摘要:由于缺少发动机噪声的覆盖,新能源汽车空调鼓风机产生的气动噪声成为影响乘车舒适性的重要噪声源,主要针对某新能源汽车空调鼓风机系统进行气动噪声特性分析和优化,以适应更加严苛的噪声控制要求。采用ANSYS数值模拟软件和半消声实验室,通过对原始叶轮模型流场和声场的研究分析复杂的轮毂、叶片、气流和结构部件周期性相互作用产生的气动噪声特性,并开展轮毂型线和叶顶弧度对气动噪声的影响研究,其中轮毂型线模型最大可以分别降低43阶次叶频噪声和总声压级5.0 dB和4.2 dB,叶顶弧度模型最大可以分别降低43阶次叶频噪声和总声压级4.0 dB和2.7 dB。研究结果对优化新能源汽车空调鼓风机在受限空间内气动噪声控制具有一定的参考意义。
关键词:声学;汽车空调鼓风机;叶片;气动噪声;降噪优化
由于新能源汽车在日常行驶时缺少内燃机噪声的掩盖,空调系统的噪声将成为影响乘员舒适性的主要噪声源,其中鼓风机中含有的叶轮等旋转部件是气动噪声的主要噪声源。为了满足更严苛的新能源汽车NVH(Noise,vibration and harshness)标准,应对此类空调鼓风机进行详细的气动噪声特性研究。
目前大部分学者均通过实验或数值模拟方法对气动噪声的产生机理进行研究。Tare 等[1]研究分析了气动噪声与湍动能系数的关系,并提出了通过调节叶片间距降噪的方法。赵立杰等[2]认为风扇叶尖间隙是产生气动涡流噪声的主要来源。朱正权等[3]基于大涡模拟及FW-H(Ffowcs Williams-Hawkings)方程进行某汽车空调调节系统离心风机流场及气动噪声仿真,认为离心风机的主要噪声源是叶轮的旋转噪声以及蜗舌和出口处的涡流和回流。在离心风机降噪方面,YANG 等[4]、李孟宇[5]选取了叶片出口角、蜗舌间隙、集热器倾角及转速作为变量对离心风扇进行结构优化,经改进后汽车空调系统峰值噪声明显降低。Woodward 等[6]、Shibata[7]在离心压气机上采用后掠式扭曲叶片,同时使叶片在出风口处适度前倾,降低静子叶片前缘尾迹强度,减少流动分离,使附面层和分界层所形成的旋涡迅速解体,从而降低气动噪声。Younsi 等[8]通过设置较小的叶轮出口半径减小了施加在旋转叶片上的轴转矩,使得叶轮靠近蜗舌区域呈现出更均匀的流场,以降低噪声。Moreau 等[9]和Heo[10]等从优化叶片锯齿形和S 型尾缘角度减小漩涡的脱落幅度和尾缘处的压力脉动。Yamada 等[11]分析跨音速离心压气机的叶片数目对叶顶间隙流场的影响并对其进行优化。刘晓峰等[12]研究某大涵道比的民用发动机压气机轴流风扇,认为轮毂的下凹位置和深度对风扇的流场和效率有很大的影响。
综上所述,目前关于风机叶轮气动噪声方面的研究多集中于气动噪声的影响因素分析,以及通过对叶片安装角、叶片结构、叶轮轮径比、叶片分布、蜗舌等参数的优化来降低气动噪声方面。对于离心风机中轮毂结构对气动噪声特性的影响研究成果较少,尤其是对于应用于新能源汽车的空调鼓风机,由于其轮毂结构受限于电机安装位置和叶片高度程度较大,轮毂型线对鼓风机的流场和声场具有较大的影响,这对于为新能源汽车气动噪声的降低提出了更高的设计要求。其次汽车用空调鼓风机叶轮被安置于受限空间内,其气动力不仅增加了叶轮的辐射噪声,还影响到附近的结构件,周期性的结构部件振动也对气动噪声的辐射做出了较大的贡献,因此在对新能源汽车空调鼓风机气动噪声的研究中需要进一步对其轮毂结构以及气动力作用部件进行噪声特性分析,使其满足乘坐舒适性方面的更高要求。
1 实验与数值计算方法
1.1 研究对象
实验所用的空调鼓风机系统如图1 所示,右侧上部为进风口,在其下方安置有空滤、蜗壳、叶轮等结构,最下方为电机及其法兰盘,左侧安置有分配箱。空滤主要的作用是对从进风口进入的新鲜空气进行过滤,提高车内的空气质量。分配箱是利用内部流道和风门来控制和分配从蜗壳出来的气流,从而实现汽车内全部空间的风力调控。本文主要针对如图1(b)所示的右侧进风箱开展研究。

图1 空调鼓风机系统示意图
1.2 实验平台
空调鼓风机系统噪声测定实验在半消声实验室内进行。实验室的声学环境符合GB/T6882-2016[13]要求,经测试,实验室背景噪声为16 dB,远低于运行工况噪声值,无需进行声压级修正。试验设备包括:DATaRec-4 数据采集卡、Artemis 采集分析系统、GRAS 麦克风和测试用笔记本,具体型号、参数和数量如表1所示。
表1 主要试验设备型号及参数

试验测试平台如图2 所示,测试标准满足JB/T 4330-1999[14]。在空调鼓风机前方左右两侧各布置一个麦克风,如图2所示,左侧麦克风为POS1,右侧麦克风为POS2,均戴有风罩并避开气流对其冲击。汽车空调鼓风机在额定工况工作,即转速为3 500 r/min。
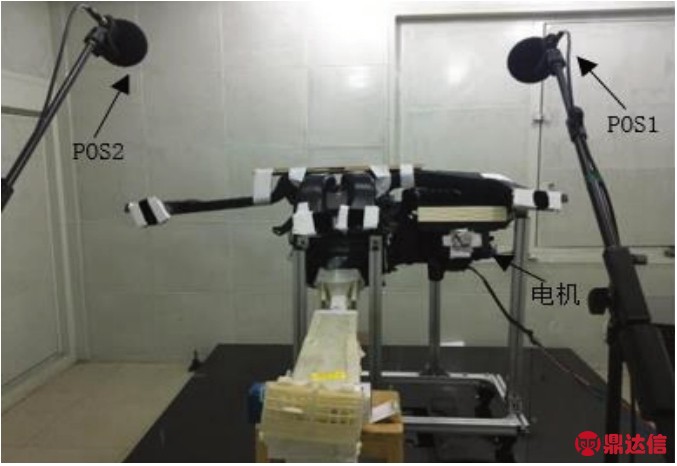
图2 测试平台及麦克风安装位置
1.3 数值计算方法
在进行实际流场仿真计算时将对流场、声场影响不大的电机和电机法兰盘部分进行简化,优化后的三维计算模型如图3所示,其主要几何参数如表2所示。
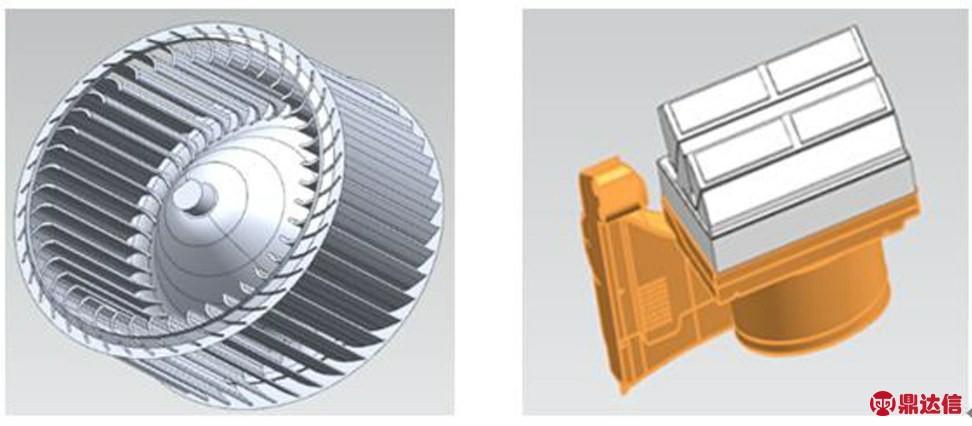
图3 鼓风机计算三维模型
表2 汽车空调鼓风机参数
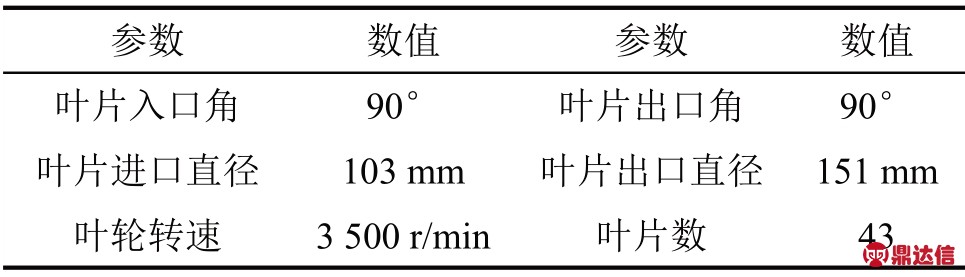
将叶轮组件作为旋转区域,使其按照给定方向作转速运动;将蜗壳、空滤、进风口等流场区域作为静止区域,使其在仿真时处静止状态。两区域间相对运动及数据传递分别通过滑移网格和Fluent软件中的interface 命令完成。经网格无关性验证,确定后续计算时叶轮区域网格按2 mm进行划分,静止区域网格按4 mm进行划分,网格总数为879万[15]。
稳态计算时选用RNG k-ε 湍流模型,利用SIMPLE 算法进行求解,将计算域入口设定为速度入口,将计算域出口设为回流;旋转区域运动方式设定为frame Motion,转速选取为额定工况时的3 500 r/min;将厚度为34 mm的空滤段设定为多孔介质层Porous Zone,孔隙率为0.8。
将瞬态计算时旋转区域运动方式设置为Mesh Motion,开启FW-H方程,并选择旋转和静止区域组件作为输出声源信息的区域,用于半自由声场计算。瞬态计算时间的选取主要取决于关注的频率成分以及计算的收敛性。根据转速可知空调鼓风机基频为58.3 Hz,该型鼓风机叶轮为43 片,气动噪声主要分布在前43阶,第43阶次叶频频率为2 506.9 Hz,因此本文关注的最大频率fmax =5 000 Hz。根据采样定理[16]设定对应的时间步长为Δt=3×10-5 s。经试算确认用4 个旋转周期保证湍流流场的充分发展,最终迭代步数为N=3 000。
1.4 数值计算结果与实验对比验证
为验证仿真可靠性,在仿真计算中参照实验位置设置监测点位置,通过FFT 与A 计权处理可得到两监测点的噪声频域图,将仿真结果与实验结果进行比对,如图4 所示。该汽车空调鼓风机的主要噪声为叶轮自身旋转形成的离散噪声和宽频噪声,实测与仿真结果均在2 500 Hz 附近出现峰值,且仿真结果所得的POS 1和POS 2 位置的43阶次叶频噪声分别为43.5 dB 和45.6 dB,与实验值43.6 dB 和46.9 dB 较为接近。但仿真结果中低于700 Hz 的低频噪声部分与试验相比有一定误差,这一方面是由于存在低频的机械噪声,另一方面是由于鼓风机采用的电机为2 极、12 齿槽结构,额定转速为3 500 r/min,故700 Hz处峰值是电机电磁噪声引起,仿真时并未考虑鼓风机机械部分产生的机械噪声与电机的电磁噪声,而这两种噪声主要集中于中低频段。

图4 仿真与实验噪声频谱图对比
评估空调鼓风机的总声压级时对总声压级进行A 计权,POS 1 测点实验值与仿真值分别为65.9 dB和60.8 dB,POS 2 测点对应数值为66.8 dB 和62.1 dB。仿真结果与试验存在5 dB 左右误差的原因主要在于:流场数值仿真计算中忽略了电磁噪声、机械噪声对整体声压级的影响,这主要体现在700 Hz及以下;半消声室各消声壁面及试验台对噪声存在折射、反射现象,对总声压级造成了一定的影响;建立仿真模型时对原模型进行了一定的简化,而实际上简化部分可能对噪声声压级产生一定的影响;由数值仿真计算所得的是基于自由声场的计算结果,而实际试验是在半自由声场中进行,因此计算结果与实际有部分差距。但综合来说,数值仿真计算具有可行性,计算结果具有可靠性。
2 原型鼓风机计算结果
图5 为汽车空调鼓风机叶轮及其截面(Z=0.05 m)声功率级分布图,发现叶轮轮毂与叶片顶部的声功率级明显高于其他部位,且靠近蜗舌位置的叶片声功率级要高于其他部分。图6所示的在叶片附近设置的流动压力脉动监测点频谱显示该空调鼓风机叶轮旋转的峰值压力为2 500 Hz 时的43 阶次叶频噪声。推测是作为导流器的轮毂及后续的叶片流道设置不合理促使叶片和气流产生强烈的周期性相互作用,形成了阶次噪声。
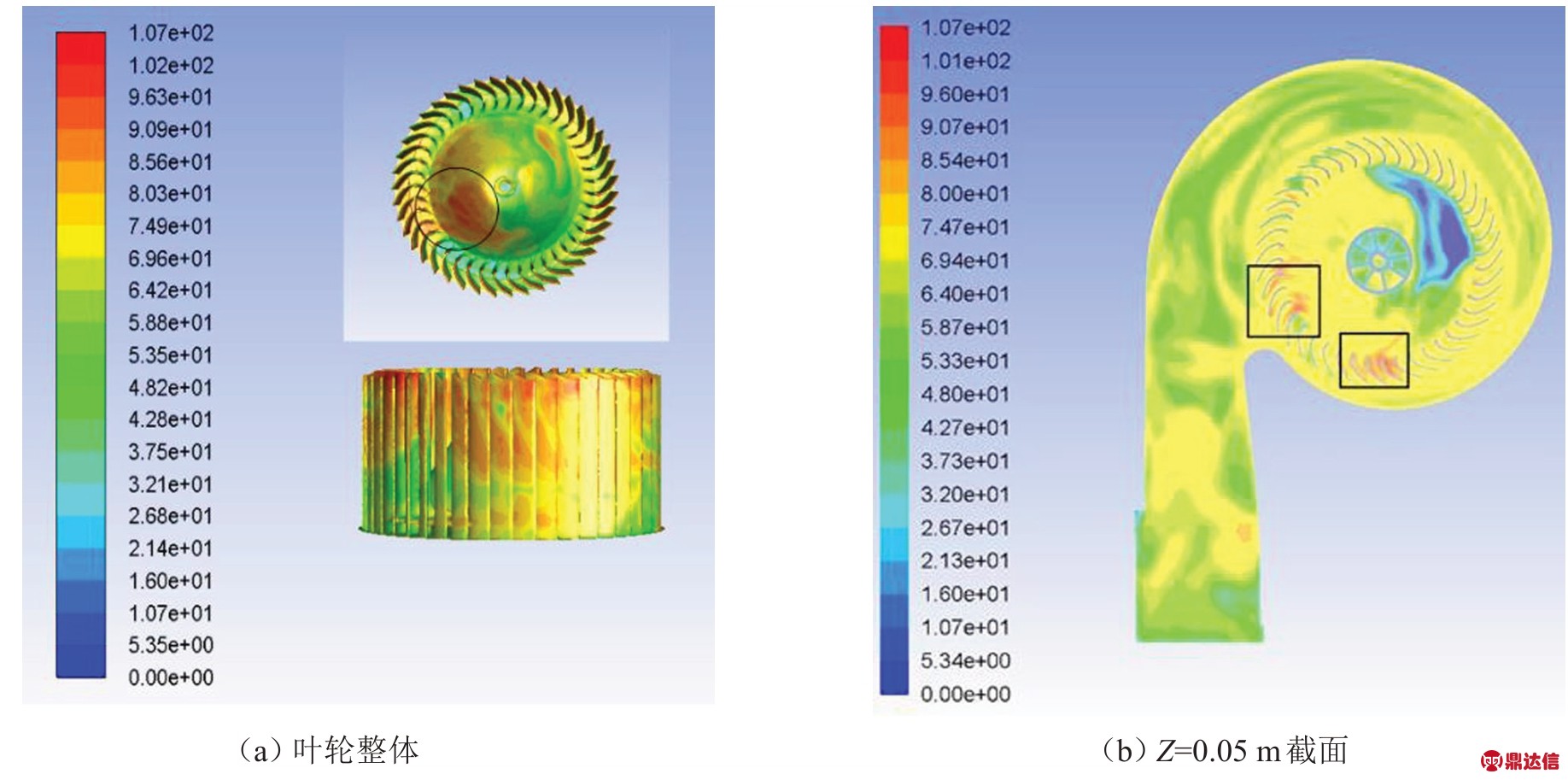
图5 叶轮声功率级分布
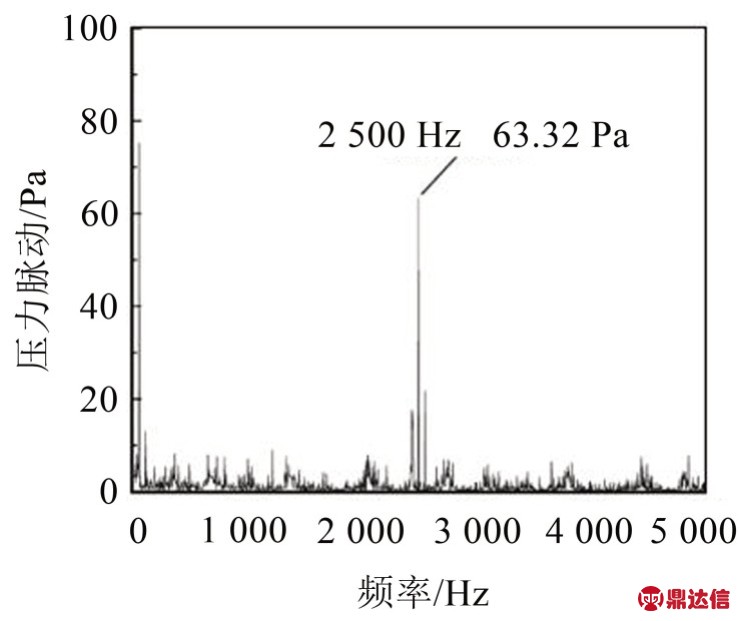
图6 叶片附近处压力脉动频谱图
图7 为鼓风机叶轮整体及截面(Z=0.05 m)的湍动能分布云图,可以看出叶片底部靠近轮毂处、叶片顶部、靠近蜗舌处的叶片的湍流运动较为强烈。
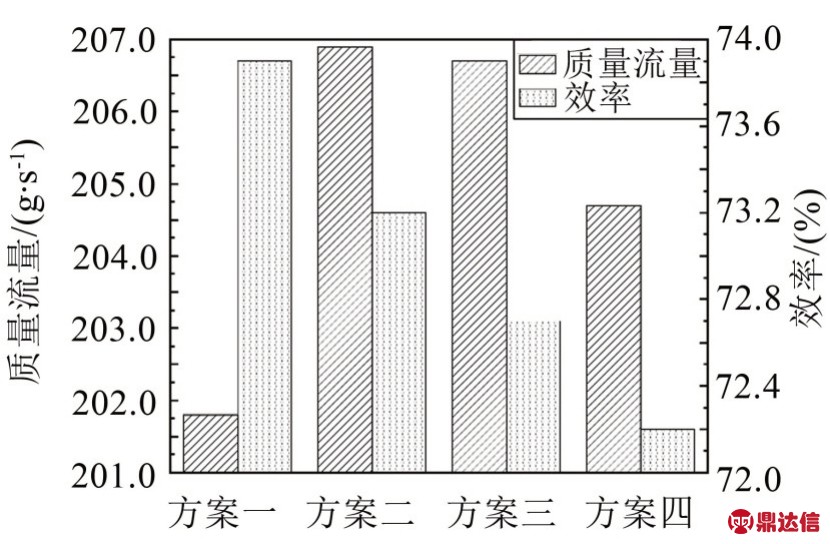
图7 叶轮湍流动能分布
鼓风机叶轮某截面的流动状况如图8 所示,可见在叶轮轮毂表面出现了明显的气体流动周向不均匀现象,低速区域回流明显,高速区域流速过大,如图8(b)所示。气流在导流器轮毂上从轴向流动转为径向流动过程中流动的不合理会导致叶片上气动载荷不均匀,截取声强较高的两叶片之间的气流矢量流动图8(c),通过观察发现在叶片气流入口处有低速回流现象,进气角和几何进口角不匹配导致部分能量耗损。靠近蜗舌处的叶片气流出口处流速较高,蜗舌处气流有局部回流至叶片流道内,见图8(e),周期性的气流对蜗舌处的打击以及涡流运动既增大了声功率又影响了运行效率。
此外在图8(d)所示流场中还发现叶轮入口处的空滤平面附近和叶片顶部也具分布有较高的湍动能,叶片的顶部旋转气流流动对其产生了强烈的气流激振作用。由综合分析可知流场的不合理分布所导致的轮毂、叶片和气流周期性相互作用是产生阶次噪声的主要原因之一。
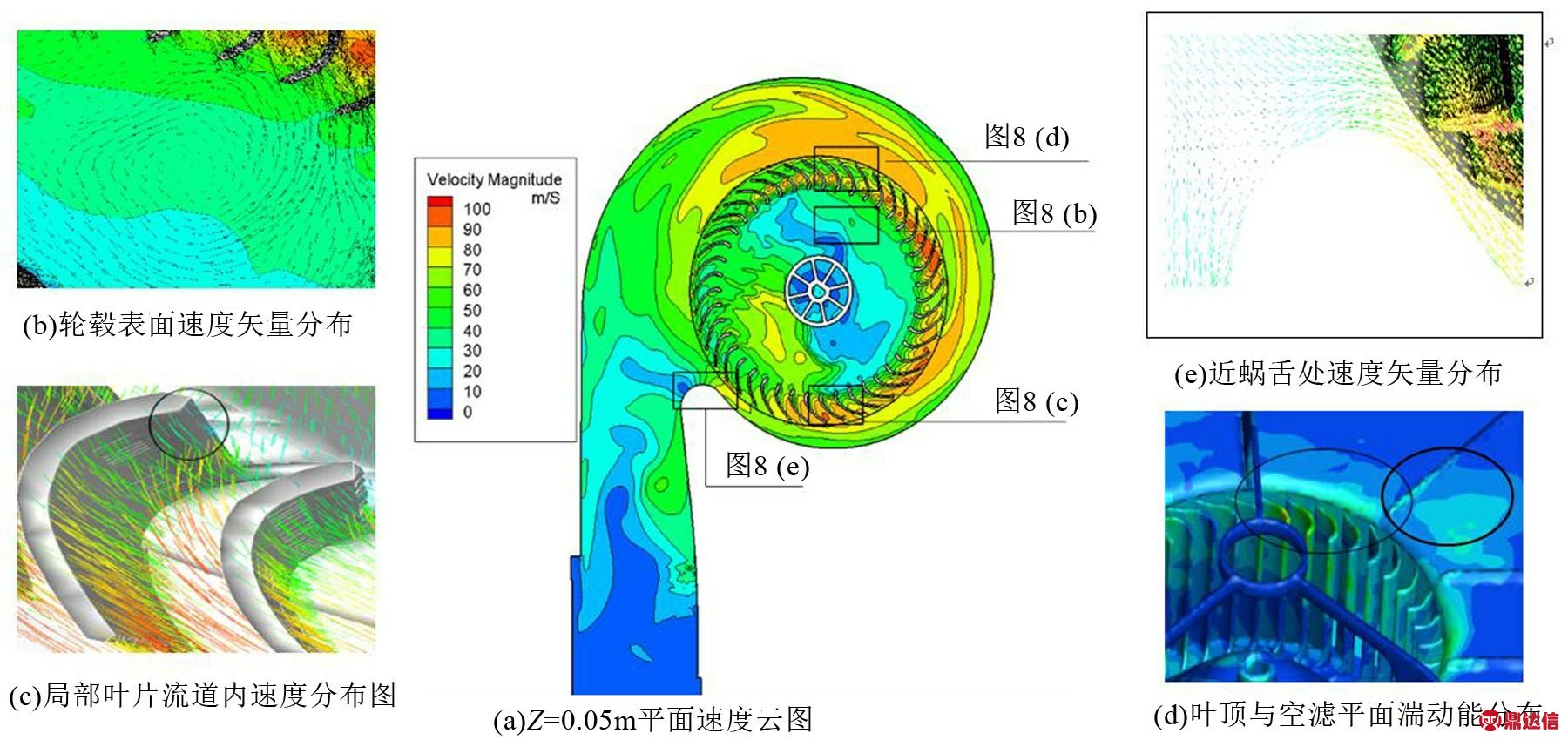
图8 叶轮流动状况分析
3 轮毂型线影响分析
3.1 轮毂型线
通过以上仿真分析可以发现轮毂部位的声功率明显大于其他部分,该处有大量低速气体聚集,湍动能强度较大,气流在叶轮离心力下要在后盘区域逐渐转为径向流动,因而不理想的轮毂型线设计会产生涡流,增大对叶片的冲击和导致气动噪声的产生,因此本节拟讨论轮毂型线对气动噪声的影响,设计3种轮毂型线优化方案,改变叶轮轮毂型线的凹凸程度,对叶轮其余结构不做处理,图9为叶轮轮毂型线结构改变前后示意图,方案一为原模型。对改后结构进行流场及声场仿真计算,仿真方法、噪声监测点、压力脉动监测点设置均与原模型一致。

图9 轮毂型线优化方案
3.2 轮毂型线流场和声场分析
图10为对叶轮进行轮毂线型优化后与原模型质量流量和效率的对比结果。优化后的模型其叶轮出口监测面处的质量流量相比原模型均略有增大,最大增加0.6 g/s;原模型效率为73.9%,方案二效率与原模型相比降低了0.23%,其余各方案效率较原模型相比整体变化不大;通过流动压力检测发现,方案四的叶轮进出口流动阻力相比原模型降低4.6%,有利于提高整体流量及整机效率,二者分别提高0.4 g/s与0.78%。
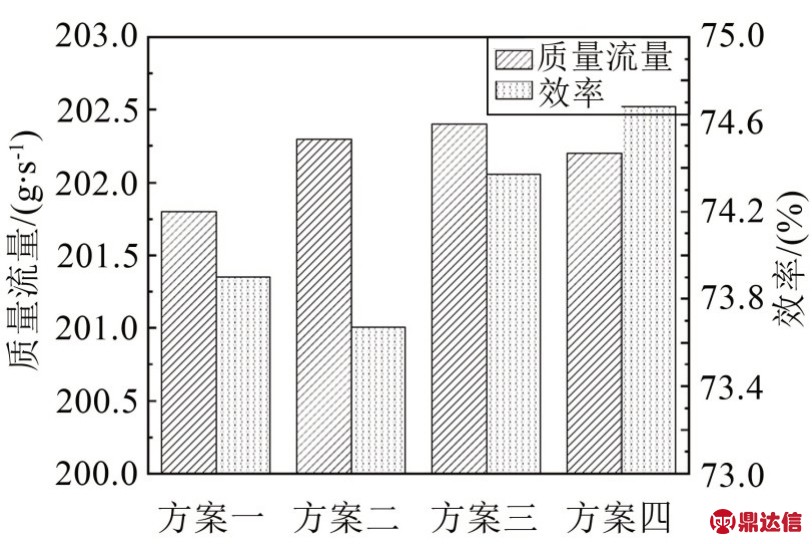
图10 原始模型与优化模型中质量流量和效率对比
图11 为叶轮的优化模型与原模型中噪声监测点总声压级以及43阶次叶频噪声峰值的对比结果,可以看出方案四降低各测点的总声压级以及43 阶次叶频气动噪声最为明显,POS1 与POS2 两个测点总声压级分别降低了2.1 dB 与4.2 dB,43 阶次叶频气动噪声则分别降低了4.2 dB与5.0 dB。因此对叶轮进行轮毂型线优化能有效降低气动噪声,方案四降低各测点的总声压级以及43 阶气动噪声最为明显。
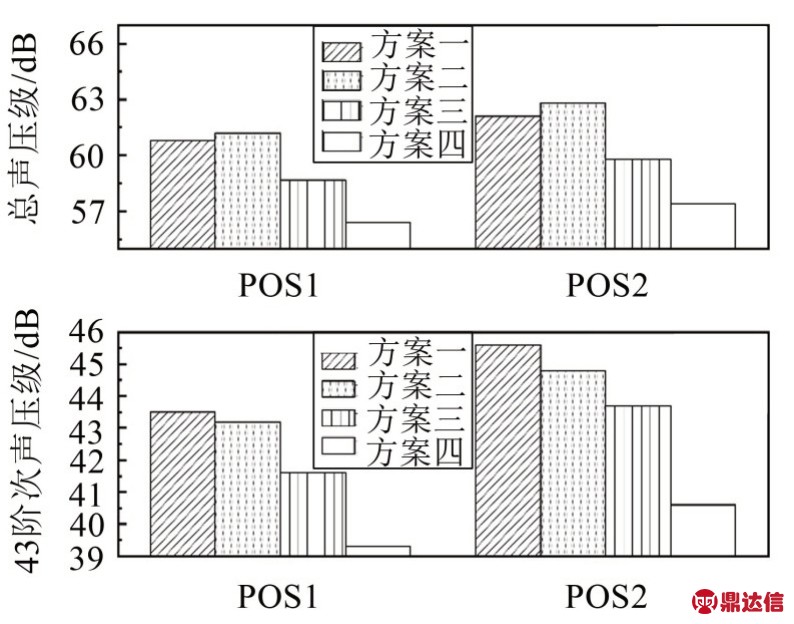
图11 原始模型与优化方模型中两测点声压级对比
分析方案四的流动情况,截取y=0 截面的湍动能云图与流线图与原模型进行对比,如图12和图13所示,可发现在对叶轮进行轮毂型线优化后,轮毂和叶片之间气流的回流与原模型相比强度降低,叶片、轮毂处湍动能强度降低,即气流对轮毂和叶片的冲击减小,减少了气流动能的损耗,与声场仿真结果一致,由于气流对轮毂及叶片的冲击减弱,因此通过叶轮监测面的质量流量以及鼓风机整机效率也略有增加。
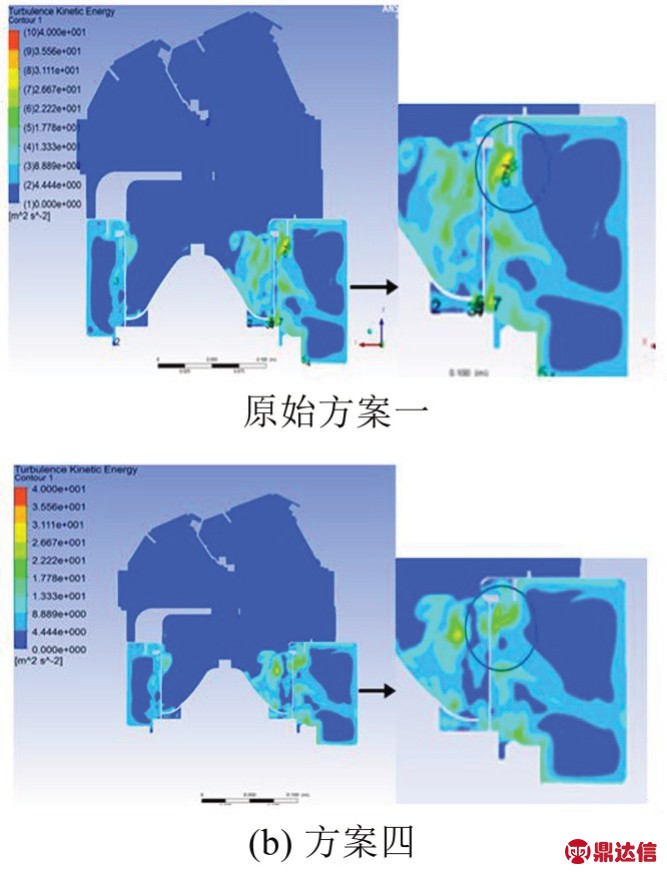
图12 y=0截面湍动能云图及局部放大图
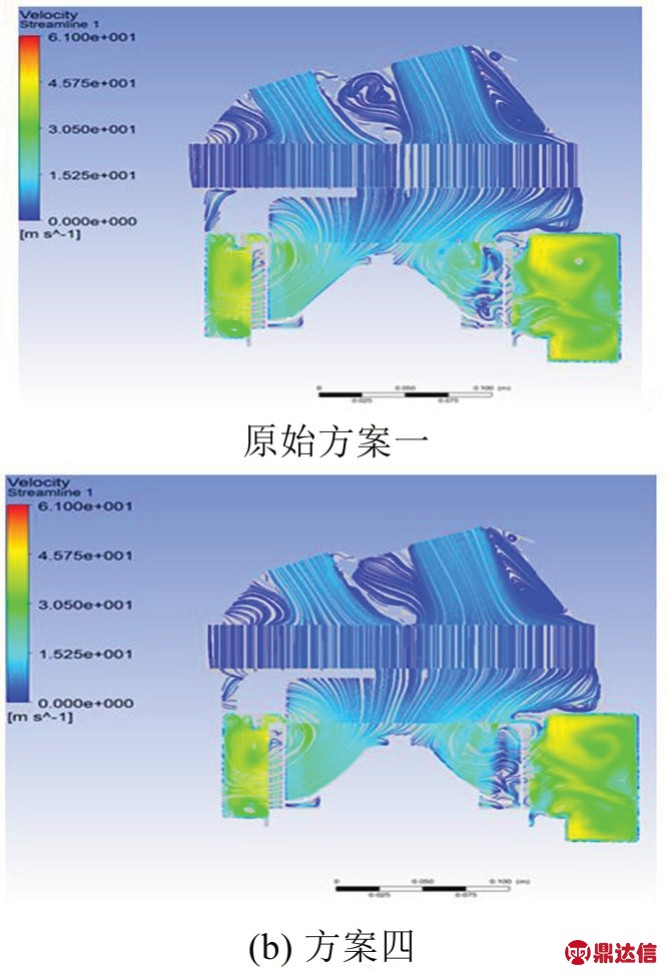
图13 y=0 截面流线图对比
4 叶顶弧度影响分析
4.1 叶顶弧度
原有叶片顶弧为直角结构,而根据对原始模型的分析可以看出,叶片顶部具有较高的湍流动能,气流在此处有较高的能量损失,这是由于气流在该处轴向速度较大,径向速度较小,有较大的冲角,因而涡流更大,流动分离更为明显,这也是该处声功率强度较大的原因。故有必要对叶轮叶片顶角弧度进行分析,优化气流在此处的流动状况,降低该处的湍流动能,减小气流对叶片顶部的冲击,进而降低气动噪声。原有叶片顶端采用直角设计(方案一),拟采用倒圆角30 度、45 度、60 度3 种方案作为设计优化方案,对叶轮其余结构均不做处理,如图14 所示。对改后结构进行流场及声场仿真计算,仿真方法、噪声监测点、压力脉动监测点设置均与原模型一致。
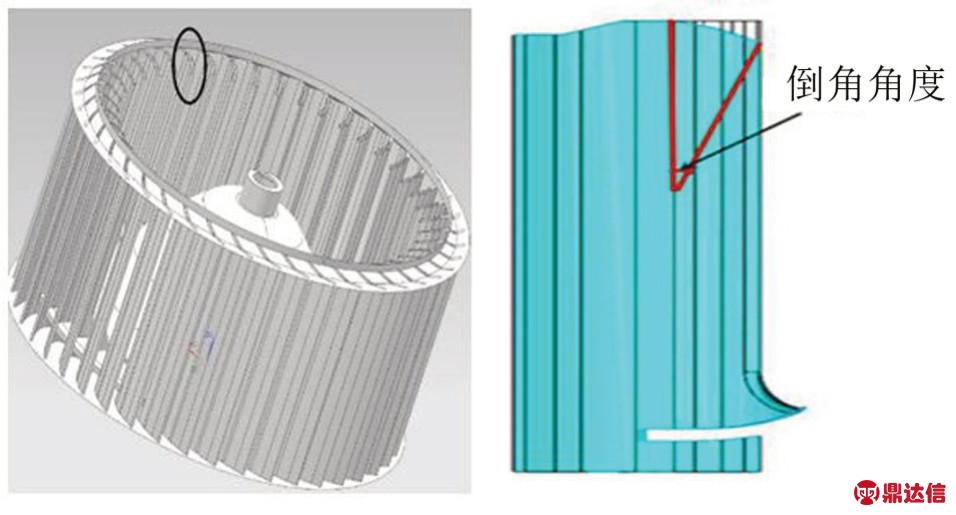
图14 叶顶倒圆角优化方案
4.2 倒圆角叶片流场和声场分析
图15 为对叶片顶部进行倒圆角处理后与原模型总声压级以及43阶阶次噪声峰值对比结果,由图可知,在对叶轮进行顶弧角度优化处理后,在POS2测点处方案四的总声压级降低了2.7 dB,同时其43阶气动噪声最大降低了4.0 dB;而在POS1测点处方案二的总声压级最大降低1.6 dB,方案四的43 阶气动噪声降低了2.9 dB。
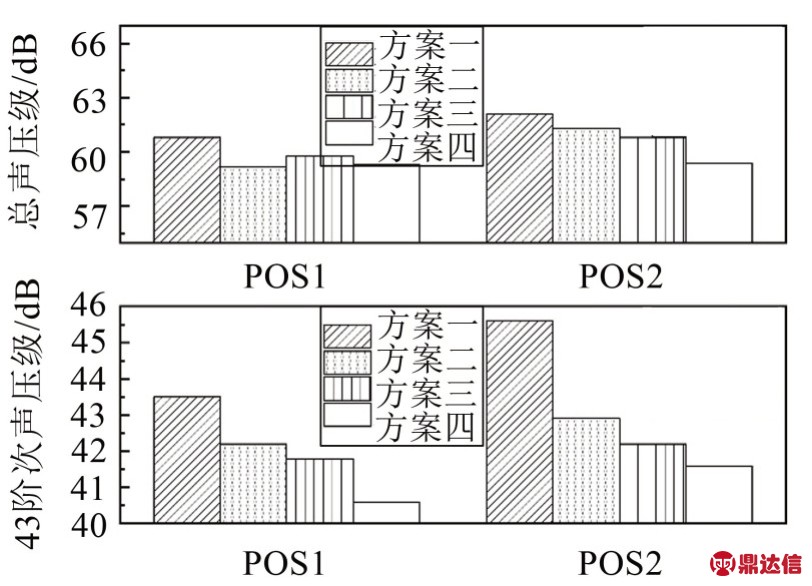
图15 原始模型与优化模型噪声对比
而叶轮出口监测面处的数据如图16所示,可见各模型的质量流量较原模型均略有增大,最大增加5.14 g/s,效率较原模型相比虽略有降低但变化不大,最大降低约1.24%。因此综合评估,方案四在基本不降低性能的基础上具有最优的降噪效果。
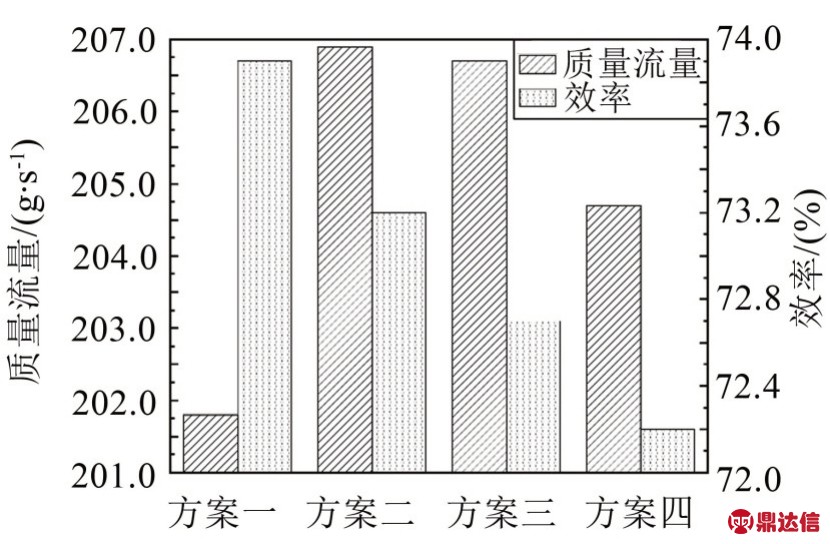
图16 原始模型与优化模型质量流量与效率对比
图17为优化方案四的叶轮湍动能分布,与原模型对比如图7(a)所示,可见原始叶轮在叶片顶部区域具有高湍动能,在进行叶片顶弧优化处理后,叶轮上无整体湍动能峰值明显的部位,且顶部湍动能降低。说明叶片顶部的倒圆角设计对于该区域气流流动有改善作用,从而降低了气动噪声。
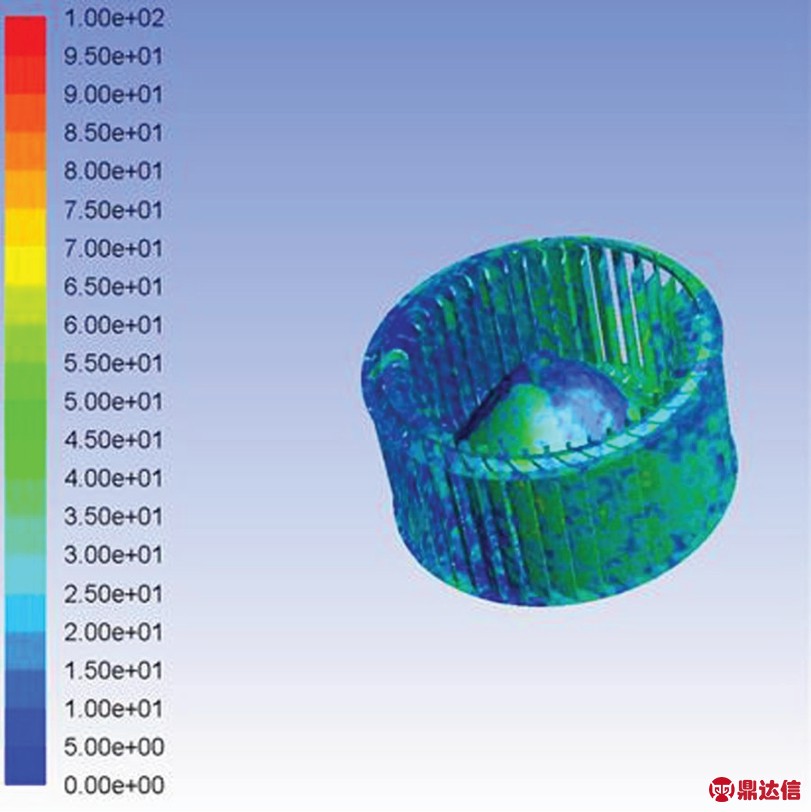
图17 方案四中湍动能分布
叶片顶部湍动能的降低也减弱了对叶轮上方薄弱平面即空滤下表面的气流冲击力,如图18 所示。该平面较薄,且距离叶轮较近,为30 mm,较大的旋转气动力会作用于上方平面上,引起该结构振动,是气动噪声另一个重要的传播路径。从图18 可以发现,方案四中叶轮附近气流对上方空滤表面的激振力较原模型相比降低了15%。
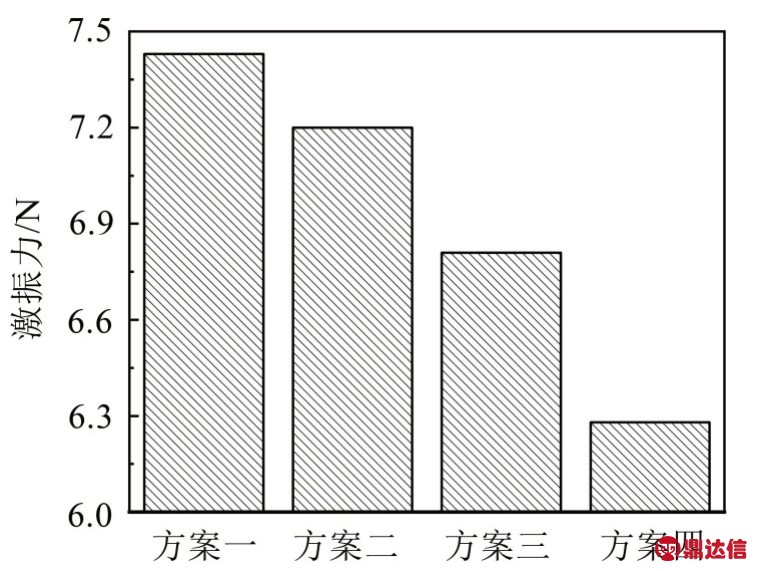
图18 原始模型与优化模型激振力对比
对该鼓风机原模型的实验研究也表明[17],叶轮上方空滤表面受到的气动载荷也加剧了噪声的传播和辐射。如图19所示,当原始模型中该平面被均匀贴上胶泥即改变其阻尼特性后,测得的43阶次叶频噪声受到明显抑制。因此叶片顶部的流场不只影响旋转气流的湍流噪声和阶次噪声,也会对周围的薄弱面进行激振,加剧结构振动和流固耦合噪声。对叶轮顶弧角度进行优化处理后的仿真分析也验证了这一点。
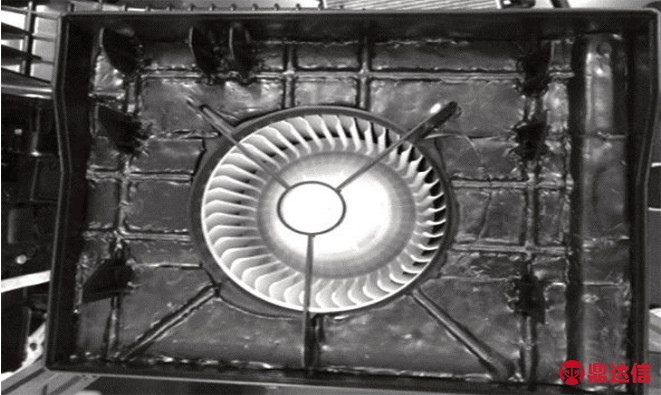
图19 叶轮上方平面贴胶泥示意图
4.3 降噪效果检验
由于实际条件所限,仅制作了倒圆角叶轮优化样件。在相同的实验条件下(进风箱、蜗壳、电机、分配箱等其它部件均保持一致,且空滤平面上未贴胶泥),对方案四中60 度倒圆角叶轮鼓风机系统进行了测试,原模型样件和优化方案四样件测试结果对比如图20 所示。原始样件及优化样件的测试结果和仿真计算结果汇总在表3 中。对比测试结果可知,100 Hz 以下中低频段幅值变化不大,100 Hz~700 Hz内优化结构的幅值略有增加,平均在3 dB以内,700 Hz 以上的频段除了2 500 Hz 外幅值也基本变化不大,重点关注的阶次2 500 Hz 处幅值则在结构优化后有较大幅度的降低(优化样件中POS1 和POS2测点43阶次叶频噪声相比原始样件分别降低4.0 dB 和8.6 dB),最终表3 中两种结构的总声压级测试结果表明优化后结构的总声压级更低(总声压级相比原始样件分别降低了3.4 dB、3.7 dB)。其中100 Hz~700 Hz 内幅值误差略有增加,对总声压级的贡献不大,因此本文在分析过程中暂时将其忽略不计。高频段2 500 Hz 处噪声主要由叶轮旋转引起,与叶轮结构密切相关,可以反映阶次噪声的优化效果。另外总声压级考虑了所有频率叠加的影响,其优化前后的对比可以反映声波最终的辐射效果。从这两方面来看,叶轮结构优化后降噪效果明显。原始结构和优化结构仿真计算的结果对比也和上述规律一致,但优化结构实验值与原始结构实验值相比降噪幅度更大的原因在于仿真计算中未包含流固耦合计算,故由叶轮旋转导致的对其上方空滤平面激振所产生的噪声并未包含在内,但实际噪声测量中则包含了该部分噪声。这也进一步表明根据优化方案四对叶顶弧度所进行优化有效降低了气动噪声。
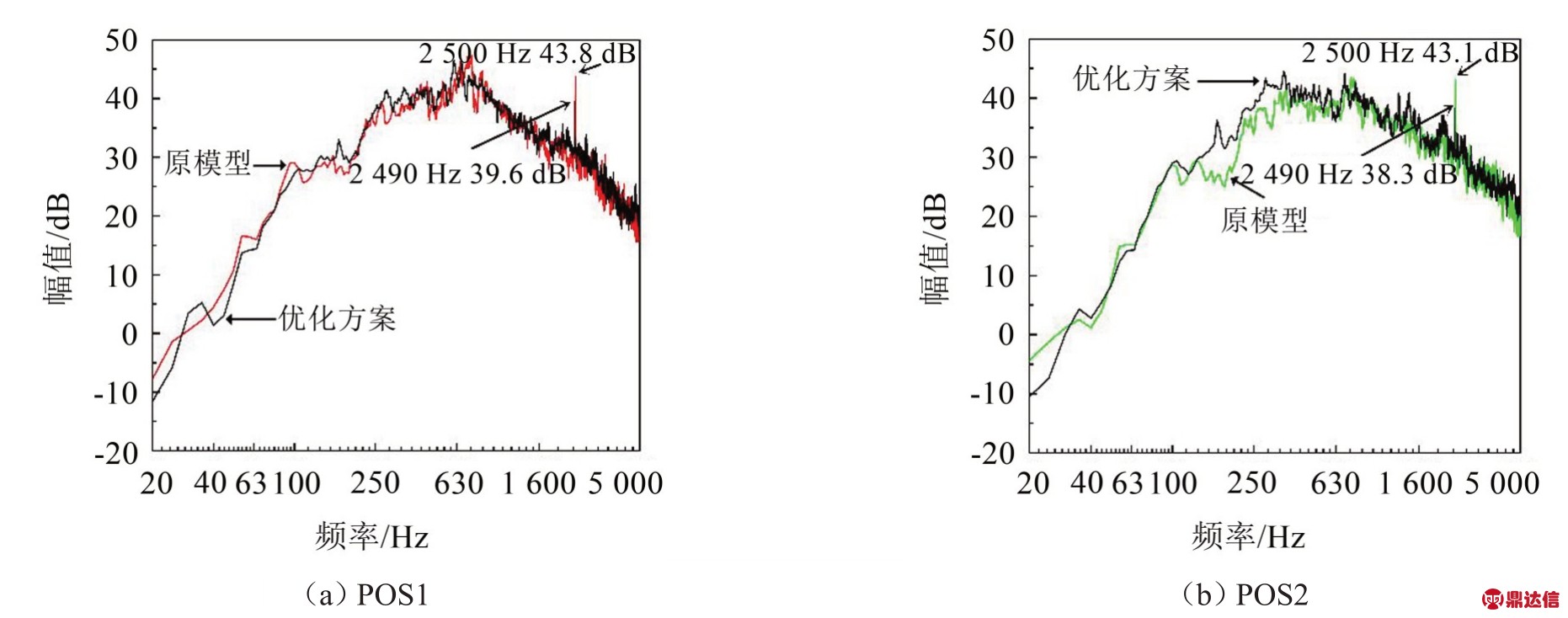
图20 优化方案四与原模型样件噪声测试频谱对比
表3 空调鼓风机气动噪声试验与数值模拟对比分析/dB
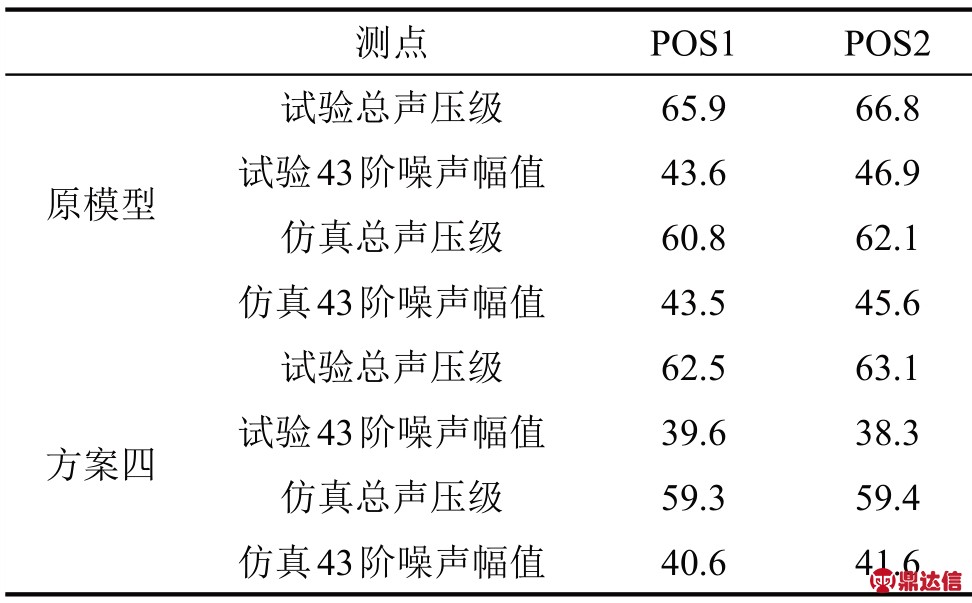
将根据优化方案四所得的实验结果与仿真结果也进行了对比,由于存在电机噪声与机械噪声的干扰,POS1 和POS2 测点实验值的总声压级分别高于仿真值3.2 dB 和3.7 dB,而43 阶次叶频噪声实验值则略低于仿真计算值,POS1 和POS2 两测点的实验值分别比仿真值低1.0 dB和3.3 dB,但误差均小于5 dB,和原模型的实验与仿真结果对比结论一致。
综上所述,对叶轮顶弧的优化能够有效降低气动噪声,在对汽车空调鼓风机进行降噪分析时应考虑叶轮顶弧的影响。
5 结语
本文通过数值模拟计算和实验测试分析了应用于新能源汽车的空调鼓风机的气动噪声特性,并研究了轮毂线性和叶片顶弧对气动噪声的影响。具体结论如下:
(1)在叶轮轮毂处、叶片顶部、靠近蜗舌处的叶片的湍流运动和声功率较为突出,流场的不合理分布所导致轮毂、叶片和气流的周期性相互作用是产生阶次噪声的主要原因之一。
(2)轮毂型线对进入叶片流道内的气流起重要的导向作用,优化模型可以在质量流量和效率变化不大的情况下,使轮毂和叶片之间气流的回流和湍动能强度较原模型降低,使气流对轮毂和叶片的冲击减小,从而降低气流动能的损耗和气动噪声的幅值。仿真结果表明在两个测点位置总声压级分别最多降低2.1 dB 与4.2 dB,43 阶次叶频气动噪声分别最多减小4.2 dB与5.0 dB。
(3)叶片顶部不只影响旋转气流的湍流噪声和阶次噪声,也会对周围的薄弱面产生激振,加剧结构振动和流固耦合噪声。实验结果表明,在质量流量和效率变化不大的情况下,优化后的模型总声压级在两个测点位置处分别最多降低3.4 dB 与3.7 dB,43阶次叶频噪声分别最多减小4.0 dB与8.6 dB。