摘 要:
在渗透汽化膜组件被密闭于真空罩的设计中,渗透蒸汽中一部分将会在真空罩内表面冷凝,这有利于膜下游的渗透蒸汽分馏和冷凝回收。本文对真空罩内冷凝行为进行了分析,建立了冷凝传热的物理和数学模型,定义了真空罩冷凝效率及其计算公式。进行了渗透汽化+真空罩冷凝的实验,测试结果与理论计算值较为符合。分析了蒸汽温度、真空罩外部空气温度和膜渗透通量等因素对真空罩冷凝效率的影响。研究结果对真空罩渗透汽化膜装置设计和工程化具有参考价值。
关键词:渗透汽化膜装置 真空罩 冷凝传热 自然对流传热 冷凝效率
随着化石能源的日益枯竭,燃料乙醇等来源于可再生资源的生物燃料将成为理想的替代品。生物发酵生产燃料乙醇是目前生物质燃料和原料的重要发展领域之一[1-3]。而提高乙醇产率、降低生产成本、更加节能和环保是发酵工艺中的研究重点。研究表明,采用发酵与膜分离相耦合组成的渗透汽化膜生物反应器发酵乙醇能有效减轻乙醇对微生物细胞生长和发酵过程的抑制并提高发酵强度[4]。
O'Brien等人证明了PDMS膜生物反应器系统在发酵过程的优越性,但也指出了其用于收集膜下游的低浓度乙醇蒸汽的低温制冷设备能源费用高于传统的批发酵[5];Fan Senqing等人改进了渗透汽化分离工艺,采用常温自来水冷凝装置和MVR技术冷凝膜下游的渗透蒸汽,成功地消除了膜下游的高耗能低温强冷装置,实现了PDMS膜生物反应器系统中发酵-渗透汽化操作的连续耦合,提高了系统的发酵性能、能量效率和运行稳定性[6,7]。
本文构建了新的真空罩渗透汽化膜装置并进行实验,发现真空罩可以将膜下游渗透蒸汽部分冷凝下来,这有利于膜下游的渗透蒸汽分馏和冷凝回收。本文对真空罩的冷凝效率进行了理论计算,并与实验结果进行对比分析,为后续膜组件的大型化、工程化设计提供了理论依据。
1 真空罩的传热和冷凝理论分析
真空罩将渗透汽化膜下游的部分蒸汽冷凝下来,这有利于膜下游的渗透蒸汽分馏和冷凝回收,同时也将对膜下游渗透蒸汽分馏和冷凝回收单元的设计产生影响,所以有必要对真空罩的冷凝和传热行为进行分析。

图1 真空罩形状和内部结构
如图1所示,真空罩由不锈钢材质的圆柱形筒体和椭圆形封头组成。物理模型如图2所示,真空罩冷凝蒸汽整个传热过程包含了三个环节,为简化求解,作如下假设:(1)只计算真空罩圆柱形筒体部分的换热,忽略封头部分的换热;(2)气-液表面无温差,界面上液膜温度等于蒸汽饱和温度[8];(3)液膜为浓度低于7%的乙醇水溶液,近似取水的物性。
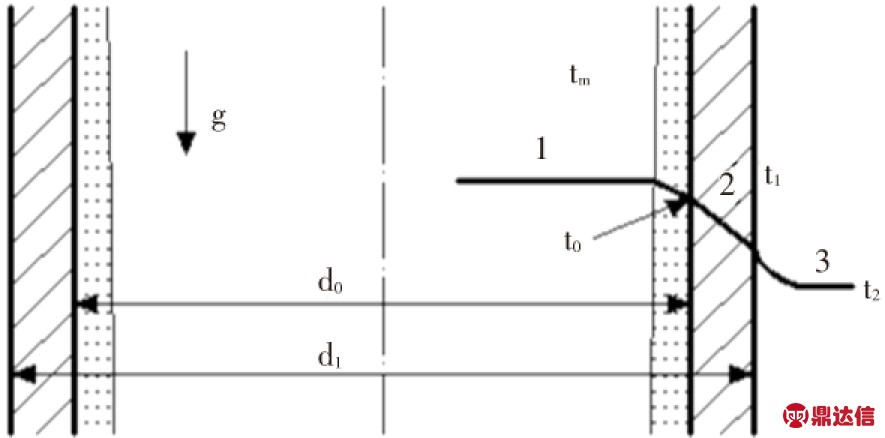
1.冷凝传热;2.热传导;3自然对流传热
图2 真空罩蒸汽冷凝传热物理模型
1.1 真空罩内膜状冷凝
部分渗透蒸汽在真空罩内壁面形成一层凝液薄膜的过程属于膜状冷凝。根据W.Nusselt推导的垂直平面或垂直管上膜状冷凝的冷凝传热系数公式并加以修正得到h0[9]:
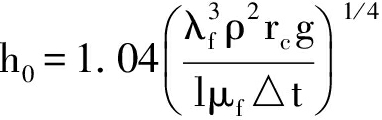
(1)
式中:l为真空罩高度m;λf、ρf、μf分别为膜温tf下凝液的导热系数(W·m-1·℃-1)、密度(kg·m-3)、黏度(Pa·s);rc为冷凝潜热(J·kg-1);△t为饱和蒸汽温度tm与壁面温度t0的差值(℃)。
真空罩内冷凝传热速率Q0为:
Q0=h0A0△t0=h0πd0l(tm-t0)
(2)
外壁面的温度t1为 :
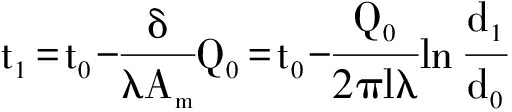
(3)
式中:λ为不锈钢的导热系数(W·m-1,℃-1);Am为真空罩的对数平均传热面积(m2); d1为真空罩外直径(m)。
1.2 真空罩外自然对流传热
真空罩外只依靠外壁面与空气之间温度场的不均匀引起传热,属于自然对流传热[10]。拉格利数Ra为格拉晓夫数Gr和普朗特数Pr之积:

(4)

(5)
式中:t1、t2分别为真空罩外壁面温度和空气的温度(℃)。β为空气体积变化系数;vg为定性温度下空气的运动黏度(m2·s-1)。
真空罩外壁面与空气之间的自然对流传热系数h1和传热速率Q1为:

(6)
Q1=h1A1△t1=h1πd1l(t1-t2)
(7)
式中:b和n根据Ra数查得[11];λg为定性温度下的空气的导热系数(W·m-1·℃-1)。
1.3 真空罩冷凝传热的总传热系数
采用MATLAB软件对方程(2)和(7)进行联立数值迭代方法求解,可以得到真空罩冷凝传热过程的总传热系数U:
U=1/(1/h0+δ/λ+1/h1)
(8)
式中:δ为真空罩壁厚(m),δ=d1-d0。
1.4 真空罩冷凝效率
把真空罩内凝液质量Mv与膜渗透物的质量Mp之比定义为冷凝效率ε:
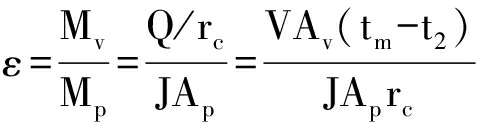
(9)
式中:Mv和Mp分别为真空罩内凝液质量与膜渗透物的质量(g);Av和Ap分别为真空罩表面积与PDMS膜面积(m2);J为PDMS膜的渗透通量(g·m-2·h-1。
2 实验
2.1 实验材料
本实验采用自制的聚二甲基硅氧烷( PDMS)复合平板膜[12,13],膜规格为300mm×300mm,单张有效膜面积为0.08m2,共使用两张膜对称布置。实验对质量分数为5%的乙醇水溶液进行分离。
2.2 实验装置
PDMS膜渗透汽化分离集成系统流程装置如图3;膜组件内部结构如图1,膜器为对称板框式。
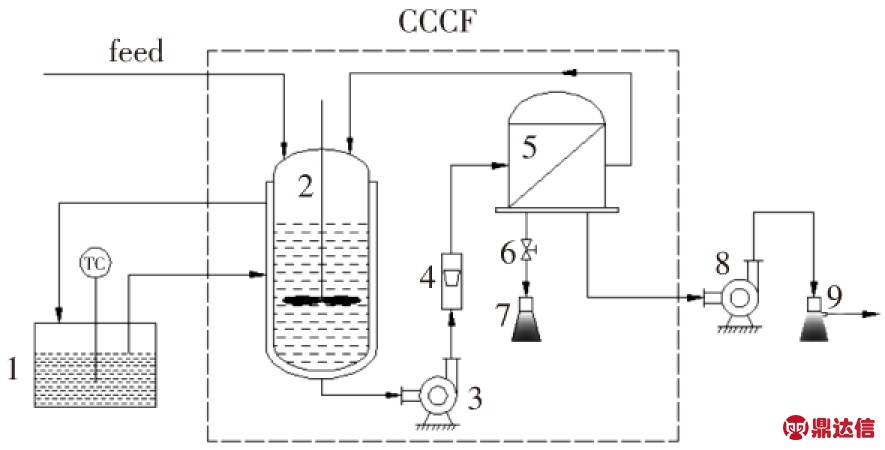
1.超级恒温槽;2.料液罐;3.循环泵;4.流量计;5.膜组件;6.止水夹;7.收集瓶A;8.真空泵;9.收集瓶B
图3 PDMS膜生物反应器集成系统流程
2.3 实验方法
PDMS膜渗透汽化封闭循环系统分离乙醇的流程如图3所示。这个系统与以前所采用的系统[14,15]最主要区别是在膜组件外增加了真空罩(见图1),省去了渗透蒸汽冷凝回收段中常温自来水冷凝器装置。料液由循环泵输送到渗透汽化膜组件内进行乙醇的渗透汽化原位分离。料液在料液罐、循环泵和膜组件之间进行封闭循环,膜下游得到乙醇-水混合蒸汽,部分水蒸气和少部分乙醇蒸汽在真空罩中冷凝并收集于收集瓶7中,剩余部分含高浓度乙醇的蒸汽被真空泵8吸入并压缩输送到大气环境中自然冷凝为液体并收集于收集瓶9中。定时取出收集瓶7和收集瓶9中的冷凝液进行质量测量和酒精浓度测量。试验中随着渗透汽化的进行,需要往料液罐中添加适量乙醇,以维持料液浓度恒定。料液罐有测温口和取样口,料液流量由流量计控制,渗透下游保持绝压7kPa左右。
3 结果与讨论
本文利用修正Nusselt模型对渗透汽化膜装置的真空罩在不同蒸汽温度、不同室温情况下的冷凝传热系数h0、自然对流传热系数h1、总传热系数U、蒸汽理论冷凝质量MV进行了计算,由此可计算理论冷凝效率εV。通过渗透汽化+真空罩冷凝实验,可以得到实验冷凝效率εV。
3.1 真空罩理论传热速率影响因素
影响真空罩理论传热速率的因素有蒸汽与空气的温差、真空罩的材质等。由于真空罩的材质是不锈钢,导热系数随温度的变化不大,可以忽略,所以主要影响因素为蒸汽与空气的温差。本研究计算了温差△t=12~32℃时真空罩的冷凝传热性能相关参数。
如图4所示,真空罩的总传热系数U和自然对流传热系数h1都随温差增大而增大,冷凝传热系数U随着温差增大而减小。同时,总传热系数U与自然对流传热系数h1成正相关变化,与冷凝传热系数h0成负相关变化。由于空气的传热性能远小于液体,因此影响真空罩传热性能的因素中,自然对流传热占主导作用。所以实际操作中,在蒸汽温度一定的情况下,可以通过降低空气的温度增大温差、加快空气流动等方式增强对流传热。
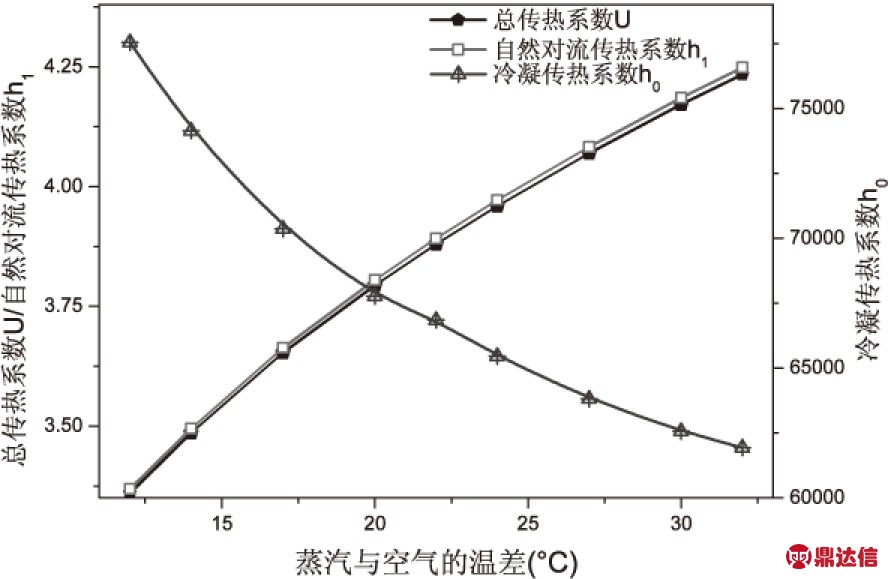
图4 真空罩的总传热系数、自然对流传热系数和冷凝传热系数与温差的关系
3.2 真空罩冷凝效率的影响因素
影响真空罩冷凝效率的因素较多,但主要影响因素有蒸汽温度、空气温度、膜渗透通量等。
3.2.1 蒸汽温度的影响
如图5所示,当蒸汽温度tm≤40℃时,真空罩的理论冷凝效率εV随tm的增大而逐渐减小,实验冷凝效率εV随tm的增大而逐渐增大;当tm>40℃时,εV和趋于平稳;εV和
的平均差值为14.95%。这在一定程度上反映了理论计算与实验的对比误差。
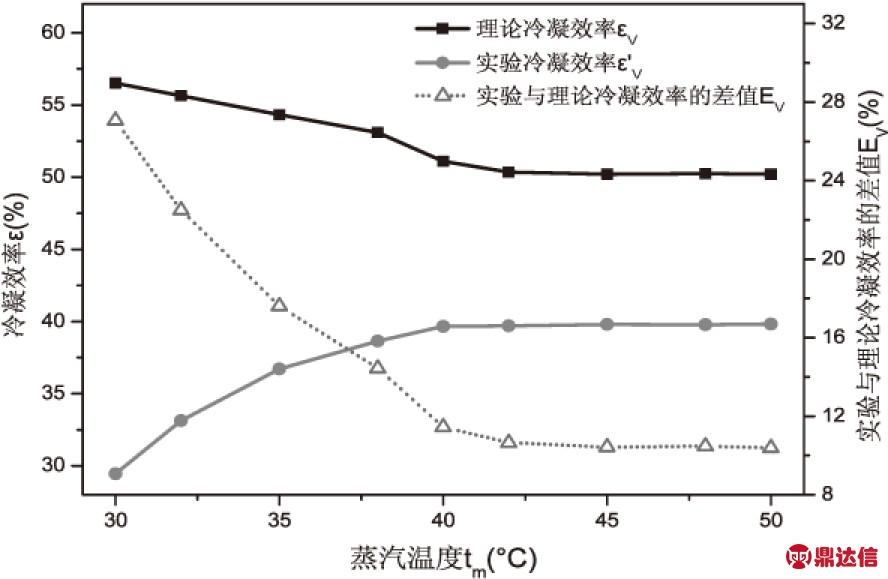
图5 蒸汽温度对真空罩冷凝效率的影响
3.2.2 空气温度的影响
如图6所示,真空罩的理论冷凝效率εV和实验冷凝效率都随空气温度t2的增大而逐渐减小,εV和
的平均差值为14.85%。其主要原因是当蒸汽温度(40℃)、渗透通量(1000g·m-2·h-1)不变时,膜的渗透物质量Mp基本不变,空气温度升高,液膜温差以及蒸汽和空气的温差减小,而气化潜热不变,则总传热量减小,凝液量减小。
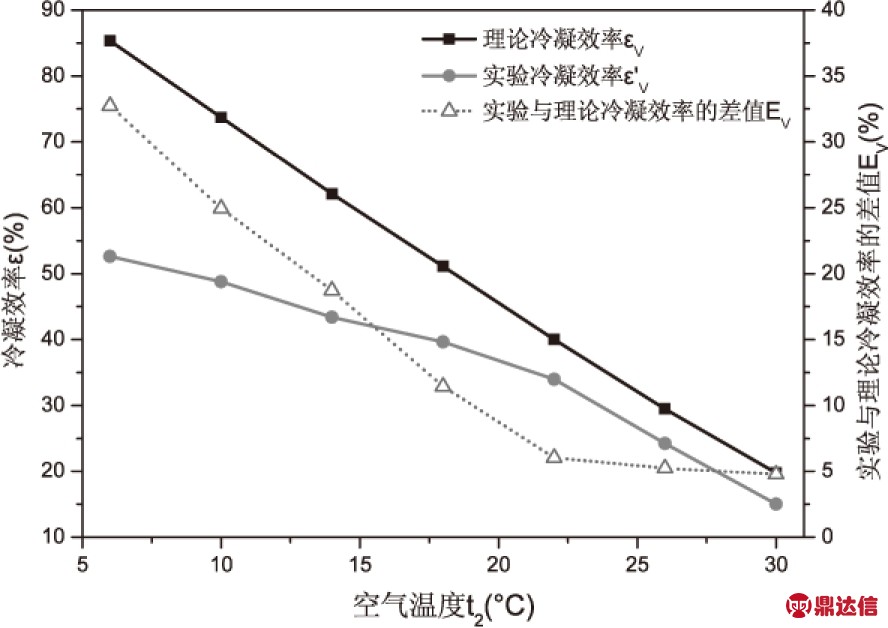
图6 空气温度对真空罩冷凝效率的影响
3.2.3 膜渗透通量的影响
如图7所示,真空罩理论冷凝效率εV随膜渗透通量J增大而减小。这是由于当空气温度和蒸汽温度不变时,真空罩理论冷凝量MV是一个定值,随着J的增大,膜渗透物质量Mp不断增大,所以εV不断减小。实验冷凝效率随J的增大而逐渐增大。εV和
的平均差值为56.84%。
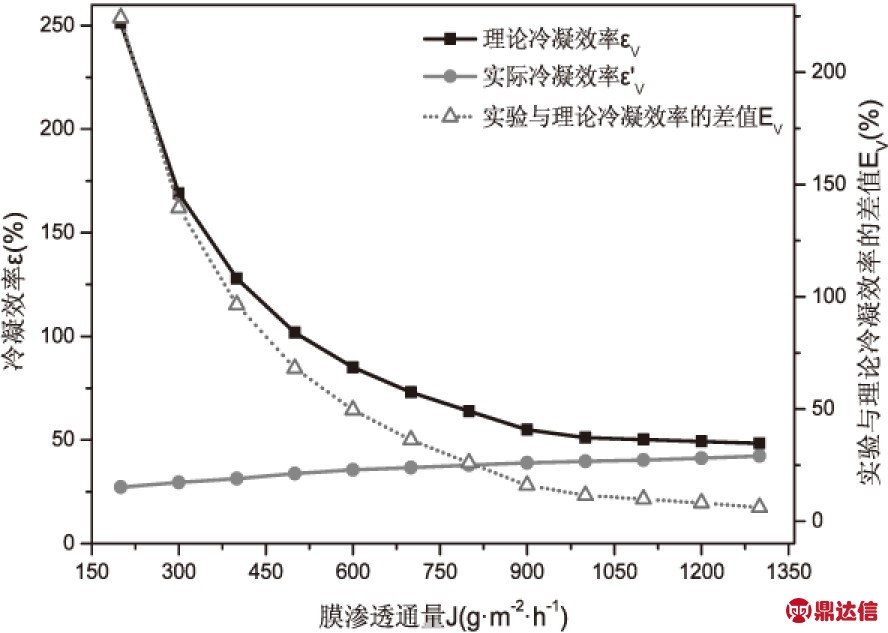
图7 膜渗透通量对真空罩冷凝效率的影响
4 结论
(1)根据经典Nusselt模型计算出的真空罩冷凝传热特性分布规律与实验结果比较吻合,表明数学模型选择是恰当的。
(2)基于冷凝和传热分析,定义了真空罩的冷凝效率,分析了蒸汽温度、空气温度和膜渗透通量等对真空罩冷凝效率的影响,对理论和实验冷凝效率进行了对比讨论。这对CCCF工艺生物质发酵生产燃料乙醇的渗透汽化膜分离装置设计等具有一定的参考价值。