摘要:火焰合成法是指前驱物在燃烧器中经过一系列复杂的物理化学反应过程得到产物纳米颗粒的方法,具有一步合成的优点,是现代工业规模化制备高性能材料的一种重要方法。火焰合成过程机理涉及物质的相态变化、颗粒生长团聚和热量质量交换等复杂过程,探究火焰合成过程是实现产物颗粒调控的关键。本文对火焰合成过程中的关键部分,如前驱物、为合成过程提供高温氧化环境的燃烧器、产物颗粒等进行分析,阐述了火焰气溶胶技术中颗粒的生长及转变路径、不同燃烧器的结构及其温度场、流场特点,并分析了不同燃烧器合成的纳米TiO2进行了粒径及晶型特点的研究进展。指出火焰合成TiO2生长机理和形态调控的基础研究对工业制备钛白粉具有指导意义。
关键词:火焰合成;纳米材料;二氧化钛;燃烧器
火焰合成法也称为燃烧合成法,是指产物颗粒的原材料即前驱物经气化或雾化通过载气输送到由燃烧器提供的高温火焰场中,进而经过一系列复杂的物理化学反应得到产物纳米颗粒[1]。火焰合成制备的常见纳米氧化物包括TiO2、SiO2及其掺杂体系等。
钛白粉即TiO2颗粒,具有较高的白度且化学性质稳定,被广泛应用于造纸、涂料和塑料等领域。TiO2的晶型包括锐钛型、金红石型、板钛型,其中最常用的是锐钛型和金红石型。锐钛型在可见光短波部分相较于金红石型具有较高的反射率,因此锐钛型TiO2具有较好的光催化性能,被广泛用作催化剂载体。金红石型TiO2具有较强的吸收紫外线能力[2],其对紫外线波段的反射率低于锐钛型,因此常被用于涂料、化妆品等领域。近年来我国催化和涂料行业发展迅速,因此对锐钛型和金红石型TiO2的需求呈不断上升趋势[3−4]。
工业钛白粉的制备方法主要包括硫酸法和氯化法。硫酸法属于湿法合成,虽然原料价廉,但是存在三废问题。氯化法相比于硫酸法不仅工艺简单,能够实现产品的连续生产,且钛白粉产品质量较好,在国内外受到广泛推广,具有逐渐取代硫酸法的趋势。但是目前国内氯化法技术部分尚未完全成熟,产品性能尚不能满足高端钛白粉的需求,对于氯化法核心工艺高温氧化的机理认识有待加深[5]。分析工业高温氧化过程中产物的形成过程和原理,有望实现对火焰合成颗粒形态的有效调控。本文从火焰合成技术、燃烧器结构及特点等方面进行概述,对不同燃烧器制备的TiO2进行了分析,将对使用火焰法制备TiO2及其他纳米颗粒具有一定的指导意义。
1 火焰合成前驱物进给
火焰合成是将前驱物以液相或气相状态输送到火焰场中经过反应、成核、碰撞、凝聚及生长等物理化学反应得到目标产物。前驱物进料方式不同,其合成技术有所不同,主要分为气相进给合成技术和液相进给合成技术两大类,如图1所示。
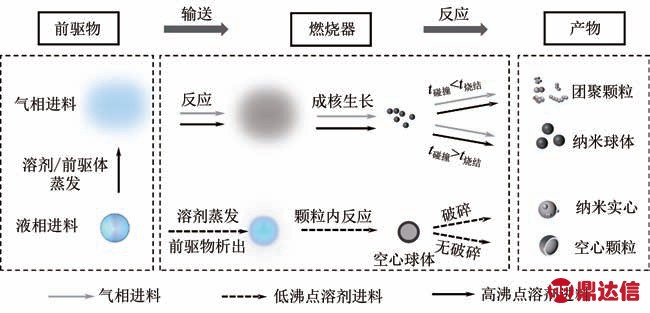
图1 颗粒生长示意图
气相进给合成技术是指前驱物以气相状态进入火焰场中进行反应,但是以气相状态进料的前驱物要具有较低沸点或者较高的饱和蒸气压,满足该特点的前驱物较少,因此限制了气相进给合成技术的使用。前驱物以气相进料的火焰合成被称为“气相−颗粒相”的转变过程[6−9]。气相前驱物进入火焰场后发生化学反应生成产物分子,产物分子在火焰场传输过程中均相成核形成稳定的核结构而后生成初始颗粒,或者气相产物在初始颗粒表面发生非均相成核沉积在颗粒表面。初始颗粒在后续生长过程中发生碰撞和烧结,若颗粒的碰撞特征时间大于烧结特征时间,则两个颗粒由于颗粒表面原子扩散和晶界扩散等作用发生烧结现象,将两个未分离的颗粒烧结成一个较大的球形纳米颗粒;若颗粒的烧结特征时间大于碰撞特征时间,两个颗粒在烧结成一个较大纳米颗粒之前由于分子的布朗运动已经发生碰撞分离,此时将会形成不规则的团聚颗粒或者团聚体。
液相进给合成技术是指前驱物以液相形式进料。相较于气相进料,液相进料在前驱物选择方面具有较大优势,能够获得更高的纳米颗粒产量。液相前驱物可以是纯溶液,也可以是原材料的水溶液或者有机溶液,这些液相前驱物通过机械或者其他作用变成小液滴进入火焰场中进行反应。液相进料过程中决定颗粒生长路径的主要因素是溶剂沸点与溶质前驱物分解温度的比值[10]。文献表明当溶剂沸点与溶质前驱物分解温度的比值大于1.05时[11],即为高沸点溶剂进料。由于溶剂沸点较高,火焰场温度可能达到溶质前驱物分解温度而未达到溶剂沸点,出现溶质前驱物发生分解而溶剂尚未蒸发完全的现象,此时液相气溶胶技术的颗粒生成路径会遵循气相进给合成技术的颗粒生长路径,能够得到粒径较小的纳米颗粒。当溶剂沸点与溶质前驱物分解温度的比值小于1.05时,由于溶剂沸点较低会出现溶剂相比溶质前驱物先蒸发或者完全燃烧,此时溶质前驱物会在液滴表面进行反应、析出,形成壳型或者中空的颗粒。随着火焰场温度进一步升高,甚至会出现部分壳型结构破碎的现象,颗粒碎片在高温环境中会继续发生分解继而成核长大,最终形成纳米实心颗粒[12−14]。
气相进给能够快速实现气相到颗粒相的转变,且得到粒径较小的产物,但前驱物自身的低沸点或高饱和蒸气压性质限制了气相进给合成技术的规模化应用。相比较于气相进给合成技术,液相进给合成技术因前驱物以液相(前驱物或将前驱物溶解于水或者有机物等溶剂中)输送,通过鼓泡载流、雾化或者喷雾的形式变成小液滴甚至微米级液滴进入火焰场中进行反应,使得元素周期表上各种元素都能通过该方法实现高温反应,成为制备各种纳米材料的一种高效方法。近几年清华大学李水清团队[15−18]分别采用气相和液相路线开展了火焰合成研究,并利用相选择性激光诱导击穿光谱对不同火焰合成技术中颗粒的生长路径及机理进行了分析研究。
2 合成燃烧器
燃烧器是火焰合成系统中的关键核心装置,其结构决定了燃料和氧化剂的输送和混合等过程,进而产生不同温度以及流动状态的火焰结构,因此燃烧器类型的选择对颗粒性质起到了决定性作用[1]。常见的燃烧器分为同轴扩散火焰燃烧器、平焰燃烧器、对冲燃烧器、滞止火焰燃烧器和火焰喷雾热解装置等。图2给出了几类典型合成燃烧器的结构示意图,下面将分别对各类燃烧器结构及其特点进行系统介绍。
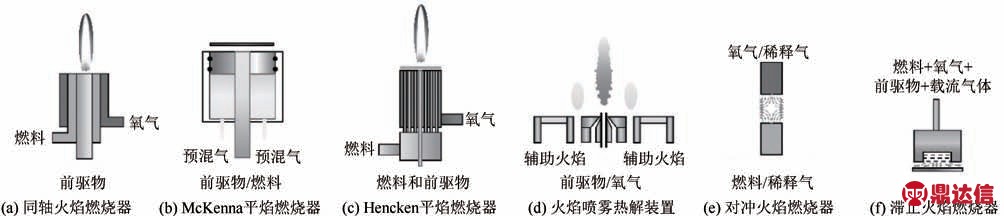
图2 典型合成燃烧器结构示意图
2.1 同轴扩散火焰合成燃烧器
同轴扩散火焰合成燃烧器的早期使用源于Juillet团队[19−20],其使用的同轴扩散火焰合成燃烧器由3根同轴布置的空心圆管组成,其中前驱物和载流气体从中心圆管进入,最外层的圆管为氧化气,中间夹层为燃料气。中心管通入前驱物和载流气的优势在于能够对前驱物在进入火焰场之前进行一定程度的稀释,从而抑制火焰场中颗粒团聚过程,得到粒径较小的产物颗粒。Formenti等[20]使用了如图3所示的4根同心圆管,在前驱物气流和燃料气之间进一步增加了一层用于输送氮气或其他惰性气体的通道,目的是减少燃料气向前驱物层的扩散,使得火焰底部高出燃烧器出口一定距离,进而促使颗粒产物在距离圆管一定的高度处生成。Xie等[21−22]对甲烷扩散火焰中的OH*化学自发光进行研究,表明燃烧器形成的火焰分为两个部分,其中火焰上游燃料与氧化剂混合均匀且燃烧较为充分,火焰下游出现光辐射现象是由下游部分甲烷燃料不充分燃烧产生的煤烟导致。Xu 等[23]使用模拟的方法对天然气氧气燃烧流场进行模拟分析,结果表明火焰场中轴向温度在600~3600K 范围内变化。Stelzner 等[24]将甲烷与二氧化碳混合气作为燃料气置于外层,氧气作为氧化剂由内层通入,通过增强氧化剂侧氧气和稀释燃料气侧二氧化碳来改变温度范围,获得燃烧场中最高温度的变化范围为2200~3000K。
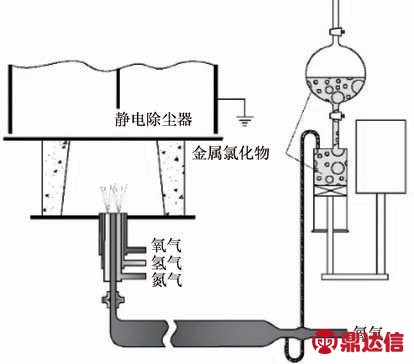
图3 同轴火焰燃烧器结构示意图[20]
同轴扩散火焰合成燃烧器的特点在于燃烧无回火、火焰场稳定、安全性高、结构简单且便于工业放大,但是在使用同轴扩散火焰燃烧器制备纳米TiO2和其他纳米颗粒时,发现同轴扩散火焰燃烧器存在以下不足:①高温火焰区域较长,导致颗粒的生长不易控制;②火焰场中的颗粒在流动过程中会附着于燃烧室管壁上,产生结疤现象。针对前者,程易等[25]在使用同轴扩散火焰燃烧器制备TiO2纳米颗粒时发现,通过增加前驱物的载气流速,可以使中心圆管产生的火焰形态由层流状态转变为湍流,从而缩短了火焰区长度[26−27],减小了TiO2纳米颗粒的生成粒径。针对该类型燃烧器的颗粒壁面附着现象,Sunsap等[28]在同轴空心圆管的最外层圆管内通入氮气或者惰性气体,从而使火焰与耐高温玻璃管间形成了一层气膜,有效解决了颗粒物的壁面沉积问题。
2.2 平焰燃烧器
2.2.1 McKenna平焰预混燃烧器
McKenna平焰预混燃烧器的使用最早可以追溯到20世纪70年代[29],在后续研究中Ulrich[30]提出将Mckenna平焰燃烧器应用于工业规模的二氧化钛生产。Ehrman 等[31]对SiO2/TiO2混合气溶胶进行研究,详细描述了McKenna 平焰预混燃烧器,其典型结构如图4(a)所示。整体结构由包裹在不锈钢套筒中并用O形圈密封的重力烧结青铜塞组成,在距离燃烧器上表面1cm附近安装平行于燃烧器表面的冷却盘管,并通入循环冷却水,用于防止燃烧器表面出现烧结现象,预混气能够在燃烧器表面约1.5mm处形成沿径向均匀分布的预混火焰。Jin等[32−34]使用甲烷、氢气、氧气、二氧化碳作为预混气研究McKenna燃烧器中火焰的结构,得到不同当量比下火焰的最高温度范围为1600~1800K。Jiang 等[35]对McKenna燃烧器流场进行分析,使用数码相机观察到当气体流速不变时增大燃料与空气的当量比,火焰形状呈现由平坦火焰转变为褶皱火焰进而出现蜂窝火焰等三种形态,对燃料与空气的当量比以及气体流速综合分析认为燃烧流场是由当量比和气体流速相互耦合决定的。
后续发展研究中,Pratsinis 团队[36−37]使用了与McKenna 平焰燃烧器相似的结构,如图4(b)所示,将甲烷、氧气、氮气在通入燃烧器之前进行预混合,并与以氩气作为载流气的TiO2前驱物四异丙醇钛或钛酸四异丙酯[titanium(Ⅳ)isopropoxide,TTIP]一起输送至燃烧器中。为了促进燃料气与氧化气间的充分预混,采用上部具有64 孔的莫来石蜂窝并中心管内布置玻璃珠,用以形成出口处的稳定扁平火焰。在此过程中,前驱物TTIP 的温度要比燃烧器及管路低20K,防止TTIP在输送过程中出现冷凝现象。McKenna平焰预混燃烧器由于其产生的火焰形状扁平,可以看作一维平面,所以也被人们认为是标准火焰,被广泛应用于光学诊断。
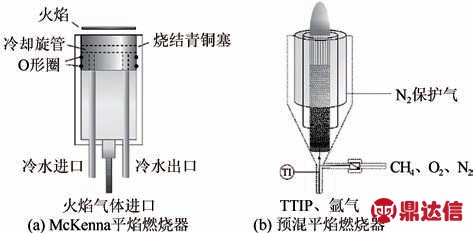
图4 平焰燃烧器结构示意图[31,36−37]
2.2.2 Hencken平焰扩散燃烧器
Hencken平焰燃烧器也被称为多元扩散平焰燃烧器,早期由Wooldridge 等[38]用于制备SiO2纳米颗粒。如图5所示,燃烧器由哈氏合金蜂窝器和附件组成,其中蜂窝器内装有173 根不锈钢燃料毛细管,每根燃料管的周围设置6个氧化剂通道。流经不锈钢毛细管的燃料气与蜂窝通道的氧化气将在燃烧器上方进行扩散燃烧,形成数以百计的扩散火焰单元,这些小的扩散火焰整体组合形成了平铺的层流火焰,为前驱物的火焰合成提供了一个高温场所,促进产物颗粒的生长。在燃料气和氧化气的外侧设有保护罩,覆盖区域和氧化气通道相同,能够确保流体流动过程一致。覆盖区域通入氮气或者其他惰性气体用来提高火焰的稳定性,同时形成一层气膜减少空气夹带,也提供了一个与火焰场相反的低温冷却区。在蜂窝器的中心布置管径较大的管道,贯穿整个燃烧器,前驱物以及气体通过该中心管道到达燃烧器的上方,在平焰提供的高温环境中进行化学反应。Feng等[39]使用过滤瑞利散射技术对Hencken燃烧器进行模拟分析,得到火焰锋面处温度变化范围为200~2100K,燃烧后区域温度范围为1000~2000K。Qi 等[40]使用甲烷为燃料,氧气与氮气或二氧化碳的混合气作为氧化剂,使用B型热电偶测得Hencken 燃烧器轴线温度范围为1200~1600K,且燃烧器出口处温度较高,在大约25mm处出现最高温度,这得益于Hencken燃烧器的特殊结构。清华大学李水清团队[18,41−42]采用激光诱导荧光技术对Hencken的流场状况进行了分析,根据瞬态羟基分布将燃烧器的反应区分为两个部分,火焰上游从燃烧器出口到轴向位置25mm处为层流区,前驱物在该区域内发生水解反应,火焰下游部分即轴向位置大于25mm为湍流区,且燃烧场中气体流速的增加会产生较大的剪切速率,导致湍流区域的扩大。
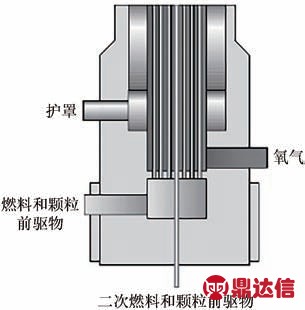
图5 Hencken平焰燃烧器结构示意图[38]
Hencken 平焰扩散火焰虽然与Mckenna 平焰预混火焰同属于平焰火焰,但却不需要冷却装置来防止燃烧器表面出现烧结现象,这与其较高的气体流速有一定的关系。二者的相同点在于其火焰都是平铺的火焰,因此Hencken燃烧器也常用于光学诊断研究。
2.3 对冲燃烧器
对冲燃烧器也称为逆流扩散火焰燃烧器,最初被Katz 等[43−44]用 来 进 行SiO2 和TiO2 的 制 备 分 析。Hung等[44−45]使用的对冲燃烧器由两根垂直相对的矩形管组成,如图6所示。矩形管分为三部分,中央通道用于传输燃料和氧化气,中央通道管内有填装玻璃珠的侧通道。两个矩形管的出口相对,上方的矩形管通入氧气和氩气的混合气,流经被多孔板和玻璃纤维支撑的玻璃珠床进行充分混合,混合后的氧化剂气体通过三个不锈钢筛网形成均匀流体从上方矩形管中流出;下方矩形管中的燃料气氢气和氩气经玻璃珠充分混合,经由不锈钢筛网形成均匀流体与相对的氧化剂形成对冲火焰。燃烧器的出口处为熔融石英板,能够在承受高温的同时,使得燃烧气体沿着矩形燃烧器的长边流出,形成平坦的火焰。为了防止产物在出口处沉积,将前驱物从矩形燃烧器的侧通道通入,侧通道玻璃珠使前驱物与惰性气体均匀混合。Liang 等[46]采用模拟方法研究对冲火焰燃烧器的温度分布,以甲烷和氢气作为燃料气,空气为氧化剂,得到温度分布在300~2000K之间,且火焰最高温度在距离滞止平面大约2mm处。
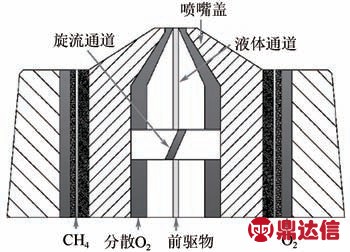
图6 对冲燃烧器结构示意图[44]
对冲火焰与McKenna 平焰火焰、Hencken 平焰火焰都能得到近似一维的扁平火焰,这样的火焰被研究者们广泛应用于原位激光诊断和光学测量,但三者间又存在差异。对冲火焰中将平均轴向速度为零的位置称为滞止平面,因此也称对冲火焰为滞止点火焰,而McKenna火焰与Hencken火焰没有类似平面。此外,虽然对冲火焰得到的初级粒子尺寸与其他燃烧器的初级粒子尺寸相似,但是由于对冲火焰的特殊结构限制了颗粒的团聚,所以能够得到低团聚度的球形纳米颗粒。在对冲火焰燃烧器的研究历程中,Zhang 等[16]对该燃烧器进行了改进,将常规采用的矩形管更改为同心圆管,前驱物、燃料气、氧化气和氮气通过下方的圆管通入到火焰场中,上方圆管通入高温氮气,通过调整前驱物和燃气的进料量可对滞止平面位置进行灵活调控,使其由原来的两个圆管出口中间位置上移,这样会使得火焰平面与滞止平面间存在一定距离,在该空间内粒子的生长可以通过光学辅助成像系统完成在线分析测量。
2.4 滞止火焰燃烧器
对于火焰合成制备纳米颗粒,研究者发现减小颗粒在火焰场中的停留时间能够在保持其前驱物浓度不变的前提下获得粒径较小的纳米颗粒。火焰场中加入低温或者水冷基板[47],如图7所示,在缩短火焰长度的同时能够实现高温火焰场与低温基板之间较大的温差,生成的颗粒能够快速沉积在基板上并形成薄膜,因此滞止火焰也常被用来制备纳米薄膜材料。
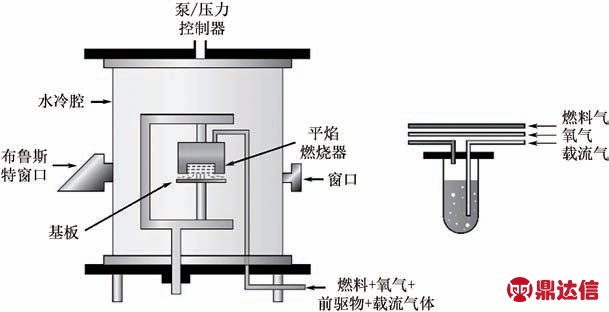
图7 滞止火焰装置图[47]
滞止火焰燃烧器结构特征主要为燃烧器火焰上方设有低温或者水冷基板,存在以下主要特点:①较高的温度梯度能够得到粒径较小的纳米颗粒;②控制水冷或低温基板与火焰出口的距离能够调节颗粒在高温场中的停留时间,减少颗粒的团聚现象;③低温基板有利于纳米颗粒在基板表面形成结构均匀的纳米薄膜。除此之外,基板距离燃烧器出口处的位置相对固定,保证了颗粒在火焰场中的停留时间及所经历的温度历程相同,使得沉积在基板上的颗粒粒度分布比较集中。Feng等[48]使用双色测温法对滞止火焰的温度进行测量,得到火焰最高温度为1800K,且滞止板位置距离燃烧器出口处距离增加,火焰的平均温度呈现出上升的趋势。滞止板位置对于火焰的流场有重要影响,较低的位置会产生较大的速度梯度,从而影响火焰场中的燃烧状况。
2.5 火焰喷雾热解装置
元素周期表上几乎所有金属元素的氧化物、盐及其单质都可以使用火焰喷雾热解技术(FSP)来制备,尤其对于低挥发性的前驱物,火焰喷雾热解技术是一个较好的选择[49]。Sokolowski 等[12]早期用乙酰丙酮铝喷雾在苯−乙醇中合成Al2O3纳米颗粒,之后随着火焰喷雾热解技术的逐渐成熟及燃烧器结构的不断优化,越来越多的高性能材料能够使用该装置进行制备。图8为火焰喷雾热解燃烧器的结构示意图,该燃烧器主要由喷嘴和用于引导燃料气和氧化气的同轴通道组成。前驱物分散在有机溶剂中并通过最中心的圆管到达火焰场,其中有机溶剂不仅能够溶解前驱物,以液相形态携至火焰场,同时在火场中燃烧释放大量的热,从而提高火焰场温度。在前驱物与燃料气之间设有环隙通道,将气流量较大的氧气作为分散气通过环隙通道,在通道末端设置旋片对分散气施加旋流,旋流的存在能够使前驱物更充分地被分散气撞击而雾化成微米级的液滴,此类合成方式对纳米颗粒的生成至关重要。与此同时,在分散气外围通入的燃料气和氧化气将在喷嘴上方形成包裹着中心雾化火焰的高温火焰场,进一步为前驱物在火焰场中的反应提供稳定的高温环境。Pratsinis 等[50]使用二甲苯作为燃料得到反应器温度分布范围为300~3600K,相同燃料当量比情况下前驱物流量不同产生的温度区间范围有所区别。Luliis 等[51−52]以甲烷与空气当量比0.8 产生预混火焰,前驱物溶剂为乙醇的条件下实验测得距燃烧器出口2cm、4cm、6cm 处温度值约为2947K、2880K、2757K,随着距离燃烧器出口处位置的增加,温度呈现出先升高后下降的趋势。Liang 等[53]以甲烷和氧气作为燃烧气体,为防止燃烧过热采用氮气作为吹扫气,得到不同前驱物溶液下燃烧器的最高温度变化,其中使用水作为前驱物溶剂得到火焰温度为802K,而乙腈和2−乙基乙酸作为混合溶剂得到火焰温度为1810K,这说明火焰喷雾热解装置的火焰温度与前驱物溶剂有很大关系。
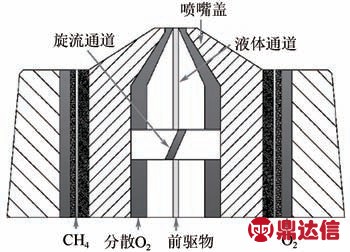
图8 火焰喷雾热解结构燃烧器示意图[50]
火焰喷雾热解装置能够产生较高的温度和较大的温度梯度[54]。较高的局部温度能够使材料颗粒更均匀,具有更高的结晶度,同时高温可以促使颗粒进一步烧结、团聚,进而促进颗粒生长。较高的温度梯度能够使高温场中产生的纳米颗粒快速冷却,冷却后的纳米颗粒由于温度降低到熔点以下,因此团聚现象减缓,生成粒径较小的纳米级颗粒。除此之外,火焰喷雾热解与其他燃烧器的不同点还在于:①前驱物进料通常溶解于有机溶剂中,可能出现火焰喷雾热解燃烧器中燃料气和氧化气产生的热量占比较小,而有机溶剂的燃烧放热占比较大的情况;②火焰喷雾热解前驱物是以喷雾的形式进料。环隙通道的分散气常以与轴向成一定夹角射入流场,促使由中心管喷出的前驱物发生剪切破碎,最终形成雾化微液滴喷入到火焰场中,有利于超细颗粒的生成。
火焰喷雾热解装置由于其特殊的结构和流场特性能实现材料的批量生产,目前已经被广泛应用于工业纳米氧化物、混合氧化物和掺杂氧化物的制备,如金属单一氧化物、金属混合氧化物、氮氧化物等。近期关于火焰喷雾热解的研究专利主要包括两个方面:一是对前驱物和产物颗粒进行改进,如通过实验方法筛选最佳前驱物溶剂[55],或者对得到的产物进行球混或者煅烧后处理来进一步得到混合纳米氧化物[56];二是对装置设备进行改进[57],如日本的新型发明专利是将火焰喷雾热解产生的火焰与前驱物形成的喷雾形成90°位置分布,在燃烧器外围加上热解炉层,避免前驱物在高温环境中产生的颗粒与火焰直接接触,从而在热解炉形成的高温环境中反应得到粒径分布较窄的无机氧化物颗粒。
上述为同轴扩散火焰燃烧器、平焰燃烧器、对冲燃烧器、滞止火焰燃烧器及火焰喷雾热解装置的结构及温度场流场特点,表1为各燃烧器关于其温度场的调研信息。不同燃烧器使用不同的燃料气和氧化剂得到的温度范围不同,且温度范围大小与燃烧器的结构有很大的关系,例如滞止火焰燃烧器因存在滞止水冷板出现较大的温度梯度,综合分析不同燃烧器的温度场和流场特点才能实现对颗粒产物的调控。
表1 不同燃烧器温度信息
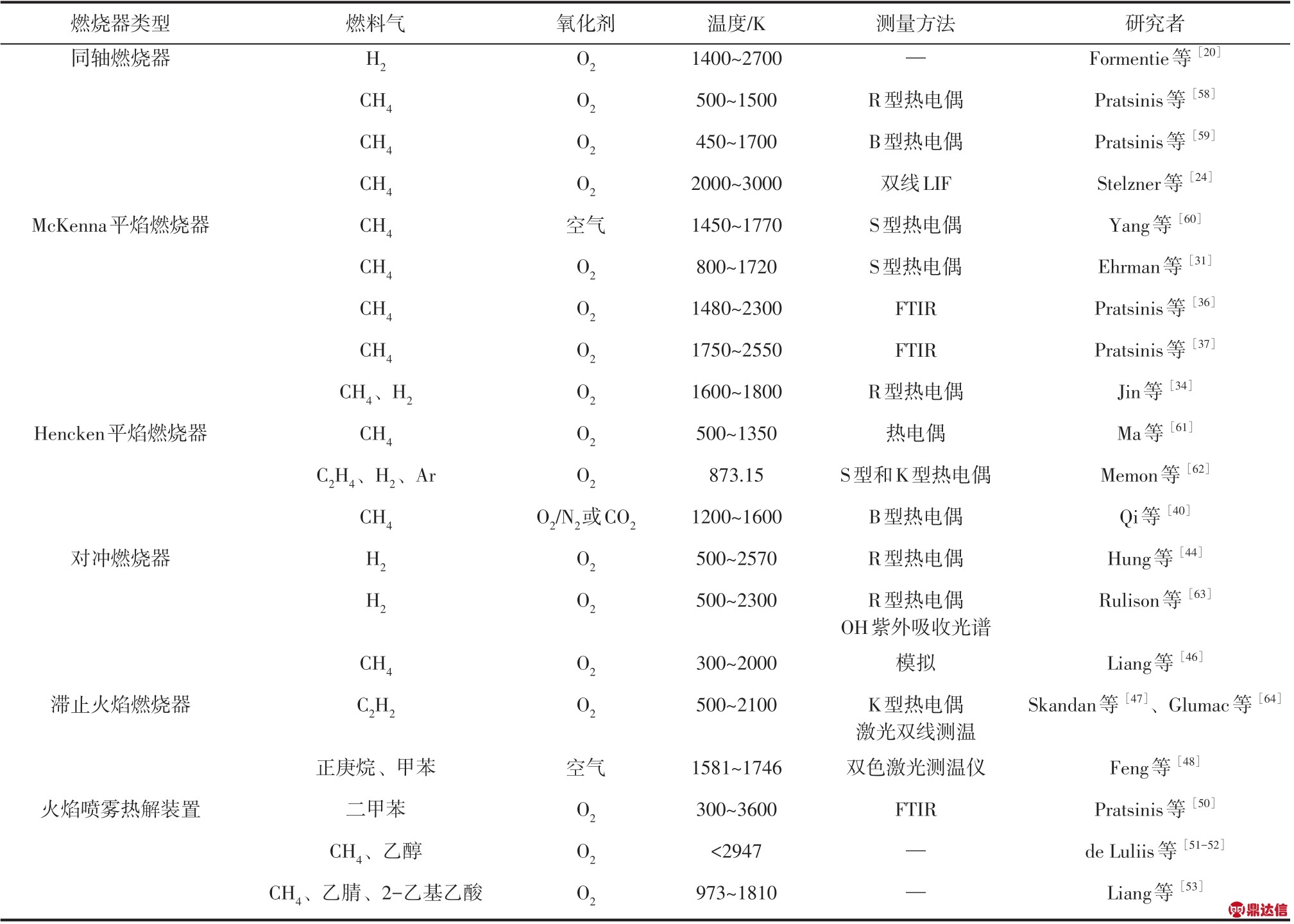
3 TiO2制备及分析
颗粒的粒径、形貌等物理特性与颗粒形成时的温度以及颗粒在火焰场中的停留时间有关。其中温度是实现TiO2晶型转变的关键,文献指出锐钛型转变为金红石型TiO2的温度为610~915℃,板钛型在650℃温度下可以转变为金红石型[65−66];颗粒在火焰场中的停留时间对颗粒晶型的影响体现在颗粒晶型转变需要一定的时间和温度条件,停留时间足够长可确保颗粒中的锐钛型转变为金红石型,但与此同时,停留时间也影响颗粒的粒径,颗粒在高温火焰场中的停留时间延长将意味着有更多的时间完成团聚或者烧结过程,长时间的团聚或者烧结会使颗粒不断生长,导致产物颗粒的粒径发生变化,出现较大的TiO2颗粒。对于高端颜料级钛白粉而言,根据颗粒衍射效率与粒径之间的关系,最佳颗粒粒径范围应为可见光波长的一半,即200~350nm,因此TiO2颗粒的粒径过大将严重削弱其使用效果[67−70]。
3.1 不同燃烧器下的TiO2制备特性
不同燃烧器由于其结构不同,产生的火焰结构、温度等有所区别,得到的二氧化钛在粒径和晶型上也有所差异,如表2所示。分析不同燃烧器的结构及其产物形貌对于制备钛白粉纳米材料具有重要的指导意义。
表2 不同燃烧器制备TiO2相关信息
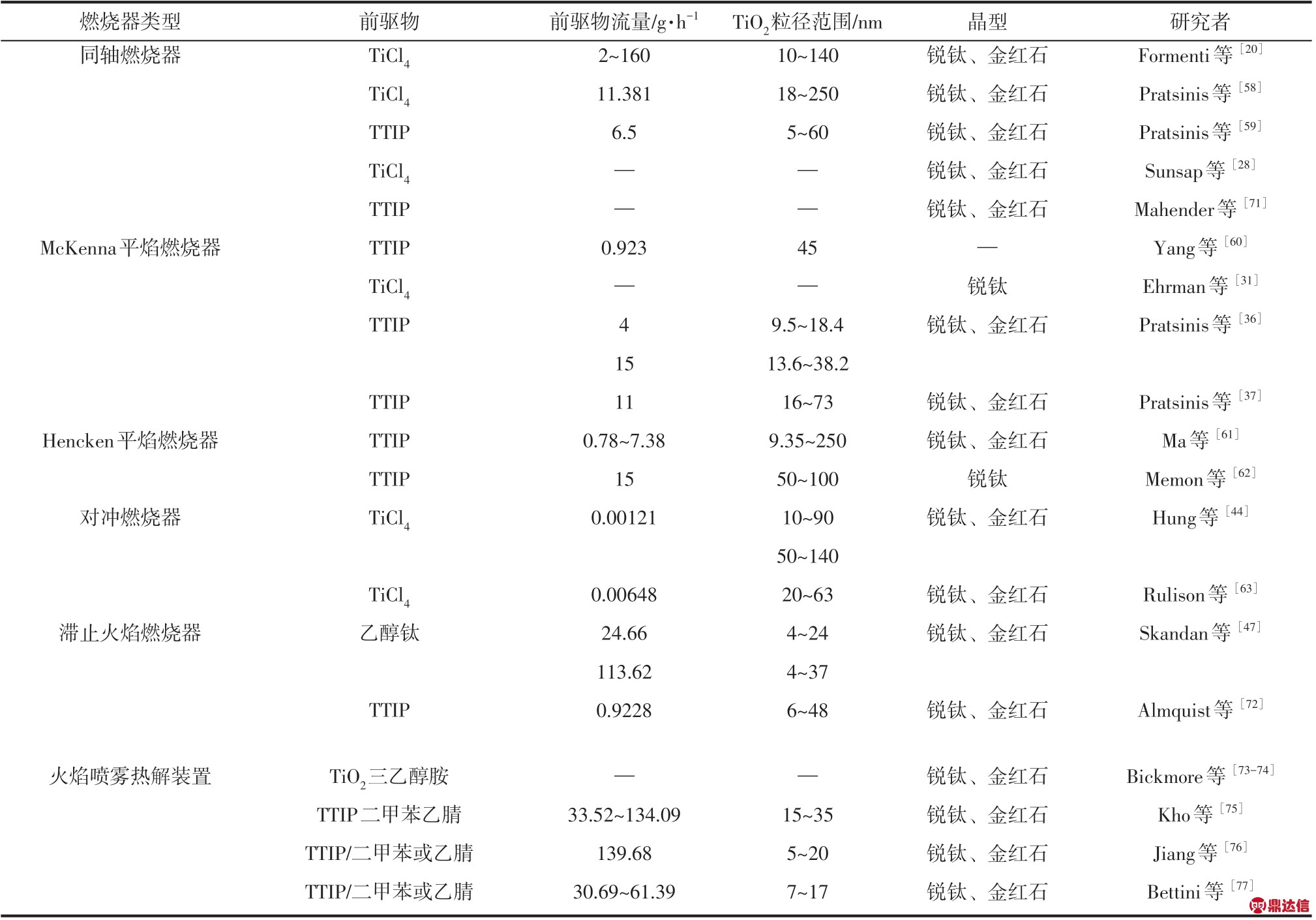
Formenti 等[20]采用4 通道圆管同轴扩散火焰燃烧器制备了TiO2纳米颗粒,将TiO2的前驱物TiCl4通过氧气作为载流气体输送到火焰场中,前驱物气流层与燃料气之间增加了氮气流通道以推迟燃料气氢气向前驱物的扩散,同时在最外层设置氧气气流。测试表明,该燃烧器的火焰温度可达1700K以上,产物晶型为锐钛型TiO2 夹杂少量金红石型TiO2,最小粒径可达6nm,通过改变TiCl4气体流速等实验操作条件,计算得到TiO2 的最大粒径为44nm。Mahender 等[71,78−79]使用液态石油气作为燃料气,以TTIP作为前驱物鼓泡进料,燃烧后的产物附着在玻璃纤维过滤器中,经SEM与TEM测量分析得到锐钛型与金红石型占比分别为63%和28%,颗粒平均粒径为26nm,且相比较于德固赛P25(二氧化钛纳米级白色粉末,锐钛型和金红石型的质量比约为79/21),具有更好的光催化性能。Sunsap 等[28]在同轴燃烧器中调节燃料与氧气的流量比,从0.2 增加到0.3,TiO2平均粒径从121.6nm增加到181.2nm,金红石型质量分数变化范围为7.1%~13.0%。
Ehrman 等[31]使用McKenna 平焰预混燃烧器研究SiO2、TiO2颗粒,使用TiCl4在火焰中合成TiO2纳米颗粒,得到锐钛型TiO2 其平均粒径为13nm±1nm。对比分析发现,使用McKenna平焰预混燃烧器得到的SiO2颗粒平均粒径(10nm±1nm)要小于TiO2颗粒。分析原因可能是由于在火焰场中二者的团聚行为不同,TiO2的团聚通过固态扩散实现,而SiO2的团聚通过黏性流动实现。Pratsinis团队[36−37]以TTIP为前驱物制备纳米TiO2,产物晶型分析表明在较高温度和较长的停留时间下更易得到金红石型二氧化钛,同时贫氧环境也有利于金红石型二氧化钛生成。在不同TTIP 浓度条件下,燃烧器上方不同距离处的产物粒径分布不同,主要分布在9.5~44nm 之间,同时也存在少量直径大于60nm 的大颗粒。
Ma等[61]使用Hencken平焰扩散燃烧器制备了粒径较小的二氧化钛纳米颗粒,将TTIP 与CH4混合物由Hencken燃烧室下腔通入,经陶瓷管道到达燃烧器的出口表面,氧气和氮气从燃烧室上腔进入,能够得到最小粒径为15nm 的二氧化钛颗粒,且颗粒中锐钛型二氧化钛质量分数为84.5%,金红石型仅为15.5%。改变氧/氮比能够在距离燃烧器出口3cm处得到粒径范围在15~22nm间的TiO2颗粒。在一定的氧/氮比条件下,随着收集高度的增大,产物颗粒间的碰撞频率增加,颗粒在火焰场中的停留时间延长,一定程度上强化了颗粒间的团聚作用,最终发展成直径为65~250nm 的较大颗粒。Memon等[62]以H2为燃料气通过Hencken平焰燃烧器制备得到锐钛型TiO2,TEM分析表明TiO2粒子多数呈现多面体形状,粒径分布在50~100nm 之间,产物颗粒中不含有金红石型的原因主要是火焰场温度较低,平均约600℃,该温度范围不足以使锐钛型TiO2发生晶型转变。研究还发现,较低温度和较高载气流速能够减少产物颗粒在火焰场中的停留时间,产生无定型颗粒,使锐钛型产物纯度有所降低。
Zhang 等[16]将TTIP 进行鼓泡通过对冲火焰燃烧器制备TiO2纳米颗粒,并使用热泳采样和TEM 分析得到的滞止平面处颗粒粒径约为10nm。Hung等[44−45]使用对冲火焰燃烧器制备SiO2/TiO2的包覆氧化物,发现在前驱物中添加TiCl4改变了火焰的发光层分布,使第二发光层低于第一发光层约几毫米,且间隔有黑色区域。采用动态光散射法测量得到低温下的TiO2粒径范围为10~90nm,而高温环境下的颗粒较大,为50~140nm,且得到的包覆复合材料中TiO2主要是金红石形态,前驱物中Si 与Ti的浓度比为1.0 时能够得到包覆效果较好的纳米颗粒。
Skandan 等[47]使用滞止火焰燃烧器制备TiO2纳米颗粒,将TiO2的前驱物乙醇钛与乙炔燃料、氧气、载流氮气进行预混得到预混平焰。前驱体在高温火焰场内发生分解,并伴随着火焰气流在低温基板附近冷却凝聚。由于基板位置固定,颗粒在火焰场的路径和所处温度环境相同,最终得到了粒径均匀的纳米颗粒产物。但不同前驱物流速形成产物颗粒的粒径分布有所不同,低浓度(0.0018mol/min)进料条件下得到的产物颗粒粒径分布在4~24nm 之间,而高浓度(0.0083mol/min)进料条件下得到了4~37nm范围内的TiO2纳米颗粒。Almquist等[72]采用滞止扩散火焰燃烧器制备TiO2粉体颗粒,前驱物TTIP 通过鼓泡蒸发器进料,并在火焰出口上方放置水冷钢板用来沉积纳米颗粒,实验过程中水冷板与燃烧器之间的火焰温度可达1400℃以上,分析表征后得到TiO2有效粒径范围为6~48nm,且颗粒中大部分以锐钛型为主,金红石型含量较少。
Bickmore 等[74]以二氧化钛水溶胶与三乙醇胺在乙二醇溶液中进行反应制备得到Ti 的金属醇盐前驱物,将该前驱物溶解于乙醇并雾化进入火焰场中,制备二氧化钛纳米颗粒粉体。通过XRD分析,火焰喷雾热解得到的二氧化钛颗粒为金红石型与锐钛矿型的混合物,其中金红石型占比约为10%,通过TEM 分析得到颗粒粒径分布范围为10~100nm,且大部分颗粒的粒径约为34nm。Kho等[75]采用TTIP(溶解在甲醇中)、二甲苯、乙腈等按照一定比例混合作为前驱物,使用火焰喷雾热解制备得到二氧化钛纳米颗粒,发现在富氧和贫氧条件下得到的二氧化钛有所不同,富氧条件下以锐钛型为主,金红石型较少,质量占比约为4%,而贫氧条件下金红石型二氧化钛占比高达94%,锐钛型二氧化钛含量较少,锐钛型和金红石型TiO2的粒径均在20~35nm之间。
分析前述多种燃烧器TiO2制备相关工艺参数及条件,表3进一步总结了燃烧器制备二氧化钛的前驱物选择以及燃料气、氧化气等。
表3 典型合成燃烧器的前驱物及入口气相类型

3.2 产物及特点分析
表2给出了不同燃烧器在不同前驱物流量下得到的TiO2颗粒粒径分布范围,可以看到,不同燃烧器在相同的前驱物流量范围内得到的产物TiO2颗粒的粒径存在差异,前驱物流量是影响颗粒粒径的重要因素,但颗粒的粒径应是燃烧器提供的温度场、流场以及前驱物流量导致的浓度场等综合作用的结果。图9为不同燃烧器得到的TiO2粒径范围,根据3.1 节进行综合分析,不同燃烧器由于其特殊的结构以及操作条件,产物TiO2粒径分布有所不同。同轴扩散火焰燃烧器能够得到的TiO2纳米颗粒粒径分布在6~250nm范围内,McKenna平焰燃烧器能够得到粒径范围较小的颗粒(9.5~73nm),Hencken 平焰燃烧器能够得到粒径范围较大的颗粒(9.35~250nm),通过对冲火焰燃烧器得到的颗粒粒径最小为10nm,最大颗粒粒径能够达到140nm,火焰喷雾热解装置得到颗粒粒径在10~100nm 之间,对于滞止火焰燃烧器,其制备颗粒的最小粒径为4nm,粒径范围在4~48nm之间。
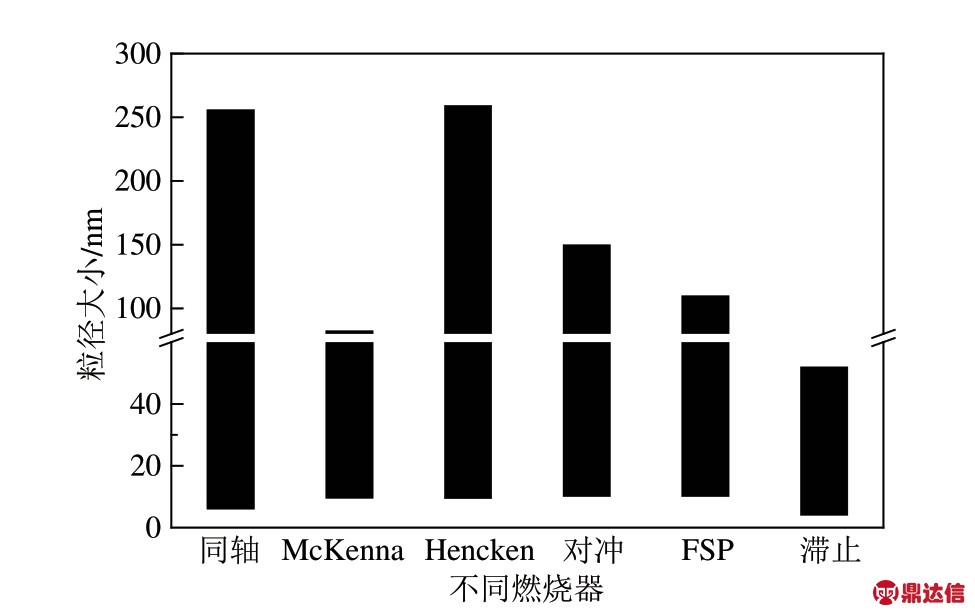
图9 不同燃烧器得到TiO2粒径范围
通过分析发现在所涉及的燃烧器当中,滞止火焰燃烧器得到的TiO2产物粒径相对较小,这是由于滞止火焰燃烧器具有较高的冷却速率,能够产生较大的温差,火焰场中生成的纳米颗粒在较大温差下快速冷却,减少团聚和烧结现象,同时较高温差能够使部分锐钛型二氧化钛转变成金红石型二氧化钛。McKenna平焰燃烧器的产物粒径范围较小,且TiO2产物以锐钛型为主,这是因为平焰燃烧器的火焰结构较短,颗粒在火焰场中停留时间缩短,部分锐钛型TiO2来不及转变为金红石型就离开火焰场。相较于McKenna平焰燃烧器,改进后的Hencken平焰燃烧器具有较长的焰程,能够实现部分金红石晶型的转变。对冲火焰燃烧器能够得到金红石型TiO2,主要得益于其较高的火焰温度和较长的平焰结构。虽然对冲火焰燃烧器产生的火焰近似于平面结构,但是氧化气与燃料气具有较高的气流速度,火焰场中生成颗粒沿着火焰滞止平面流出火焰场,在较长且较高温度的火焰场中能够实现颗粒晶型的转变。火焰喷雾热解装置能够得到仅含有锐钛型或者金红石型的TiO2,这得益于其独特的结构优势,不仅能够实现前驱物以较高的速度进入火焰场中,而且前驱物中的有机溶剂在火焰场中能够释放大量的热,实现火焰场温度的快速升高,这些也有利于产物晶型的转变。值得注意的是在标准大气压和常温下,金红石型在热力学性能上比锐钛型更为稳定,但是Zhang等[80]的研究表明颗粒粒径低于14nm时锐钛型呈现出更稳定的状态,Memarzadeh等[81]的工作表明晶型与颗粒的大小密切相关,且缺氧条件下颗粒表面若存在大量的氧表面空位则更易形成金红石结构,这与Pratsinis 等[58]和Kho 等[75]的结论一致。同轴扩散火焰燃烧器相较于其他燃烧器具有结构简单、易工业放大的优势,且同轴扩散火焰场可以通过调节气体流量来改变层流或者湍流状态,进而调节产物粒径,较长的火焰结构能够实现液相−颗粒相或者气相−颗粒相的转变过程。除此之外,同轴火焰燃烧器也能像平焰燃烧器一样借助光学辅助元件完成对火焰场中信息的在线诊断,获得火焰场的相关信息,例如火焰场的温度、反应热、放热等信息[82−83],完成对火焰场中的相关反应和机理的描述分析。
4 结语
与氯化法高温氧化过程相似的火焰合成法能够快速得到二氧化钛及其他氧化物纳米颗粒,了解火焰合成方法的内容以及合成过程,能够实现对产物纳米颗粒的生长机理分析,进一步实现对产物形态的调控。本文从TiO2纳米颗粒出发,综述比较了火焰合成方法中不同燃烧器的技术特点,主要内容如下。
(1)根据前驱物进料方式的不同,火焰合成可分为气相进给合成和液相进给合成,其中气相进给合成更容易获得粒径较小的纳米颗粒,液相进给合成能够得到空心结构的纳米颗粒。
(2)燃烧器是火焰合成过程中的核心装置,常见的燃烧器包括同轴扩散火焰燃烧器、McKenna平焰预混燃烧器、Hencken平焰扩散燃烧器、对冲火焰燃烧器、火焰喷雾热解装置、滞止火焰燃烧器等,各种燃烧器由于结构存在差异,其温度场和颗粒生长路径不同,适用的场合有所区别。
(3)燃烧器对TiO2纳米颗粒形态影响颇大,综合分析得到不同的二氧化钛的前驱物以及实验工况条件,并对产物TiO2粒径和晶型进行了分析比较,指出同轴火焰燃烧器相对于其他燃烧器操作简单,易于工业放大,借助激光测量技术能够实现对产物颗粒的可控合成,对于燃烧合成法制备TiO2具有一定的借鉴和指导意义。