摘要:某吸气式发动机试验台的空气调压阀及液压驱动系统状态复杂、可靠性低、故障易发。为提高调压阀运行的安全性、可靠性和精确性,设计了其运行环境参数的监控系统。基于工业以太网和NI cRIO实时控制系统,实现了液压驱动系统的油压、油温、油液污染度、液压缸位移及阀后管路压力等运行环境参数的远程在线监测、显示、记录和报警,并通过对油冷机和排气电磁阀的开关控制,实现了对液压油油温及管路压力的闭环控制。测试结果验证了该监控系统的正确性和实用性。
关键词:调压阀;液压系统;运行环境参数;远程;在线监测;闭环控制
0 引言
空气调压阀系统是某吸气式发动机试验台提供模拟来流的关键系统,由4台不同口径和流量的调压阀组成,它以液压系统为驱动源,通过液压缸活塞杆的直线运动带动阀杆的上下运动,改变阀门的开度,实现对阀后空气压力和流量的闭环调节,为来流模拟设备提供空气介质。作为机、电、液强耦合系统,液压系统是调压阀的中枢,液压系统的运行状态直接决定调压阀的运行状态,调压阀的工作状态也直接或间接地通过液压系统的运行状态和参数反映出来。
此外,为提高调压阀调节的快速性和准确性,在其启动前,还需要向阀后的管路中预充填一定压力的空气,预充填压力这一运行启动的工艺参数,也直接决定着调压阀建压的动态特性和来流模拟设备的安全。曾经由于某台调压阀的内漏,使其阀后空气管路压力快速升高,超出预充填压力,导致其运行状态难以精确受控并影响试验台的安全。为此,为了预防阀门内漏对试验状态的影响,需要通过一定的控制措施来精确控制预充填压力参数。
调压阀的液压和工艺运行参数不但能实时反映出其运行的环境状态,还对其启动运行特性起着决定性作用。因此,有必要对运行环境参数实施监控,从而掌握调压阀的运行状态,保障其安全、可靠、精确运行。为此,设计了调压阀运行环境参数的监控系统。
1 运行环境参数的监测原理
调压阀的运行环境参数由液压运行环境参数和工艺运行环境参数组成。参数的监测主要利用各种传感器和检测设备实施数据监测和记录。为此,需要合理选定监测参数,并进行监测测点的布局。
1.1 监测参数的选取
调压阀液压系统由共用的液压源系统和4套独立的液压伺服系统组成。监测液压运行环境参数时,监测对象是表征液压系统工作状况的主要参数。为此,监测如下参数:
(1)液压油的油温:液压油是液压系统的工作介质,而液压油的油温是保证液压系统正常、可靠运行的重要参数,监测油温可以有效了解液压系统的性能和工况;
(2)油源压力:油源压力是反映液压设备工作特性的基本参数,表征着液压系统带负载的能力;
(3)油液污染度:液压设备的故障60%~70%以上是由于油液的污染引起的,对污染度的监测和控制是提高液压设备可靠性的重要保证;
(4)液压缸油压:液压缸有杆腔和无杆腔的压力变化可以表征出液压缸进油、回油情况以及液压缸活塞杆的运动情况,进而直接表征调压阀阀杆的运动情况;
(5)液压缸活塞杆位移:调压阀利用液压缸活塞杆的直线运动带动阀杆的上下运动,因此,监测液压缸活塞杆的位移信号,可以实时监测到调压阀的开度情况。
综上,液压系统运行监测参数为:1个液压油油温参数,1个液压油油源压力参数,1个油液污染度参数,8个液压缸有/无杆腔压力参数,4个液压缸活塞杆位移(阀门开度)参数。
此外,选取4台调压阀的阀后空气管路压力参数作为工艺运行环境参数。
1.2 监测测点的布局
根据监测参数及其数量要求,结合液压系统管路和元件的布局,单台调压阀的液压系统元件及测点的布局如图1所示。其中:4台调压阀共用电磁换向阀10以下的液压源系统,电磁换向阀10以上的液压伺服系统相互独立,其他3台调压阀的元件与测点布局与此类似。在液压油的油箱内布置液压油的油温测点;在压油滤出口管路上布置油源压力测点;利用压油滤自带的压差发讯器作为油液污染度测点;利用液压缸自带的位移变送器作为液压缸活塞杆位移测点;在液压缸有杆腔、无杆腔油管与阀块的连接处,通过三通接头安装液压缸油压测点。
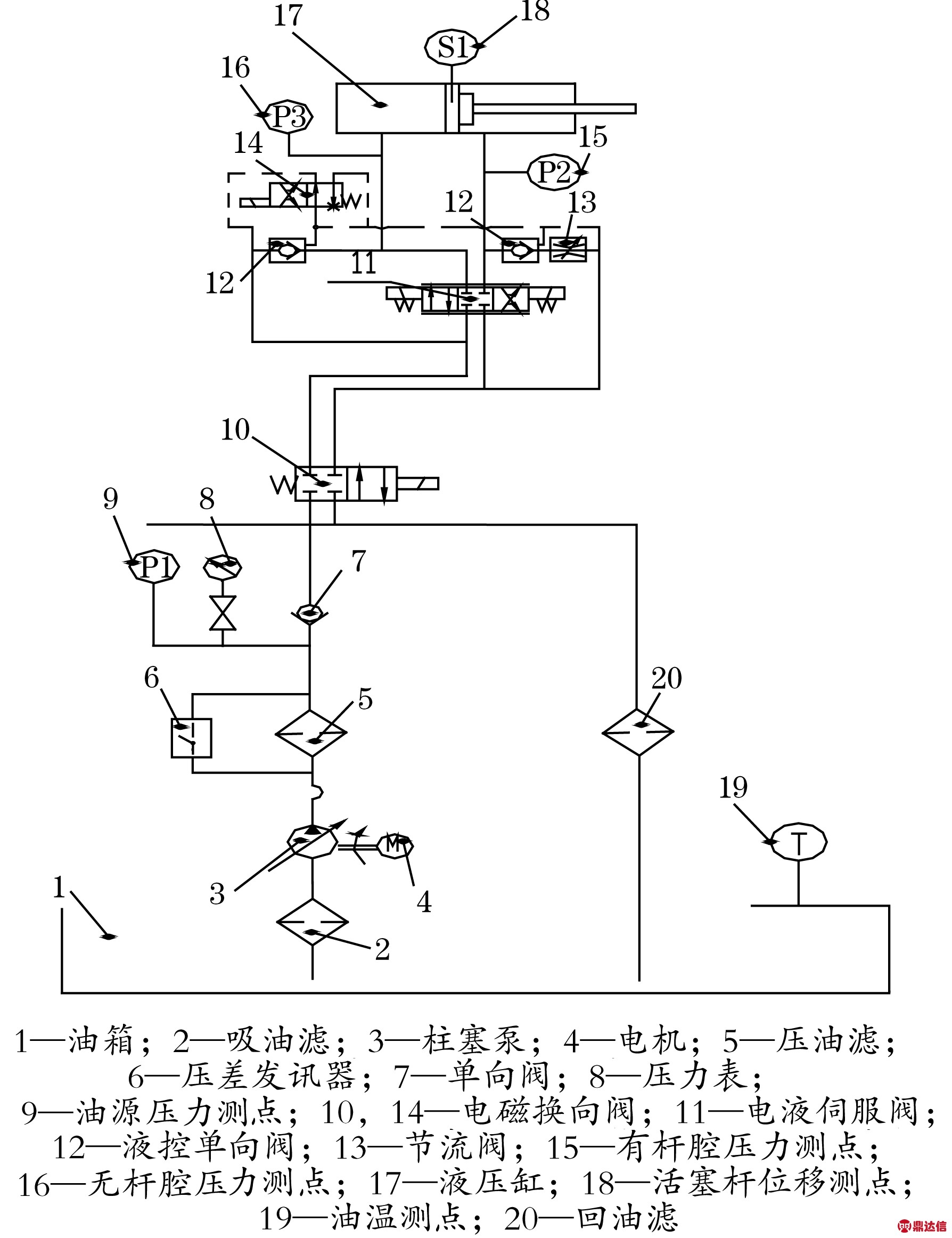
图1 液压系统元件及测点的布局图
此外,在调压阀出口的空气管路上布置4个压力测点,监测预充填压力参数。
2 运行环境参数的闭环控制原理
2.1 油温的闭环控制原理
为保证调压阀液压系统的正常运行,其液压油的温度应控制在15~40 ℃的范围内。当油温超出规定范围,会对液压系统的机械特性、密封特性带来巨大的影响,危及系统的可靠运行。因此,在实时监测油温,并对超温运行的液压系统进行实时报警的同时,还需要采取措施对液压油实施降温冷却。为此,基于油温闭环控制原理,通过对油冷机的开关控制实现对油温的闭环控制。
如图2所示,在测控计算机中,提前设定好油冷机启动和关机温度,当监测的油温高于设定的启动温度40 ℃后,经过闭环控制算法处理,计算机发出开指令信号至驱动电路板,驱动电路板再将驱动指令信号发送给油冷机控制器,触发油冷机启动运行;反之,当油温低于关机温度15 ℃后,驱动指令由高电平变为低电平,油冷机关机。通过发送闭环控制指令给油冷机,触发控制其开关机,从而实现对油温参数的闭环控制。
2.2 预充填压力的闭环控制原理
为预防阀门内漏带来的预充填压力上升的问题,通过对预充填压力的远程闭环控制,将该运行参数控制在试验需要的、合理的、安全的范围内。为此,在3台常用调压阀的阀后空气管路上各安装1台高压排气电磁阀,通过远程闭环控制排气电磁阀工作,将内漏的多余空气排出管路。
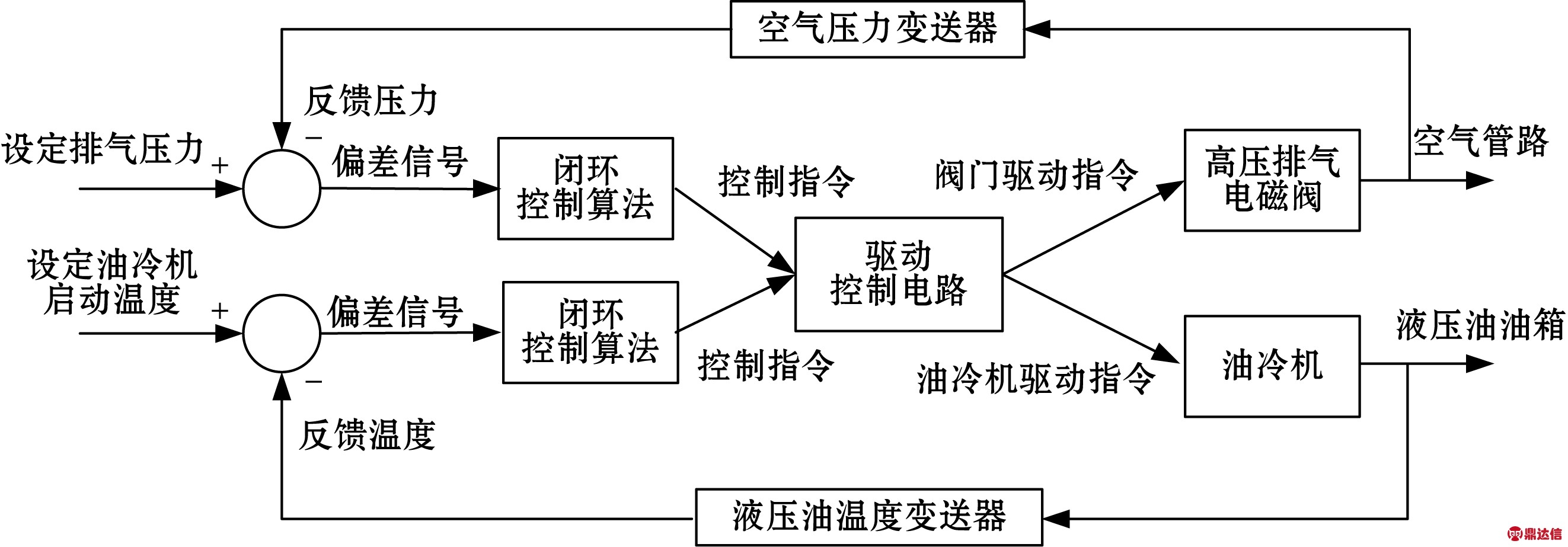
图2 油温和预充填压力的闭环控制原理图
如图2所示,空气管路上的压力变送器将实时采集的预充填压力值负反馈至计算机中,通过与设定的期望充填压力值比较生成偏差信号,通过闭环控制算法生成控制指令,控制指令再经过驱动控制电路生成最终的驱动指令,控制排气电磁阀的开启或关闭,实时、连续、自动地控制排气电磁阀的开关,将超压内漏空气自动排出,以保证预充填压力维持在设定的期望值附近。
3 系统的实现
3.1 硬件系统实现
硬件系统采用基于上、下位机的分布式结构,其结构图如图3所示。
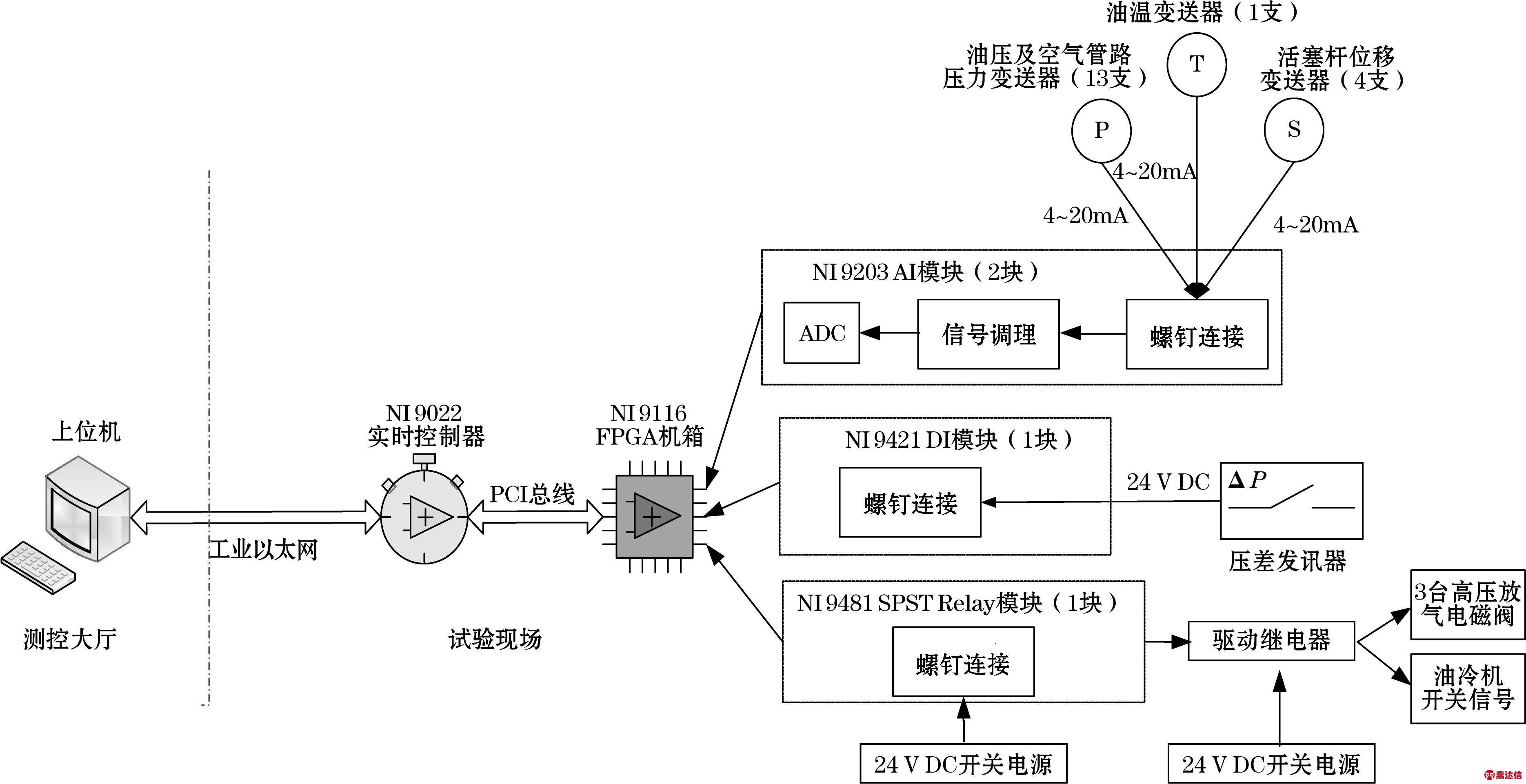
图3 硬件系统结构图
下位机系统位于试验现场,主要由传感器、执行机构和实时控制系统组成。传感器主要由压力(13支)、温度(1支)和位移(4支)变送器组成,输出4~20 mA标准信号。对于油液污染度的检测,当压油滤出口和入口压差超过0.35 MPa,压差发讯器发出24 V DC开关量信号。执行机构主要由1台油冷机和3台排气电磁阀组成。油冷机选用工业油冷机,制冷功率为25 kW,控制方式为温度固定型,在控制面板上设定温度控制范围,通过外部触发信号或现场手动信号控制油冷机工作。排气电磁阀为DN20 PN 35 MPa高压电磁阀。实时控制器系统采用NI CompactRIO系统,它是一款坚固耐用、可重配置的嵌入式控制系统,主要由3部分组成:实时控制器、可重配置的FPGA(现场可编程门阵列)机箱和工业级I/O模块。其中:实时控制器选用NI cRIO- 9022实时控制器,主频为533 MHz,VxWorks实时操作系统主要可靠准确地执行LabVIEW实时应用程序,完成闭环控制算法和控制信号的计算、采集的监测信号的计算和与上位机的通信。FPGA机箱选用8插槽NI 9116机箱,用于安装I/O模块,机箱中的FPGA直接和每个I/O模块相连,用来高速访问I/O电路。I/O模块主要用来对传感器信号进行隔离、转换以及信号调理,选用2块C系列9203 AI模块、1块9421 DI模块和1块9481 SPST Relay模块完成AI、DI和DO功能。
上位机系统位于测控大厅,由一台研华IPC610型工控机组成,主要完成控制指令的下发和监测参数的实时监测、显示、记录和报警等功能。
3.2 软件系统实现
系统的软件基于LabVIEW 2010软件平台开发,包括运行在FPGA上的FPGA.VI,运行在实时控制器上的RT.VI 及运行在上位机的Host.VI。通过工业以太网并基于TCP/IP协议的方式将实时控制器与上位机连接,从而在Windows 环境下进行上位机的开发设计。上位机需要安装LabVIEW软件、Real-Time 模块、FPGA 模块、NI-RIO 驱动软件等。
FPGA 与实时控制器(RT程序)的数据交换是数据采集的关键,在本设计中,采用扫描方式的FPGA编程模式,RT直接用I/O变量映射C模块的I/O,不需要编写专门的FPGA程序,由工具包自动编程实现,最高扫描频率为1 kHz。
RT程序开发主要分为3部分:通过读取I/O端口中的数据获取监测参数信号并将其送入队列;RT作为服务器与上位机通信,采用基于数据的生产者消费者模式将数据上传至上位机进行存储。实时控制器与上位机的通信采用TCP /IP 协议的方式进行通信,基于生产者消费者的TCP 队列模式实现同步控制及数据传输。上位机通过TCP/IP 协议将指令发送至实时控制器,实时控制器继而通过读/写控制函数将指令下发至FPGA.VI,实现数据采集的控制,而采集的数据写入队列再经TCP/IP 协议上传到上位机;实现空气压力和油温的闭环运算,通过实时采集值与下载至实时控制器的设定值的比较,确定NI 9481模块相应端口的0/1状态,从而形成控制指令。
上位机程序包含控制参数设置模块、通讯模块、数据显示与记录模块和报警模块。控制参数模块设定闭环控制的压力和温度参数值;通讯模块实现与下位机的通讯;数据显示记录模块的功能是对采集的各状态参数进行实时数据显示和数据记录;报警模块的功能是对液压油油温和油液污染度进行超标报警,其中:油温超过40 ℃油温报警,压油滤前后压差超过0.35 MPa,油液污染度信号报警。采用事件驱动的模式完成程序主体结构的设计。
4 测试结果
图4给出了DN40调压阀液压缸油源、有杆腔、无杆腔压力曲线。图5给出了DN40调压阀开度监测曲线。

图4 DN40调压阀液压缸压力监测曲线
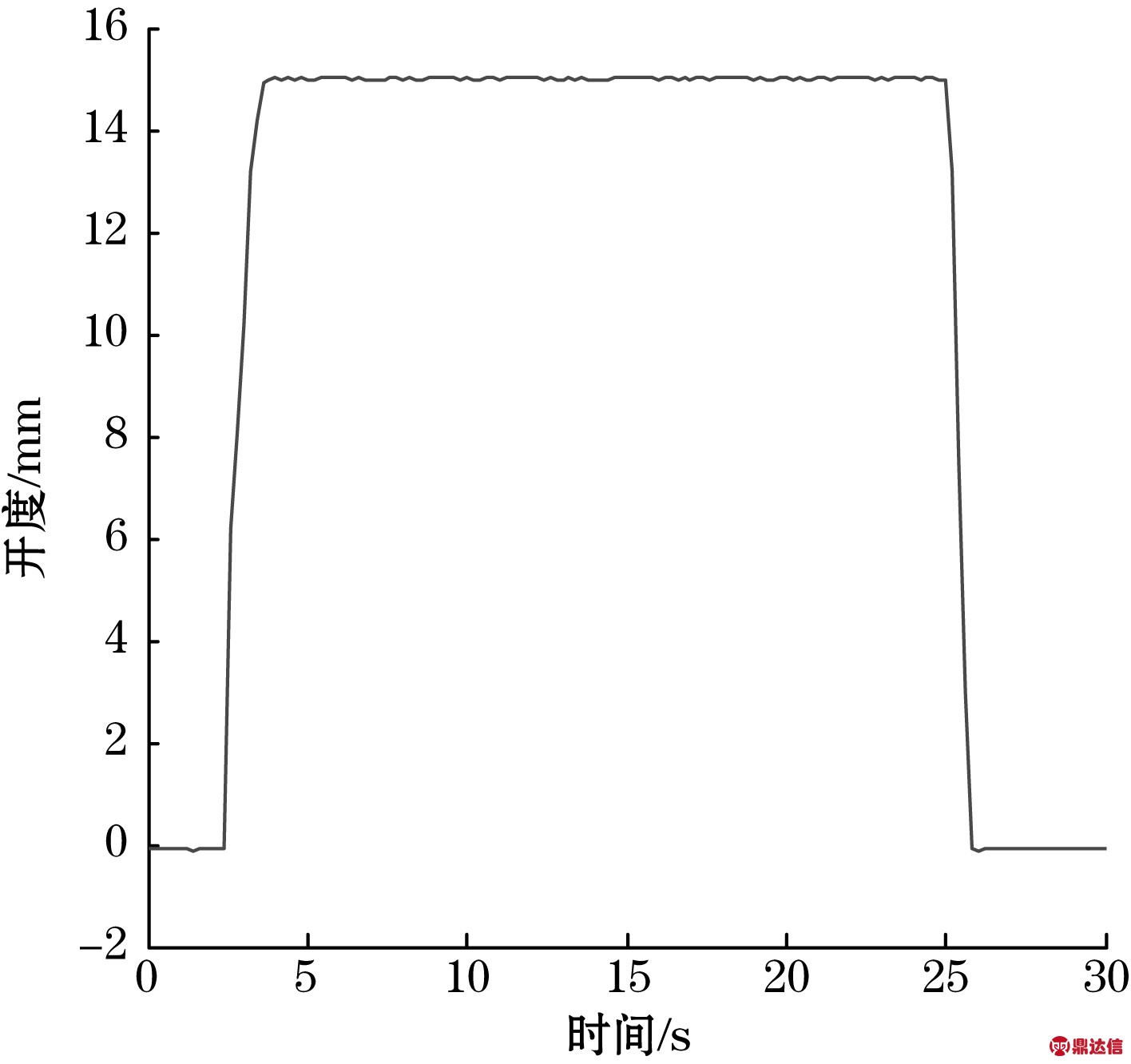
图5 DN40调压阀开度监测曲线
从图4、图5可以看出,调压阀关闭时,液压缸无杆腔压力与总油源压力基本相等,为16 MPa左右,有杆腔压力为0 MPa,活塞杆开度信号为0 mm。开阀时,有杆腔压力快速上升,无杆腔压力快速下降,有杆腔的压力大于无杆腔的压力,活塞杆上升,带动调压阀阀杆上升,活塞杆开度信号快速提升至15 mm,此后,开度信号、有杆腔、无杆腔压力信号稳定,这一过程,液压系统做功产生热量,油温略微上升。调压阀开度稳定后,有杆腔与无杆腔的压比与理论值D2/( D2-d2)=2.07(液压缸缸径D=50 mm,活塞杆杆径d=36 mm)也基本一致。由此,验证了运行环境参数监测的正确性。
图6给出了液压油油温降温监测曲线。从图6可看出,当油温高于40 ℃后,油冷机启动运行,开始快速降温,至15 ℃停止,通过监控系统和油冷机对油温的实时监控,保证了油温处于正常使用的范围内,验证了油温闭环控制系统设计的正确性。
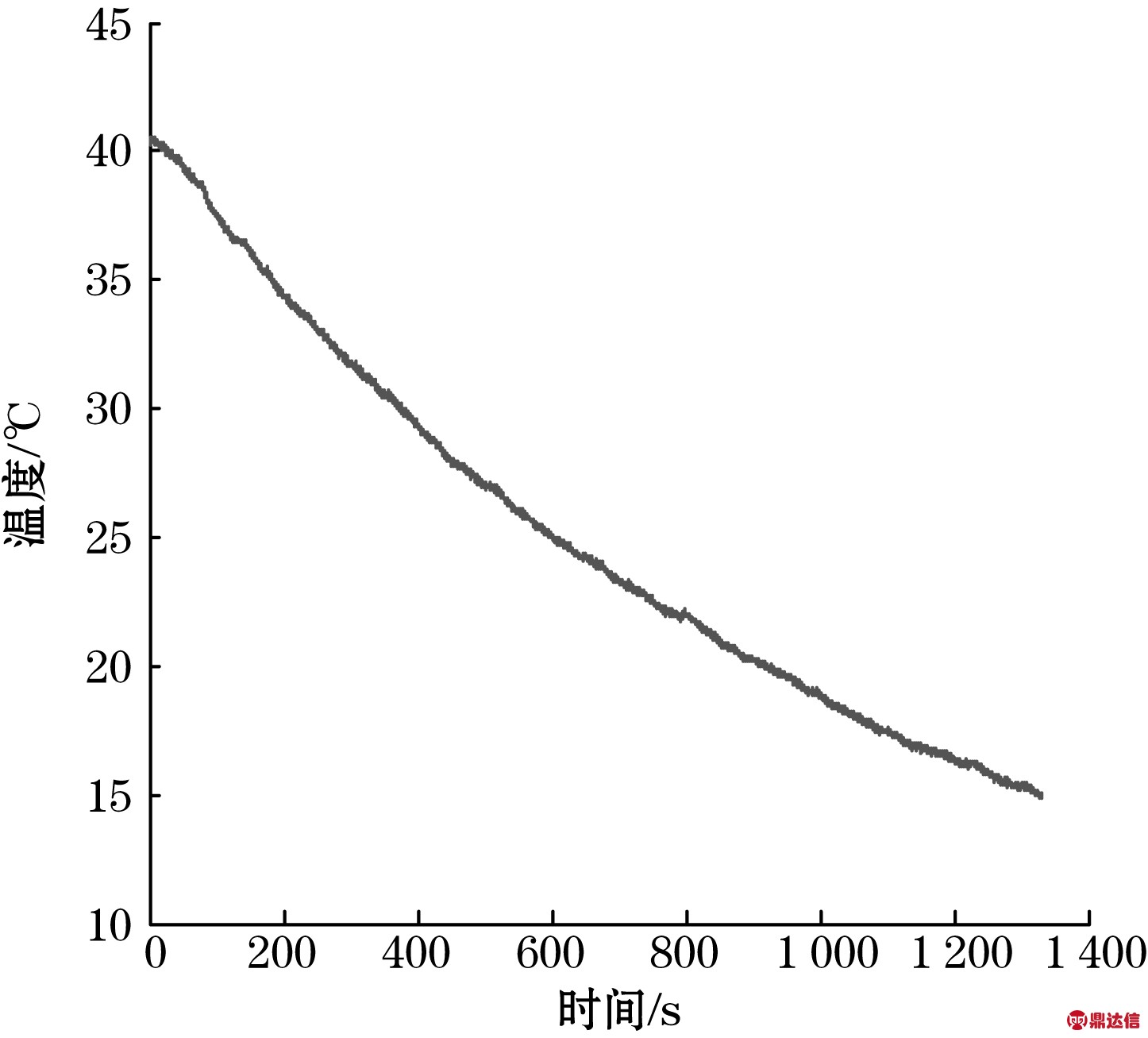
图6 液压油油温降温监测曲线
图7给出了DN100调压阀某次内漏时,自动排气与调压过程的压力监测曲线。通过曲线可以看出,空气管路预充填完毕,压力达到期望值后,由于阀门内漏,压力值继续缓慢上升。开启自动排气后,压力下降并一直稳定维持在设定的期望值附近,直至调压阀进入调压阶段,从而验证了预充填压力闭环控制系统的可靠性和实用性。
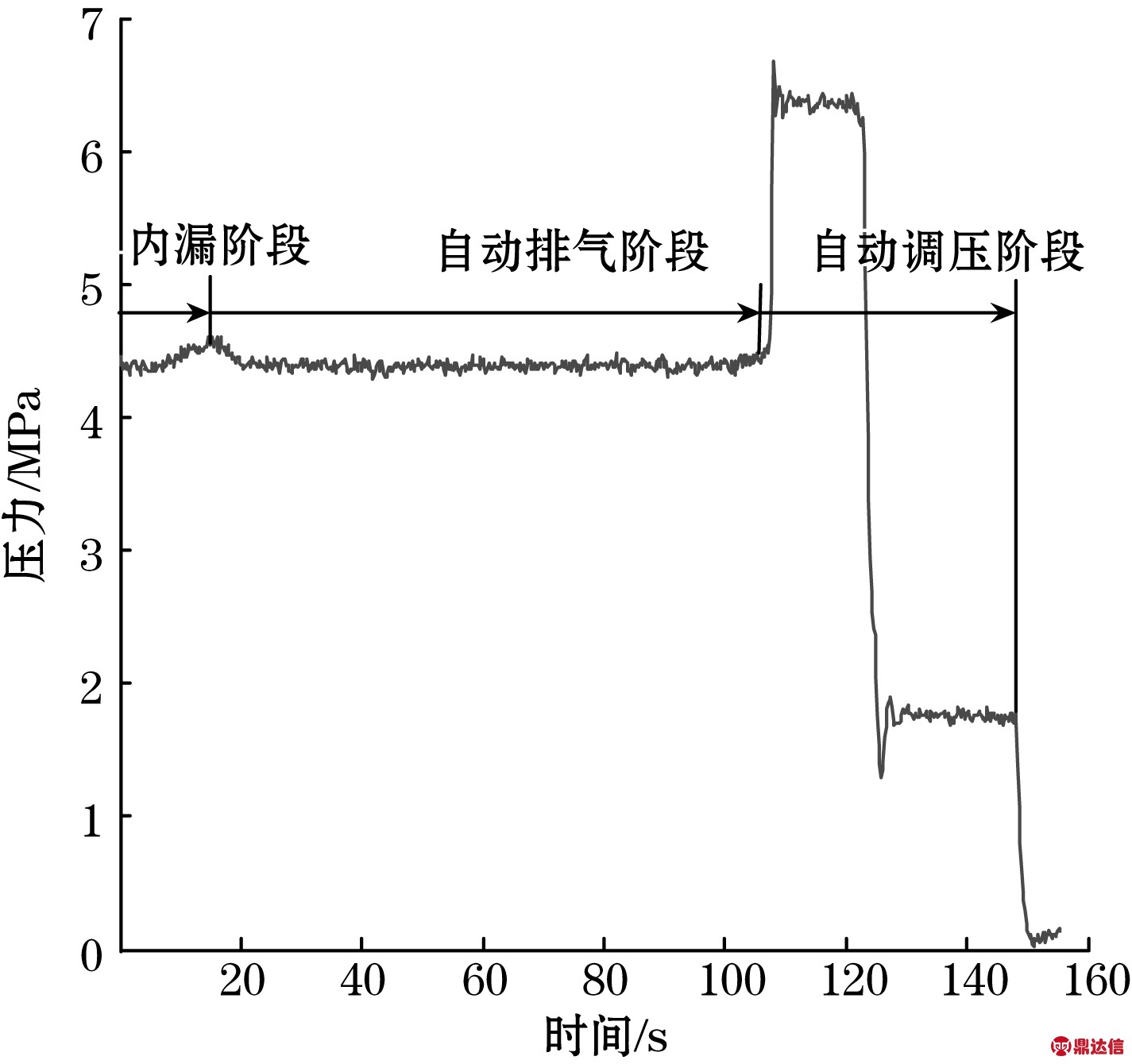
图7 调压阀自动排气与调压过程压力监测曲线
5 结论
基于工业以太网和分布式控制系统开发了调压阀运行环境参数的监控系统,可以全面、准确地监测和控制其液压及工艺运行环境参数。通过测试结果看出,监测结果与理论计算一致,符合调压阀的实际运行状况,验证了该系统的正确性和有效性。该系统为掌握调压阀的运行状态,保证其安全、可靠运行提供了有力支撑。