摘要:针对过滤分离器集水槽油水界位液位测量的实际问题,设计了新型传感器并搭建了检测系统。系统硬件部分主要包括动态微小电容采集模块、主控芯片模块、RS485转换模块和电源模块,软件部分主要包括电容检测芯片Pcap01的基本配置、主控芯片ATmega128与芯片通讯及数据处理、上位机液位计算程序等。多组实验证明传感器系统的精度较高,灵敏度较好,整体误差控制在3%以内,可满足过滤分离器集水槽油水界位液位的快速、高精度测量要求。
关键词:过滤分离器;油水界位;传感器;电容测量;Pcap01;STM32F407
0 引言
在野外油库收、发油管路中安装的过滤分离器采用卧式结构,流量范围在100~150 m3/h,实时流量大,作业时间长,一次性收发量大,且由于油源复杂、质量较差,所过滤出的游离水含量较多,水分会逐渐积聚在底部沉淀槽中,若游离水超过一定量后,使得过滤分离器油水分离性能下降,影响过滤出的燃料质量[1],因此需对此类过滤分离器沉积水进行监控。
过滤分离器集水槽水位的检测属于油水界面的检测问题,目前油水界面的检测方法有多种,各有优缺点。过滤分离器本身的实际工况及条件对油水界面检测提出了具体需求:在有工作压力的动态工况条件下,实现对油水界面的水位检测;量程应满足集水槽的高度要求;其不能出现机械运动部件,以确保稳定工作。综上,很难找到一种完全适用于过滤分离器集水槽油水界位检测的方法。因此,本文针对实际问题,设计了过滤分离器集水槽油水界位传感器,主要解决过滤分离器集水槽水位在线、实时检测问题,为实现过滤分离器运行状态监控以及实现排水的自动控制提供一种检测方法。
1 分段阵列式极板电容油水界位传感器设计方案
文献[2-4]及实验验证,油和水的相对介电常数存在较大差异,室温下,二者之间存在将近40倍的比例关系,因此,基于介质相对介电常数不同的原理进行油水分界面的液位检测是可行的。但实际上,针对过滤分离器的使用工况,这种方法仍然不能满足实际要求。温度会影响介质的相对介电常数,喷气燃料和水的介电常数都会随温度的变化发生改变;存在着电容值与液位高度间的非严格线性关系的测量原理误差,且无法得知实时介电常数。
1.1 总体设计方案
利用多组极板阵列取代单一极板对的形式,逻辑上将测油段、测水段、测油水分界面段分开,各段独立,几段同时测量各相。根据实际使用量程,从上至下,共分为5段1/5量程(均为30 mm)的极板电容,每个电容结构相同,相互绝缘并独立引线,每段独立检测电容,通过多个极板型电容传感器的测量结果判断并最终计算油水分界面的位置,如图1所示。
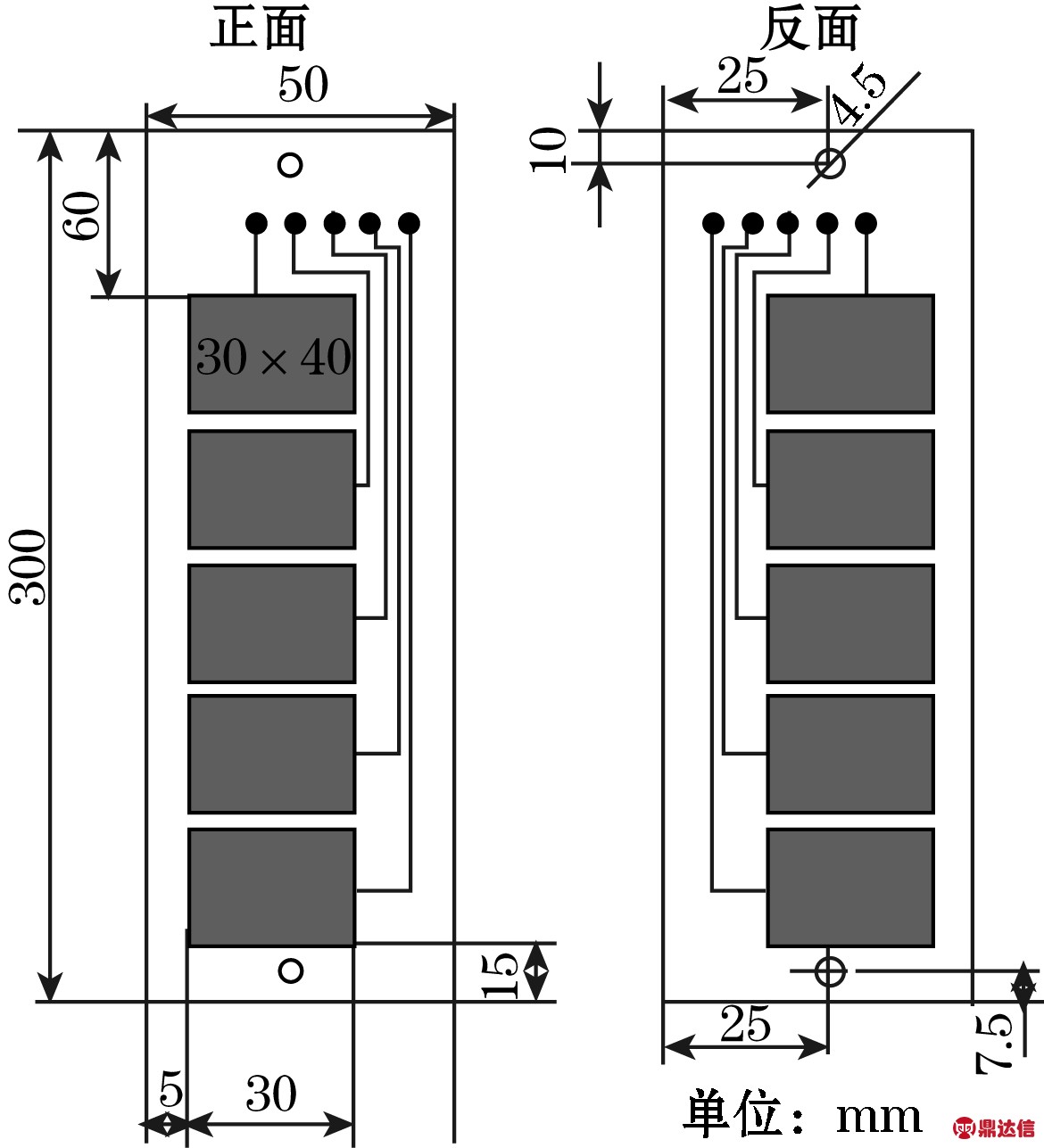
图1 分段阵列式极板电容传感器结构图
电容极板材质选择铜金属片;传感器极板结构采用双面PCB板,PCB板的材料为环氧玻纤;为保证极板间相互绝缘、不漏电,在整块极板表面喷涂一层绝缘材料,绝缘材料的选择应防止极板间油、水两种介质不会在极板上停留,以造成“虚假”液位。综合考虑,选择聚四氟乙烯作为绝缘材料。聚四氟乙烯性能优异:温度适用范围广,防粘性好,化学稳定性和耐腐蚀性强,可满足使用要求,保证传感器的稳定性。
1.2 检测原理
由设计结构图,传感器等效为在量程范围内划分成m个1/m的独立微小液位计来共同测量整个量程范围内的总液位,通过m个极板电容的测量结果,最终判断油水界面的位置和对应的水位高度。
当极板上喷涂绝缘材料后,充满介质油部分和充满介质水部分的每个极板电容都被分成了3部分。当极板中充满油时,如图2所示,该极板的电容由电容C10(介质为油)、C11(介质为绝缘涂层)、C12(介质为绝缘涂层)3部分组成,极板间含介质油的总电容值C1可以看做是以上3个电容并联而成,同理,极板间含介质水的总电容值C2可以看做是C20(介质为水)、C21(介质为绝缘涂层)、C22(介质为绝缘涂层)3个电容并联而成。则总电容值C的值为

(1)
式中:ε0为真空的介电常数;ε0=8.854×10-12 F/m;ε1、ε2、ε3分别为油、水、极板绝缘层的相对介电常数。
如图2所示,极板从上到下5段电容的等效电容分别为C1、C2、C3、C4、C5,介质油处在上部两块极板中,电容值为C1、C2,介质水处在下部两块极板中C4、C5,而中间段中含有油、水两种介质,存在一油水分界面,对应的电容值为C3。根据油、水的介电常数的差异,则不同段的电容值也会不同,由于水的相对介电常数远远大于油的相对介电常数,则可得到:C1=C2<C3<C4=C5,通过测量得到C1~C5的电容值,则可判断出各段极板间介质情况及油水分界面所处的位置,油水分界面水位的高度A0为
A0=LX+2H+2d0
(2)
式中:d0为竖直方向上两块相邻极板的距离;H为一组平行极板的高度;LX为油水分界面所在段的水位高度。
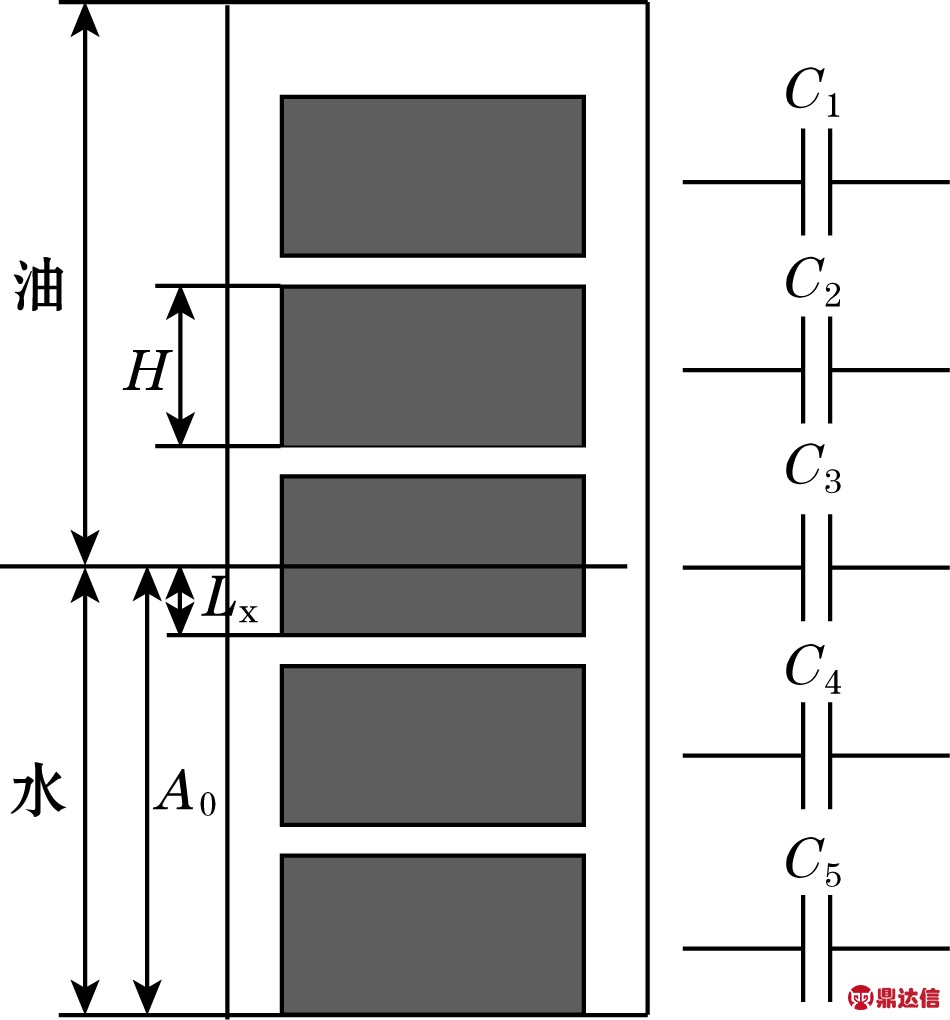
图2 电容传感器结构及等效电路图
最终液位值A0与LX、H、d0相关,H、d0也可认为常数,则A0只与LX的测量精度有关,这极大提升了油水界面的液位测量精度。
为得水位位置及高度,需据各段电容值求得介电常数,此过程较复杂且中间环节多、杂散及寄生电容都会影响到精度,故提出一种界面计算方法。据式(1)及图2,通过极板满油、满水及有油、水两种介质的实时电容值间的差值、比值运算,消除杂散、寄生电容的影响,即:
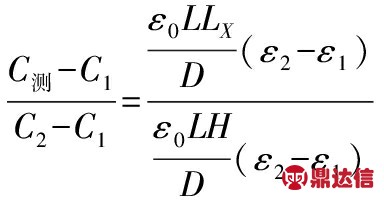
(3)
化简可得:
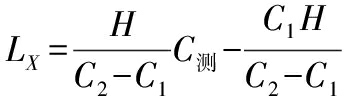
(4)
式中:C测为油水分界面所在段测量得到的混合介质实时产生的总电容值;C1为油水分界面所在段充满介质油时的电容值;C2为油水分界面所在段充满介质水时的电容值。
2 分段阵列式极板电容油水界位传感器的实现
2.1 传感器的总体构成
传感器的总体系统构成如图3所示,分段阵列极板电容作为敏感元件实现液位到电容的转换,通过Pcap01芯片进行电容的高精度检测,数据通过SPI总线送至ATmega128a主控芯片处理并经转换模块转成RS485信号制,严格遵循Modbus RTU 协议,最终送至上位机进行数据处理,通过滤波处理和算法计算得到最终的液位值,数值通过4.3″(1″=2.54 cm)电容触摸LCD屏进行显示;同时将数据送至PC机,通过Modbus Slave软件对传感器传出的数据进行监测,对传感器进行测试和调试。
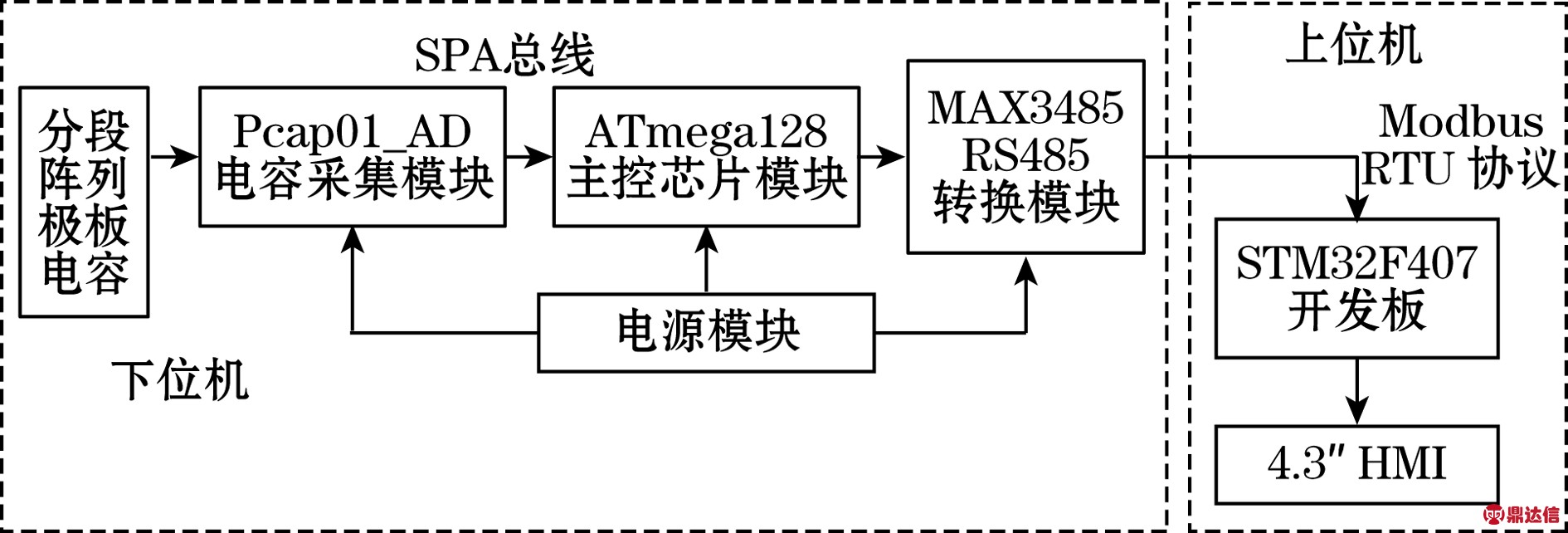
图3 传感器总体系统框架
2.2 硬件设计
硬件设计主要包括动态微小电容采集模块、主控芯片模块、RS485转换模块和电源模块,这几部分构成了传感器系统的下位机。其中电容检测模块是系统硬件设计的关键,直接影响到传感器检测的线性度、精度和重复性等指标。
2.2.1 动态微小电容检测模块
动态微小电容检测模块主要由Pcap01_AD芯片构成检测电路,如图4所示。根据前期的实验结果,基本确定了所设计分段阵列检测极板的电容范围大致处于[18~2 000 pF]区间;所选芯片基于PICOCAP专利技术,内置48biteDSP处理器,通过简单的外围电路配置,就可实现低功耗、高精度微小电容的快速检测;检测精度可达6 aF(在5 Hz和10 pF基础电容下),检测范围从几fF到几百nF级,完全满足实际测量要求。
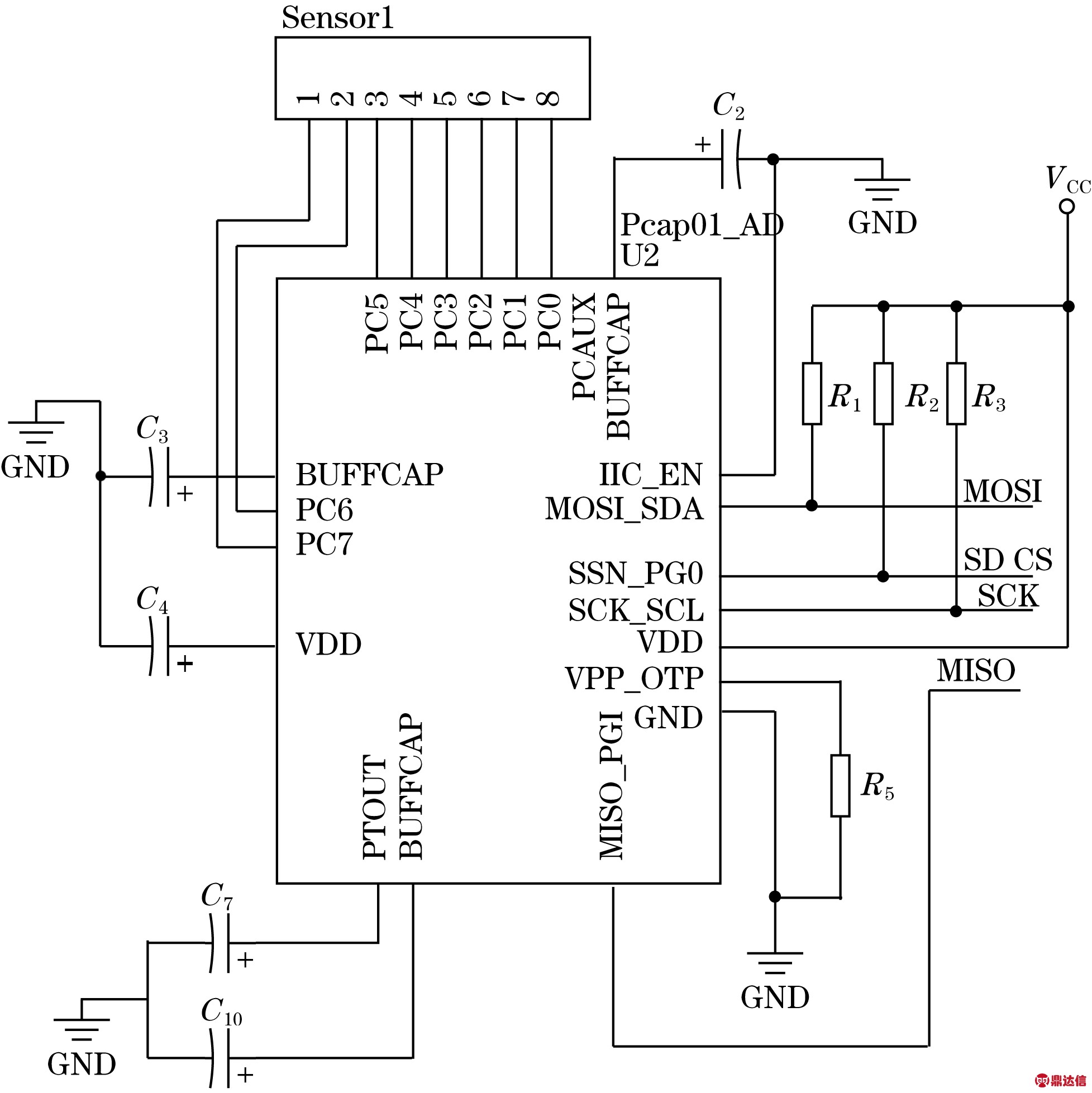
图4 Pcap01_AD动态微小电容检测电路
为提升抗干扰特性,传感器的连接选择单一传感器的漂移模式,极板电容和参考电容分别与芯片的PC引脚连接;利用内置的RDC测温模块的片上电阻测温,PTOUT外接33 nF的COG电容后并接地,PT0、PT2REF引脚悬空;极板电容与参考电容组成一个Low-Pass滤波,芯片通过测量充放电时间来测量微小电容,直接输出24位数字信号,无需AD转换,并通过MOSI_SDA、SCK_SCL、SSN_PG0、MINO_PG1四条SPI总线跟单片机完成通信,以实现对芯片的读写控制和电容数据的传输;通过连接接地电容,补偿内、外部寄生电容,减少PCB板的走线,进一步减小寄生电容[5]。
2.2.2 主控芯片模块
主控芯片选择ATMEL的基于AVR内核RISC结构的8位低功耗、高性能配置单片机,内置128K可编程Flash、2个可编程串行USART、4KE2PROM、4KSRAM等丰富的片上资源,运算速度快,稳定性极佳,适合在野外极端恶劣条件下使用,符合过滤分离器的实际使用条件。
主控芯片模块电路如图5所示。由ATmega128芯片构成最小系统,通过SPI接口电路与Pcap01芯片连接,配置外部晶振电路和按键复位电路。该模块主要实现与Pcap01芯片的通讯,控制测量循环过程,对测量数据的读取与处理,并打包发送,实现与上位机的数据交互。
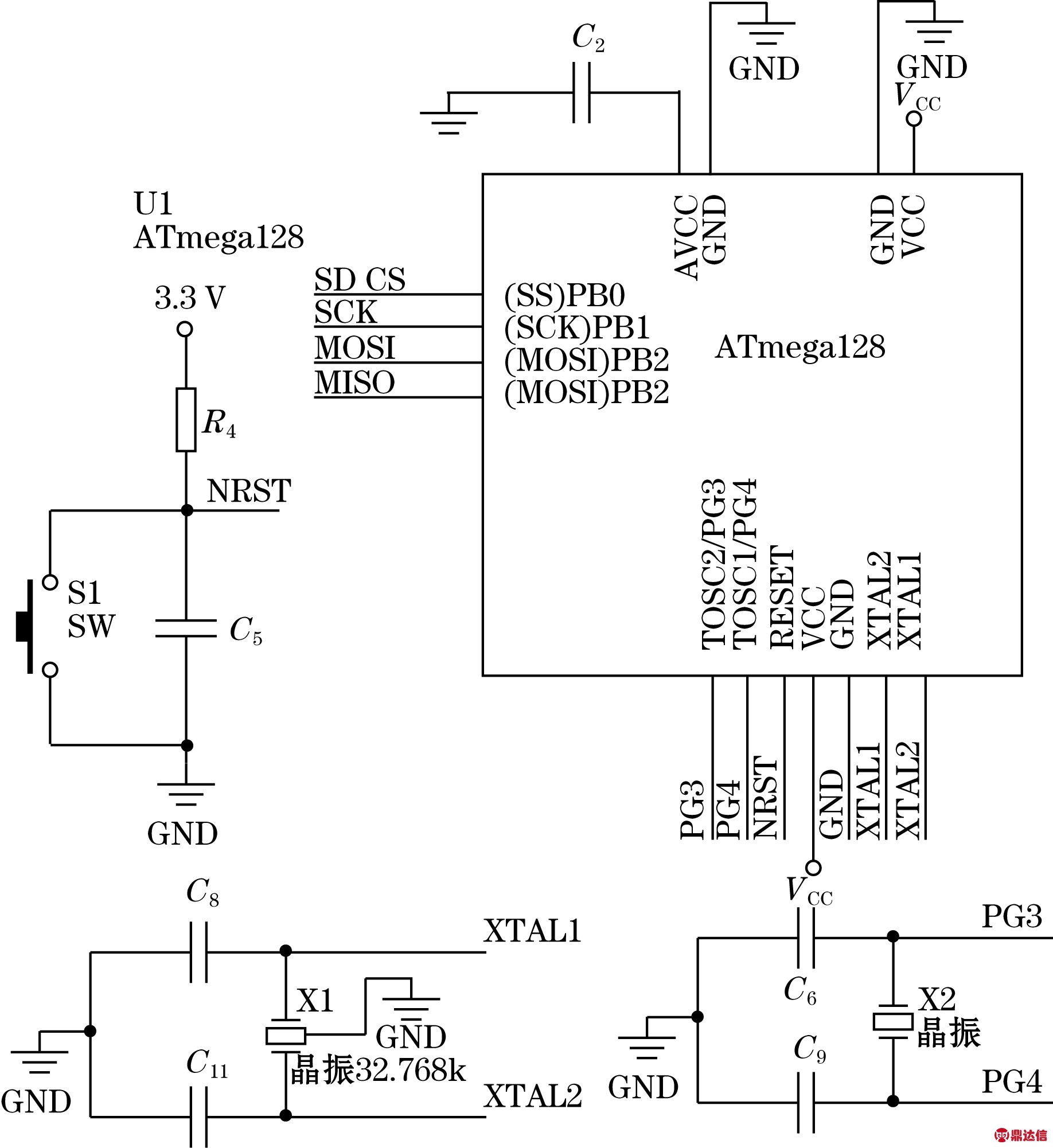
图5 ATmega128主控芯片电路
2.2.3 通讯模块
数据采集与处理流程大致为:电容检测芯片测量得到电容值的数字量,由主控芯片处理,电容检测电路接口遵循标准ModBus协议RTU模式,通过RS485接口通讯将电容信号数据发送给上位机。主控芯片对采集到的电容数字量按照ModBus协议进行处理,采用MAX3485芯片组成RS485转换电路,实现低功耗、高效率的无差错信号传输;RS485串口通过两线制的半双工方式工作,抗干扰能力强,传输距离长,最终上位机通过转换后将信号进行处理显示[6]。
2.3 软件设计
系统的软件设计主要包括电容检测芯片Pcap01的基本配置、主控芯片ATmega128与电容芯片通讯及数据处理、上位机液位计算程序等。软件的总体流程如图6所示。首先,对Pcap01芯片完成基本寄存器和标准固件固化等配置,然后配置主控芯片ATmega128时钟、I2C模块等实现与芯片的控制和通讯,通过芯片将电容数据进行采集,遵循Modbus RTU协议将数据传送至基于STM32F407的开发板,开发板通过Keil软件使用C语言进行数据接收处理、液位判断计算等相关程序编写,配置显示屏实现液位数据显示;同时数据传至PC机通过Modbus Slave监测。各部分间的通讯基于Modbus通讯协议,并按照RTU通讯模式进行通讯,实现包含液位信息的电容数据从下位机顺利传输到上位机进行显示。根据检测原理,根据五段电容值的比较判断确定油水分界值,根据分界线计算固定补偿值,并根据分界线最终计算得到油、水均值以得到实际液位值[7]。
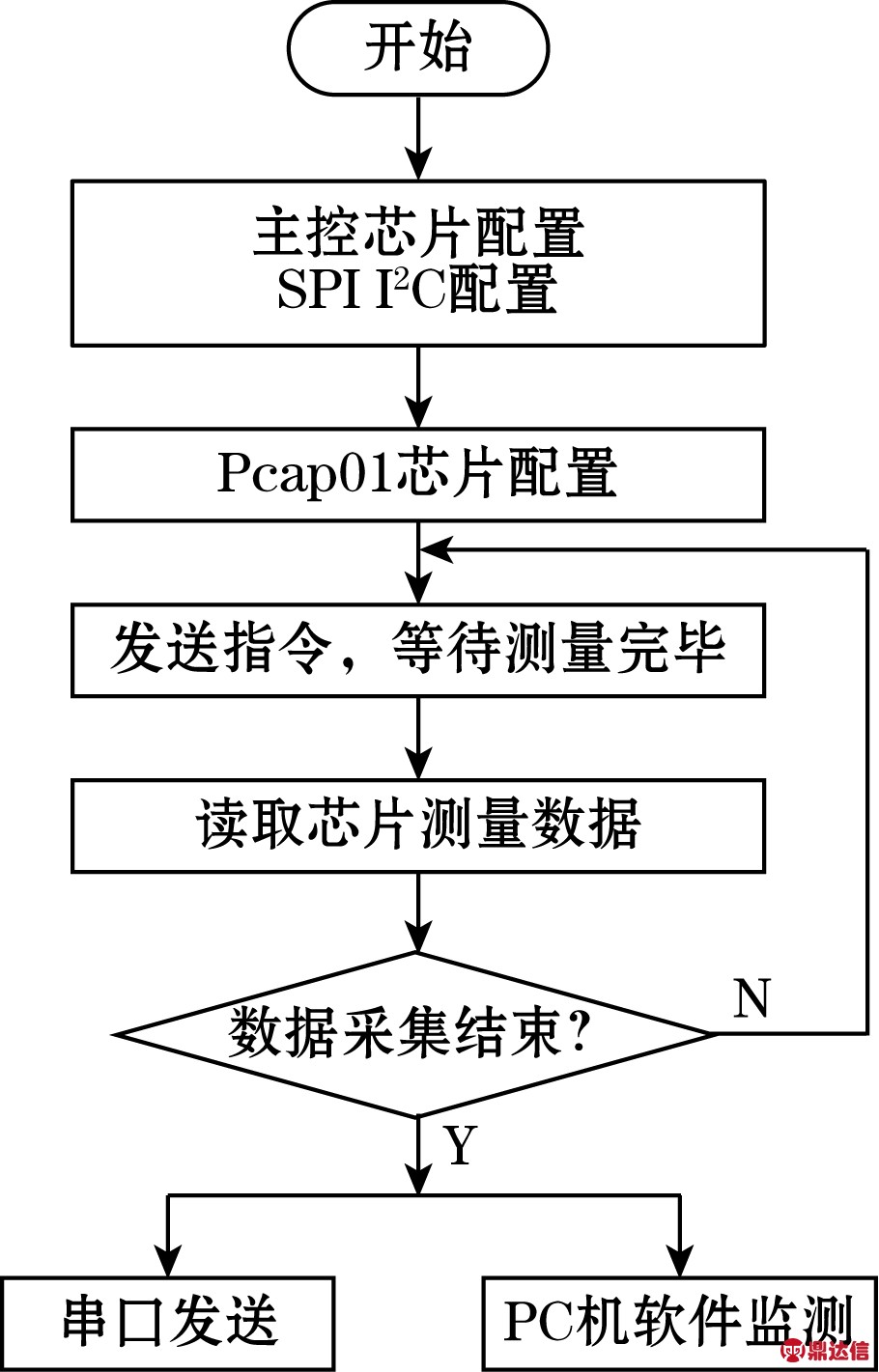
图6 软件总体流程图
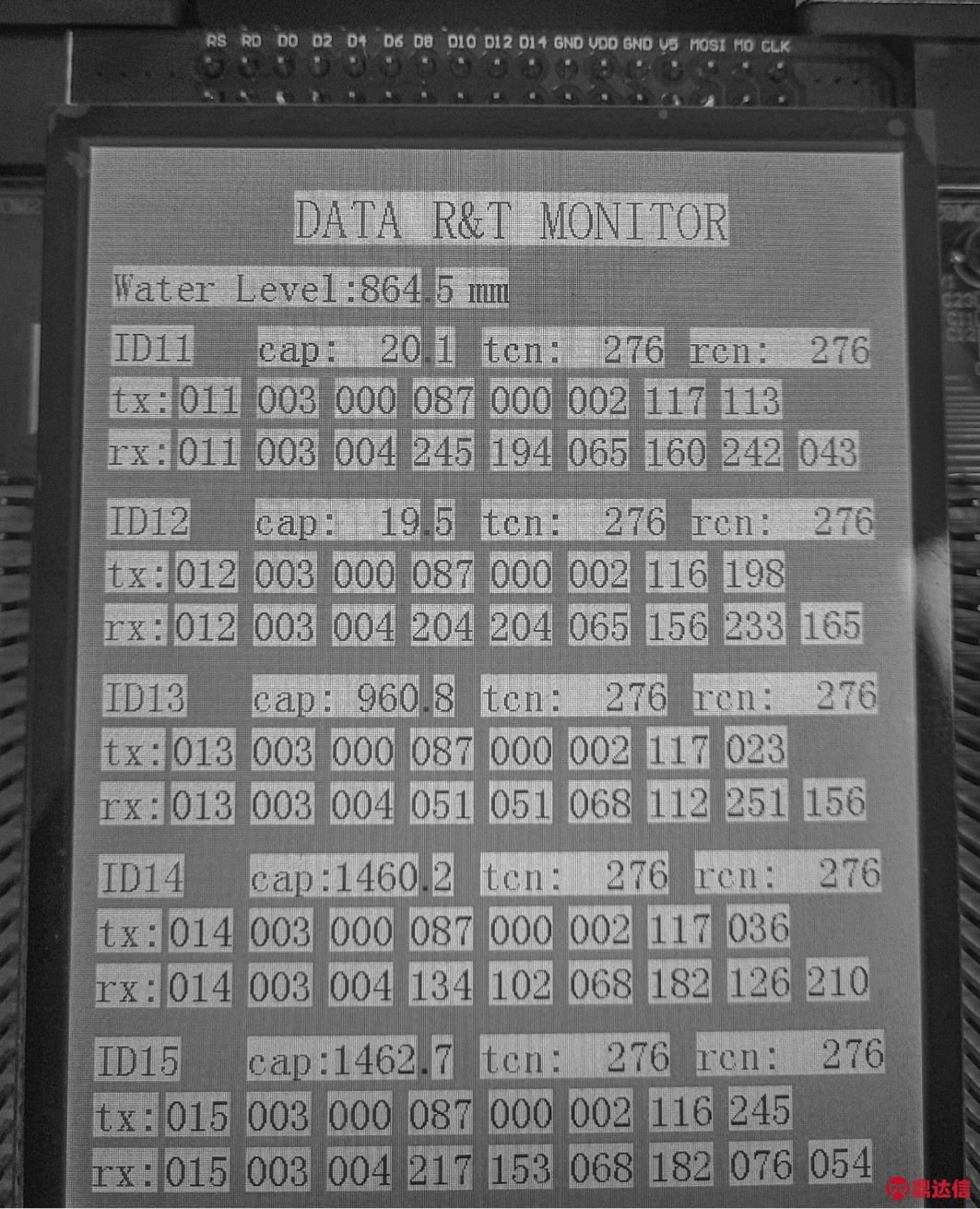
图7 软件显示界面示意图
3 实验结果
3.1 系统运行调试
将设计好的硬件连接,软件调试完成,软、硬件结合,进行油水分界面液位高度的实际测量,通过PC端Modbus Slave对传感器传出的数据进行监测,对传感器进行测试和调试。如图7所示,系统可成功运行,传出五段极板的实时电容值和最终的油水界位值,并通过LCD电容显示屏进行显示。
3.2 结果与误差
通过自制的模拟容器加入3号喷气燃料,利用漏斗逐渐加注蒸馏水,油水界面也随之升高,分别记录显示屏内实际油水界面的液位值,并记录容器内壁标注的界面实际高度,两者对比可得液位测量的误差,最终得到多组数据,选择其中20组数据,结果如表1所示。
表1 油水界面液位测量误差分析
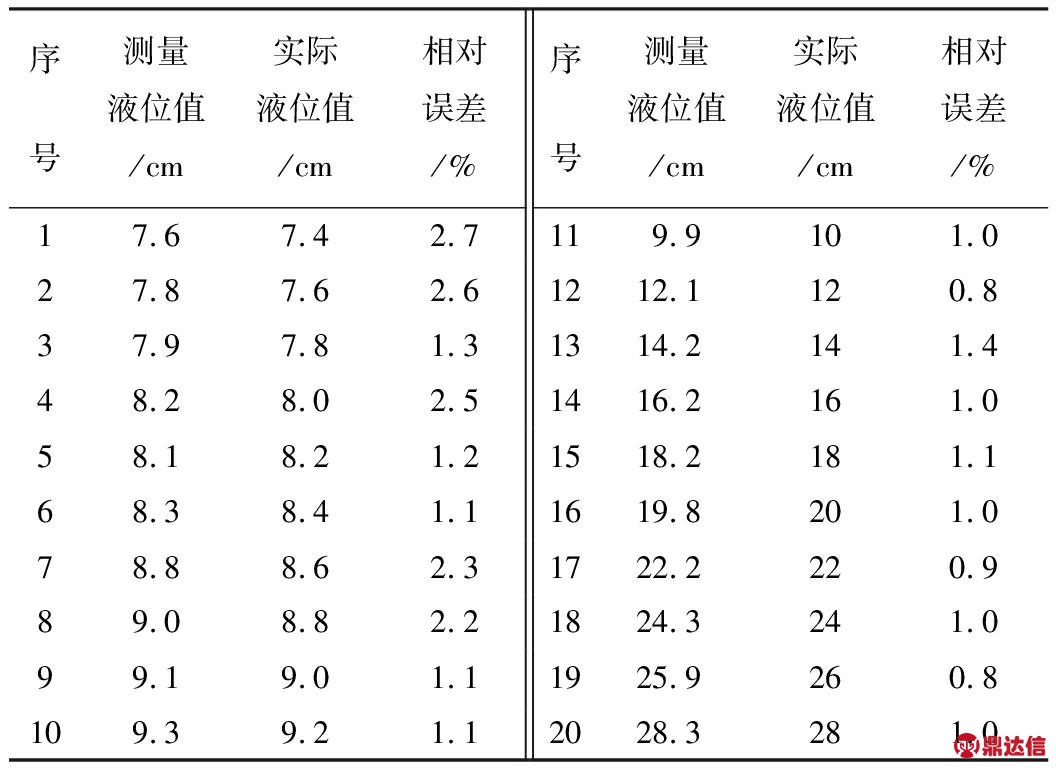
前10组数据验证在一块极板内传感器的精度,后10组数据梯度较大,显示在水位较高时传感器的精度,整个测量范围覆盖传感器的设计量程;通过实际测量,传感器系统的灵敏度较高,测量精度较高,相对误差较小,整体控制在3%以内,满足国家标准中对电容液位计3.5%的误差规定。
4 结束语
设计了新型传感器并搭建了系统进行实现,选用了高精度电容测量Pcap01_AD芯片实现微小电容检测,软件实现了数据接收处理、液位判断计算最终通过显示屏进行液位显示并可通过PC端软件进行监测。系统搭建后成功运行,多组实验证明所设计的传感器系统精度较高,灵敏度较好,测量精度控制在3%以内,可满足过滤分离器集水槽油水界位液位的快速、高精度、在线测量的要求。