摘 要:为了提高混凝土预制件生产线效率,设计了基于PLC的四轴气动摆模机械手控制系统。该系统以S7-200 PLC为控制核心,Smart 700为人机界面。分析了机械手的结构与功能,在此基础上设计了控制系统的硬件组成,根据机械手的实际作业需要和工作流程的特点,完成了软件系统的编写。试验结果表明该控制系统抗干扰能力强,控制精度高、性价比高、性能稳定、操作简单,同时具有良好的可扩展性和可维护性,能满足摆模需求,符合工业应用要求。
关键词:PLC;控制系统;摆模机械手
引言
随着制造业自动化需求的日趋增加,机械手在工业生产中得到越来越广泛的应用[1-2]。摆模机械手是机械手在混凝土预制件行业的重要应用,该设备主要是代替人工,完成将边模精确的摆放至模台指定位置并固定的作业,由此提高生产效率,减少安全事故的发生。控制系统作为机械手的重要组成部分,其性能的好坏直接关系到机械手能否达到预期的设计要求[3]。目前工业机器人中所用的“运动控制器+PC”的构架形式控制系统,以PC为硬件平台,依靠运动控制卡实现运动轴的实时控制。虽然上下位关系清晰,但系统稳定性差、可靠性低、可扩展能力弱,且功能冗余,性价比很低[4]。本研究基于S7-200 PLC设计了摆模机械手控制系统, 由于PLC具有易于扩展、模块化、灵活性等优点,设计的控制系统不仅能满足机械手的工作要求,同时系统具有结构紧凑、性价比高、安全稳定、控制精度高、操作方便、良好的可扩展性和可维护性。
1 机械手的结构与功能分析
混凝土预制件产品多种多样,工程建设领域常见的预制件有管道、桥梁、轨枕等,建筑领域常见的预制件有墙板、楼板、楼梯、阳台、梁、柱等,生产混凝土预制件时,需要根据其形状,首先把磁性边模固定在钢制模台面上,然后浇筑混凝土。磁性边模的结构如图1所示,边模由不锈钢板制成,固定有加强筋板,两侧安装有磁铁和插销,压下磁性边模上的插销可使边模与模台磁力固定。

图1 边模结构示意图
机械手结构组成如图2所示,整体采用龙门式结构,主要包括X轴桁架、Y轴大梁、Z轴升降臂和集成执行爪等。机械手具有4个自由度,即纵向X轴移动、横向Y轴移动、竖直Z轴移动以及绕Z轴的转动(C轴运动)。X轴、Y轴、Z轴的移动采用伺服电机驱动齿轮在齿条上运动来实现,由直线导轨导向,保证运动的直线度;C轴的旋转运动采用伺服电机驱动齿轮组。

图2 机械手的结构示意图
机械手的末端执行机构为集成执行爪部分,结构如图3a所示,该部分采用气动驱动的方式,气动系统原理图如图3b所示。该气动系统由气动三联件、电磁换向阀、气流调节阀、夹爪气缸、缓冲气缸、压销气缸组成。用一个三位五通的电磁换向阀控制夹爪气缸驱动夹爪抓放边模,同时能保证卡爪可靠的夹紧边模,防止因断电而导致边模的脱落。压销气缸用于边模的磁力固定,缓冲气缸作为补偿机构,可以将Z轴方向上所存在的误差吸收。集成执行爪上的夹爪气缸、压销气缸、缓冲气缸均由电磁阀控制其运动方向,用气流调节阀来调节其运动速度。
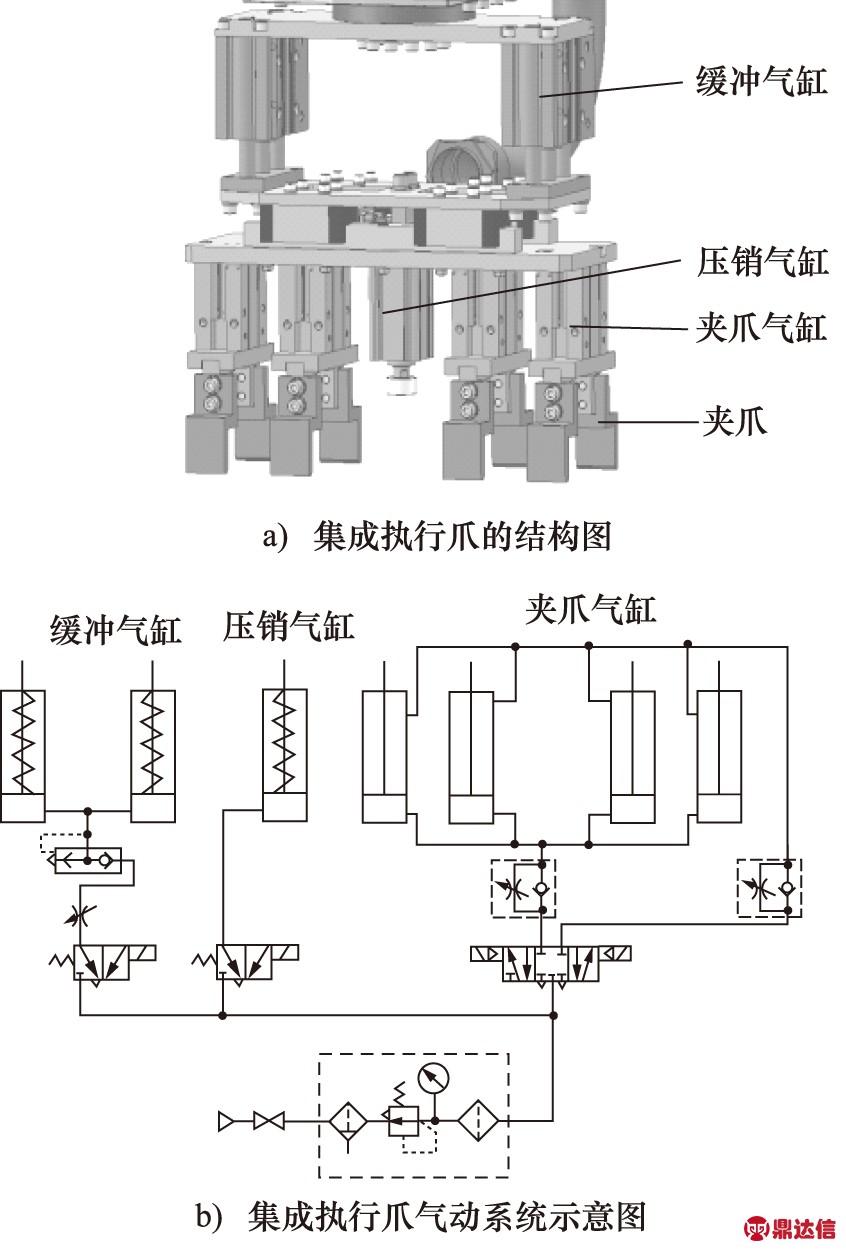
图3 集成执行爪的结构及气动系统示意图
2 控制系统的硬件组成
机械手控制系统采用S7-200系列CPU224XP CN型PLC为控制核心,该型号PLC集成了14个输入点,10个输出点,2个串行通讯端口,支持PPI、MPI和自由口通讯方式,可与伺服驱动器、PC机和触摸屏等进行通讯,具有高速脉冲输出功能和运动控制功能,能很好地控制伺服电机的工作,使其实现较精确的位置控制[5-6]。由于一个CPU224XP CN型PLC最多可控制两个伺服驱动器,故采用两个PLC实现机械手的四轴联合运动,其中1号PLC控制Y轴、Z轴的运动,2号PLC控制X轴、C轴的运动。两个PLC采用RS485通讯电缆连接,通过PPI通讯协议进行数据的传输,1号PLC作为主站,2号PLC作为从站,主站通过“网络读取”(NETR)或“网络写入”(NETW)指令从从站中读取数据或向从站中写入数据[7],控制轴运动、气缸动作、指示灯的显示等。
伺服电机采用台达ECMA系列,伺服驱动器采用台达ASDA-A2系列,该系列伺服驱动器支持多种轴控操作, 内含电子凸轮功能, 搭配20-bit分辨率编码器,可达到高速位移、精准定位等运动控制需求。伺服电机采用“脉冲串+方向”的控制方式,PLC的两个数字量输出口分别输出脉冲串信号和方向信号,即可完成电机的正反转、启停及速度控制。四个伺服驱动器的通讯端口与2号PLC的Port1通讯口连接,PLC可通过Modbus协议读取来自各伺服驱动器的信息,如编码器反馈回来的当前速度、绝对坐标位置和伺服驱动器的运行状态等。Smart 700触摸屏作为人机界面,与1号PLC 通过PPI通讯协议建立高速无缝连接,可实时显示和处理PLC中传输的数据,便于进行系统监控和故障排除。综上,控制系统的硬件连接如图4所示,整个控制系统硬件设计上充分考虑了机械手工作的稳定性、可靠性以及各种控制元件连接的灵活性和方便性。
表1 I/O口地址分配表
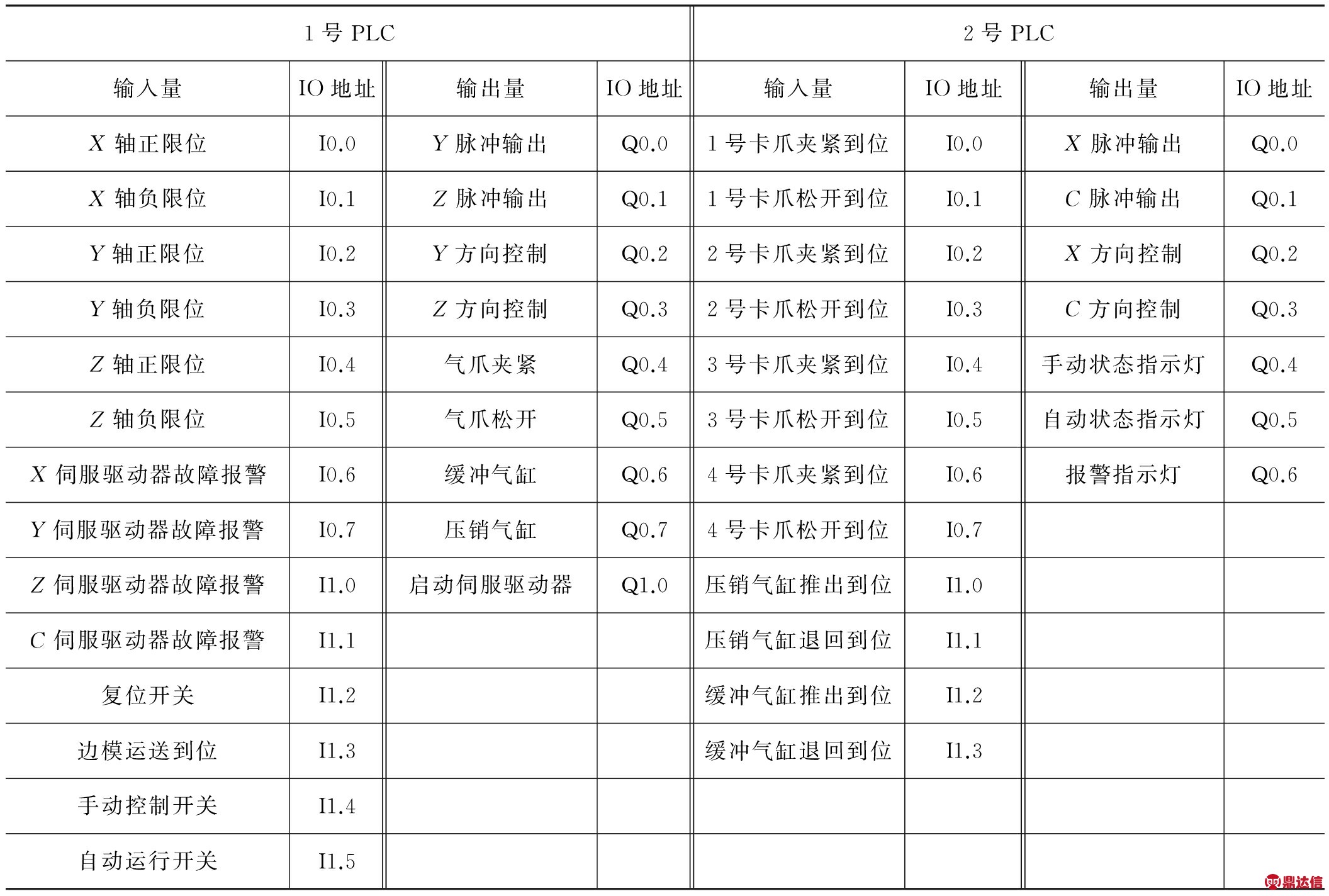
3 控制系统的软件设计
3.1 PLC程序设计
据外围硬件系统的设计,本系统PLC需处理的控制量主要包括各种数字量信号的输入、传感器信号的处理、气动元件的驱动、伺服驱动等。其中气缸均是用电磁阀控制其伸缩,在气缸的两端安装有磁性开关,用于反映气缸杆的位置。在各轴的极限位置安装了行程开关,用于判断是否达到轴向限位。边模输送带上安装行程开关,用于判断边模是否运送到位,指示灯显示运行状态及报警状态。综上,系统PLC的I/O口地址分配如表1所示。
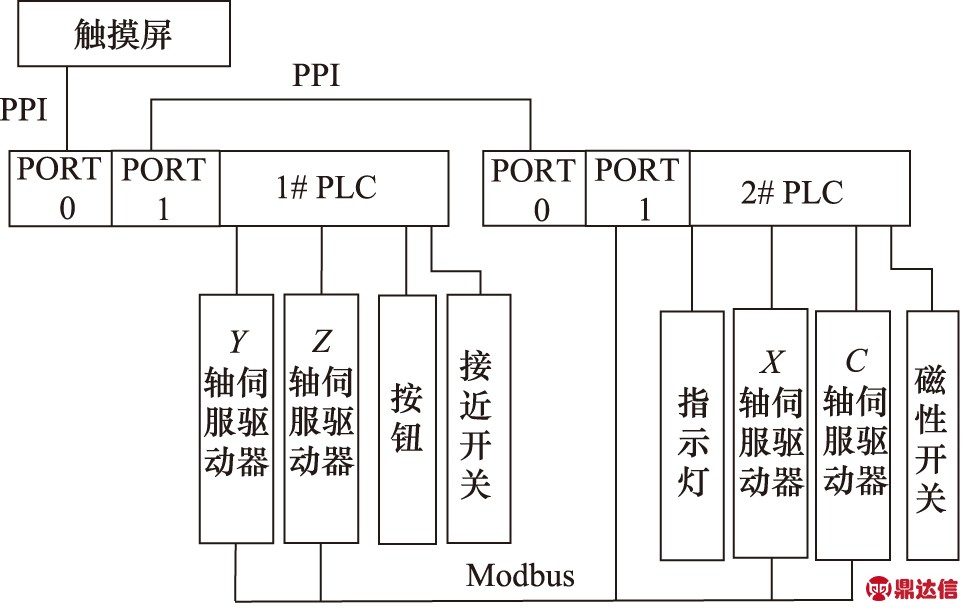
图4 控制系统硬件连接示意图
系统使用STEP7-Micro/WIN V4.0 SP9软件对PLC进行程序编写,采用梯形图的编程语言。每个PLC程序包括一个主程序和若干个子程序,PLC在每个扫描周期内循环的执行主程序,在主程序中调用子程序。子程序包括自动控制,X轴手动控制,Y轴手动控制,Z轴手动控制,C轴手动控制,限位处理,故障报警,PPI读写,数据读写等,将写好的程序下载到PLC中,开机运行后PLC 通过各个传感器和继电器收集信号,逻辑处理后针对各执行机构进行顺序控制,并完成与其他PLC及触摸屏的通讯交互[8]。
3.2 人机界面设计
Smart 700触摸屏采用组态软件WinCC flexible开发其人机画面。WinCC flexible具有开放简易的扩展功能,集成了ActiveX控件,带有丰富的图库,提供大量的图像对象供用户使用,同时还提供配方功能。利用配方可方便的实现机器的参数化、工作量的转换和分批量处理的任务[9]。整个监控系统包括3个组态画面,即自动运行画面、手动控制画面、故障报警画面。
手动控制画面如图5a所示,实现单独控制X轴、Y轴、Z轴、C轴正反转、启停、运动速度、气动夹爪的夹紧与松开、缓冲气缸的伸出与缩回。
自动运行画面如图5b所示,作为监控系统的主画面,包括控制模块、显示模块、配方模块。控制模块中包括手动控制按钮、自动运行按钮、复位按钮。按下自动运行按钮,机械手执行自动运行程序。按下手动控制按钮,画面切换到手动控制界面,同时进入手动控制模式。按下复位按键,机械手自动回到设定的机械原点位置;显示模块即实时显示机械手自动运行时当前各轴的运动速度和绝对位置;配方模块即显示当前摆放边模的种类和具体的数据,在系统运行的过程中,可以随时对数据记录做添加、删除和修改,并下载到PLC中,使机械手能完成不同大小和不同位置边模的摆放,增加了系统的柔性。
3.4 样机试验分析
故障报警画面主要负责系统的故障显示,当系统出现故障时,如伺服驱动器运行故障,轴运动达到限位报警状态等,发出提示消息,进入报警画面,以便管理维护人员及时发现,及时维修。
机械手的控制面板示意图如图6所示。系统的工作流程如图7所示。按下启动按键,系统接通电源,电源指示灯亮,此时系统开始进入初始化,触摸屏初始化后显示主页面,各传感器部件进行自检,各气缸处于缩回状态,启动伺服驱动器,机械手回到设定的机械原点;系统在初始化判断完成后,进入等待运行模式,此时若将控制面板上的选择开关拨到手动或按下触摸屏中的手动按钮,系统进入手动控制模式,若将选择开关拨到自动或按下触摸屏中自动运行按钮,则系统进入到自动运行模式,自动运行的过程如下:
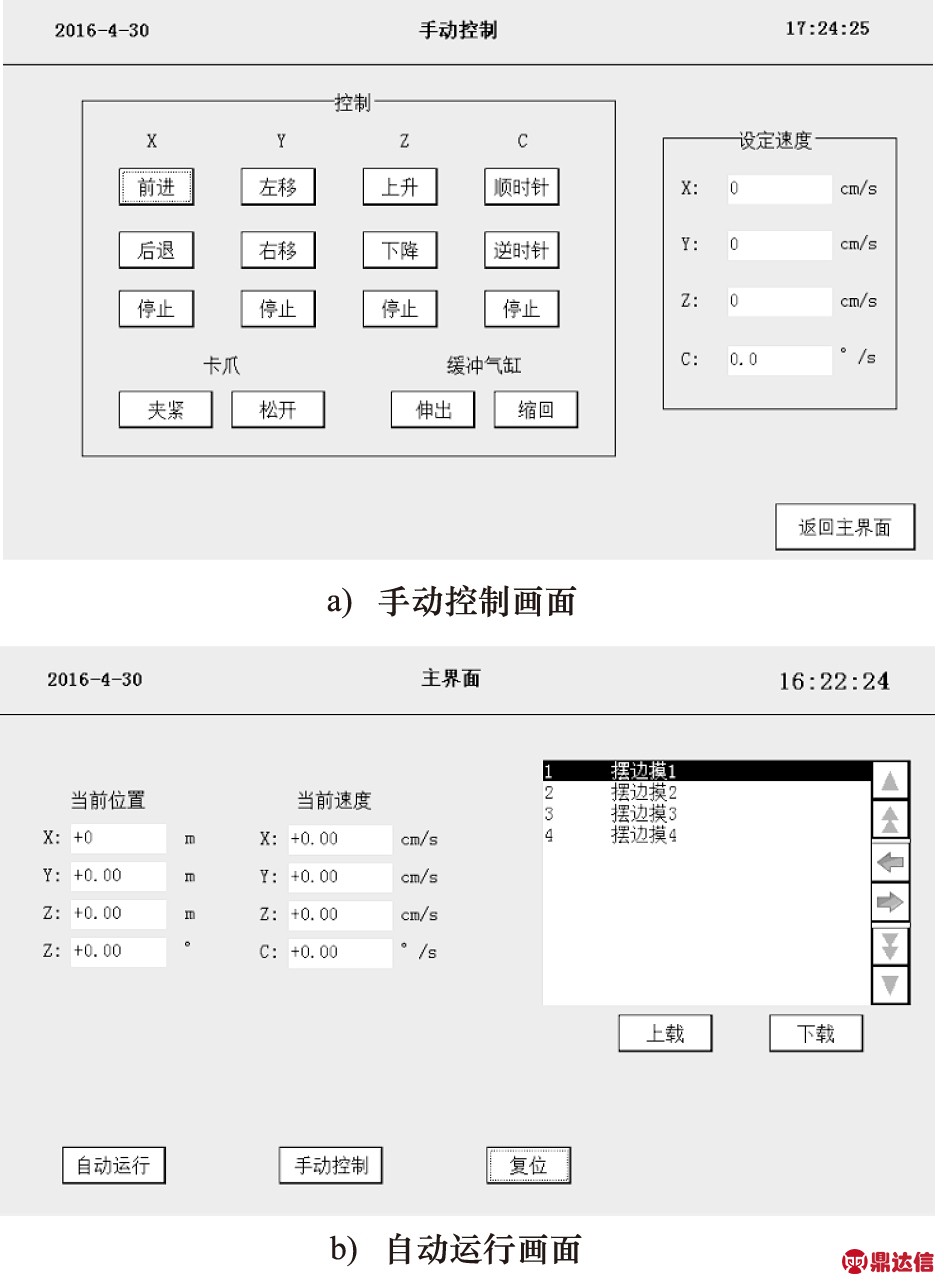
图5 人机界面组态画面
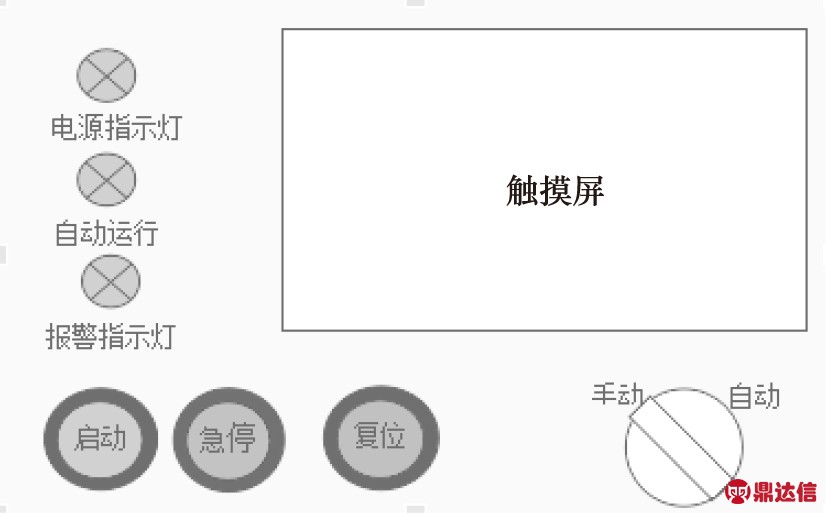
图6 控制面板示意图
(1) 机械手从机械原点出发,四轴联合运动,使集成执行爪到达边模输送带的上方,等待边模运送到位信号;
(2) 接收到边模运送到位信号后,机械手沿Z轴下降指定距离,卡爪气缸伸出,驱动卡爪夹紧边模, 传感器检测到夹紧到位后,等待2 s,保证卡爪夹紧完全。然后机械手沿Z轴上升一定的距离,防止机械手在下一步的运行过程中,边模与传送带等其他设备发生碰撞;
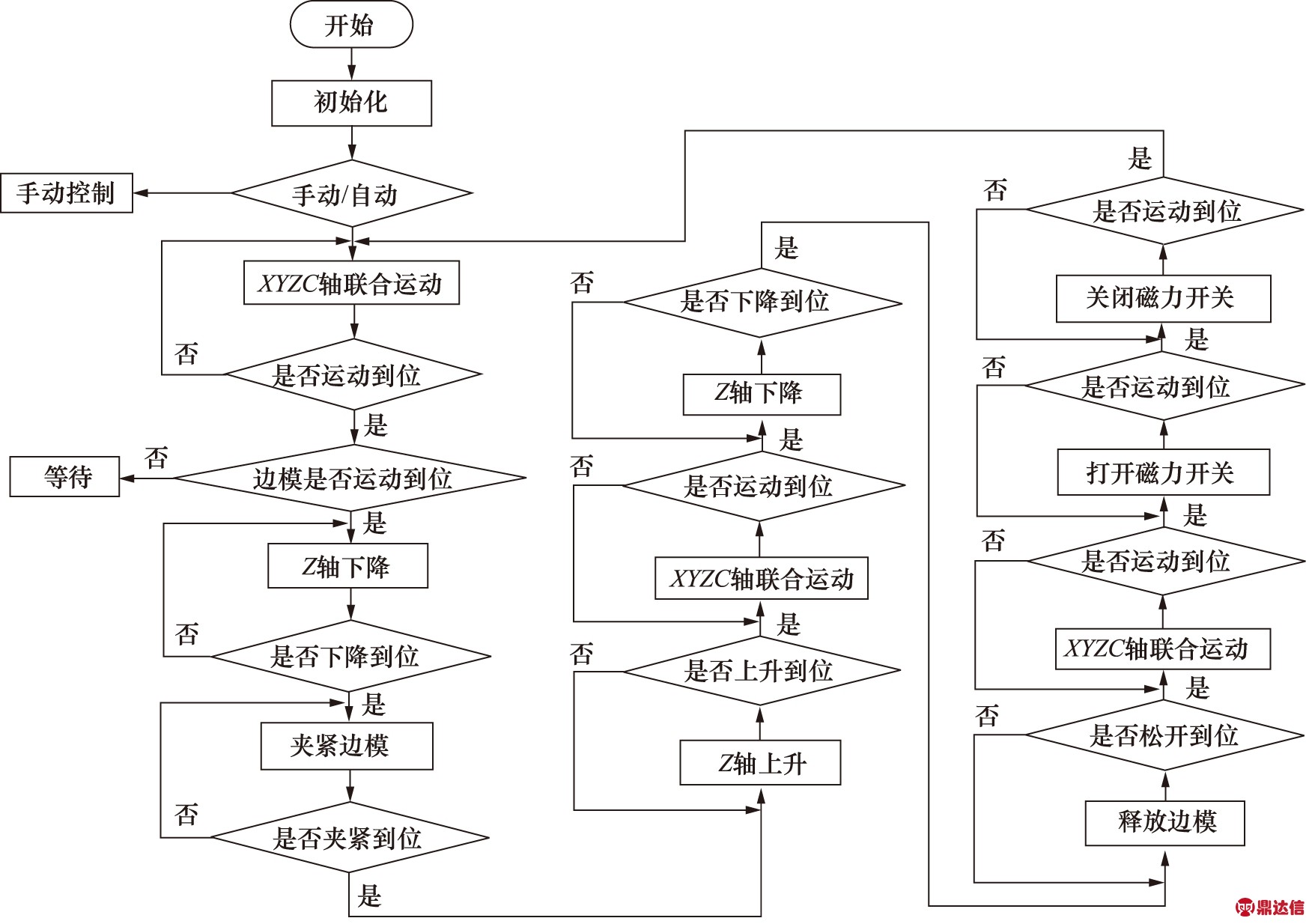
图7 机械手工作流程图
(3) 集成执行爪运动到边模摆放位置的上方,同时调整好边模摆放的角度后,沿Z轴下降到距边模上方一定的距离,缓冲气缸伸出,驱动边模继续沿Z轴下降到模台上,若此时的模台的精度与实际设计有一定的误差,则缓冲气缸可将此误差吸收,保证了系统的安全性;
(4) 传感器检测到缓冲气缸伸出到位后,卡爪气缸收缩,卡爪松开,释放边模。X轴、Y轴联合运动将集成执行爪移动到边模的一侧插销位置上方,压销气缸伸出,压下磁性边模的磁铁插销,传感器检测到伸出到位后,压销气缸缩回,重复压销动作,将边模两侧的插销压下,完成边模完全固定;
(5) 集成执行爪回到边模输送带的上方,等待下一个边模的运送到位,循环的开始下一个边模的摆放。
在自动运行模式下,合上急停开关,系统断电,整个系统停止工作,只有松开急停开关后,整个系统才可以开始工作,增加了整个装置的安全性。
3.3 工作流程分析
将设计的控制系统在如图8所示的样机上进行了试验,结果表明该控制系统可较好的实现对机械手的控制,完成预期设计的目标。
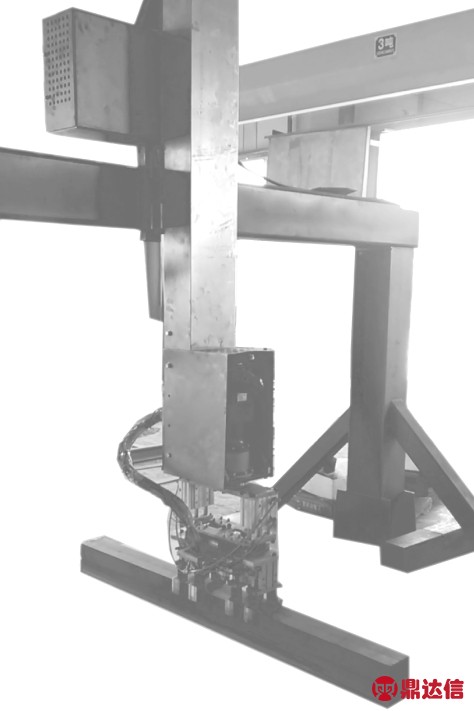
图8 样机试验图
4 结论
本研究在分析了气动摆模机械手的结构和功能的基础上,重点介绍了控制系统的软硬件设计。
(1) 采用S7-200 PLC作为控制核心,使系统具有较强个的抗干扰能力和良好的可扩展性和可维护性,使用PLC自带的高速脉冲控制伺服驱动器,实现了对机械手四轴的精确运动控制;
(2) 采用Smart 700作为人机交互界面,编写功能齐全、直观的操作界面,操作简单;
(3) 系统设计了自动控制模式和手动控制模式,方便用户操作,设置急停功能,保证了系统的安全性,使用配方功能,增加系统的柔性,设计了故障报警功能,方便对设备的故障的维修。