摘 要:随着石油开采进入中后期,油井含水率逐渐增加,井下油水分离系统的研究变得越发重要,油水分离器是井下油水分离系统的核心所在,对其进行设计研究对石油开采工程有着积极作用。文章结合水力旋流原理及超亲水油水分离膜材料,对常规液-液水力旋流器进行结构改造,提出基于膜分离的井下油水分离器方案,并完成了相关尺寸设计计算,同时建立相关模型进行仿真分析,通过与常规旋流器的内部速度场、压力场、油水分布规律进行对比以及相关样机实验与仿真结果的对比分析验证了该方案的可行性。
关键词:油水分离器;结构改造;尺寸设计;仿真分析;样机试验
0 引言
随着国内各大油田开采进入中后期,油井采出液含水率逐渐增高,这不仅会导致油田生产成本提高,生产效益变差,而且若废水处理不当也可能造成环境污染。井下油水分离技术可有效解决上述问题,按分离原理可将其分为重力分离、离心分离和膜分离,就目前井下油水分离系统而言,应用较广的是以有杆泵与井筒重力沉降分离组合系统为代表的重力分离与以井下电潜泵和水力旋流器组合系统为代表的离心分离[1]。
旋流式油水分离器虽然有着体积较小、结构紧凑、分离效率高、物流停留时间短等优势但对含水率、粘度等操作参数敏感,若参数出现较大波动或无法准确实时监测,则井下旋流分离器稳定性将难以得到保障。另外,其适应性也受到限制,水力旋流器多用于含水率大于90%的产液中,若应用于含水率较低的油井则分离效率低下;重力式井下油水分离系统虽然能耗低,分离效率高,但由于其单位时间分离量限制,因此只适用于产量较低的油井[2];膜分离技术虽然具有分离效率高、能耗低、操作简单、无化学变化等特性[3],但由于存在膜污染、膜堵塞等问题,使其在各领域的应用也受到了限制。
当前井下油水分离系统研究重点主要集中在分离器的结构设计、串联增效、并联增量、结构优化、流场分析及注采系统的设计等方面,极少以改变分离机理为出发点。针对上诉问题,文章结合水力旋流原理及超亲水油水分离膜材料,对常规液-液水力旋流器进行结构改造,提出基于膜分离的井下油水分离器方案,并建立相关模型进行了仿真,通过与常规旋流器的内部流场分布规律进行对比分析以及相关样机实验验证了该方案的可行性。
1 油水膜分离器设计
以常规液-液旋流分离器经典结构为基础,进行相关尺寸设计,并把圆锥段器壁改为超亲水/超疏油分离膜材料,使其形成多孔介质错流过滤机理。
1.1 错流过滤机理
错流过滤技术是利用膜多孔的结构,通过原料液的错流冲刷和膜管内外形成的压力差实现过滤目的的[4],图1 示出错流过滤过程。
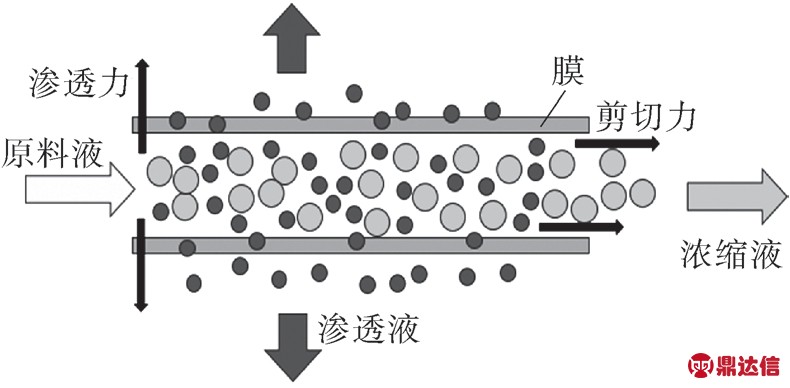
图1 错流过滤过程示意
在错流过滤过程中,水流在多孔介质表面形成2 个分力,一个是垂直于膜面的法向渗透力,另一个是平行于多孔介质表面的剪切力,该剪切力会对截留滤饼产生一定的冲刷作用,使得多孔过滤介质不易发生结垢和浓差极化现象。
1.2 分离器单元结构尺寸设计
根据标准的水力旋流器,按其相似准则和几何尺寸比例关系,进行计算和比例放大。即依照设计参数处理量Qi、压降Δ P 等要求选择合适的旋流器,再利用相似准数关系和一定尺寸比例关系完成设计计算[5]。具体尺寸注释如图2 所示。
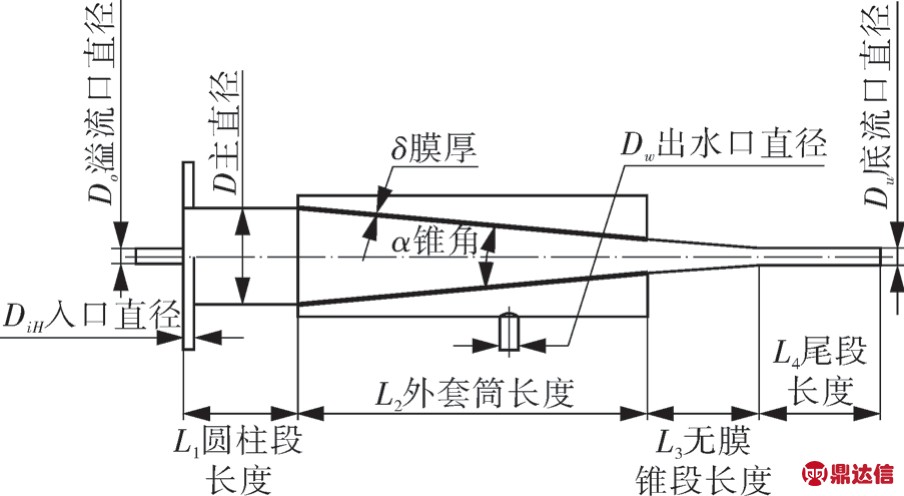
图2 膜分离器参数注释示意
1.2.1 分离器单元主直径
通常情况下,因井下空间限制,旋流器径向尺寸一般不超过50 mm[6],分离器单元主直径选定为:D=40 mm,综合各类经典尺寸,选定锥角为: α=10°,L2=150 mm。
由尺寸关系推出分离器单元中亲水膜有效面积Sm 为:
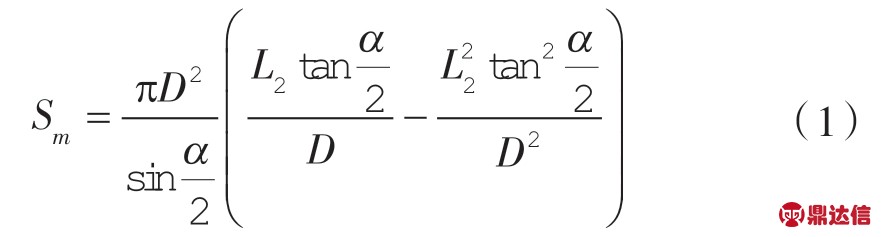
经计算,膜锥筒有效面积:Sm=127.07 cm2;所选膜由试验测得平均水通量98.52 L/(min·m2),膜通量试验测定的平均液柱高度为60 mm,换算成压力约为587 Pa,为了初步预估该膜在工具中的实际水通量,根据文献[7]:
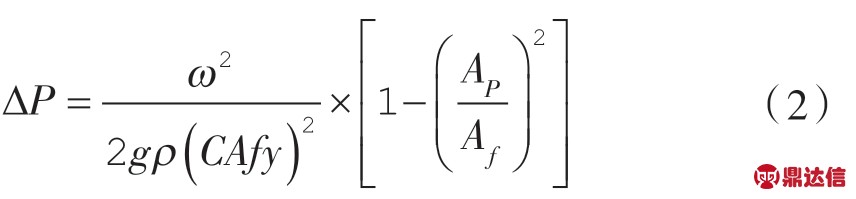
式中 ω ——质量流率,kg/s;
C ——微孔系数,无因次;
Af ——液体有效流通面积,m2;
Ap ——液体流通面积,m2;
y ——膨胀因子,无因次。
令
则,Δ P=K ω2 初步选定工具使用中实际压差Δ P=0.05 MPa,根据式(3)关系可以初步预算出所选膜在0.05 MPa 时的实际通量为:

即膜锥筒有效水通量约为11.43 L/min,因此,在设计过程中要保证水通量低于11.43 L/min。
1.2.2 分离器单元处理量
初设分离器单元处理量Qi=10 L/min,以70%的除水分离效率为设定目标,即水通量:

式中 φ ——含水率,%;
η ——除水分离效率,%。
取含水率φ为90%,经计算得:Qw=6.3 L/min,远低于预估值11.43 L/min,满足设计要求。
1.2.3 进口直径
常规液-液旋流分离器进口速度一般为5~15 m/s[8],选用平均入口速度为:Vi=8.5 m/s,则:
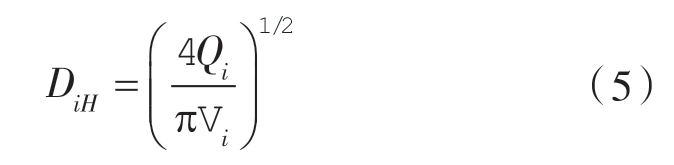
经计算,当量入口直径DiH ≈4.9978 mm,取整后,DiH=5 mm。
1.2.4 溢流口直径
综合各类经典旋流器尺寸比例关系,由于需要较大的溢流分流比,取溢流口直径略大于入口直径,为Do=6 mm。
1.2.5 底流口直径
由于绝大部分水相从膜锥壁渗透流出,底流口流率较小,因此,在常规底流口尺寸比例(Du/D ≈0.25~0.33)下适当减小底流口直径,取Du/D= 0.15,即底流口直径为Du=6 mm。
1.2.6 圆柱筒长度
圆柱筒长度经典尺寸比例L1/D=1.0,但在此结构中,为了混合相能在圆柱段形成较充分发展且稳定的旋流,适当增长圆柱筒长度,取L1/D=1.25,即圆柱段长度:L1=50 mm。
1.2.7 膜材料选择
参照文献[9]的方法,进行了相关膜筛选试验,通过对比结果试验最终旋转的膜材料性质 如下:
超亲水/疏油膜,纸质纤维材料,水通量极大,截油性能优越,截油压力高达0.5 MPa,耐压、耐温、耐腐蚀。
1.2.8 其它尺寸选取
为了水相能尽快从出水口流出,取出水口直径大于底流口直径,为Dw=8 mm;膜的厚度测量得到δ=1 mm;取底流管长度L4=50 mm。
1.3 工作原理
如图3 所示,油水混合相通过进液流道经过切向进液口高速射入圆柱筒,在圆柱筒中形成高速圆柱旋流场,由于油水两相存在密度差,油水两相产生离心沉降分层,水富集层分布在外层紧贴筒壁,油富集层分布在内层轴心。同时,由于直径变小,离心作用力增大,混合相进一步离心沉降分层。此时,外层水相直接接触筒壁的超亲水/疏油分离膜材料,由于分离网膜材料具有过水截油性能且不锈钢网锥筒支撑体上设置有密布孔a,水相可透过分离膜流入外筒,从出水口排出至注水流道。同时,内层油相富集形成油核经过溢流口排出至举升流道,底流口较低浓度的混合液同样经过底流管排出至举升流道,至此实现了比常规液-液旋流器更高精度的油水分离。
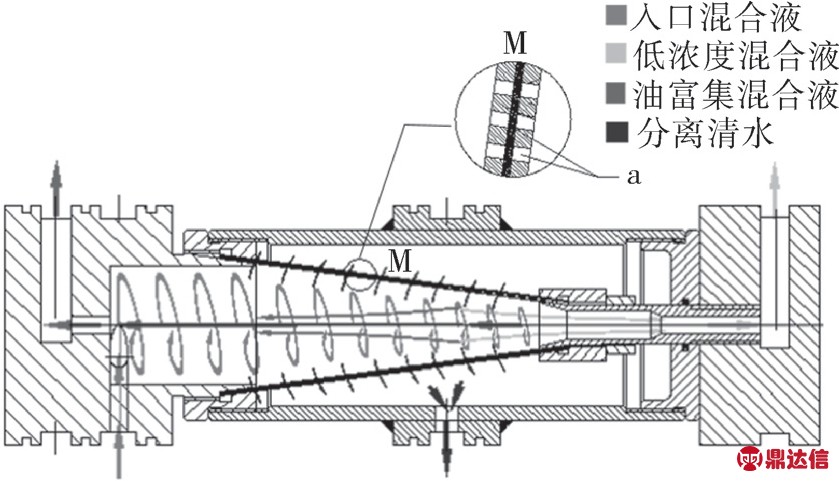
图3 油水分离器单元工作原理示意
1.4 入口最优速度区间确定
入口切向速度的大小代表着内部旋流的强度,切向速度越大分离性能越好,但过大的切向速度会产生过大的剪切应力使油滴破碎乳化,不利于分离[12]。为了确定所设计的井下油水膜分离器分离性能的最佳入口速度,保证其它参数相同前提下,采用不同入口速度(不同入口流量: 6~14 L/min,跨度:1 L/min)进行了试验结果如图4 所示。
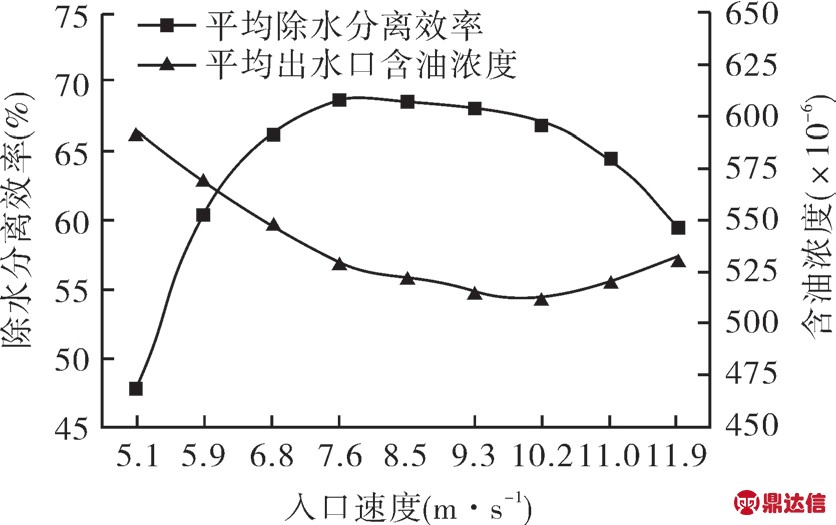
图4 油水分离器单元工作原理示意
由图可知,分离器除水分离效率随着入口速度的增加先快速增大,然后相对保持平稳,最后快速减小,除水分离效率最高点速度在7.6m/s 左右;出水口含油浓度随着入口速度的增加先快速降低,然后相对稳定,最后缓慢上升,出水口含油浓度最低点速度约为10.2 m/s。综合分析,最佳入口速度在7~10 m/s 之间,即最佳处理量区间为8~12 L/min。
2 流场仿真前处理
为了区分方便,下文中对基于膜分离的旋流分离器和常规液-液单锥水力旋流器分别以英文缩写代号CSBOMS(Cyclone Separator based On Membrane Separation)与CSCCS(Conventional Single Cone Cyclone Separator)表示。
2.1 流体域模型网格划分
采用O 形分块结构化六面体网格,网格尺寸大小设置为2 mm,对进口和溢流口进行局部加密,最终分离器单元模型网格划分如图5(a)所示,所得网格单元数量为394 758,最小网格质量为0.493。常规液-液旋流分离器模型网格生成如图5(b)所示,网格单元数为193 572,最小网格质量为0.652。
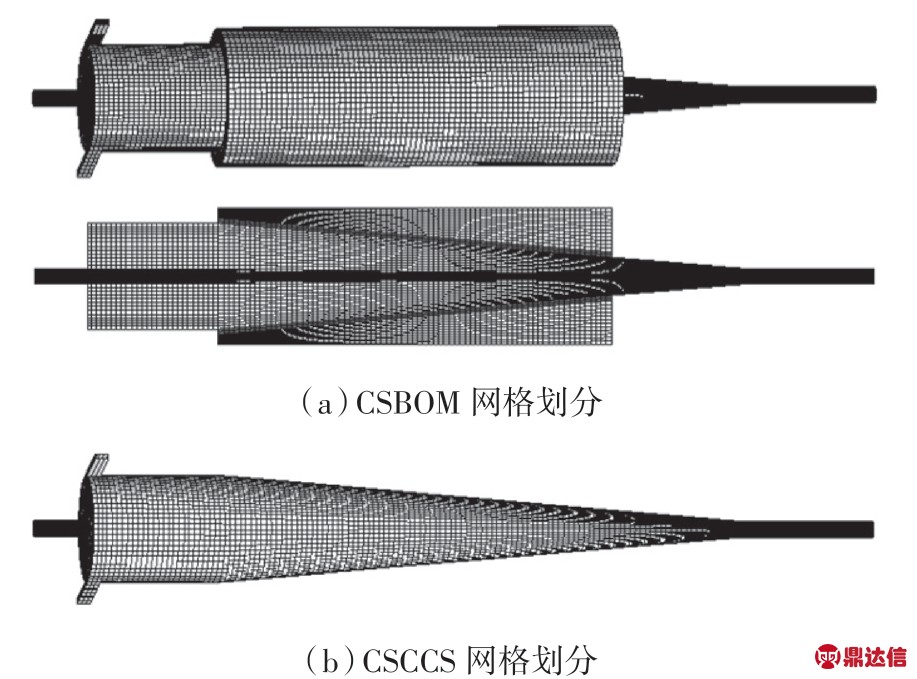
图5 网格划分示意
2.2 模型和参数设置
相关边界条件、模型选择、初始条件、求解器选择、求解参数等选择如表1 所示。
表1 数值模拟参数汇总
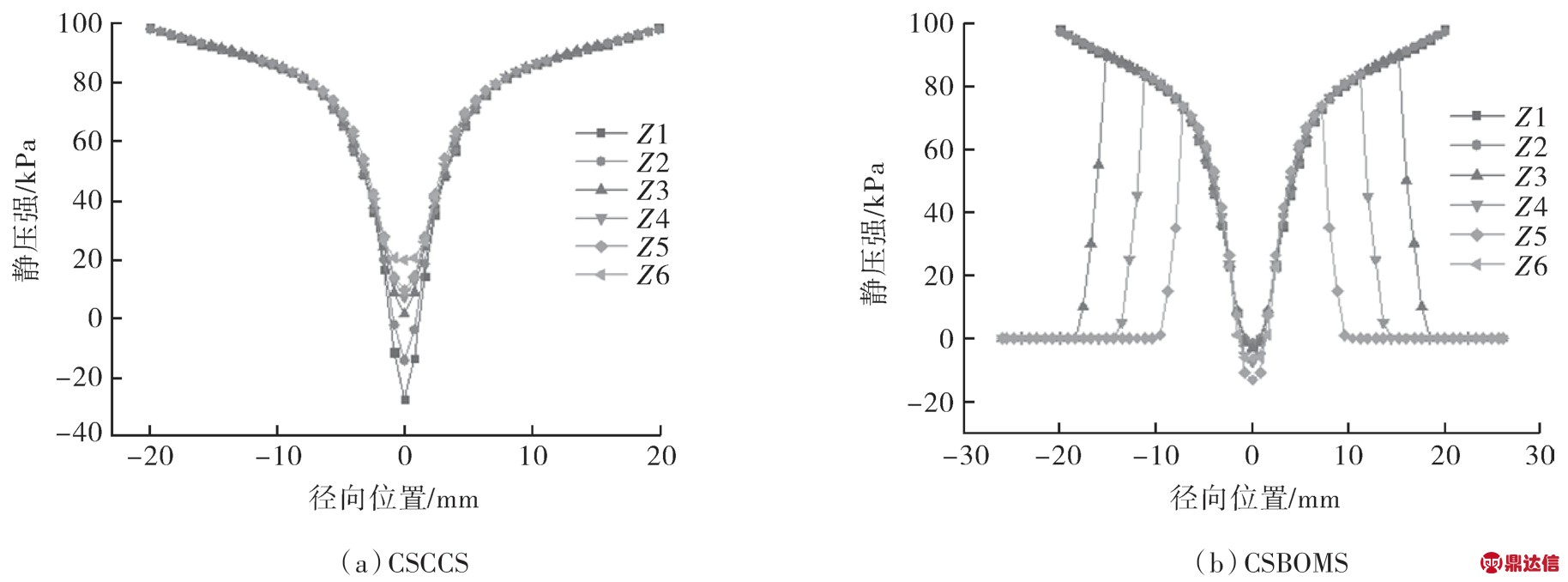
此外,为了清晰地描述分离器内部流场分布特点,特定义几个流场横截面,各横截面具体位置如图6 所示。
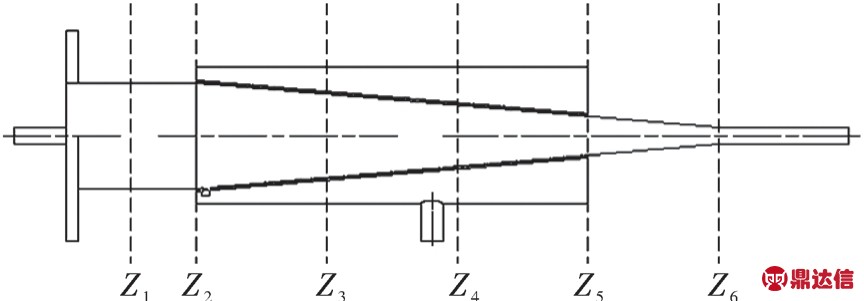
图6 旋流器截面示意
3 内部流场对比分析
3.1 速度场对比
旋流器内部速度场分布规律决定着旋流器分离性的优劣,由于流体在旋流器内作螺旋流动,因而把旋流器速度矢量分解为切向速度,轴向速度与径向速度,切向速度代表旋流强度,轴向速度关系液体停留时间,因此文章主要对二者的切向速度和轴向速度进行了对比分析,后期处理中,规定溢流口轴向速度方向为正。
3.1.1 切向速度对比
切向速度的大小代表着内部旋流的强度, 切向影响着分离性能,因此,对旋流器内部切向 速度场的定性及定量分析对旋流器的研究有着 重要意义。
如图7(a),CSCCS 切向速度分布规律为:切向速度整体呈对称分布,速度大小随径向位置的增大而增大,在接近壁面时快速下降至零,在轴心位置切向速度也为零,相同径向位置,切向速度大小随轴向位置的下降,在摩擦剪切阻力作用下缓慢变小,但由于锥体截面面积的缓慢减小,能抵消流体角速度的损耗,使旋流场相对稳定;观察图8(a),切向速度变化可由速度最高点分为两段:外层快速上升段和内层快速下降段,以最高分界点径向位置为分界可把流场分为外旋流(准自由涡)和内旋流(强制涡),这也符合历年来多数学者得出的旋流器切向速度分布规律。如7(b),CSBOMS 切向速度分布云图与CSCCS 总体规律相似,均呈对称分布,观察图8(b),最大切向速度位置和大小也相近,均在Z1 截面附近,大小接近8.5 m/s,这与入口速度8.5 m/s 相吻合,对比图8(a),与CSCCS 不同的是,CSBOMS 在多孔介质锥段内,其切向速度的最大值向旋流器壁面处移动,切向速度也随着轴向减小,这是由于流体进入多孔介质锥段时,近壁层大部分水相直接渗透通过多孔介质层,使锥筒内近壁层流体能量大幅衰减,因此切向速度下降。切向速度是决定分离器分离性能的最重要因素之一,通过对比得知,基于膜分离的旋流分离器切向速度分布与常规旋流器分布规律相似,因此能实现旋流腔内油水离心分层。
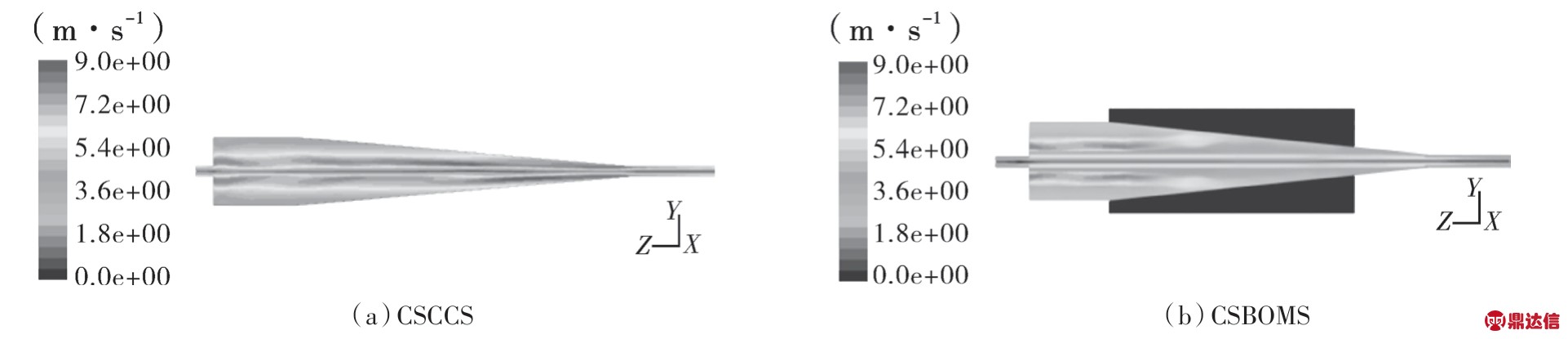
图7 旋流器切向速度分布云图
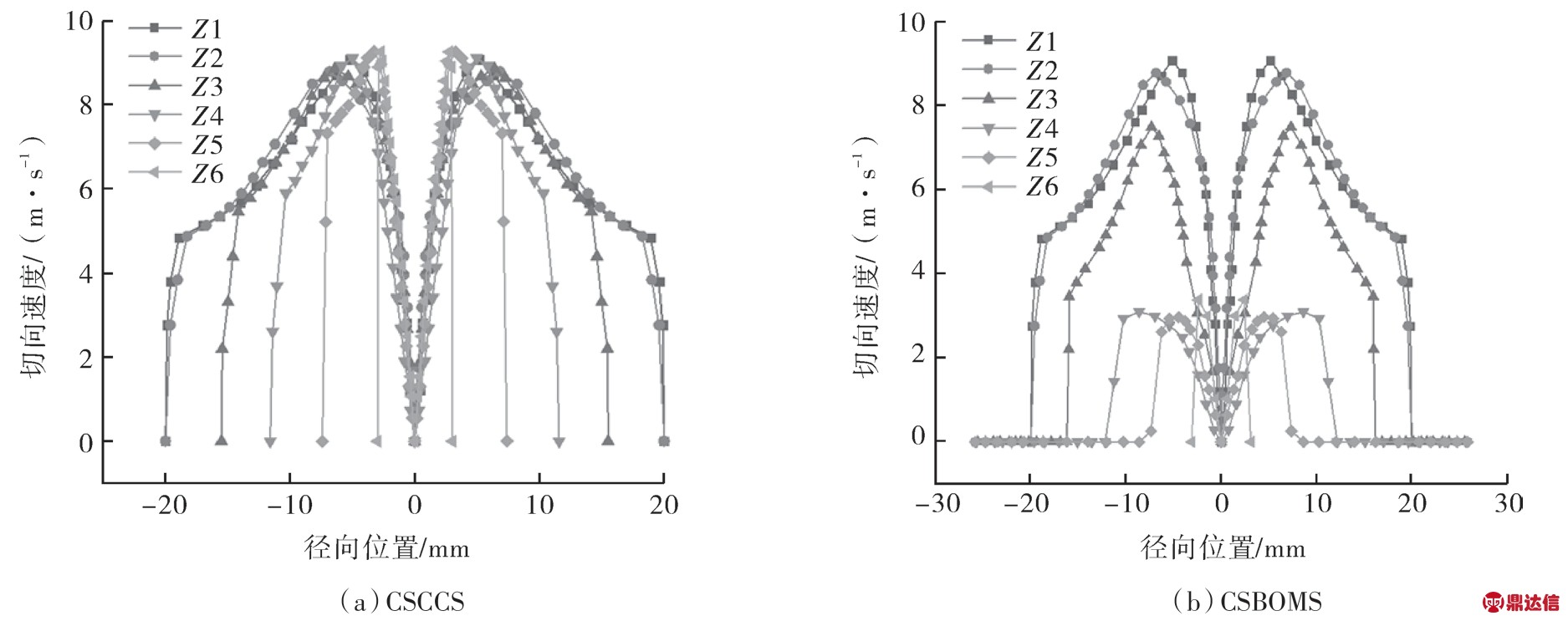
图8 不同截面切向速度曲线
3.1.2 轴向速度分布规律对比
旋流器内部轴向速度大小决定了混合液在内筒中的停留时间,停留时间越久分离越充分,所以研究旋流器轴向分布规律有一定工程实际意义。
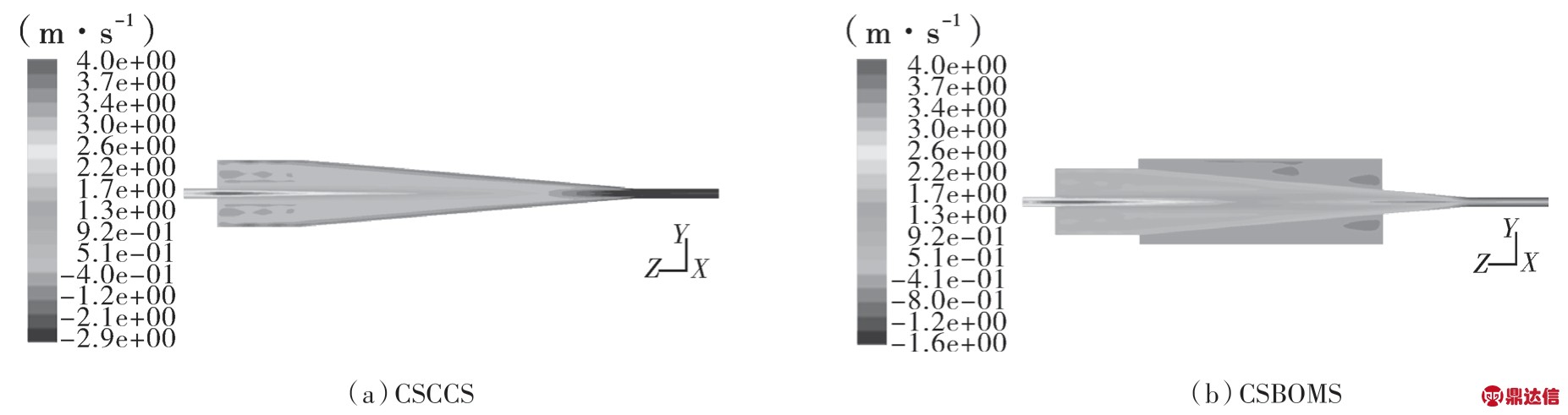
图9 旋流器轴向速度分布云图
由图9(a)可知,CSCCS 轴向速度呈轴对称分布,大小从近壁面随径向位置的减小而增大,方向由负变为正(Z 轴正向),在零点径向位置形成零轴向速度包络面,零速度包络面外层流体轴向速度向下,为朝下的外旋流,零速度包络面内轴向速度朝上,形成朝上的内旋流,轴心处的轴向速度最大。由图9(b)可知,CSBOMS 轴向速度分布云图与CSCCS 规律近似,主要区别是尾管段轴向速度值较小,是由于大部分水相通过多孔介质层进入了外筒,降低了底流口的流量,因此底流口速度值大大降低。对比图10(a)(b)可以看出,CSBOMS 在锥段截面处(Z3 与Z4 截面)向下的轴向速度值较常规分离器小,同样由于大部分水相通过锥壁流入外筒所致,且轴向零速度点较高,在Z5 截面轴向位置附近,而CSCCS 轴向零速度点靠近Z6 截面。
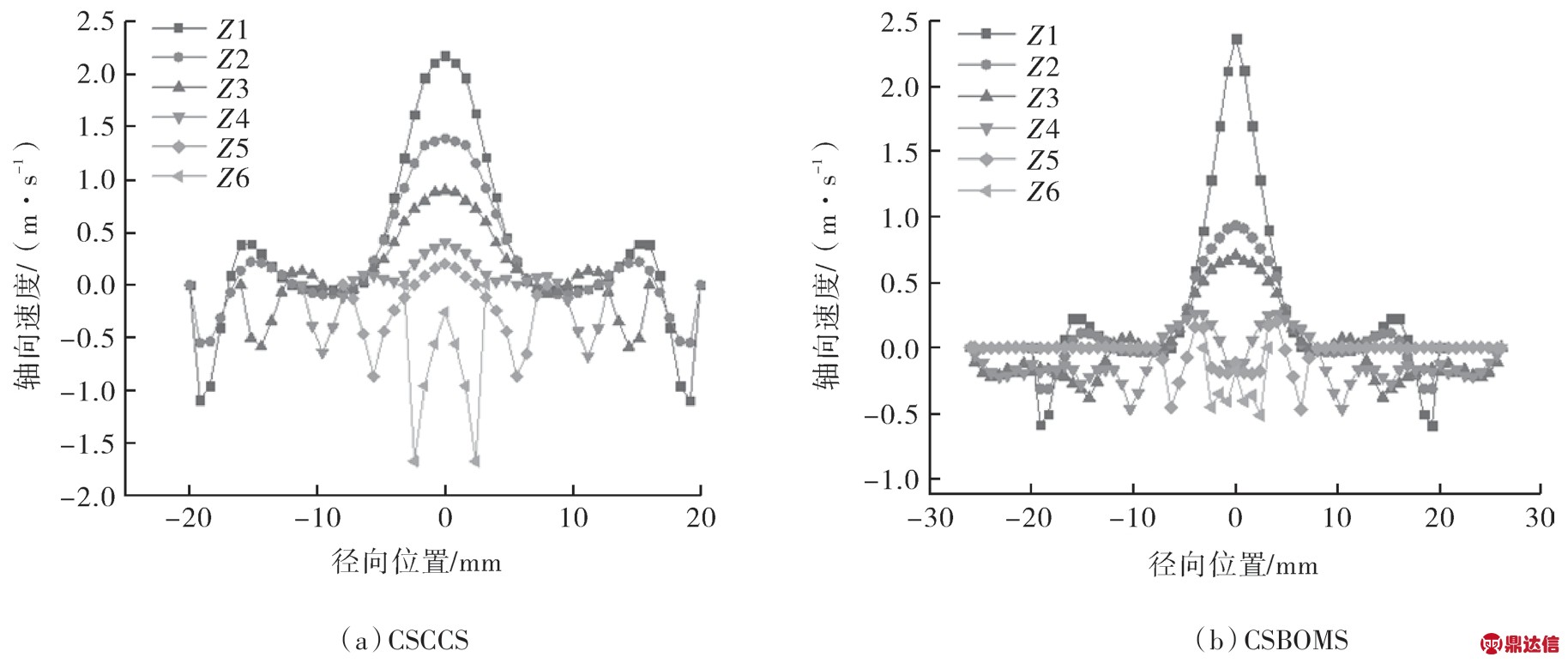
图10 不同截面轴向速度曲线
3.2 压力场对比
旋流器的压降是衡量旋流器能耗指标的重要参数[11],而静压场分布场特征很大程度上关系着分离器的分离性能,因此研究旋流器内部压力分布规律有其重要意义。如图11 示出CSCCS与CSBOMS 静压分布云图,图12 示出CSCCS 与CSBOMS 不同截面静压变化曲线图。
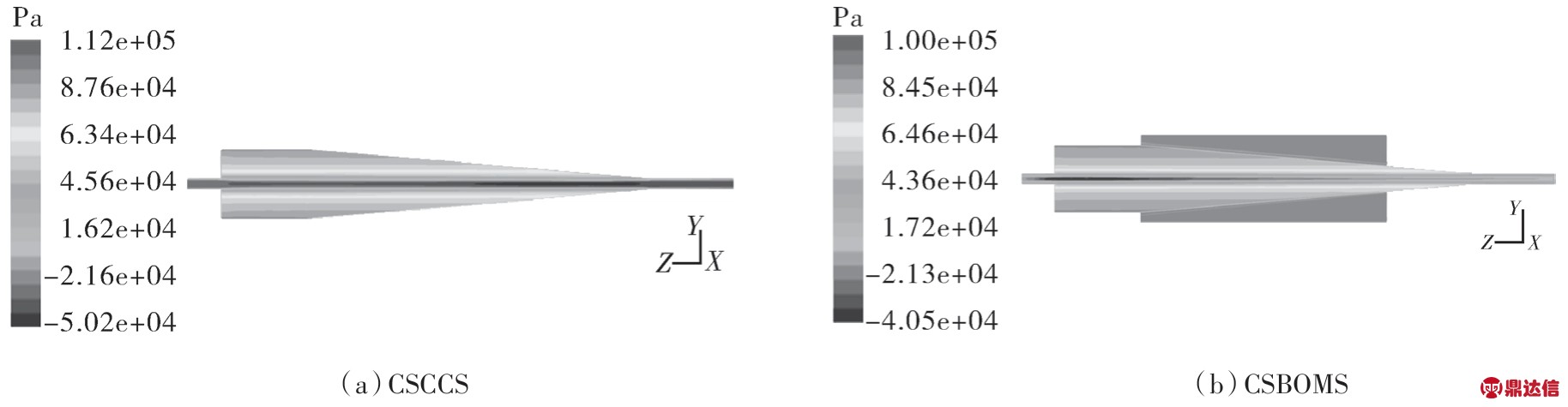
图11 静压云图
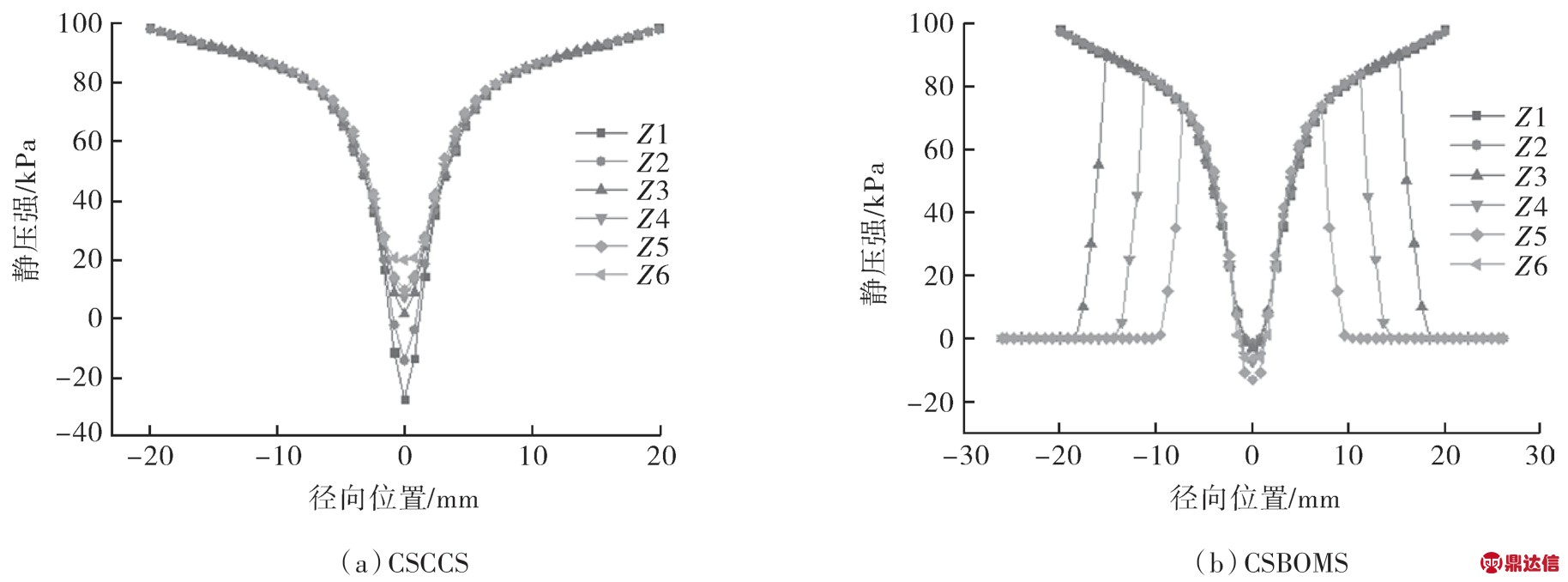
图12 不同截面静压曲线
由图11 和12 可以看出,CSBOMS 内部流域静压力分布规律与CSCCS 基本相同,总体呈对称分布,随着径向位置的减小,压力逐渐变小,在轴心出形成负压,且在靠近溢流口处轴心位置静压强最低。对比分析图11(a)与(b),CSBOMS 轴心负压半径较小,一定程度上可能会导致油相聚集半径较CSCCS 大(后文如图13 所示);观察图12(b),由Z3,Z4,Z5 截面静压变化曲线规律可知,液体在流过多孔介质膜后静压强发生突变,快速下降至零。
3.3 油水分布对比
旋流器内部油相体积分数分布规律是旋流器分离性能最重要直观指标,它直观的反映了分离器内部油相聚集程度,油相聚集半径,上下出口油相浓度指标等重要指标,因此,研究旋流器的分离性能,必须要分析旋流器内部油相分布规律。
由图13(a)可知,CSCCS 内部油相聚集非常集中,油相体积分数最大值为1,最小值接近零,且在圆锥段油核半径非常小,分布稳定对称,在尾管段整体呈深蓝色,说明底流口油相浓度低,油相主要通过溢流口流出,说明CSCCS 分离性能好。观察图13(b),CSBOMS 内同样形成了红色油核,但油相聚集程度较低,油相聚集半径较常规旋流器大,且在尾管段也有较高的油相分数,但在锥段多孔介质内壁面同样形成了深蓝色水富集层,使得水富集层直接接触油水分离膜多孔介质,水相透过分离膜锥筒后在外筒呈深蓝色,说明膜分离分离性能好。
观察图14(a)可知,CSCCS 从Z2~Z6 不同截面的油相分布规律基本相同,说明常规旋流器流场较稳定,而从图14(b)可知,CSBOMS 在不同的截面上油相分布规律不同,说明膜分离由于锥段水相流出多孔介质层的能量损失造成流场波动,使轴心油相聚集不够稳定,这与前文膜分离旋流器速度场及压力场分析结论相吻合。
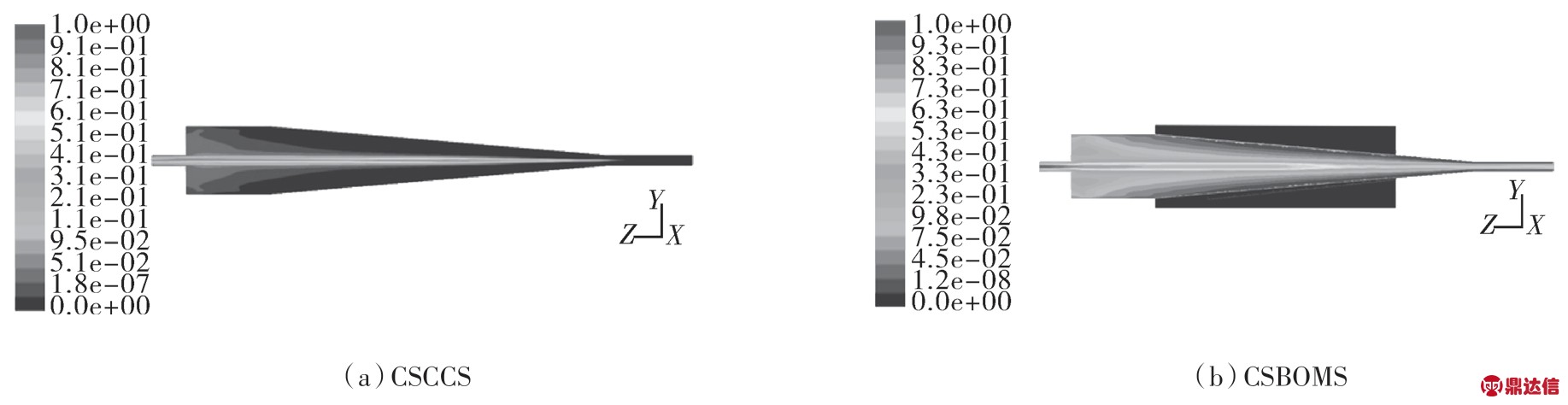
图13 油相体积分数云图
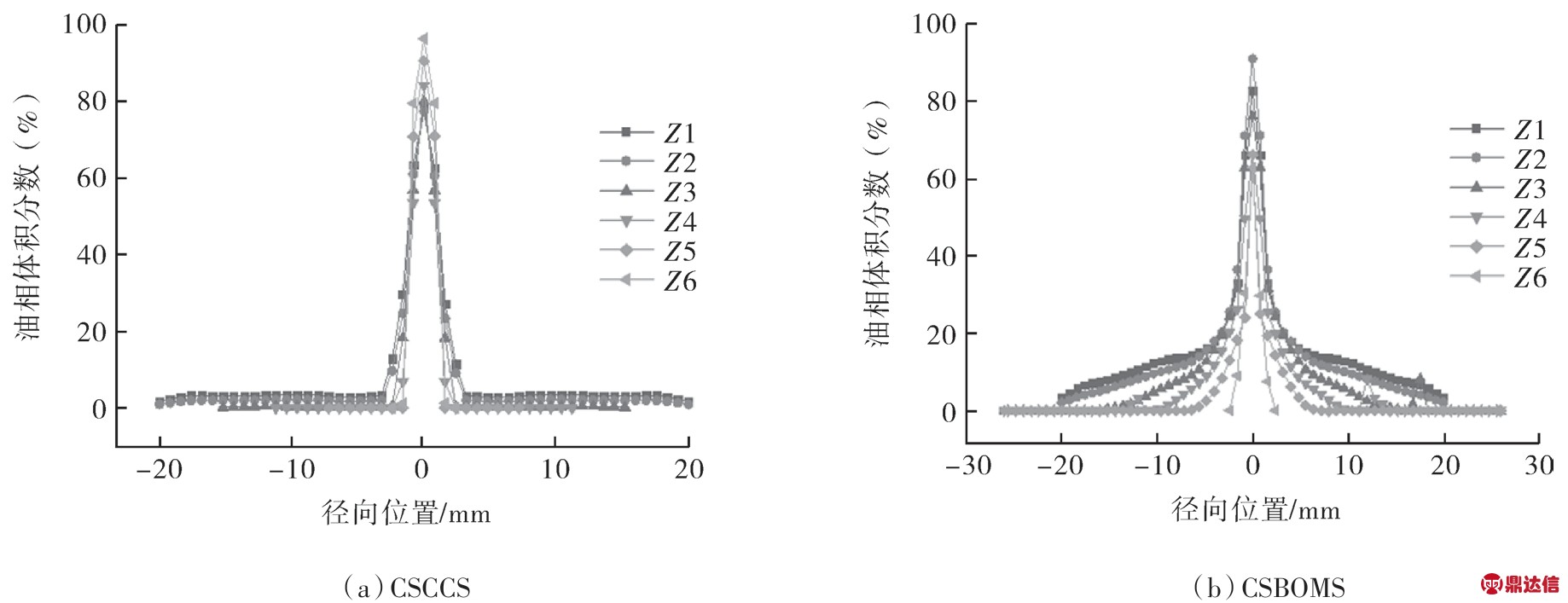
图14 不同截面油相分数曲线
3.4 CSBOMS 与CSCCS 分离效率
3.4.1 CSCCS 分离效率
通过后处理Flux Reports 命令计算CSCCS 底流口的油相质量浓度为0.160 3%,溢流分流比为0.22,运简化效率计算公式可得ηj 为:

式中 cu ——底流口含油浓度;
ci ——为水力旋流器入口浓度。
根据式(6)计算得到的CSCCS 分离效率为98.22%;则运用综合分离效率公式可得到η为:

式中 F ——分流比。
根据式(7)计算得到CSCCS 综合分离效率为84.19%。底流口油相百万分浓度φp 计算式为:

式中 φm——质量浓度。
根据式(8)计算得到φp =1.6×10-3。
3.4.2 CSBOMS 分离效率
CSBOMS 出水口分流比为0.71,出水口油相质量浓度为0.001 51%,换算成百万分浓度为为1.5×10-5;底流口分流比为0.13,油相质量浓度为2.33%,换算成百万分浓度为为2.319 2×10-2; 分析数据可得:(1)底流口含油浓度较高,相比CSCCS 的1.6×10-3 底流口含油含油高出10 多倍,但CSBOMS 底流口较高浓度的混合液会和溢流混合液一起举升至地面,不排放到地层,因此对CSBOMS 底流口含油浓度要求不必过高;(2)出水口油相质量浓度接近于零,这是由于在多孔介质模型设置时把油相的阻力系数设置为水相的 1 000 倍,油相基本不能通过多孔介质,出水口的油相浓度接近于零,故在计算CSBOMS 分离效率时不宜采用3 种常规计算公式来计算分离器的分离效率,因此采用出水口的水相质量分离效率来表征CSBOMS 分离性能,定义为除水分离效率:

式中 mw——出水口水的质量,kg;
miw——入口中水的质量,kg。
最终计算得到CSBOMS 除水分离效率ηw= 78.90%。故基于膜分离的旋流器能除去接近80%的水相,并能保证出水口含油浓度稳定达到直接回注标准。
4 样机试验验证
为了测试基于膜分离的井下油水分离器实际分离性能,验证膜分离器结构设计的可行性与合理性,并对照仿真分析结果,以FLUENT 仿真软件相同操作参数条件下进行了分离器单元样机实验,样机如图15(a)所示。
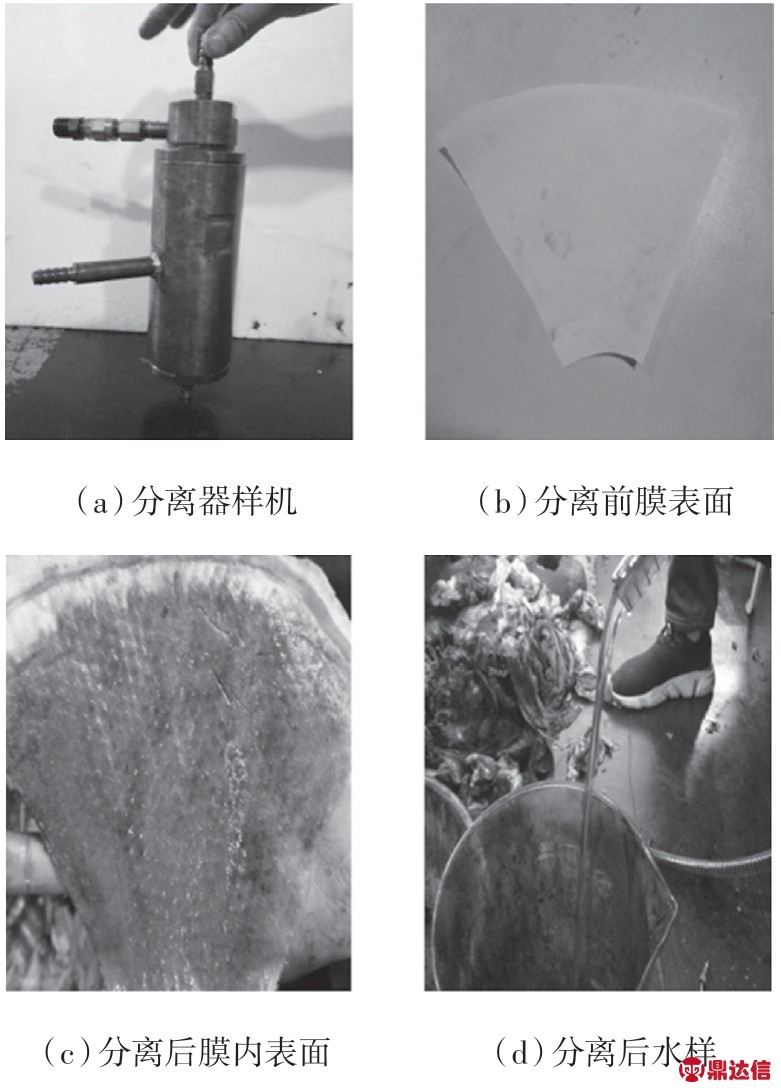
图15 相关样机试验图
在温度50 ℃、入口流量10 L/min、入口速度8.5 m/s 的条件下对含水率90%,黏度4.71 mPa·s的液样进行油水分离,得到数据见表2。
表2 试验原始数据
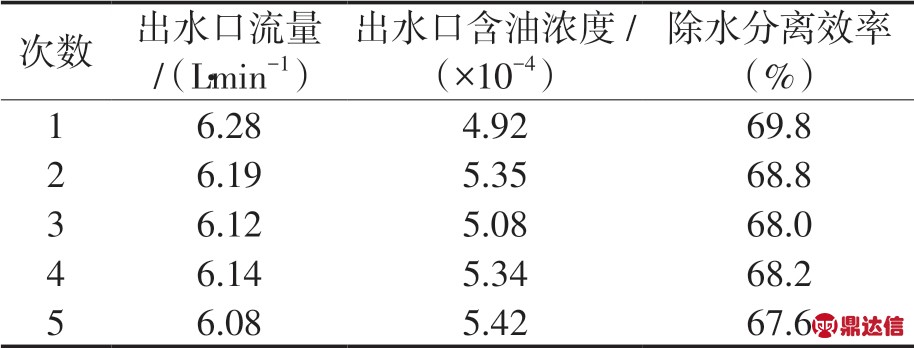
对比仿真分析结果与试验效果,5 次试验平均除水分离效率约为68.48%,相比现已投入应用的DOWS 系统60%左右的除水分离效率该方案有一定优势,而与仿真分析得到的78.90%除水分离效率相比,试验结果存在-13.2%的偏差,主要原因是仿真分析是不存在真实试验中原油附着、污染等产生的膜通量损耗问题;另外,真实液样中难免有少量的泥砂,一定程度上会导致膜堵塞;再者,考虑到试验设备运行稳定性问题,入口流量和压力存在轻微波动,所以存在小偏差是合理。
如图15(c)所示,膜材料在样机试验后内外表面均虽然有明显油渍,但比较干净,说明能达到预期分离效果,有较好的分离性能,证明了此结构的合理性。从图15(d)中可以明显观察到,出水口水柱清澈,取样测得含油浓度均在1×10-3 以下,能达到井底直接回注标准。
如图16 所示,对比前后5 次试验发现,前3次试验结果中,除水分离效率有小幅降低趋势,后两次实验结果相对稳定,说明在前2 次试验,膜的通量性能有较明显损耗,但后续连续使用时,分离膜的分离性能下降比较缓慢,保证分离膜有相对较长的使用寿命。5 次试验出水口含油浓度变化无明显上升或下降趋势,说明膜截油性能稳定,分离性能良好。综上所述,基于膜分离的井下油水分离器单元有较好分离性能,有一定的可行性。
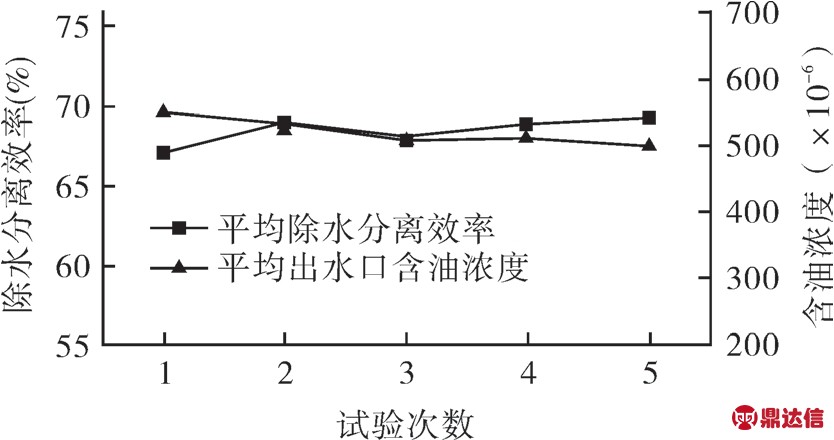
图16 除水分离效率与出水口含油浓度变化曲线
5 结语
将常规旋流分离技术与膜分离进行了有机结合,提出了基于超亲水膜的井下油水分离器,通过试验确定了最佳入口速度,并完成了分离器单元内部流场仿真分析,运用数值模拟方法将基于膜分离的旋流分离器内部流场规律与常规旋流分离器进行了对比,并通过样机试验与仿真结果相比较验证了方案的可行性,该方案不仅有常规旋流式分离器处理量大,可实现连续动态处理的优点,而且通过错流过滤机理,可提高其膜的自清洁性能,同时能够避免常规式井下旋流分离器因为工况、产能等波动短暂性或间歇性失去分离性能,导致未分离产液直接从底流口进入回注管柱,造成污染事故等问题。 相信随着膜技术的高速发展,此种结构的膜分离器的分离效率会进一步提升,为石油开采工程提供一定的参考价值。