摘 要:为解决子午线轮胎有限元模型建立、材料参数赋值等效率低的问题,进行了轮胎仿真前处理自动化设计。利用AutoCAD二次开发技术实现了多段线和样条曲线自动处理以及材料图层快速创建;利用HyperMesh二次开发技术实现了轮胎网格自动划分、rebar单元快速创建、三维模型快速生成;为便于轮胎材料参数的输入和更新,设计了材料参数赋值界面。通过具体模型自重加载仿真,验证了前处理自动化设计的准确性,提高了有限元建模效率,降低了人工操作出错的概率。
关键词:子午线轮胎;有限元模型;前处理;二次开发
0 引言
随着有限元仿真技术的不断发展,国内越来越多的企业开始采用有限元仿真与试验相结合的方式来检测轮胎的性能[1]。轮胎仿真分为前处理和后处理两部分,前处理主要包括有限元模型建立、rebar单元创建、材料赋值等。目前轮胎有限元仿真已经形成一个相对固定的流程,具体流程如图1所示。
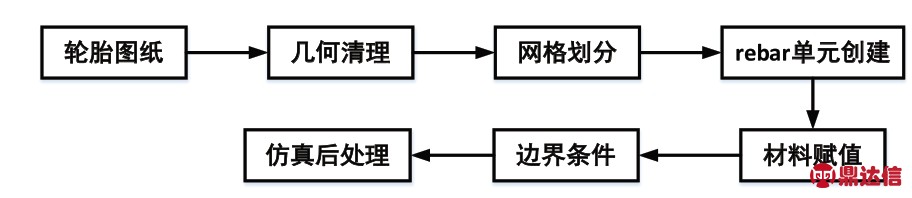
图1 轮胎仿真流程
轮胎有限元建模的问题主要集中在划分网格以及创建rebar单元两方面,传统轮胎网格划分流程是:先对二维图纸进行几何清理,然后手动添加分割线求得网格节点,在HyperMesh中按区域连接节点形成单元,得到轮胎仿真模型[2]。国外大型轮胎企业基本都有自己的轮胎专用分析软件[3],国内企业在轮胎有限元仿真方面仍在不断探索。在国内,陈振艺[4]开发的前处理软件Appta,通过对单元网格进行处理,可自动生成rebar单元,且能够方便地设置材料类型与参数;王友善[3]开发了基于AutoCAD环境下的轮胎前处理工具,可实现便捷的轮胎网格划分、rebar单元生成、材料参数赋值等;胡坚皓[5]通过AutoCAD二次开发技术生成可在ABAQUS中进行有限元仿真的INP文件,但仍需手动添加分割线进行轮胎网格划分;覃韬[2]利用C++编写算法实现了轮胎网格自动划分,程序适用性强且能够进行网格的细化。
国外在轮胎有限元建模与仿真分析方面一直处于领先地位,大型轮胎企业基本都有自己的轮胎专用分析软件,由于技术保密等原因,公开的相关资料较少。国内学者开发的前处理工具普遍存在手动干预较多等问题,有限元建模、材料赋值等前处理工作量大、效率低,严重制约着轮胎企业的生产和研发进程,因此迫切需要开发出能够实现轮胎前处理自动化的工具。
1 二次开发技术简介
1.1 AutoCAD二次开发技术
AutoCAD为用户实现特定功能提供了多种二次开发渠道,包括C语言、VB语言和AutoLISP语言等。AutoCAD软件内部嵌入了Visual LISP编译器,用户可方便地开发以及调试程序,而且AutoLISP语言包含了许多专用函数,可快速地进行图元选择以及图元数据提取,所以采用AutoLISP语言进行二次开发。
AutoLISP语言中提供了多种获取图形库中信息的命令,例如“entlast”命令可获取最新生成的图元名;“ssget”命令可根据实体类型、颜色、图层名等捕捉相应的对象集合[6]。此外,AutoLISP语言可以通过command函数执行AutoCAD软件的命令[7],例如通过(command“line”p1 p2)可画出指定起点和终点的直线。
1.2 HyperMesh二次开发技术
HyperMesh为便于用户对特定模型的前处理,提供了Tcl/Tk二次开发接口。Tcl语言是一种通用的计算机脚本语言,其开发环境内嵌于HyperMesh中,可对软件进行特定功能的开发。
HyperMesh工作目录下的command.tcl文件记录了用户执行的所有命令以及设置的具体参数,可通过修改该文件来进行相关功能的开发。利用Tcl语言进行二次开发时需要先删除command.tcl文件中的冗余代码,比如视图的调整、显示样式的选择等,同时应将Hard code进行修改,以提高程序的可移植性[8],另外应增加相关代码,获取需用户手动输入的参数,增强人机交互。
2 轮胎前处理流程自动化设计
轮胎结构设计过程中,由于考虑到模具后期加工等问题,二维结构图会体现轮胎的几何细节,增加了网格划分难度,会导致后期有限元仿真中断或无法收敛,因此在HyperMesh进行有限元建模前,需要通过AutoCAD软件进行几何清理。
由于轮胎结构复杂、材料种类繁多,所以有限元建模工作较为繁琐。另外子午线轮胎冠带层、带束层和胎体层均为帘线橡胶复合材料,有限元模型的rebar单元创建困难,所以需要进行合理的前处理流程设计,并通过结合HyperMesh软件原有功能,实现轮胎前处理自动化,具体流程如图2所示。

图2 前处理自动化设计流程
2.1 样条曲线处理
轮胎结构图中包含较多的多段线和样条曲线,但HyperMesh软件不支持这两种线型,所以需要提前对多段线和样条曲线进行处理。
多段线由直线或直线与圆弧组合而成,AutoCAD中提供了“explode”命令,可方便地对多段线进行分解,拾取多段线程序如下:
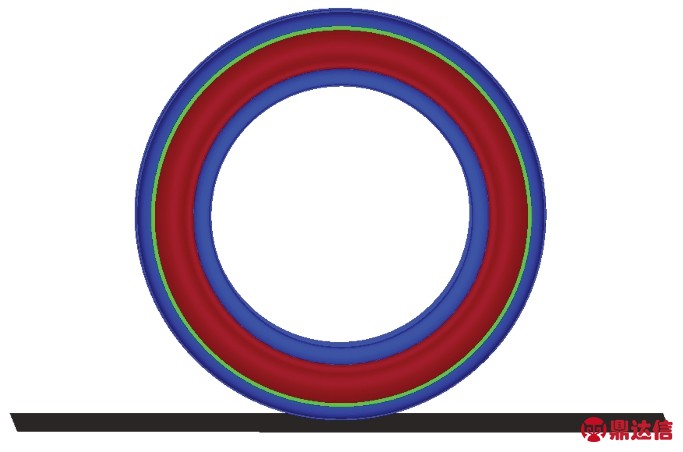
样条曲线通过“splinedit”命令转化为多段线,而且可指定转换精度,但在转换后存在样条曲线被大量短圆弧代替的情况,因此程序先将结构图中的样条曲线移至指定图层,转换为多段线并进行自动分解。设置仅显示“样条曲线”图层,对于分解质量不高的区域,进行手动圆弧拟合,具体流程如图3所示。
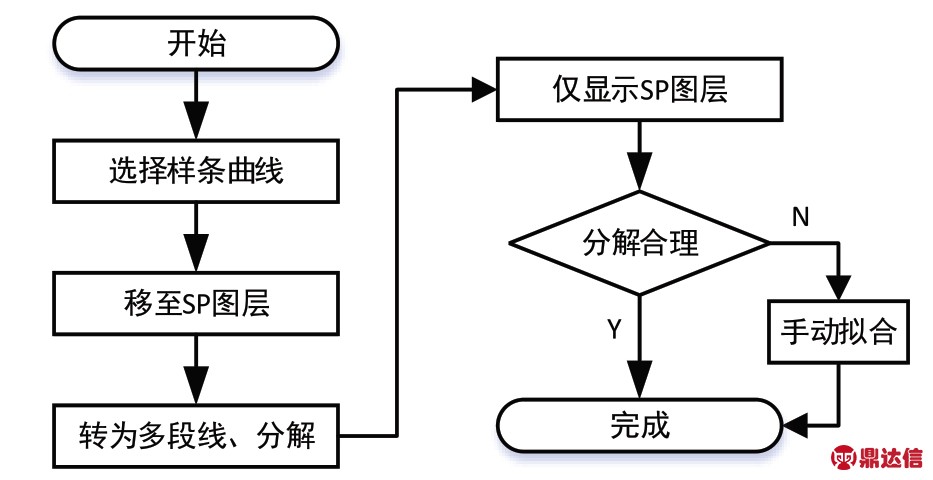
图3 样条曲线的处理流程
样条曲线处理的部分程序如下:
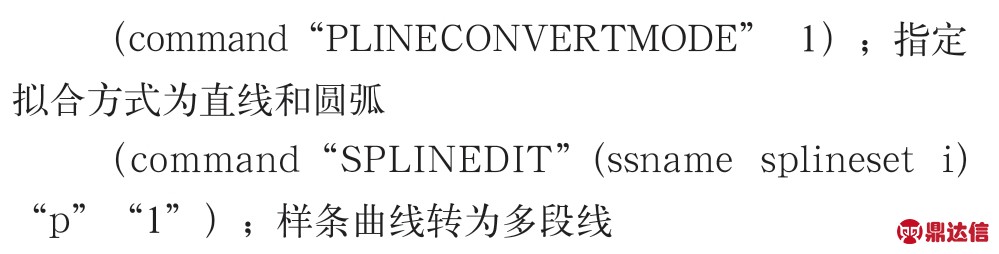
2.2 材料图层建立
通过在AutoCAD中按材料类型建立图层,存储为DXF格式,将此文件导入HyperMesh后,会自动创建与图层同名的component。由于子午线轮胎的结构复杂,采用人机交互的方式输入冠带层、带束层、胎体层等的数量,自动建立材料图层后,程序将多余的直线、圆弧删除,所建立的图层为多段线形式,需要再将多段线分解,具体流程如图4所示。
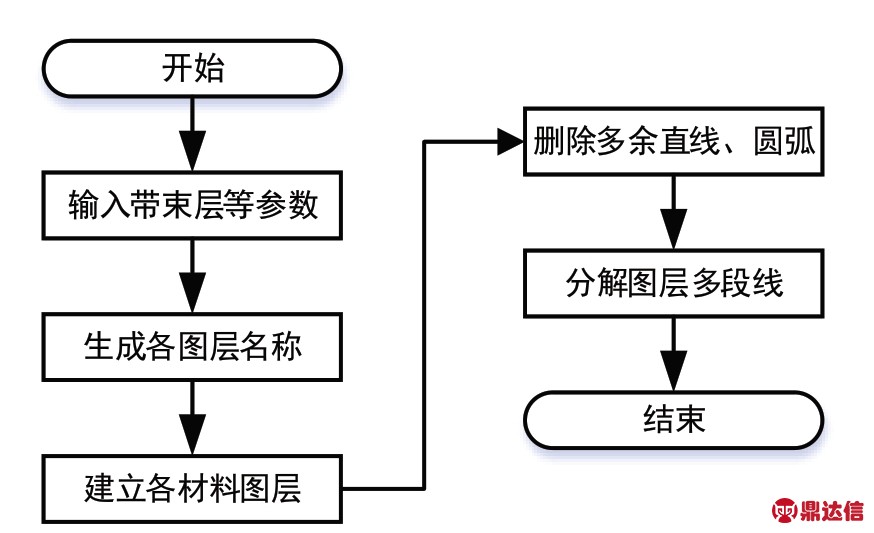
图4 材料图层建立流程
2.3 网格划分与rebar单元创建
2.3.1 网格划分模块
为得到更高的网格质量,在Autocad中给轮胎图纸添加网格分割线。图5所示为添加网格分割线后得到的二维轮胎截面图。经过材料图层建立的轮胎图纸导入HyperMesh,软件会生成与CAD中图层同名的component,通过component自动创建曲面surface,部分代码如下:
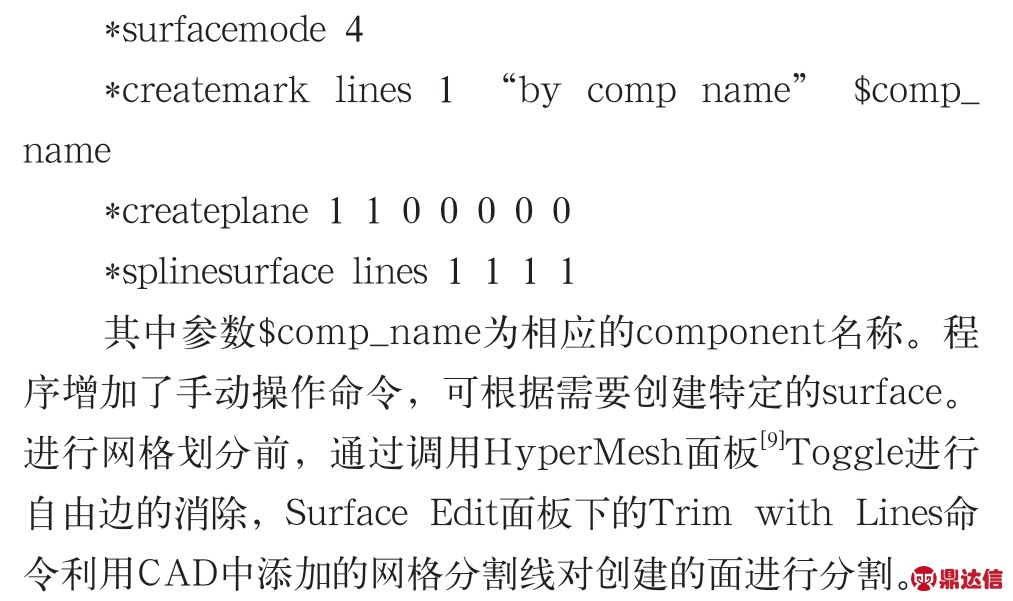
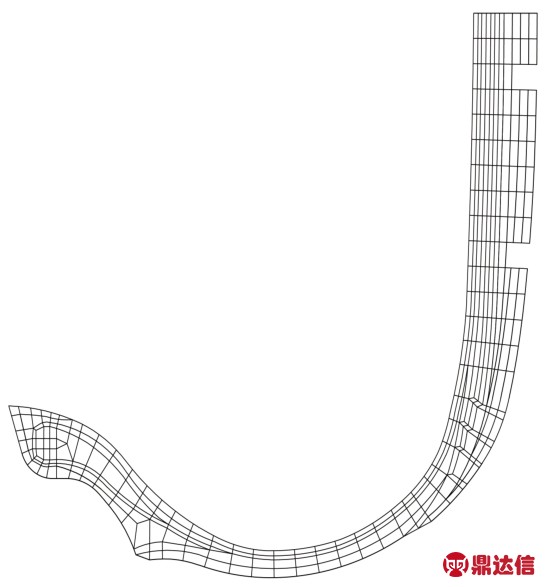
图5 轮胎几何截面图
网格划分采用二维自动网格划分方式,设置合适的网格尺寸,避免因尺寸小于分割线尺寸导致的网格质量不高问题。经过网格自动划分得到的轮胎二维截面图如图6所示。
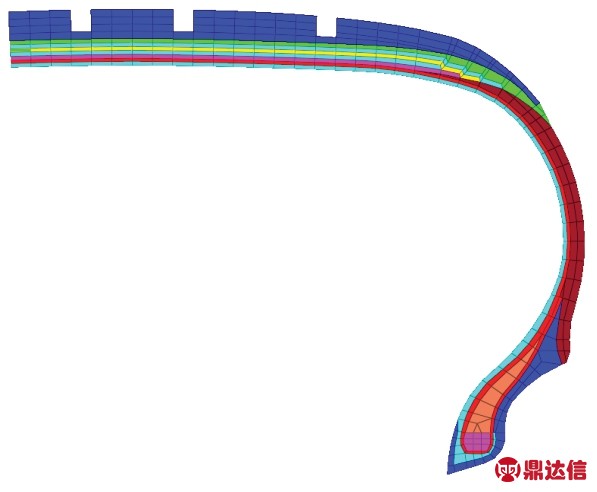
图6 轮胎半截面网格模型
2.3.2 rebar单元创建模块
通过在橡胶基体单元中创建二节点面单元(SFMGAX1),为轮胎的带束层、胎体层等进行增强,充分反映帘线-橡胶复合材料的特性。
rebar单元是通过对网格节点进行线性插值,在橡胶基体单元的指定位置进行创建。具体方式为通过创建节点选择面板,用户分别选择带束层或胎体层等的上、下边缘的起始和终止节点,程序自动捕捉位于起始节点与终止节点间的所有节点坐标,根据用户指定的位置,插值生成新节点,从而创建rebar单元。由于每层区域的厚度不相同且不均匀,为保证rebar单元创建的通用性,用户指定的位置参数为新节点与上边缘的距离d占该位置厚度H的比例。自动创建的指定比例为0.5的rebar单元如图7所示。
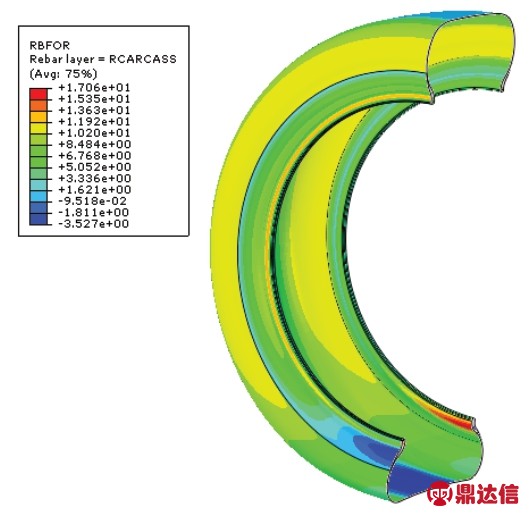
图7 rebar单元创建
2.4 三维有限元模型生成模块
在生成完整的轮胎截面有限元模型时,需要逐个镜像component,过程繁琐,通过程序可自动进行镜像,生成的模型如图8所示。轮胎的自重加载仿真、滚动磨损仿真、滑水仿真等,需要建立三维轮胎有限元模型。在Hypermesh中编写自动化程序,指定在圆周方向上的旋转角度和和份数,通过对二维截面进行旋转自动生成满足仿真要求的三维模型。图9所示为旋转40°并16等分的轮胎模型,可以在自重加载仿真中作为接地区域,圆周方向上剩余区域可指定较少份数,既能保证仿真精度又能提高效率。
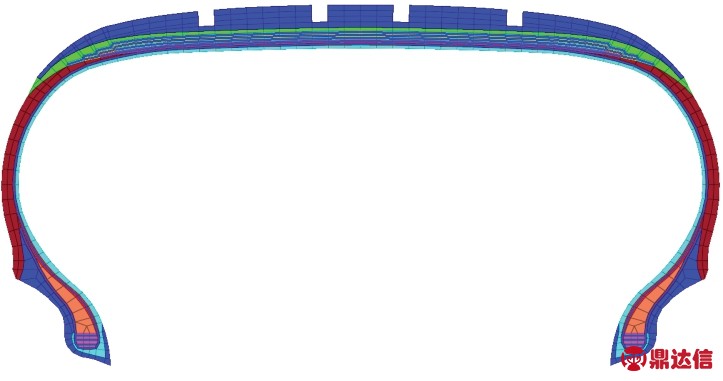
图8 轮胎二维网络模型
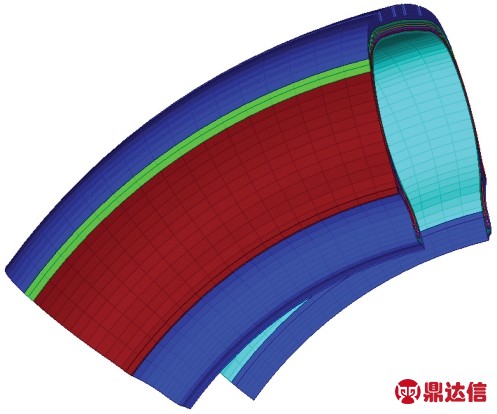
图9 40°轮胎三维网格模型
2.5 材料属性创建模块
在HyperMesh中进行材料属性创建时,各个部件的材料参数需要手动输入,过程中需要进行大量的重复操作,所以需要设计界面简化操作。子午线轮胎中主要包含橡胶材料以及钢丝帘线材料,创建材料参数赋值界面,可快速地完成材料参数的输入,材料参数也能进行快速地更新。设计的GUI界面如图10所示,先进行轮胎冠带层、带束层和胎体层数量的更新,再进行材料参数的赋值,其中橡胶材料超弹性本构模型可选用Mooney-Rivlin模型、Yeoh模型和Neo-hooke模型。
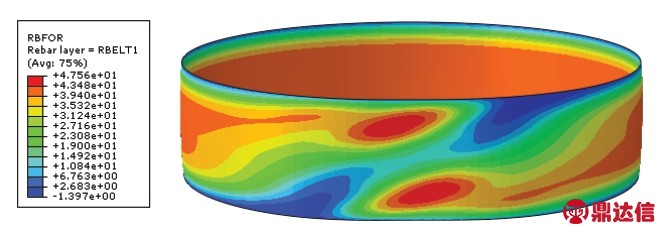
图10 材料属性赋值GUI
3 CAE前处理自动化实例验证
通过本文的有限元建模自动化对205/55R16型号半钢子午线轮胎进行建模,并为其2层带束层、2层冠带层和1层胎体层创建rebar单元,输入材料参数后将生成的Input文件导入Abaqus进行轮胎自重加载仿真,建立的轮胎与路面接触的仿真模型如图11所示。
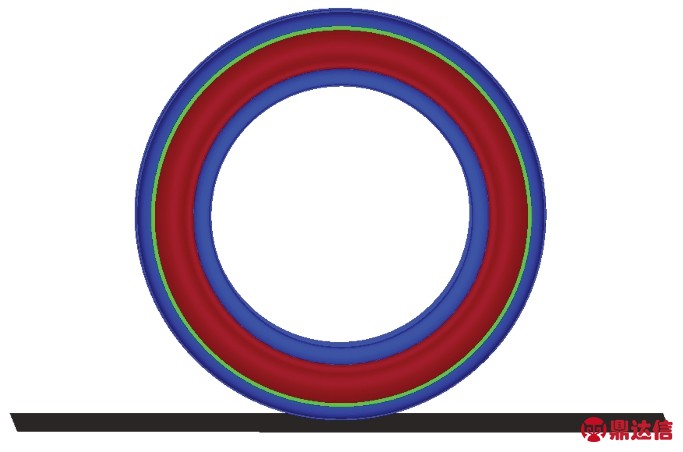
图11 轮胎自重加载工况模型
仿真过程中,将轮胎模型轮辋与胎圈的接触位置简化为刚体约束。自重加载工况先固定住轮辋,然后对轮胎进行充气,向轮胎内表面施加0.22Mpa的均布压力;最后进行轮胎自重载荷加载,对路面施加Z轴方向的位移,实现轮胎与路面的接触,再施加1/4车重载荷5000N完成加载。
通过分析自重加载工况下橡胶材料和骨架材料的应力分布特点,验证建立的轮胎有限元模型的正确性。图12和图13所示负载工况下两层带束层的帘线轴力分布情况,带束层1和带束层2的帘线轴力关于轮胎中分面和180°子午面反对称,符合两带束层帘线角关于轮胎中分面对称布置的实际情况。
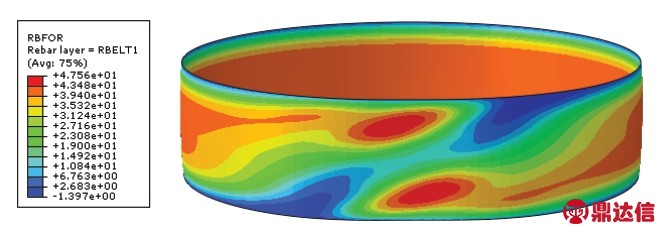
图12 带束层1帘线轴力云图
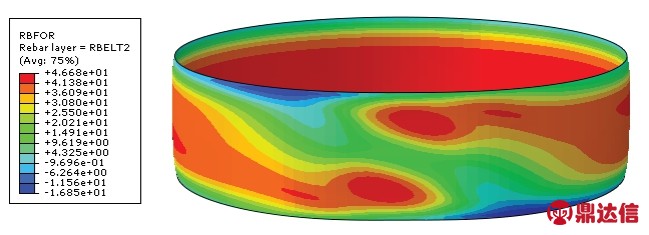
图13 带束层2帘线轴力云图
图14为自重加载工况下与子午向夹角为0°的胎体层帘线轴力云图,其轴力沿轮胎轴向和周向的分布都是不均匀的,接地端中心区域受压,并沿周向和轴向扩散;从图15可以看出,在接地端胎圈附近出现帘线轴力最大值。
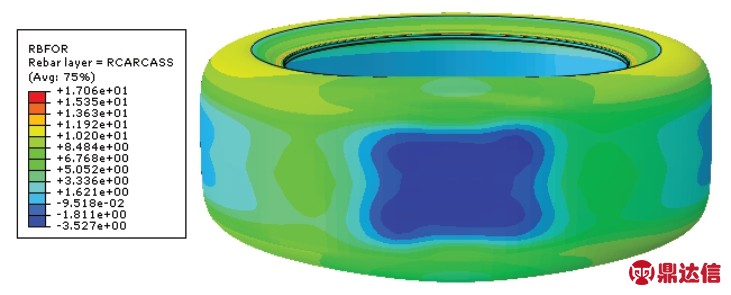
图14 胎体层帘线轴力云图(视角1)
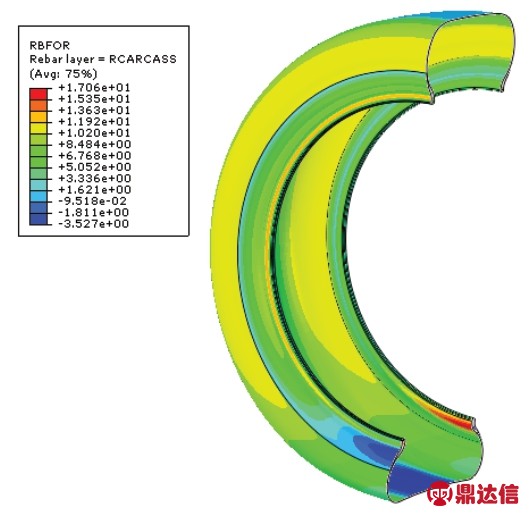
图15 胎体层帘线轴力云图(视角2)
图16为轮胎橡胶材料部分的应力云图,可以看出由于接地压力的作用,轮胎产生了较大变形,子午面内的应力分布关于轮胎中分面对称。由于轮辋的作用,使得胎圈处产生了复杂的应力应变状态;在带束层两侧端部位置,出现了一定范围的应力集中,此位置为各种骨架材料的交汇处,而且是接地位置的端部,所以应力分布情况复杂;在接地子午面纵向沟槽的底部,也出现了较大的应力。
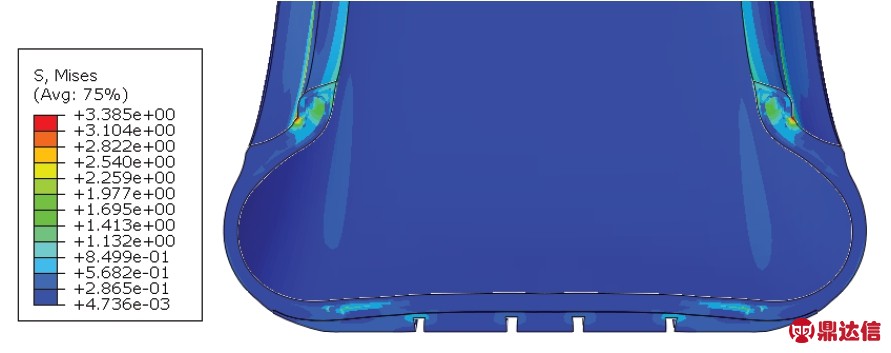
轮胎橡胶材料应力云图
通过该实例可以看出,带束层帘线、胎体层帘线等骨架材料的应力分布与帘线的铺设角度情况相符;橡胶材料的应力分布与花纹结构和轮胎加载工况一致,仿真结果与轮胎实际应用情况相吻合。仿真分析结果验证了轮胎前处理自动化设计的正确性。自动化前处理流程相比现有手动前处理,大大提高了建模效率,并且在几何清理过程中,避免了手动处理出现的多段线和样条曲线的遗漏。
4 结语
本文分析了子午线轮胎前处理的具体流程,通过对AutoCAD和HyperMesh二次开发,进行了轮胎有限元仿真前处理自动化设计,有效地提高了前处理的效率,同时避免了人工操作出错等问题。前处理自动化设计能固化操作流程,有助于企业仿真工作的标准化,同时也为轮胎仿真的快速实现奠定了基础。