摘 要 针对螺杆压缩机的油气分离器,应用PumpLinx软件对不同入口方式、不同油滴直径以及不同容积流量的分离器进行了三维数值模拟。在仿真中,气–液两相流场符合流体N-S方程,先用RNG k-ε模型计算连续相的压缩气体,得到分离器内部旋转流场的流线、速度、压力的分布规律,再用离散相模型计算加入离散相的液态油滴,得到了油滴的运动轨迹追踪图。通过对两相流场模拟结果的对比分析,PumpLinx软件可以较好地模拟入口方向、容积流量对流场分布规律的影响以及油滴直径对分离效率的影响,为油气分离器的优化设计提供了一种有效的研究手段,具有重要的工程应用价值。
关键词 PumpLinx,油气分离器,数值模拟,气液两相流,油滴轨迹
1.引言
螺杆压缩机在压缩空气的运行过程中,部分润滑油会在高温条件下变成油雾并扩散到被压缩的空气中,从而影响压缩机的运行和能耗。这些油气混合物,大部分的油滴直径一般都在1~50 μm [1]。为了提高压缩空气的品质,需要尽量多的分离出液相油滴,因此对油气分离相关设计提出了更加严格的要求。
在工程中,一般采用油气分离器进行处理。油气分离器通常采用两级分离。首先,对于大直径的油滴和大部分小直径的油滴,在油气分离罐中采用旋风分离法进行离心粗分;剩余的油气混合物,利用亲和聚结法(即滤网)进行精分。如果一级分离的效率足够高,那么进入二级油分滤芯的油量就会减少,分离效率也就越好。因为分离效率的高低是评价压缩空气纯净度和品质一个重要指标。
随着计算流体力学技术的快速发展,也为油气分离器的数值模拟仿真研究提供了一种重要途径。周华,孙为民等人采用此技术对油气分离器内部的结构进行优化设计,得到了更好的结构模型;褚晓东采用此技术对离散相的油滴轨迹进行追踪;丁晟,钟崴等采用此技术对液态油滴追踪,得到了油气分离器的分离效率。但是,目前对油气分离器分离效率的影响因素的研究工作较少。
本文应用PumpLinx软件对螺杆压缩机的油气分离器进行分析研究。PumpLinx软件是美国Simerics公司专门针对各类泵的水力学模拟计算开发的CFD软件,其中的两相流模块具有计算速度快、高度自动化的直角笛卡尔网格生成器、计算结果可靠等优点,能够预测空化、压力和流动。而且,不会受到试验和测试手段等因素的干扰,大大缩减了对油气分离器的研究周期,有利于其结构优化,具有重要的工程应用价值。通过 PumpLinx软件对油气分离器的数值模拟,可以得到压缩空气在分离器内的速度、压力分布,以及液相油滴的运动轨迹追踪图。本文重点研究了不同入口方式、不同油滴直径以及不同容积流量对油气分离器分离效率的影响。
2.控制方程
在油气混合物中,气主要指要压缩的空气,采用理想气体状态方程;油指的是润滑油。流动的控制方程包括连续方程、动量守恒方程和能量守恒方程。
2.1.连续方程

式中ρ——流体密度;
——流体速度矢量;
S m ——液滴蒸发进入气相的质量。
本文中,不考虑油滴的蒸发,因此这一项为0。
2.2.动量方程

式中——应力张量;
ρ——重力;
F——离散相粒子对气流的作用力。
2.3.能量方程

式中k——导热系数;
E——总能;
Sh ——油滴通过对流换热和辐射换热向气流传递的热量。
3.理论分析
3.1.结构模型
在螺杆压缩机的运行过程中,空气混合物在外力的作用下以一定的速度切向(或径向)进入油气分离器内,在外桶内壁和内桶外壁之间作旋转流动,旋转方向向下。当绕过内桶底部后,再向上旋转,经过滤纸,从油精分离器中出去。即经过油分和滤芯二次过滤后,洁净的压缩气体从排气口排出,经过最小压力阀输出到施工设备中使用。而油滴在离心力的作用下,被甩到了外桶内壁,而后被壁面捕捉,在自身重力的作用下落到油气分离器的底部。如果温度超过温控阀的设定温度,则经冷却器冷却后,进入过滤器后流入压缩主机;如果油温未超过温控阀的设定温度,则直接经过油过滤器过滤后进入压缩主机。
本文重点研究的是一次油分分离,因此在对螺杆压缩机的油气分离器进行数值模拟计算时,为了节省时间,对实际应用的油气分离器物理模型进行了相应的简化,取消了实际分离器内部安装的滤芯。简化后的结构如图1所示。
3.2.数学模型
对于油气分离器气液两相流的数值模拟,通常包含气相场以及气液两相计算。常见的计算主要有 2种类型:欧拉–欧拉型算法和欧拉–拉格朗日算法。其中,欧拉描述流体的物理量,认为是随空间点及时间而变化的:拉格朗日描述流体质点的物理量,认为是随流体质点和时间变化[2]。由于欧拉–欧拉型算法相对复杂,并且成本较高。因此,本文采用的离散相模型是属于欧拉–拉格朗日算法。即把空气视为连续相,采用欧拉方法进行计算,而把油滴视为离散相,运用拉格朗日方法进行追踪计算。
3.3.网格划分与计算格式
油气分离器内部几何结构比较复杂,为了适应其结构特点,本文计算采用了二叉树笛卡尔网格。应用PumpLinx软件可以快速生成网格。相对于以往网格生成速度慢,此软件具有节约时间的优势。同时,具有自适应、网格数量少、局部加密便捷、精度高、收敛性好等优点。在模型中,网格个数为 81,637,其划分如图2所示。
方法求解,一般选取稳态的分析,利用压力求解器求解连续方程、动量方程与能量方程,对流项的数值差分格式采用迎风格式离散,离散后的线性方程解法采用共轭梯度法计算。
3.4.湍流模型
在油气混合物中,油滴相的含量在总体含量中占的比重较少,体积分数一般少于10%,因此将油滴认为是稀相,满足离散相模型的使用条件。油气分离器内气相场采用RNG κ−ε改进的双方程模型。文献资料表明,此模型对于弯管流[3]、冲击射流[4]和旋转流[5]等流动类型都具有较高的精度,而油气分离器内的流场恰恰是由上述几种流动类型构成的,因此,选择RNG κ−ε模型来模拟油气分离器内部的湍流。
3.5.边界条件
1)在油气分离器的入口处采用给定速度(或给定容积流量)边界条件,在出口处采用给定静压出口边界条件,在所有壁面处均采用无滑移边界条件。
2)对于离散相的油滴,对油滴的运动轨迹进行求解时,所做的假设如下:不考虑油滴的蒸发过程;射入的油滴粒子之间是相互独立的、均匀的圆形;忽略油滴在流动过程中相互碰撞导致的油滴破碎和结合。

Figure 1.Structure model of oil and gas separator
图1.油气分离器的结构模型
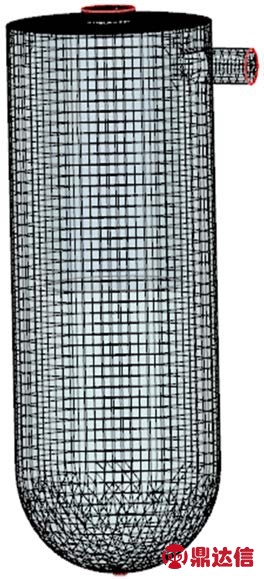
Figure 2.Grid division of oil and gas separator
图2.油气分离器的网格划分
4.油气分离规律的研究
油气分离器的典型工况为:温度358 K,润滑油密度为972.2 kg/m3,动力粘度为0.00148 Pa.s。空气密度为1.225 kg/m3,动力粘度为1.79×10−5 Pa.s。在本工况下,液相油滴含量较少,体积浓度小于10%,满足离散相模型的使用条件[6]。
4.1.入口方向对流场分布规律的影响
油气分离器的入口方向不同,流体的流线、速度、压力分布规律也不同,从而影响其分离效率[7]。为此,模拟分析了流体的切向进入和径向进入两种方式。经 PumpLinx软件模拟仿真,油气分离器的流线图如图3所示。
由图3可知,沿切向进入油气分离器的流体,存在较强的旋流效果,可使油滴产生较大的离心力,容易附着在油气分离器外桶内壁上,因而分离效率相对较高。而沿径向进入油气分离器的流体,产生的旋流效果不如切向明显,这是因为流体进入后直接碰撞内桶外壁,流速的旋向流动减弱。并且,流体在进入油气分离器后,在其背面产生对流,导致旋流速度减小,油滴产生的离心惯性力也减小,难以附着在分离器外桶内壁上,因而降低了油气分离器的分离效率。显然,利用 PumpLinx软件进行仿真,其内部流线可以更为直观的看到。此结论只适应本工况,对于径向进入油气分离器来提高油气分离效率的结构,正在进一步研究中。
图4、图5分别为切向进入结构和径向进入结构在进口截面处速度和压力分布图。
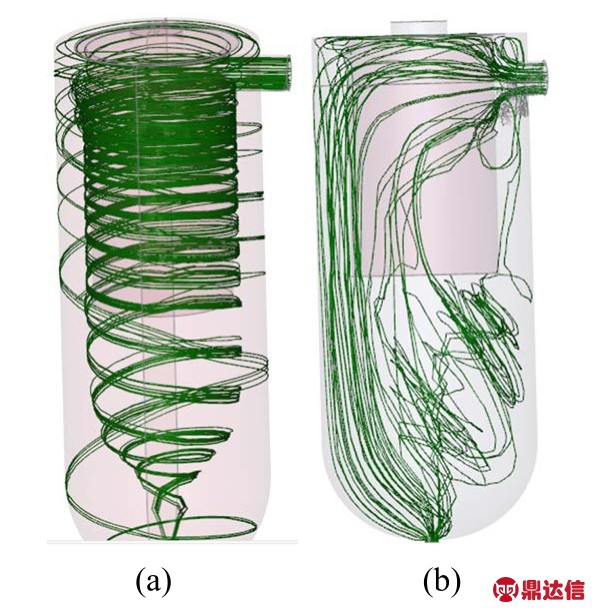
Figure 3.Flow charts of oil and gas separator.(a)Flip in, (b)radial entry
图3.油气分离器的流线图。(a)切向进入,(b)径向进入
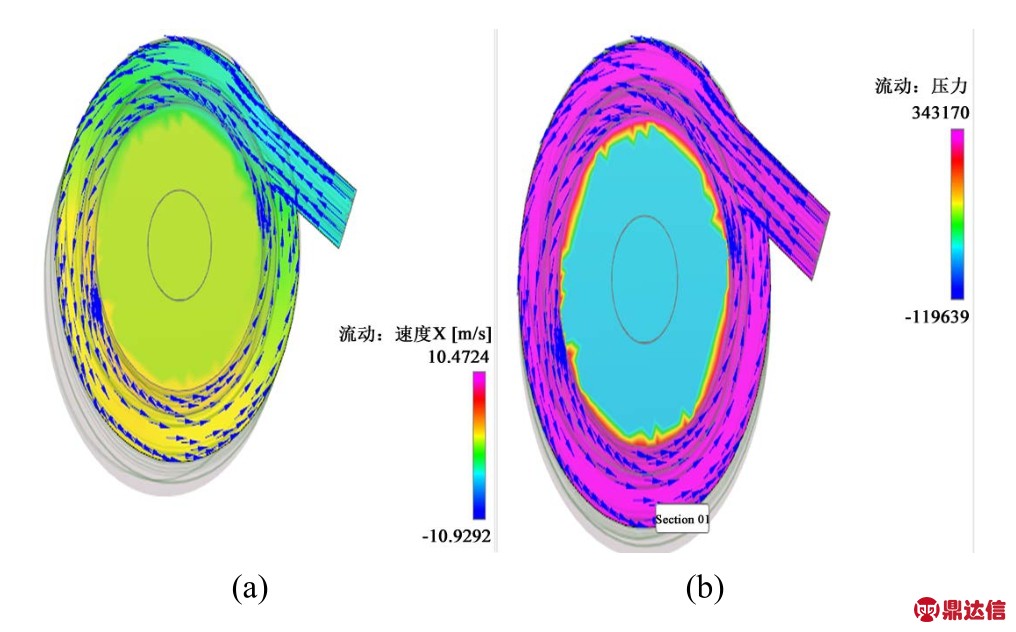
Figure 4.Distribution of speed and pressure of tangential entry.(a)Leakage velocity distribution, (b)distribution of tangential pressure
图4.切向进入的速度和压力分布图。(a)切向速度分布,(b)切向压力分布
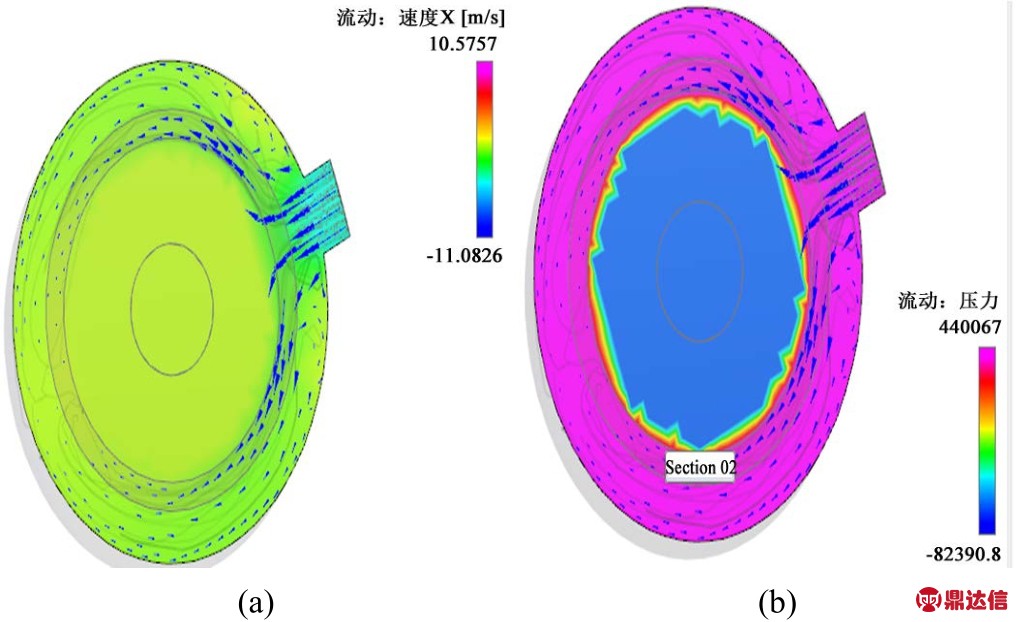
Figure 5.Distribution of radial entry velocity and pressure.(a)Radial velocity distribution, (b)Distribution of radial pressure
图5.径向进入的速度和压力分布图。(a)径向速度分布,(b)径向压力分布
由图4分析可知,沿切向进入油气分离器的流体,只在入口处发生了轻微的碰撞,压力变化相对均匀,流体在油气分离器的外桶内壁和内桶外壁之间做高速圆周运动。由图5可知,沿径向进入油气分离器的流体,在入口处与内桶外壁直接碰撞,压力分向两侧,且沿两侧进行对流,两股流体碰撞,旋流减弱。显然,切向入口更易分离。
通过进一步分析可知,气流与外桶内壁面的碰撞过程中,油滴由于自身的惯性,速度会急剧减小并被壁面吸附,从而提高油气分离效率。利用 PumpLinx软件进行仿真,可以直观形象的说明切向入口比径向入口好,进一步验证加强混合物与壁面碰撞是油气分离效率提高的一个影响因素。
4.2.油滴直径对分离效率的影响
研究表明,在重力的作用下,如果混合物的流速相对缓慢,大的油滴经过一定时间后都会被壁面捕捉而下落到油气分离器的底部。而直径小的油滴,下落时间长,并且有可能会悬浮在空气中,无法从气体中分离出来。而油气分离器的作用就是尽可能的把这部分直径相对较小的油滴分离出来。本文利用PumpLinx软件分别对不同直径的液态油滴颗粒,在分离器中的运动轨迹进行了模拟。图6是直径为30 μm、20 μm、1 μm的油滴运动轨迹。
从图6可以看出,不同直径的油滴在分离器内被分离的时间和运动轨迹明显不同,直径大的颗粒易于分离[8]。因为油滴从进气口进入油气分离器后,大部分的油滴直接撞击到桶壁上而被附着,其余的一部分油滴会在气流的作用下,继续做旋转运动[9]。在离心力的作用下,被甩到桶壁或者桶底,最后剩余的少量小直径油滴,由于随流性好,不容易分离出来,会随着气流流出。数值模拟仿真结果和相关经验理论相吻合。说明利用 PumpLinx软件进行仿真,可以更为直观的看出油滴直径的大小对分离效率的影响,进一步验证了大直径油滴容易分离的结论。说明直径的大小是影响油气分离器分离效率的一个因素。
4.3.不同容积流量对分离效率的影响
本文模拟了不同容积流量对一次油分效率的影响。工况为:排气压力0.7 MPa,排气温度91℃,进气温度20℃,油滴直径50 μm。为了研究不同容积流量下,一次油分对分离效率的影响,本文选择了3个工况点,分别为40 m3/min、60 m3/min、100 m3/min。经计算,对应的速度分别为8.8 m/s、13.2 m/s、22 m/s。其流线图如图7所示。
从图7中流线可以看出,不同容积流量下的油滴在分离器内被分离的时间和运动轨迹明显不同。从(a)、(b)图可知,随着容积流量的增大,油滴的分离效率明显提高。显然,在图(b)尺寸结构和工况下的油气分离器,即容积流量为60 m3/min时,分离效率较高。说明,增大容积流量(也即增大进口速度)是提高油气分离效率的有效办法之一。但是,并不意味着,容积流量越大越好。由(b)、(c)流线图的对比可知,当容积流量过大时,分离效率反而降低。分析原因,当速度增大时,压阻上升,导致油气运行路径变短,没有充分进行旋风分离。另一方面,漂浮在油气分离器底部液面上的油雾状油,会在气流较大速度的影响下被夹带出去,从而导致分离效率降低。对于此工况,工厂中油气分离器进口速度设定值是13~15 m/s。由图可知,利用PumpLinx软件仿真,其结果与理论是相符的。
图8、图9分别为不同容积流量在进气口截面处速度和压力分布图。
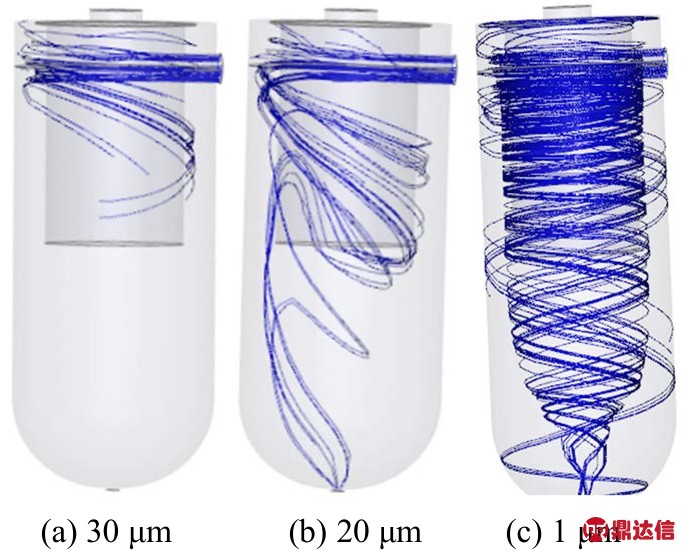
Figure 6.The trajectory of oil droplets of different sizes
图6.不同粒径油滴的运动轨迹图

Figure7.Flow charts under different volume flows
图7.不同容积流量下的流线图
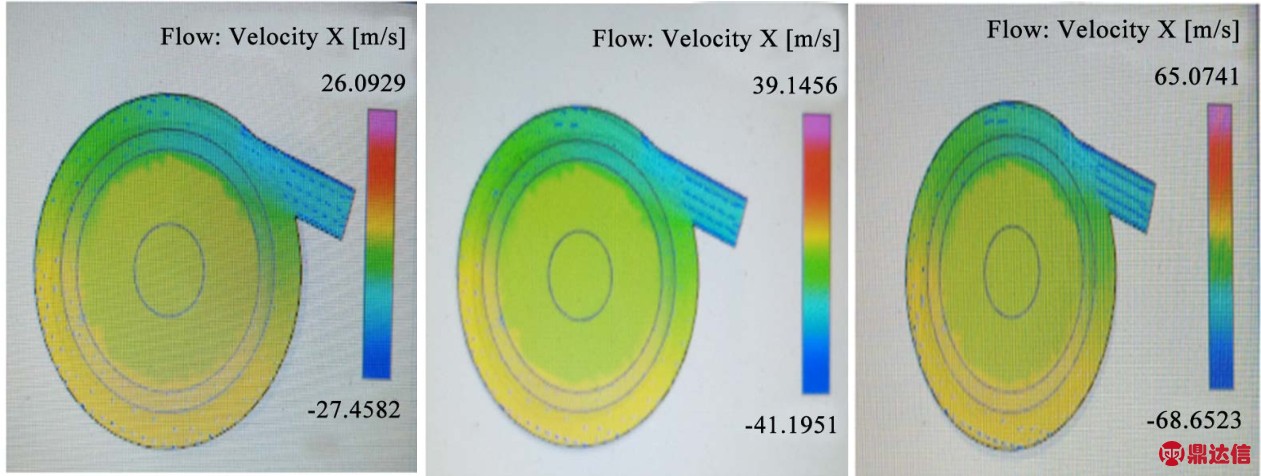
Figure 8.Speed distribution of different volume flows at inlet sections.(a)40 m3/min velocity distribution, (b)60 m3/min velocity distribution, (c)100 m3/min velocity distribution
图8.不同容积流量在进气口截面处速度分布。(a)40 m3/min速度分布,(b)60 m3/min压力分布,(c)100 m3/min速度分布
从图 8、图 9可以看出,随着流量的增加,进气口截面处速度和压力范围也相应变大。说明管径在设计时,应该合理设置尺寸。否则,管径太小,相同工况下容积流量过大,导致压阻上升,气流噪声也会相应增大,容易引起共振,影响油气分离效率。在实际设计中,要尽量避开共振的产生。一般,在增大容积流量时,要进行相应的噪声分析测试,将油气分离器的进口速度控制在合适的范围内。如果容积流量过小,则表现为管径过大,容易造成资源的浪费,不经济。这两种情况,都会影响油气分离的效率。从PumpLinx软件仿真图片可以清晰地看出,在容积流量为60 m3/min时,即速度为13.2 m/s时,压力、速度分布相对均匀。在某公司中,此工况下油气分离器进口速度参考值是13~15 m/s。通过仿真结果和参考值的比较,说明运用PumpLinx软件仿真结果是与理论参考相符合的,是接近实际工况的。
5.结论
采用 PumpLinx软件数值模拟和实验理论相结合的方法,对油气分离器中一级油气分离的特性进行研究,得到以下结论:
1)本次工况中,利用PumpLinx软件仿真图可清晰看出:沿切向进入油气分离器的流体,比径向进入结构旋流效果要好。究其原因,切向入口的油滴是旋转落下的,而径向进入的油滴没有经过旋转直接落到油气分离器的底部。因此,切向入口结构的油滴更容易附着在外筒壁面上,有利于油气的分离。因此,利用对 PumpLinx软件仿真结果的分析,进一步验证加强混合物与壁面碰撞是影响油气分离效率提高的一个因素。
2)利用PumpLinx软件模拟了油滴的运动轨迹,得到了不同粒径油滴的运动特征。不同直径的油滴,在分离器内被分离的时间和运动轨迹明显不同。直径越大的油滴,在分离器内停留的时间越短,越容易附着在壁面上,油气易分离;直径越小的油滴跟随气流运动的时间越长,因其随流性好,不易分离,随气体出去的机率较大。利用PumpLinx软件分析,进一步说明油滴直径是影响油气分离的一个因素。
3)通过利用PumpLinx软件进行数值模拟分析得出,适当增大容积流量可以有效提高油气分离器的效率,但是要控制在合适的范围内。
4)PumpLinx软件具有设计计算速度快、仿真模拟能力强等优点,可以更为形象的模拟出流体的运动轨迹。说明将此软件数值模拟计算方法运用于压缩机油气罐的特性研究是有实际价值的,为后期优化油气分离器的结构提供了重要参考。
本文通过对 PumpLinx软件数值模拟的结果和某公司内压缩机实验的结果进行比较,得出两者结论基本吻合。说明运用 PumpLinx软件得到的结果与生产实践中实验所测数值十分接近,体现了软件的精确度。同时,改善了数值模拟与生产工况结合不密切的问题,对于实际工况具有指导意义,也有利于油气分离器的优化设计研究,具有重要的工程应用价值。
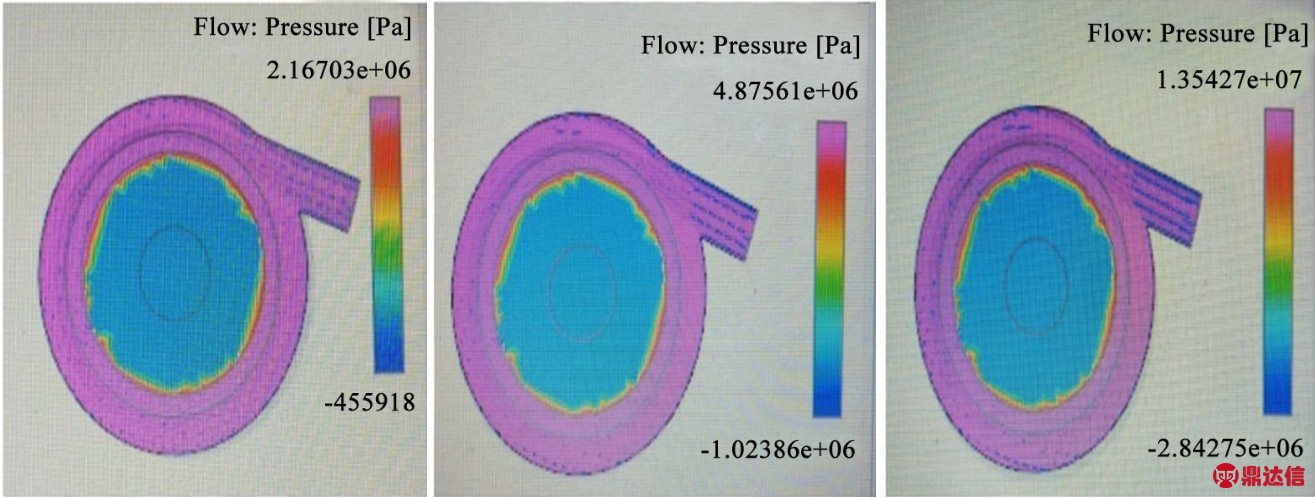
Figure 9.Pressure distribution of different volume flows at inlet sections.(a)40 m3/min pressure distribution, (b)60 m3/min pressure distribution, (c)100 m3/min pressure distribution
图9.不同容积流量在进气口截面处压力分布。(a)40 m3/min压力分布,(b)60 m3/min压力分布,(c)100 m3/min压力分布