摘要:为研究旋转组合密封圈表面结构对密封性能的影响规律,对方圈表面分别加工单槽和双槽等不同表面结构,利用ABAQUS仿真分析不同表面结构的旋转组合密封圈在完成过盈安装与流体加载后的应力及接触压力分布,并研究油槽宽度变化对组合密封性能的影响。仿真结果表明:在过盈安装与流体加载情况下,O形圈的最大von Mises应力均有所减少,而带槽密封圈最大von Mises应力都出现增长,且过盈安装状态下应力增幅较大;带槽密封圈接触面被油槽分为多段,每段接触压力曲线相似,而接触压力均有不同程度的增大;方圈最大von Mises应力值在过盈安装状态下随着宽度增加而增大,在流体加载状态下随着宽度增加有不同程度的减小。方圈表面增加油槽有利于在动密封面上形成多个动压润滑区域,对增强密封性能、改善润滑条件具有一定作用,但增加油槽后会增大方圈应力,增加疲劳损坏风险。
关键词:组合密封;表面结构;高压动密封;密封性能
随着密封技术的进步和应用领域的拓展,对密封件的耐压性能和使用寿命都提出更高要求。组合密封因综合了不同密封结构和材料的优势,性能得到较大提升,在深海勘探、石油钻井、航空试验等多领域得到广泛应用和研究[1-3]。文献[4-5]针对往复活塞密封建立了不同计算模型,分析了预压缩量及工作压力等参数对泄漏量的影响。文献[6]基于软弹流润滑模型建立了组合密封数值模型,研究了表面粗糙度、介质压力和运动速度等参数对密封圈性能的影响。文献[7]利用Abaqus/CAE内核程序创建了格莱圈的计算模块,通过该模块对格莱圈的密封性能进行分析计算。文献[8-9]对不同结构特征的滑环式组合密封圈进行了仿真研究,分析了结构参数对于密封性能的影响规律。针对工程应用问题,文献[10]研究了齿形滑环组合密封在高压下的密封性能,并结合试验进行了摩擦力矩计算。文献[11]以深海高压环境下的组合密封结构为对象,研究了组合密封结构在深海高压环境下几何变形情况及密封界面上接触应力的分布规律。文献[12]针对液压缸在振动工况下出现的内泄漏问题,提出一种轴向振动作用下格莱圈密封泄漏量的计算方法。
旋转组合密封与回转轴的接触面为动密封面,在仿真研究中为简化模型,常常将密封圈表面当作平面处理。由于组合密封圈材料性能差异大,特别在高压条件下使用,表面结构的影响不容忽视。文献[13]对旋转组合密封圈建立了三维模型,对影响其动密封特性的介质压力、O形圈压缩量、滑环厚度等参数进行仿真,并对滑环接触表面开有0.3 mm的半圆槽结构进行研究,结果表明增加油槽后密封接触压力会显著增大,但该文献对开槽密封圈的接触压力和应力分布规律及结构参数的影响未做进一步研究。本文作者采用有限元分析软件ABAQUS对不同表面结构的组合密封性能进行仿真研究,对组合密封的使用及结构改进提供一定参考。
1 旋转组合密封表面结构
旋转组合密封圈由橡胶弹性体O形圈和改性聚四氟乙烯(PTFE)方圈组成,与O形圈、唇形密封等旋转密封不同,为保证高压下的密封性能,组合密封圈与回转轴接触面较宽。为减少摩擦损耗,改善高压下的启动性能,方圈表面往往会增加油槽以减少接触面积,改善润滑性能。常见的表面结构有单槽及双槽结构,如图1所示。文中主要选用内径为100 mm的某型外轴用格莱圈进行仿真分析,其工作压力范围0~20 MPa,O形圈直径3.53 mm,沟槽宽度4.2 mm,设定油槽长度L=0.75 mm,宽度W=0.5 mm。
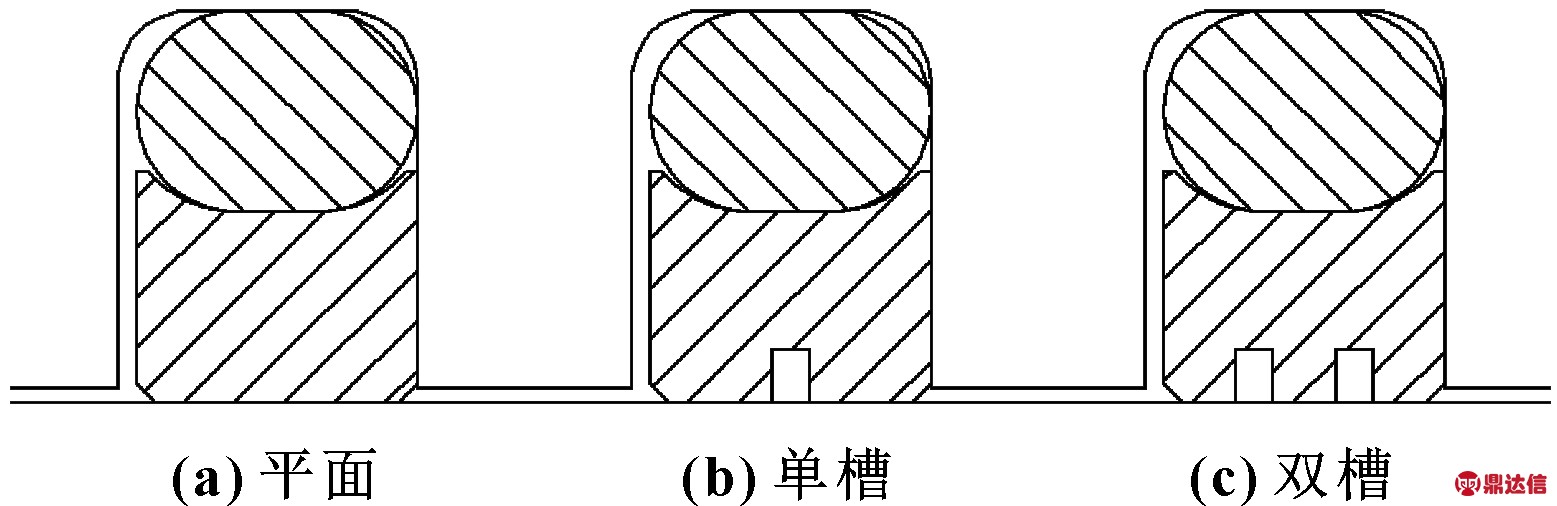
图1 不同表面结构的组合密封圈示意
Fig 1 Schematic of different surface structure combination seals (a)flat structure;(b)single groove structure;(c) double groove structure
2 有限元建模与仿真
2.1 有限元建模
采用轴对称模型对旋转组合密封圈进行建模,有限元模型如图2所示,模型上部为流体侧,下部为空气侧。方圈采用线性模型描述,单元类型选用CAX4R单元;O形圈采用超弹性Mooney-Rivlin本构模型描述,采用CAX4RH单元以适应大变形特征。回转轴与沟槽采用刚体结构,固定沟槽参考点作为初始边界条件。
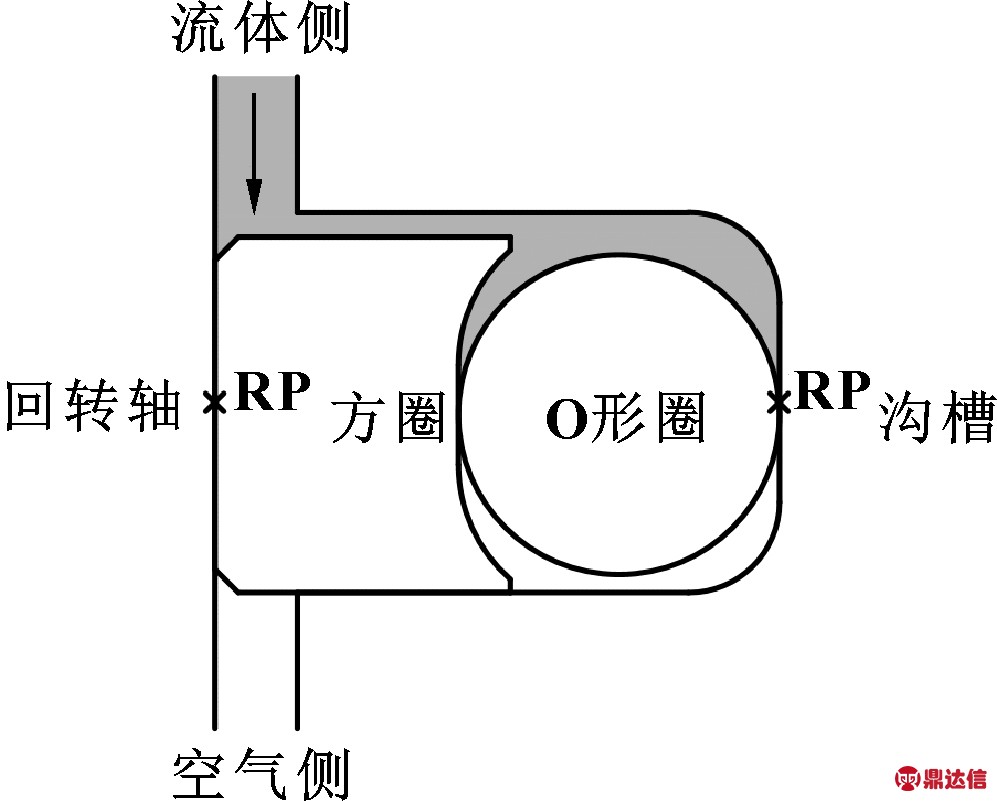
图2 旋转组合密封有限元模型结构示意
Fig 2 Schematic of the structure of the rotating combination seal finite element model
组合密封材料及性能参数见表1。其中O形圈选用丁腈橡胶,参照文献[8],设定模型参数C1为1.87 MPa,C2为0.47 MPa。
表1 密封材料性能参数
Table 1 Sealing material performance parameters
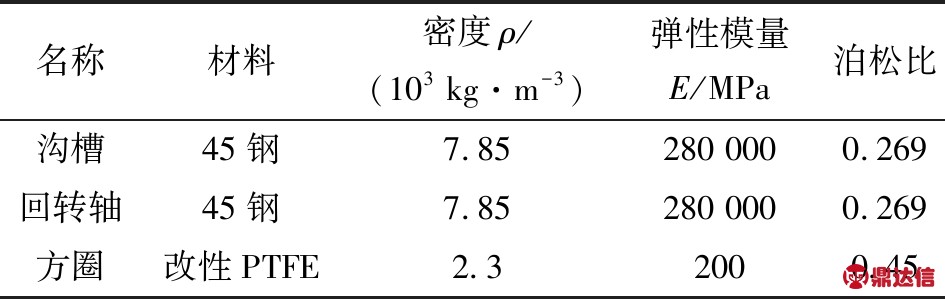
组合密封各接触面均为采用罚函数法定义的面-面接触类型,根据密封结构共定义4对相互作用面,各接触对及摩擦因数设定见表2。
表2 组合密封圈接触对定义
Table 2 Definition of contact pairs of combination seal
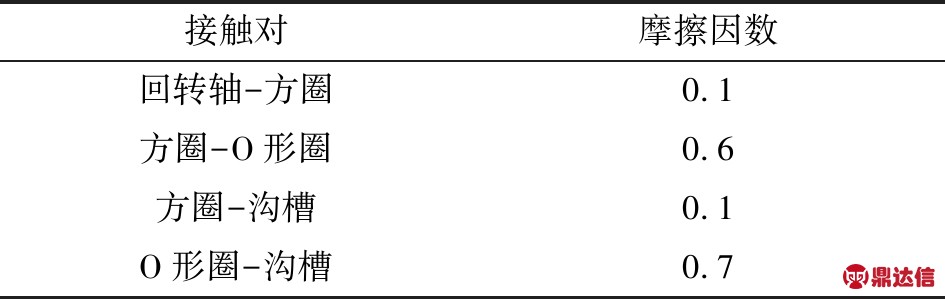
流体压力加载时,可通过ABAQUS流体渗透功能自动寻找各密封面接触与分离的临界点,使结果更加客观准确。本例中主要设置3个压力渗透面,分别为回转轴-方圈(压力渗透面I)、方圈-O形圈(压力渗透面II)、沟槽-O形圈(压力渗透面III),如图3所示。同时,针对组合密封表面结构变化后的受力特征,假定流体加载后方圈油槽内充满压力油,将油槽内表面也设定为压力渗透面,分段定义方圈与回转轴接触面并施加流体载荷,利用流体渗透功能进行分析计算。
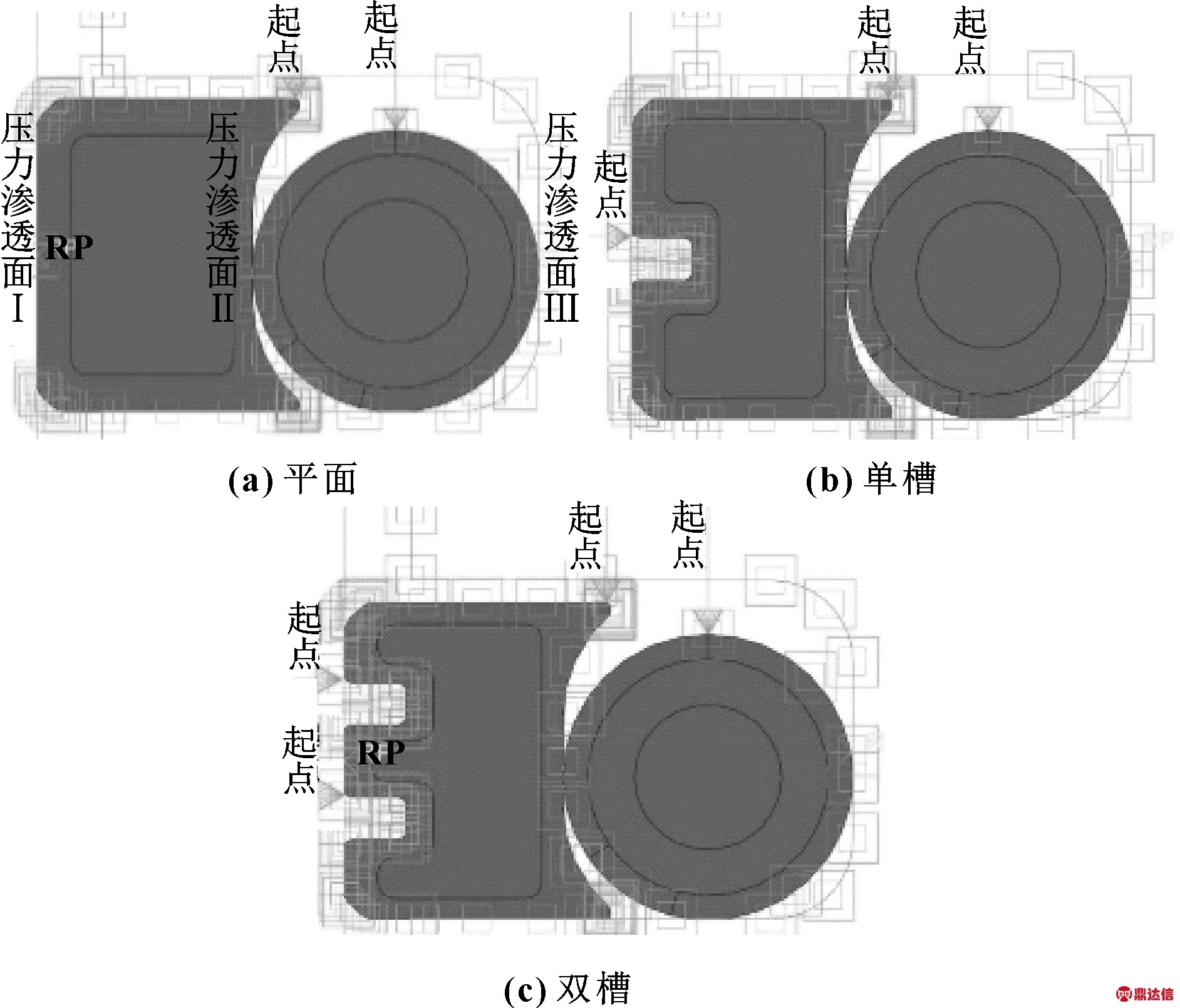
图3 不同表面结构组合密封模型及流体压力渗透示意
Fig 3 Combination seal model of different surface structures and schematic of fluid pressure permeation(a)flat structure; (b)single groove structure;(c) double groove structure
2.2 分析计算步骤
分析计算主要分为2个过程进行。首先模拟组合密封圈的过盈安装过程。本例有限元模型中,轴与沟槽初始距离0.81 mm。按照密封手册要求,高压下密封间隙不应大于0.2 mm。仿真中主要通过前2个载荷步实现此过程:在第一个载荷步中,回转轴向右移动0.04 mm,使密封结构中各接触关系平稳建立起来;在第二个载荷步中,回转轴继续向右移动0.6 mm,实现密封间隙0.17 mm,从而完成过盈安装。最后在第三个载荷步中施加流体压力载荷,完成流体加载过程。
3 仿真结果与分析
3.1 不同表面结构对密封性能的影响
设定流体加载压力20 MPa,对平面、单槽、双槽组合密封圈在过盈安装、流体压力加载后的密封性能进行对比分析。
3.1.1 不同表面结构对应力分布的影响
不同表面结构的组合密封圈在完成过盈安装和流体加载时的应力分布分别如图4、5所示。
由图4可知,过盈安装时,带槽密封圈最大von Mises应力值出现不同程度增加,其中单槽密封圈增加44.9%,双槽密封圈增加37.9%;高应力分布区域呈现一定差异,平面密封圈集中于方圈近空气侧,带槽密封圈主要集中在方圈油槽附近,且高应力区域明显增多;O形圈应力分布区域基本一致,主要在O形圈内部靠近沟槽底部一侧,带槽密封圈的O形圈最大von Mises应力值略有减少。
由图5可知,流体加载后,组合密封圈应力值较未加载时大幅增加。对比平面密封圈,带槽密封圈最大von Mises应力值均有增加,但增幅较过盈安装时小,其中单槽密封圈增加9.7%,双槽密封圈增加5.7%。平面密封圈和带槽密封圈的高应力分布区域相似,方圈近空气侧与回转轴及沟槽接触处、方圈背部与O形圈接触的尖角处都为高应力区域。带槽密封圈高应力分布区域还集中在油槽附近,其中单槽上部和双槽的上部是应力较为集中区域。O形圈应力分布区域基本一致,各密封接触面以及与方圈背部尖角接触处均为应力集中区域,带槽密封圈的O形圈最大von Mises应力值均有减少。
由上述仿真结果可知,表面结构对于组合密封圈应力分布有较大影响。在过盈安装和流体加载状态下,带槽密封圈应力值都出现一定增长,方圈高应力区域显著增多,而O形圈最大应力值出现减小。分析原因为,方圈表面增加油槽后降低了结构强度,过盈安装时容易产生变形,出现应力大幅增加的现象,流体加载后,方圈油槽内受到油液压力使变形状态得到改善,应力增幅相应减少。由于O形圈仅受接触面及流体压力作用,表面结构的改变对其影响较小。
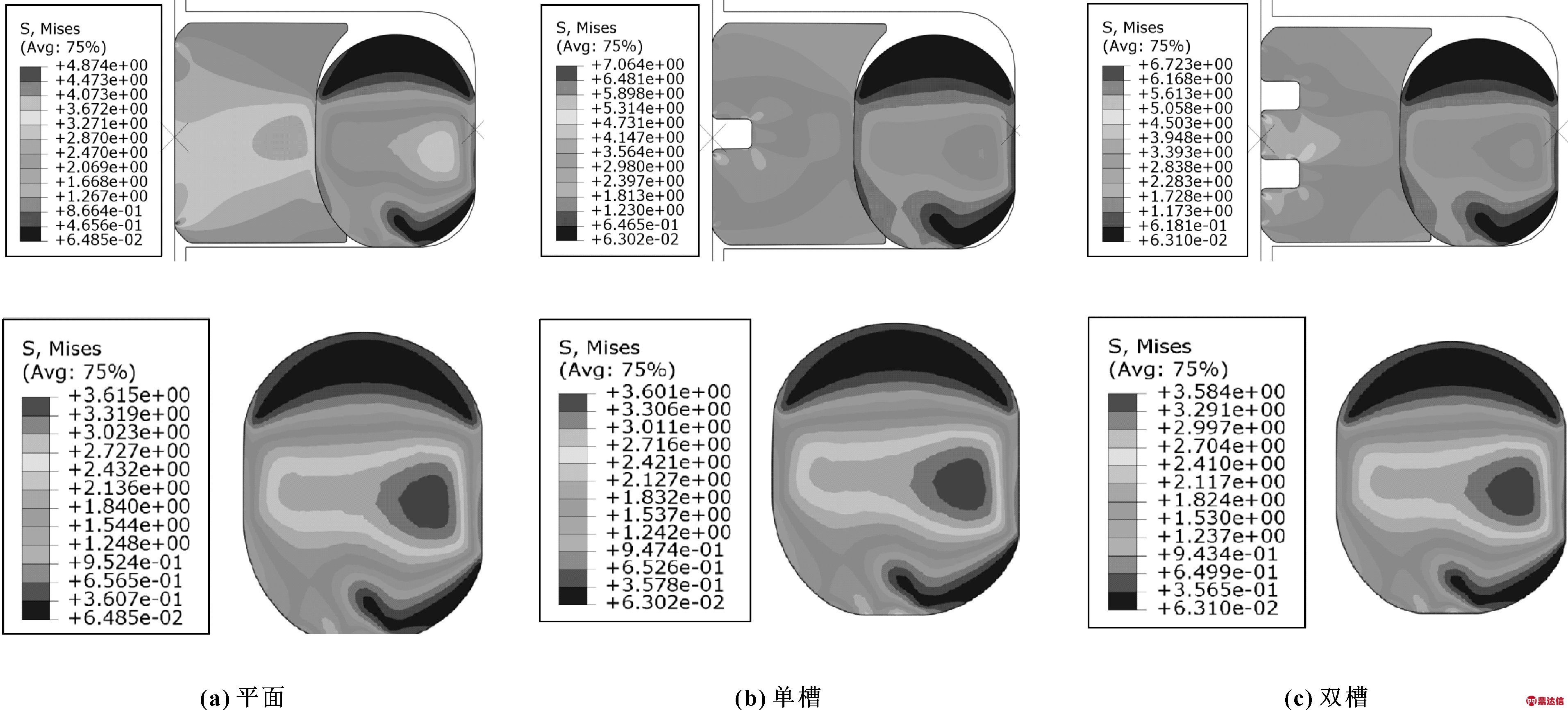
图4 不同表面结构的组合密封圈过盈安装时应力分布
Fig 4 Stress distribution of combination seals with different surface structures during interference (a)flat structure;(b)single groove structure;(c) double groove structure
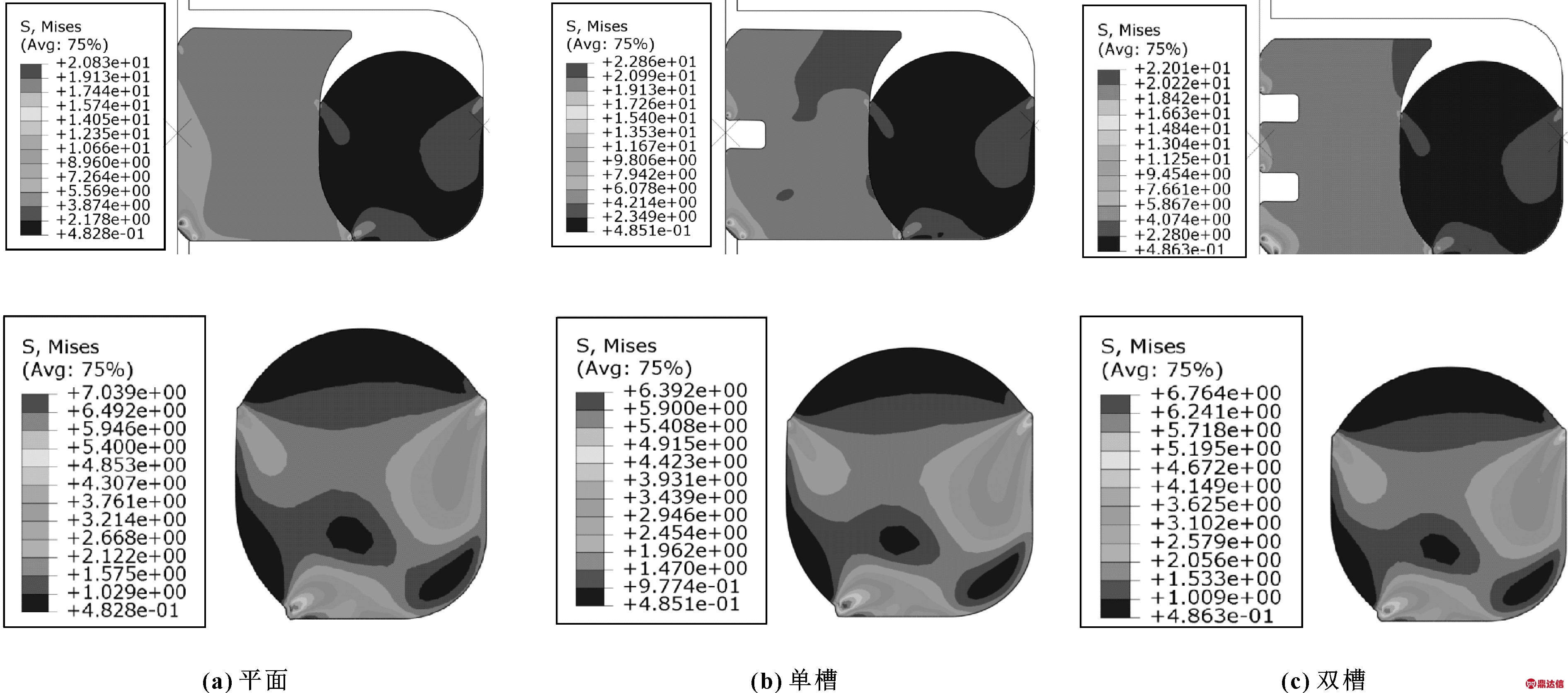
图5 不同表面结构的组合密封圈流体加载时应力分布
Fig 5 Stress distribution of combination seals with different surface structures under fluid loading (a)flat structure;(b)single groove structure;(c) double groove structure
3.1.2 不同表面结构对接触压力分布的影响
完成过盈安装及流体加载后,通过后处理创建路径方式,提取方圈与回转轴密封接触面上接触压力值。为方便对比分析,将方圈接触面划分为不同区域,如图6所示。其中A区为近流体侧,B区为近空气侧,CD和EF分别为油槽两侧。

图6 组合密封圈接触区域划分示意
Fig 6 Schematic of contact area division of combination seals
图7—9所示分别为平面、单槽、双槽密封圈在完成过盈安装和流体加载时的接触压力分布曲线。图中坐标原点对应方圈在流体侧与回转轴接触起点。
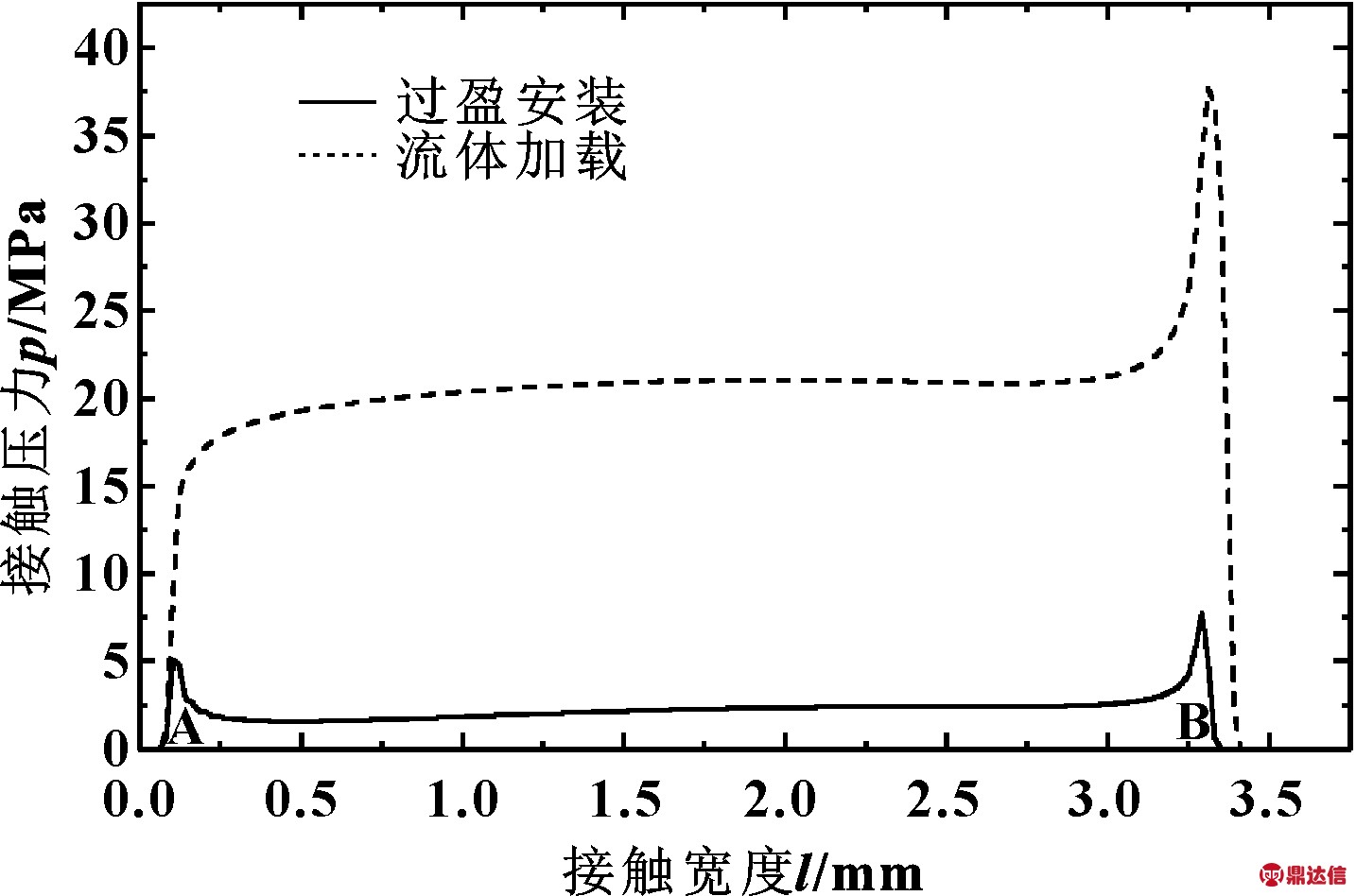
图7 过盈安装和流体加载时平面密封圈接触压力分布对比
Fig 7 Comparison of contact pressure distribution of flat combination seal after interference installation and fluid loading
由图7可知,过盈安装状态下,接触压力曲线A区(流体侧)和B区(空气侧)各出现一个峰值,其中B区峰值大于A区峰值,峰值附近压力梯度变化较大,峰值间压力分布相对平缓。流体加载后,密封面各结点接触压力大幅增加,接触压力曲线呈现单峰值形态,压力峰值出现在B区,峰值附近压力梯度变化较大。此压力分布有利于动密封接触面产生流体动压润滑区域,对改善高压下密封接触面的润滑状况十分有利[14]。
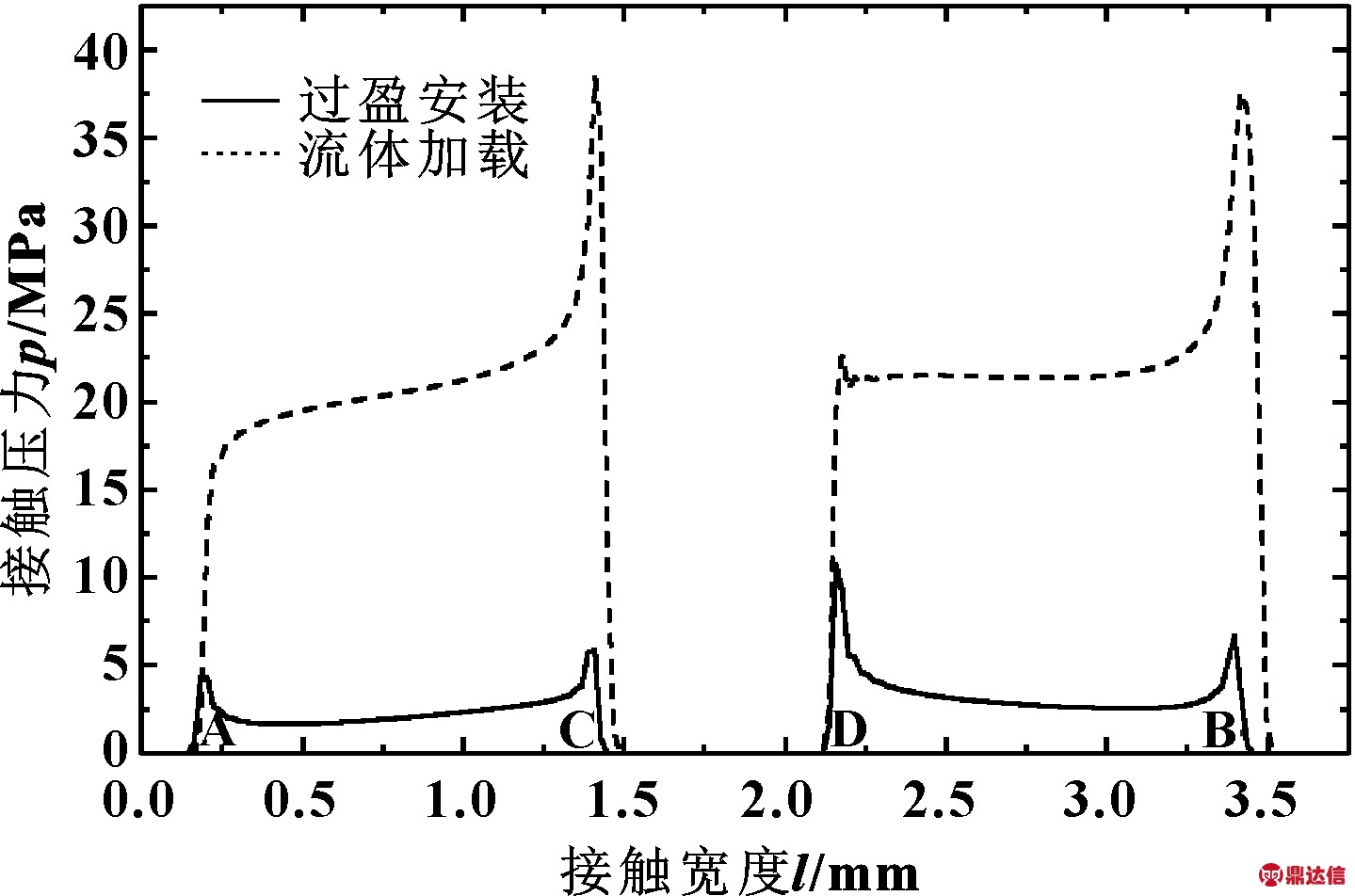
图8 过盈安装和流体加载时单槽密封圈接触压力分布对比
Fig 8 Comparison of contact pressure distribution of single groove combined seal after interference installation and fluid loading
由图8可知,单槽密封圈接触面被油槽分为两段,接触压力曲线呈现形态相似的两段。过盈安装状态下,曲线出现4个峰值区域,除A区(流体侧)和B区(空气侧)外,曲线靠近油槽处(C区和D区)出现了2个较高的峰值,且D区峰值大于C区峰值;峰值间压力梯度也出现一定变化。流体加载后,密封面各结点接触压力大幅增加,两段接触压力曲线与平面密封圈相似,均呈现单峰值形态,其中C区和B区峰值压力接近40 MPa。
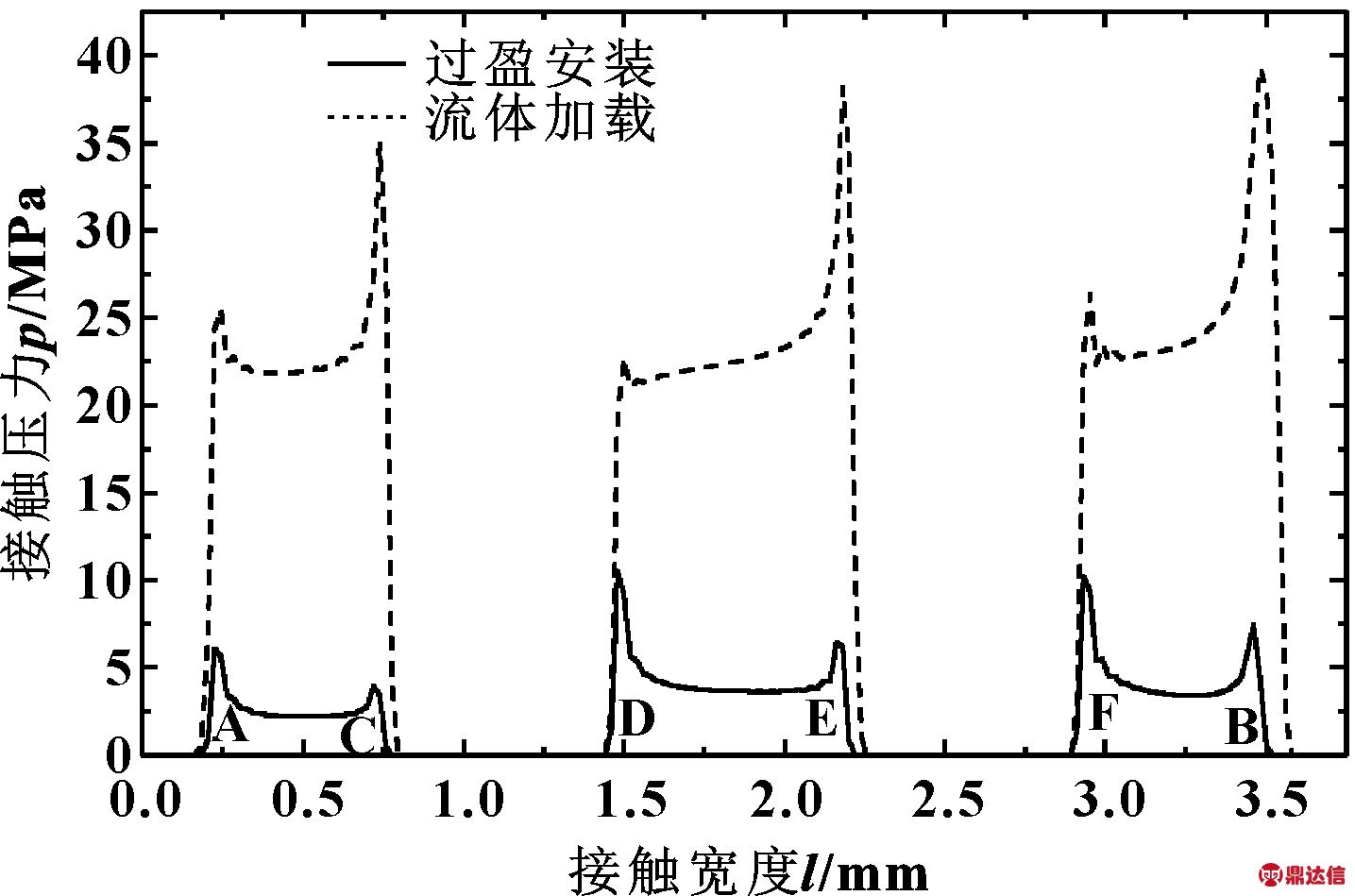
图9 过盈安装和流体加载时双槽密封圈接触压力分布对比
Fig 9 Comparison of contact pressure distribution of double groove combination seal after interference installation and fluid loading
由图9可知,双槽密封圈接触面被油槽分为三段,各段接触压力曲线形态相似。过盈安装状态下,曲线共有6个峰值区域,除A区(流体侧)和B区(空气侧)出现峰值外,曲线靠近油槽处(C区和D区、 E区和F区)均出现峰值,其中D区峰值大于C区峰值,F区峰值大于E区峰值。流体加载后,密封面各结点接触压力大幅增加,三段接触压力曲线均呈现双峰值形态。其中A区、D区和F区峰值较小,而C区、E区和B区峰值依次增大。
综合仿真结果,表面结构对于组合密封圈性能有较大影响。表面增加油槽后,组合密封圈动密封接触面被油槽分为多段接触面,从一定程度上提高了接触压力,且有利于在密封面上形成多个动压润滑区域,对于增强密封性能、改善润滑条件具有一定作用。但增加油槽后会增大方圈应力,特别是双槽密封圈应力增加较多。因此方圈进行表面结构加工时,应注意减少油槽边角应力集中的影响。同时,带槽密封圈使用时可适当增大密封间隙以降低摩擦损耗。在高压下使用时,还可选择较大尺寸的密封圈提高结构强度。
3.2 油槽尺寸参数对密封性能的影响
设定流体加载压力20 MPa,固定油槽长度L=0.75 mm,分别计算宽度W为0.32、0.52、0.72、0.92 mm 4种尺寸参数下密封性能的变化。计算得到的不同油槽宽度的组合密封圈完成过盈安装及流体加载后的应力分布如图10所示。
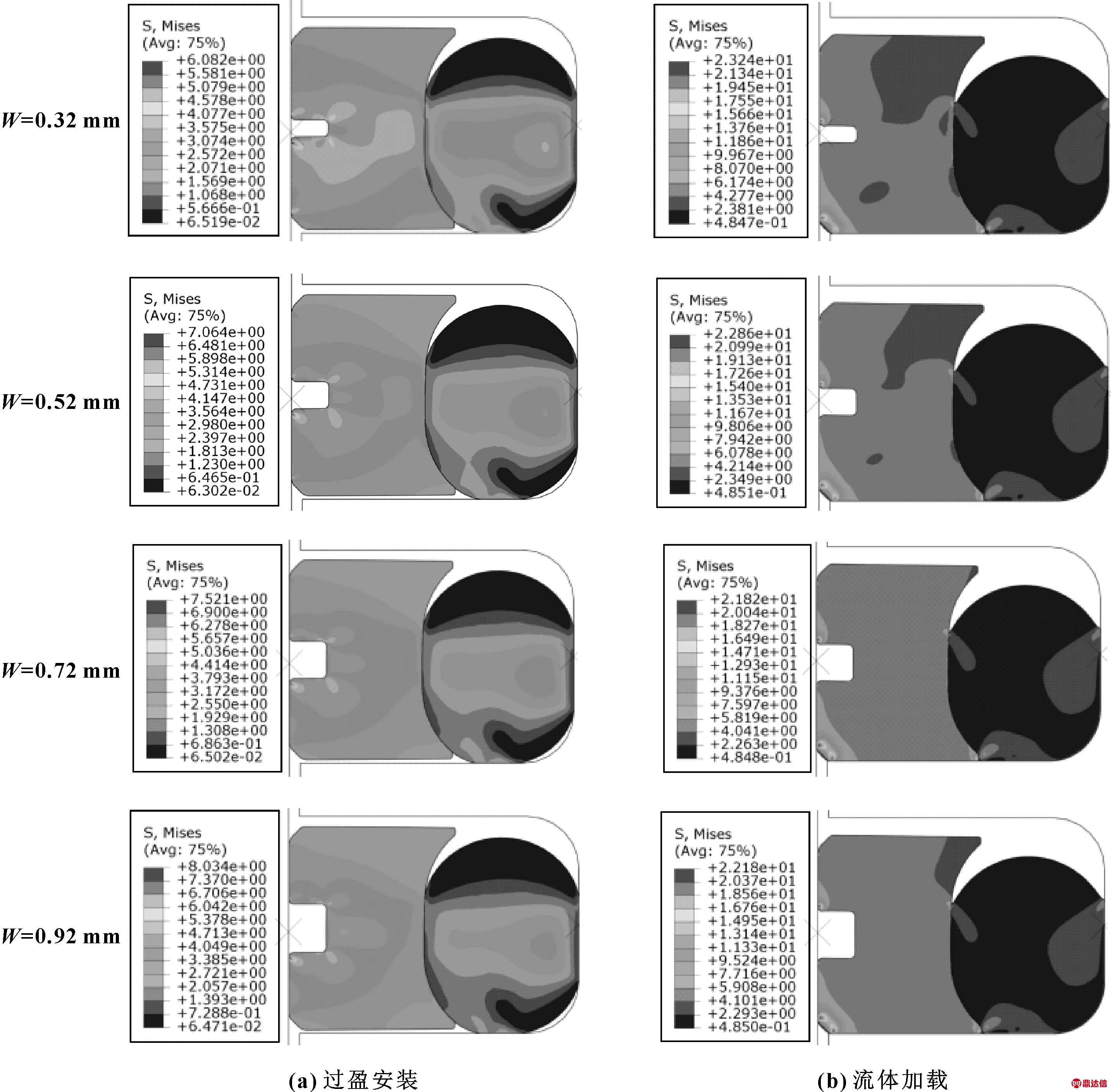
图10 过盈安装和流体加载时不同油槽宽度的组合密封圈应力分布
Fig 10 Stress distribution of combination seals with different oil groove widths after interference installation (a) and fluid loading (b)
由图10可知,过盈安装状态下,最大von Mises应力值随油槽宽度增加均有所增大,对比油槽宽度为0.32 mm的密封圈,其余密封圈最大von Mises应力值分别增加16.1%,23.7%,32.1%。流体加载后,组合密封圈应力值较未加载时均有大幅增加,但随着油槽宽度增加,最大von Mises应力值出现不同程度的减少。在过盈安装和流体加载状态下,不同油槽宽度的密封圈高应力分布区域基本一致。由图11可知,过盈安装和流体加载时O形圈高应力分布区域也基本一致,且随油槽宽度增加,最大von Mises应力值均有减少。
由上述仿真结果可知,油槽宽度变化对组合密封圈最大von Mises应力值影响较大,对应力分布影响较小。过盈安装状态下,方圈最大von Mises应力值随油槽宽度增加而增大;流体加载状态下,方圈最大von Mises应力值随宽度增加出现不同程度的减小;O形圈在过盈安装与流体加载状态下,最大Von Mises应力均随宽度增加而减少。
通过后处理创建路径,提取方圈与回转轴密封接触面上接触压力值,对不同油槽宽度的组合密封圈在过盈安装和流体加载后的接触压力进行对比,如图12和图13所示。图中坐标原点对应方圈在流体侧与回转轴接触起点。
由图12可知,过盈安装状态下,不同油槽宽度的密封圈接触压力曲线形态相似。密封接触长度随油槽宽度增加而减小。油槽两侧峰值呈现不同变化趋势,C区与D区接触压力峰值随油槽宽度增大而增大,而A区与B区峰值随油槽宽度变化较小,峰值间压力梯度随油槽宽度增加而增大。
由图13可知,流体加载后,密封面各结点接触压力大幅增加,不同油槽宽度的密封圈接触压力曲线形态相似。靠近空气侧接触压力曲线(DB段)除接触宽度不同外,曲线几乎重合,显示此段受油槽宽度变化影响较小。而靠近流体侧接触压力曲线(AC段),峰值压力随油槽宽度增加而减小。
综合仿真结果,油槽宽度变化对组合密封圈性能影响显著。过盈安装状态下,油槽宽度增加引起密封接触压力增加,峰值间压力梯度增大,方圈最大von Mises应力值也相应增大。流体加载状态下,油槽宽度变化主要对近流体侧接触压力峰值产生显著影响。随着油槽宽度增加,密封接触长度相应减小,方圈最大von Mises应力值也出现不同程度的减小。
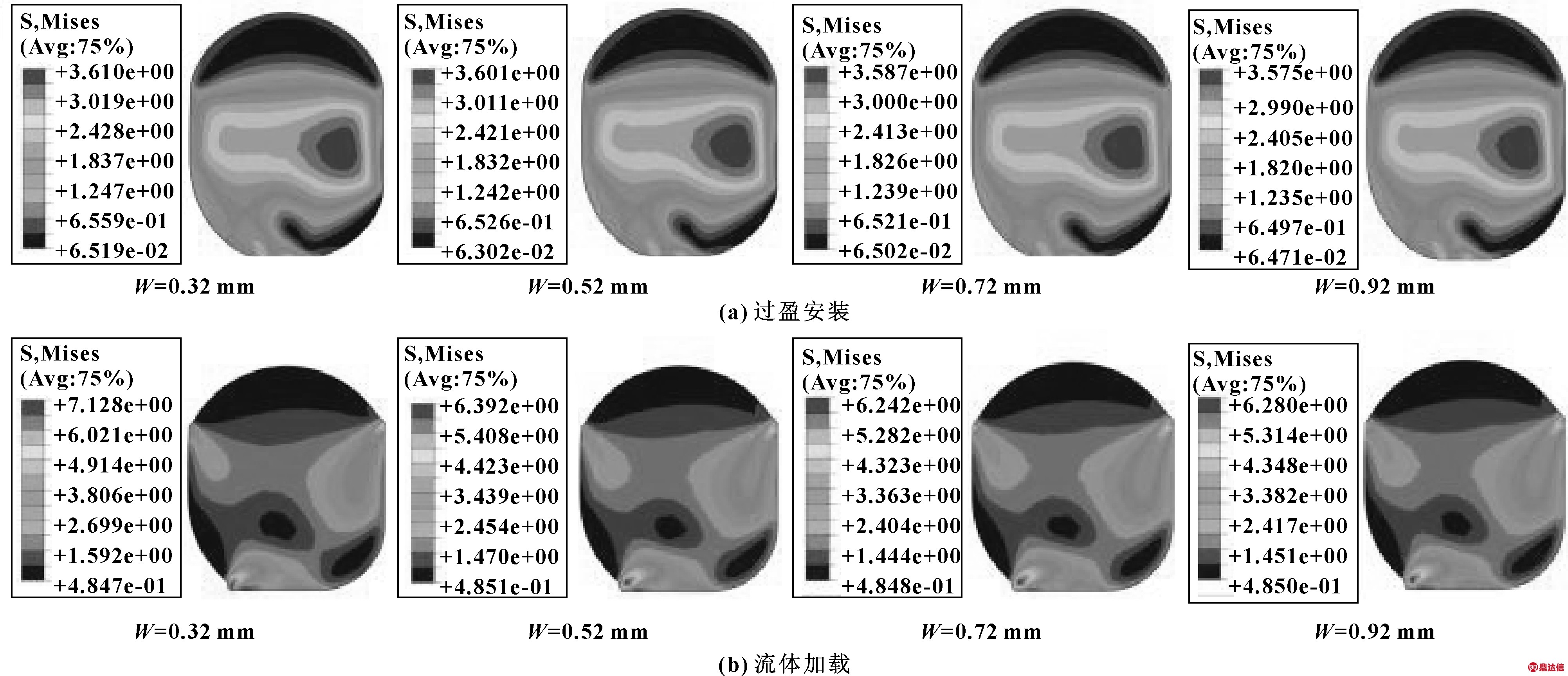
图11 过盈安装和流体加载时不同油槽宽度的组合密封圈O形圈应力分布
Fig 11 O-ring stress distribution of combination seals with different oil groove widths after interference installation (a) and fluid loading (b)
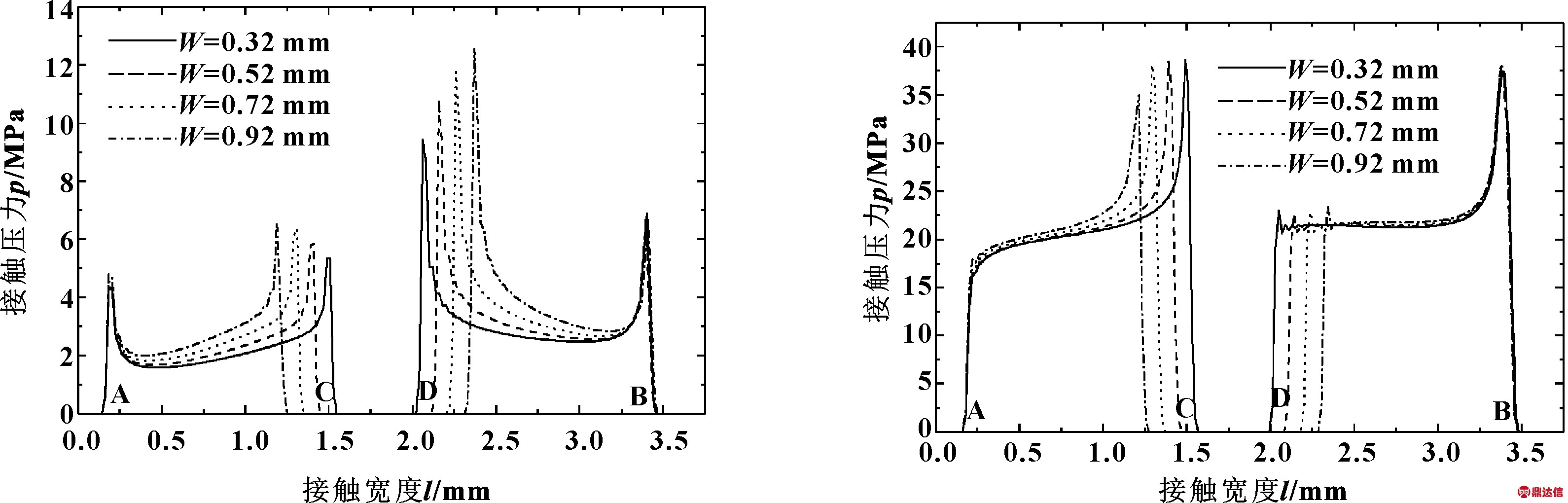
图12 不同油槽宽度密封圈过盈安装时接触压力分布对比 图13 不同油槽宽度密封圈流体加载时接触压力分布对比
Fig 12 Comparison of contact pressure distribution of Fig 13 Comparison of contact pressure distribution of sealing rings with different oil groove sealing rings with different oil groove widths during interference installation widths under fluid loading
4 结论
(1)表面结构对组合密封圈性能影响较大。在过盈安装与流体加载情况下,带槽密封圈最大von Mises应力都出现增长,但流体加载状态下应力增幅较过盈安装时小,高应力区域明显增多。带槽密封圈动密封接触面被油槽分为多段,接触压力均有不同程度的增大。
(2)油槽宽度变化对组合密封圈性能影响显著。油槽宽度增加使动密封面接触长度减少,密封接触压力和方圈最大von Mises应力值在不同状态下呈现不同变化趋势。组合密封圈应力分布区域受油槽宽度变化影响较小。
(3)方圈表面增加油槽有利于在动密封面上形成多个动压润滑区域,对增强密封性能、改善润滑条件具有一定作用。但增加油槽后会增大方圈应力,增加疲劳损坏风险,因此需注意采取措施改善应力集中的影响。带槽密封圈使用时可适当增大密封间隙以减少摩擦损耗,高压下使用时可选择较大尺寸的密封圈以增强可靠性。