摘要:低温胶粘剂在航空航天、低温超导以及民用工业等领域有着广泛的应用。低温条件下,由于胶粘剂冷收缩产生应力以及胶粘剂与被粘材料之间的线胀系数存在差异等因素,胶粘区域可能出现微裂纹等破坏现象。为了检测胶粘剂在深低温下的密封性能,研制了一个低温漏率检测系统。低温冷源采用小型制冷机,最低制冷温度10 K。漏率检测采用氦质谱检漏仪,极限检测漏率为5.0×10-11 Pa·m3/s。
关键词:胶粘剂;低温;泄漏率
低温胶粘剂是指在深低温条件下具有足够粘接强度的胶粘剂。随着航天技术与超导技术的不断发展,低温胶粘剂的应用越来越广泛,目前在液氮温区、液氢温区甚至液氦温区都有一定的应用。比如为了降低发射成本,对于液氢、液氧等低温推进剂的储箱,目前现代航天器广泛使用复合材料替代金属材料来减轻重量,其中低温胶粘剂的性能对于复合材料低温储箱性能有非常重要的影响[1~3]。另外,在液氦温区超导磁体中,磁体线圈中的层间绝缘、匝间绝缘以及对地绝缘中都存在着粘接结构[4~6]。当然,低温胶粘剂在民用工业中也有广泛的应用,如低温生物容器、非金属无磁杜瓦以及作为电缆的灌封槽等材料中都有应用[7,8]。
在低温环境下,由于胶粘剂冷收缩产生应力以及胶粘剂与被粘材料之间的线胀系数有差异等原因,胶粘连接处可能会发生破坏现象。例如,1996年,美国洛克希德马丁公司提出的“冒险星”(Adventure Star)计划,开始研制一个复合材料液氢储箱项目,希望采用质量更轻的复合材料来降低发射成本,但由于树脂与纤维的线胀系数相差较大,在降到液氢温度后热应力剧增,导致树脂基体产生微裂纹,项目最终失败。由此可见,室温下的性能标准是不能用来预测其低温性能[4,5]。
基于此,本文研制了一个低温胶粘剂漏率测试系统,能够测试胶粘部件连接处在任意设定温度以及不同升降温速率条件下的漏率,对于低温胶粘剂的研制以及性能改良具有一定的指导意义。
1 测试原理
目前,在众多的检漏方法中,充气法与氦质谱仪检漏是最常用的2种方法。充气法是指在待测系统内充入一定的气体,一段时间以后观察气体的压力有无降低。充气法原理简单易懂,但是通常需要一定的时间来观察,尤其在漏率较小的情况下,需要较长的时间才能得到检测结果,比较耗时。本文采用的是氦质谱仪检漏法,是根据质谱学原理制成的磁偏转型质谱分析计,通过测量收集到的氦离子流来测算漏率,具有检测快速可靠、精度高等特点[9]。
氦质谱检漏仪有“正压检漏”与“负压检漏”2种模式。正压检漏模式下,在待测系统内充入一定的氦气,通过质谱仪探测待测系统外氦气的浓度来确定漏率。在负压模式下,将待测系统与质谱仪连接构成封闭空间,通过在待测系统外喷吹氦气,检测待测系统内氦气的浓度来确定漏率。本文研制的低温胶粘剂漏率测试系统中主要采用正压法进行检测。
为了获得深低温环境,目前主要使用液氮、液氦等低温液体以及使用制冷机2种方法。使用液氮液氦等低温液体具有降温迅速的特点,但需要借助低温杜瓦、低温输液管道等设备,操作上存在不便,某些场合液氮液氦的供给也存在一定的困难;另外,控温难也是使用低温液体的不足。本文使用自主研制的脉冲管制冷机作为测试系统的低温冷源,相对于目前市场上的商用制冷机,脉冲管制冷机具有降温迅速(约30 min降到20 K以下)、体积小质量轻(整机16 kg,商用制冷机一般130 kg左右)、振动小(线性压缩机驱动且冷头无运动部件)以及功耗低(输入电功300 W以内,商用制冷机一般在6 000~8 000 W)等特点 [10~17]。
研制的低温胶粘剂漏率检测系统主要包括氦质谱检漏仪、低温制冷机和样品3大部分,其系统结构原理示意图见图1,图2是实物照片。检测方法为正压法,将一端封闭的中空管内充入氦气后用待测胶粘剂将其密封住,然后将此管子与低温制冷机冷头连接后开始降温,通过氦质谱检漏仪探测管子胶粘连接处外部的氦气浓度来确定漏率。
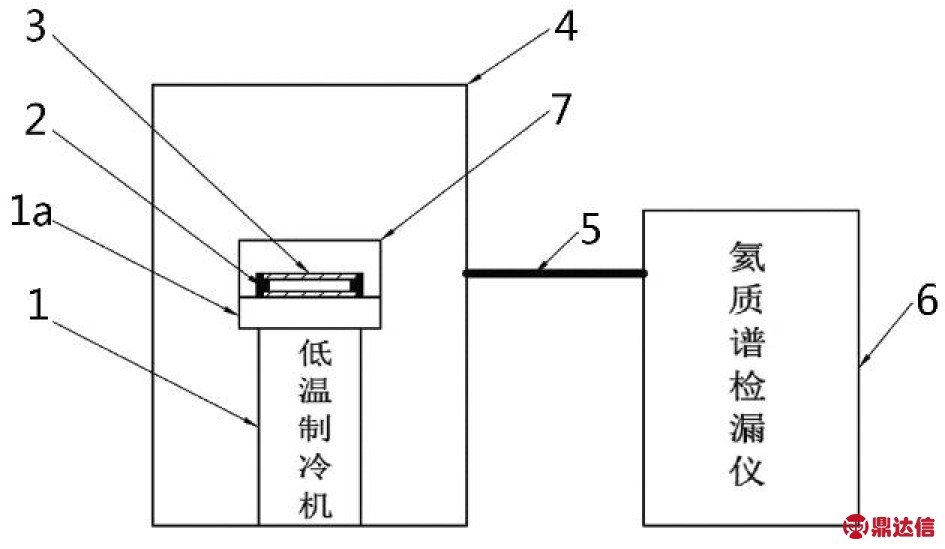
图1 低温胶粘剂漏率测试系统结构示意图
Fig.1 Schematic of developed leak rate measurement apparatus for cryogenic adhesive
(1.低温制冷机;1a.低温制冷机冷头;2.待测胶粘部分;3.充有氦气的待测管;4.真空罩;5.真空连管;6.氦质谱检漏仪;7.热辐射罩)
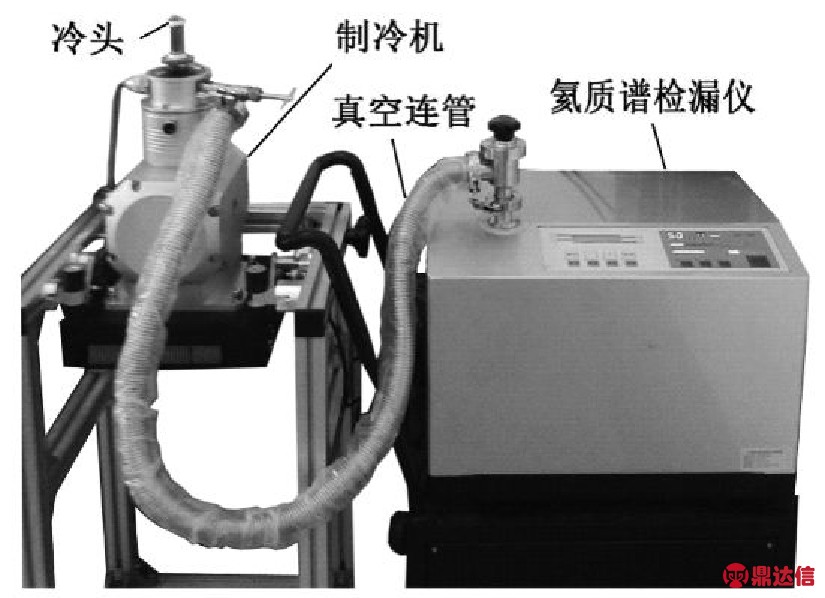
图2 低温胶粘剂漏率测试系统实物照片
Fig.2 Photograph of developed leak rate measurement apparatus for cryogenic adhesive
2 实验过程与结果讨论
检测开始时,需要将充有氦气的待测管固定在低温制冷机的冷头上,并盖上热辐射罩(热辐射罩的主要用途是保证待测管温度能够与冷头保持一致,同时,为了保证氦质谱检漏仪能够检测出从待测管上胶粘剂连接处泄漏的氦气,热辐射罩上留有一定数量的小孔)。氦质谱检漏仪通过真空连管与制冷机的真空罩连通,当开始检测时,氦质谱检漏仪将充有氦气的待测管外部的所有空间进行抽真空,此时只要待测胶粘处氦气有漏,氦质谱检漏仪就能够及时快速的测出漏率。当氦质谱检漏仪启动以后就可以启动低温制冷机进行降温,观察氦质谱检漏仪上漏率随低温制冷机温度的变化。制冷机可以根据实际需要进行设定温度、升降温速率等操作。
图3是样品的具体安装过程示意图。首先根据胶粘剂的特性选择相对应材料的待测管,然后将待测管的一端封闭,封闭的方法可以采用焊接或者使用已经检测过不漏的胶粘剂进行密封等方法。在一端封闭以后,保持待测管的封闭端竖直朝上、开口端竖直朝下,将充气接头对准待测管的开口端,挤压氦气袋将氦气充入待测管内后快速将开口端用待测胶粘剂密封上,然后进行固化待测。充氦气过程中要保证待测管的封闭端竖直朝上、开口端竖直朝下的原因是氦气密度较低,能够自动往上方飘动。
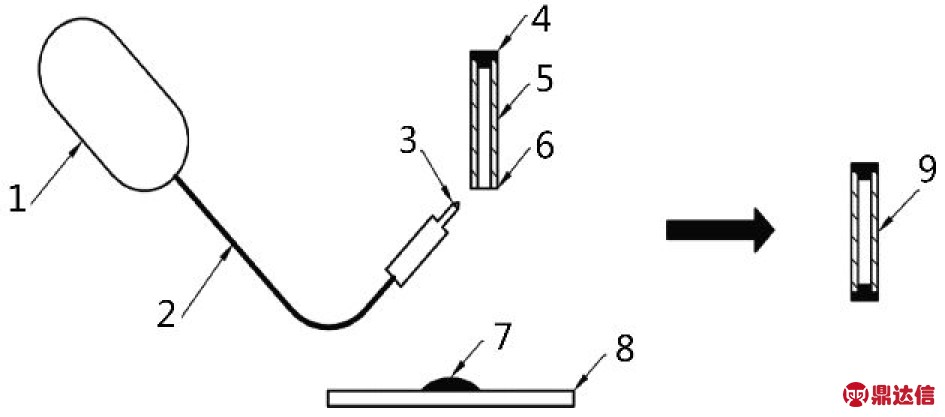
图3 样品安装示意图
Fig.3 Assembly procedure for sample
(1.氦气袋;2.充气管;3.充气接头;4.被粘管封闭端;5.被粘管;6.被粘管开口端;7.胶粘剂;8.底板;9.充有氦气的待测管)
在实际检测过程中发现,有时由于在待测管充入氦气后没有立即使用待测胶粘剂进行密封,充入待测管的氦气由于分子的自由扩散运动而从待测管中漏走,从而造成在升降温过程中漏率一直保持在某个很低的数值上不动,造成不漏的假象。为了确保待测管内充有氦气,对于经过检测后漏率数值不动的样品,需要待其回到室温后从制冷机内取出,再次进行检测。检测方法如图4所示,将氦质谱检漏仪的探测头对准胶粘部分,用尖嘴钳或者剪刀等工具将胶粘连接部分去除,此时,若氦质谱检漏仪检测到的漏率发生明显的变化,则说明待测管内确实充有氦气。
在低温胶粘剂漏率测试系统搭建好以后,对若干样品进行了检测。
图5是1#和2#样品的泄漏率随制冷温度变化的曲线,可以看到,随着制冷温度的不断降低,1#样品的漏率一直保持在5.0×10-11Pa·m3/s不变,但此时不能轻易得到此样品在低温下不漏的结论,因为此时存在着氦气没有成功充入待测管或者氦气充入以后在进行低温测试前的室温条件下就已经漏完的可能性。因此,待此样品回复到室温以后,仍需按照图4所示再次进行检验校核。对于1#样品,按图4进行检验时发现,当夹破胶粘连接部分以后,氦质谱检漏仪的漏率读数瞬间增大到了10-5 Pa·m3/s,由此可以断定1#样品在深低温条件下确实是不漏的。
对于2#样品,在制冷温度降低到140 K之前,样品的漏率也一直保持在5.0×10-11Pa·m3/s不变,但到了140 K以后,漏率开始骤然上升,并在131 K时增大到最大值7.0×10-7 Pa·m3/s,然后开始迅速降低,并在124 K重新回复到5.0×10-11 Pa·m3/s后保持不变。显然,可以得出2#样品的胶粘部分在降温到140 K以后出现了漏气现象的结论。在131 K增大到最大值后开始迅速降低的原因是充入到待测管内的氦气已经全部漏完。
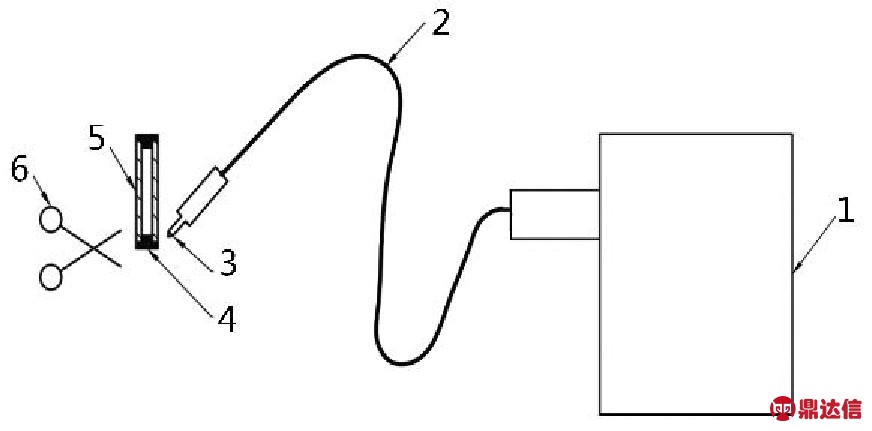
图4 待测管内是否充有氦气测试原理示意图
Fig.4 Schematic for testing helium in measured tube (1.氦质谱检漏仪;2.连接管道;3.氦质谱检漏仪探测头;
4.待测胶粘部分;5.充有氦气的待测管;6.钳子)
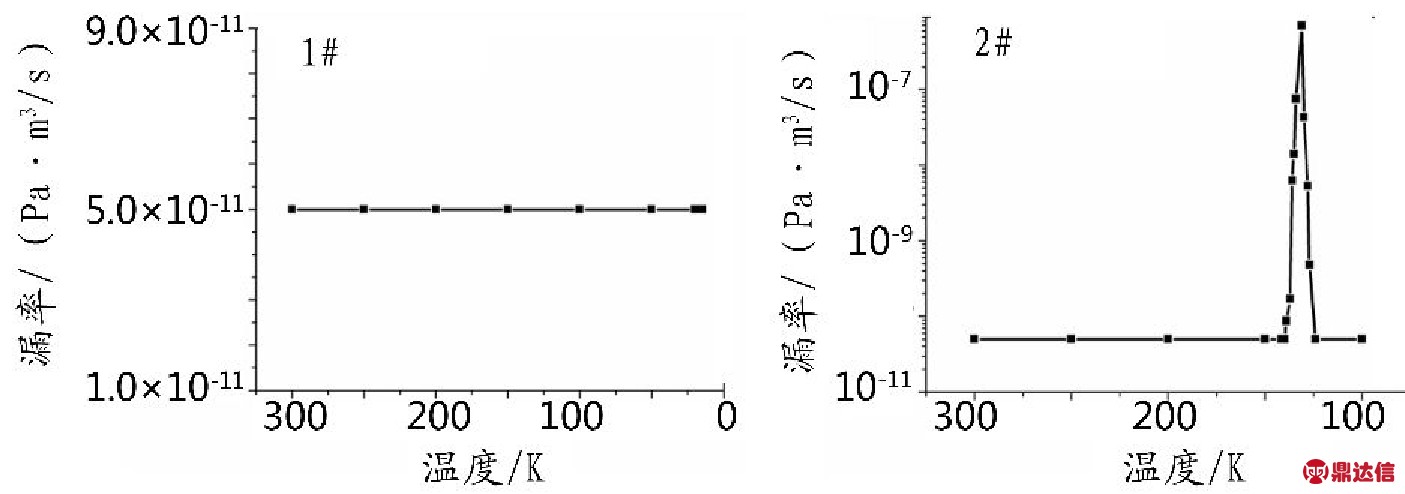
图5 1#样品漏率随制冷温度的变化
Fig.5 Dependence of sample leak rate on cooling temperature
3 结论
在深低温条件下,由于胶粘剂冷收缩产生应力以及胶粘剂与被粘材料之间的线胀系数差异等原因,胶粘连接部分可能会发生破坏现象。为了检测胶粘剂在深低温下的密封性能,研制了一个低温漏率检测系统。低温冷源采用小型制冷机,最低制冷温度能够达到10 K,并可以根据需求对制冷温度、升降温速率等参数进行设定。漏率检测采用氦质谱检漏仪,能够检测的极限漏率为5.0×10-11Pa·m3/s。