摘 要: 某企业大阵列电阻应变片修剪过程主要采用人工方式,效率低,劳动强度大,修剪质量不稳定,严重制约了企业的发展。针对此问题,设计研发了一台电阻应变片自动修剪设备。根据技术要求和试验论证,运用SolidWorks软件对总体方案进行了三维实体设计,对关键零部件进行了选型和设计。整个系统以LabVIEW为平台,采用工控机+数据采集卡的控制模式,运用闭环控制技术和气动控制技术,保证了系统的控制精度和易操作性。测试结果表明,该设备运行稳定,安全可靠,经济环保,各项参数均满足生产要求,有效地提高了企业的生产效率。
关键词: 大阵列电阻应变片;自动修剪;闭环伺服控制;工控机
电阻应变片是一种粘贴在弹性体的表面,将弹性体的机械变形转换为电信号输出的敏感元件,广泛应用于应力分析、测试计量、称重/测力传感器以及各种工程结构强度的诊断与评估等领域[1-2]。由于制作工艺复杂,电阻应变片通常都是整版阵列生产,然后再进行修剪、测试、分类[3]。某企业现有的做法是人工裁剪,这种修剪方法不仅生产效率低,工人劳动强度大,而且修剪尺寸精度低,同一批次产品的外形尺寸存在较大波动,不利于对产品质量的稳定控制。为了提高应变片的生产质量及生产效率,实现生产过程自动化、智能化[4],该企业提出了研制一种电阻应变片自动修剪设备的技术需求。
针对此需求,设计研究了一种大阵列电阻应变片自动修剪设备。该设备采用真空吸附技术固定电阻应变片膜片,通过高精度二维伺服滑台移动定位,使用气动技术驱动超薄刀片进行修剪,结构轻巧,操作简单,绿色节能。实现了大阵列电阻应变片的自动化、数字化修剪,有效提高了生产质量,降低了生产成本,进而提升了企业的市场竞争力。
1 总体方案设计
1.1 技术要求分析
某企业生产的模型号电阻应变片膜片平面图如图1所示,整版尺寸规格为102 mm×115 mm,厚度约为0.08 mm,共分布260个应变片。单个应变片见图右上角放大图,其尺寸为7.4 mm×4.4 mm,阵列为12行×22列,采用焊点相对的排列方式,行、列间距为0.5 mm[5]。
技术目标是将单个应变片产品从整版中分离出来,以便后续检测分选。技术要求是:(1)单个应变片的尺寸修剪精度为0.10~0.20 mm。(2)修剪效率不低于15 片/h。(3)具有膜片定位功能。(4)具有急停、复位及报警功能。(5)具有扫条码识别功能。(6)具有数据记录、查询功能。
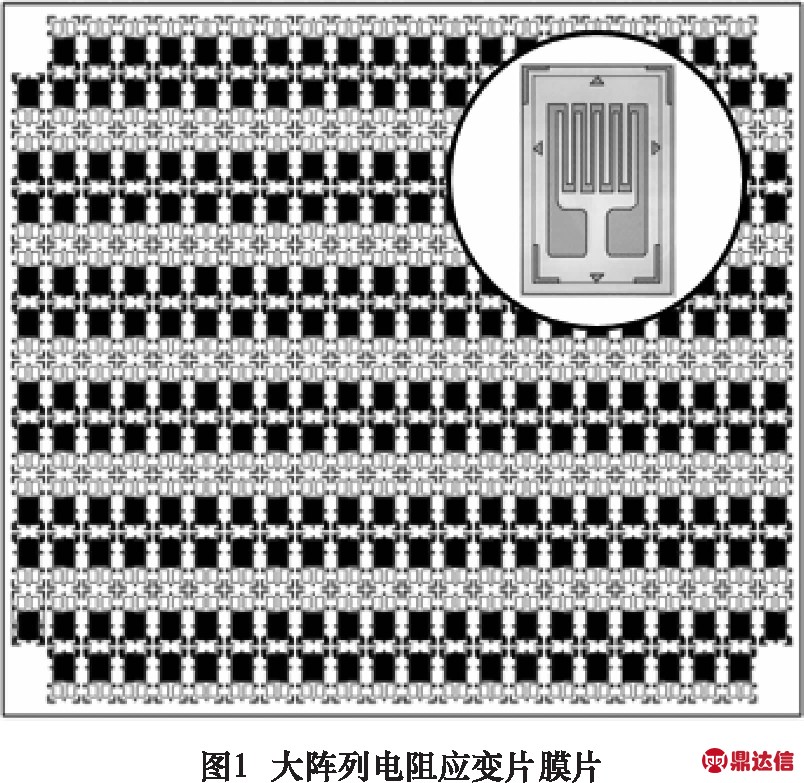
1.2 操作流程
(1)操作人员将电阻应变片膜片放置在吸附平台上定位固定。
(2)膜片固定后,按下启动按钮进行自动修剪。
(3)修剪完成后,刀具回原点待机。
(4)自动分选机构对修剪的应变片进行分选。
(5)分选完成后,吸附平台回原点待机,进入下一次工作循环。
1.3 总体方案设计
在生产后期需要将单个应变片产品从整版中分离出来,进行检测,最后根据检测结果进行分选。目前,某企业的修剪方法是人工使用剪刀沿着应变片单元外边框将单个产品修剪下来,外形尺寸波动较大;对应变片的电阻、电压测量主要依赖人工测试,测试效率低,容易出错;分选全部是人工分选,效率低,劳动强度大[6]。经过与企业的深入沟通,决定做方案时,整体考虑,即检测、修剪、分选一体机设计,前期先做自动修剪部分,以解企业的燃眉之急。
在方案论证时,通过试验发现激光修剪、旋转圆刀片修剪效果都不理想,主要表现在修剪切边毛刺大,不整齐,老化试验不合格等,最后发现采用刀片进行划片修剪效果较好,各参数均满足技术要求。电阻应变片阵列膜片整体厚度0.1 mm左右,尺寸小,重量轻,不能弯折,定位固定、修剪难度较大,考虑到经济性、实用性,选择二维线性机构,结构简单,控制方便。阵列膜片固定采用真空吸附装置,刀具先X方向修剪,然后旋转90°Y方向修剪,X、Y方向上的移动定位使用高精度二维伺服滑台。整体方案主要包括自动检测装置、自动修剪装置、自动分选装置和工控机控制系统,其中自动修剪装置主要包括机架、电阻应变片定位、固定装置和刀具机构。运用SolidWorks对整体方案进行三维设计,结果如图2所示。
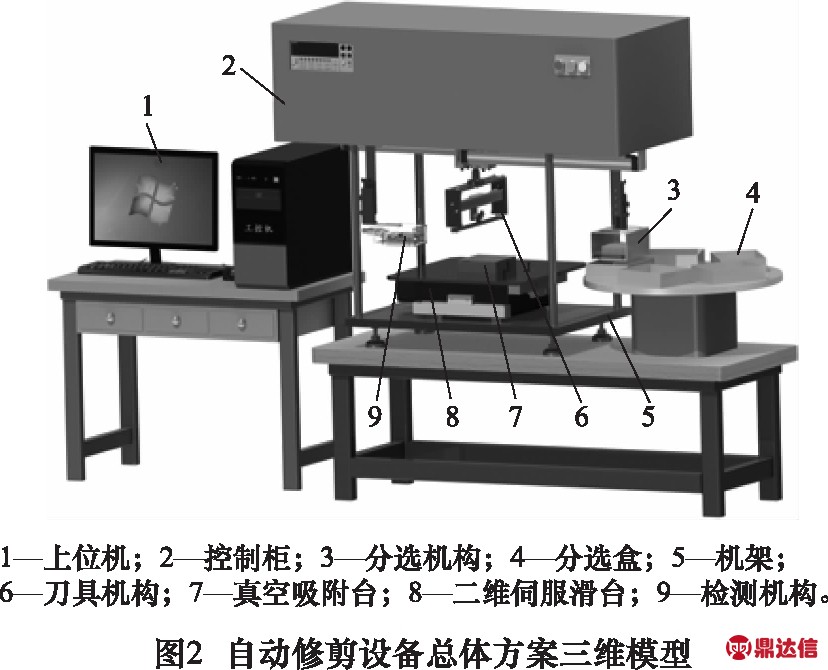
2 主要零部件设计选型
2.1 真空吸附装置
真空吸附装置主要有上端盖、密封垫、下腔体构成[7],其正视图和俯视图如图3所示。下腔体采用铝合金板材铣削加工,底面厚6 mm,四周壁厚10 mm,在四周棱台上加工有M5的螺纹孔,一个侧面加工有Rp1/4管螺纹孔,用于连接气动接头。上端盖采用铝合金板材加工,厚度3 mm,上平面上加工有安装孔、阵列圆形吸附孔和阵列沟槽,并且在平面的4个角上刻有参考定位线。阵列吸附孔直径为0.1 mm,采用激光加工,主要用于对应变片膜片进行吸附固定,平均每个应变片单元对应4个吸附孔;沟槽宽0.3~0.5 mm,深0.6 mm,采用线切割加工,主要用于自动修剪时刀片走刀,阵列为13行×23列;上端盖工作平面采用铣削+抛光的加工方法,表面粗糙度Ra 0.05 μm左右,主要是为了电阻应变片膜片能和吸附表面紧密贴合,吸附牢靠,不漏气。
2.2 刀具装置设计
(1)刀片选择
刀片主要用于片膜片的分切,选择德国鲁茨LUTZ三孔刀片,其尺寸为43 mm×22 mm×0.1 mm,刀刃表面涂有硬质涂层,使用寿命长,切削无毛刺,广泛应用于工业塑胶、薄膜、铝箔、胶带、纸张等高速分切。
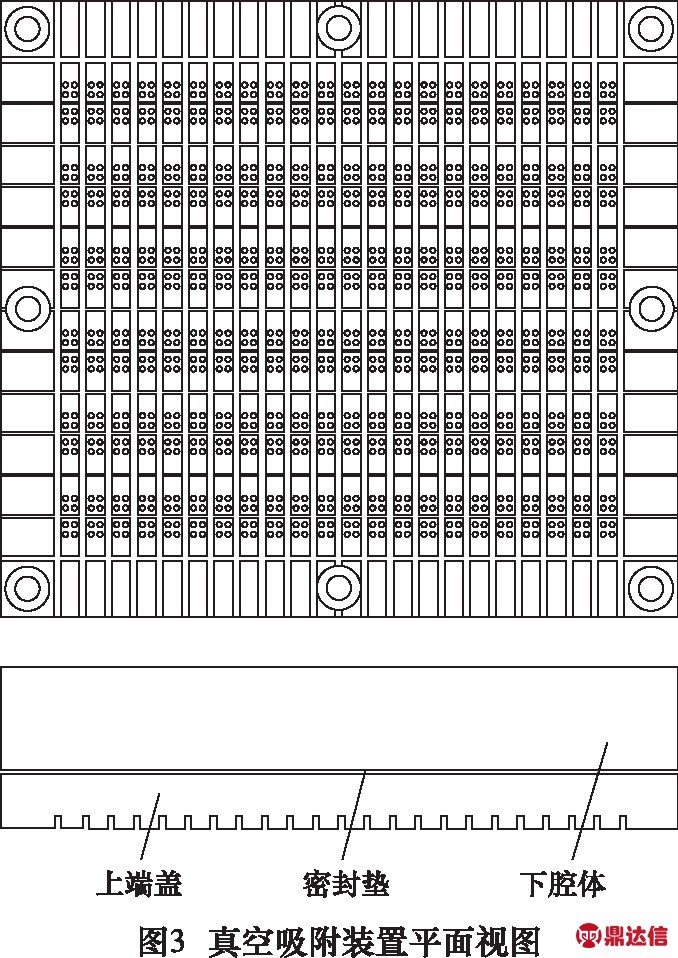
(2)刀片移动机构
刀片移动机构主要是驱动刀片快速移动,实现应变片膜片的划切,选择费斯托FESTO公司生产的无杆气缸,其型号为DGC-12-200-KF-P-A,采用循环滚珠轴承导轨,有效行程200 mm,最大移动速度1.2 m/s,重复精度0.02 mm,理论推力68 N。
(3)刀具旋转机构
刀具旋转机构主要实现刀具装置的上、下移动和90°旋转运动,采用费斯托FESTO公司的摆动/直线气缸,其型号为SL-25-80-270-P-A-S2-KF-B,直线行程80 mm,最大摆角270°,摆动重复精度0.1°,可精确设定摆角,安装方便,定位精度高[8]。
(4)刀具装置设计
刀具装置如图4所示,主要有安装板、定位板、无杆气缸、刀片夹板、压板、压板导向杆、调节弹簧等构成[9]。应变片单元的间隙为0.5 mm,要保证修剪精度,刀片的安装精度要求较高,主要有刀片和吸附平台的垂直度以及和气缸滑台平面的平行度,为了补偿安装误差和系统误差,刀片必须设计成活动可调的。刀片的安装角度、上下位置及前后位置都可活动调节,在刀片安装板的一侧加工有均分分布的刻度线,在刀片安装轴的一端加工有定位线,通过定位线和刻度线的位置,调整刀片的安装角度;刀片的上下位置通过刀片安装板的U型槽调节;在刀片安装轴和刀片安装板之间装有碟形弹簧,通过调节预紧力调节刀片的前后位置。
膜片在X方向修剪完成后,是一条一条分开的,这时吸附固定不牢靠,在Y方向修剪时,由于刀片的剪切力的作用,条形膜片的位置会发生变动,为此设计了压板,在压板中间开设有走刀槽,压板和定位竖板弹性连接,并配有导向杆导向,当刀具装置向下运动时,压板和膜片接触,并通过压缩弹簧将膜片压紧,通过弹簧作用可以调节压紧力大小,以便压板平面和膜片充分接触。
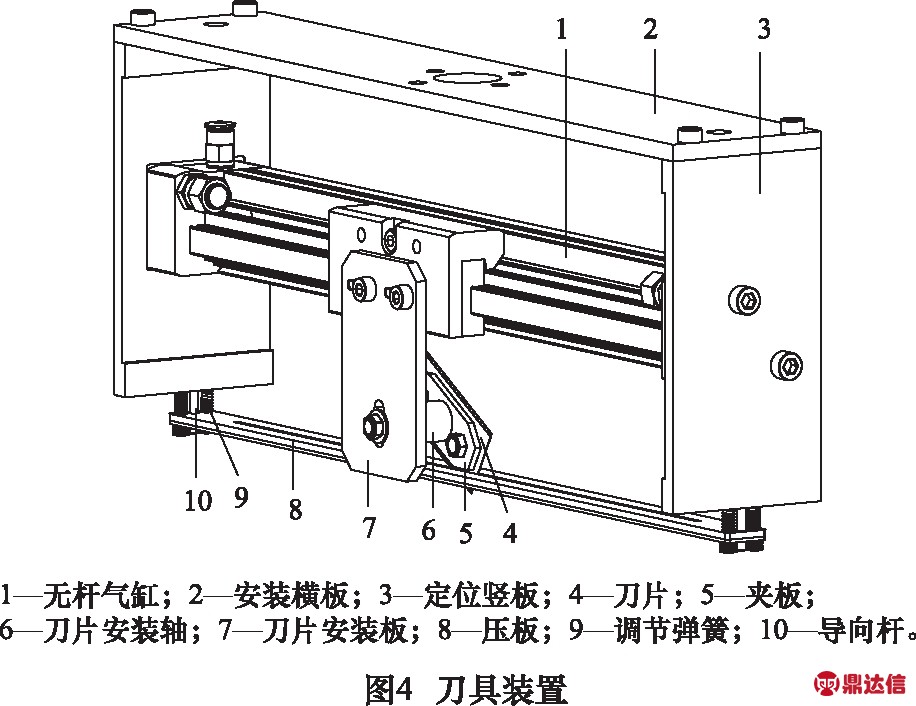
3 控制系统设计
根据电阻应变片的加工技术要求,为了对其修剪质量进行控制与追踪,要求控制系统具有生产数据的记录存储与实时查询功能,单片机和PLC控制系统很难满足这一功能要求[10]。因此,本文采用以工控机+多功能数据采集卡的硬件平台,以LabVIEW为程序开发环境的控制系统方案。整个控制系统主要由上位工控机、多功能数据采集卡、执行元件(伺服驱动器、伺服电动机、气缸、真空吸附台)、控制检测元件(电磁阀、真空阀、光栅尺、限位开关、磁感应开关)以及通讯线缆等组成,其控制系统原理图如图5所示。
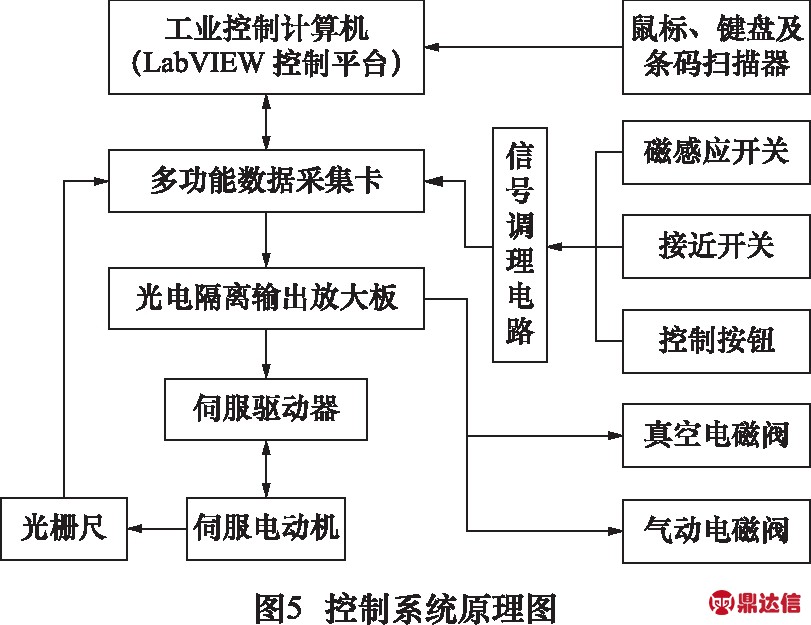
伺服电动机采用位置控制模式,通过控制脉冲的数量、频率和方向信号,来控制伺服电动机的运行状态[11],进而控制伺服滑台在X和Y方向上的位置。控制伺服电动机的脉冲信号需要一定的功率,多功能数据采集卡PCI-6221发出的脉冲信号驱动能力不足,导致信号失真,无法精确控制,因此通过输出放大板对信号进行放大。工控机通过数据采集卡、光电隔离输出放大板、伺服驱动器实现对伺服电动机进行脉冲控制,伺服电机通过驱动滚珠丝杠实现滑台在X和Y方向上的运动,滑台运动位移通过光栅尺传感器实时测量反馈,数据采集卡通过高速计数器端口实时读取光栅尺脉冲信号并传送给工控机[12]。工控机根据位移设定值与实际反馈值之间的偏差调整伺服电机的运行状态,从而形成一个稳定的闭环控制系统。
为了防止伺服滑台越位,在滑台的前后、左右两端安装有电感式接近开关;磁感应开关用于检测无杆气缸和摆动/直线气缸活塞的位置;控制按钮用来实现起动、停止、复位和急停功能;气动电磁阀用于控制气缸的运行状态;真空电磁阀用于控制真空吸附装置真空的产生和断开。开关、按钮及电磁阀属于数字I/O信号,工作电压为DC 24 V,数据采集卡输入/输出电压为DC ±10 V,因此需要信号调理电路和信号放大电路进行调节适配。
自动修剪装置工作时,首先上位工控机发送控制指令到数据采集卡,通过伺服驱动器来控制伺服电动机的运转,通过电磁阀来控制气缸和真空吸附装置实现刀具的动作和膜片的固定,并将滑台移动位置和气缸的状态实时反馈回工控机,最终实现各个执行机构动作的精确匹配,完成膜片的修剪。
4 样机研制及试验
4.1 样机研制
大阵列电阻应变片自动修剪装置主要有机械结构、控制系统及气压系统组成。结构部分主要采用标准件和自行设计加工,人机交互界面及控制程序采用Lab view软件进行设计开发,气压系统的气源采用空压机供给,真空采用真空发生器产生。对整机进行组装、调试,研制的试验样机如图6所示。其主要设计参数为:工作电压AC 220V;工作气压0.7 MPa;外形尺寸:980 mm×550 mm×600 mm;整机重量75 kg。
4.2 试验及数据分析
根据电阻应变片的检测工艺要求,合格的修剪应变片应尺寸外形满足技术要求,剪切面光滑整齐,毛刺高度在许可范围内。因此应变片修剪完成后,要进行尺寸精度检测及老化试验,影响其老化的因素之一是修剪的质量,即切割边沿的毛刺及整齐度。对10张应变片膜片进行切割试验,从2 600个修剪好的应变片中随机抽取100个样品进行检测,外形尺寸使用螺旋测微器进行检测,修剪质量通过读数显微镜进行观察测量,部分试验数据如表2所示。
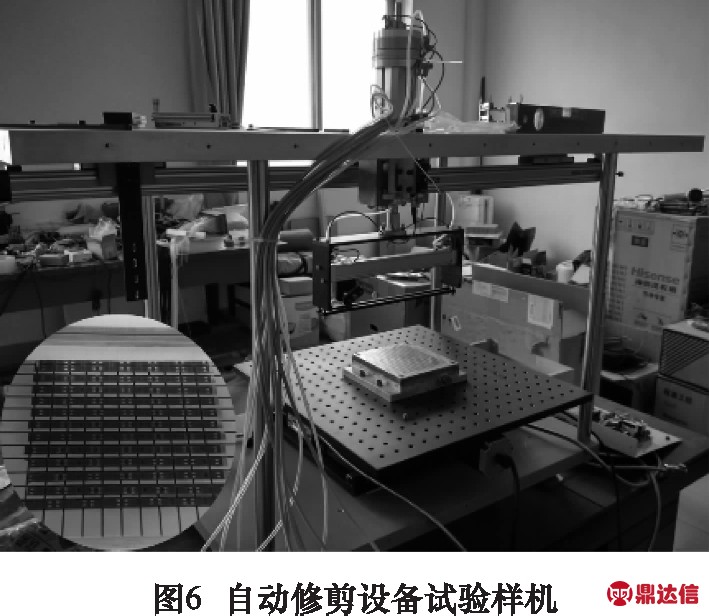
表1 部分应变片的修剪试验数据
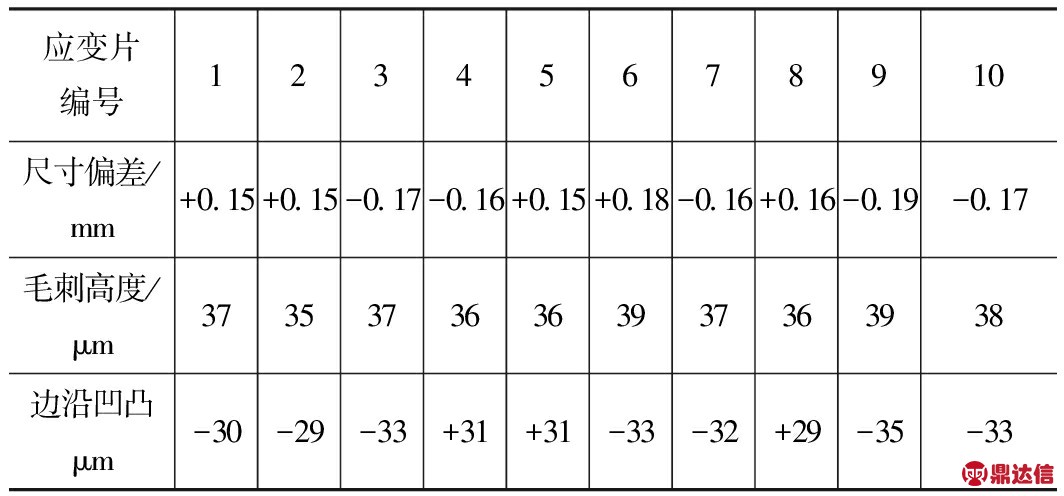
试验数据分析结果表明,修剪的应变片外形尺寸偏差均在技术要求范围内,且偏差平均值为0.16 mm。自动修剪设备主要是由手工装配,有些部件是靠装配人员的经验来完成,每一台设备在装配的过程中都有不可控的机械装配特性和误差[14],影响外形尺寸精度的因素主要有刀片的平行度、垂直度、吸附平台的平整度以及伺服滑台的运动精度等,可以通过控制算法对尺寸偏差进行补偿,以进一步提高修剪精度。
从试验数据分析来看,应变片的修剪质量在可接受范围内,但修剪质量还有进一步提升的空间,影响修剪质量的主要因素有刀片剪切角、剪切速度、走刀槽宽度以及压板的压力等。正交试验设计是一种解决多因素问题的有效方法,相比全面试验,它可以减少试验次数,缩短试验的周期,能获得反映全面情况的实验资料,找出影响因素的最优水平组合[15]。因此可以通过正交试验设计的分析结果,找出剪切角、剪切速度、走刀槽宽度以及压板压力的最优水平组合,从而进一步提高修剪质量。
5 结语
根据某企业大阵列电阻应变片的修剪现状和技术需求,利用机械制造技术、闭环控制技术和气压传动与控制技术设计研发一台应变片自动修剪设备。经过一段时间的运行测试,该设备的各项参数均满足技术要求,性能可靠稳定,操作简单易懂,能有效提高生产效率,降低劳动强度。
目前该设备已投入企业试运行,并且申请了知识产权保护(ZL201511030434.7)。随着工业4.0时代的到来,智能制造技术、机器视觉技术获得了飞速发展,如何将这些新技术新工艺运用到该设备上,进一步提高修剪质量、修剪速度和定位方法,是课题组下一步的研究计划。