[摘要] 以2.0T高压共轨柴油机和Bosch第二代高压共轨燃油喷射系统为基础,制定了起动控制策略,并通过试验,在喷油量一定的情况下,优化了起动控制策略中起动调整转矩常数、喷油比例和喷射定时等参数。结果表明:起动调整转矩常数设为25N·m,使燃烧和放热重心都在上止点附近,燃油燃烧充分;2次预喷和1次主喷的喷油比例设置为20%-20%-60%,可缩短发动机起动时间和稳定起动过程中的最高缸压;通过正交试验确定了最优喷射正时,有效降低了起动循环最高缸压均方差,并提高了起动首循环热效率。发动机经优化后,缩短了的起动时间,提高了起动的平顺度和平稳性,燃油燃烧更加充分,从而全面提高了发动机的起动性能。
关键词:高压共轨柴油机;起动控制策略;参数优化;正交试验
前言
柴油机具有动力大、燃油经济性高、运行可靠和经久耐用等优点,在国民经济的各个领域内都得到了广泛的应用。2017年起,随着国V排放标准的实施,对于柴油机性能和排放污染物控制的要求越来越高。高压共轨电控燃油喷射技术的引入,可实现对喷油压力、喷油量、喷油定时和喷油规律的精确控制,进而实现对整个燃烧过程的控制,从而提高柴油机的动力性和经济性,并降低排放污染[1-2]。
起动性能是衡量柴油机性能优劣的重要指标之一,国内外对柴油机起动控制策略开展了大量的研究,以改进其起动过程。但由于高压共轨柴油机起动控制策略中涉及的参数多,参数相关性强,控制自由度大,所以对高压共轨柴油机起动控制策略中参数的匹配标定与优化十分复杂[3]。
本文中基于2.0T高压共轨柴油机,搭建了试验台架,利用Bosch提供的工具库接口确定了发动机起动控制策略,并通过试验,研究了起动控制策略中起动调整转矩常数、喷油比例和喷射定时等参量对柴油机起动特性的影响规律,并通过正交试验方法以较少的试验次数得到了较高的试验效率,根据因素水平的最优组合进行参数优化,切实地提高了该高压共轨柴油机的起动性能。
1 试验系统
试验台架和测试设备框图如图1所示。试验中采用的发动机为本课题组与某企业合作开发的2.0T高压共轨柴油机,该发动机具有真空阀控制VNT增压器、缩口型燃烧室、高压共轨喷射系统,其具体技术参数如表1所示。采用的Bosch第二代高压共轨系统的主要参数如表2所示。
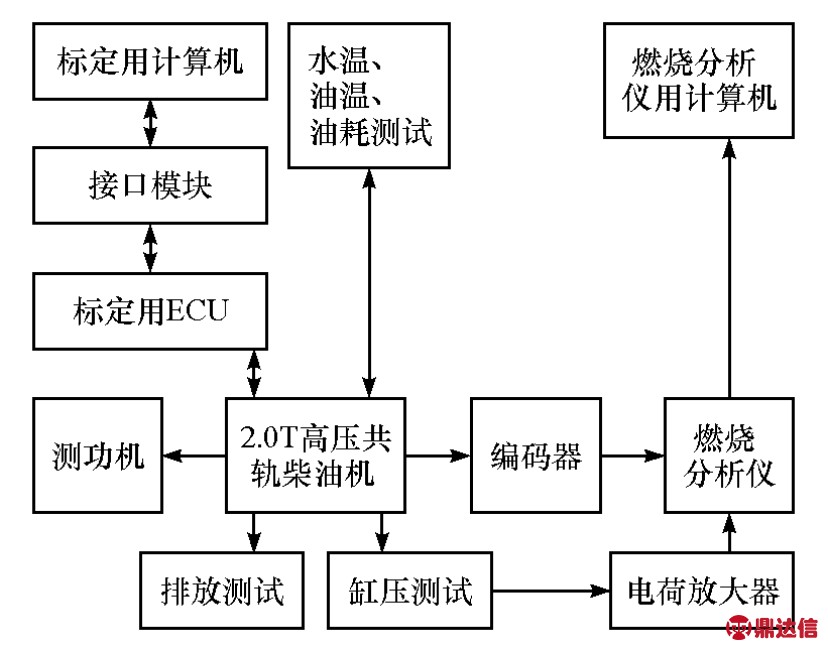
图1 2.0T高压共轨柴油机试验系统
发动机与标定用ECU的一端相连,ECU的另一端通过ETK与接口模块ES590相连,ES590再通过CAN总线与标定用计算机连接,从而实现在线实时观察和采集数据并进行标定。发动机后端连接电涡流测功机CW260,用来测试转矩、转速等参数。为分析不同条件下起动过程中气缸内燃烧状况,在第1缸电热塞处安装Kistler5018型气缸压力传感器,并将所测得的缸压经电荷放大器处理后送至DS9100型燃烧分析仪。为了测取示功图,在发动机曲轴前端安装光电编码器,以同步测量曲轴转角和上止点信息。燃烧分析仪根据这些参数进行压力升高率和放热率等计算处理。同时,发动机还安装了油耗仪、温度、压力等传感器,以测量油耗、进排气、水温、机油温度和压力等参数。利用这些参数,可计算出燃烧热效率和喷油轨压等指标,作为衡量柴油机起动控制策略优劣的依据。
表1 柴油机主要技术参数
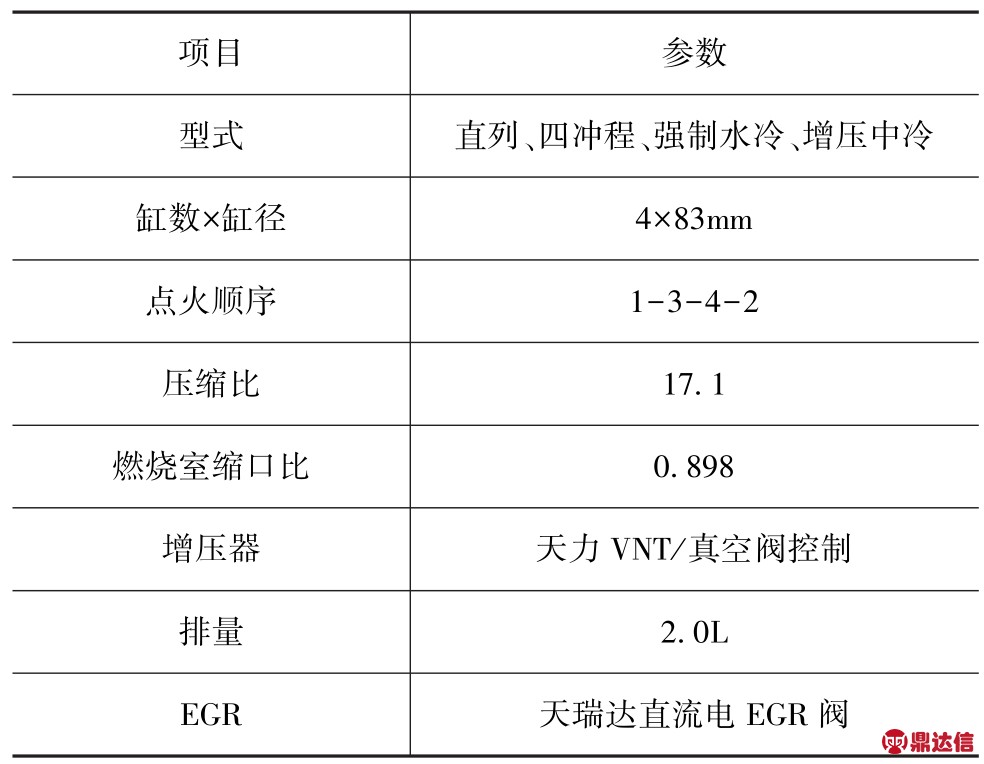
表2 燃油喷射系统主要技术参数
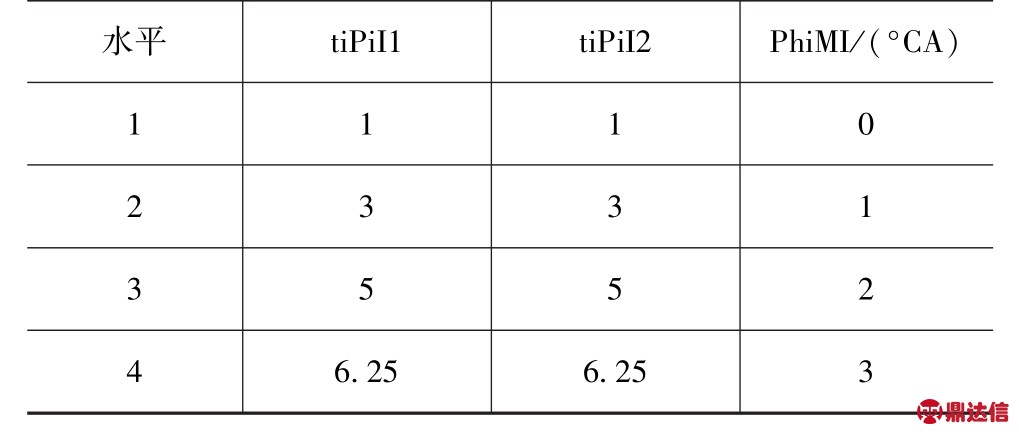
2 起动控制策略
2.1 起动工作状态转换
高压共轨柴油机的运行工况比较复杂,在制定总控制策略时须根据其运行状态划分不同工况,分别设计相应的子控制模块[4-7]。本发动机的工作状态分为运行准备状态、起动状态、运行状态、运行完成状态和停止状态,各状态间根据一定逻辑进行转换。对于起动状态,只有从运行准备状态转换为起动状态这一种情况,其转换策略如图2所示。
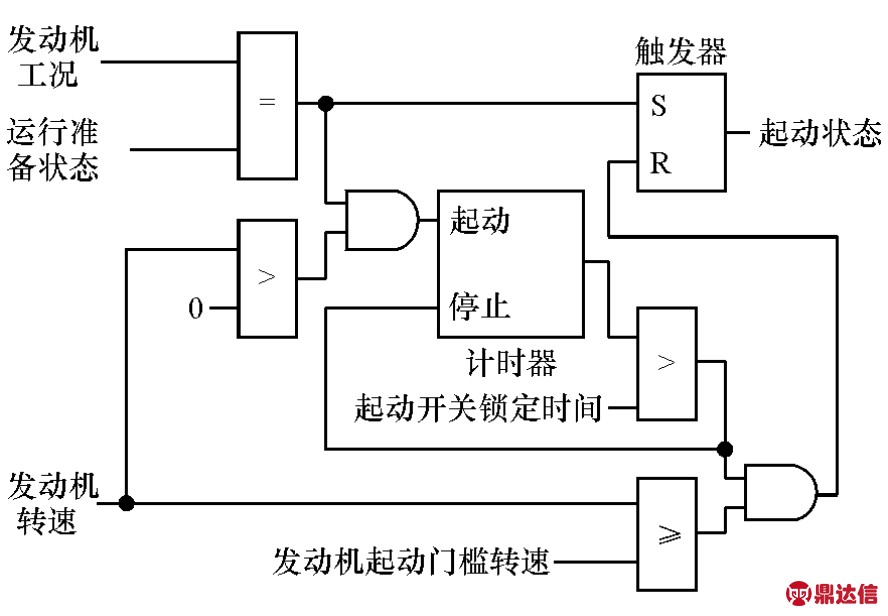
图2 起动工作状态转换策略
根据气压和发动机温度,通过相关的起动门槛转速MAP,查出转入起动状态的临界转速。如果发动机转速超过该临界转速,且当前处于运行准备状态时,发动机将进入起动状态。策略中还设置了一个计时器,只当发动机转速高于临界转速一定时间后上述判断条件才起作用,防止了因发动机瞬时转速波动而产生的工作状态误判。
2.2 起动喷油量计算
起动喷油量是保证柴油机顺利完成起动过程的关键控制参数之一[8-10],起动喷油量设定得过少不能顺利完成起动过程,而过多则影响燃油经济性和HC,CO和微粒等排放特性。本文中采用基于转矩的喷油量计算方法,如图3所示。基于这种算法,首先要确定起动条件下所必要的假想的起动转矩,它通过发动机转速、发动机温度和气压等参数算得;然后,根据油量和起动转矩之间的转换关系获取起动喷油量。这种方法利于整车动力传动系统的集成化控制,且可兼顾发动机动力性、经济性和排放性能[11]。
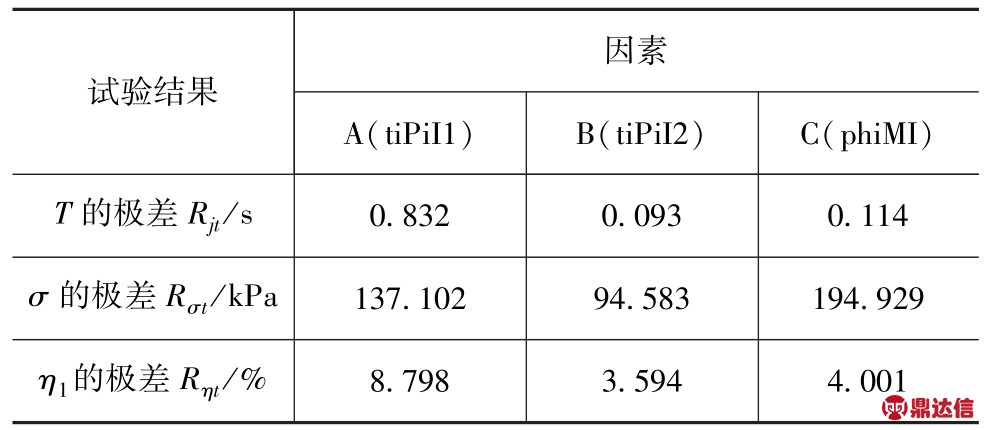
图3 起动喷油量计算策略
起动喷油量计算中所需起动转矩参数的计算策略如图4所示,当起动转矩控制开关处于断开状态时起动转矩等于零,否则起动转矩等于起动基础转矩和起动转矩限制常数中的较小值。起动基础转矩由基本转矩、起动调整转矩和起动矫正转矩3部分组成。其中,基本转矩可根据发动机转速和发动机温度查起动基础转矩MAP得到;如果把起动基础转矩定得过高,虽能保证冷起动的性能,但会产生过大的油耗和排放,反之如果将起动基础转矩定的过低,则会影响发动机起动的可靠性,因此,在起动策略中引入了起动调整转矩,用来根据发动机转速动态调整起动转矩的大小,根据图4中起动调整转矩的计算策略可知,起动调整转矩对起动转矩的调整作用体现为一斜坡函数,当发动机转速低时为起动转矩提供较大的补偿,随着转速的提高起动调整转矩的补偿作用逐渐减小。
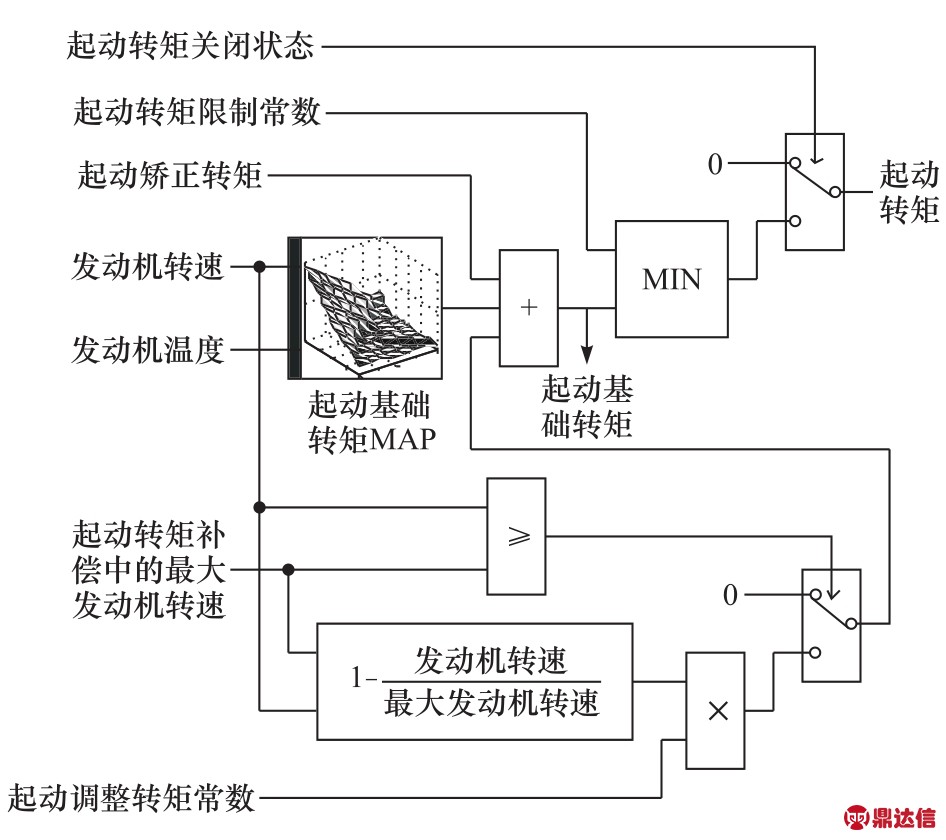
图4 起动转矩计算策略
起动矫正转矩是在起动基础转矩的计算中需要考虑的矫正量,其计算策略如图5所示。起动矫正转矩的大小主要取决于发动机转速和发动机温度两个因素,利用这两个参数查起动转矩加性矫正MAP,再乘以由气压决定的矫正因子,即可得到起动矫正转矩。
2.3 喷射方式
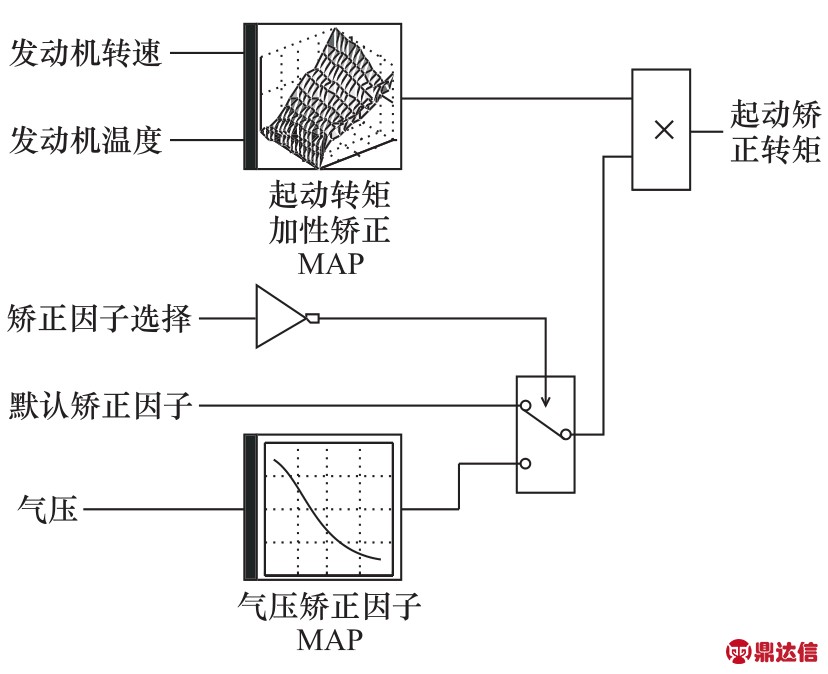
图5 起动矫正转矩计算策略
2.0 T高压共轨柴油机燃油喷射系统的CRIN2喷油器每循环可支持5次喷射,包括2次预喷、1次主喷和2次后喷。2次预喷和1次主喷主要影响发动机的起动性能,2次后喷主要用来改善发动机的排放性能,提高燃烧后期燃烧温度和缸内湍流动能,降低排气中的碳氢化合物,并提高排气温度为后处理提供更好的工作条件。本文的目的是优化发动机起动性能,因此重点研究预喷 2(PiI2)、预喷 1(PiI1)和主喷(MI)这3次喷射,具体喷射方式如图6所示。图中,tiPiI2为预喷2提前时间相对于基础MAP的系数,tiPiI1为预喷1提前时间相对于基础MAP的系数,phiMI为主喷提前角。2次预喷提前时间的基础MAP如表3所示。
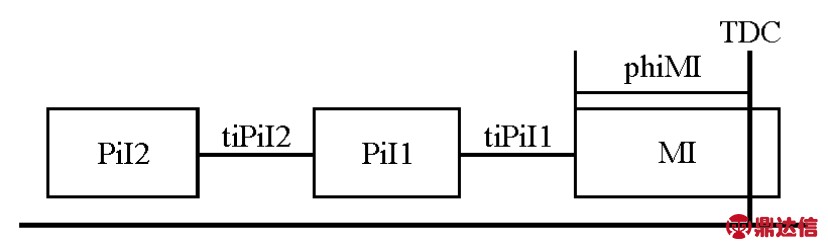
图6 喷射方式
表3 两次预喷提前时间的基础MAP
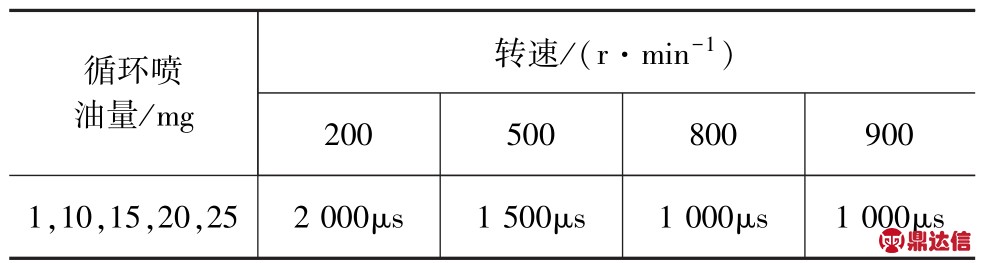
3 起动控制策略参数优化
3.1 起动调整转矩常数的影响
由图4所示的起动转矩计算策略中的起动调整转矩常数定义可知,其大小直接关系到斜坡函数的初始值。本文中在喷射次数、起喷转速、预喷油量和预喷时间等参数不变的条件下,通过3组对比试验研究了其对起动性能的影响。试验环境为:室温25.1℃、湿度40%、大气压力 993kPa、冷却液温度30.5℃。试验结果如表4所示。
表4 起动调整转矩常数对起动性能的影响
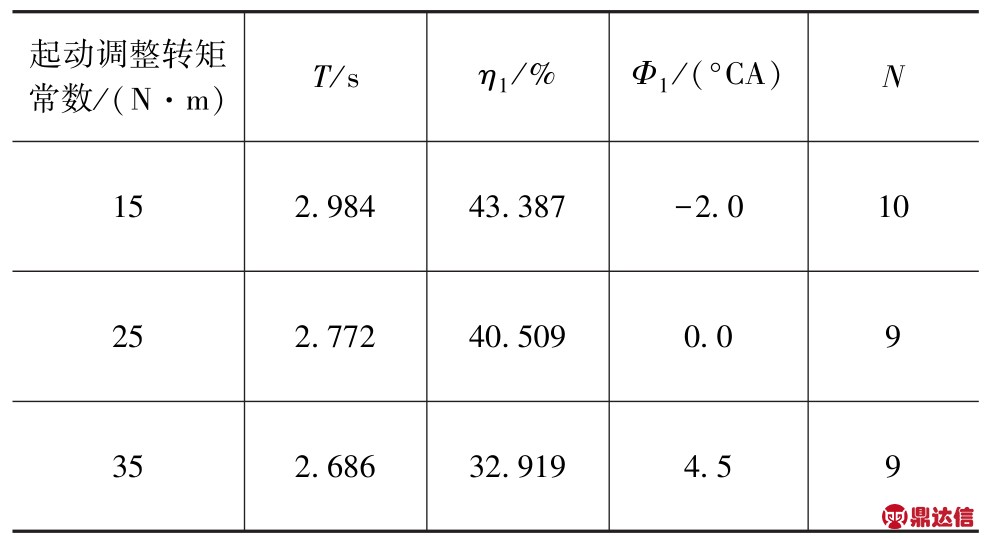
表中:T为起动时间;η1为首循环燃烧热效率,其定义为发动机首循环有效功率的热当量与消耗燃料所含热量的比值;Φ1为首循环放热率达最大值时的曲轴转角;N为起动循环数(后续试验中变量的定义同此)。由表4可知,随着该常数的增大,起动时间缩短,起动循环数减少,但当其设定过高时首循环最高缸压和燃烧效率都有明显下降。这主要是由于随起动调整转矩常数的增大总起动喷油量增加。因此,其设定为15N·m时,主喷油量相对较小,燃烧放热重心在上止点之前;当其设定为35N·m时,主喷油量相对较大,导致喷射重心后移,燃油雾化时吸收热量,导致缸内温度降低,着火延迟期延长,所以燃烧放热重心出现在上止点后4.5°CA左右;当其设定为25N·m时,燃烧、放热重心都在上止点附近,燃油燃烧充分。因此,在后续试验中将起动调整转矩常数的值均设定为25N·m。
3.2 不同喷油比例对起动性能的影响
在起动控制策略中其它参数不变的条件下,进行了3次喷油的比例对发动机起动性能影响的试验研究。试验中,针对2次预喷和1次主喷设计了15种喷油比例组合,并按照预喷 1(PiI1)、预喷 2(PiI2)、主喷(MI)3个参数所分配的比例由小到大排列的顺序进行试验,如表5所示。试验环境为:室温24.1℃、湿度30%、大气压力982kPa、冷却液温度31.6℃。
表中σ为起动循环最高缸压均方差(后续试验中变量的定义同此)。根据起动循环个数的多少,将上述试验分成4组,其中起动循环次数等于7的分为I类;等于8的分为II类;等于9的分为III类;大于9的分为IV类。通过表5可明显看出,当起动循环次数少时,起动时间也相应较短,I类试验的起动时间均低于2.5s;II类试验的起动时间在2.5~2.7s之间;III类试验的起动时间在2.7~2.8s之间;而IV类试验的起动时间均大于2.9s。
表5 不同喷油比例对起动性能的影响
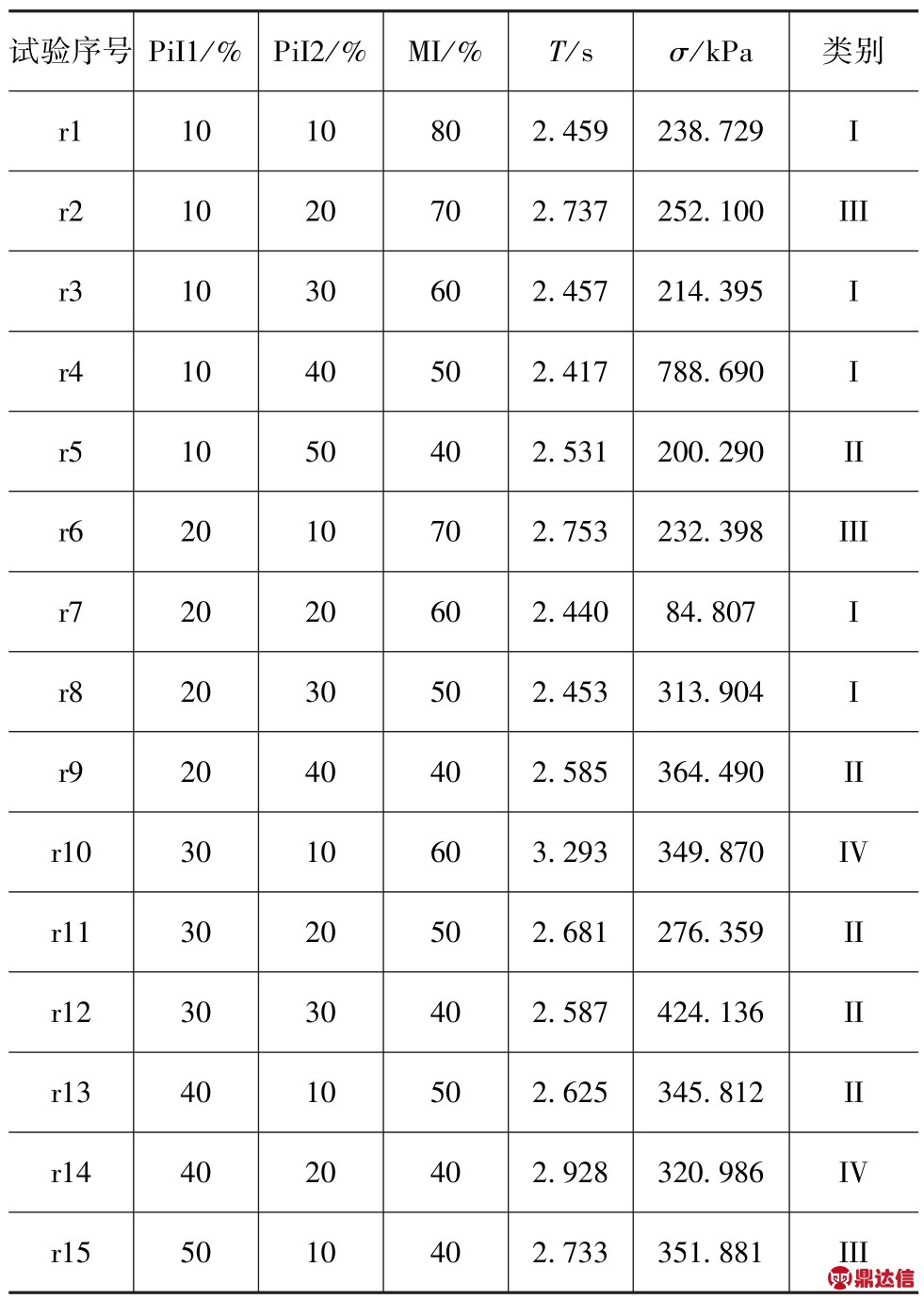
起动过程是一个瞬态的过渡过程,为更全面地测试不同喷油比例对起动性能的影响,除起动时间外,还计算了每种喷油比例条件下起动循环最高缸压波动的均方差σ,用来衡量每种情况下起动循环的稳定性。由表5可知,在4类试验中,起动循环最高缸压波动的均方差σ最小的几种喷油比例组合分别为r7,r5,r6和r10,说明上述喷油比例组合的起动过程分别在4类试验中是最稳定的。下面以这4种组合作为代表性的试验方案,对发动机起动首循环和起动后期循环的燃烧规律进行比较分析,结果如图7所示。
由图7可知,喷油比例组合r5的起动性能在首循环和末循环示功图中表现均比较突出,由于预喷量较大,预喷2的比例达到了50%,缸内气体混合均匀,燃油在上止点前0.5°CA左右全部喷入缸内,雾化效果好,因此传热损失减少,柴油在燃烧室内提前达到自燃条件,直接实现预混燃烧,缸压明显高于其它几种比例组合,且起动循环数较少,起动时间较短。组合方案r6,r7和r10的示功图表现接近,它们的喷射结束点均在上止点前1°CA附近。方案r6和r10在首循环中燃烧重心更接近上止点,但燃烧性能随循环数的增加逐渐下降,在末循环中这两种喷油比例组合的缸压下降明显,且起动循环数多,起动时间很长。而方案r7的示功图表现稳定,起动循环最高缸压波动的均方差σ为各方案中最小,起动运转最为稳定,且起动时间最短。综上所述,喷油比例组合r5和r7的性能要高于其它方案。下面通过对比这两种方案的放热规律,来进行最后的优选,如图8所示。
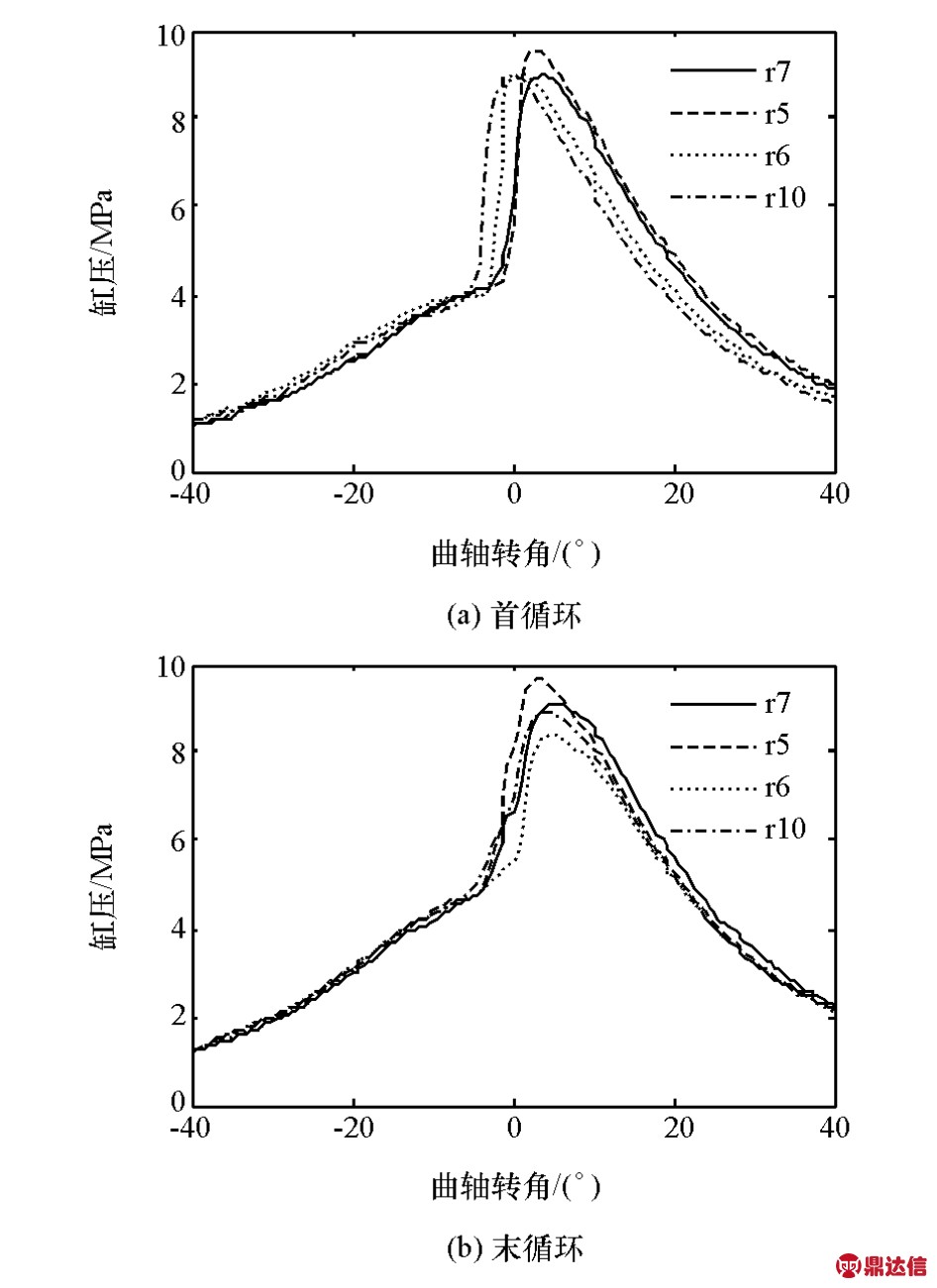
图7 4种比例组合起动首循环和末循环示功图对比
由图8可知,方案r5和r7的首循环放热率曲线都呈单峰,r5的最大放热率更高,而r7的放热重心更接近上止点。在末循环放热率曲线中,方案r7由于预喷油量小,前期喷射预混量较小,故其预混燃烧量小于扩散燃烧量,对应的放热率曲线出现双峰,且峰值先低后高;方案r5正相反。综合比较两种方案,r7的起动循环最高缸压波动小,有利于提高车辆起动的舒适性;全过程运转没有出现失火现象;起动循环数少,起动时间短,且在中、后期循环中放热率高、燃烧稳定,因此,选取方案r7进行下一步起动喷射时间的正交试验优化。
3.3 起动喷射时间的正交试验优化
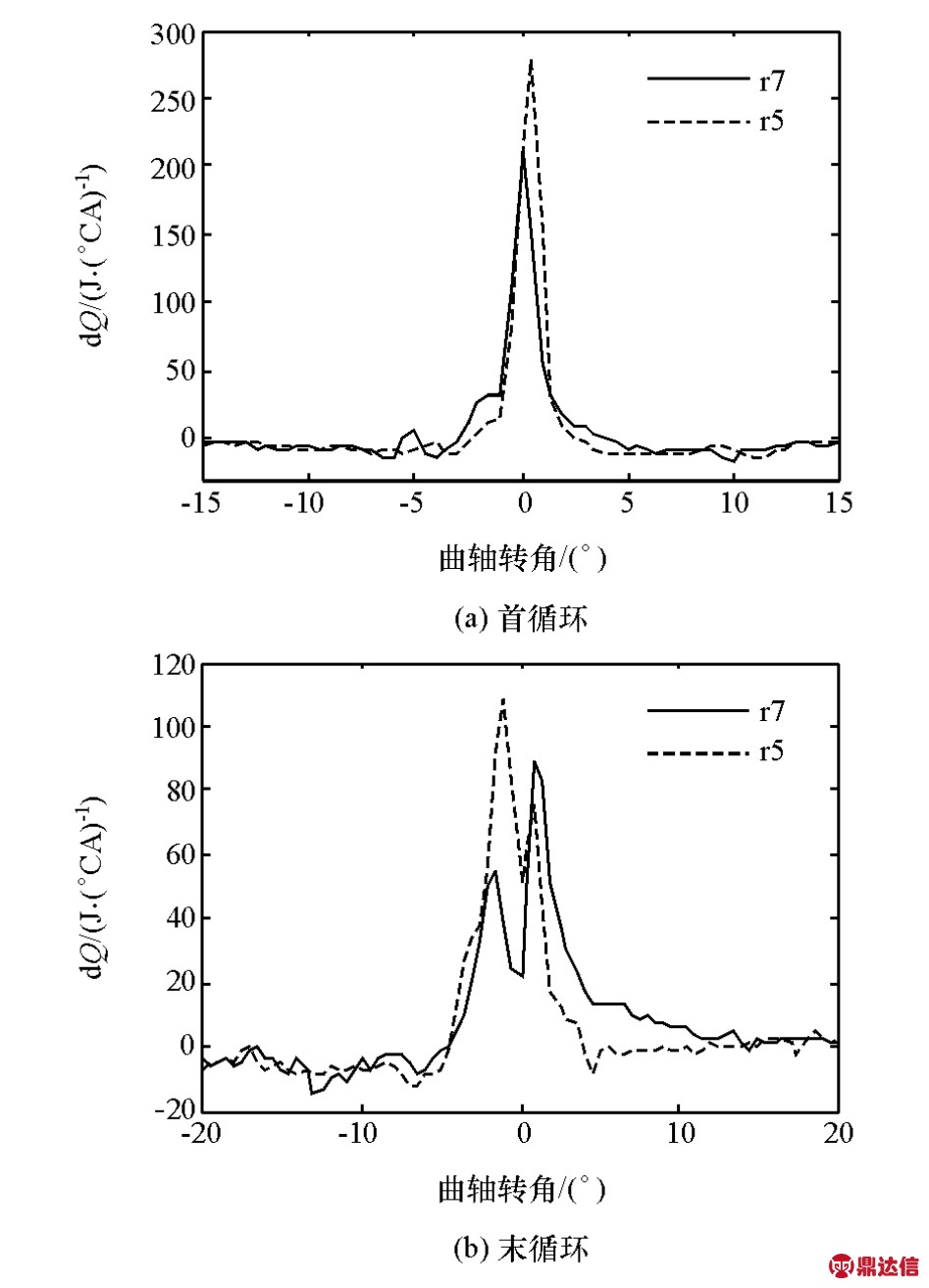
图8 方案r5和r7起动首循环和末循环放热率曲线对比
在起动策略中的喷油量计算关键参数和喷油比例确定后,本文中研究了3次喷油的喷射时间对起动性能的影响,优化了两次预喷提前时间和主喷提前角的参数设置。由于这3个参数间的相关性较强,故采用正交试验法进行优化,正交试验法能够在试验点较少的情况下,获得较全面的试验信息和较高的试验精度,抑制试验干扰,获得全面的优化结果[12]。
首先,确定正交试验中对应于上述3个参数的3个因素A,B和C,分别为预喷1提前时间相对于基础MAP的系数tiPiI1、预喷2提前时间相对于基础MAP的系数tiPiI2和主喷提前角phiMI;其次,考虑到发动机的实际硬件条件,确定了各因素的4个水平,如表6所示;最后,采用标准正态表L16(45)进行16组试验,结果如表7所示,表中剩余的两个因素D和E栏中的数值无实际意义。试验环境为:室温30.4℃、湿度 38%、大气压力 994kPa、冷却液温度33.5℃。
表6 各因素的水平
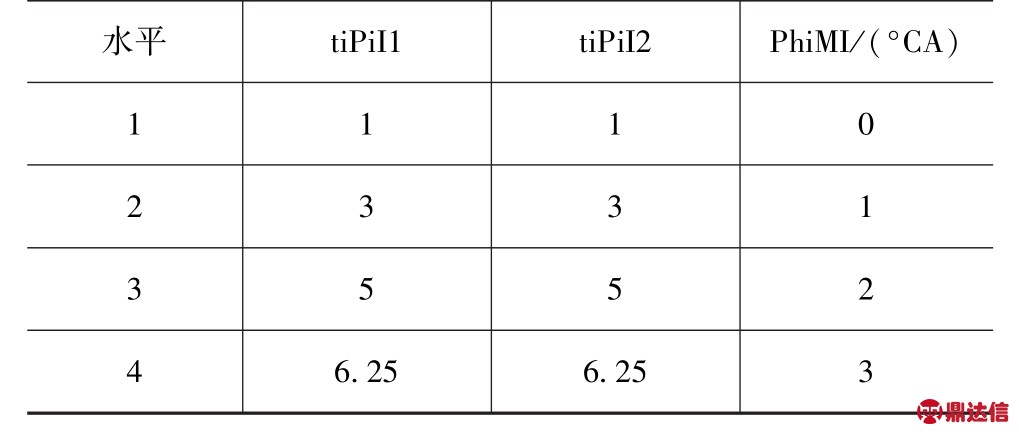
表7 16组正交试验结果
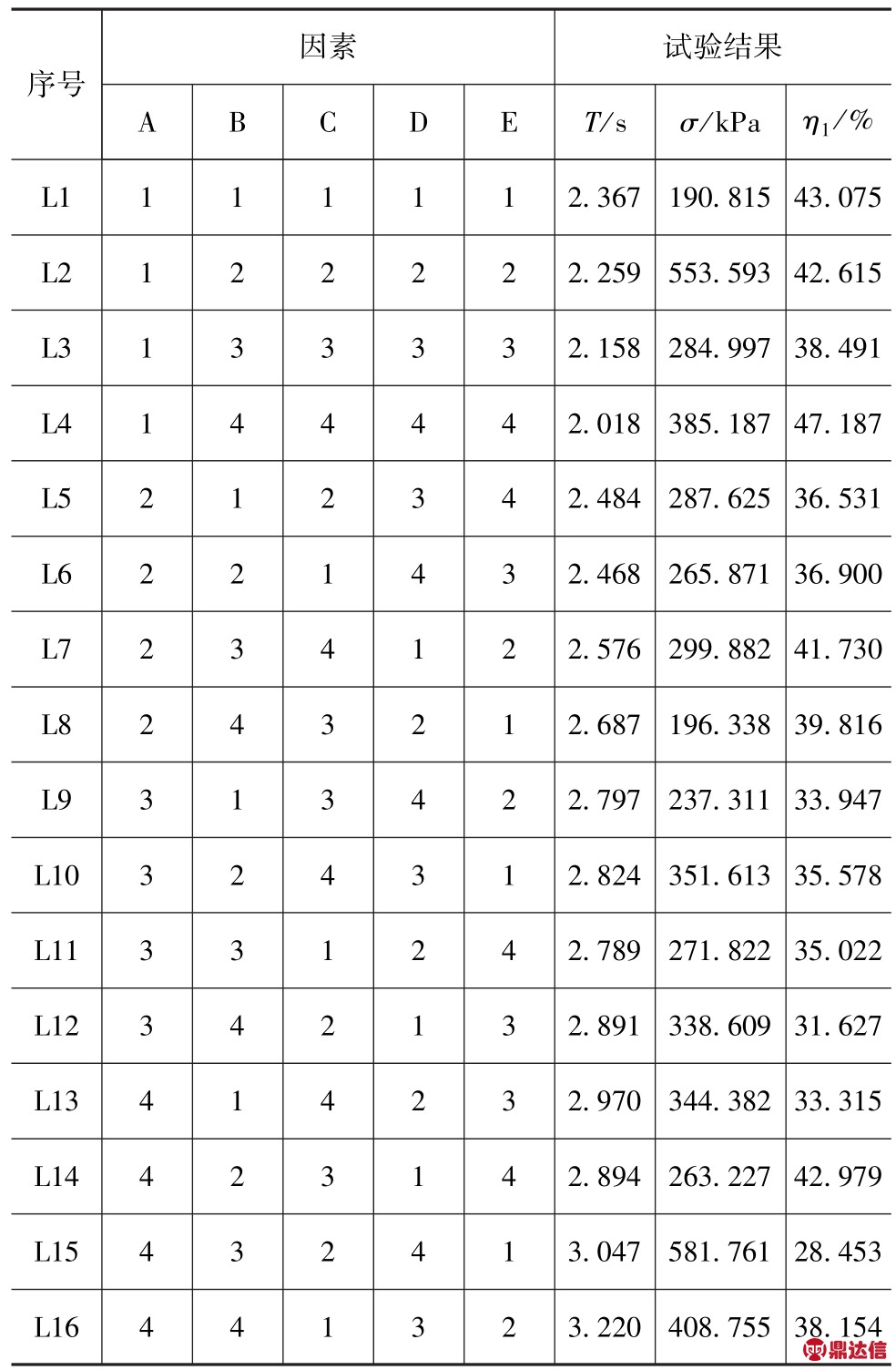
采用极差分析法分析正交试验的结果,利用各因素的极差可判断它们对试验结果的影响程度,并通过各因素均值的大小确定最优的水平组合。试验中用j代表因素,用i代表水平,则各因素极差Rj的分析结果如表8所示,各水平对3个因素的均值Kji的影响如图9所示。
表8 各因素的极差Rj
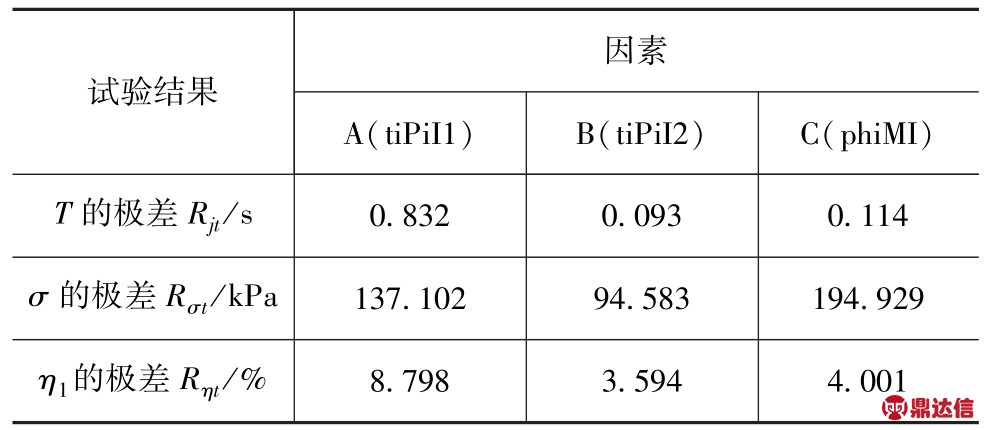
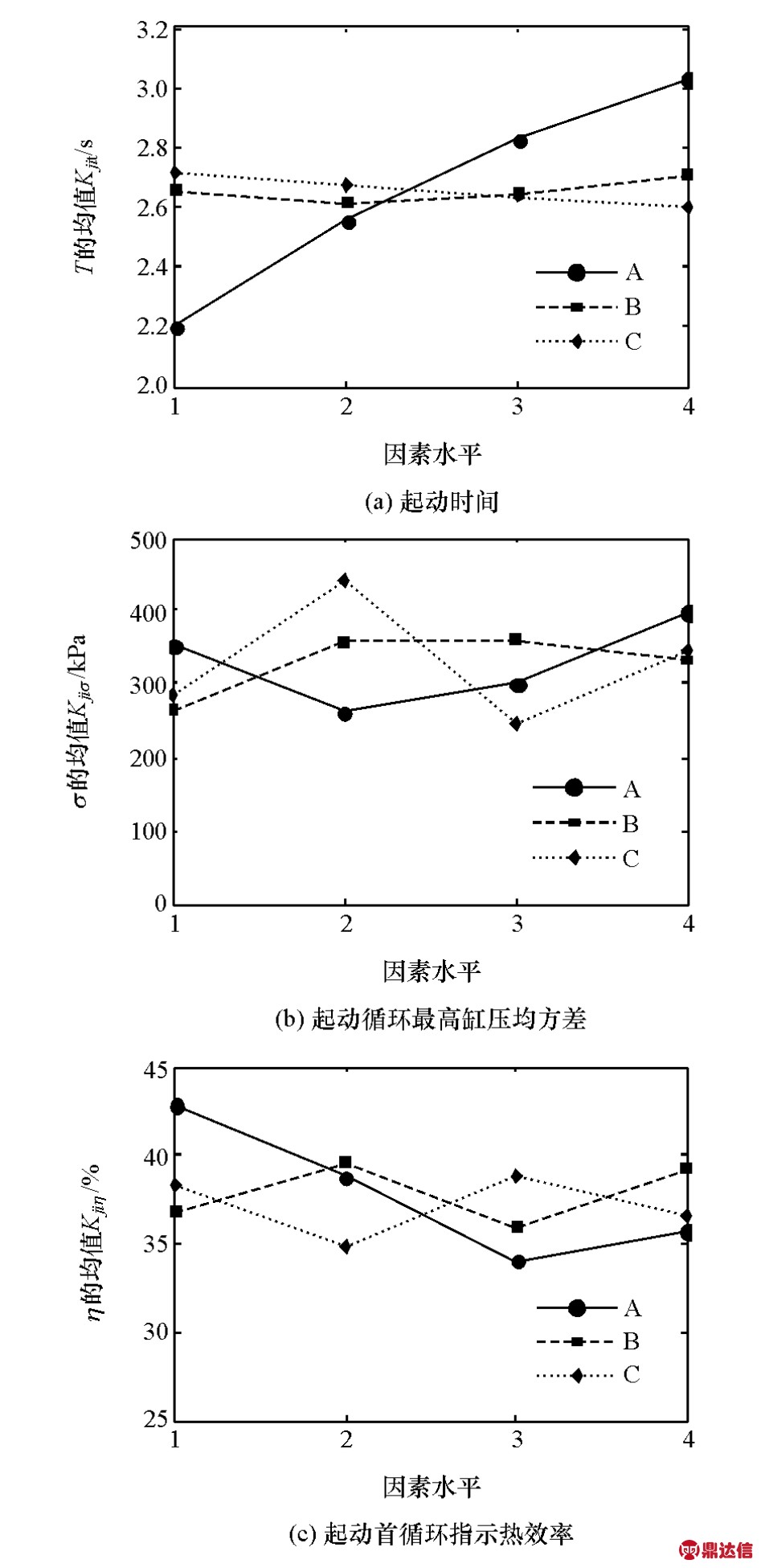
图9 各水平对3个因素试验结果均值Kji的影响
试验结果对应各因素的极差决定了该因素对该试验结果的影响程度,因素对应的极差越大,该因素的影响力越强。因此,由表8可知:各种因素对起动时间影响程度的顺序为tiPiI1>phiMI>tiPiI2;各种因素对起动循环最高缸压均方差影响程度的顺序为phiMI>tiPiI1>tiPiI2;各种因素对起动首循环指示热效率影响程度的顺序为tiPiI1>phiMI>tiPiI2。
根据各因素水平对各因素试验结果均值的影响情况,可确定最优的因素水平组合。从起动时间上看,起动时间越短发动机的起动过程越自然顺畅,因此,由图9(a)可知,对于起动时间来说各因素水平的最优组合为A1,C4和B2;从起动循环最高缸压均方差上看,σ越小发动机的起动过程越平稳,由图9(b)可知,对于起动循环最高缸压均方差来说各因素水平的最优组合为C3,A2和B1;从起动首循环指示热效率上看,η越高燃油燃烧越充分,因此,由图9(c)可知,对于起动首循环指示热效率来说,各因素水平的最优组合为A1,C3和B2。
综合起动时间、起动循环最高缸压均方差和起动首循环热效率的正交试验结果,最终确定的最优因素水平组合为:预喷1提前时间相对于基础MAP的系数tiPiI1等于1;预喷2提前时间相对于基础map的系数 tiPiI2等于3;主喷提前角 phiMI等于2°CA。
4 结论
(1)针对2.0T高压共轨柴油机,制定了起动控制策略,并对起动控制策略进行了参数优化试验研究。结果表明,通过起动策略优化,缩短了发动机的起动时间,提高了最高缸压的平稳度,并改善了燃油的燃烧效率,从而大大提高了发动机的起动性能。
(2)起动调整转矩常数设定过低会导致起动循环次数的增加,降低冷起动性能;起动调整转矩常数设定过高虽会缩短起动时间,但也会大大降低首循环最高缸压和燃烧效率。因此,要适当调整起动调整转矩常数,使燃烧、放热重心都在上止点附近,从而提高燃烧效率,并有效减少起动循环次数,缩短起动时间。在本起动策略中起动调整转矩常数的最优值为25N·m。
(3)3次喷油的比例对发动机起动性能的影响较大,总体趋势上预喷1的喷油比例较低时起动循环次数少、起动时间较短;预喷2和主喷的比例主要影响起动循环最高缸压均方差即起动的稳定性。通过多种组合方案的对比分析,最终确定本起动策略的最优喷油方案为:2次预喷和1次主喷的喷油比例为20%-20%-60%。由此可知,少量的预喷油量在压缩行程中燃烧,能使主喷期气缸内的压力和温度升高,主喷射喷油量燃烧的着火延迟期缩短,从而减少起动循环次数并有利于提高燃烧的稳定性。
(4)针对相关性较强的3个喷油正时参数采用正交试验方法进行优化,在起动时间、起动循环最高缸压均方差和起动首循环热效率3个方面进行考量,最终确定的最优因素水平组合为:预喷1提前时间相对于基础MAP的系数tiPiI1等于1;预喷2提前时间相对于基础MAP的系数tiPiI2等于3;主喷提前角phiMI等于2°CA。由此可知,适当增加预喷1与预喷2的时间间隔、减小主喷与预喷1的时间间隔、增大主喷提前角有利于加快起动速度,提高热效率,但为保证起动的平顺性,预喷1与预喷2的时间间隔不宜过大。试验结果表明,正交试验方法适用于高压共轨发动机起动控制策略中高相关性参数的优化,可通过较少的试验次数,确定因素水平的最优组合,还可看出因素对试验结果的影响趋势。