摘 要:由于钛合金零件加工时切削力大,导致加工后零件易变形。而薄板类零件结构刚性差,易发生变形,钛合金薄板类零件精度难以控制。对钛合金薄板类零件的结构特点和加工难点进行分析,应用ANSYS软件进行薄板类零件变形特点仿真分析,探索真空吸盘在降低钛合金薄板类零件的装夹变形方面的工艺应用,设计专用的数控程序,优化加工工艺流程,通过理论分析和加工验证,降低了钛合金薄板类零件的加工变形,提高了钛合金薄板类零件的加工精度,证明了真空吸盘装夹方式在钛合金薄板类零件精度控制方面的有效性。
关键词:钛合金;薄板;精度控制;真空吸盘;仿真分析;变形控制
航空结构件品种繁多、形态复杂、选材各异,使得加工变形问题变得更加突出,是现代飞机制造的若干瓶颈问题之一[1]。在航空平视显示设备中,光学分组件中的镜组定位一般靠薄板类零件进行,因此零件精度要求很高。此类薄板类零件多为厚度约为5 mm的板料,且材料多为难加工的钛合金,加工时要对其进行X、Y、Z三个方向的加工,由于厚度小、材料难加工,在加工过程中极易因切削作用而产生“让刀现象”,造成上厚下薄和尺寸超差现象。加工后变形明显,甚至在加工前就存在一定的变形。传统的加工方法很难保证产品的精度要求且加工周期长。本文采用刚性分析、切削力分析和切削路径规划、热矫形、真空吸盘装夹等多重手段,可保证此类薄板类零件的加工精度,提高加工效率。
根据零件特点和加工难度,以具有代表性的钛合金薄板类零件为参考,设计了尺寸为324 mm×135 mm的零件(见图1)进行加工方法的研究,探索钛合金薄板类零件精度控制方法以及适用范围。提出的技术指标如下:1)保证图样中主要几何公差要求;2)保证零件外观质量要求;3)保证图样中其他技术要求;4)给出此方法使用范围;5)提高加工效率,保证合格率≥80%。
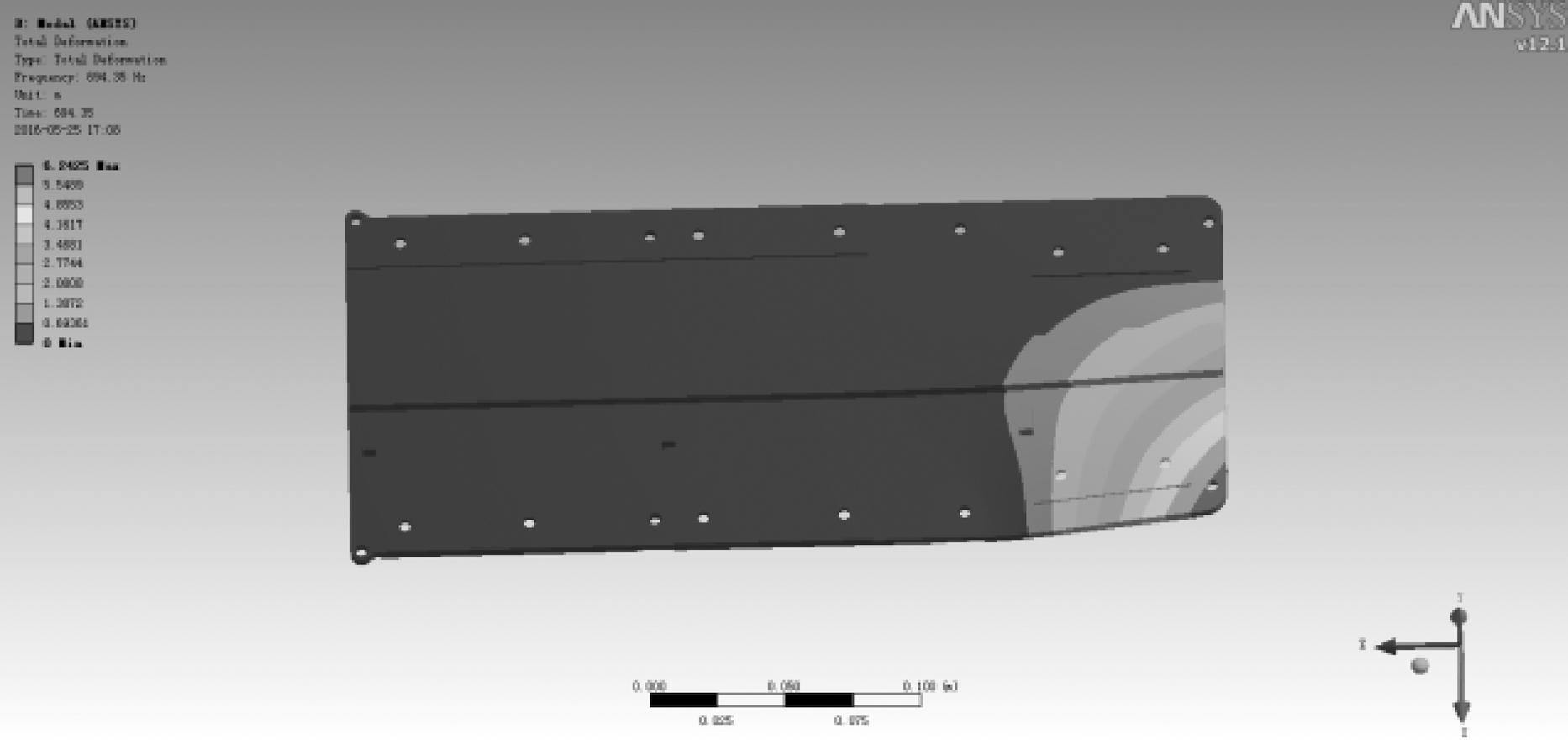
图1 XX-02-1底板零件图样
1 研究过程
1.1 零件结构特点及工艺难点
当零件壁厚或板厚与轮廓尺寸或内径曲率半径之比