摘 要:材料表面渗金属技术是一种有效的表面强化技术。介绍了离子渗金属、固体渗金属、液体渗金属、气体渗金属等技术的工作原理及研究进展,对比分析了各种技术的优缺点,并探讨了表面渗金属技术未来的发展趋势。
关 键 词:表面渗金属;表面强化;合金层;渗入元素
汽车、航天、航海等领域技术的迅速发展,对齿轮[1]、轴[2]等零部件的要求越来越严格。为满足使用要求,采用表面强化手段以提高零部件表面硬度、改善耐磨性是有效的途径[3]。渗金属技术就是表面强化手段之一,与其他表面强化手段相比,该技术具有简单易行、操作方便,能渗入高熔点金属元素(如Ni、Cr、Mo、Ta、Ti等),渗层与基体结合牢靠等优点,因此,可以使普通碳素钢的表层具有某种特殊钢的成分与性能,从而替代部分昂贵材料[4]。
1 材料表面渗金属技术
表面渗金属技术是在一定温度和真空条件下,利用渗入金属原子在工件表面的吸附、扩散,形成含有渗入金属元素的合金层,以此来改变材料表面的组织、成分及性能[5]。
根据渗入元素的形态不同,表面渗金属技术可分为离子渗金属、固体渗金属、液体渗金属、气体渗金属等[3,5],如图1所示。这些方法中,有些已投入工业应用,节约了经济成本,减少了能源损失。
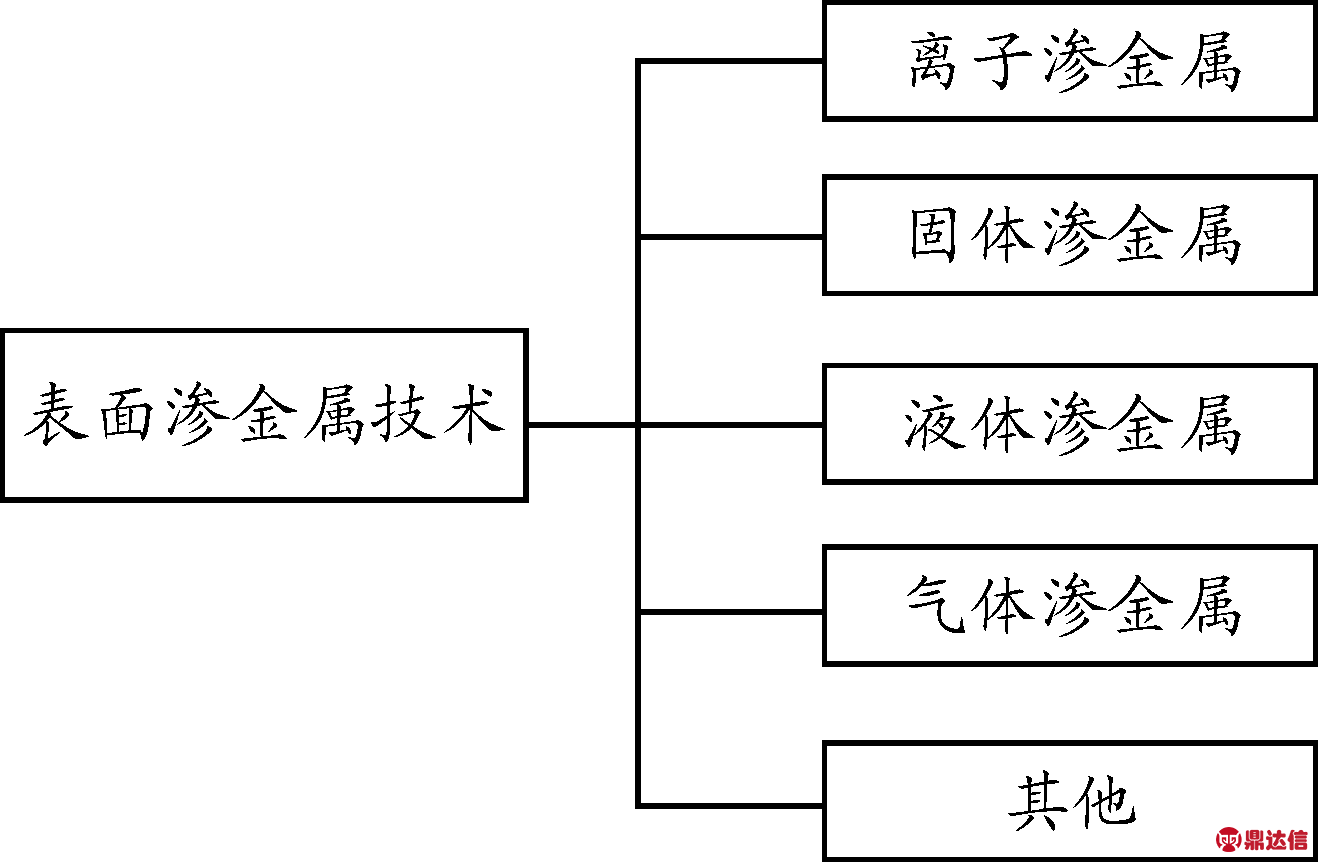
图1 表面渗金属技术分类
1.1 离子渗金属
离子渗金属技术是通过辉光放电等方法使欲渗金属粒子或离子溅射出来,并在高温条件下扩散进入工件表面,从而形成合金层的方法。目前,该技术主要有离子溅射渗金属、双层辉光离子渗金属、离子轰击膏剂渗金属、交变电场真空离子渗金属、脉冲辉光放电渗金属、气相辉光离子渗金属、多弧离子渗金属等方法[6]。本文主要介绍前3种离子渗金属方法。
1.1.1 离子溅射渗金属
离子溅射渗金属是依靠高速、高能量的等离子体轰击靶材从而得到渗入金属原子,其原理如图2所示。设备的真空室内设置有阴极和阳极,将金属靶材(即欲渗金属)置于真空室中的阴极处,并将绝缘后的工件放在靶材附近。当真空室的真空度达到使用要求后,调节电源电压,在阳极和阴极之间、金属靶材之间都会出现辉光放电现象。随即通入氨气,此时会在金属靶材之间形成大量的等离子体。等离子体在电场的加速下,具有足够的动能轰击靶材,轰击后的金属靶材溅射出许多原子,这些原子扩散进入工件,形成含有靶材元素的合金层。
该方法可以通过改变工作温度、工作电压、保温时间等参数,控制合金层厚度以及合金元素成分的含量。与直接轰击工件的渗金属方法相比,这种方法可以防止渗入工件的金属元素重新被溅射出来,提高了沉积速率,同时,工件不直接与电源相连,可减少粒子对工件的轰击。
王艳[7]利用该方法在纯铜表面渗镍(Ni),研究了工艺参数对合金层厚度和成分的影响。通过实验发现,镍原子是由基体表面不断向内部进行扩散的,且随着温度的升高,镍的含量不断提高,渗层也在不断变厚。
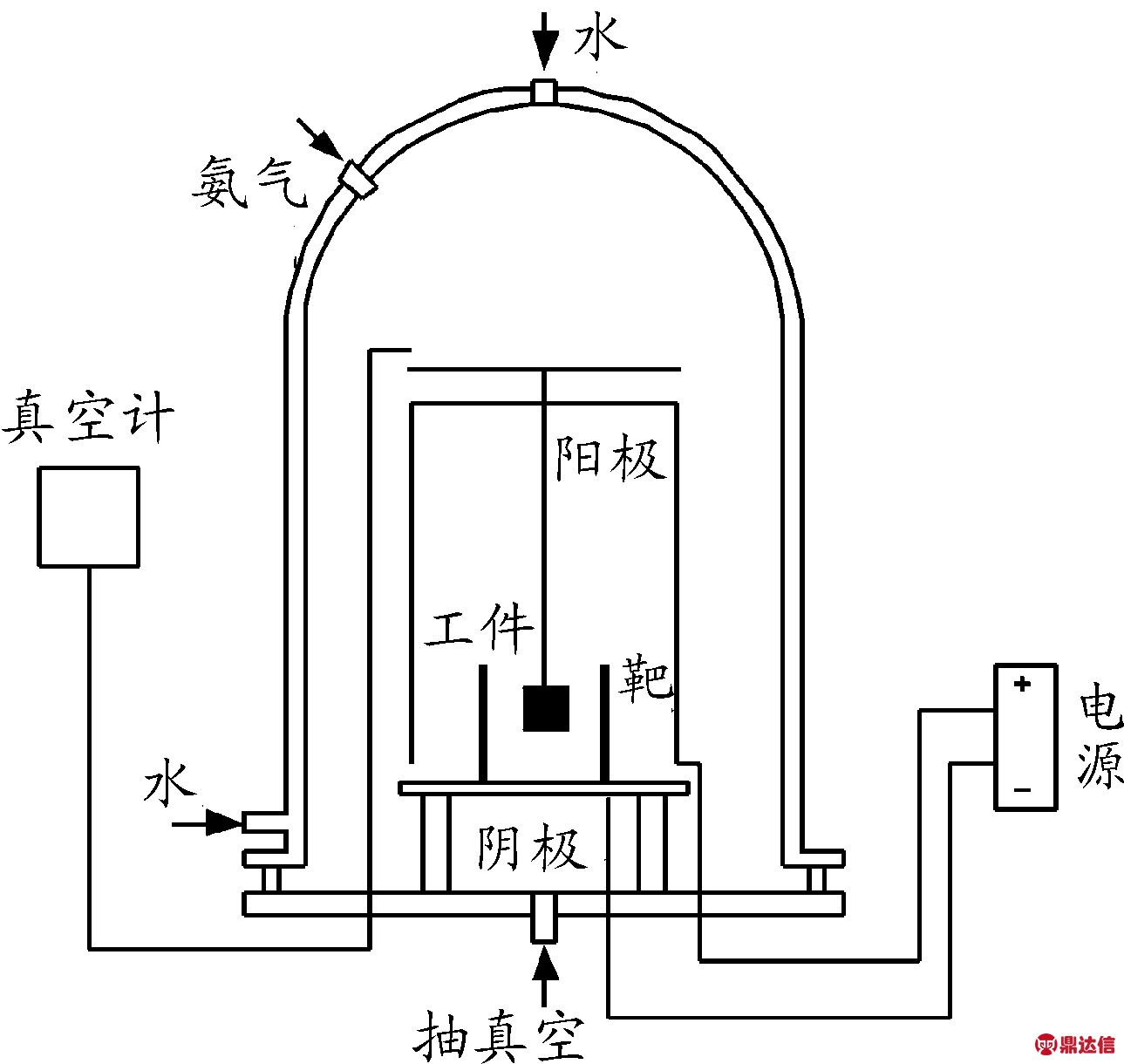
图2 离子溅射渗金属原理图
1.1.2 双层辉光离子渗金属
双层辉光离子渗金属是在离子氮化技术的基础上发展起来的[8],其原理如图3所示。真空罩内设置有阳极、阴极和源极,在阳极与阴极、阳极与源极之间各设有一个可调直流电源。将工件置于阴极处,当真空腔内抽真空至一定压强后通入少量惰性气体(一般采用氩气),接通两个直流电源并调节电压,此时会在阳极与阴极,以及阳极与源极处分别出现辉光放电现象,产生大量的离子。离子轰击源极溅射出的金属元素快速飞向工件,同时辉光放电产生的电能转化为热能,迅速使工件表面的温度上升至高温,溅射出来的离子被工件高温的表面吸附,扩散渗进工件表面,从而形成合金层[6,9]。
这种方法也可以通过调整工作温度、电位、保温时间等工艺参数,控制合金层的厚度以及合金元素成分的含量。利用该方法制备的涂层,可以与基体形成冶金结合,因此结合性能良好。同时,涂层与基体能够进行充分扩散,不易形成硬脆相,因此涂层表面致密。
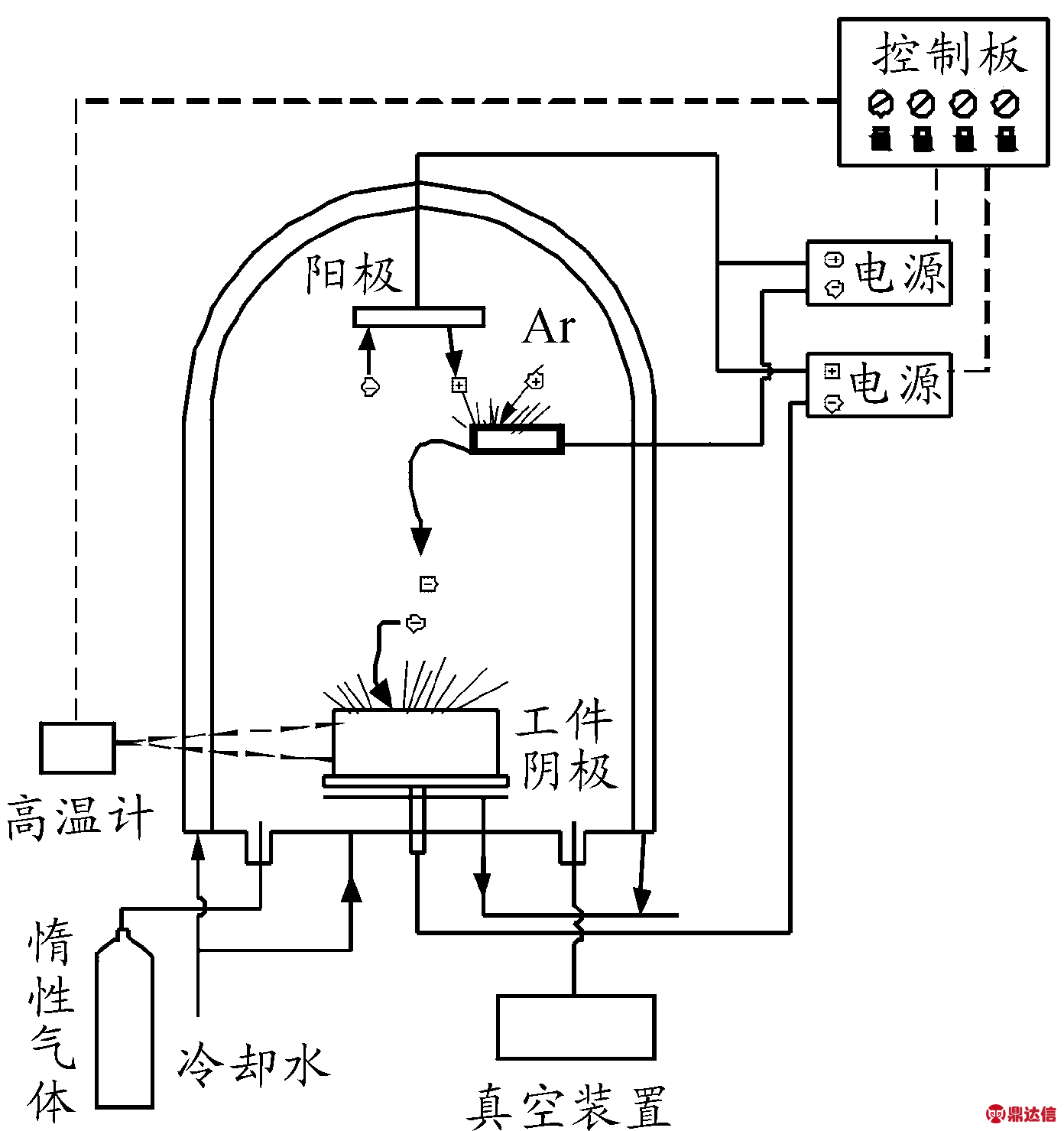
图3 双层辉光离子渗金属技术原理图
许多研究人员利用该方法在金属表面上进行了单元渗的工艺研究。例如,李转利等[10]采用该方法在316L不锈钢表面进行了渗铝处理,研究了工艺条件对渗铝层厚度和渗层表面铝含量的影响。通过实验发现:渗入时间3 h,316 L不锈钢表面铝涂层的厚度约为31.7 μm,渗层主要由FeAl3、FeAl和Fe2Al5三种相组成。高强等[11]采用该方法在316L不锈钢的表面渗入Cr元素,实验结果表明:在316 L不锈钢表面制备的Cr层厚度可达到21 μm,涂层表面的Cr含量为92%,主要由Cr层和Cr在α-Fe中的固溶体相组成。
双层辉光离子渗金属不仅能应用于单元渗金属,还能对合金元素进行二元及多元渗,如Cr-Ni共渗、Cr-Ni-Mo共渗、Cr-Ni-W-Mo共渗等。例如,朱晓林等[12]采用该方法在Q235钢表面制备Cr-Ni合金层,探究了Cr-Ni合金层对基体腐蚀性能的影响。通过实验发现:所形成的Cr-Ni合金层均匀致密,与基体材料相比,腐蚀性能明显改善。贺志勇等[13]利用该方法在铸铁表面进行Cr-Ni-Mo共渗后,材料表面性能得以强化,耐磨性得到明显改善,耐蚀性增强。
1.1.3 离子轰击膏剂渗金属
离子轰击膏剂渗金属的原理是预先在工件表面涂覆一层含有欲渗金属的膏剂(渗剂),然后将工件放入离子渗碳炉中,利用辉光放电产生的离子对工件的轰击作用使欲渗元素扩散进入工件表面,并发生一系列的物理、化学反应,从而形成合金渗层。该方法不仅工艺简单,而且渗速快、渗层均匀、无污染[14]。与前两种方法相比,这种方法的最大特点是设备成本低,不需要额外电源或金属靶材,即使对于形状复杂的工件,也只需将膏剂均匀涂覆在工件表面,就可获得均匀的合金渗层。
贺志勇等[15]利用该方法在20钢和45钢表面渗铝,研究了渗入铝元素后材料表面抗氧化性的变化情况。结果发现:在600 ℃和800 ℃的工作温度下渗铝后,试样的抗氧化性提高了约2~3倍。
1.2 固体渗金属
固体渗金属技术主要是采用金属粉末或者膏剂形成涂层,因此也称为固体粉末/膏剂渗金属。该技术是将工件表面预先涂覆粉末或膏剂(渗剂),然后放在某种介质(如坩埚等)中加热。当达到一定温度后,粉末或膏剂中的元素就会渗入工件表面,与工件内的元素形成合金渗层。这种技术的最大优点是环境污染小,且结合强度高,但是,其工艺时间过长,温度高,容易引起工件心部的组织过热而造成使用性能降低,同时,密封问题是关键,若对加热容器密封不好,容易产生腔内外的气体对流,引起渗剂与工件发生氧化反应。
曾潮流等[16]采用该技术在Ni3Al试样表面渗入Cr和Al元素,探究了渗入元素对试样的高温热腐蚀性能的影响。实验表明,渗入的Cr、Al元素在基体表面形成了CrO3、Al2O3氧化物,对基体起到了保护的作用,从而改善了Ni3Al的耐蚀性能。赵晓博[17]利用该技术在20钢和45钢表面渗入Cr元素,研究了工艺参数对合金层厚度和质量的影响。实验发现,在580~650 ℃下保温3~5 h可获得2~8 μm的渗Cr层,且渗层致密均匀。Qiao等[18] 利用该技术在镍基合金表面共渗Co-Al元素,形成了Al2O3薄膜。通过实验发现:Al2O3薄膜能有效防止表面氧化,从而使工件具有良好的抗氧化性。Pang等[19]在镍基海绵表面渗Ce-Cr/Al元素,旨在形成Ce-Cr中间层和氧化铝外层。实验结果表明:Ce-Cr/Al双层涂层的抗氧化性优于Ce-Cr涂层和Cr/Al涂层。
1.3 液体渗金属
液体渗金属技术形成涂层的整个过程都是在熔融盐浴中进行,因此也称为熔盐渗金属。该技术最早是由日本丰田研究所提出,他们认为,采用盐浴的方法可以在材料表面形成金属的碳化物涂层。在加热过程中,悬浮着的金属原子与工件表面产生一系列物理、化学反应,从而形成渗层。在工作过程中,熔盐不断产生对流,使得金属原子在工件表面各处分布均匀,从而使工件表面的渗层均匀性较好。
这种技术的基本原理如图4所示,合金渗层的形成大致分为3个过程:分解、吸附、扩散。首先,盐浴中发生化学反应分解成活性金属原子;然后,活性金属原子吸附在材料表面上,并与材料表面的碳原子形成金属碳化物;最后,金属原子与碳原子相互扩散,致使合金渗层不断增厚。在反应初期,金属原子吸附在工件表面并融入奥氏体中,从而减少了碳在奥氏体中的浓度,多余的碳原子从奥氏体中析出并与工件表面的活性金属原子发生反应。随着金属碳化物的不断生成,工件表面的碳原子和活性金属原子的浓度不断减少,于是,在工件的表层与基体之间形成了碳原子和金属原子的浓度梯度,引起了碳原子和金属原子从高浓度向低浓度的不断扩散,使得表面的碳原子不断增多,继续生成金属碳化物。最后,反应生成的金属碳化物晶粒相互接触,形成连续而致密的薄层。
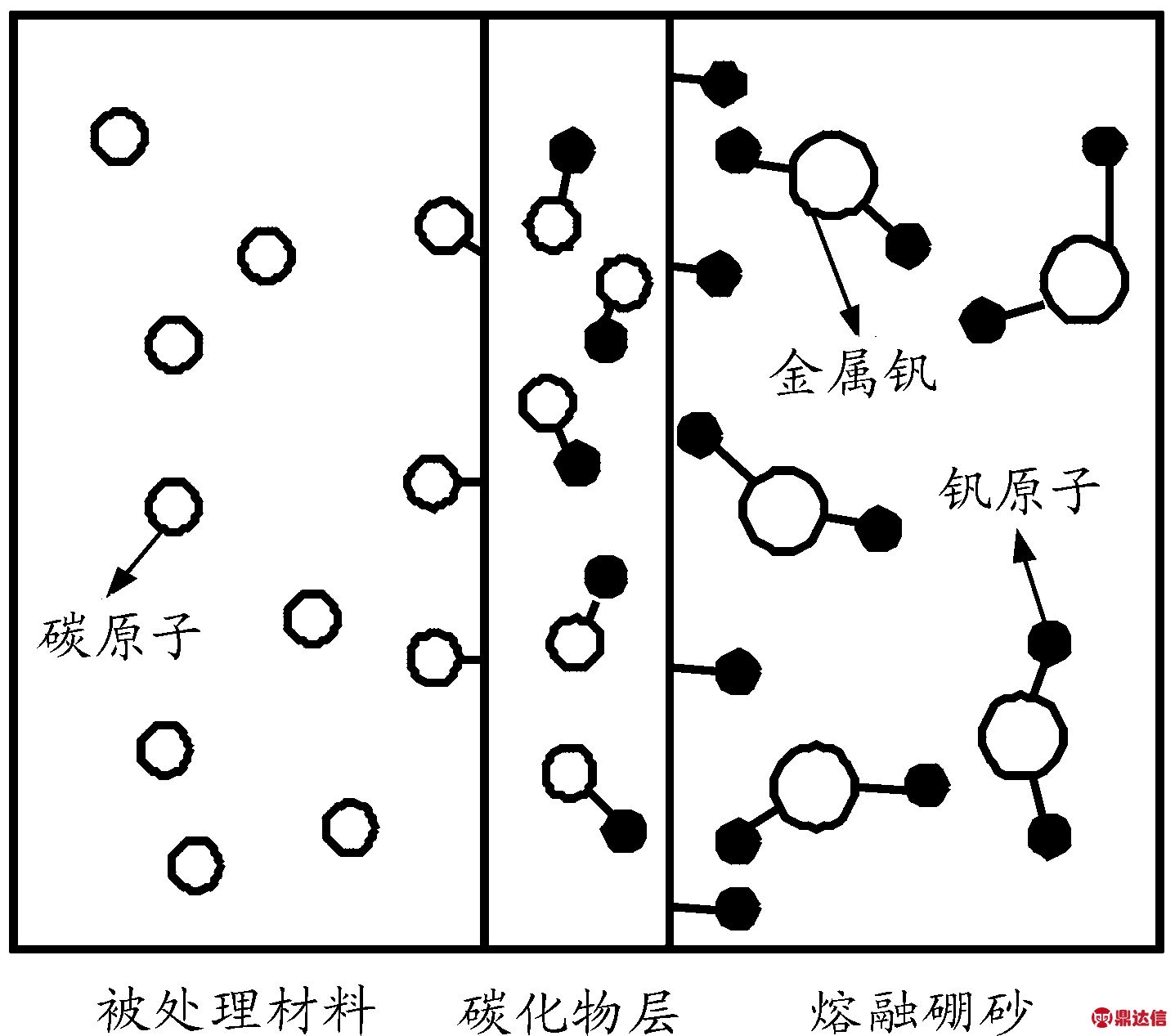
图4 熔盐渗金属技术原理图
该技术的主要特点是:操作简单;对工件表面具有清洁作用,可去除氧化膜;温度要求低,工件变形小;在复杂的工件上也能获得均匀致密的涂层。目前,这种技术主要应用于模具,但是,熔盐中的残盐难以清洗等问题限制了其应用。
程立本[20]采用该技术对GCr15进行渗铬处理,分析研究了渗铬工艺对渗层的影响。通过实验发现:在850 ℃时渗铬,可得到较厚的碳化物涂层,涂层硬度也较高。张坤等[21]研究了纯铝和纯镁的液相浸渗过程,发现由于浸渗的不均匀使得液态的金属氧化。
1.4 气体渗金属
气体渗金属技术可分为直接气体渗金属、间接气体渗金属和气固快速渗金属等。
1.4.1 直/间接气体渗金属
直接气体渗金属是把工件与欲渗金属元素的卤化物直接放置在渗炉中,同时将其加热到高温,使金属元素扩散进入工件表面,形成合金层。间接气体渗金属法是将欲渗金属通过某种介质扩散至工件表面。在高温环境下,置于炉中的金属卤化物,无论是固体还是液体均会变成气体,气体分解成的活性原子扩散至工件表面,从而形成一层金属间化合物层,赋予工件表面某种特殊的优良性能。
1.4.2 气固快速渗金属
气固快速渗金属是前苏联研究人员研究开发的,包括感应加热渗金属和电接触加热渗金属,二者的区别在于加热方式不同。与固体渗金属技术相比,该技术的优势在于金属元素扩渗速度快,渗层形成时间短。例如,电接触加热温度到1 180 ℃,保温2 min,即可在45钢表面形成50 μm的铬层[22]。而感应加热渗金属是将欲渗金属涂敷在工件表面上,再利用感应圈进行感应加热,使欲渗金属与工件表层发生反应以形成合金层。
于进文等[23]利用高频感应加热渗金属方法在Ti6Al4V合金表面渗入铬,研究了渗层的显微组织及摩擦性能。通过实验发现:渗入的Cr层与基体形成了冶金结合,化学成分呈现梯度变化,且硬度与摩擦性能明显提高。高原等[24]利用感应加热渗金属在正火态的20钢和45钢表面渗入Mo、Al等元素,探究了工艺参数度渗层的影响。实验结果表明:加热速度越快,保温时间越长,形成的合金层越厚。
1.5 其他
除了上述表面渗金属技术外,铸渗技术同样可以在工件表面形成合金层。该技术是将铸造技术和冶金强化技术结合起来,利用铸造工艺凝固时产生的余热将欲渗金属熔化、分解、扩散至铸件表面,从而形成具有特殊性能的合金层[25]。利用这种技术形成的渗层主要由两部分组成:一是浇注的液体金属元素,二是欲渗金属元素。浇注的液体金属浸入渗剂中,使其部分熔化而产生化学反应,形成以渗剂元素为主的合金包容层。与此同时,凝固的余热使欲渗元素发生分解反应,产生大量的活性原子扩散至铸件表面,形成以铸件元素为主的合金扩散层。铸渗法主要适用于不经加工和热处理的铸件。
金属铸渗技术可依据预置渗剂方式和渗入渗剂的驱动力进行分类。例如,根据预置渗剂方式不同,可分为普通砂型铸渗和干砂消失模铸渗[26-30]。其中,普通砂型铸渗主要是将欲渗金属涂覆在型腔表面需强化的部位,待铸型干燥后浇注,在铸件冷却凝固后就会在铸件表面形成合金铸层;干砂消失模铸渗是将可发性聚苯乙烯(EPS)预先涂覆在型腔表面,再将欲渗元素粉末粘附在其表面,在浇注过程中,EPS遇高温分解气化并逸出,导致欲渗元素粉末与型腔表面之间产生空隙,而高温金属液在毛细管力作用下渗入空隙,从而形成了具有特殊性能的合金层。根据渗入渗剂的驱动力不同,可分为普通铸渗、压力铸渗、离心铸渗和负压铸渗[31]。
金属铸渗技术的主要优点是工艺和设备简单、生产周期短、成本低、工件不变形,且能够制备较大厚度的复合材料。但同时也存在一些问题,如铸渗合金层质量不高,易产生气孔等缺陷;铸渗层质量对工艺参数要求较高,主要受渗剂与液体金属之间的浸湿性和浇注温度的影响,需严格控制工艺参数等。
2 结束语
表面渗金属技术是一种有效的表面强化技术,不仅技术工艺简单、成本低,而且,通过合理选择渗入金属元素,可以获得性能优良的表面合金化层,这有利于延长工件使用寿命,降低材料成本。但是,就目前的研究现状而言,值得研究人员深入探讨的是适合我国国情的既实用又经济的表面渗金属技术。此外,针对渗金属工艺普遍存在的耗时较长等问题,如何通过对渗金属工艺、催渗剂的深入研究以缩短生产周期、提高生产效率,都需要深入地研究。