性更好。即采用F50作为最终的进给测量速度。
4 结语
以刀柄夹持长度测量实验为例,实现基于PMAC的五轴数控机床的探针自动化测量功能,排除人为操作误差,大大缩短用于测量的辅助时间,提高生产效率。减少了空间的装夹、搬运次数,防止变形与磕碰[10]。
并通过对比不同速度下测量值,确定了最佳进给速度,确保其测量稳定性。通过万用表通断法较为准确地测量出探针预行程补偿值,保证其精确性。综合实验结果,自动化测量系统达到了预先目标,在保证加工质量的同时,提高生产效率,延长机床使用精度,实现了在线精准快速地工件测量。