摘要:混凝土的孔隙率越低,其强度越高。混凝土中的孔通常来自于搅拌引气和水的蒸发两个方面。现行各种提高混凝土强度的措施都不能完全消除搅拌引{气带来的孔隙。提出真空搅拌混凝土技术,并通过试验验证了该技术的作用效果。当水泥浆、纤维素醚改性水泥浆和超高性能混凝土三种水泥基材料搅拌时的真空度从0降低到-0.096 MPa时,它们的流动度都减小,表观密度和抗压强度都增加,其中水泥浆的抗压强度增加9.6%,纤维素醚改性水泥浆的抗压强度增加85%,超高性能混凝土的抗压强度增加30.8%。相对于常规搅拌,在接近绝对真空(真空度为-0.096 MPa)条件下搅拌,超高性能混凝土在700~1100 nm处的孔数量峰值消失,在7~11 nm处的孔数量峰值大幅降低。真空搅拌工艺可以成为提高水泥基材料强度和调控水泥基材料孔结构的一种新技术。
关键词:真空搅拌混凝土; 水泥基材料; 超高性能混凝土; 物理力学性能; 孔径分布
1 引 言
混凝土的孔结构对其强度、体积稳定性和耐久性具有重要影响。通常情况下,混凝土的孔隙率越低,其强度越高。混凝土中的孔通常来自于两个方面:(1)搅拌引气。新拌混凝土在机械搅拌过程中与空气接触,在混凝土内形成气泡,混凝土硬化后,未破坏的气泡便在混凝土中形成孔隙;(2)水的蒸发。未参与水泥水化的水不断蒸发,会在混凝土中形成孔隙。减水剂技术的不断发展和广泛应用,可以大幅降低混凝土的用水量,减少混凝土因水分蒸发而形成的孔隙,从而提高混凝土的强度。目前,通过高效减水剂技术的应用,混凝土的水胶比已经可以降低到0.15以下,强度已经可以提高到200 MPa以上,甚至更高[1-2]。然而,减水剂的应用只能减少混凝土因水分蒸发形成的孔隙,却不能减少混凝土因搅拌引气形成的孔隙。而且,减水剂的表面活性会使混凝土更容易引气[3]。其它提高混凝土强度的技术,如无宏观缺陷水泥(MDF)[4]和均布超细粒致密体(DSP)[5],这些技术都不能消除搅拌引气给混凝土带来的孔隙。
除了减水剂之外,混凝土中使用的其它有机外加剂很多就是表面活性剂,容易导致混凝土在搅拌成型过程中形成气泡。增稠剂(或增粘剂)还会增加混凝土中液相的粘度,进一步导致混凝土在搅拌成型过程中形成气泡[6]。
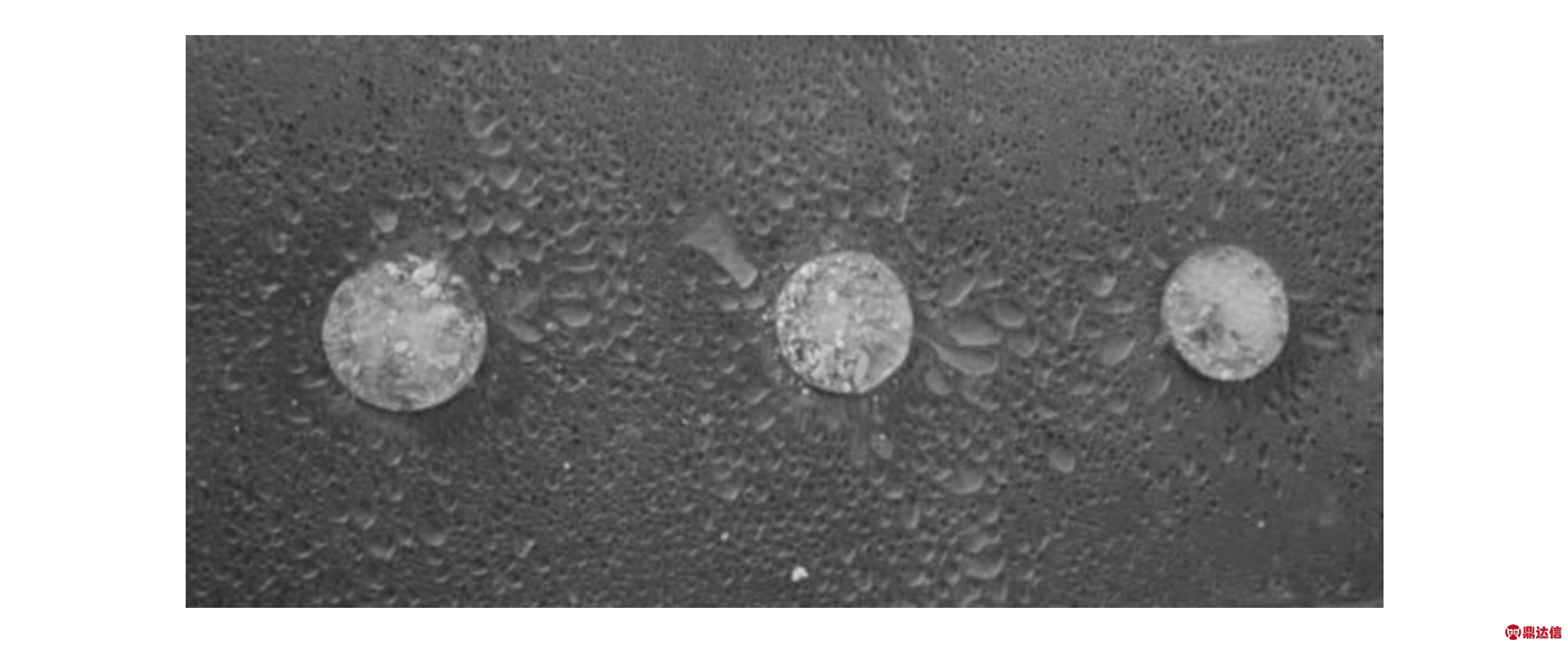
图1 混凝土的表面气泡图
Fig.1 Surface bubble of concrete
在混凝土中使用消泡剂,虽然可以消除混凝土中部分引入的气泡,尤其是较大孔径的气泡,却不能完全消除混凝土中的气泡,还可能导致大量气泡上浮到混凝土表面(图1),影响混凝土的匀质性。
本文提出的“真空搅拌水泥基材料”是指将水泥基材料的所有组成原料放入到搅拌筒中,密封搅拌筒,使用真空泵将搅拌筒抽成不同真空度的真空,然后开启搅拌机,在真空环境下搅拌至规定时间后,再慢慢开启进气阀门,恢复搅拌筒内气压至常压,打开密封的搅拌筒,将水泥基材料浇注成型为试块或者构件。
“真空搅拌水泥基材料”包含了“真空搅拌混凝土”(vacuum mixing concrete,VMC)和“真空搅拌砂浆”(vacuum mixing mortar,VMM)等概念。
本文所提出的“真空搅拌混凝土”不同于“真空脱水混凝土”(或“真空吸水混凝土”),“真空脱水混凝土”是指混凝土在常规条件下搅拌完成之后,在振捣过但未初凝的混凝土表面铺设真空吸水垫将其封闭,开动真空泵使真空吸水垫的真空腔内形成真空,把混凝土内多余的水吸出,并压缩混凝土,提高混凝土密实度和强度等性能[7-9],有时也称“真空混凝土”[10]。显然,“真空吸水混凝土”不能消除混凝土在搅拌过程中因为引气而形成的孔隙,而是相当于降低了混凝土的水胶比,减少了混凝土中因水的蒸发而形成的孔隙,其降低混凝土孔隙率的机理完全不同于本文所提出的“真空搅拌混凝土”。
作为真空搅拌水泥基材料的探索性研究,本文比较普通水泥浆、纤维素醚改性水泥浆和超高性能混凝土(UHPC)三种水泥基材料在不同真空度条件下搅拌成型后,它们在物理力学性能方面的差异以及UHPC在常规条件下和接近完全真空状态下孔径分布的差异。选择纤维素醚改性水泥浆作为研究对象之一,是因为纤维素醚的表面活性效果和增粘作用容易导致混凝土引气[6]。
2 实 验
2.1 原材料
(1)水泥,湖南恒宇建材有限公司生产的普通硅酸盐水泥,规格为P·O 42.5(GB 175-2007);
(2)纤维素醚(CE),赫克力士-天普化工有限公司生产羟丙基甲基纤维素醚,型号为C9115型;
(3)硅灰,挪威埃肯公司提供;
(4)石英砂,湖南大明工业砂采选有限公司生产,40~70目;
(5)减水剂,西卡(中国)公司提供的3301MH型聚羧酸减水剂,含固量40%;
(6)水,自来水。
2.2 实验配合比
实验配合比和水泥基材料搅拌时的真空条件如表1所示。N1~N5均为配合比相同的水泥浆,水灰比都是0.3,真空度分别是0、-0.026 MPa、-0.051 MPa、-0.076 MPa和-0.096 MPa;N6~N10均为配合比相同的纤维素醚改性水泥浆,水灰比都是0.3,纤维素醚质量都是水泥质量的0.4%,真空度分别是0、-0.026 MPa、-0.051 MPa、-0.076 MPa和-0.096 MPa;N11~N15均为配合比相同的超高性能混凝土,其中减水剂的质量是指含固量为40%的减水剂的质量,水胶比都是0.17,真空度分别是0、-0.026 MPa、-0.051 MPa、-0.076 MPa和-0.096 MPa。最低真空度取-0.096 MPa而不是-0.101 MPa,是因为此时水的沸点是32.9 ℃,正常搅拌情况下,水泥基材料中的水分不会蒸发。
表1 实验配合比和真空条件
Tab.1 Experimental mix proportion and vacuum conditions
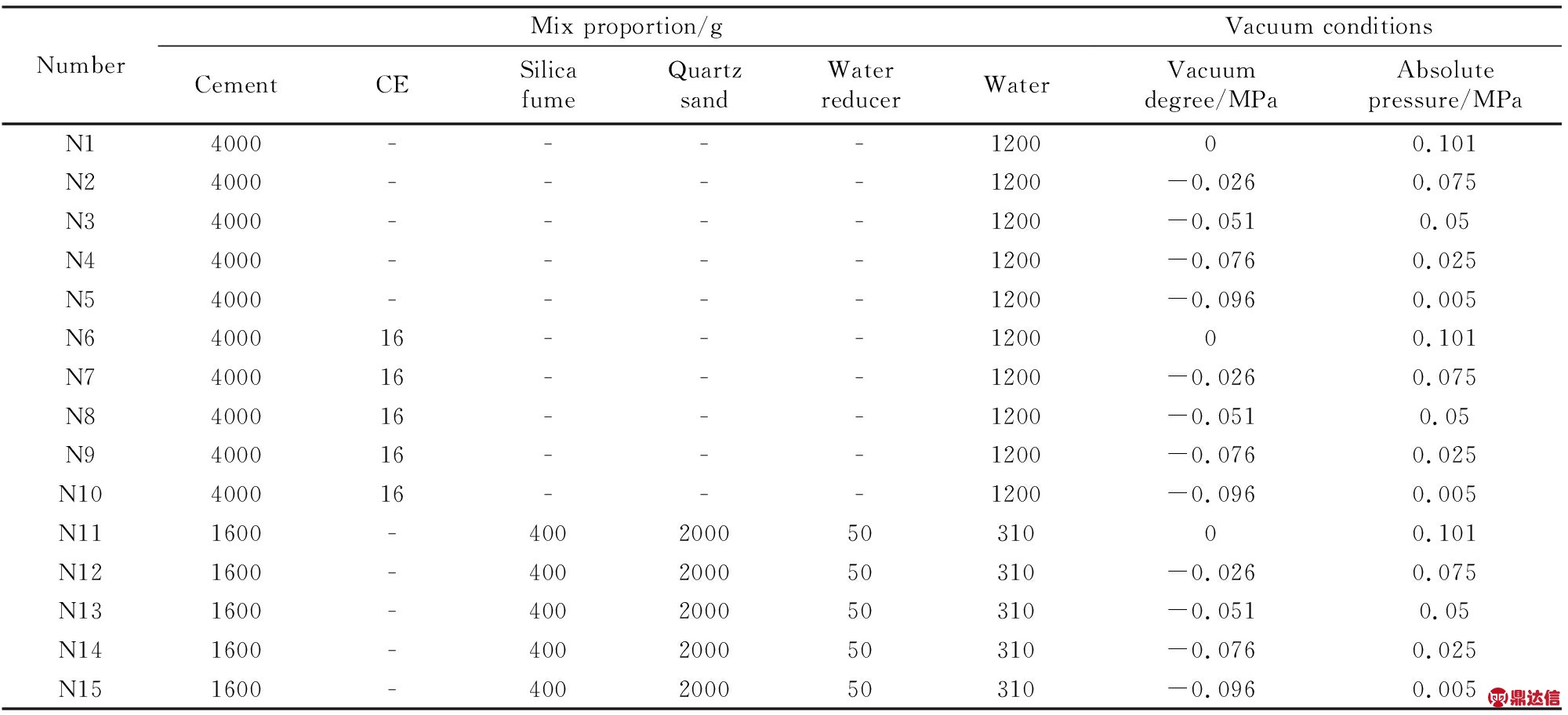
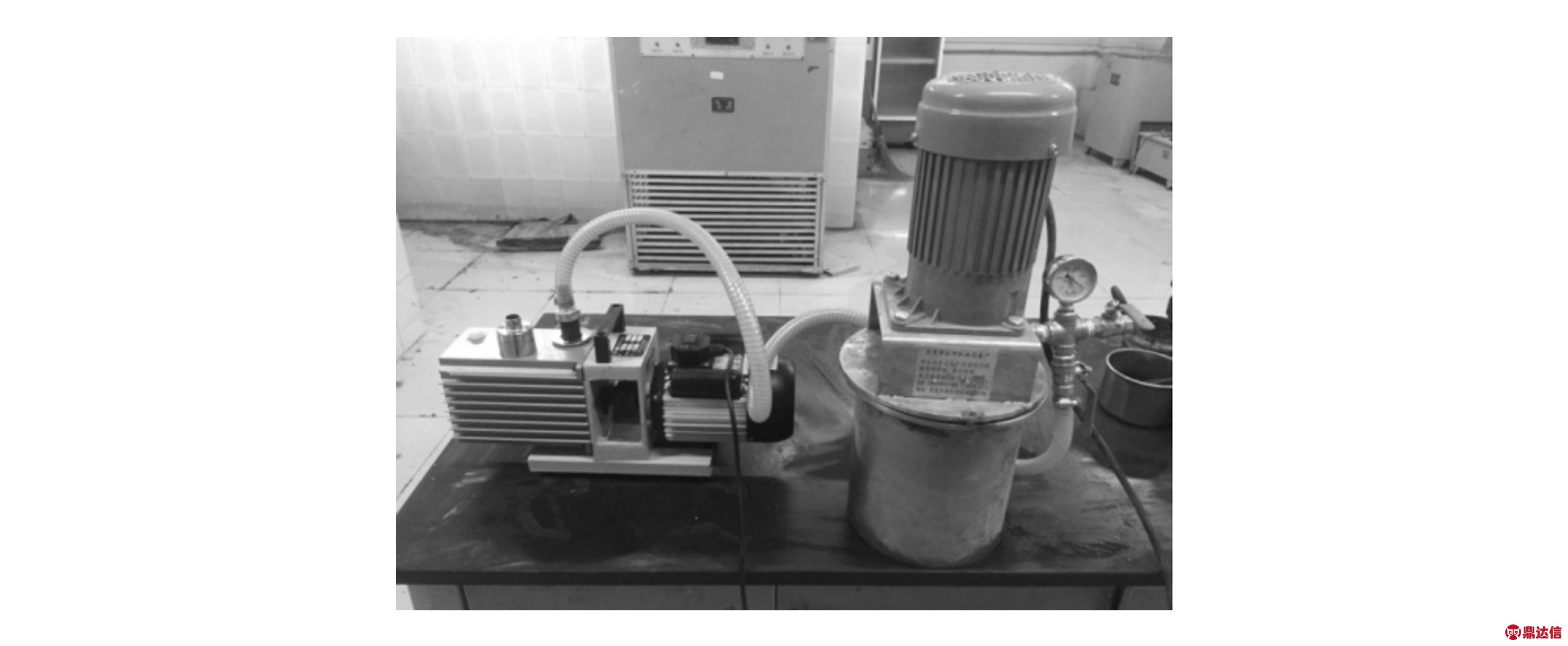
图2 小型混凝土真空搅拌机
Fig.2 Small concrete vacuum mixer
2.3 实验方法
(1)小型混凝土真空搅拌机。如图2所示,自制,组成部分包括真空泵、搅拌筒和电机三个部分,真空泵的抽气速度为4 L/s,电机的功率为1800 W,转速200 r/min,搅拌筒的体积为10 L,可用搅拌筒密封,搅拌筒盖与电机固定在一起。
(2)水泥基材料的搅拌工艺。将所有干粉按比例称量好,在塑料封口袋中混合均匀。在搅拌筒中倒入规定质量的水,再将粉料缓慢加入到搅拌筒中,密封搅拌筒,关闭进气阀门,启动真空泵,将搅拌筒内气压抽至规定的真空度,停止真空泵,启动电机,搅拌水泥基材料,搅拌过程中观察真空表的变化,要随时停止或启动真空泵,使搅拌筒内气压保持在规定的真空度,偏差不得超过±0.002 MPa。水泥基材料搅拌三分钟后,停止电机,慢慢开启进气阀门,恢复搅拌筒内气压至常压。
(3)流动度测试方法。按照《水泥胶砂流动度测定方法》(GB/T 2419-2005)测定。
(4)抗压强度实验方法。将搅拌好的水泥基材料按照《水泥胶砂强度检验方法(ISO法)》(GB/T 17671-1999)规定的方法成型40 mm×40 mm×160 mm棱柱体试块,在温度(20±3) ℃,相对湿度≥95%的环境中养护1 d后脱模,再继续养护至28 d龄期后,将试块折断,测试抗压强度。
(5)硬化水泥基材料的表观密度测量。将养护28 d后的棱柱体试块表面用拧干的湿抹布抹干,用天平称取质量,除以试块的体积(256 cm3),即得到硬化水泥浆的表观密度。
(6)压汞测孔法。本实验测试了UHPC的孔径分布,将UHPC制成40 mm×40 mm×160 mm的棱柱体试块,在温度(20±3) ℃,相对湿度≥95%的环境中养护1 d后脱模,再继续养护至28 d龄期后,用锤子轻轻敲碎试块,从中部取出2.5~3.0 mm试样,在真空干燥箱中在干燥48 h(60 ℃),采用美国MICROMERITICS仪器公司生产的AutoPore IV 9500型全自动压汞仪进行测试,测试汞压力范围为0.10~60000.00 psia(即689.5 Pa~413.7 MPa),测试的孔径范围为3.0 nm~300 μm。
3 结果与讨论
3.1 流动度
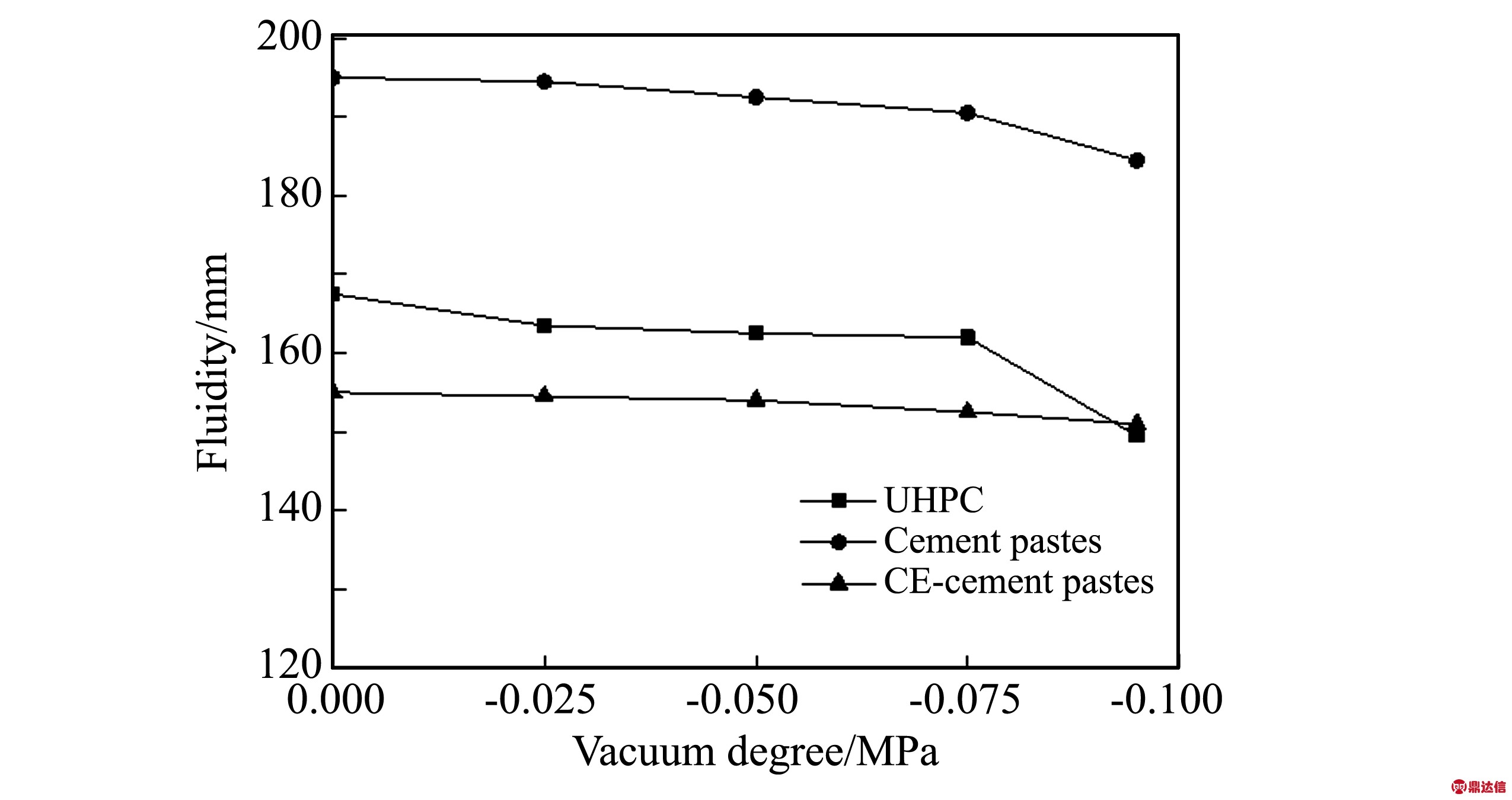
图3 真空度对水泥基材料流动度的影响
Fig.3 Influence of vacuum degree on fluidity of cement-based materials
在不同真空度条件下搅拌,水泥浆、纤维素醚改性水泥浆和超高性能混凝土三种水泥基材料的流动度变化情况如图3所示。由图3可知,随着真空度的降低,三种水泥基材料的流动度都减小。当搅拌时的真空度从0降低到-0.096 MPa时,水泥浆的流动度从195 mm下降到184.5 mm,下降5.4%;纤维素醚改性水泥浆的流动度从155 mm下降到151 mm,下降2.6%;超高性能混凝土的流动度从167.5 mm下降到149.5 mm,下降10.7%。相对于纯水泥浆,纤维素醚改性水泥浆的流动性下降了20.5%,这是由于纤维素醚的增稠作用导致的[11] 。
相对于常规条件,在不同真空度条件下搅拌的水泥基材料,它们在搅拌过程中与空气接触更少,因此在搅拌过程中引入的气泡较少,在接近完全真空条件下(真空度为-0.096 MPa),水泥基材料在搅拌过程中则几乎不引气。
由于气泡的滚动效果,水泥基材料中引入的气泡可以提高其流动性。因此,随着搅拌真空度的降低,水泥基材料中引入的气泡减少,三种水泥基材料的流动性都降低。
3.2 表观密度和抗压强度
在不同真空度条件下搅拌,水泥浆、纤维素醚改性水泥浆和超高性能混凝土三种水泥基材料的表观密度变化情况如图4所示。由图4可知,随着真空度的降低,三种水泥基材料的表观密度都增加。当搅拌时的真空度从0降低到-0.096 MPa时,水泥浆的表观密度从2075.8 kg/m3增加到2108.2 kg/m3,增加1.6%;纤维素醚改性水泥浆的表观密度从1655.1 kg/m3增加到2046.6 kg/m3,增加23.7%;超高性能混凝土的表观密度从2265.2 kg/m3增加到2412.9 kg/m3,增加6.5%。
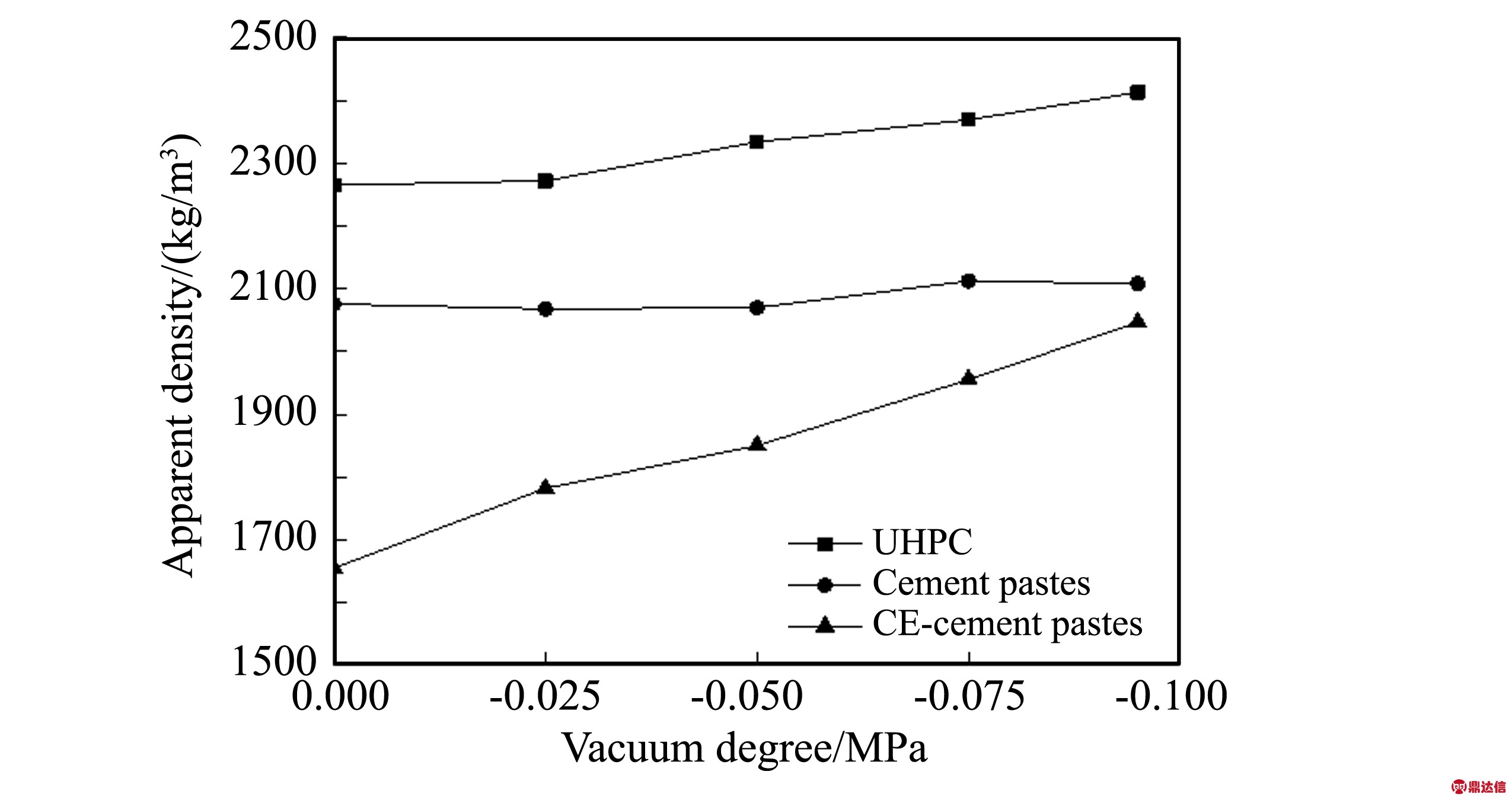
图4 真空度对水泥基材料表观密度的影响
Fig.4 Influence of vacuum degree on apparent density of cement-based materials
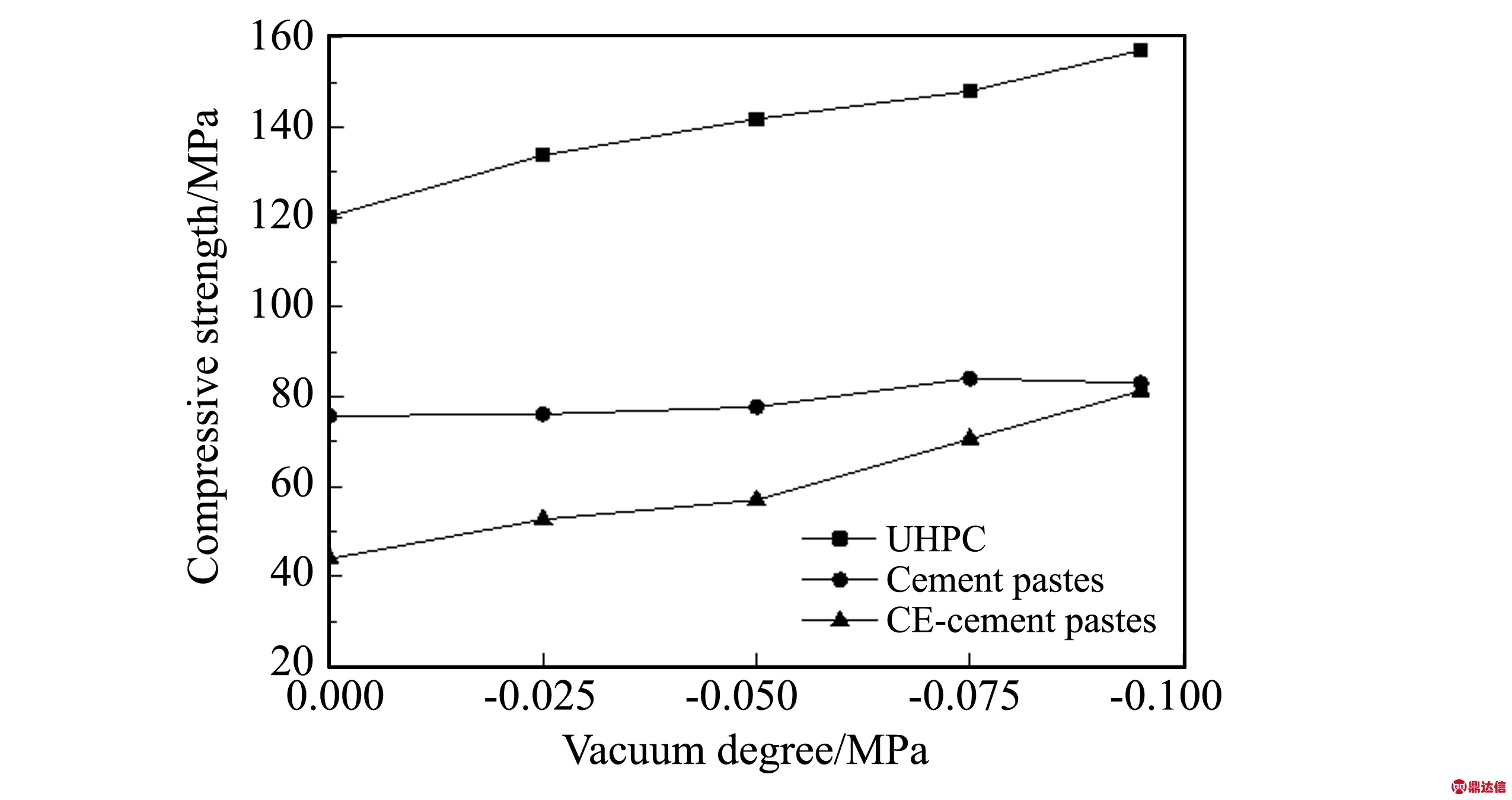
图5 真空度对水泥基材料抗压强度的影响
Fig.5 Influence of vacuum degree on compressive strength of cement-based materials
在不同真空度条件下搅拌,水泥浆、纤维素醚改性水泥浆和超高性能混凝土三种水泥基材料的抗压强度变化情况如图5所示。由图5可知,随着真空度的降低,三种水泥基材料的抗压强度都增加。当搅拌时的真空度从0降低到-0.096 MPa时,水泥浆的抗压强度从75.7 MPa增加到83 MPa,增加9.6%;纤维素醚改性水泥浆的抗压强度从43.9MPa增加到81.2 MPa,增加85%;超高性能混凝土的抗压强度从120.1 MPa增加到157.1 MPa,增加30.8%。相对于纯水泥浆,纤维素醚改性水泥浆的表观密度和抗压强度分别下降了20.3%和42%,这是由于纤维素醚的引气作用导致的[6,11-12]。
水泥基材料在搅拌过程中引入的气泡,在新拌水泥基材料中不断演变(如合并、扩散和破灭),水泥基材料硬化后,未破灭的气泡便在水泥基材料中形成孔隙[6] 。因此,随着搅拌时真空度的降低,水泥基材料中引入的气泡减少,最终形成孔隙率也会减少,表观密度和抗压强度会增加。但对于不同水泥基材料,真空搅拌时表观密度和抗压强度增加的幅度不一样,对于普通水泥浆,水灰比较大,水泥浆的最终孔隙中,水分蒸发形成的孔隙比例高,搅拌引气形成的孔隙比例低,因此真空搅拌对普通水泥浆抗压强度的增加不是很明显(提高9.6%);对于超高性能混凝土,水胶比低,减水剂通常还具有一定的引气效果[3],水分蒸发形成的孔隙比例要低一些,搅拌引气形成的孔隙比例要高一些,因此真空搅拌对超高性能混凝土抗压强度的增加比较明显(提高30.8%);对于纤维素醚改性水泥浆,由于纤维素醚具有很强的引气效果[6],尽管水灰比与纯水泥浆一样,但搅拌引气形成的孔隙比例非常高,因此真空搅拌对纤维素醚改性水泥浆抗压强度的增加非常明显(提高了85%)。从图4和图5可以看出,在常规条件下,纤维素醚改性水泥浆由于搅拌引气明显,其表观密度和抗压强度与水灰比相同的纯水泥浆相比要明显偏低,但在接近绝对真空条件下(-0.096 MPa)搅拌,其表观密度和抗压强度已经接近纯水泥浆。
在完全真空条件下,“真空搅拌混凝土”由于混凝土在搅拌时与空气隔绝,不会在混凝土中引入气泡(即使外加剂具有很强的引气效果),混凝土中的孔仅仅来自水的蒸发,从而几乎可以消除新拌混凝土的气泡,降低硬化混凝土的孔隙率,提高硬化混凝土的密实性和强度。显然,混凝土真空搅拌工艺可以消除减水剂、增稠剂等外加剂因引气而给混凝土带来的负面效果。
3.3 孔结构
根据压汞法的测试结果,在常规搅拌条件下,超高性能混凝土的表观密度为2.393 g/mL,孔隙率为7.2%;在真空搅拌(真空度为-0.096 MPa)条件下,其表观密度为2.404 g/mL,增加了4.6%,孔隙率为3.92%,下降了45%。
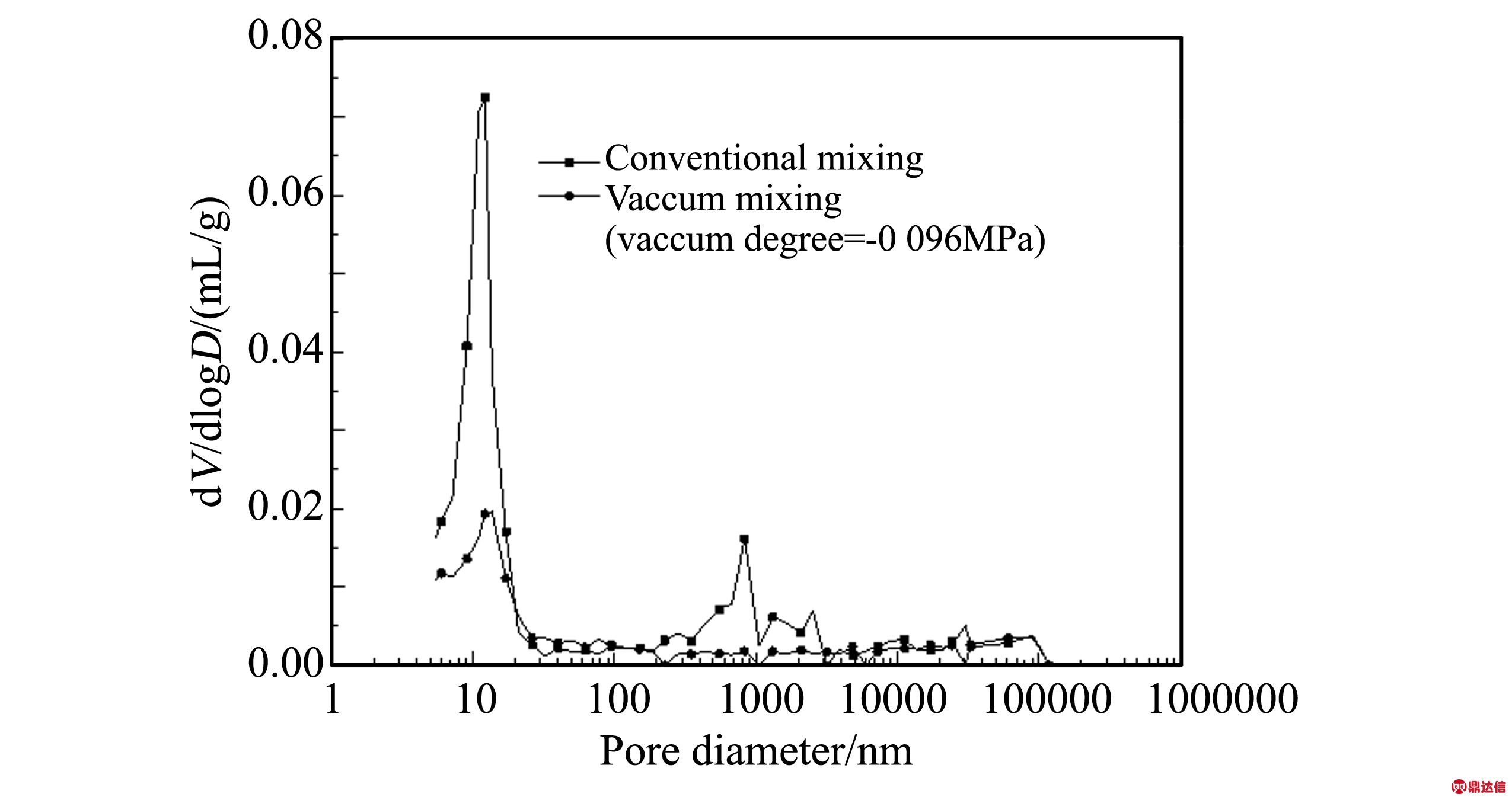
图6 真空搅拌超高性能混凝土的孔径分布
Fig.6 Pore distribution of vacuum mixing ultra-high performance concrete
图6比较了真空搅拌(真空度为-0.096 MPa)和常规搅拌条件下,超高性能混凝土的孔结构。由图可知,在常规搅拌条件下,超高性能混凝土的孔径分布曲线在7~11 nm和700~1100 nm两处存在明显的孔数量峰值,而在真空搅拌(真空度为-0.096 MPa)条件下,超高性能混凝土在700~1100 nm处的孔数量峰值消失,在7~11 nm处仍存在孔数量峰值,但峰值大小显著低于常规搅拌条件下的超高性能混凝土。
从超高性能混凝土的孔径分布来看,相对于常规搅拌,在接近绝对真空(真空度为-0.096 MPa)条件下搅拌,超高性能混凝土在700~1100 nm处的孔数量峰值消失,在7~11 nm处的孔数量峰值大幅降低。由表2[13]可知,这两处孔数量的降低都会影响混凝土的强度,这就是混凝土强度明显提高的原因,同时,还可以预计,7~11 nm处的孔数量峰值的大幅降低,还会减少混凝土的收缩和徐变,当然,这需要后续实验予以验证。
表2 水泥浆孔尺寸对水泥基材料性能的影响[13]
Tab.2 Influence of pore size of cement pastes on properties of cement based materials[13]

4 结 论
当水泥浆、纤维素醚改性水泥浆和超高性能混凝土三种水泥基材料搅拌时的真空度从0降低到-0.096 MPa时,它们的流动度都减小,表观密度和抗压强度都增加。其中水泥浆的抗压强度从75.7 MPa增加到83 MPa,增加9.6%;纤维素醚改性水泥浆的抗压强度从43.9 MPa增加到81.2 MPa,增加85%;超高性能混凝土的抗压强度从120.1 MPa增加到157.1 MPa,增加30.8%。相对于常规搅拌,在接近绝对真空(真空度为-0.096 MPa)条件下搅拌,超高性能混凝土在700~1100 nm处的孔数量峰值消失,在7~11 nm处的孔数量峰值大幅降低。
实验结果表明,真空搅拌工艺可以成为提高水泥基材料强度(尤其是高强水泥基材料)的一种新工艺,这对促进混凝土的技术进步具有重要意义。使用真空搅拌混凝土的成本也非常低,只需要对搅拌机进行密封,并增加一台真空泵即可。