摘要:伊拉克某油田现有的C列第3级生产分离器由于原设计缺陷,造成原油处理C列处理能力严重不足,出现气液夹带、液位超高等问题。对分离器进行技术评估后认为,由于该分离器本来直径就小,再加上气出口位置偏低,分离缓冲空间小,造成气液分离不充分,液相波动时液体冲入气管线,形成气液夹带。另外,由于设备内部没有任何辅助分离结构,气体中的液滴无法聚集沉降,气体含液率高。技术改造方案为:将气管线出口由侧面改到罐顶,利用直径500 mm人孔作为气体出口;设置集气包,在内部安装叶片式捕雾芯;将现有气管线出口用盲板封堵,作为通风孔。根据改造方案进行工艺计算,以液相分离计算的结果以及控制时间的要求来确定液位设置,结合分离器的内部结构及气液分离情况来确定桑德-布朗系数,计算最大气体流速和气体停留时间。改造完成后,分离器能够满足气液分离的要求,C列产量增加,液位控制稳定,达到了生产去瓶颈的目的。
关键词:气液两相分离器;工艺计算;外置集气包;桑德-布朗系数;技术改造
伊拉克某油田采用3级气液分离方式进行原油生产,主要设备为两相气液分离器,分离后原油进入拱顶储罐进一步脱气、缓冲,然后外输。每个脱气站共有3个原油处理列,分别为A、B、C列,单列的理论处理能力为8 000 m3/d。油气分离器均为20世纪90年代的苏式设备,由于原设计缺陷,C列处理能力严重不足,出现气液夹带、液位超高等问题,火炬燃烧火焰经常黑烟滚滚,实际处理能力只有约5 000 m3/d。
随着原油产量的增加,急需解决C列处理能力不够的问题,解决生产瓶颈。如果购买新的生产分离器并进行安装,需要大约1年的时间以及大量资金的投入,考虑到现场生产的紧迫性以及节省投资的要求,决定在减少停产维修时间和降低成本的前提下,采用技术改造的方式达到C列生产去瓶颈的目的。
1 C列生产现状及存在问题
站内生产分离器均为卧式重力分离器,各列生产流程如下:单井来油→集油管汇→1级分离器→2级分离器→3级分离器→大罐→增压泵→外输。
C列生产分离器设计参数见表1。相比1级和2级分离器,3级分离器设备直径和长度都明显偏小,内部没有任何辅助分离结构,无法强化油气分离[1],使气液很快达到平衡状态。因此当2级分离器来液含气量大的时候,气体携液量比较高,同时出现泡沫层和假液面[2],液位迅速升高后,液体进入气管线,造成C列管汇紧急切断阀关断全列停产。
表1 C列生产分离器设计参数
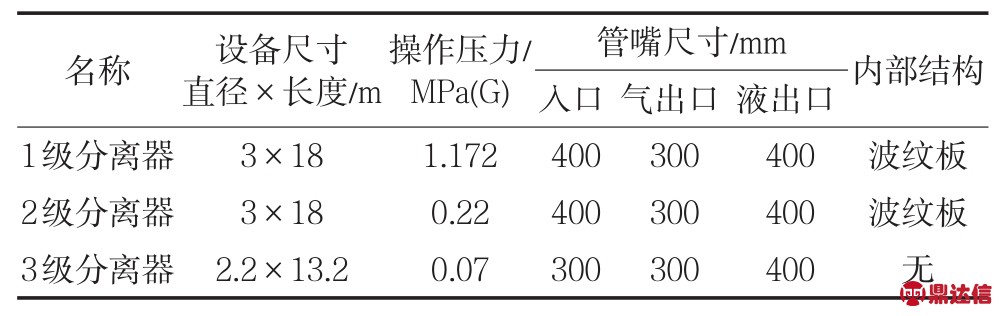
C列第3级分离器见图1,3级分离器液位设置见表2,逻辑关断控制见表3。
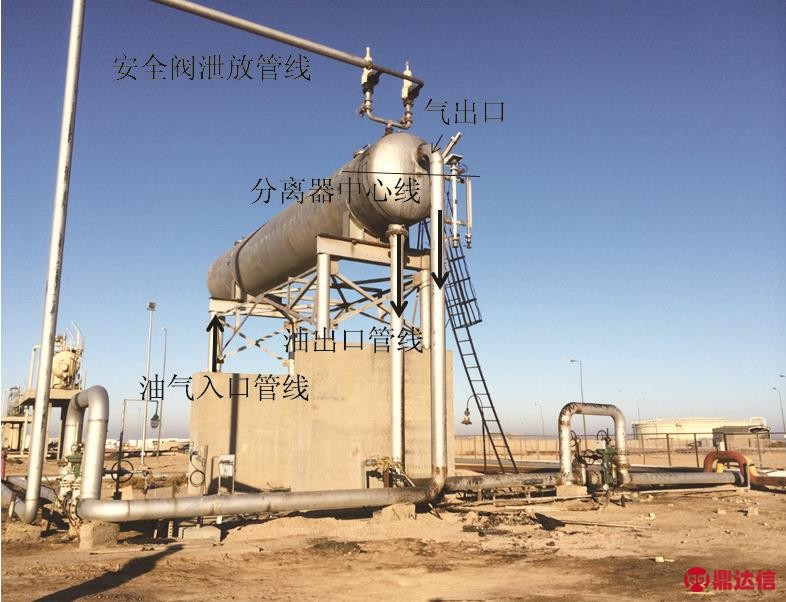
图1 C列第3级生产分离器
表2 C列3级生产分离器液位设置(改造前)
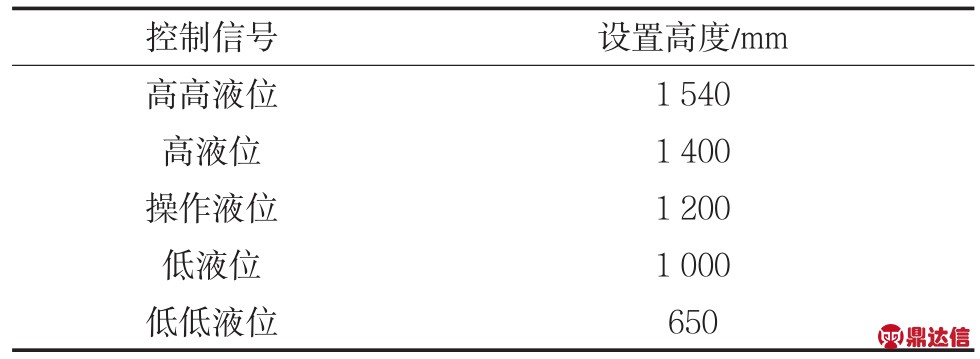
为了解决处理能力不够的问题,首先对C列产能进行评估,评估原则为:按照至少3 min液位控制时间和3 min停留时间来核算分离器的处理能力。停留时间按照容器底部到低液位(LLL)的容积进行计算,液位控制时间按照低液位到高液位(HLL)的容积计算,另外在高液位和高高液位(HHLL)之间有至少0.5 min的缓冲时间。采用K系数法计算分离器中的最小气相容积。
表3 分离器逻辑关断控制

第3级分离器天然气出口管线安装在容器封头一侧,气管线管嘴公称管径300 mm,管底高度为1 650 mm,高高液位距离管底只有110 mm,因此,当来液不稳定以及罐内泡沫堆积时,由于气出口位置偏低,缓冲空间小,设备内部没有任何辅助分离结构,气体中的部分液滴无法充分聚集沉降,液相波动时泡沫极易冲入气管线,造成气液夹带。
评估结果为,由于受限于第3级分离器,C列实际生产能力仅为5 247 m3/d。
2 分离器改造技术方案
针对以上分析,分离器改造方案为:将气管线出口由侧面改到罐顶,利用直径500 mm人孔作为气体出口;设置集气包,在内部安装叶片式捕雾芯(利旧);将现有气管线出口用盲板封堵,作为通风孔。
2.1 工艺计算输入条件
对以上改造方案进行工艺计算。首先对改造后的分离器进行液位设置调整,调整后的液位设置见表4,生产运行参数及物性参数见表5。
表4 C列3级生产分离器液位设置(改造后)
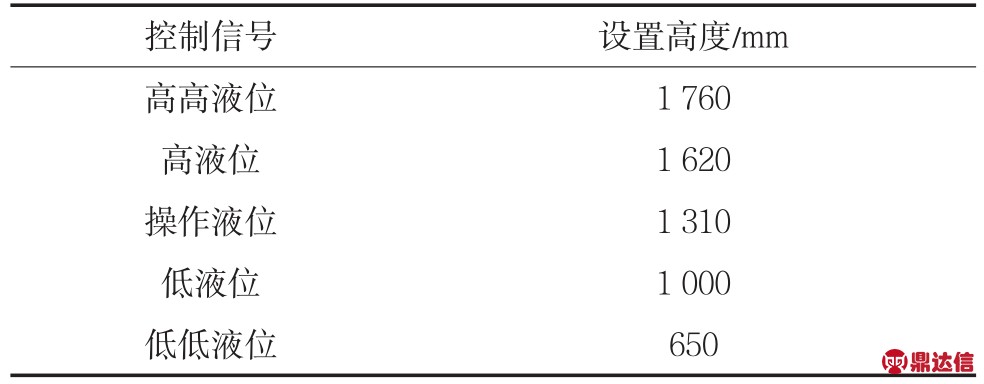
表5 分离器生产运行参数及物性参数

注:*液体黏度是在60℃时;**原油流量波动系数为1.06;***天然气流量波动系数为1.2。
2.2 工艺计算
2.2.1 液相分离计算
计算从原油中分出气泡的时间作为分离器液体停留时间。核算改造后的液体缓冲、控制和分离时间是否满足要求。

式中:Vg为气泡匀速上升速度,气泡上浮速度慢,雷诺数小,流态一般总处于层流区,m/s;Do为气泡直径,m;g为重力加速度,m/s2; ρl为液体密度,kg/m3; ρg为气体密度,kg/m3; μl为分离条件下原油动力黏度,Pa·s。
核算直径400 μ m的气泡从分离器底部到低液位的垂直距离上从液相中分离所需要的时间。在温度57℃时需要3.8 min的时间才能从液相分离出来,因此,需要保证液体的停留时间大于3.8 min。计算结果见表6。
表6 分离器液相停留时间计算结果

根据液位设置计算改造前后分离器的分离缓冲时间,保证液体停留时间3.8 min的前提下,调整HLL来保证控制时间[3],计算结果见表3、表4。高高液位由1 640 mm提高到1 760 mm后,液体控制时间由2.02 min提高到3 min,保证了油气分离效果[4],满足了缓冲控制要求,如表7所示。
表7 改造后C列3级生产分离器时间设置 min

2.2.2 气相分离计算
在满足液相停留空间要求后,采用K系数法[5]计算改造后的分离器气相空间是否满足气相分离要求。计算过程如下:
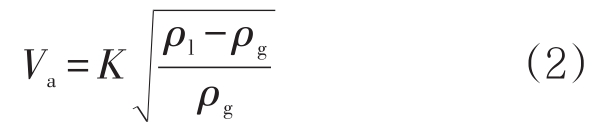
分离器内气体最大流速为式中:Va为最大气体流速,m/s;K为桑德-布朗系数。
根据API Specification 12J(SPEC 12J)《美国石油学会标准》[6],K的取值主要依据表8。表中给出的K系数是按照分离器安装有丝网除雾器来考虑的。对于容器内没有捕雾结构的分离器,K系数需要乘以0.5[7]。因此,分离器计算按长度超过3 m的卧式分离器K值的一半计算,K取0.15。
表8 最大允许速度下的K因子
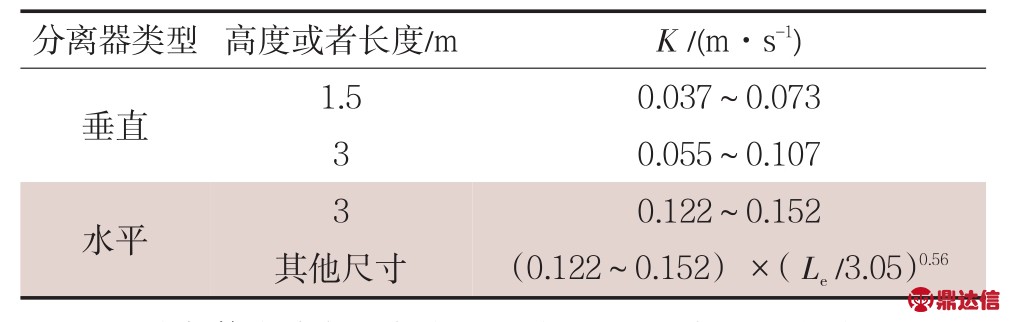
注:Le为气体在分离器中从入口到出口的距离,人孔到入口的距离为10 m。
最小气体通过面积为

式中:Av为最小气体通过面积,m2;Qg为设计气体流量,m3/s。
气相中液滴沉降速度(临界气体流速)为
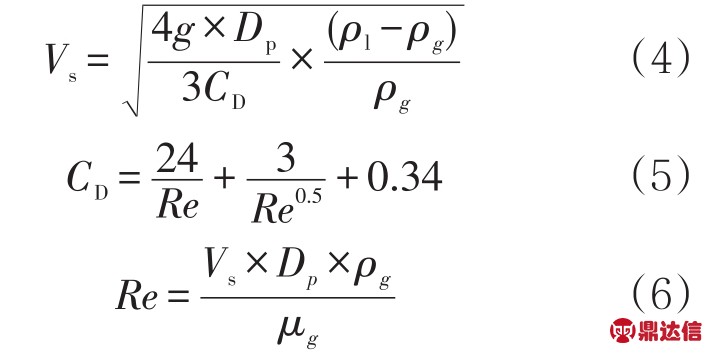
式中:Vs为气相中液滴沉降速度,m/s;Dp为液滴直径,μ m;CD为拖拽系数;Re为雷诺数。
通过迭代法计算Vs,假定CD=0.34,计算Vs,得到新的Re,代入公式计算CD、Vs,直到新的Vs和最后迭代得到的Vs差值小于1×10-4。
判断准则为液滴沉降时间小于气体流出容器气相分离部分的时间。

式中:Hd为气体中的液滴在分离器中沉降的距离,即液面以上气相空间高度,m;Le为气体在分离器中从入口到出口的距离,即分离器有效长度,m。
经过计算,气体停留时间和通过面积均满足要求。改造后的分离器满足气体分离要求,如表9所示。
2.2.3 外置集气包计算
对于小于100 μ m的液滴,在分离器内无法分离出的,或者来液波动较大时,需要脱除气体中的液滴。因此,在天然气出口位置利用人孔设置外置集气包,并安装叶片式捕雾器,气体在垂直方向通过蛇形通道,利用碰撞分离的原理[8]将气体中的液滴通过碰撞聚集成较大液滴,通过重力沉降分离出来。由于聚集后的液滴直径很难预测,K值一般取经验值。考虑到集气包为气体二次分离,且安装了叶片式捕雾器,因此K值取0.152 m/s,另外,由于水平分离部分没有安装入口分流及捕雾装置,重力分离效率[9]不高,考虑液相负荷修正系数0.6,K值为0.09。判断准则为Vs>Va(Vs、Va的计算方法同上)。计算输入见表10,计算结果见表11。
经过计算,集气包能够将直径大于420 μ m的液滴沉降下来。
表9 气相液滴沉降计算结果

注:*按照操作液位1.31 m确定气相空间高度;**气体停留时间>气相降落时间;***A′v>Av。
表10 集气包运行参数

表11 集气包液滴沉降计算结果
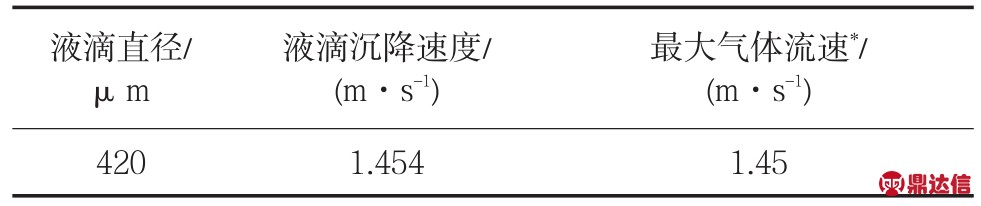
注:*Vs>Va。
3 结论
C列3级分离器改造通过分析分离器的事故原因确定了技术改造方案,核算液相分离时间为3.8 min,控制时间为3 min,满足液相中分离气泡的要求。气相分离计算结果为液滴在气体中停留时间为4.17 s,大于气相液滴降落时间2.93 s,且实际气体通过面积大于最小气体通过面积,因此改造后的分离器能够满足气液分离的要求。
分离器计算的关键是需要结合分离器的内部结构及气液分离情况来确定桑德-布朗系数,通过迭代法计算气相中最大液滴沉降速度,根据液滴沉降时间和气体流出容器的时间来判断改造后的分离器是否能够满足气体分离的要求。
通过分离器改造罐内液位得到提升,保证了液体停留时间和控制时间。增加的外置集气包可以将大液滴聚积后进行沉降,进一步降低天然气的含液率,从而提高原油收率。该项改造既节省了投资,又缩短了停产时间,将所有管段提前预制好后,仅用1天的时间进行安装,不影响正常生产。最终,C列产量增加到8 200 m3/d,液位控制稳定,达到了C列生产去瓶颈的目的。