摘要:设计了一种新型旋风分离器。相对于PV型旋风分离器,新型旋风分离器采用弧形导流板分隔进气的入口结构、 分流型排气的出口结构、 加长型的筒体和锥体的结构,有锥顶过渡段的灰斗结构,并匹配了合理的尺寸。 为了验证新型分离器的性能,设计并搭建新型结构和基准PV型旋风分离器的冷模对比实验装置,在入口气速为14.4~26.1 m/s、 入口含尘质量浓度为0.01 kg/m3时,同时测量2种分离器的效率和压降。 对比实验结果表明: 相对于基准PV型分离器,新型旋风分离器能够减小压降约32.36%,同时保证新型分离器的效率与基准效率相当。
关键词:旋风分离器;结构优化;分流型排气管;压降;分离效率
旋风分离器是一种常用的干式气固分离设备,在石油化工、煤化工、电力环保等各行业得到广泛的应用。在节能减排的大背景下,开发出能够大幅度减小分离器压降的新型旋风分离器有着非常重要的意义。然而,截止目前所研究和开发的旋风分离器都是从旋风分离器高度、排气管结构、入口结构、灰斗结构等单方面入手[1-2],导致改进的分离器效率和压降总是同时增大或减小,难以做到维持高效的同时减小压降[3]。鉴于此,设计了一种新型旋风分离器,综合了旋风分离器入口、排气管、筒锥及灰斗等结构改进的方法,使之在保持高效率的同时能够大幅度降低能耗,为开发新型旋风分离器及推广其工业应用提供新的思路。
1 新型旋风分离器的结构设计方案
旋风分离器的设计首先必须要解决选型的问题。由于在现有的绝大部分炼油厂流化催化裂化装置上采用的是高效PV型旋风分离器[4],并且其设计和应用较为成熟,性能的计算方法也较为完善,因此选则其作为新型分离器设计和对比试验的基准。
对于入口结构,根据时铭显等[5]提出的PV型旋风分离器的设计方法,设计为矩形截面;为了增加颗粒在分离器内的停留时间,设计为270 °蜗壳形式。并根据祝立萍[6]设计的进口弧形导向板,能够减小分离器的阻力损失;Lim等[7]在切流入口增加了一块挡板,内侧引入洁净气流,提高分离器效率;沈恒根等[8]设计了对称180 °蜗壳双进口的分离器,能够增加旋流的对称性和稳定性,提高分离器效率。综上研究得出入口结构改进的思路:在蜗壳式旋风分离器入口中间增加一块隔板,把入口气流分割成2个部分,并且保证隔板按照一定的包角与分离器筒体相切,以增加进气的对称性和旋流的稳定性。
对于排气管结构,其下口直径比对效率和压降有着双重影响,会同时影响分离器效率和压降[9],因此是分离器所有结构中最重要的参数之一,为了达到大幅度减阻的目的,必须要从排气管结构入手。
根据陈建义等[10]发明的PV-E型旋风分离器得出思路,新设计了一种加长型的分流型排气管。此种排气管整体包含了渐扩段、直筒段、二次渐扩段和出口直筒段。在排气管的筒体及锥体部分,沿圆周方向开有若干条狭缝,开缝角度为60 °,这些狭缝实际上起气流通道作用,极大地增大了气流的出口面积,因而可大幅度减小压降。这种开缝的方向和排气管外壁的切向呈一定角度,并与排气管内外气流的旋转方向相反,所以气流是经过急剧变向后才进入狭缝的,这样气流中夹带的颗粒因惯性能够再次得到分离;并且由于内旋流也具有较大的旋转动能,因此能够把夹带进入排气管的尘粒从缝中二次离心分离出去,从而确保整体压降大幅度减小的同时而分离效率不致下降。
对于分离器筒体及锥体高度,时铭显[11]发现适当地增加分离空间高度,能够延长颗粒在分离器内部的停留时间,使被卷吸到内旋流的颗粒再次分离,提升整体的分离效率,因此,本文中的设计为加长型的筒锥结构。并且,由于排气管设计部分设计了加长型的分流型排气管,也必须设计加长型的筒锥结构与之匹配。
对于灰斗结构,徐俊等[12]将灰斗的水平顶盖改为锥形过渡段,能够消除灰斗中的顶部灰环,提高效率。王成等[13]发现灰斗也存在最佳直径和最佳高度,其对分离效率有一定的影响,因此,设计了含特定尺寸的带锥形过渡段的灰斗结构。
新型分离器的各个主要结构的形式与基准PV型的对比如表1所示。
表1 新型分离器主要结构的形式与基准PV型的对比
Tab.1 Comparisons between the main structures of the new separator and the reference PV type
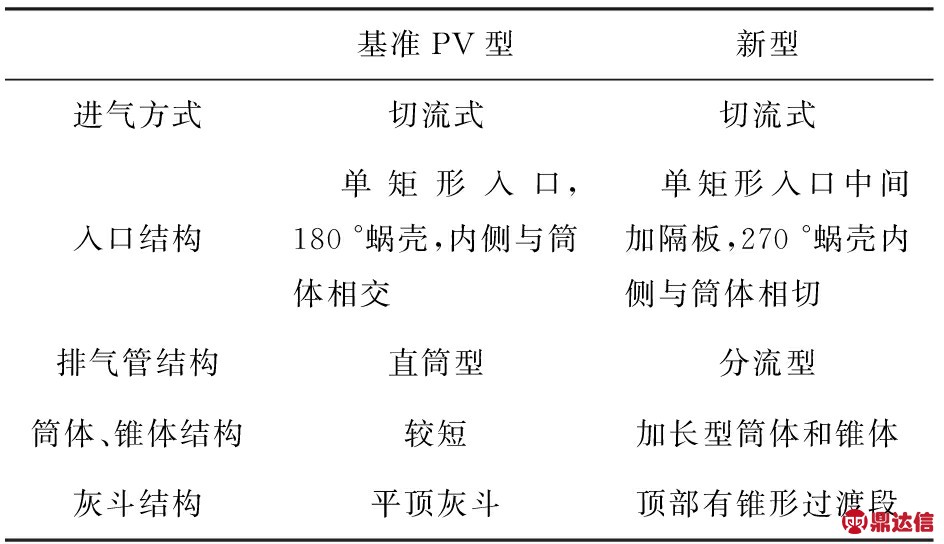
确定新型旋风分离器的结构形式以后,在基准PV型旋风分离器的基础上,将表1中的结构进行组合,就构成了新型分离器。表2列出了基准PV型与新型分离器的结构尺寸。
表2 两种分离器的结构尺寸
Tab.2 Main sizes of two kinds of cyclone separator
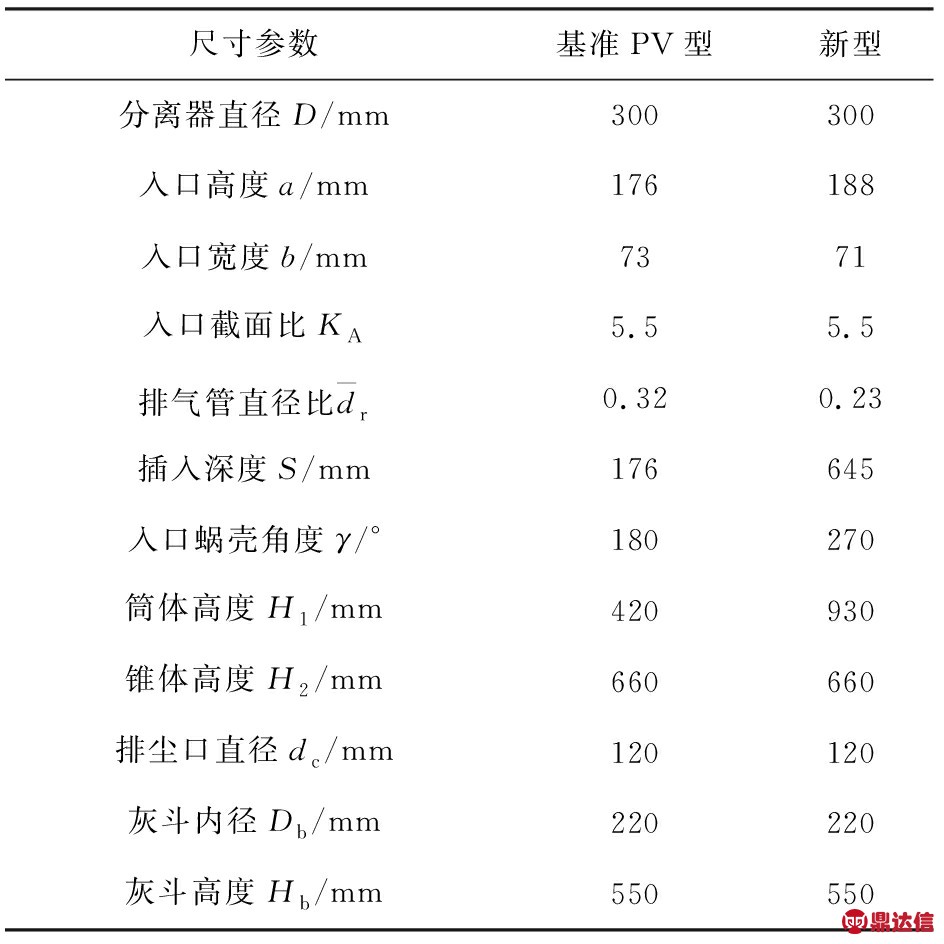
根据表2中的具体数值,设计出新型旋风分离器,其结构尺寸如图1所示。
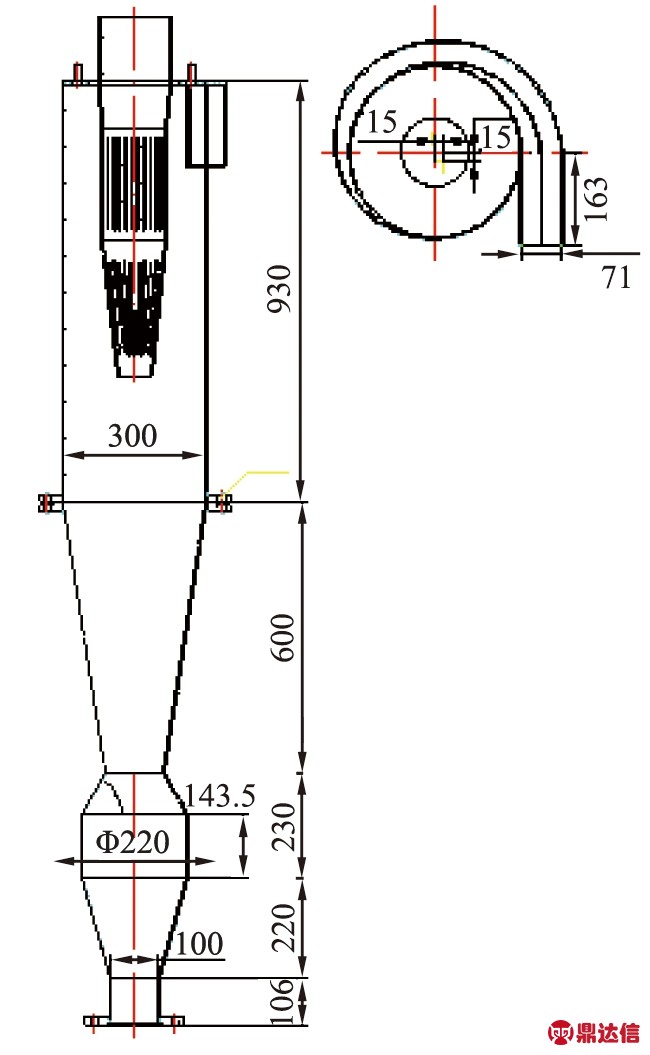
图1 新型分离器的结构尺寸
Fig.1 Structure dimension of new type of separator
实验中需要实时测量空气湿度与温度,保证实验在一个合适的环境中进行。本文中采用干湿球温度计来测定湿度与温度,测量时需注意保证湿球浸泡在水中。
旋风分离器的压降与入口气速用U形管压差计测量。在旋风分离器的入口、出口以及料腿位置都设有测压点,所有测压点的静压采用U形管压差计测定(见图2),压降为入口点静压与出口点静压之差。
2 实验验证
2.1 实验装置
为了研究不同结构旋风分离器的分离效果,采用新型结构与基准PV型对比试验的方法。并且,为了排除各种操作参数和粉料物性参数的影响,本实验安排在操作条件完全相同时,用同一种粉料在同一时间完成2种分离器的对比实验。实验系统如图2所示,主要由通风系统、加料系统、旋风分离器模型和测试仪器仪表组成。
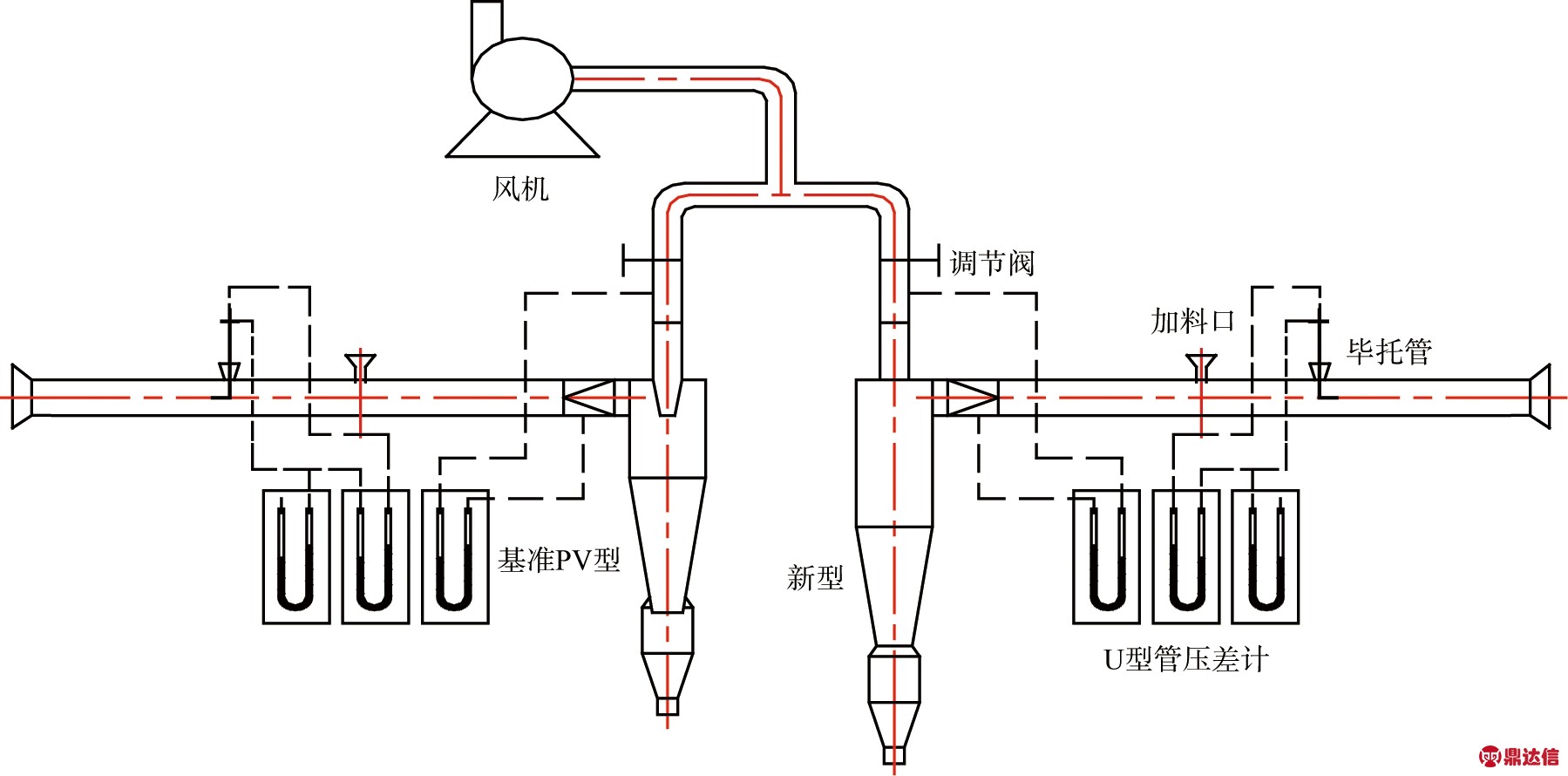
图2 实验系统示意图
Fig.2 Schematic diagram of experimental facility
2.2 实验参数测量方法
为了研究新型结构旋风分离器分离性能,采用滑石粉为实验粉料,采用常温负压操作,测量并比较滑石粉在入口质量浓度为10 g/m3,入口气速分别为14.4、 17.6、 19.6、 21.4、 26.1 m/s时的分离效率和压降值。
滑石粉颗粒的形状是不规则非球形,用比重瓶测其颗粒密度为2 780 kg/m3。用Eyetech激光粒形粒度仪测定其球形度为0.76,中位径为12.5 μm,粒径分布如图3所示。
采用标准毕托管测量入口气速Vin,如图4所示,需要经过以下换算得到最终的入口气速。
毕托管测量点的气体流速
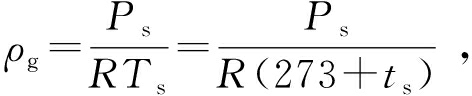
(1)
式中:Δh为毕托管动压,Pa;ρg为气体密度,kg/m3。
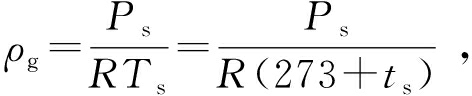
图3 滑石粉的粒度分布
Fig.3 Particle size distribution of talcum
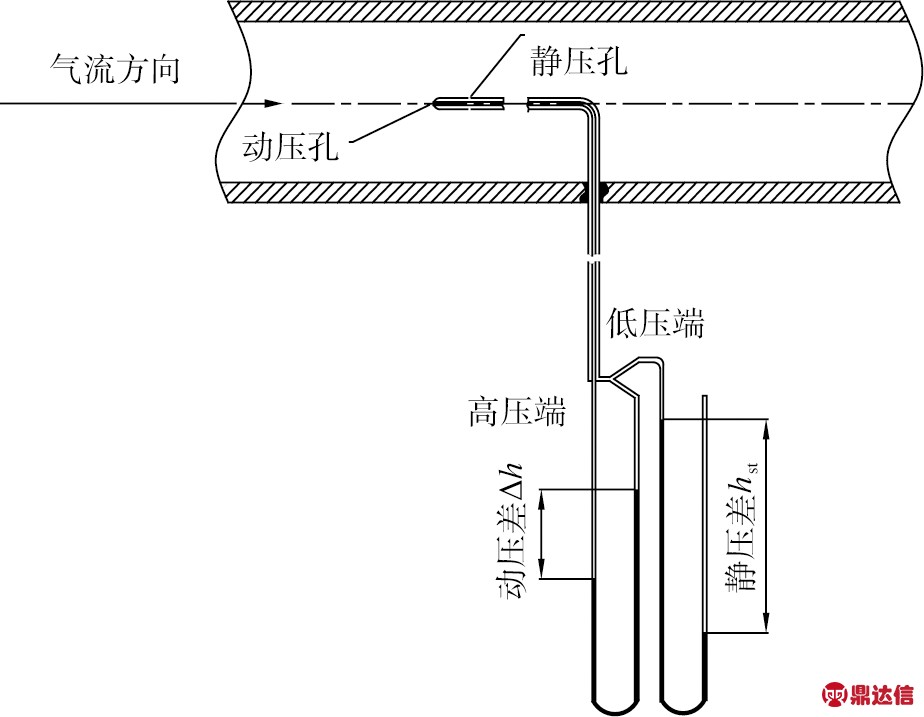
图4 毕托管测速方法示意图
Fig.4 Schematic diagram of velocity
measurement method of pitot tube
设管道内气体处于湍流状态,管道内平均气速与最大气速Vg的比值一般为0.84~0.86,取平均值0.85,则通过管道的流量

(2)
式中d为入口管道直径,m。
根据理想气体状态方程有
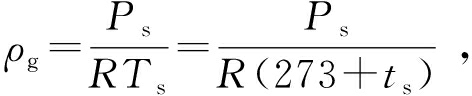
(3)
式中:Ts为绝对温度,℃;ts为大气温度,℃。
实验采用负压操作,故Ps=Pa-ps,大气压力Pa=0.101 3 MPa,在常温条件下,空气的气体常数R≈286 J/(kg·K),则

(4)
式中:ps为毕托管静压,Pa。
通过Vin与Qin的关系可得入口气速为
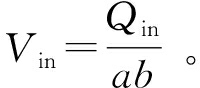
(5)
分离效率E由称重法确定,
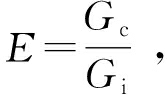
(6)
式中Gc、Gi分别为收料量和入口加料量,kg。
入口加料与最终收料质量采用TSCALE电子秤,其量程为0~30 kg,精度为0.1 g。
2.3 实验步骤
1)实验前做好实验准备,检查实验装置系统是否正常,用电子秤准确称量设定质量的粉料,并采用实验粉料对其进行跑合。
2)记录实验环境的温度、湿度,检查测量系统是否正常运行。
3)打开离心风机,通过毕托管测试观察调节阀门开度,使得入口气速达到实验值,通过U形管差压计,读取入口静压、 进出口压降及料腿压降。
4)通过加料器将粉料连续、均匀地加入入口水平管道,开始进行旋风分离实验。实验中要保证在规定的时间内将所有的实验粉料连续、均匀地加入到旋风分离器,待粉料全部加入到旋风分离器内后关闭风机。
5)待旋风分离器内气流完全消失,颗粒完全沉降下来后,打开收料斗收料,使用电子秤称量粉料质量。
3 结果与分析
3.1 新型分离器优化结果
新型与基准PV分离器的实验结果对比如图5所示。对于压降,新型分离器的压降较基准PV型分离器下降幅度明显,并且随着入口气速的增加,这种下降的幅度也越来越大。在入口气速为14.4 m/s时,压降数值减小了550 Pa,降幅为31.25%;在实验入口气速最大为26.1 m/s时,此时压降数值减小最多,为1 720 Pa,降幅为29.60%;而在这2个速度之间压降的平均降幅为32.36%。
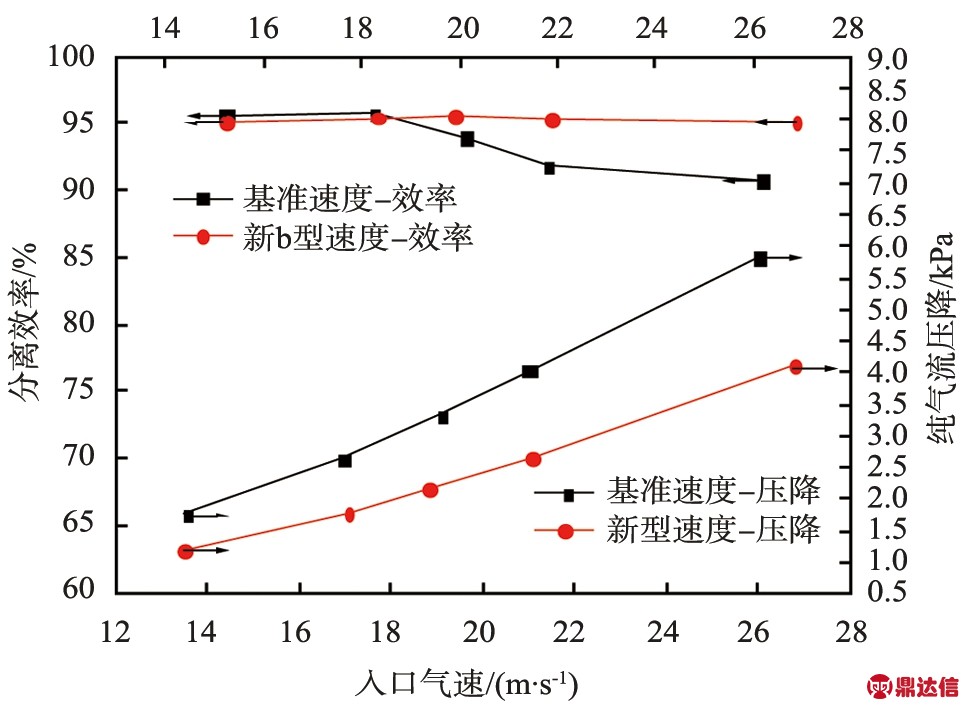
图5 新型与基准PV分离器实验结果对比
Fig.5 Experimental results of new
separator and reference separator
新型分离器的效率开始略微低于基准PV型分离器的效率,但是随着入口气速的增加,效率的差值也越来越小;待入口气速大于18.2 m/s时,新型分离器的效率全部高于相同气速下基准PV型分离器的效率,并且随着入口气速的增加,效率的差值越来越大。在入口气速为19.6 m/s时,新型分离器效率较基准提高了约1.6%,效果非常明显。
按照设计要求,分离器最重要的指标是其最高效率点。由图5可以看出,新型分离器的最高效率点对应的入口气速为19.4 m/s,对比基准PV型分离器为17.6 m/s,所以在入口面积相同时,新型分离器的处理量明显大于基准PV型分离器。对于最高效率的具体数值,新型分离器的效率为95.5%,较基准型降低了约0.1%,降低的数值非常小,因此可以认为2种分离器效率相当;同时在此入口气速,新型分离器的压降较基准型降低了约1 390 Pa,降幅达到了34.33%。
综合考虑新型分离器的压降、效率可以看出,新型结构相对基准PV型分离器有着明显的优势,能够在保证分离器高效率的同时大幅度降低了分离器的压降,并且能够提升分离器的处理量,最终达到高效低阻的目的。
3.2 新型分离器优化结果原因分析
通过以上实验结果可以看出,新型分离器达到了高效低阻的目的,能够在保证分离器有着高效率的同时大幅度的降低分离器的压降,具体的原因分析如下:
1)首先设计了一种加长型的分流型排气管。这种分流型排气管整体包括了上端直筒段和下端锥体段,并且在排气管的筒体及锥体部分,沿圆周方向开有若干条纵向狭缝。这些狭缝实际上起到了气流通道的作用,极大地增大了气流的出口面积,使气流的整体出口面积变为仅排气管底端开口时的6.2倍,使分离器内的轴向速度降低了很多,进而减小了气流在分离器内部的动能损失,因而可以大幅度减小压降[14-15]。
排气管外壁开缝的方向和切向呈60 °,并与分离器内部气流的旋转方向相反,如图6所示,所以气流在进入狭缝之前必定会急剧变向,这样气流中原来夹带的颗粒就会因惯性再次被分离而难以进入狭缝;并且内旋流由于也具有较大的旋转动能,因此能够把夹带进入排气管的尘粒从缝中二次离心分离出去[16],从而确保整体压降大幅度降低的同时而分离效率不致下降。
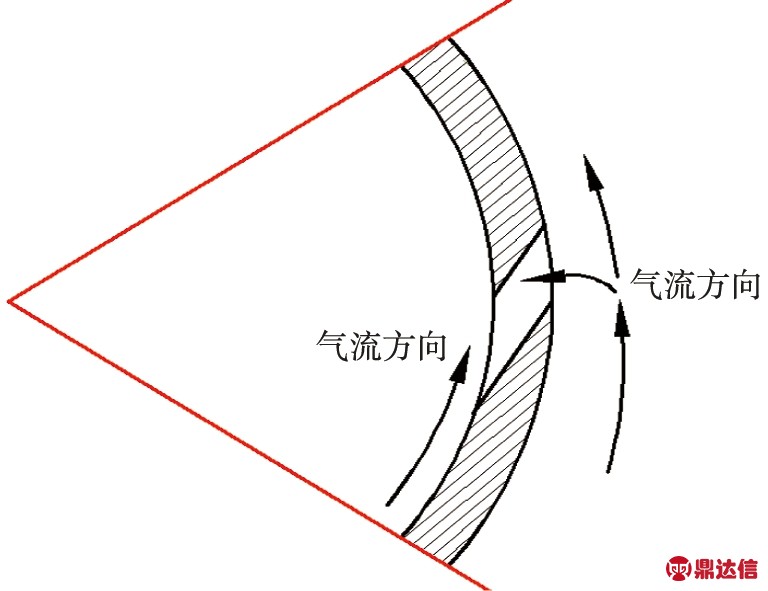
图6 排气管缝隙示意图
Fig.6 The diagram of gap in diverged vortex finder
2)新型结构设计的入口结构形式采用270 °的蜗壳矩形入口形式,并在分离器入口中间增加了一块隔板。此设计能够增大气流的入口动量矩[17],并且能减小入口来流与回转气流的相互挤压作用和混掺现象,减弱分离器顶部环形空间的短路流,也缩短了内侧尘粒达到器壁的时间。而且更加均匀的进气方式增强了分离空间流场的对称性及底部旋流的稳定性,抑制了锥体段的摆尾现象和底部的窜流返混,故此,新的入口结构设计能够提升分离器的效率。
3)设计了顶部有锥型过渡段的灰斗,削弱了灰斗顶部的上灰环[18],因此能够减弱灰斗中气流的返混夹带,提升分离效率。
4)设计了加长型的筒体和锥体结构,使之与加长型的分流型排气管相匹配。筒体和锥体的增长能够增加分离空间的高度,因此能够延长颗粒在分离器内部的停留时间,并且分离空间的增长能够增加自然旋风长度,使被卷吸到内旋流的颗粒再次分离,能够提升分离器的分离效率[19]。
4 结论
为了减小分离器压降,同时保证分离效率不降低,设计了一种新型的旋风分离器。新型分离器采用了弧形导流板分隔进气的入口结构、分流型排气的出口结构、加长型的筒体和锥体的结构,有锥顶过渡段的灰斗结构。
通过与基准PV型旋风分离器的对比试验,以及对新型分离器中具体结构部分的分析,可以得出如下结论:
1)对于直径为的新型分离器,能够大幅度的地减小分离器的压降,平均降幅约为32.36%。随着入口气速的增加,新型分离器较基准PV型分离器压降减小的幅度越来越大。
2)相较于基准PV型分离器,新型分离器的分离效率曲线更为平缓,因此有更好的操作弹性。随着入口气速的增加,整体效率先增加再减小。入口气速大于18.2 m/s时,新型分离器的效率高于相同气速下基准PV型分离器的效率,且随着入口气速的增加,效率的差值也越来越大;如在入口气速为19.6 m/s时,新型分离器效率较基准提高了约1.6%。
3)新型分离器的最高效率点对应的入口气速为19.4 m/s,对比基准PV型为17.6 m/s,所以在入口面积相同时,新型分离器的处理量明显大于基准PV型分离器。对于最高效率的具体数值,新型分离器的效率为95.5%,较基准降低了约0.1%,降低数值非常小,因此认为2种分离器效率相当。
综上所述,在一般的工业运用场合,新型分离器能够在大幅度降低分离器压降的同时,保证分离器有95%左右的高效率,且能提升分离器的处理量,具有良好的操作弹性,因此拥有广泛的应用前景。