摘要:为兼顾高分离精度及大处理量的要求,微小型旋风分离器并联得到越来越多应用。运用离散相模型和实验研究了螺旋并联分配管对旋风分离器分离性能的影响,分析了螺旋分配管分级和改变“序态”特性。结果表明,大颗粒易于从分配管前端出口逸出,依次进入旋风分离器固体颗粒呈现不同粒径分布,总体呈现分级特性;螺旋管对细颗粒物具有改变“序态”作用,进入旋风分离器颗粒粒径呈现外小内大趋势,内部相比外部颗粒浓度更高;内侧大颗粒构成的粒子环促进细小颗粒的去除,从而提高旋风分离器分离效率。实验进一步验证螺旋分配管分级和改变“序态”特性。研究结果对微小型旋风分离器并联设计具有指导意义。
关键词:旋风分离器;分离;螺旋分配管;数值模拟;粒度分布
引 言
旋风分离器作为一种除尘或除雾设备,广泛应用于石油化工[1-2]、燃煤发电[3]、环境工程[4-5]等诸多行业。作为静设备,旋风分离器具有成本低、效率高、长周期运行等优点。近年来,颗粒物污染引起社会的广泛关注,大气中的细颗粒物(PM2.5) 对环境和人体危害极大,它们十分细小、比表面积较大,通常富集各种有毒有机物和贵金属元素[6-8]。当气体中颗粒浓度低时,旋风分离器对直径小于切割粒径的污染物分离效率低。为解决这一问题,旋风分离器向微小型化发展[9-10]。较小直径的旋风分离器通常以较高压力操作,小直径旋风分离器切割粒径更小,分离精度更高。但不可避免的是较小直径的旋风分离器处理量也降低。为了达到高分离效率和大的处理量,微小型旋风分离器并联已获得越来越多的应用[11-15]。其次,为了进一步提高分离效率,很多学者研究发现,细颗粒物进口位置对旋风分离器分离特性有重要影响[16-25]。细小颗粒位于旋风分离器进口外侧,大颗粒物位于旋风分离器内侧更容易分离,这是因为位于进口外侧具有更高的向心加速度,小颗粒物更容易贴近内壁沉降;其次位于旋风分离器外侧小颗粒经过短路流逃逸概率越小;另外对于大颗粒来说,进口位置对大颗粒分离效率影响较小,位于内侧的大颗粒进入旋风分离器形成颗粒环,有利于规避细小颗粒从溢流排风管流出。很多学者根据这一规律,研究了不同种类的旋风入口排序器,保证进入旋风分离器颗粒呈现外小内大规律,进一步提高分离效率。例如,Wang等[26]发现带有预沉降的入口优于普通切向入口管,对分离效果很有帮助,入口管存在渐开线或者螺旋型的离心沉降,在离心力的作用下,大小颗粒受离心力不同而在径向截面内发生迁移,在出口可实现颗粒的大小及浓度的排序。Zhang等[27]通过研究正切圆入口,改善了旋流器性能,小曲率半径入口增加了切向速度和压力梯度,增强了入口颗粒的径向规则分布,使分离精度得到改善。研究还发现,随着曲率半径的减小,入口段固体颗粒的径向分布更规则。Huang等[28]在旋风分离器入口处安装由12根管组成的分层器,改变了入口处空气质量流量和粒子分布,从而增加旋风分离器入口外部颗粒浓度,减小了旋风分离器切割粒径,提高了分离效率。Misiulia 等[29]发现螺旋入口(helical-roof inlet)旋风分离器能够影响小颗粒向内旋流流入数量,从而提高旋风分离器效率。Fu等[30]通过研究四个新颖的入口颗粒分选器,使得较小的颗粒从矩形进口处的径向外侧进入旋风分离器,从而增强PM2.5分离。
旋风分离器并联分配管通常由直管道构成,旋风分离器对称或等距布置于分配管上,对于分配管来说,最重要的是保证进入每根旋风管内流量均匀,从而保证每根旋风管在正常工况内。但是对于直管道来说,进入旋风分离器颗粒“序态”并未发生变化,旋风分离器分级效率仍然由单管决定。因此,本文构想利用螺旋管道中介质产生离心力场,实现颗粒的排序,颗粒在入口截面呈现外小内大规律,从而进一步提高分离效率。
本研究基于FLUENT软件,采用RSM雷诺应力模型,对螺旋管改变颗粒物“序态”进行分析,研究了螺旋管出口粒径分布,进一步通过模拟旋风分离器计算分离效率,并通过实验验证模型准确性。对旋风分离器并联提供参考。
1 数值模拟
1.1 CFD模型
图1为螺旋分配管三维结构图。螺旋管道为横截面为160 mm × 160 mm的矩形,直径为1200 mm,螺距为600 mm的垂直左旋螺旋。旋风分离器组由十二根旋风沿螺旋轨道并联而成,旋风分离器入口由螺旋管道外侧引出,入口中轴线与螺旋线切线夹角为45°。
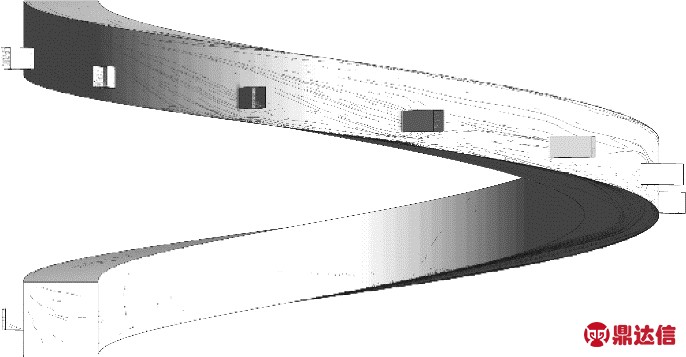
图1 螺旋结构示意图
Fig.1 Sketch of spiral channel
旋风分离器的结构如图2所示,尺寸参数如表1所示。切向式进口布置在旋风分离器柱段顶部,含尘气体切向进入旋风后形成旋流。在离心力和气体曳力作用下,较粗的颗粒会向边壁移动并沉降,从底流口排出;较细的颗粒则向中心移动,并从溢流口排出。
表1 旋风分离器几何参数
Table 1 Dimensions of cyclone

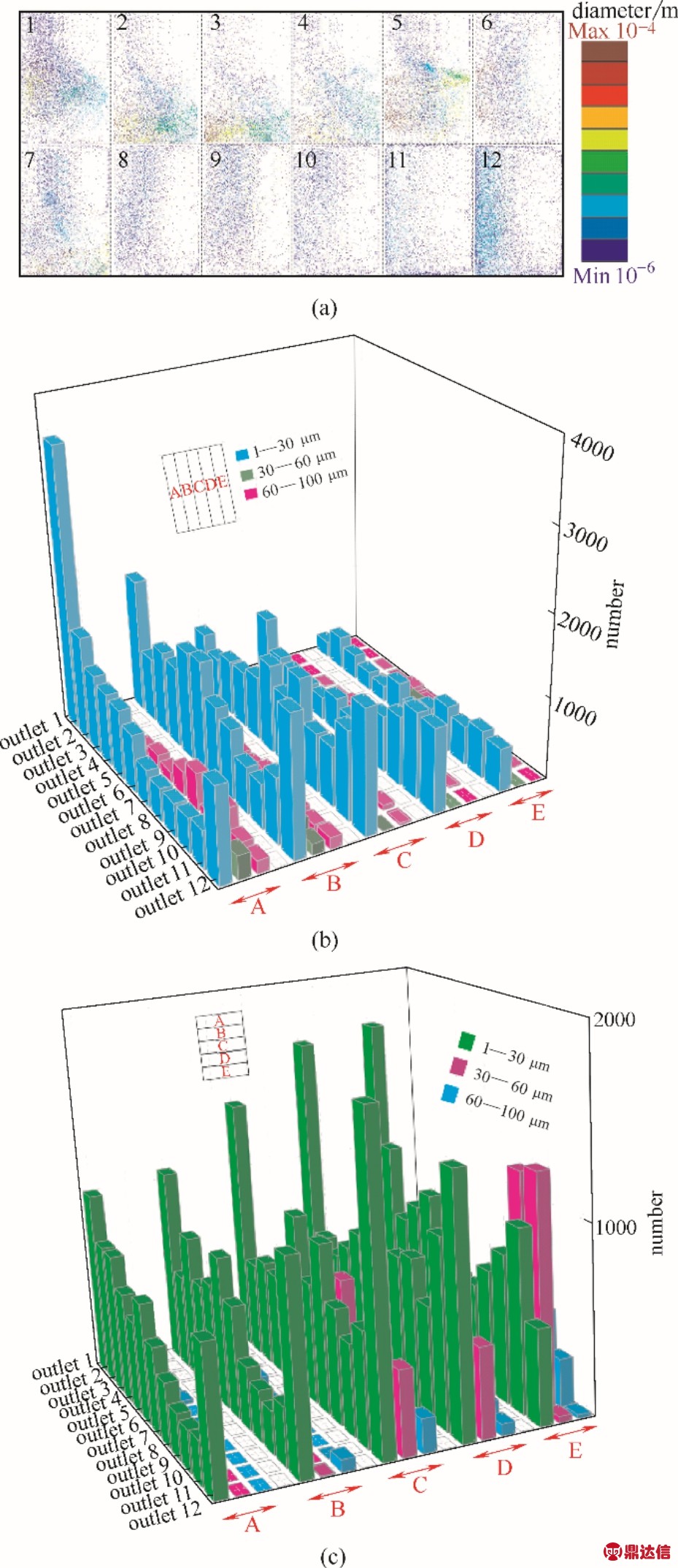
图2 旋风分离器尺寸
Fig.2 Geometry and dimensions of cyclone
1.2 网格无关性验证
本文采用Ansys ICEM软件划分螺旋通道和旋风分离器网格,均采用六面体结构网格划分,如图3所示。针对螺旋通道模型,前期试算采用了四种网格,并在相同边界条件和初始条件下运算,随机所取线段为螺旋分配管中部端面上,其两端点坐标为(-6260258)和(-5360360),导出其速度值,对比如图4所示。当网格数超过80万个时,对网格的进一步加密对计算精度影响较小,且会增加额外的计算时间。故最终选取计算域网格数为871536个。
1.3 湍流模型与边界条件
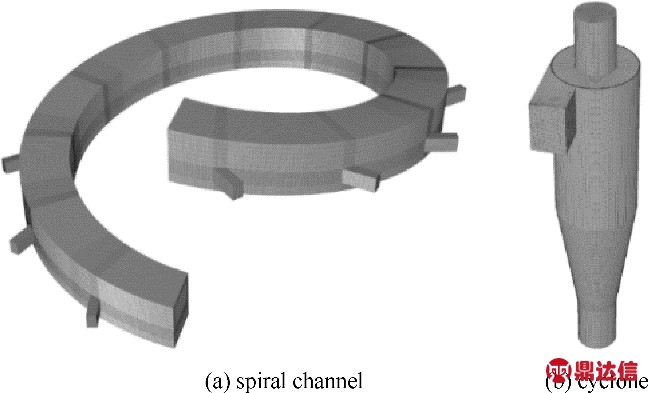
图3 模型网格
Fig.3 CFD grid

图4 网格无关性验证
Fig.4 Grid independence verification
本文采用Ansys Fluent 17.0对两个计算模型进行数值模拟计算,湍流模型均选用RSM雷诺应力模型,该模型适用于应变场较复杂的各向异性流场,尤其是存在大流线曲率或涡旋的流场。近壁面均采用标准壁面函数进行处理。速度压力耦合采用SIMPLE算法,压力的离散格式选取 Body Force Weighted,动量项、湍动能项、湍流耗散项以及雷诺应力项均选取高精度的QUICK格式。
螺旋通道模型的进口边界条件设置为速度入口(velocity-inlet),入口气速为13.02 m/s(入口流量为1200 m3/h),水力直径为160 mm,湍流强度取5%;12个出口的边界条件均设置为压力出口(pressure-outlet),出口压力为标准大气压,回流水力直径为34 mm,湍流强度取5%。
旋风分离器模型的进口边界条件设置为速度入口(velocity-inlet),入口气速为20.57 m/s(入口流量为100 m3/h),水力直径为34 mm,湍流强度取5%;溢流口边界条件设置为压力出口边界,出口压力为一个大气压。
2 模拟结果及分析
2.1 螺旋管道内颗粒分布
螺旋管内粒子迹线如图5所示,细小颗粒在螺旋管内停留时间为0.7 s,选取时间区间0~0.8 s,每隔0.005 s获得不同颗粒粒径的分布。12个出口沿螺旋管由小到大标号,从图5可以看出,固体颗粒均匀进入螺旋管道后,在离心力的作用下,大颗粒最先贴外壁,从前面几个出口溢出进入旋风分离器,细小颗粒继续沿着螺旋管道运动,总体呈现分级特性,使依次进入旋风分离器组固体颗粒呈现不同粒径分布。在螺旋管底部,细微颗粒会发生回流,这样导致进入最后一个出口颗粒数会增加。
进一步统计每个出口的颗粒数,结果如图6(b)所示。进入螺旋管内粒子初始粒径分布符合单峰分布,粒径位于30~70 μm占65%,如图6(a)所示。由模拟结果可知,大粒径粒子(30~100 μm)集中于前面出口,数量呈递减趋势,小粒径粒子 (1~30 μm)在每个出口数目基本一致,最后一个出口由于回流效应粒子数较其他出口有所增大。因此,可根据螺旋管分级特性,根据不同出口不同粒径范围设计不同规格(切割粒径)的旋风分离器,在提高处理量的同时提高分离效率。
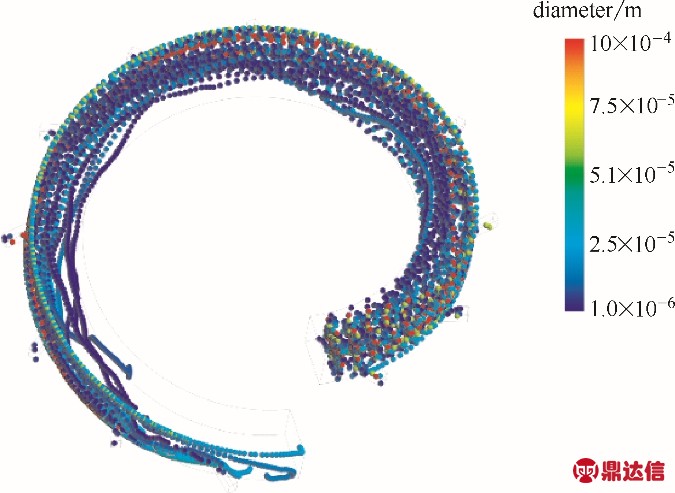
图5 螺旋通道内大小颗粒迹线
Fig.5 Grid independence verification
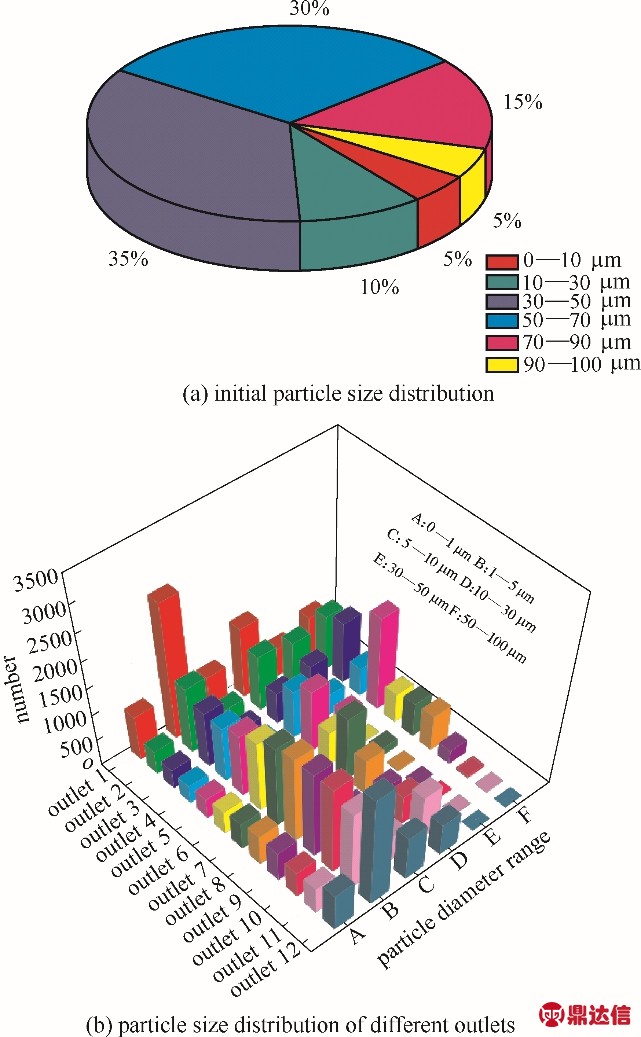
图6 螺旋通道内颗粒粒径分布
Fig.6 Particle size distribution in spiral channel
2.2 出口的粒径分布
在得到不同出口粒径范围的基础上,进一步分析每个截面不同位置处的粒径分布,验证之前构想利用螺旋管道中介质产生离心力场,实现颗粒的排序,得到进入旋风分离器(内大外小)“序态”,从而进一步提高分离效率。
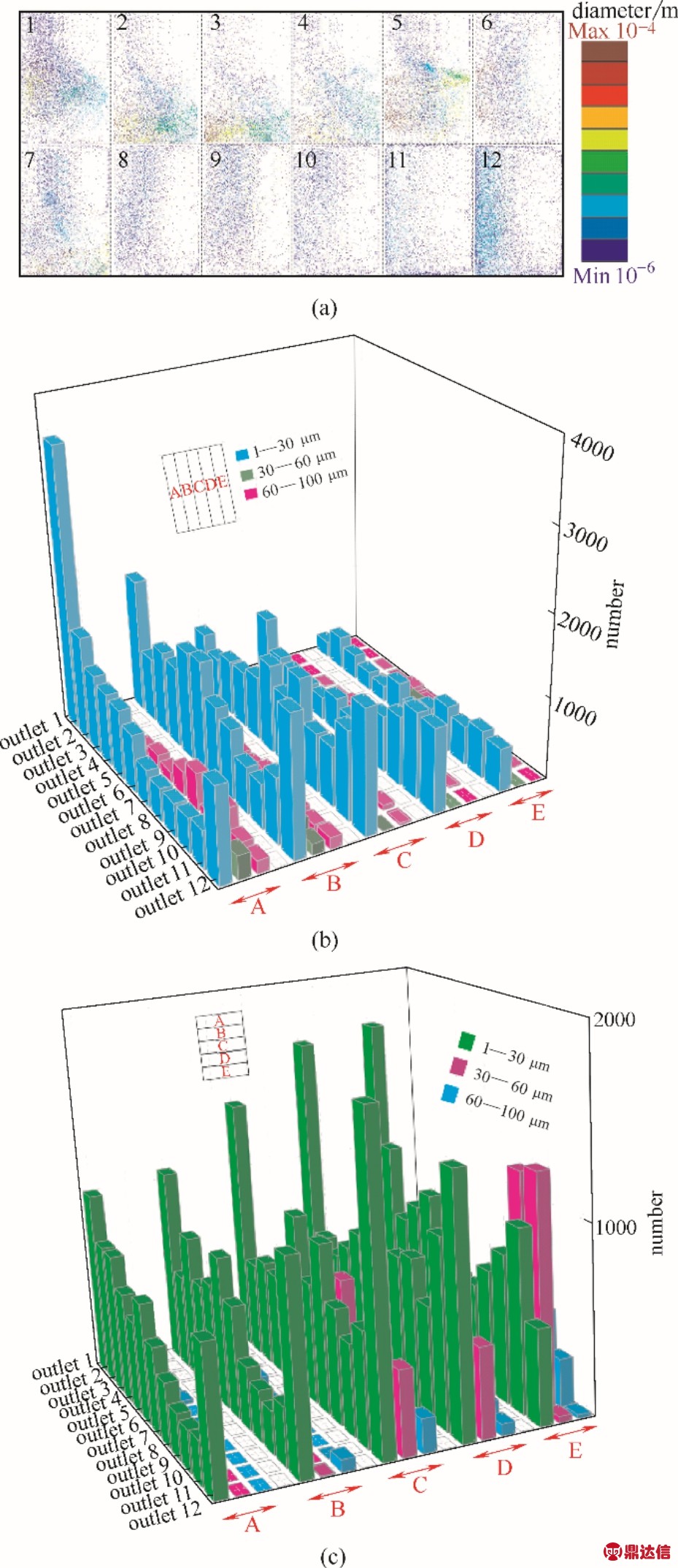
图7 不同出口粒子分布
Fig.7 Particle distribution of different outlets
12个进口的粒子散点图如图7(a)所示,可以看出,12个出口粒径分布都呈现内大外小趋势,每个散点图左部对应旋风分离器外侧。从出口1到12,粒径整体呈减小趋势,越靠近螺旋管后面分支,粒子直径越小,这也与图6(b) 对应。将每个出口截面从左到右、从上到下各分为了五个区域,分别统计了这两种情况下不同粒径范围内的颗粒的位置情况,结果如图 7(b)、(c) 所示。12 个出口散点图都具有一致的规律:即大颗粒粒子位于左侧(对应旋风分离器内侧);小颗粒粒子位于右侧(对应旋风分离器外侧),且粒子浓度较右侧更高,这对于旋风分离器来说更容易形成大颗粒粒子环,从而提高分离效率。
2.3 分离效率
将每个出口的粒径分布作为旋风分离器入口的颗粒的粒径分布。由于计算模型中的固相与气相体积比非常小,本文采用离散相模型(DPM)来追踪粒子轨迹,同时考虑颗粒相与连续相的耦合。考虑到流体离散涡及湍流扩散对颗粒运动的作用,使用随机游走模型。在螺旋管道算例中,出口离散相边界条件设置为捕获(trap),其余壁面条件设置为反弹,且反弹系数设置为 0.8。在旋风分离器算例中,底流口离散相边界条件设置为捕获(trap),溢流口离散相边界条件设置为逃逸(escape),其余壁面条件设置为反弹,且反弹系数设置为0.8。旋风分离器的性能用分离效率来表征,其分离效率为

其中,η为旋风分离器分离效率,mtrapped为捕获粒子质量,mtracked为追踪粒子总质量,i为旋风分离器序号。
通过计算得到,每根旋风分离器分离效率相比均匀进入的都有所提高,如图8(a) 所示。红色虚线代表粒子均匀进入旋风分离器的分离效率,绿色柱状图代表每根旋风分离器分离效率,蓝色虚线代表增加螺旋分配管后总分离效率,通过螺旋分配管出口改变颗粒“序态”作用,旋风分离器组总分离效率提高4%。
3 对比实验
3.1 实验测试
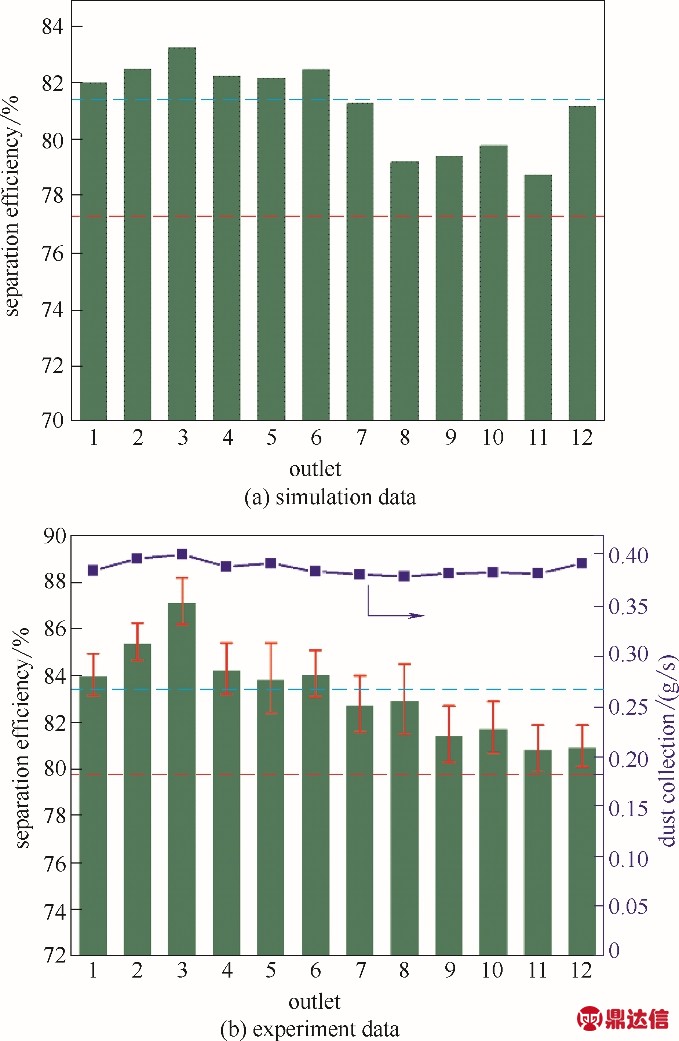
图8 旋风分离器分离效率
Fig.8 Separation efficiency of cyclones
为了进一步验证螺旋分级特性和出口“内大外小”特性,搭建了相同的实验装置,如图9所示。实验装置由三根螺旋管构成,中间管路有 12个出口,12个出口接DN75旋风分离器,由旋风分离器溢流口和底流口分别出来的净化气和含尘气流入底流汇管和溢流汇管,然后进行尾气处理。所用物料为平均粒径为5 μm滑石粉,充气密度为280 kg/m3。风机为风量为1000 m3/h的漩涡风机,入口颗粒浓度为 20 mg/L。实验测试的工况下,螺旋通道进料量约为5.56 g/s。滑石粉经加料器进入混合器,在混合器内混合均匀后进入螺旋装置分离。同时测量了每根旋风分离器的体积流量。
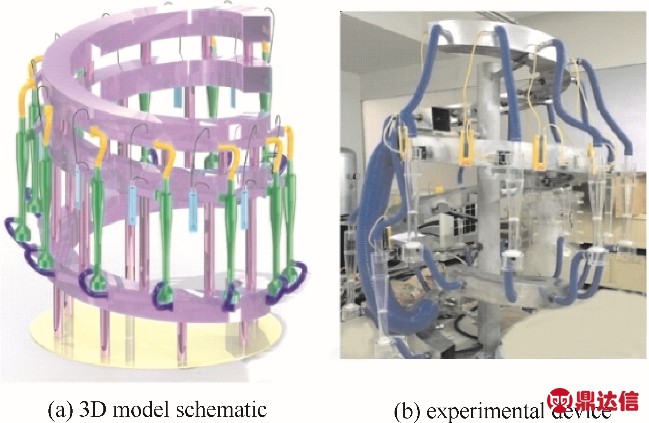
图9 实验装置示意图及实物图
Fig.9 Diagram of experimental apparatus
3.2 实验结果
如图8(b)所示,图中蓝点代表每个旋风子的集尘速率,红色虚线表示单根旋风分离器分离效率实验的结果,绿色柱状图代表每根旋风分离器分离效率,蓝色虚线代表增加螺旋分配管后的总体分离效率,相比提高了约4个百分点。其分离效率值较数值模拟较高原因是实验过程中采样和称量环节存在一定误差,但趋势大致相同。
各并联旋风分离器的体积流量如表2所示,其展示的流量的均匀性能满足了作为分配管的基本要求,使每根旋风分离器处于额定工况下,不影响其分离效率。
表2 螺旋通道各出口体积流量
Table 2 Volume rate of 12 outlets
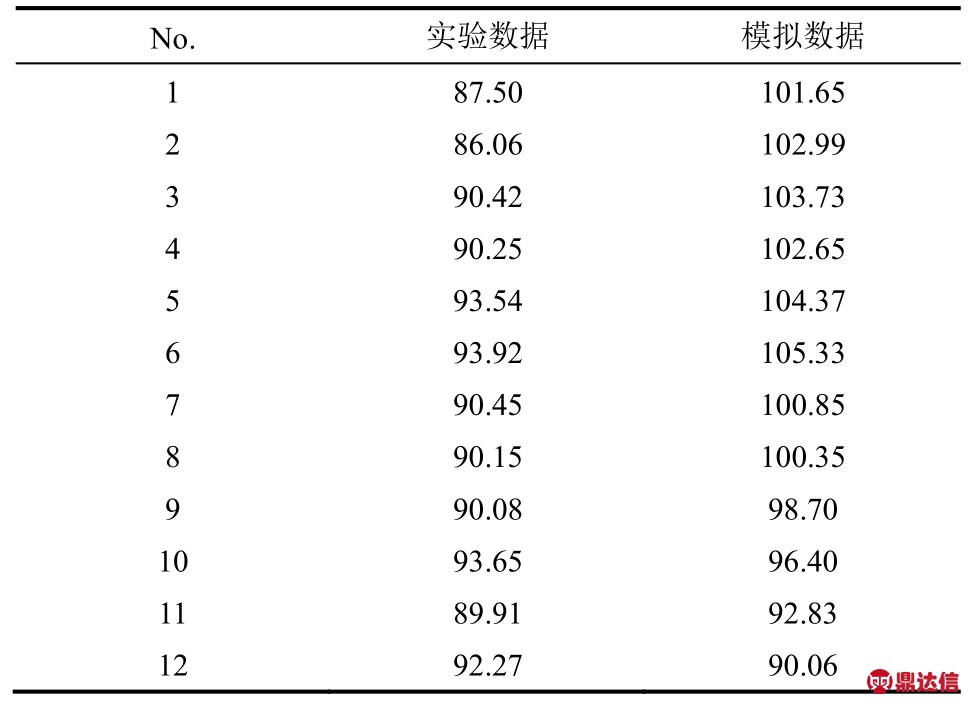
将螺旋管出口分为12小格,如图10所示。通过对出口采样,将采样器引出 12条软管完成粉尘的收集,并统计每个小格的粒径规律,可以发现,粒径分布实验数据规律完全符合模拟结果,都呈现出颗粒由左到右呈递减规律,由上到下呈递增规律,所测粒径如图11所示。其中,粒径序号由(x,y)组成,x为竖直位置编号,y为水平位置编号。粒径峰值由左往右变小,由上往下变大。图10中12个小格数值代表粒径分布d50,同样符合这一规律。因此,通过实验验证了螺旋管出口改变“序态”机制的正确性。
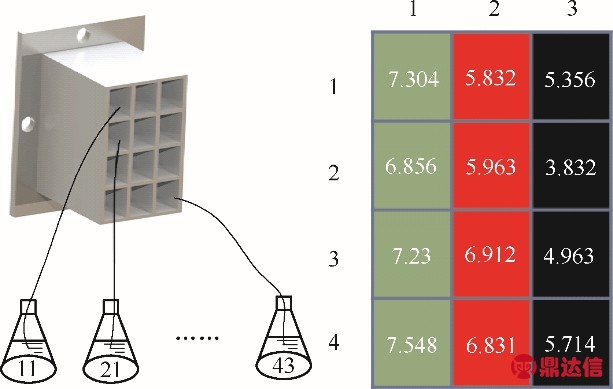
图10 采样方法与旋风分离器入口截面12格d50
Fig.10 Sampling andd50in 12 regions of cyclone inlet
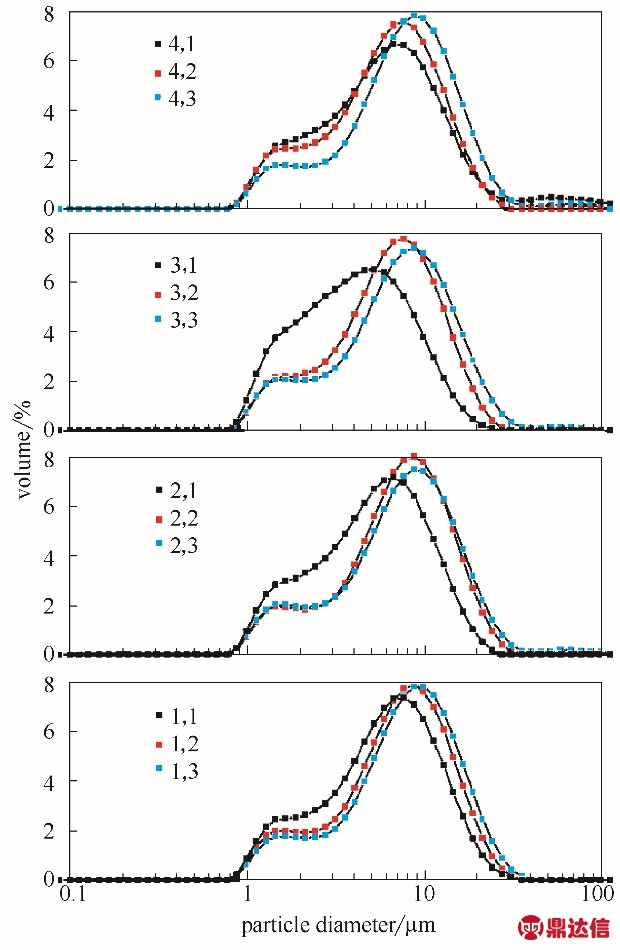
图11 旋风分离器入口截面12格粒径分布
Fig.11 Particle size distribution in 12 regions of cyclone inlet
4 结 论
利用Fluent软件,模拟了螺旋分配管对细颗粒运动的影响,重点分析了粒子分级和改变“序态”的特性,研究了螺旋分配管对旋风分离器分离效率的作用;搭建旋风分离器螺旋并联实验装置,验证了模拟结果的正确性。所得结论如下。
(1)在离心力作用下,螺旋分配管具有对粒子分级特性,大粒径颗粒先于细微粒子溢出,沿螺旋线呈递减趋势,而螺旋管对细微颗粒作用不明显,在螺旋管底部,存在颗粒回流行为。
(2)螺旋管对细颗粒物具有改变“序态”作用,使进入旋风分离器颗粒呈现外小内大趋势,且大颗粒集中于进口截面内下部,内部相比外部颗粒浓度更高。
(3)通过螺旋管改变“序态”特性,由内侧大颗粒构成的粒子环促进细小颗粒的去除,从而使旋风分离器分离效率提高,对旋风分离器的并联设计提供指导。
符 号 说 明
a——进口宽度,mm
b——进口长度,mm
D——柱段直径,mm
do——溢流管直径,mm
du——底流管直径,mm
Lc——锥段高度,mm
Lf——溢流管伸出长度,mm
Ls——柱段高度,mm
Lu——料腿长度,mm
L0——溢流管插入深度,mm
mtracked——追踪颗粒数
mtrapped——捕集颗粒数
x——竖直位置编号
y——水平位置编号
η——分离效率,%
θ——锥角,(°)