摘要:基于壁面液膜模型,进行无钩波形板汽水分离器内液膜生成情况的三维数值模拟,模拟中采用Realizable k-ε模型和壁面液膜模型对波形板内的气相和液相进行数值模拟计算,根据模拟结果分析波形板内的分离效率。研究结果表明:在不改变波形板的结构和不考虑二次携带的前提下,随进口速度或液滴直径的增加,壁面形成液膜面积和高度增加,分离效率也随之提高。当进口速度和液滴直径一定时,液膜高度和面积随蒸汽湿度的增加呈先增加后减小的趋势,当湿度达到10%时,液膜高度和面积达到最大,分离效率最佳。
关键词:波形板分离器;液膜高度;液滴直径;分离效率
在核动力装置中,如果不对湿蒸汽进行处理,汽轮机低压缸的蒸汽湿度将达到20%~25%,严重影响汽轮机的经济安全运行,因此要加装汽水分离器。波形板汽水分离器具有分离效率较高、阻力小、破膜速度高等优点,因此作为汽水分离系统最后一级分离器,被广泛应用于核动力装置中,可将蒸汽干度最高提高到99%,保证了核动力装置的安全运行[1]。最近几年,关于液滴的分离、碰撞、破碎及聚合等研究领域逐渐升温[2-4]。目前,国内外对波形板汽水分离器的研究主要包括试验研究和数值模拟两方面,在试验研究方面,主要集中在冷态工况下,对波形板汽水分离器的分离效率和结构优化的研究[5-6]。Kitron等[7]通过实验研究得出碰撞液滴破碎与聚合对液滴尺寸具有很大影响;Engel[8]研究了水滴在波形板内随壁面粗糙度的增加,液滴更易破碎成二次液滴。数值模拟可有效地了解波形板在不同工况和结构参数下的分离效率,从而为波形板汽水分离器的结构优化提供参考。张谨奕等[9]通过理论分析,建立了单个液滴在三维流场中的运动模型,并运用到波形板汽水分离器的效率分析,结果显示多数大液滴由于惯性碰撞壁面被分离,少部分小液滴随气流离开分离器。杨雪龙等[10]通过理论分析与三维模拟研究了实际运行工况下单钩波形板汽水分离器内二次携带机理,表明二次携带主要由水膜的剥落和分离造成。Marion等[11]采用数值模拟方法研究了液滴在波形板内运动,分析发现气流湍动度严重影响着液滴的破碎和聚合,液滴粒径的大小对分离器的分离效率有很大影响。目前,运用实验方法很难观测到波形板内液膜的铺展情况和高度,而运用数值模拟的方法可模拟出液膜的铺展和高度。本文将通过三维数值模拟的方法研究分离器内液膜生成情况并分析液滴分离效率。
1 计算模型及相关理论
在波形板进口蒸汽湿度为5%~20%的前提下,波形板汽水分离器内的水体积分数在0.25%~1.2%之间,水滴运动可采用离散型模型(DPM)[12]计算。
液滴成膜采用壁面液膜模型。液滴与壁面间相互作用的计算体系是基于Stanton等[13]的研究结果,该体系中有4种物理形态:粘附、反弹、铺展和飞溅。这4种物理形态取决于液滴初始碰撞壁面的能量和壁面温度。当液膜温度低于液滴的沸腾温度,碰撞只发生粘附、铺展和飞溅,但当液膜温度高于液滴沸腾温度时,液滴就会发生反弹和飞溅。撞击能量和壁面温度不同,产生结果不同。撞击能量E被定义为:
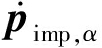
(1)
式中:ρ为液滴密度,kg/m3;Vr为液滴撞击壁面的法向相对速度,m/s;σ为液体的表面张力,N;D为液滴粒径,m;h0为液膜高度;δbl为壁面液膜高度,mm,其定义式为:

(2)
式中,μ为动力黏度。
图1为液滴与壁面相互作用结果。液体温度低于沸点Tb(壁面温度)时,撞击在壁面的液滴可发生粘附、铺展和飞溅,高于Tb可发生反弹和飞溅。
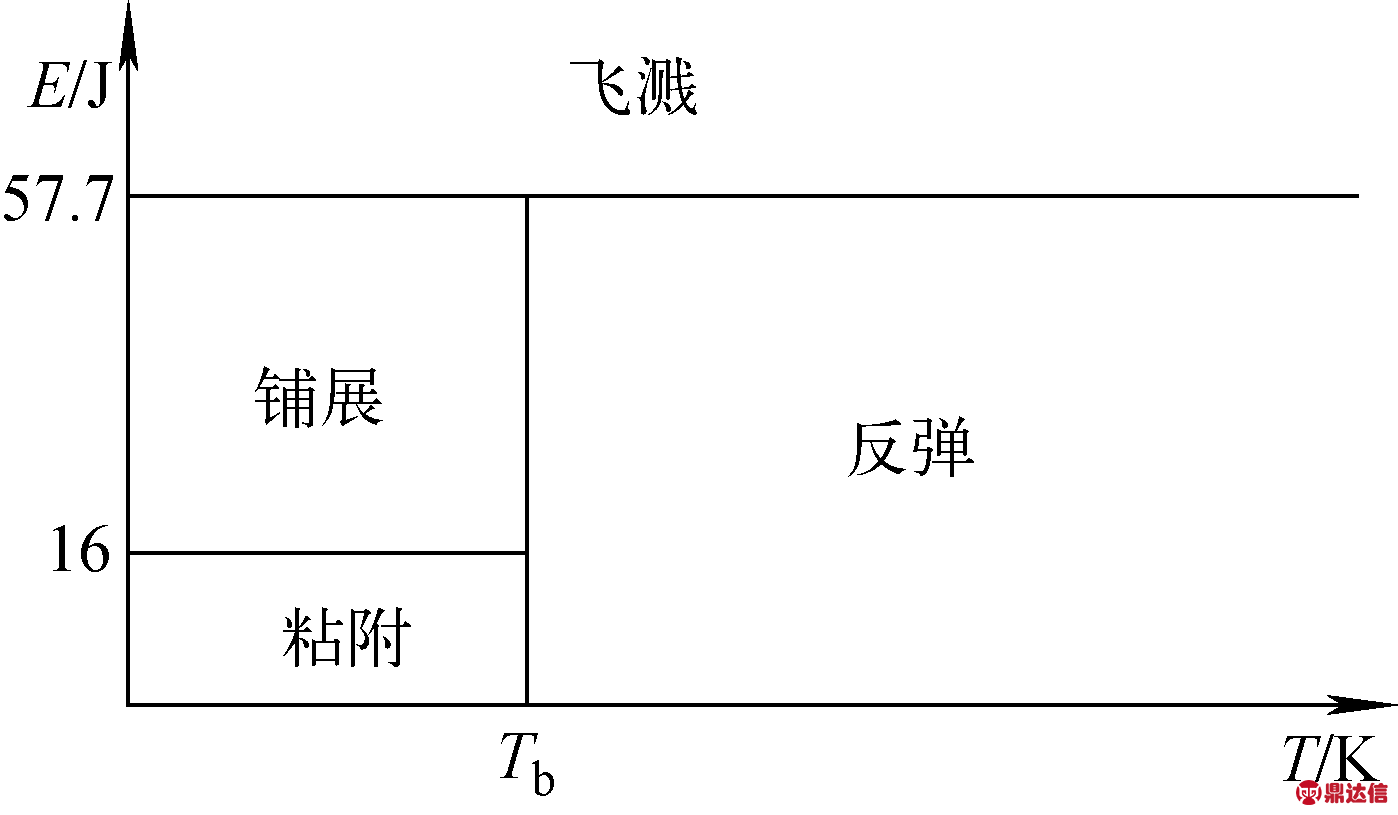
图1 液滴与壁面相互作用结果
Fig.1 Result of interaction for droplet and wall
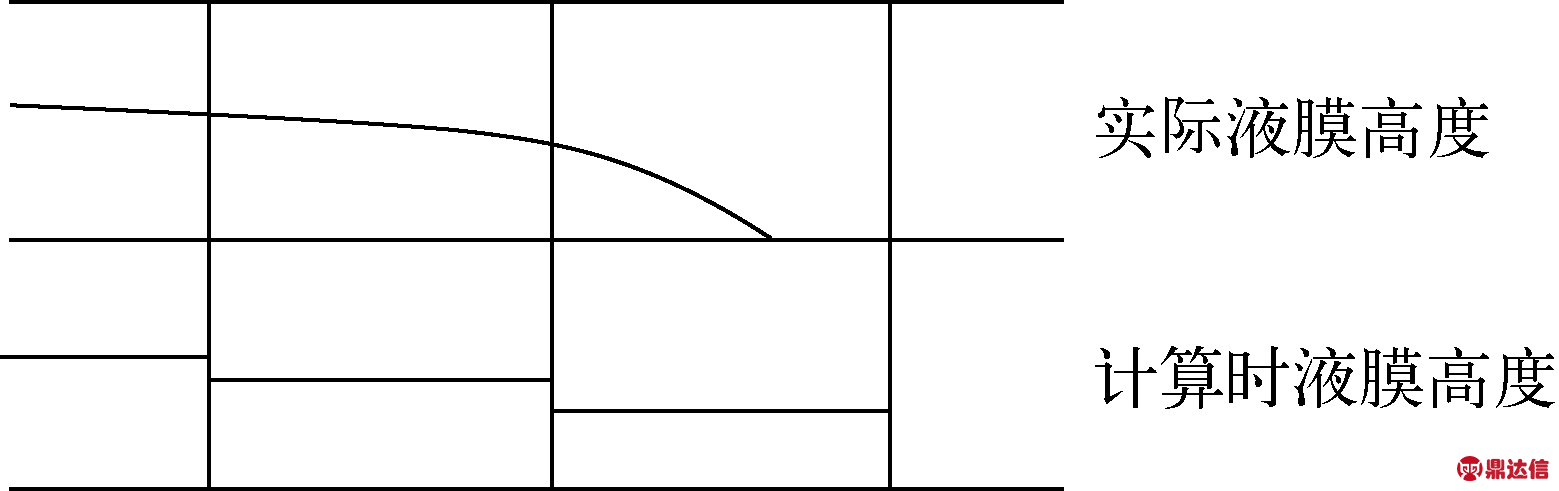
图2 壁面液膜模型液膜高度与实际液膜高度对比
Fig.2 Comparison of wall-film model and actual liquid film heights
壁面液膜模型中的液膜高度与实际的液膜高度是不同的,如图2所示。
计算时设定每个单元格内的高度是平均值,每个单元格内的质量m即可用h0表示:
m=ρsh0
(3)
式中,s为单个网格面积。
模型的动量方程如下:


(4)
式中:up为液相速度;h0为粒子所在位置的液膜高度;为仅限于曲面的梯度算子;pf为液膜的表面压力;
为液相表面上的压力梯度;τg为液膜表面气体流动剪切应力;tg为气体与液膜表面相对运动方向的单位向量;τw为壁面对液膜表面压力;tw为液膜和壁面相对运动方向的单位向量;
为液膜的撞击压力;
为撞击质量源;
为保持液膜表面所需的力;g为重力加速度;aw为液膜和壁面相对运动方向的加速度;下标α为液相计算点所在位置。
由式(1)、(4)可得出液膜高度h0。
几何模型采用普通压水堆核电站实际波形板尺寸。网格划分采用结构性网格,网格数50万,采取边界层加密。波形板内部流动假设为定长不可压缩恒温流动。湍流模型采用在波形板数值模拟中效果良好[6,10]的Realizable k-ε模型;采用标准壁面函数求解近壁区。采用速度进口,出口设置压力出口边界,波形板底部和顶部采用周期性边界,离散边界条件为壁面液膜模型,采用二次迎风格式,离散化方法选用SIMPLE方法。
2 合理性分析
2.1 计算工况
不考虑二次携带冷态工况时进口速度小于7 m/s,进口速度为:1.1、2.2、3.3、4.4、5.5和6.6 m/s。Toshitsugu等[1]通过激光多普勒测速仪发现水滴直径为10~600 μm,平均直径为224 μm,当采用随机直径时,直径范围设置在10~600 μm区间内,且平均直径为224 μm。当研究液滴直径的影响时,波形板入口水滴直径取10、30、50、100、224 μm。根据冷态实验工况[6]蒸汽湿度为5%、10%和20%。
2.2 模型的合理性分析
本文将1.1 m/s时波形板第1级同一垂直高度上的液膜高度和Miyara[14]对垂直板壁上液膜的流动特性进行对比,结果如图3所示。
从图3a可看出,垂直高度为60、70 mm时的液膜高度曲线与图3b区域Ⅱ中微小波状曲线相对应,30~50 mm时的液膜高度曲线与区域Ⅲ中的弓形波状相对应,而在20 mm高度的液膜高度曲线与区域Ⅳ独立波状相对应。从两图的对比可看出,数值模拟的液膜流动特性与Miyara在文献中给出的液膜流动特性形态图有一定的吻合性,从而可说明模型的合理性。
2.3 分离效率合理性分析
将进入波形板的液滴总质量记为m1,波形板壁收集的液体总质量为m2,则分离效率通过下式求得:
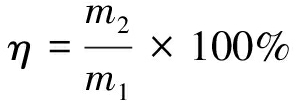
(5)
本文求出进口速度为2.2、3.3、4.4、5.5、6.6 m/s时波形板分离器的分离效率,并与文献中数据进行比较。图4示出数值模拟结果与肖立春等[15]的汽水分离器分离效率实验的分离效率对比。
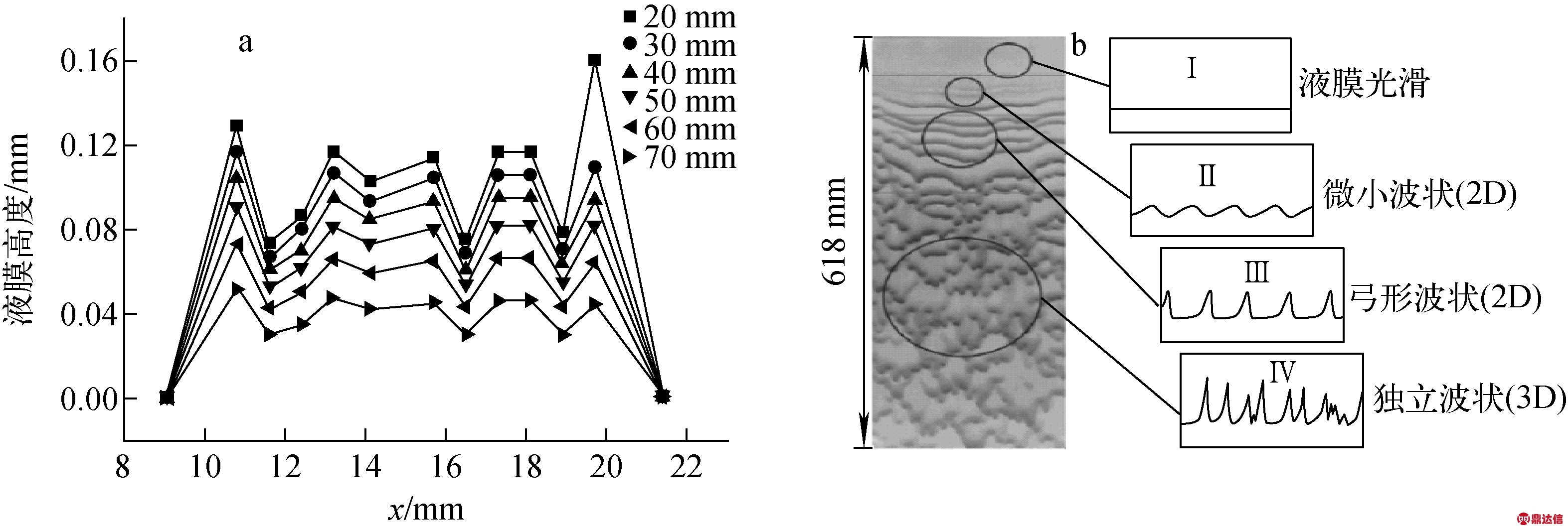
a——垂直高度上的液膜高度;b——垂直板壁上液膜流动特性
图3 板壁同一高度液膜的流动特性对比
Fig.3 Comparison of flow characteristics of the same height of plate
从图4可看出,随进口速度的增加,波形板汽水分离器的分离效率增大。实验数据和数值模拟的数据趋势相同,且两者的最大相对误差在10%以内,在可接受范围内,从而进一步验证了该模型的可信度。
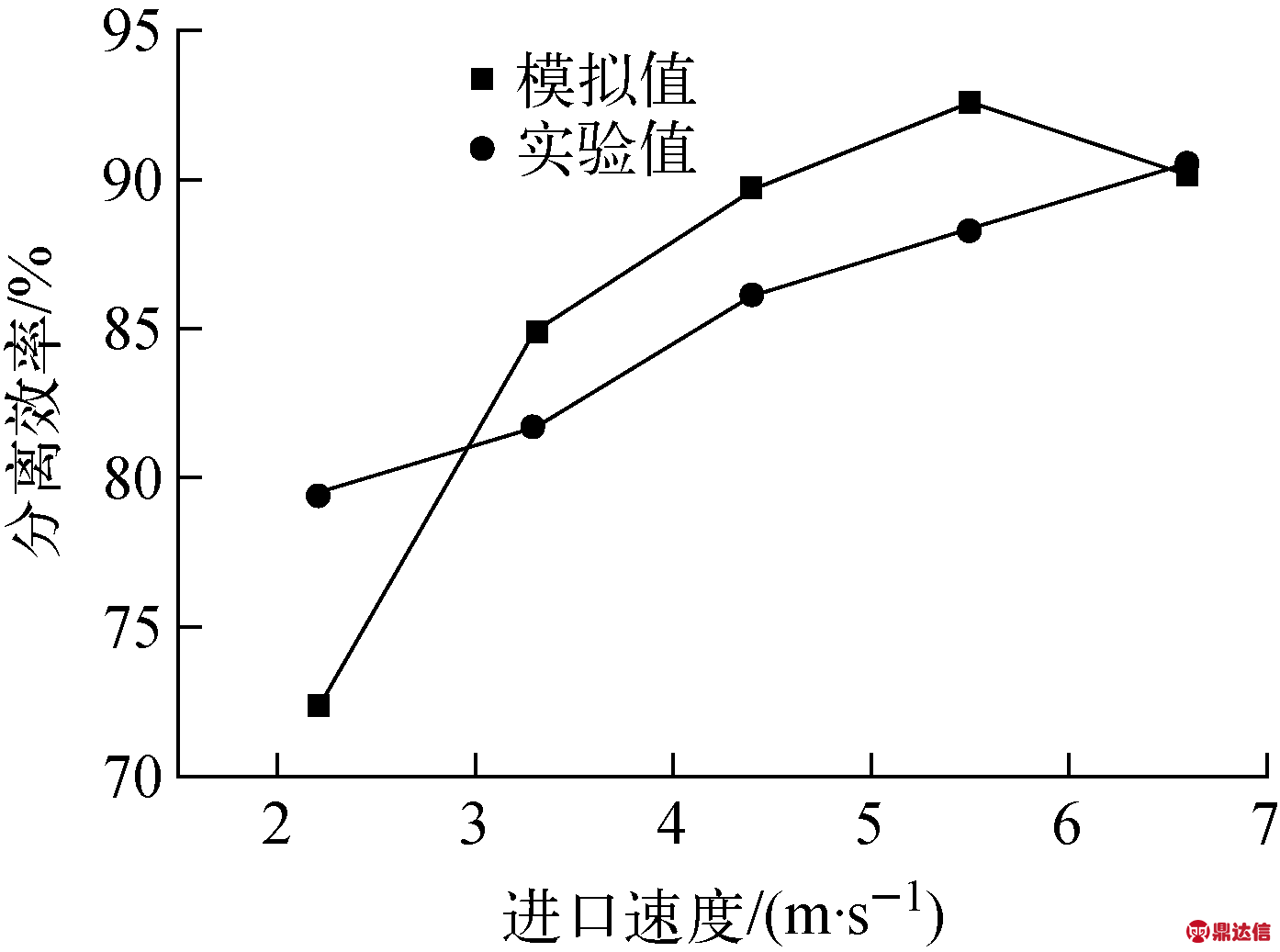
图4 数值模拟结果与实验的分离效率对比
Fig.4 Comparison of numerical simulation result and experimental separation efficiency
3 分离效率影响因素分析
在不改变波形板结构的前提下,影响波形板分离器效率的变量有进口速度、液滴直径、蒸汽湿度。本文将对这3个因素进行模拟分析。
3.1 进口速度
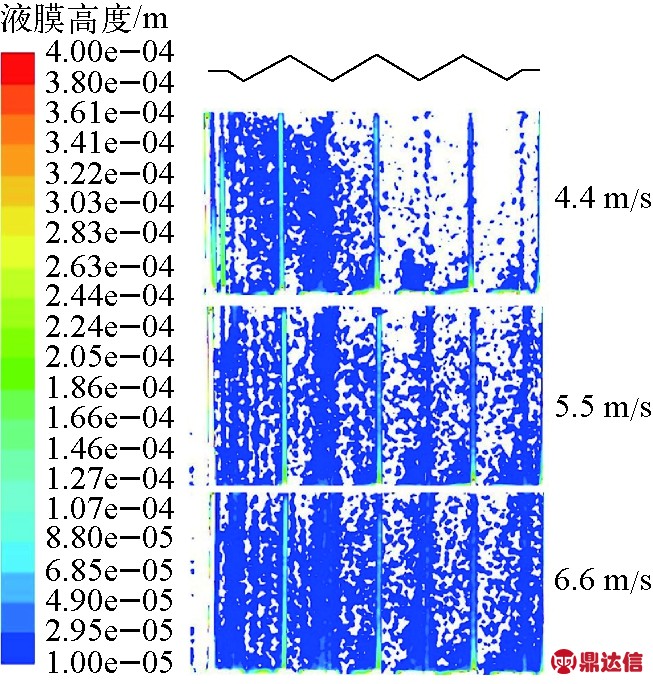
图5 不同进口速度下的液膜高度
Fig.5 Liquid film heights of different inlet velocities
当液滴直径和蒸汽湿度不变时,不同进口速度下的液膜高度分布如图5所示。
液膜主要分布在板壁的波谷内,迎风面的液膜面积远多于背风面的,且多集中在波形板的前两级,这说明此波形板汽水分离主要在前两级实现。
当液滴直径为平均直径224 μm、蒸汽湿度为10%时,给出了4.4、5.5、6.6 m/s时的液膜高度,随进口速度的增加,板壁上产生液膜的面积增大。在波谷转折处由于有涡流的存在,会聚集较厚的液膜。而液膜高度越大,液膜质量越大,分离效率就越大。这说明随进口速度的增大,波形板分离器的分离效率增大。
图6为波形板分离器在不同液滴直径下分离效率随进口速度的变化。
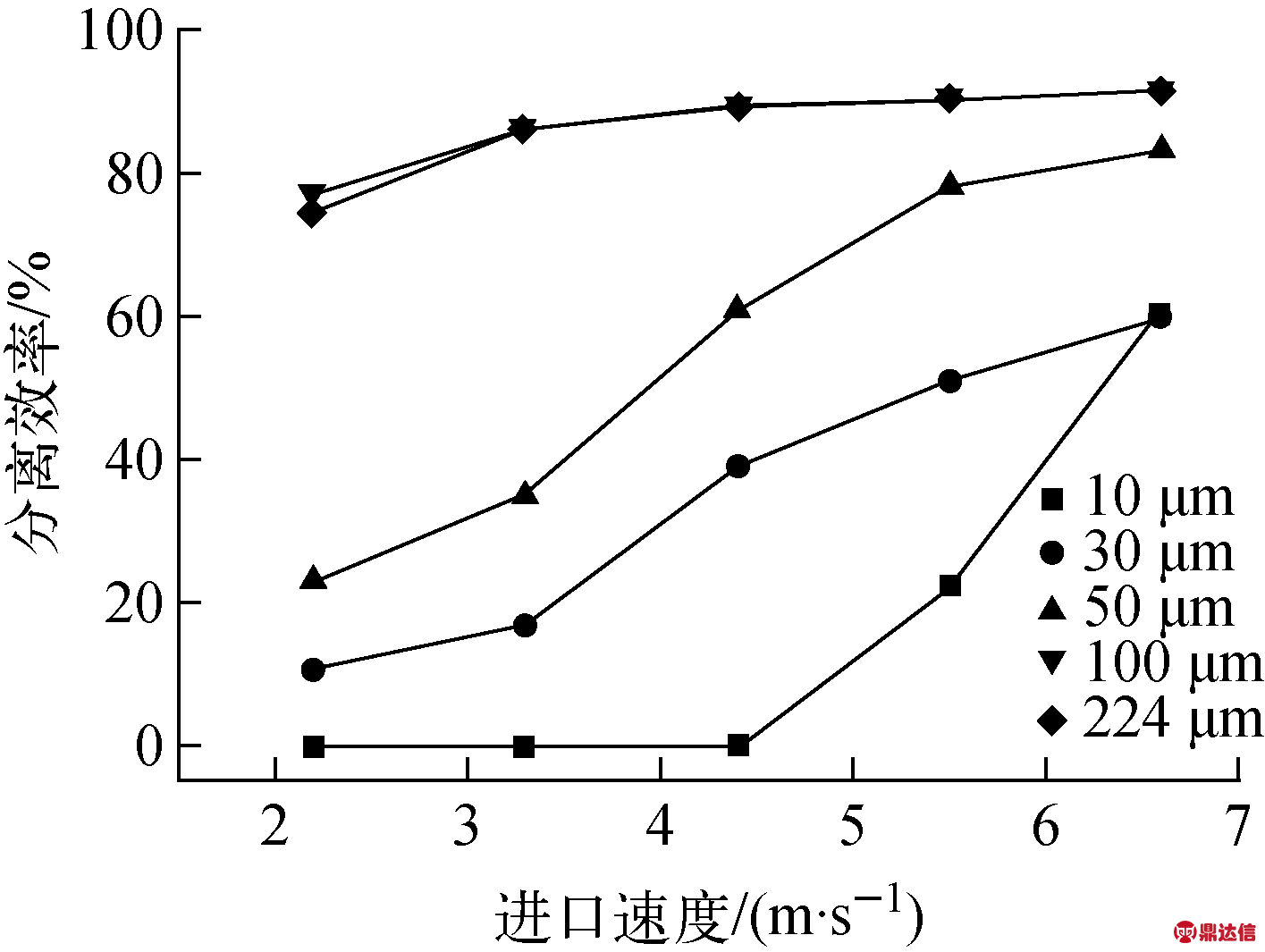
图6 分离效率随进口速度的变化
Fig.6 Variation of separation efficiency with inlet velocity
从图6可看出,流道内不同液滴直径下分离效率随进口速度的增大而增大,当进口速度大于5.5 m/s时,分离效率曲线平缓,分离效率受到液滴直径的影响较小。而液滴在10~50 μm这些粒径尺寸较小时分离效率受到进口速度影响较大,液滴尺寸较大的分离效率受到进口速度的影响相对较小。
3.2 液滴直径
以4.4 m/s为例,给出不同液滴直径下的液膜高度如图7所示。
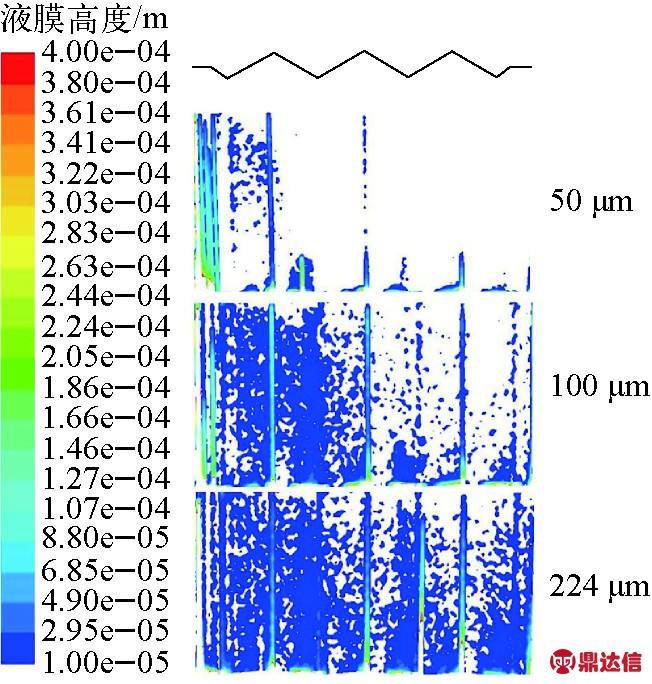
图7 不同液滴直径下的液膜高度
Fig.7 Liquid film heights of different droplet diameters
从图7可看出,随液滴直径的增大,板壁上产生液膜的面积和高度增大。当直径为50 μm时,液膜主要集中在第1级而且面积较小。当直径为100 μm时,液膜主要集中在前两级的波谷内,并且面积较大,显然100 μm时的效率会高于50 μm时的。这是由于直径较小时,液滴的惯性较小,容易被气流携带逃逸出波形板。当直径较大时,在波形板折弯时液滴不会随着气流做折弯运动,而会由于液滴的惯性作用撞击到板壁上,最终形成液膜。当直径为224 μm时,液膜主要分布在前两级,第3级也有部分液膜,液膜面积和质量是三者中最大的。
以4.4 m/s为例,统计出分离效率随不同液滴直径的变化如图8所示。从图8可看出,当进口速度一定时,随液滴直径的增大,波形板分离器的分离效率也增大。液滴直径较小时分离效率变化很大,当液滴直径大于100 μm时,分离效率变化非常小,且很高。这说明当直径大于100 μm时,液滴的惯性力已足够脱离气流去撞击到波形板上并被捕获。
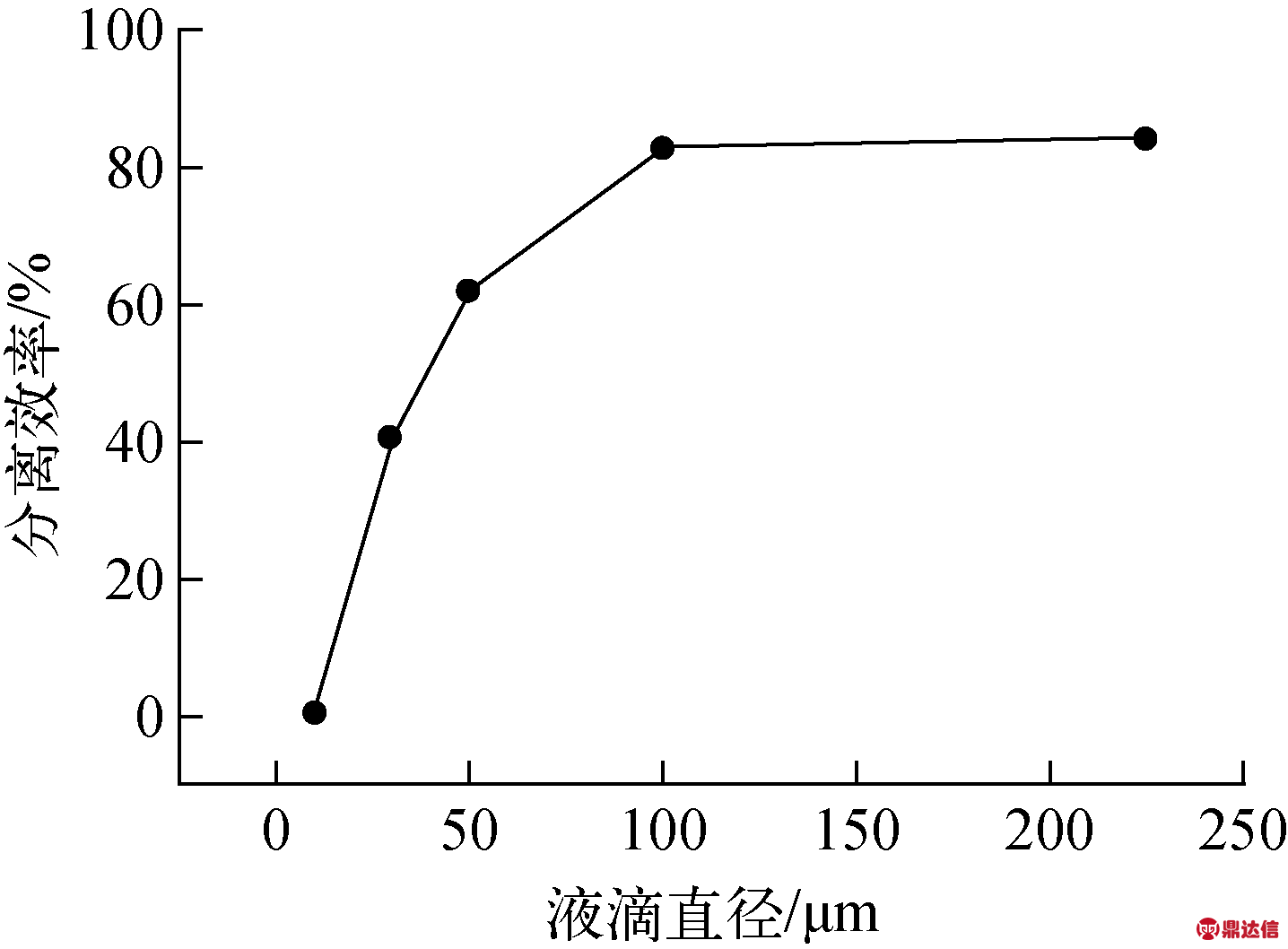
图8 不同液滴直径下的分离效率
Fig.8 Separation efficiencies of different droplet diameters
3.3 蒸汽湿度
对蒸汽湿度为5%、10%和20%进行数值模拟,结果示于图9。
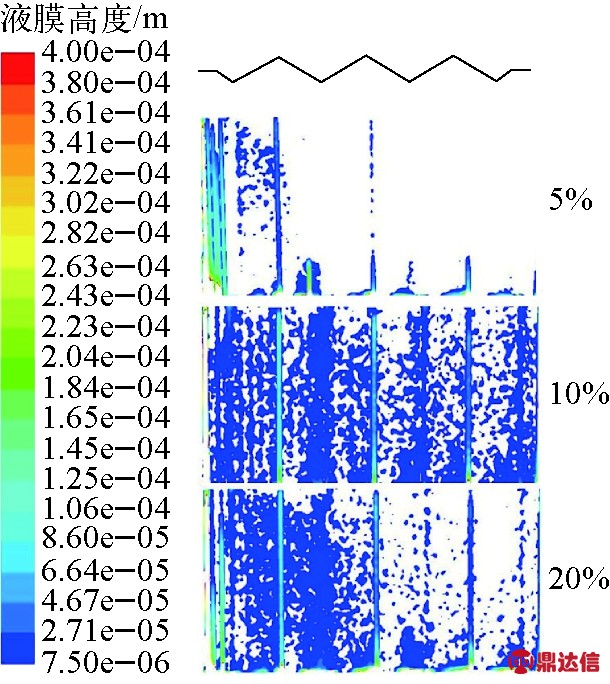
图9 不同蒸汽湿度下的液膜高度
Fig.9 Liquid film heights of different humidity
从图9可看出,湿度在5%~10%之间时,随蒸汽湿度的增大,板壁上产生液膜的面积增大且液膜高度增加。湿度在10%~20%之间时,随蒸汽湿度的增大,板壁上产生液膜的面积减小。当蒸汽湿度约为10%时,波形板更易捕捉蒸汽中的小液滴,即此时的分离效率最大。
以液滴直径100 μm为例,将蒸汽湿度5%、10%和20%时的分离效率进行对比,如图10所示。
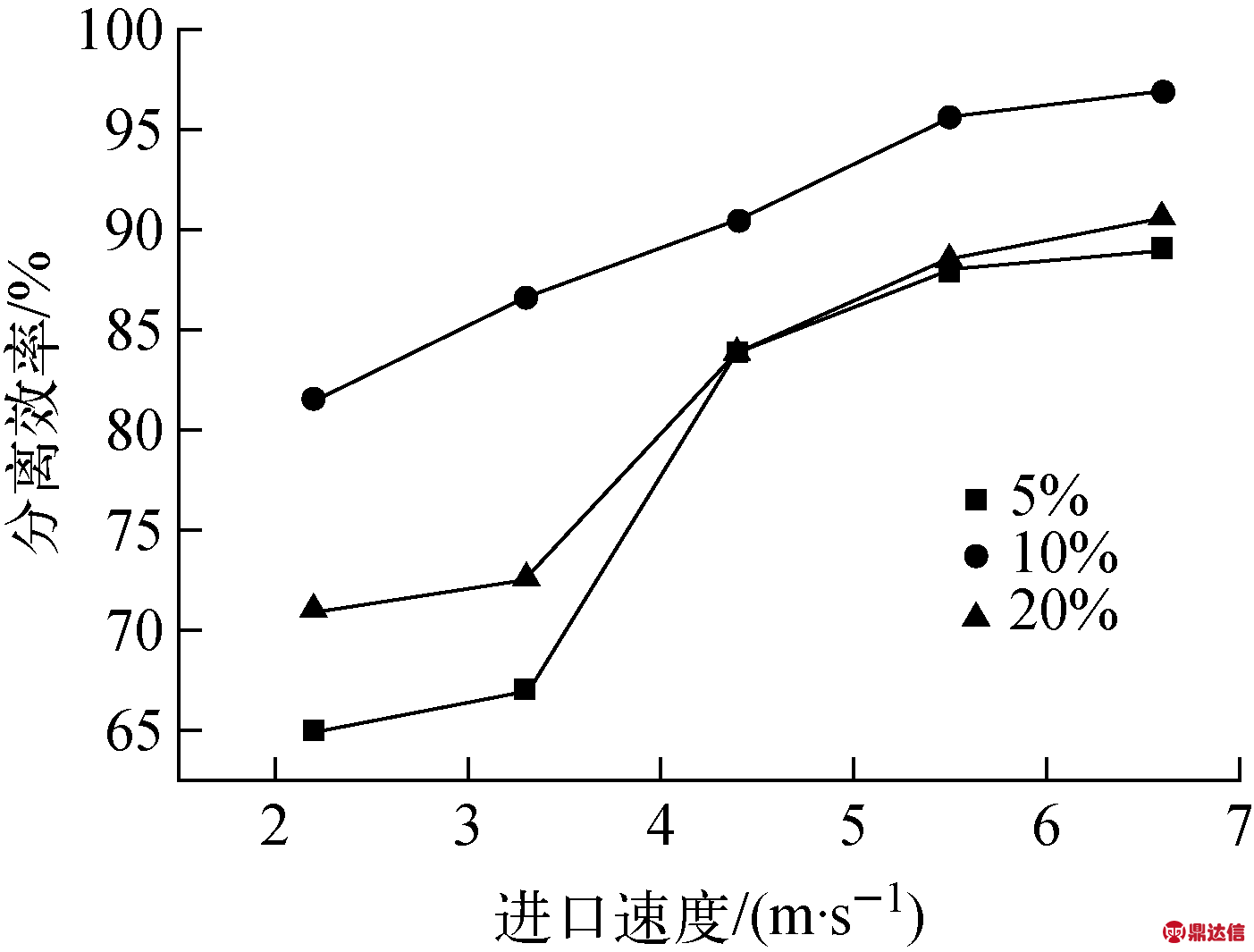
图10 不同蒸汽湿度下的分离效率
Fig.10 Separation efficiencies of different humidity
从整体上来看,无论在哪种蒸汽湿度下,分离效率均会随进口速度的增加而增大,并且当进口速度达到5.5 m/s后分离效率的变化较小。蒸汽湿度为10%时分离效率最大,20%时次之,5%时最小。这说明当蒸汽湿度为10%时,波形板更易捕捉到湿蒸汽中的小液滴。
4 结论
本文研究分析了液膜高度和分离效率与进口速度、液滴直径和蒸汽湿度的关系,主要结论如下。
1) 随进口速度的增加,板壁上产生液膜高度增大;液滴直径一致时,随进口速度的增加,分离效率增大;液滴尺寸较小时,分离效率随速度变化明显,尺寸较大时,受进口速度影响较小。
2) 随液滴直径的增加,板壁上的液膜分布面积、高度、质量逐渐增大。当进口速度和蒸汽湿度一定时,分离效率随液滴直径的增加而增大。
3) 随蒸汽湿度的增加,板壁液膜分布面积逐渐增大,分离效率也逐渐增大;当湿度达到10%后,板壁液膜分布面积会逐渐减小,随之分离效率也会减小。