摘要: 提出一种基于剪切效应的气动雾化喷嘴,对影响雾化质量的喷嘴结构参数进行试验研究.设计了3种气流孔径分别为8.0,9.0,10.0 mm的喷嘴,以自来水为工质,采用激光粒度分析仪和激光多普勒测速仪对不同喷嘴的雾化性能进行测量;描述气流孔径和气体流量对雾化微粒直径与速度分布的影响,量化并分析雾化微粒直径与速度之间的关系.结果表明:在同一气体流量条件下,采用气流孔径为10.0 mm的喷嘴所获得的雾化微粒速度最大、直径最小.随着气体流量增大,雾化微粒的速度增大,直径减小.随着距离喷嘴出口的轴向距离增大,雾化微粒直径先减小后增大,速度先增加后下降.对于气流孔径为10.0 mm的喷嘴,在距离喷嘴出口的轴向距离50.0 mm断面上,雾化微粒速度呈现双峰分布,在喷嘴轴心线附近出现谷值;在距喷嘴出口的轴向距离为200.0 mm的断面上,雾化微粒的速度在喷嘴轴线位置达到最大值.
关键词: 气动雾化喷嘴;剪切效应;微粒直径;微粒速度
雾化技术被广泛应用于燃油喷雾、农业病虫害防治、除尘等流程[1-3].传统的单相和两相喷嘴通常都伴随着高压和高能耗.若在低压条件下实现较小的雾化微粒直径,改进喷嘴结构是一个重要的途径[4].气动雾化喷嘴借助气体的能量将连续的液体打碎,通过高速气流冲击、气流剪切低速流动液体而实现雾滴破碎[5].该类喷嘴结构简单且具有良好的雾化特性.
雾化质量由雾化微粒直径、尺寸分布、雾化角、雾化微粒速度等特征参数来表征;激光粒度分析仪及激光多普测速仪(LDV)的应用促进了对雾化微粒直径、速度和分布规律的认识.李淑江等[6]通过试验研究了两相喷嘴喷雾特性随液体压力、气体压力、气液比、气相通道斜度等参数的变化规律,发现气液比相比于其他雾化参数对雾化微粒直径的影响更为明显.GONG等[7]探讨了不同工况条件下的雾滴破碎机理.林鸿亮等[8]和黄垂浪等[9]通过试验和数值模拟研究了喷嘴的结构参数对雾化微粒速度的影响.雾化效果受到气相压力、液相压力、喷嘴内部结构、进气孔径、进水孔径等参数的影响.SANGHOON等[10]通过试验研究了多孔喷嘴的喷雾特性,并与单孔喷嘴的喷雾特性进行了对比,发现多孔喷嘴的雾化微粒平均直径比单孔喷嘴的小,且多孔喷嘴能够加速喷雾过程.MLKVIK等[11]利用激光多普勒测速仪研究了喷嘴结构对雾化微粒速度的影响.
以往对于雾化喷嘴的研究主要集中于气液比、气液压力等运行参数对雾化特性的影响,并且在雾化过程中需要2个动力源分别驱动气体与液体,能耗较高.文中提出一种基于剪切效应的气动雾化喷嘴,采用风机将气体增压后通过多个气流孔喷入混合腔流动,通过试验探究气流孔径和气体流量对喷嘴的雾化微粒直径和速度的影响,分析喷嘴的雾化机理,为该类喷嘴结构的进一步优化提供参考.
1 喷嘴结构及雾化过程机理
1.1 喷嘴结构
为研究气流孔径d及气体流量qa对雾化微粒直径及速度特性的影响,设计如图1所示的喷嘴结构.该喷嘴主要由内径44.0 mm的圆柱套筒和外径30.0 mm的内套组成,套筒与内套之间通过螺栓连接并做密封处理,喷嘴内套如图2所示.套筒中部开有小孔用于通过液体管(内径3.0 mm)连通至内套中心孔;内套开设4个气流孔,气流孔的轴线处于同一平面,形成向心结构,可形成旋转气流.液体管内径D与内套横截面内径之比在0.1~0.4,如此则可以形成较大尺寸的气流束,且降低液流与壁面的碰撞概率,达到更佳的雾化效果.根据前期试验,发现气流孔径过小所产生的负压无法自动将液体吸入负压腔,且通过外接动力将液体压入负压腔后雾化发散严重,故文中将气流孔径分别设定为8.0,9.0和10.0 mm.
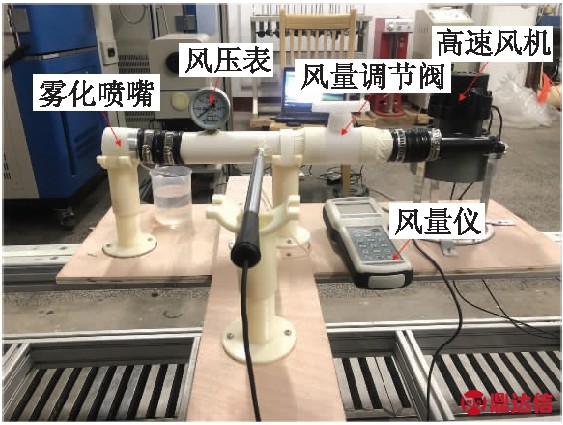
图1 剪切效应驱动的气动雾化喷嘴结构
Fig.1 Structure of pneumatic atomizing nozzle driven by shear effect
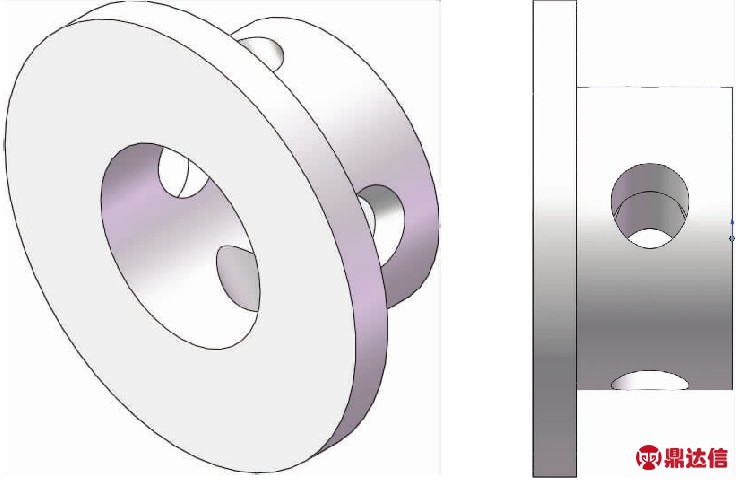
图2 剪切效应驱动的气动雾化喷嘴内套
Fig.2 Inner sleeve of pneumatic atomizing nozzle driven by shear effect
1.2 雾化过程机理
喷嘴工作时,由风机驱动气体从气流孔进入喷嘴,通过4个气流孔形成旋转气流,在4股气流交汇处形成一个负压腔.当气液两相流体从负压腔口喷出时,由于气体速度很高,而液体的流速不高,因此两相流间的相对速度较高,摩擦力大,气流对液体产生强烈的剪切与撕裂作用,液体进一步雾化,且由于螺旋作用,液体被雾化的同时向四周扩散,增大雾化微粒覆盖面积.试验过程中通过注水保持容器内的液面高度不变.
2 雾化微粒直径试验
2.1 试验装置
设计如图3所示的试验装置,研究不同气流孔径喷嘴的雾化特性.该装置主要由喷嘴雾化装置(见图4)、三坐标移动装置和激光粒度分析仪组成.其中喷嘴雾化装置主要由风机、气体流量调节阀、风速仪(用于气体流量间接测量)、压力表、雾化喷嘴及其支架组成.
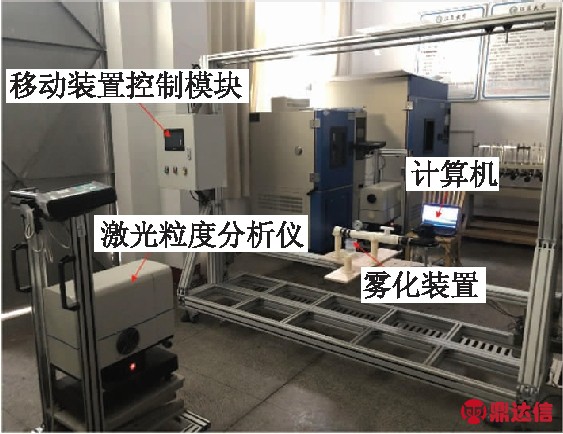
图3 微粒直径测量试验台
Fig.3 Experimental rig for droplet diameter measurement
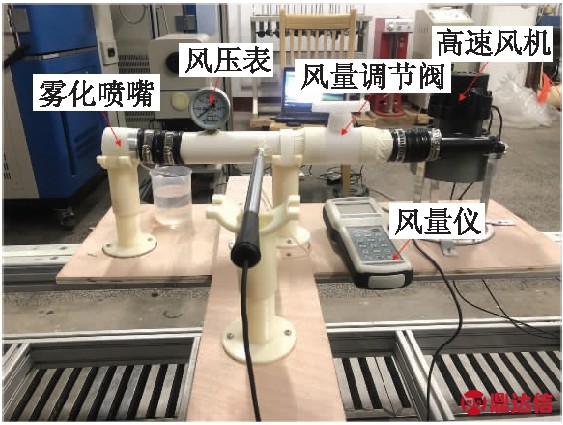
图4 雾化装置
Fig.4 Atomization device
所用装置主要技术参数如下:
1) 激光粒度分析仪.型号Winner 318B;测量粒径范围为4.6~711.0 μm;误差<±3%;测量区长度为1~10 m.
2) 风机.电压为24 V;最大转速为22 000 r/min;最大风量为151.6 m3/h;最大风压为27.05 kPa;风量与风压的关系为y≈-1.3x+55.
3) 风速仪.型号DO9847;传感器探头型号AP471S1;测量范围为0.1~40.0 m/s;精度为±0.02 m/s;使用温度为-25.0~80 ℃.
2.2 试验方案
使用激光粒度分析仪测试3种不同气流孔径的喷嘴对应的雾化微粒直径,并沿喷嘴轴向位置分析雾化微粒直径的分布.根据传统喷嘴的粒径测试结果[12],分别选取距离喷嘴50.0,100.0,200.0,300.0,400.0和500.0 mm的6个位置测量雾化微粒直径,试验工况如表1所示.
表1 雾化试验工况
Tab.1 Conditions of atomization experiments
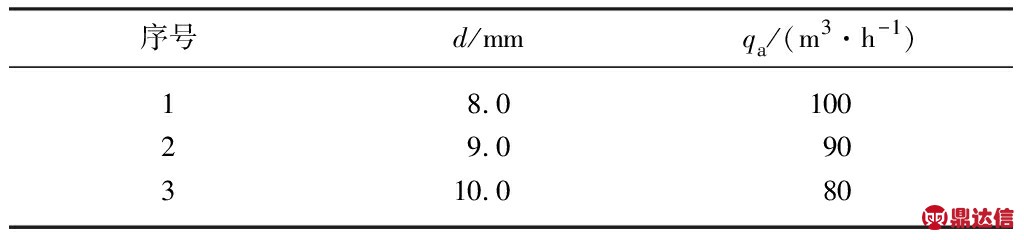
在测量过程中:① 将喷嘴雾化装置固定于试验台上并校准三坐标原点(x轴垂直于喷嘴轴线方向竖直向上;z轴为喷嘴轴线方向);② 打开激光粒度分析仪,校准激光焦点,运行数据处理软件;③ 启动喷雾装置至其运行稳定;④ 通过三坐标装置记录不同位置的喷嘴直径;⑤ 调节气体流量、更换喷嘴进行不同工况试验.为获得更精确的数据结果,对每个工况进行3次测量,取其平均值.
采用激光粒度分析仪可以得出雾化微粒平均直径的概率密度函数和概率密度分布函数.其工作原理是由激光发射器发射激光穿过雾化区域,激光接收器接收并折射到分析光谱上,再利用激光粒度分析仪得到描述微粒平均直径的常用参数索太尔平均直径D32,其为雾化微粒流场内全部微粒的体积和总表面积的比值,计算公式为
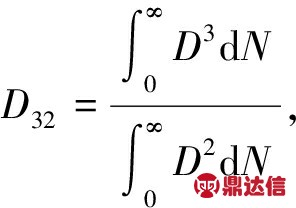
(1)
式中:D为雾化微粒的直径;N为雾化微粒数.
由式(1)可以看出,D32越小,相同体积的微粒具有的表面积越大,即雾化质量越高.
2.3 试验结果与分析
通过试验得到的雾化微粒直径在15.0~70.0 μm,试验过程中通过雾化形成的液滴迅速弥散,未出现大尺寸液滴.雾化微粒直径及所占百分比P如图5所示.
通过数据分析,发现喷嘴的气流孔径与气体流量均对雾化微粒直径有显著影响.雾化微粒直径随距喷嘴轴向距离s的变化如图6所示.
首先对3种不同气流孔径的喷嘴进行对比试验,保证试验条件一致、气体流量调节阀开度一致.图6a为雾化微粒直径随气流孔径的变化.从图中可以看出,气流孔径为10.0 mm的喷嘴获得的雾化微粒直径最小,而气流孔径为8.0 mm的喷嘴,其对应的雾化微粒直径最大.文中对3种气流孔径的喷嘴进行微粒直径试验,且气流孔的轴线与内套横截面平行,该类喷嘴性能与气流孔数、气流孔的轴线与内套横截面之间夹角相关.
选取气流孔径为10.0 mm的喷嘴开展进一步试验,结果如图6b所示.从图中可以看出,雾化微粒直径随气体流量的增大而减小,由于气体流量增大,液滴具有较大的动量,有利于撞击破碎,故雾化微粒直径减小.
随着距喷嘴的轴向距离逐渐增大,雾化微粒的直径呈现先减小、后增大、再减小的整体变化趋势,D32最小可达到17.0 μm.由于靠近喷嘴附近为负压区,液体被吸入负压区还未充分雾化,雾化微粒直径较大,随着距喷嘴的轴向距离增大,雾化微粒得以充分破碎,雾化微粒直径减小,而后,雾化微粒出现部分积聚现象,微粒直径逐步增大,达到一定轴向距离后,气体射流开始发散,再一次撞击微粒,使雾化微粒直径减小,但由于此时雾化能量不足,雾化微粒直径减小不明显.
为保证试验结果的可靠性,分别对气流孔径为9.0 mm和8.0 mm的喷嘴进行重复性试验,得到与孔径10.0 mm喷嘴一致的变化规律,图6c为孔径8.0 mm喷嘴对应的雾化微粒直径变化规律.
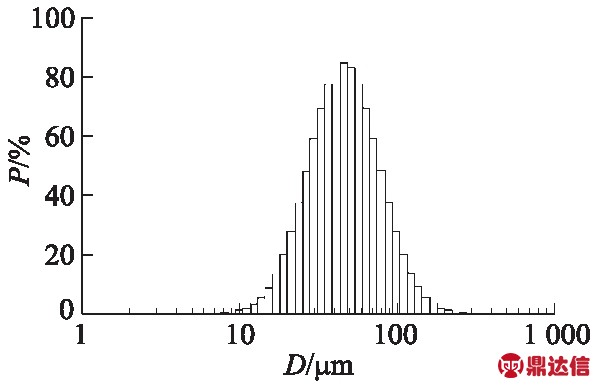
图5 微粒直径分布
Fig.5 Distribution of droplet diameters
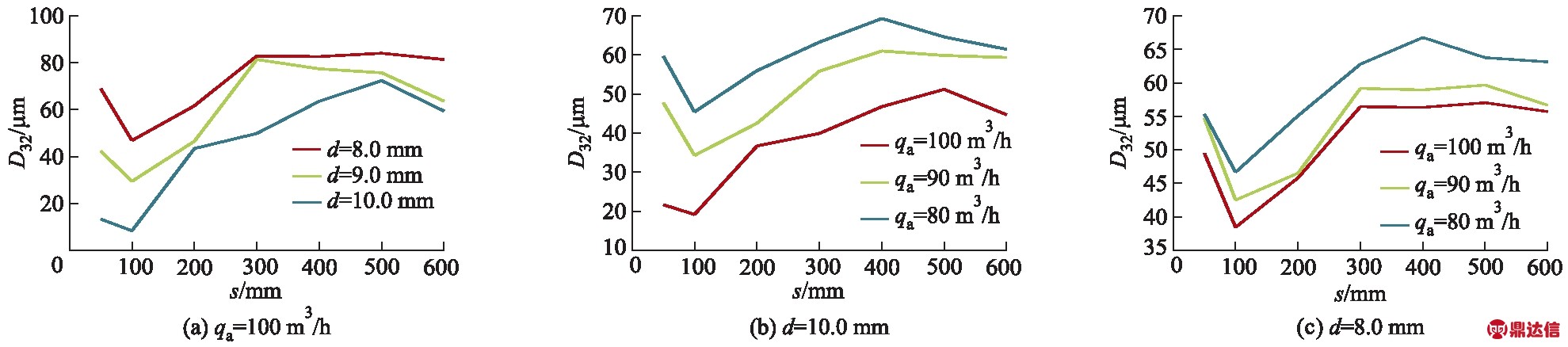
图6 雾化微粒直径的变化
Fig.6 Variations of droplet diameter
3 雾化微粒速度试验
3.1 试验装置
采用如图7所示的试验装置来研究不同气流孔径喷嘴获得的雾化微粒速度.
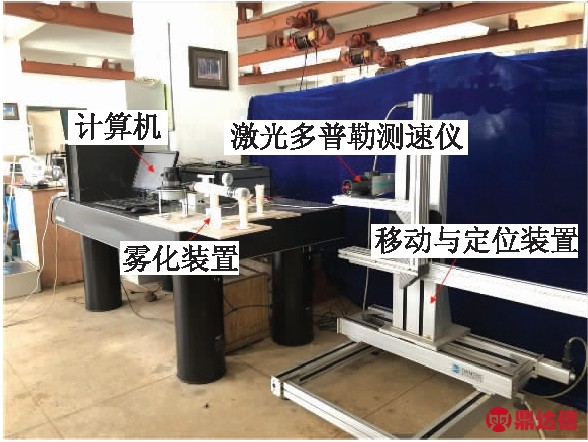
图7 微粒速度测量试验台
Fig.7 Experimental rig for droplet velocity measurement
该装置主要由喷嘴雾化装置、激光多普勒测速仪和三坐标移动装置组成.激光多普勒测速仪由激光器、光学系统、信号处理系统等部分组成,具有线性特性与非接触测量的优点,并且精度高、动态响应快,可实现三维流动的精准测量,并可以获得复杂流动结构的定量信息.
3.2 试验方案
分别选取距喷嘴轴向距离为50.0,80.0,100.0,120.0,200.0,300.0,400.0,500.0和600.0 mm的9个位置进行雾化微粒速度测量.由于雾化微粒直径试验中,在距喷嘴轴向距离100.0 mm处的雾化微粒直径最小,故增加距喷嘴轴向距离80.0 mm及120.0 mm处的速度测量.
借助激光多普勒测速仪得到雾化微粒径向和轴向的速度.由于离心作用,雾化微粒从喷嘴出口喷出呈螺旋状,径向速度的规律性较差,故本试验针对轴向速度分量w进行研究.
3.3 试验结果与分析
通过试验得到雾化微粒速度为0~16.0 m/s.根据雾化微粒直径的分布趋势,首先在同一气体流量条件下对3种不同喷嘴进行雾化微粒速度测量,结果如图8a所示.气流孔径为10.0 mm的喷嘴所产生的雾化微粒的速度最高,而气流孔径为8.0 mm的喷嘴对应的雾化微粒速度最低.
选择孔径10.0 mm的喷嘴进行进一步试验,结果如图8b所示.从图中可以看出,雾化微粒速度随距喷嘴轴向距离的增大先升高后降低.由于雾化微粒刚从喷嘴喷出时未脱离负压区,速度较低,通过负压区后速度达到最高,而后随轴向距离变大速度降低.对比气体流量变化对微粒速度的影响发现,当气体流量大时,雾化微粒速度高.在距喷嘴轴向距离500.0 mm处,微粒速度仍能达到10 m/s,而超过500.0 mm后,LDV系统的采样信号很弱,信号有效性差,说明雾滴扩散严重.
图8c为气流孔径为10.0 mm的喷嘴在距喷嘴轴向距离50.0 mm处对应的雾化微粒沿径向r的径向速度分量u的分布.由于测量存在偏差,试验结果准确性受到一定影响,但从图中雾化微粒速度的整体变化可以看出,在距喷嘴轴向距离50.0 mm处,由于雾化微粒刚从喷嘴出口喷出,形成的螺旋状喷雾未及时汇集,所以微粒速度呈现中间速度较低、沿径向±50.0 mm处增至最高、而后沿径向降低的趋势.
图8d为气流孔径为10.0 mm的喷嘴在距喷嘴轴向距离200.0 mm处的雾化微粒沿径向r的径向速度分量u的变化规律.速度在中部位置最高,从中心至四周先下降而后小幅度升高再下降.这是由于通过风机产生的螺旋状喷雾在距离喷嘴轴向距离200.0 mm处已经向喷嘴的中心线聚拢.
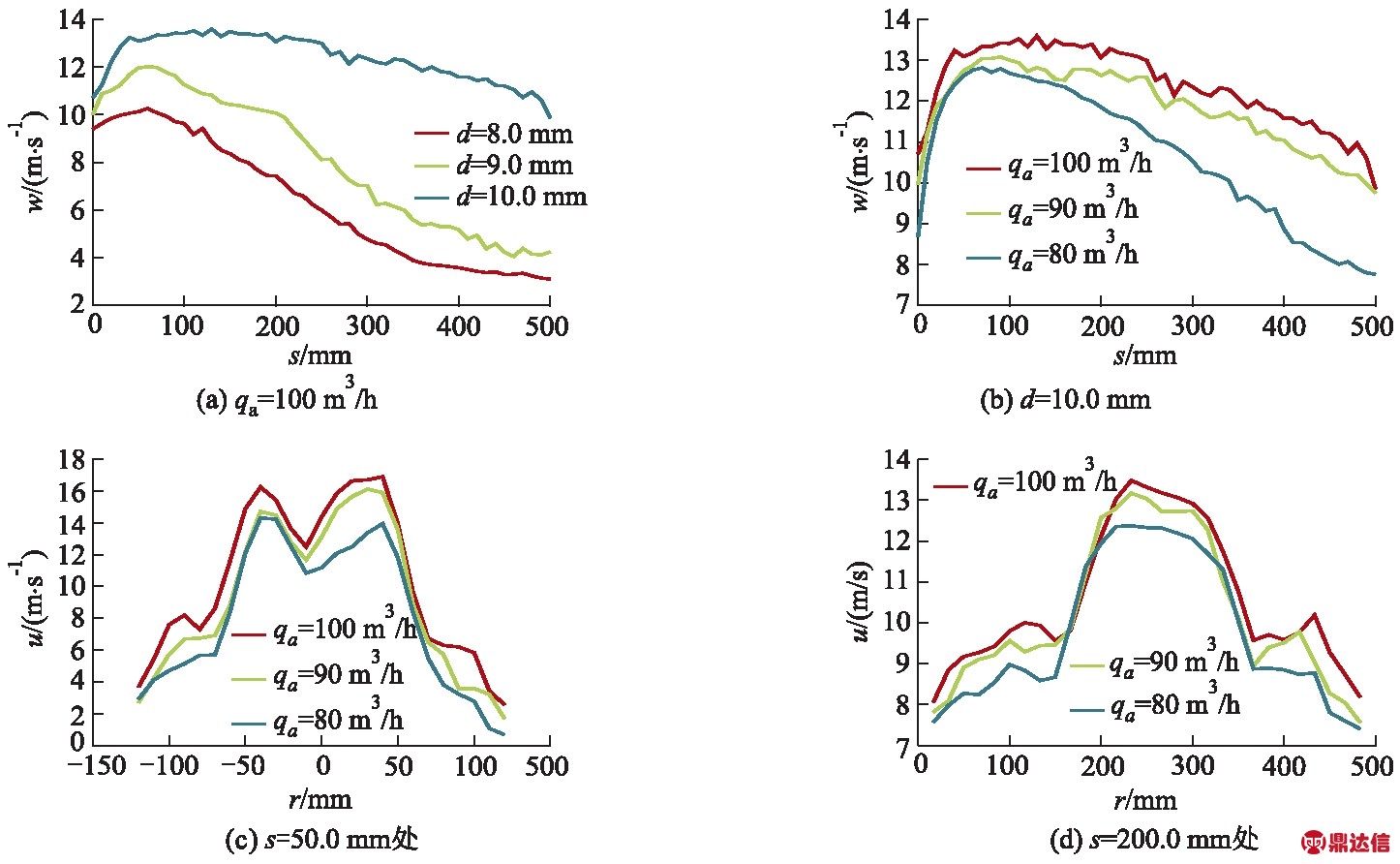
图8 雾化微粒速度的变化
Fig.8 Variations of droplet velocity
4 结 论
1) 喷嘴的气流孔径影响雾化质量.在所研究的3种气流孔径的喷嘴中,气流孔径为10.0 mm的喷嘴的雾化微粒速度最高,直径最小.
2) 对于单个喷嘴,在同一气体流量条件下,随着距喷嘴轴向距离增大,雾化微粒直径先减小、后增大、再减小;雾化微粒速度先升高后下降,且雾化微粒速度最高处的雾化微粒直径最小;在气体流量较大工况下,雾化微粒速度较高,同时微粒直径较小.
3) 在距离喷嘴轴向距离为50.0 mm和200.0 mm处,雾化微粒速度沿径向的分布特征不同.在50.0 mm处,靠近喷嘴中心线的速度较低,而后沿径向先增加后下降;在200.0 mm处,雾化微粒速度在靠近喷嘴中心线处出现最大值,而后沿径向下降.