摘 要: 烧结压力是粉末冶金制备材料过程中重要工艺参数之一,通过在石墨烯/铜中添加钛粉以改善二者润湿性,使用超声分散和球磨法进行混粉,用放电等离子烧结(SPS)的方式制备石墨烯铜基复合材料,在5,15,25,30 MPa 4种不同压力下进行烧结。用金相显微镜和扫描电子显微镜(SEM)对石墨烯增强铜基复合材料显微结构进行观察,测量试样密度,并采用硬度计、导电率测试仪对力学性能和导电性能进行测试。结果表明,随着烧结压力的升高,复合材料晶粒尺寸不断减小,导电率先上升后下降。当烧结压力达到25 MPa时,导电率最大为51.2%IACS;复合材料的密度和硬度值不断增大。
关键词: 放电等离子烧结;石墨烯;铜基复合材料
0 引 言
石墨烯是碳族材料中比碳纳米管性能更优的一种新型材料,其基本单元是由碳原子以sp2杂化构成的一层六边形平面结构。石墨烯的特殊结构决定了其优异的性能,其电子迁移率高达25 000 cm2/(V·s)[1];热导率也是已知物质中最高的(5 000 W/(m·K))[2];另外其拉伸强度(130 GPa)和弹性模量(1 100 GPa)较大[3],这些特点使得石墨烯成为增强金属复合材料导电导热性和强韧性的理想材料。
近年来,国内外学者针对石墨烯增强铜基复合材料的研究逐年增多,特别是在改善石墨烯和铜之间的润湿性。特别是在改善石墨烯和铜之间的润湿性方面取得了新的进展。甘贵江[4]分别采用“还原法”和“镀镍法”对石墨烯进行处理,有效增强了铜与石墨烯之间的润湿性,利用粉末冶金方法制备的石墨烯增强铜基复合材料抗拉强度达到241 MPa,较纯铜提升了46.1%。魏邦争等[5]采用在还原氧化石墨烯表面进行化学镀铜的方式对石墨烯进行表面改性,利用超声分散和机械搅拌的方式进行混粉,采用压制和烧结方法制备的石墨烯增强铜基复合材料导电率达到95%IACS,抗拉强度达到268 MPa。Tang等[6]利用纳米镍颗粒对石墨烯进行修饰,将石墨烯与铜粉进行均匀混粉后采用放电等离子烧结方法制备了铜基复合材料,发现添加0.1%(体积分数)的镀镍石墨烯的铜基复合材料抗拉强度相比纯铜提升了94%。
本文在石墨烯/铜中添加钛粉以改善二者润湿性,采用超声分散和球磨的方法对粉末进行均匀分散、混合,采用放电等离子烧结方法制备石墨烯增强铜基复合材料。由于烧结压力是烧结过程中影响复合材料性能的最重要因素之一,本文重点研究烧结压力对石墨烯增强铜基复合材料组织和性能的影响规律,为石墨烯增强铜基复合材料的应用提供依据。
1 实 验
1.1 试样制备
称量0.5 g石墨烯放入烧杯中,加入99.99%的分析纯酒精100 mL,搅拌后得到石墨烯溶液。称取铜粉99 g和钛粉0.5 g(试验材料规格如表1所示),先在混料机中进行机械转动将粉末混合20 h,其转速为37 r/min。随后将铜粉和钛粉的混合粉末加入石墨稀溶液中,使用玻璃棒搅拌后采用超声分散仪进行超声分散15 min,此阶段的超声处理是为了使铜粉、钛粉与石墨烯混合均匀。随后将超声后的混合溶液采用不锈钢钢球球磨5 h,球磨转速为300 r/min,球料比为10∶1。将球磨后的混合液置于真空干燥箱中进行干燥,设置温度为80 ℃,干燥20 h,直到粉末完全不含液体成分后用钢筛将干燥完成的粉末筛出以分离不锈钢钢球和粉体。
表1 实验材料
Table 1 Experimental materials

共准备4组相同石墨烯含量0.5%(质量分数)的复合粉末(每组粉末25 g)进行SPS烧结,将25 g混合粉末放入到直径Ø20 mm的圆柱形石墨模具中,随后将模具放入烧结炉内,首先调节压头压紧模具,随后关闭烧结炉阀门,关闭真空阀,进行抽真空,然后设置烧结温度﹑压力和时间,点击进入自动模式开始烧结,SPS烧结条件为:真空度是0.1 Pa以下,烧结温度为900 ℃。升温速率为100 ℃/min,烧结时间共10 min,烧结压力为5,15,25,30 MPa。随炉冷却后脱模取出试样,用砂纸磨平表面,进行微观组织分析和性能测试。
1.2 测试方法
利用MLA650型扫描电子显微镜观察石墨烯增强铜基复合材料试样的显微组织并对其成分进行分析,采用DMI3000M型光学显微镜观察金相组织,并采用Smartlab 9KW型X射线衍射仪对复合粉末进行成分分析,采用“排水法”测量石墨烯增强铜基复合材料的密度,采用D60K型数字金属电导率测量仪测定石墨烯增强铜基复合材料的导电率,1个试样测量5次取平均值,在A200型布氏硬度计上对烧结后的石墨烯增强铜基复合材料进行硬度测试,每个试样测量3个点取平均值。
2 结果与讨论
2.1 材料粉末特征
图1(a)为纯铜粉末形貌,由图可以看出铜颗粒形状主要为球形,部分铜颗粒黏着在一起;图1(b)为钛粉在铜中的分布形貌,图中绿色亮斑为钛粉,钛粉经机械混合后较均匀地分散在铜粉中;图1(c)为铜粉、钛粉和石墨烯的混合浆料经过超声分散再球磨5 h后的微观形貌,可以看出,经过球磨过程中钢球的撞击和研磨,铜粉、钛粉和石墨烯的混合粉末呈片状结构。
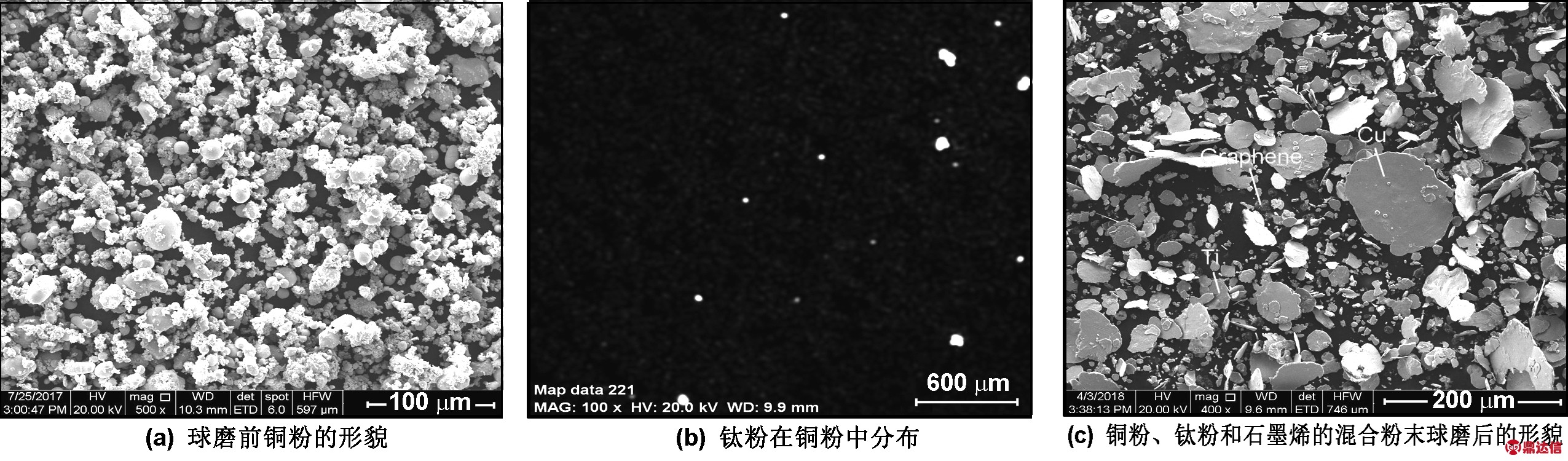
图1 纯铜及复合粉末的SEM照片
Fig 1 SEM images of the experimental powder
对经超声分散和球磨后的复合粉末进行X射线衍射分析,得到的衍射图谱如图2所示。
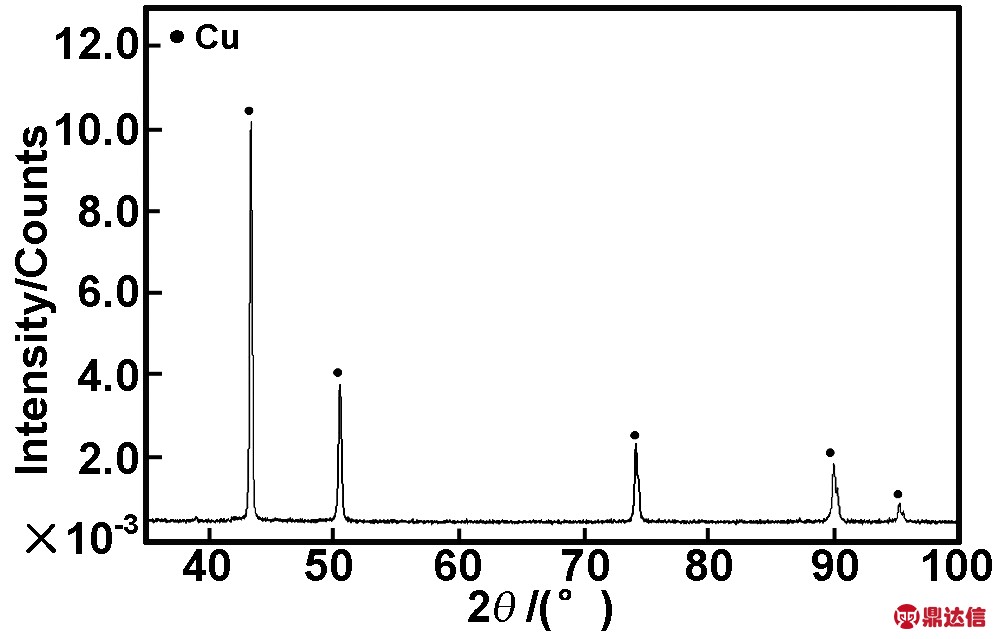
图2 经超声分散和球磨后的复合粉末XRD图谱
Fig 2 XRD patterns of composite powder after ultrasonic dispersion and ball milling
由图2可知,能谱图中仅仅显示了Cu相。由于石墨烯和钛的含量低,XRD中未发现石墨相和钛的衍射峰。另外,能谱图中没有发现氧化物的衍射峰,说明整个过程未发生铜粉和石墨烯的氧化,超声和球磨过程中铜粉和石墨烯未发生化学反应。
2.2 烧结压力对石墨烯增强铜基复合材料组织的影响
图3和4分别是不同烧结压力条件下的纯铜和复合材料金相组织照片。对比图3和4可以看出,复合材料试样的晶粒尺寸明显小于纯铜的晶粒尺寸,对比相同压力下纯铜和石墨烯/铜复合材料试样,由于石墨烯的存在对晶界迁移有着明显的阻碍作用,所以相同压力下复合材料试样的晶粒尺寸远小于纯铜的晶粒尺寸。从图3和4同样可以看出,无论是纯铜试样还是复合材料试样,在900 ℃下经5~30 MPa的压力烧结后,原来经球磨后的薄片状粉末已经变成多边形晶粒相互结合在一起,铜晶粒的晶界比较平直,同时,许多晶粒内有条状的生长孪晶。之所以会出现较多的孪晶,是因为铜的层错能低,而孪晶通常是在晶粒生长过程中形成。同时二者的组织均由等轴铜晶粒构成。
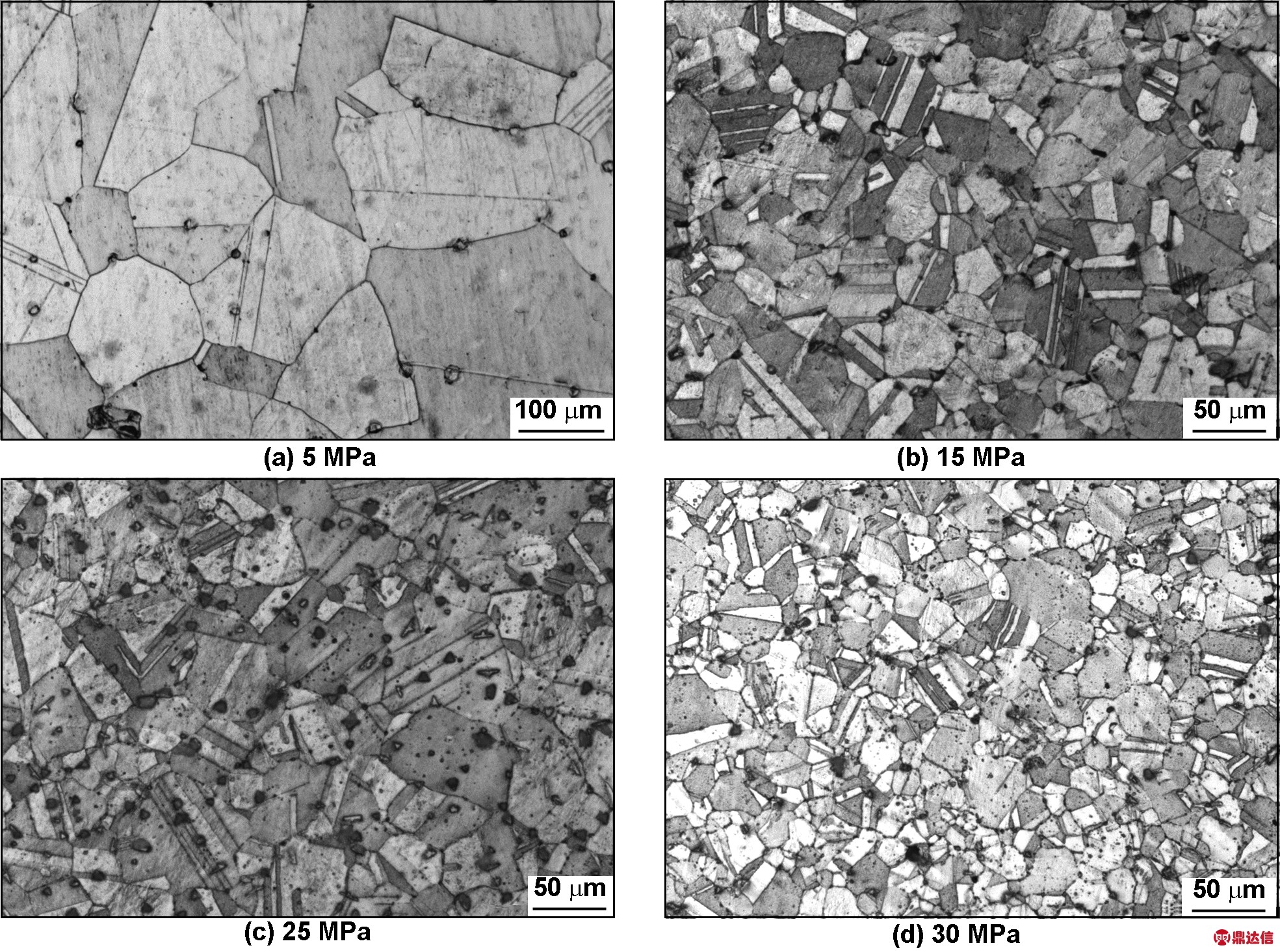
图3 不同烧结压力下纯铜的微观组织
Fig 3 The microstructure of copper under different sintering pressures
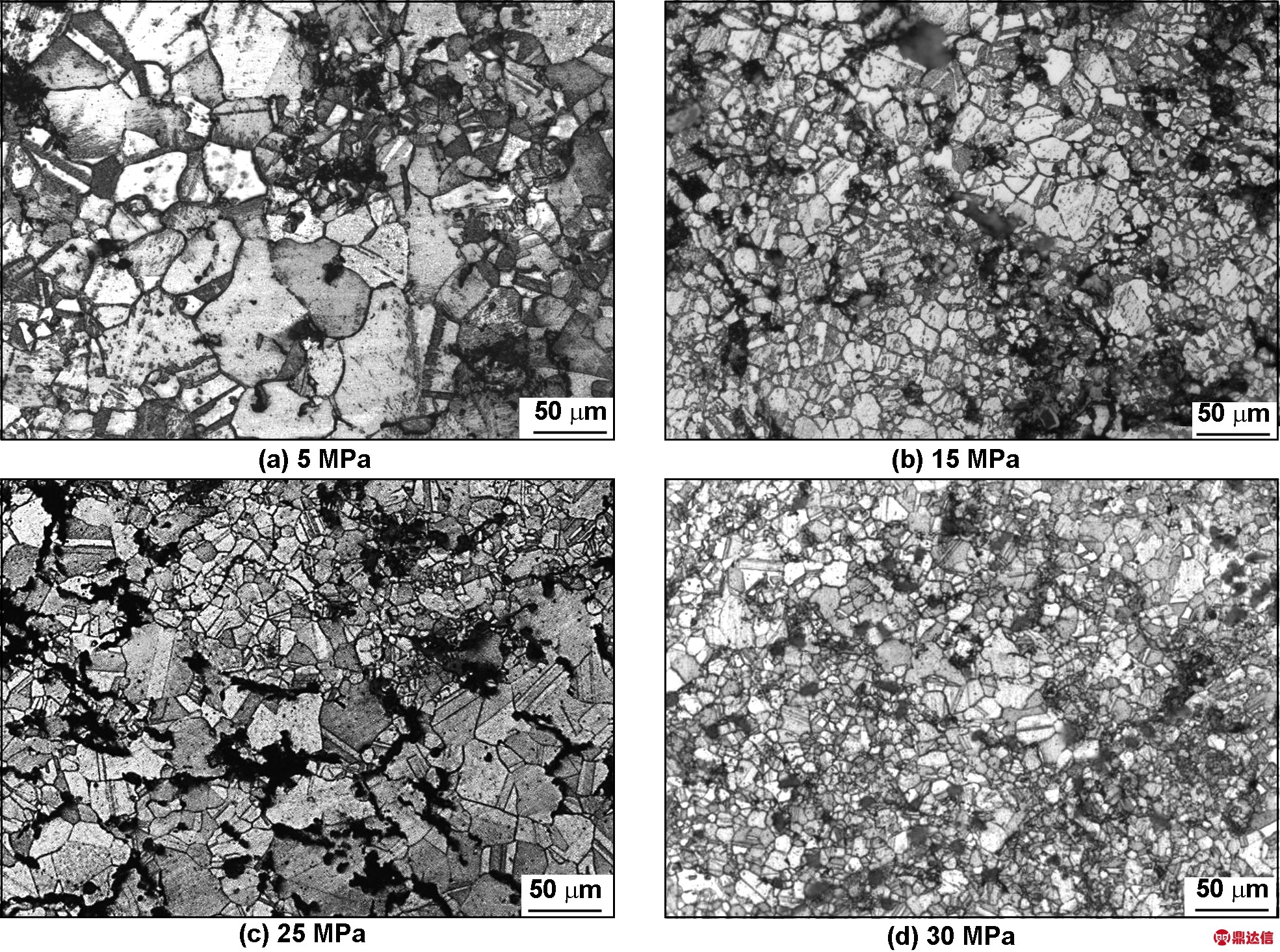
图4 不同烧结压力下复合材料的微观组织
Fig 4 The microstructure of the present composite under different sintering pressures
另外,金相观察表明,无论是纯铜试样还是复合材料试样,在900 ℃的烧结过程中,随着压力由5 MPa升高至30 MPa,基体的晶粒总体上出现了较明显的细化现象,而晶粒细化会明显改善铜合金的强度。当烧结压力为5 MPa时,基体中颗粒间不致密,形成的晶粒较粗大,这是因为在该烧结压力下,作用在材料上的剪切应力低于材料的屈服极限,致密化过程只能通过扩散蠕变进行[7]。烧结压力为15 MPa时,颗粒之间界面基本消失,孔隙缺陷明显减少,这是因为当剪切应力超过屈服极限时,材料发生塑性流动所致。当压力升高至25 MPa时,组成基体的铜颗粒连成一体,远离石墨烯的铜晶粒均出现异常长大,基本观察不到颗粒边界。当压力达到30 MPa时,继续增加压力对组织的影响不大[8],说明30 MPa足以保证烧结过程的完全进行。
2.3 烧结压力对石墨烯增强铜基复合材料密度的影响
纯铜试样和复合材料试样密度随烧结压力的变化如图5所示。由图5可以看出,复合材料的密度随着烧结压力的升高逐渐升高,最终在30 MPa的压力下复合材料的密度达到了与同条件下纯铜密度的水平。当烧结压力从5 MPa升高到30 MPa时,复合材料的密度从4.47 g/cm3增加至8.54 g/cm3,提高了91%。这是因为,在SPS烧结过程中,烧结粉末颗粒之间的联结首先是在颗粒表面进行的,由于原子的表面扩散,颗粒粘接面逐渐扩大,形成烧结颈[9]。随着烧结压力的增加,复合材料的粉末在放电等离子的烧结过程中扩散的更加充分,被压得更加密实,孔隙率也会随着压力的增加逐渐减少,所以复合材料的密度呈现增加的趋势。
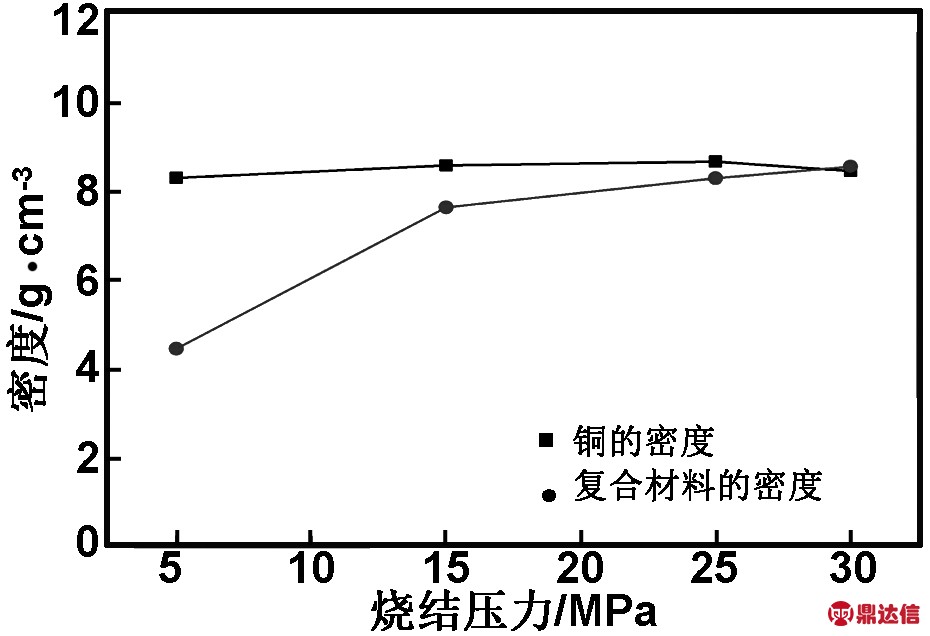
图5 复合材料的密度与烧结压力的关系
Fig 5 The relationship between the sintering pressure and density of the present composite
另外,复合材料的密度在压力<30 MPa时均小于同条件下纯铜密度,这是因为石墨烯和钛粉两种比铜的密度更低的粉末的掺入对铜颗粒进行了分隔、包裹等,导致复合材料烧结成型后的密度要低于同条件下的纯铜。而复合材料的在30 MPa烧结条件下的密度接近于同条件下纯铜的密度,这可能因为烧结压力较高时铜粉和钛粉更多的合金化提升了复合材料的密度[10],并且可能由于钛和石墨烯更多的形成了碳化钛化合物[11],这些新组织的形成使得复合材料的密度接近于同条件下纯铜的密度。
2.4 烧结压力对石墨烯增强铜基复合材料导电率的影响
纯铜试样和复合材料试样导电率随烧结压力的变化如图6所示,由图6可以看出,复合材料的导电率随着烧结压力的增加先上升后略有降低。其中烧结压力为25 MPa时导电率最大,为51.2%IACS。这是因为,复合材料的性能主要取决于相对密度,同时还受到孔隙形状和尺寸的影响。当烧结压力较低时,复合材料内部存在很多气孔,而孔隙是电子散射的中心,因而会严重影响到导电率,适当增加烧结压力能很好的减少孔隙的数量,并使得孔隙尺寸变小[12]。另外,提升放电等离子烧结压力有助于增强烧结体内各种物质的移动和晶界的迁移。由金相组织变化规律可知,适当提升压力能有效改善组织均匀性,提升复合材料的相对密度,进而提升复合材料导电率[13]。加之石墨烯在较大的压力状态下能够更好地填充孔隙,孔隙对复合材料电导率的不良影响减弱,从而一定程度的弥补了孔隙对导电率的不良影响。导电率与密度之间并非一一对应关系。这可能因为:当压力增加到一定程度时,继续增加压力会使得钛粉和铜粉更容易合金化,合金化的组织占据了更大体积的正常晶格区域,更能严重影响复合材料的导电率。因此导电率呈现随烧结压力下降的趋势。
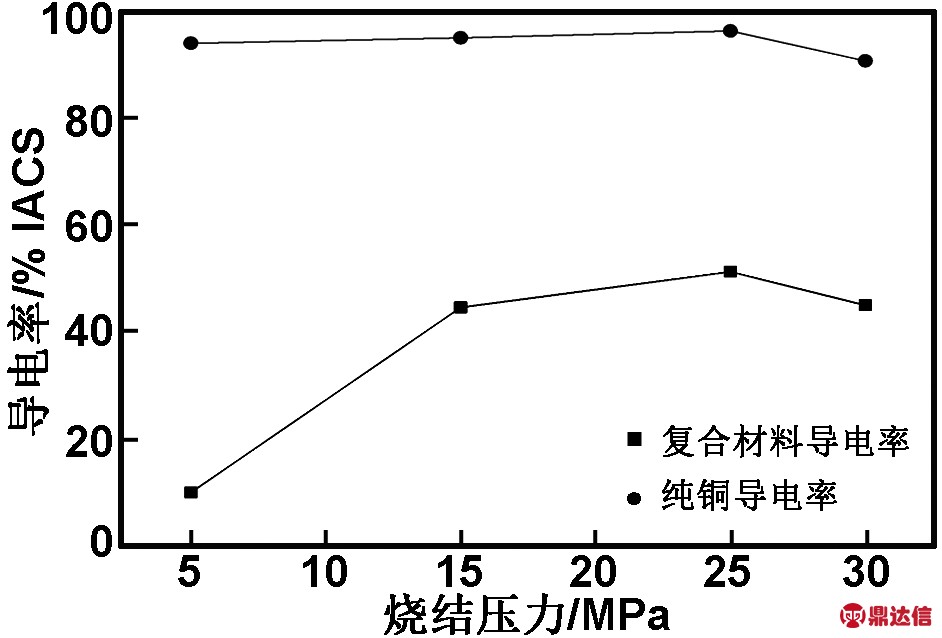
图6 复合材料的导电率与烧结压力的关系
Fig 6 The relationship between the sintering pressure and conductivity of the present composite
此外,与纯铜试样相比,在实验烧结压力范围内复合材料的导电率出现较大下降,这主要因为:(1) 石墨烯和钛粉的加入使得铜出现严重的晶格畸变和位错缺陷,这些因素会大幅度增加了电子的散射几率,引起复合材料导电率下降;(2) 石墨烯以超声球磨的方式机械地与铜混合在一起,随着石墨烯添加量的增加,石墨烯与铜基体的结合界面增多,结合界面会引起电子的散射程度增加,从而引起导电率下降;(3) 石墨烯在铜粉基体中处于各向异性的状态,难以发挥其导电率大的特点,其存在反而会阻碍自由电子的运动,因此复合材料导电率更低。
2.5 烧结压力对石墨烯增强铜基复合材料硬度的影响
图7为不同烧结压力下的复合材料布氏硬度测试结果。如图7所示,复合材料硬度随烧结压力增加而增大,当烧结压力从5 MPa增加到30 MPa时,布氏硬度值由33.4 HB上升至66.4 HB。这是因为,材料的硬度与密度有一定关系,同种材料一般随着密度的提高,材料的硬度随之提高;同时由金相组织分析可知,晶粒尺寸随着烧结压力的增加而不断减小,而细化晶粒会明显改善复合材料的强度,因此硬度也随之上升。其次,烧结压力对复合材料硬度的影响也取决于铜基体烧结状态的影响,压力升高减少了复合材料内部的孔洞等缺陷,孔隙形状在压力增加的过程中由狭长变为球形,石墨烯在基体材料中较均匀分布,孔隙缺陷的受力情况变得更好,所以硬度呈现出随烧结压力增大的趋势[14]。最后,在对粉体进行球磨和后续的烧结过程中会有一些颗粒通过表面张力团聚在一起,而当烧结压力大于团聚粉体的表观强度时,团聚的粉末会被压碎,进而有利于组织的细化和均匀,从而能够很好地提高材料的硬度[15]。
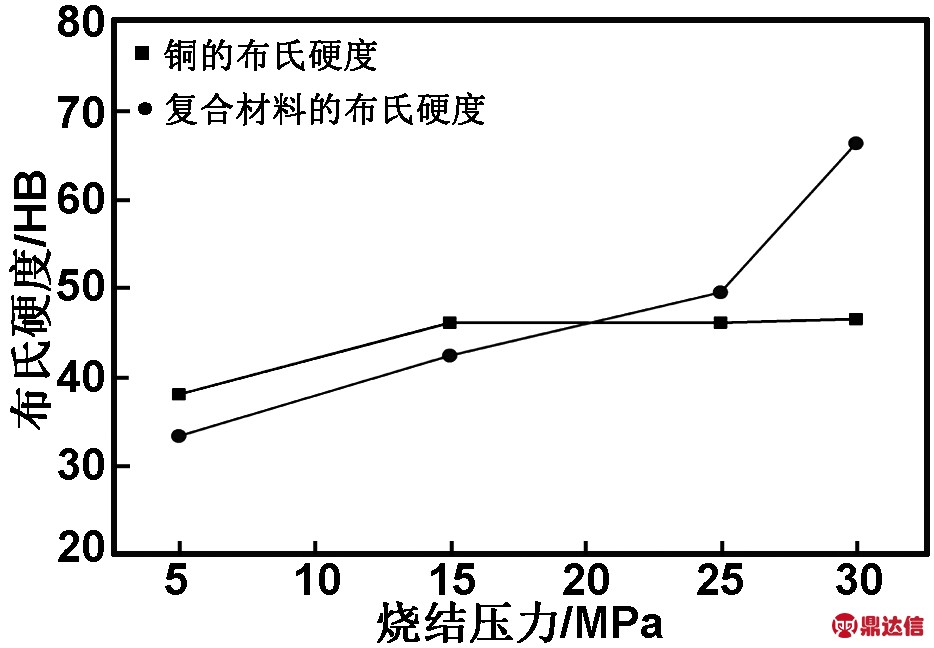
图7 复合材料的布氏硬度与烧结压力的关系
Fig 7 The relationship between the sintering pressure and Brinell hardness of the present composite
此外,在烧结压力较高时,复合材料的硬度相比同条件烧结的纯铜硬度有了显著提高,这是因为石墨烯和钛粉两种高强度材料的加入,对铜晶粒的变形产生了很大的束缚,阻碍了基体铜晶粒中的位错运动。另外石墨烯能阻碍铜晶粒的生长,使得晶粒更加细化,从而使得复合材料的硬度得到显著提高。
3 结 论
(1) 采用超声波分散和湿磨法可有效地把石墨烯均匀分散到铜基体上,获得混合较均匀的石墨烯/铜/钛复合粉末。
(2) 随着烧结压力的升高,复合材料晶粒尺寸不断减小。
(3) 在5~30 MPa范围内升高烧结压力,复合材料导电率先上升后下降,当烧结压力达到25 MPa时,导电率达最大值51.2%IACS;复合材料的密度和硬度值不断升高增大。