摘 要:提出采用感性耦合技术实现非接触式电缆故障在线诊断的方法,解决现有非接触式诊断中容性耦合信号衰减量大、诊断效果不佳问题。相比于接触式诊断,非接触式诊断避免了诊断装置与待测电缆的电气连接问题,更安全更方便。首先基于感性耦合主要影响因素(互感、宽带信号耦合能力),理论分析理想条件下感性耦合与接触式直接注入式诊断效果一致时,耦合器的材质及参数特性,对感性耦合器进行了分析设计;进而分析和仿真验证即便在耦合器实际寄生参数影响下,其衰减程度依旧小于容性耦合,最后通过实验验证感性非接触式故障诊断检测率可达93%以上、定位误差在0.42 m以内,该方法具有高的实际推广应用价值。
关键词:感性耦合;非接触式;容性耦合;接触式;衰减
1 引 言
飞机在飞行过程中受潮、紫外线、温度、振动、过载等因素的影响严重[1-2],随着飞机机龄的增加,置于飞机内部的电缆逐渐产生裂纹和磨损,易发生短路、断路及间歇性故障,使飞机的安全飞行存在极大隐患。因此亟需一种电缆故障检测定位方法,对电缆故障进行判定,达到及时排除故障、保证设备安全运作的目的。
电缆故障诊断方法迄今为止已多种多样[2-3],主要有目测法、阻抗测试法、三用表测试法、反射法等几种类型。反射法根据入射信号的不同,分为时域反射法[3-4](time domain reflectomertry, TDR)、频域反射法[5](frequency domain reflectometry, FDR)、序列时域反射法[6-7](sequence time domain reflectometry, STDR)、扩展频谱时域反射法[7-8](spread spectrum time domain reflectometry, SSTDR)及噪声域反射法[9](noise domain reflectometry, NDR)等几种形式。考虑到检测的实时性、检测率、定位精度等因素,SSTDR以其定位精度高、抗干扰性强、能够实现在线诊断,适用范围广泛等[10-12]优点而成为研究重点。
然而,不论是SSTDR还是其他反射法都需要将故障诊断装置与电缆导体直接相连,实现信号的注入与接收。这需要断开电缆的原有连接、改变系统的接口端子,增加了系统设计的复杂度、工作量和成本。为了克服接触式诊断的局限性,一些研究学者提出将无线传感器应用于电力线的诊断中,它不会对电缆造成二次损伤[13-16]。但这些方法需要使用分布式传感器,如形面波发射器(conformal surface wave,CSW),罗氏线圈、皮尔森线圈等。多数情况下一套诊断装置不单单只需一个传感器,且传感器的形状、成本、重量通常不能均衡共优。例如文献[13]采用形面波发射器进行电力线诊断时,只有当线路中存在开路故障才能被检测,这是有一定局限性的。同时文献[16]提到,无线传感器处理数据能力是有限的,并且他们均需要大容量的储能电源供电来避免频繁地更换,但这增加了传感器的体积重量,也是一大缺点。为此有国外有学者提出将非接触耦合方式应用于反射法,检测信号不再采用直接注入式,而是通过耦合器将信号耦合到线缆中去,并将反射信号耦合输出到诊断装置的信号接收端。该方法能够避免诊断装置与待测电缆之间的电气连接,无需对原有电缆线路进行改动和变化,使用简便,且该类传感器不需要供电电源,对系统的体积重量影响不大,能够极大地提高反射法在实际应用中的安全性和实用性。
信号耦合常用的有容性耦合和感性耦合两种[17-18]。Wu S等人[18]和冯慈璋等人[19]提出了将容性耦合用于STDR,实现非接触式电缆故障检测定位。相比于容性耦合,电感耦合是基于变压器耦合工作原理,有阻抗调节作用、装置简单、绝缘性好、安全。且文献[17]中对感性耦合与容性耦合作了比较,文献中提到当采用集总电容实现直接耦合时,电感耦合相对于电容耦合信号衰减要大,但仍无法避免电气连接。而在容性耦合中,根据容性非接触耦合实现原理,一方面受线缆尺寸、加工工艺等限制,衰减大,诊断效果不佳。另一方面针对不同尺寸的线缆,为了保证尽可能大的容值,套在电缆绝缘层外的导体环需紧贴电缆绝缘层,从而避免过大的信号衰减,因此耦合装置需重新设计加工,工作量及成本大大增加[18]。
针对接触式诊断及容性非接触式诊断的局限性,本文开展了感性非接触式电缆故障诊断方法研究,采用SSTDR进行验证。基于感性非接触信号耦合主要影响因素—互感,综合信号耦合影响因素材料、结构、尺寸等,对感性耦合器进行了分析与设计,实现高频检测信号的非接触耦合;针对实际设计的耦合器,考虑寄生参数带来的信号畸变、衰减问题,通过理论和仿真研究其信号耦合衰减规律,并与容性非接触耦合方式进行了对比分析;最后实验验证感性非接触式电缆故障诊断方法的可行性及有效性。
2 感性非接触式电缆故障诊断原理
2.1 SSTDR电缆故障诊断原理
SSTDR电缆故障检测定位方法原理结构如图1所示。
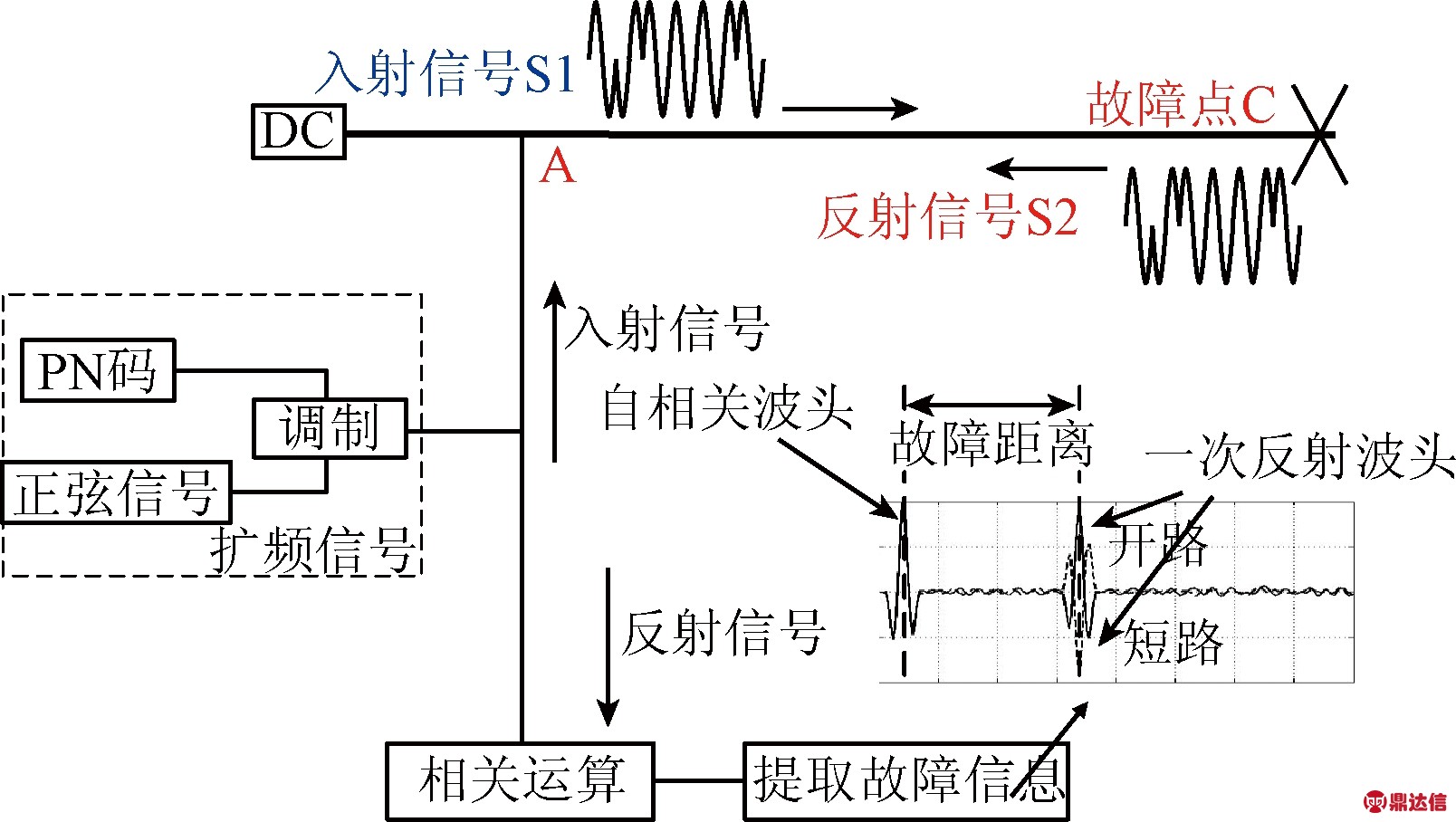
图1 SSTDR检测定位原理框图
Fig.1 The principle diagram of SSTDR cable fault detection and positioning
基于传输线中波的反射原理,由m序列与正弦波调制后的高频信号从图中的A点注入待测电缆,高频检测信号下,特定型号的电缆阻抗是一定的,设置信号注入前端阻抗与电缆特性阻抗大小一致,当待测电缆C点发生故障时,由于阻抗的不匹配信号会发生反射,同样在A点采集反射信号,根据反射信号相对于入射信号的幅值和延迟特性,判定故障类型及故障距离。由SSTDR实现原理得只要保证信号注入前端阻抗与电缆特性阻抗匹配,则对于不同型号、尺寸、阻抗大小的电缆故障均可测,这也验证了引言所述具有适用范围广泛的优点。
根据传输线理论[19],入射信号在电缆x点处的反射系数ρ为:
ρ=
(1)
式中:ZL为电缆x点处的负载阻抗,Zc为电缆特性阻抗。由式(1)可得当电缆x点处发生开路故障时,ZL=∞,ρ=1,相关运算后反射波头与入射波头极性相同;当电缆x点处发生短路故障时,ZL=0,ρ=-1,相关运算后反射波头与入射波头极性相反。
根据延时时间t和检测信号在电缆中的传播速度v计算故障距离l,如式(2)所示。
l=vt
(2)
根据SSTDR故障诊断检测定位原理,系统存在一个采样精度的定位误差,设系统采样频率为fn,因此定位误差dc为:
dc=×v×
(3)
本文SSTDR检测系统采样率为240 MHz,检测信号在特定型号的电缆(AF250)内传播速度为2×108 m/s,因此故障定位误差理论计算得在0.42 m范围内。
2.2 感性非接触耦合原理
基于感性耦合的非接触式SSTDR电缆故障检测定位结构如图2所示,检测装置与待测电缆之间通过感性耦合器实现信号的注入与接收。同样将注入电缆中的检测信号与通过耦合器耦合输出的反射信号进行相关运算,从而提取故障信息,实现电缆故障的检测与定位。为了实现信号的非接触耦合,本文通过在信号线与待测电缆的外部套上高磁导率磁环,信号线与待测电缆分别充当变压器的原副边,基于变压器工作原理,实现检测信号在高频检测信号线与待测电缆之间的信号传递。
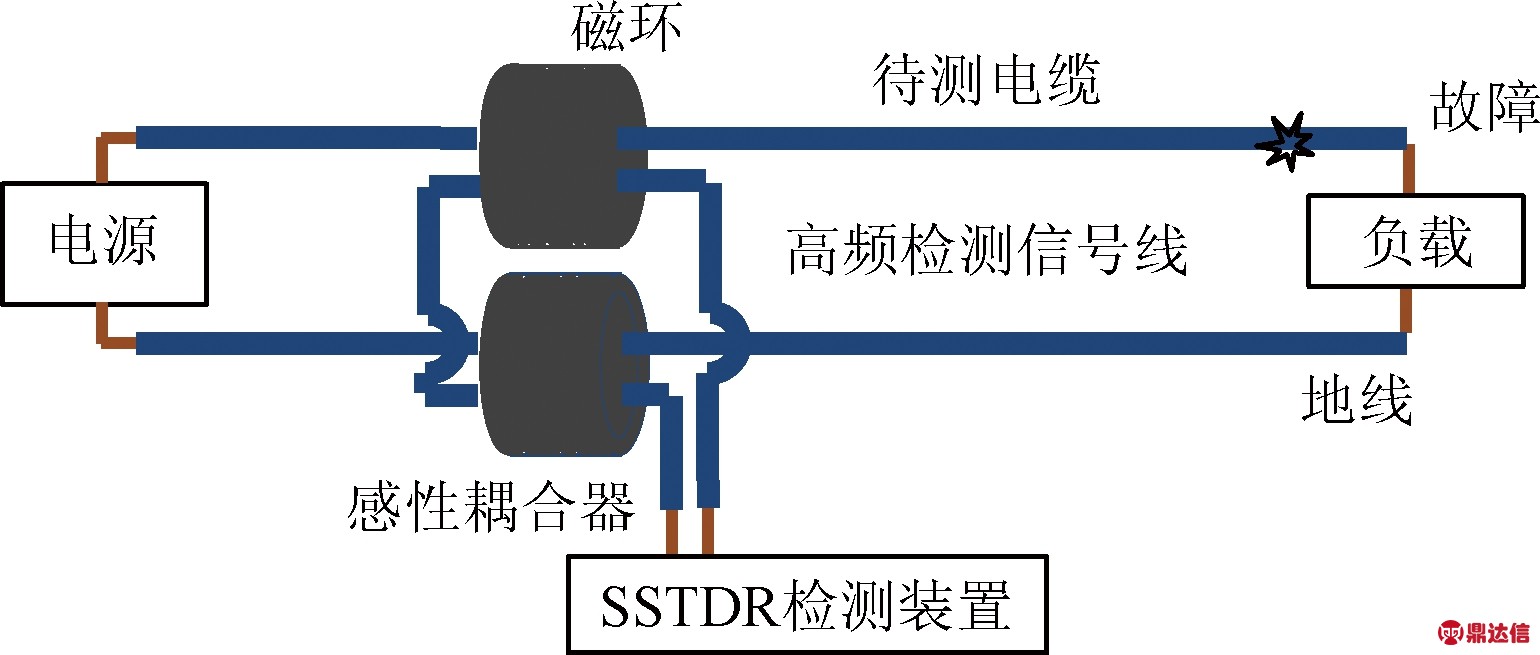
图2 感性非接触式电缆故障诊断示意图
Fig.2 Schematic diagram of inductive non-contact cable fault diagnosis
耦合器的工作原理如图3所示,根据电磁感应定律[20],当信号线中通入电流i1时,在信号线中产生磁通φ11,由于铁氧体材料的相对磁导率μr>>1,因此磁场主要分布于铁氧体所在位置,于是φ11中几乎全部的磁通都穿过了待测电缆。
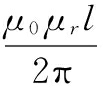
图3 两线圈的信号耦合
Fig.3 Signal coupling of two coils
Ψ11=Nφ11=φ11(N1=1)
Ψ21=Nφ21=φ21≈φ11(N2=1)
(4)
式中:Ψ11为自感磁通链,Ψ21为互感磁通链。因此自感系数L1及互感系数M21为:
L1==
M21=≈
=L1
(5)
所以待测电缆中的感应电势u21为:
u21=M21=L1
=u1
(6)
已知u1为信号线上的电压,由式(6)得在高磁导率磁环作用下,较好地实现将信号线中的电压1∶1的耦合到待测电缆中去。当反射信号耦合输出时同理,只是将变压器的原副边对换。
3 感性耦合器模型研究
3.1 感性耦合器信号耦合影响因素研究
本文SSTDR故障诊断采用1~60 MHz的宽带信号作为检测信号,在非接触式诊断中,感性耦合对检测效果的影响主要包括两个方面,一方面经耦合后的检测信号宽带特性,其决定了系统的抗干扰能力;另一方面,检测信号在耦合中的衰减特性,其决定了反射信号幅值大小,能否采集到并识别故障。而影响感性耦合这两个因素的主要是耦合磁芯的材质及材料参数。
为了尽可能地减小信号耦合导致的衰减问题,耦合器的互感值越大越好。根据变压器磁耦合原理,磁性材料的磁导率μ越大,其互感值也越大。考虑到检测信号频率较高,本文采用镍锌铁氧体材料,基于安培环路定理:
Hl=I⟹·2πr=I
(7)
式中:H为磁场强度,l为磁场闭合回路所在路径,I为回路匝链电流,B为磁感应强度大小,μ为磁环绝对磁导率大小,r为磁环半径。考虑到当电缆中通过最大载流时,耦合器应工作在非饱和状态,耦合器的内径应满足以下条件:
r最小内径≥I最大载流·/2π
(8)
式中:Bs为磁芯材料饱和磁密。按常规镍锌铁氧体材料的饱和磁密280 mT计算,考虑小型化的要求,磁环的最小内半径定于5 mm,最大载流为10 A,计算得磁芯的相对磁导率约为1 400。
为了保证耦合后的信号宽带特性,磁性材料的适用频率范围因至少大于检测信号最低频带范围(1~60 MHz)。综合以上两个因素,本文选用相对磁导率为1 500,磁芯材质为HF70的磁性材料,其基本参数如表1所示。
表1 HF70材料基本参数
Table 1 Basic parameters of the material HF70
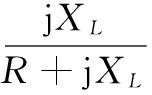
由表1可得其磁性材料磁导率为1 500>1 400,满足要求,且其适用频率为0~500 MHz,符合检测信号频带范围要求。考虑到非接触式诊断中耦合器的安装/拆卸问题,本文选用半圆柱形的铁氧体磁环相扣的结构,如图4所示为其结构示意图。
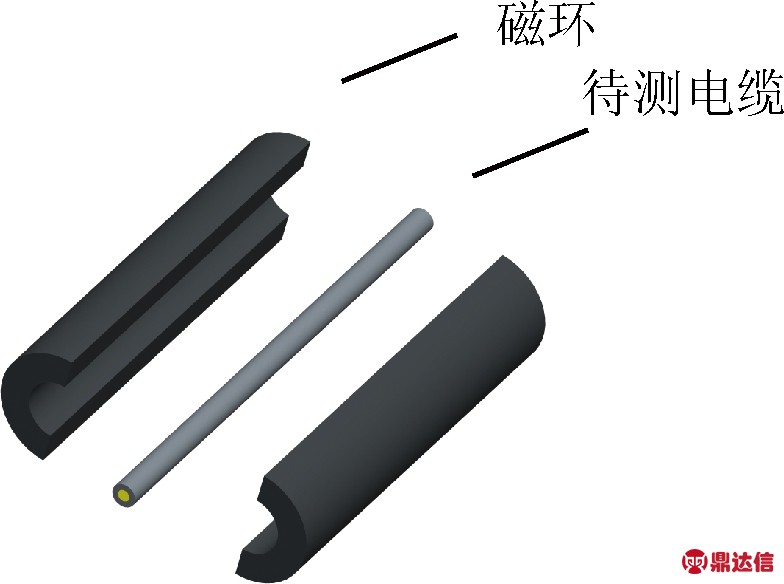
图4 待测电缆与磁环连接爆炸图
Fig.4 Explosion diagram of the cable under test and magnet ring
3.2 感性耦合器理论分析
根据导体电感计算式(5),导体电感为与电流回路交链的磁链和电流的比值,已知与电流回路交链的磁链包括导体层内部磁链和导体层外部磁链。因此待测电缆单位长度分布电感L0包括内分布电感Li和外分布电感Le[20],如式(9)所示。
L0=Li+Le
(9)
已知单位长度的待测电缆内分布电感Li为:
Li= (H/m)
(10)
式中:μ0=4π×10-7为真空中的磁导率。
套上磁环后,磁环及其内部导体的横截面图如图5所示,根据安培环路定理得:
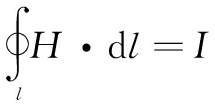
(11)
H1·2πx+Hδ·2d=I
(12)
根据磁场中分界面的衔接条件,得式(12)中H1=B/μ0μr, Hδ=B/μ0,因此计算得磁感应强度为:
B=
(13)
其中,d为磁环气隙大小,已知磁通φ为:
φ
(14)
因此穿过截面的磁通为:
φ
(15)
已知耦合器内部匝链的导线数N=1,因此磁链ψ=φ,根据电感计算式(5),理论推导得待测电缆外部套有长度为l的磁环其外电感为:
Le=ln
(16)
式中:μr为磁性材料相对磁导率,a与b分别为磁环的内半径和外半径。
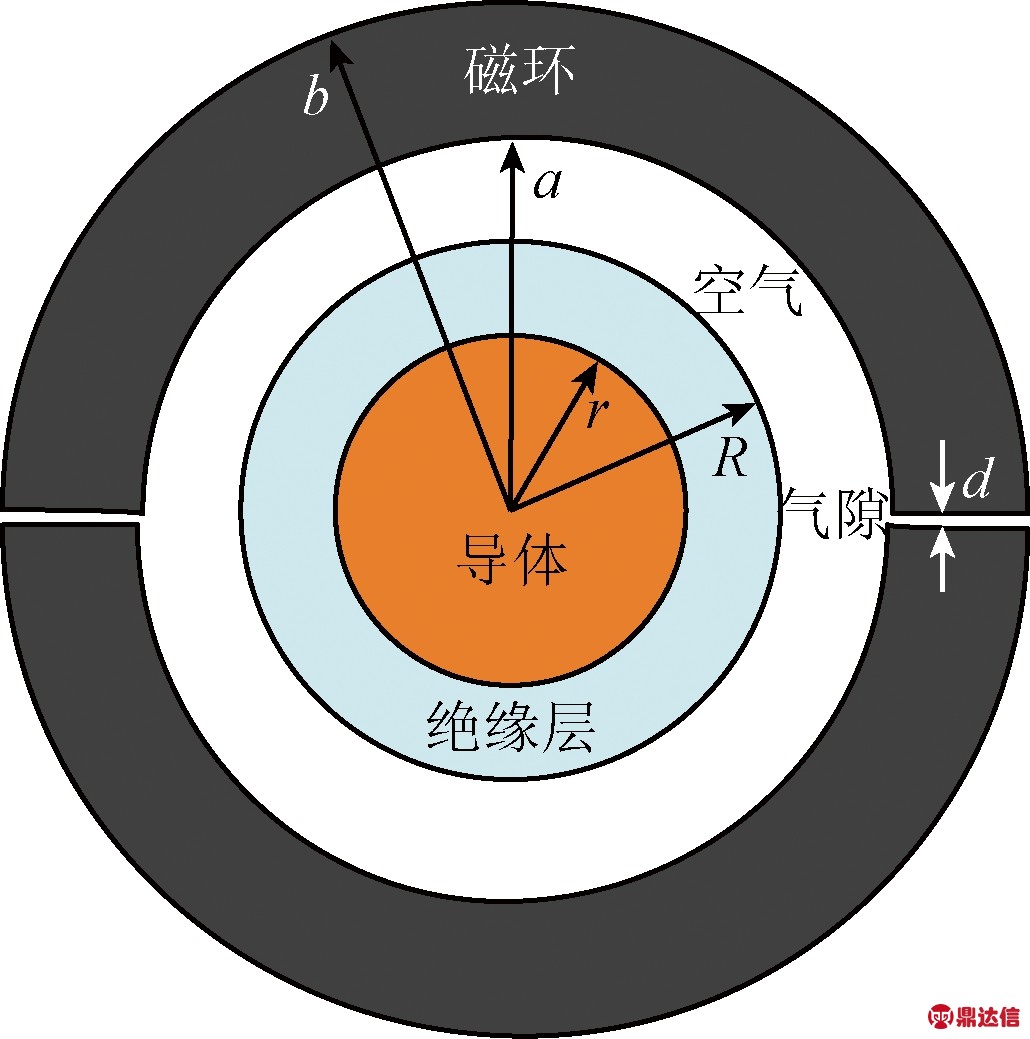
图5 带耦合器的导线横截面
Fig.5 The cross section diagram of the cable with coupler
由于磁性材料的相对磁导率远远大于真空(μr>>1),磁场主要集中于磁环本体,待测电缆的内分布电感可以忽略不计,并根据上述分析可得电缆的外分布电感近似等于信号线与线缆之间的互感值,因此:
M=L0=Li+Le≈Le=ln
(17)
为了求取实际用于电缆故障诊断时信号耦合所需的互感值大小,根据感应电压计算公式:
u=M
(18)
已知输入信号u1为幅值为1 V的扩频信号,检测信号中心频率为30 MHz,待测电缆特性阻抗为100 Ω,为了保证待测电缆中的感应电势达1 V,互感值M可以计算如下:
M=(200)/(2×π×30×106)=1.06 μH
(19)
式(19)说明了耦合器的互感值需≥1 μH。为了验证上述推理的正确性,在MATLAB中搭建了电缆故障诊断模型,仿真分析耦合器所需互感值大小,图6所示为耦合器互感值仿真设计平台结构示意图。
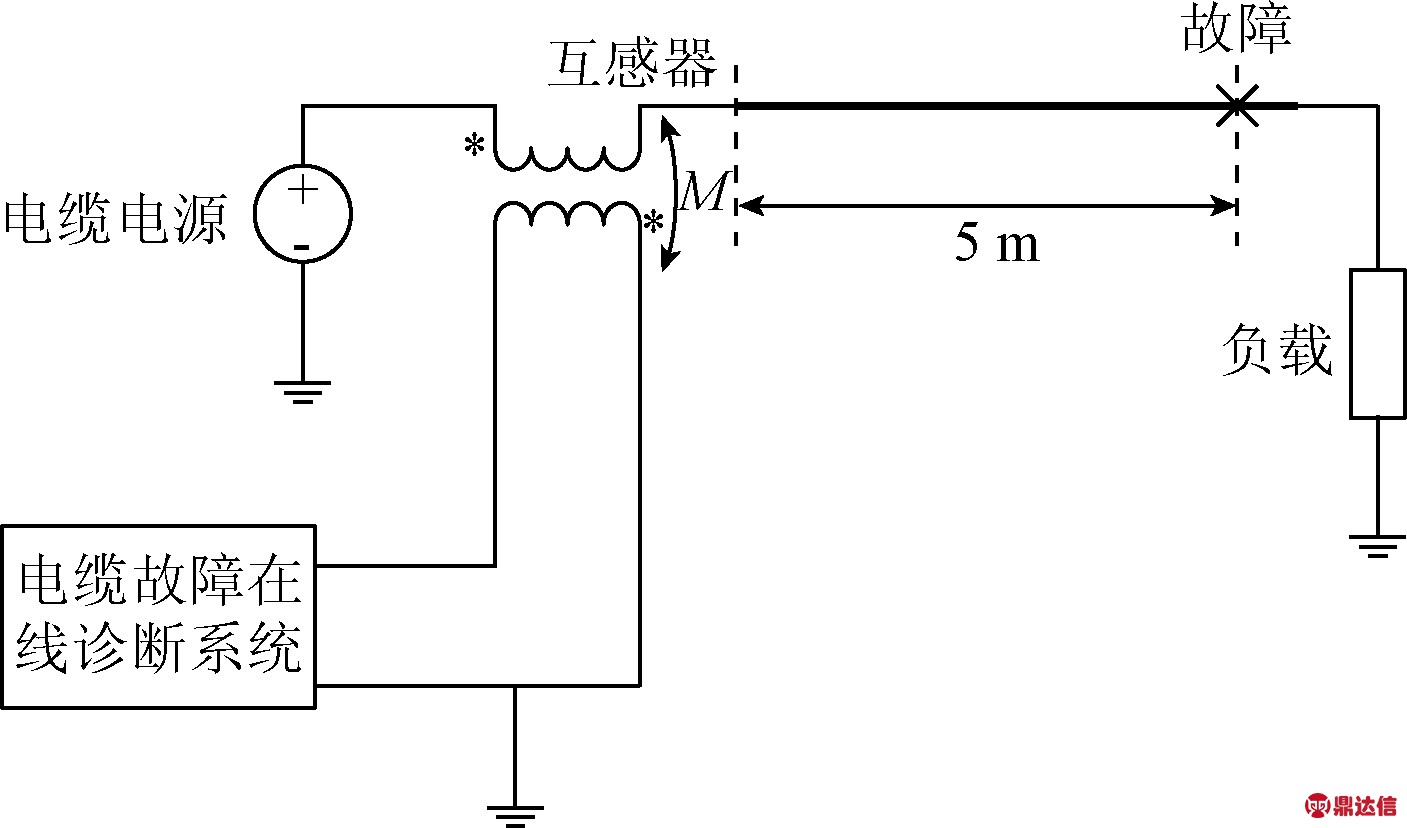
图6 耦合器互感值设计仿真平台
Fig.6 Simulation platform for coupler mutual inductance value design
仿真中耦合器用理想互感器模型代替,分别设置耦合器互感值大小为0.1、0.5、1、2 μH,将故障诊断结果与直接注入式无耦合器比较,诊断波形如图7所示。
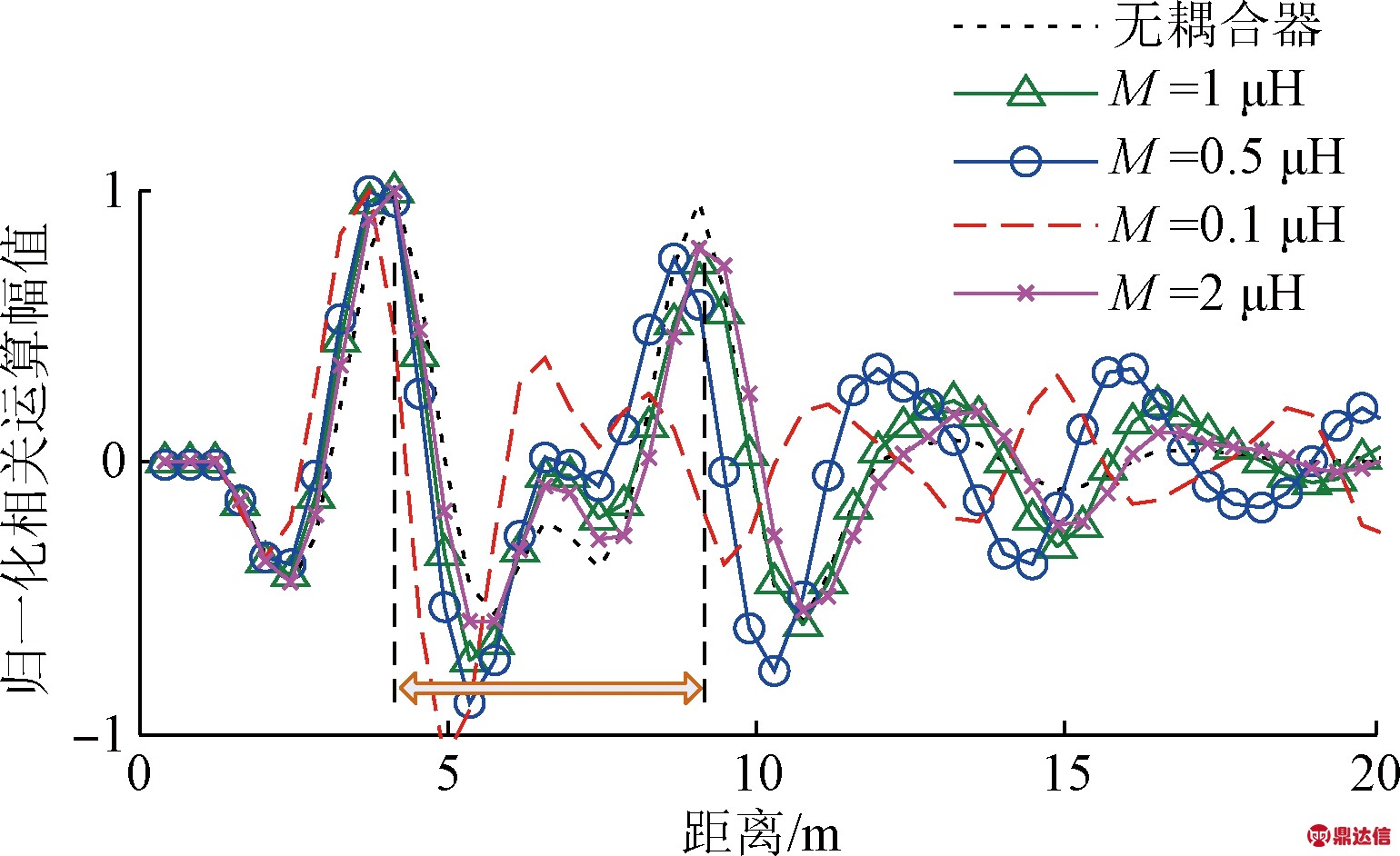
图7 耦合器互感值仿真诊断曲线
Fig.7 Simulation diagnosis curve diagram for the coupler mutual inductance value
仿真结果表明,随着互感值的增大,接触式诊断与非接触式诊断波形越来越接近。在互感值大于等于1 μH的情况下,电缆故障诊断曲线与无耦合器直接注入待测电缆波形比较吻合,故障类型判定正确,故障定位距离与无耦合器相同,保证了较好地信号耦合效果。根据该结论,耦合器的具体设计尺寸如表2所示。
表2 耦合器具体设计尺寸大小
Table 2 designed dimensions of the coupler

根据设计的耦合器尺寸大小,对耦合器互感值进行了理论计算、Ansoft有限元仿真,实物测量,其结果如表3所示。
表3 磁环耦合的线缆电感值
Table 3 Inductance value of the cable with coupler
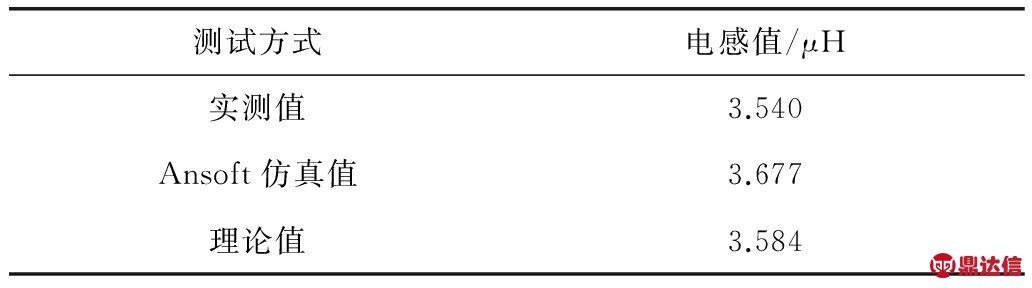
由表3得,感性耦合器作用下线缆之间互感的理论计算值、仿真值及实测值都比较接近,验证了式(17)理论推导的正确性,同时也满足了信号耦合所需达到的互感值要求。
相比于理想变压器,由于感性耦合器存在寄生参数,会对宽频检测信号的耦合特性(畸变、衰减)存在一定的影响。
4 感性耦合器耦合特性研究
由于检测信号为宽频信号(1~60 MHz),加之耦合器自身寄生参数的影响,检测信号频率不同,耦合到待测电缆中的信号幅值、相位也会不同,因此需研究分析耦合器耦合特性。
4.1 感性耦合器对检测信号宽带特性研究
在MATLAB中建立基于感性耦合的SSTDR电缆故障检测仿真模型,考虑耦合器实际寄生参数。首先对耦合器作用下信号宽带特性进行仿真研究,无故障情况下,经耦合器耦合后的入射信号与反射信号波形如图8所示。
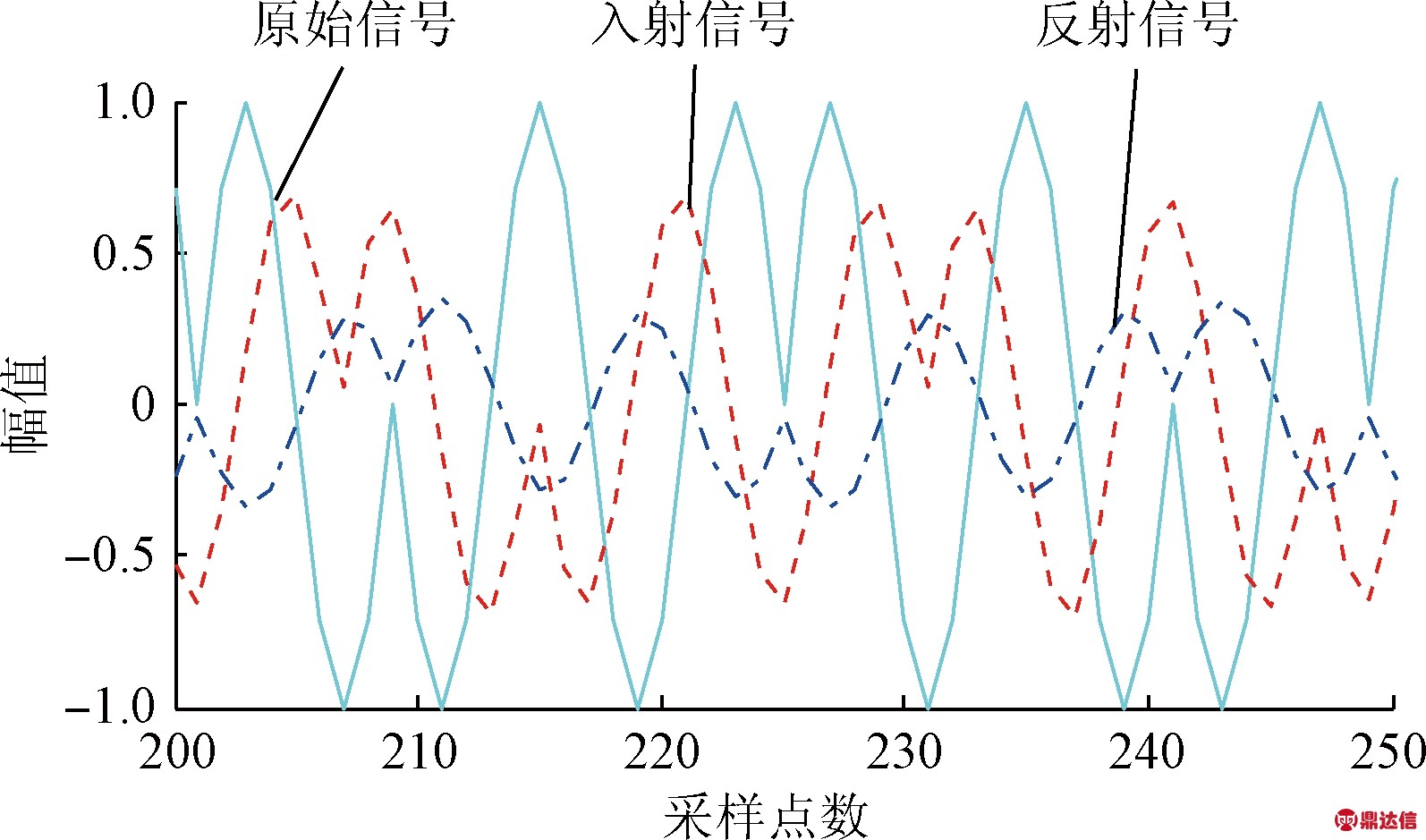
图8 信号耦合效果仿真
Fig.8 Simulation diagram of signal coupling effect
图8中实线是原始检测信号波形,虚线为经耦合器耦合后的入射信号波形,点划线是经耦合器耦合后采集的反射信号波形。由图8可得扩频信号经过耦合器耦合后,入射信号与反射信号保持了原始检测信号的形状,为了研究耦合后信号的宽带特性,对这3种信号进行了功率谱密度分析,其结果如图9所示。
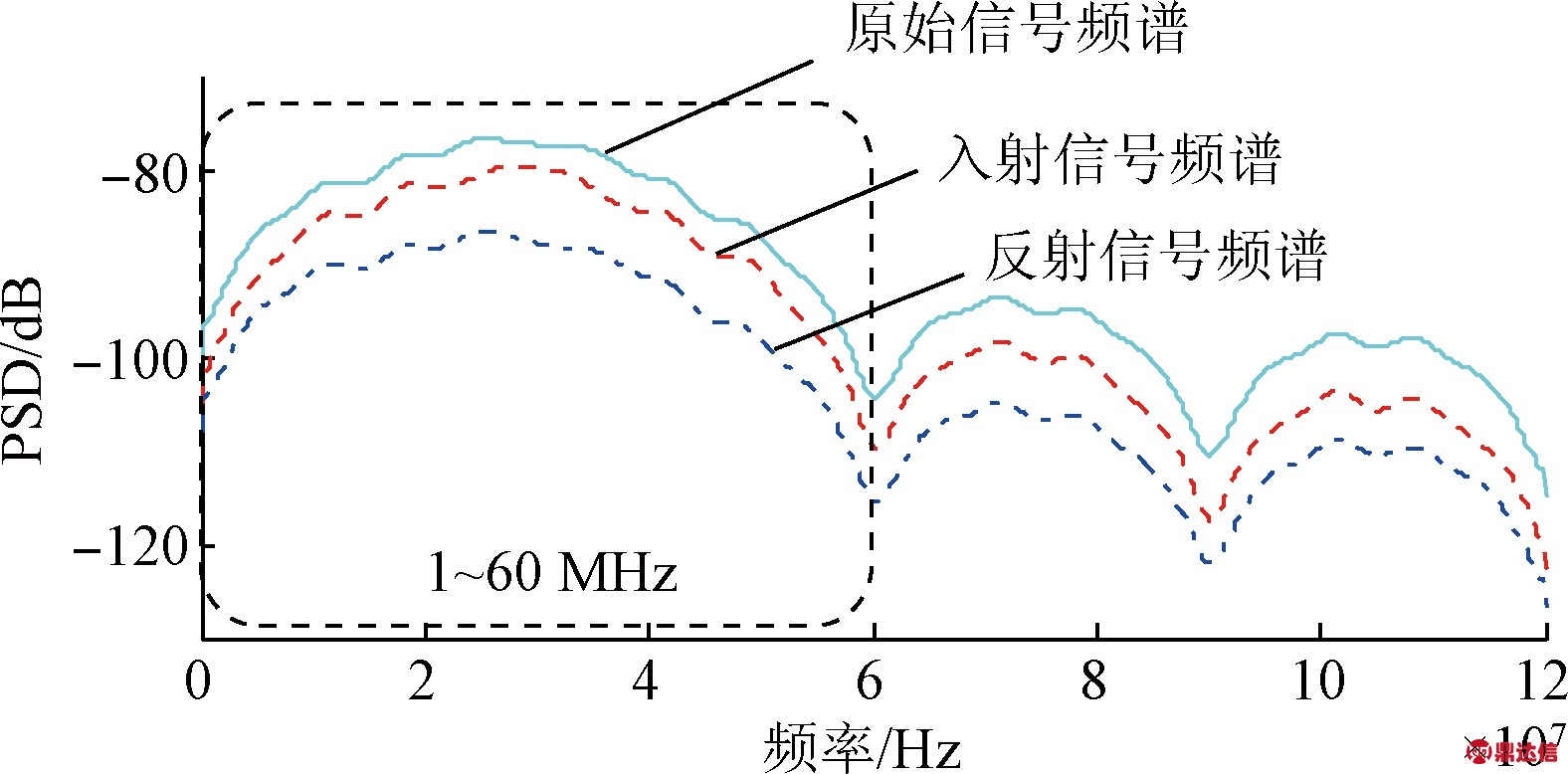
图9 检测信号原始波形、耦合后入射信号与反射信号频谱分析图
Fig.9 Spectrums of detection signal original wave, incident signal and reflected signal after coupling
结果表明经耦合器耦合后的入射信号与反射信号发生了一定程度的衰减,在不同频率点其衰减程度有所不一,但保持了原始信号的宽频特性(1~60 MHz),抗干扰能力得以保证,有助于实现电缆故障的在线检测定位。但同时由图9可得,反射波形相比于原始信号由较大程度的衰减。
4.2 感性耦合器用于电缆故障诊断衰减特性研究
由4.1节可得经感性耦合器作用后的入射信号与反射信号发生了一定程度的衰减,因此反射系数也不会如式(1)所示,为1或-1。若衰减程度过大,会使接收到的反射信号幅值过小而使反射系数值大大减小,进而无法判断出电缆故障。因此下面对感性耦合器应用于电缆故障诊断衰减特性进行理论分析。
如图10所示为感性非接触式电缆故障诊断等效电路图,等效后Rs计算得32.09 Ω,Zs计算得2.85 Ω。
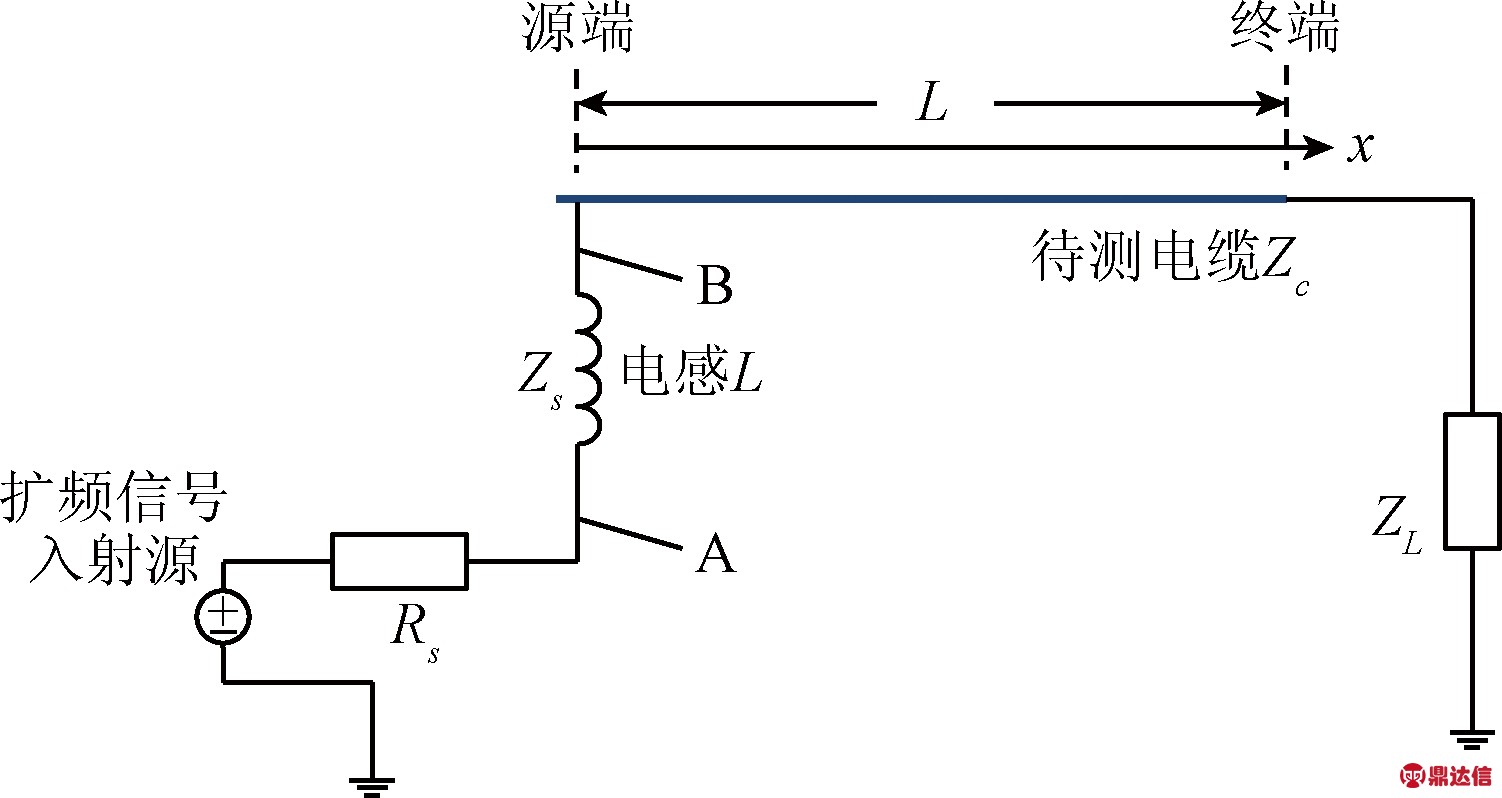
图10 感性非接触电缆故障诊断简化后的等效电路
Fig.10 Simplified equivalent circuit diagram of inductive non-contact cable fault diagnosis
根据传输线理论中任意一点的电压电流方程:
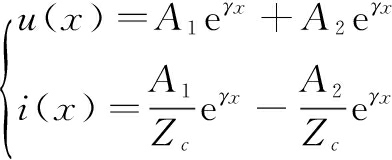
(20)
式中:A1和A2为待定系数,γ为传播常数。其计算公式如下:
A1=(U1+Z0I1),A2=
(U1-Z0I1),
γ==α+jβ
(21)
式中:U1和I1分别为始端(x=0)处的电压和电流。设整个源端阻抗为Zg,则其源端条件可以表示为:
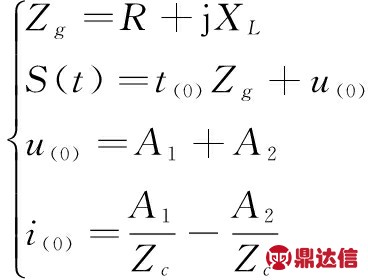
(22)
终端条件为:
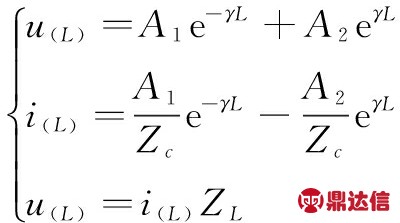
(23)
根据源端条件和终端条件可解得电缆任意一点电压为:
u(x)=[e-γx+ГLe-γ(2L-x)+ГsГLe-γ(2L+x)+

(24)
式中:Гs为源端反射系数,ГL为终端反射系数。
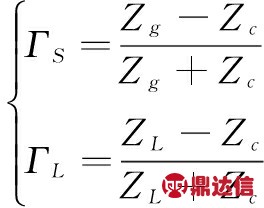
(25)
设扩频入射信号源输出的信号为s(t),由叠加定理可知,A点信号的幅值sA可由s(t)及B点信号幅值sB求出:
sA=S(t)+
SB
(26)
B点信号sB为扩频入射信号在x=0处的电压幅值,可求出A点信号sA的表达式。
采集A点信号,与入射信号进行相关运算:

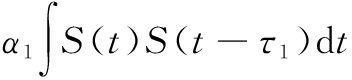
(27)
式中:τ1为一次反射信号与入射信号之间的延迟,α0为入射波头幅值大小,α1为一次反射波头幅值大小。
根据式(24)和(26),求得自相关波头幅值大小为:
α0=+
(28)
一次反射波头幅值大小为:
α1=×ГL(1+ГS)e-2γL
(29)
当电缆开路时,ГL=1,Гs=-0.514,所以:

(30)
所以故障点的反射系数计算得0.485,理论分析表明由于耦合器寄生参数的影响,检测信号在耦合过程中发生了较大程度地衰减,反射系数大大减小,由1减小到0.485。
对应地,将容性非接触式诊断反射系数大小进行理论分析,参考文献[18]的结论,设计的非接触电容容值最大能达到300 pF/m, 假定其长度0.05 m,则其容值为15 pF。容抗Xc=354 Ω, Гs=-0.87, ГL=1,因此容性非接触式诊断电缆故障点反射系数为:
ГL(1+Гs)≈1∶0.13
(31)
将式(30)和(31)比较发现,容性非接触式诊断反射系数远远小于感性非接触式诊断,理论分析表明感性耦合信号衰减程度远远小于容性耦合,在诊断中其故障特征更突出明显,易检测。因此在非接触式中感性效果相对更好。且根据参考文献[6],其对于型号为AWG22#的双绞线电缆,由诊断波形计算得在反射系数为0.375时成功地实现了故障定位,本文感性非接触式诊断反射系数为0.485,高于0.375,说明了将感性耦合器应用于电缆故障检测实现非接触式诊断的可行性。
5 感性非接触式电缆故障诊断仿真与实验研究
5.1 感性非接触式电缆故障诊断仿真研究
为了验证在非接触式诊断中对信号衰减理论分析的正确性,本文进行了感性非接触式诊断与容性非接触式诊断的仿真研究,在MATLAB中分别建立感性和容性非接触诊断模型,于待测电缆4.75 m处设置开路故障,仿真对比结果如图11所示。
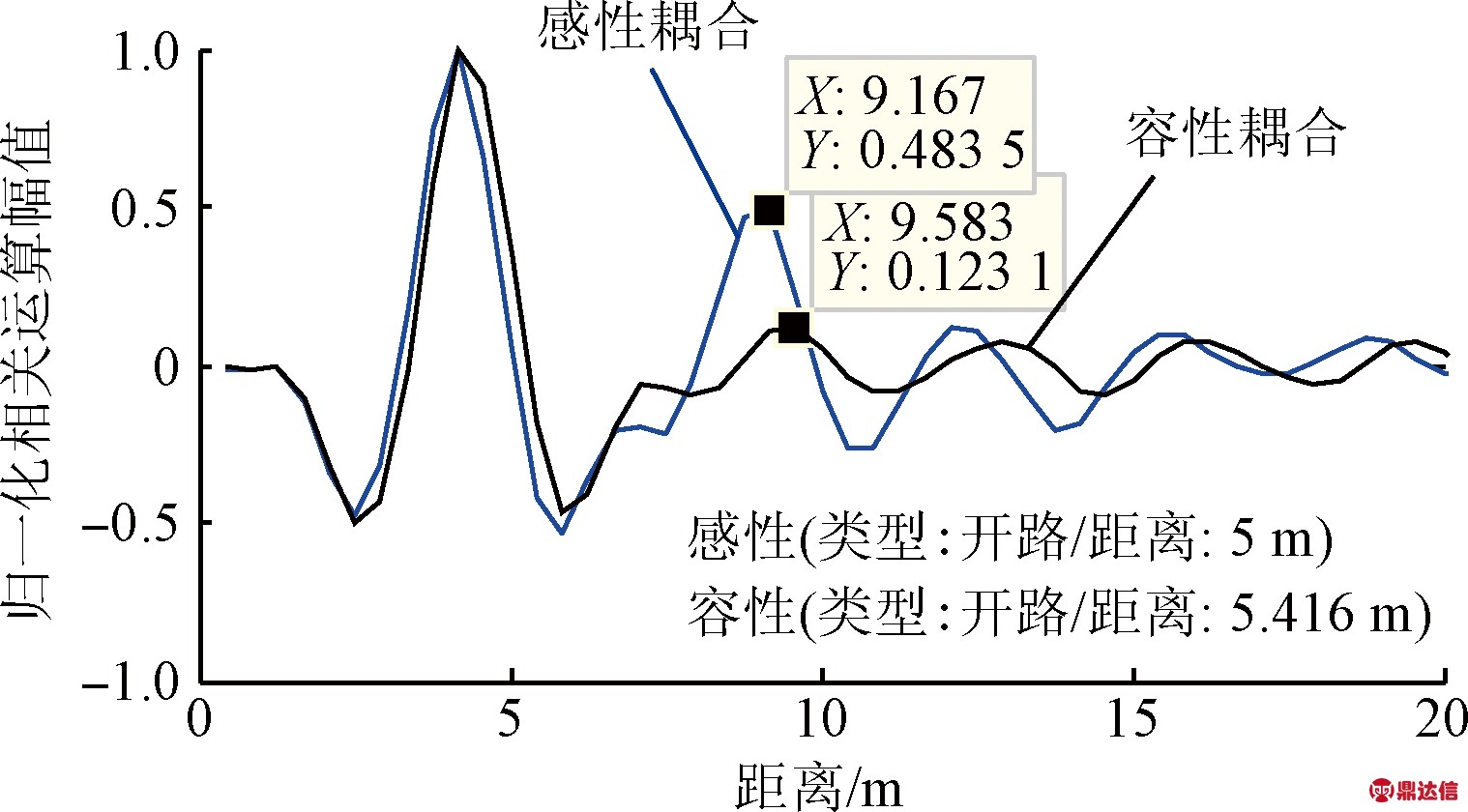
图11 实际距离4.75 m处开路故障诊断仿真结果
Fig.11 Simulation result diagram of the cable with open fault at the length of 4.75 meters
经仿真比较,采用感性非接触式诊断方法,其一次反射波头的幅值为0.483,与理论值比较接近。相反地,采用容性非接触式诊断,而反射波头幅值为0.12,远远小于感性耦合,验证了容性耦合信号衰减远远大于感性耦合的结论,与理论分析一致。且对于故障点的定位,感性非接触诊断故障距离为5 m,存在0.25 m的定位误差,在理论误差(0.42 m)范围内,电缆故障特征明显,易检测,能实现准确定位。而容性非接触式诊断由于反射系数的大大衰减问题,如归一化相关波形所示,其故障点的反射系数大小与其余点接近,故障特征识别困难,最终诊断距离为5.416 m,定位误差为67 cm,超出理论误差范围,进一步验证了感性非接触式电缆故障诊断的优越性。
5.2 感性非接触式电缆故障诊断实验研究
进一步将实际设计的感性耦合器用于非接触式电缆故障诊断实验验证,感性非接触式电缆故障诊断实验平台如图12所示。
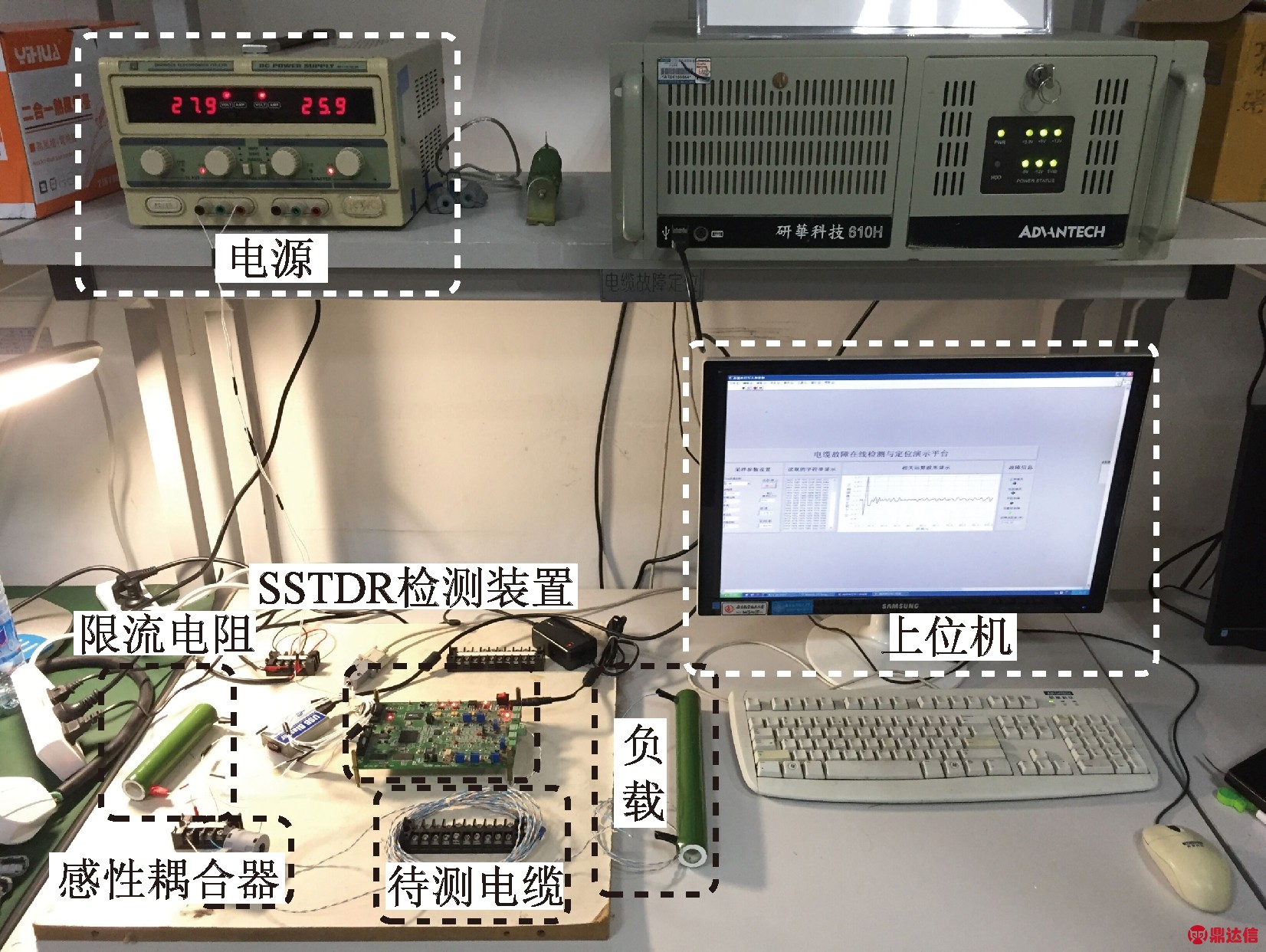
图12 感性非接触式电缆故障诊断实验平台
Fig.12 Experiment platform of inductive non-contact cable fault diagnosis
分别在待测电缆4.75、8.10 m处设置开路和短路故障,故障诊断结果如图13所示,并对检测结果进行具体的统计,统计结果如表4所示。
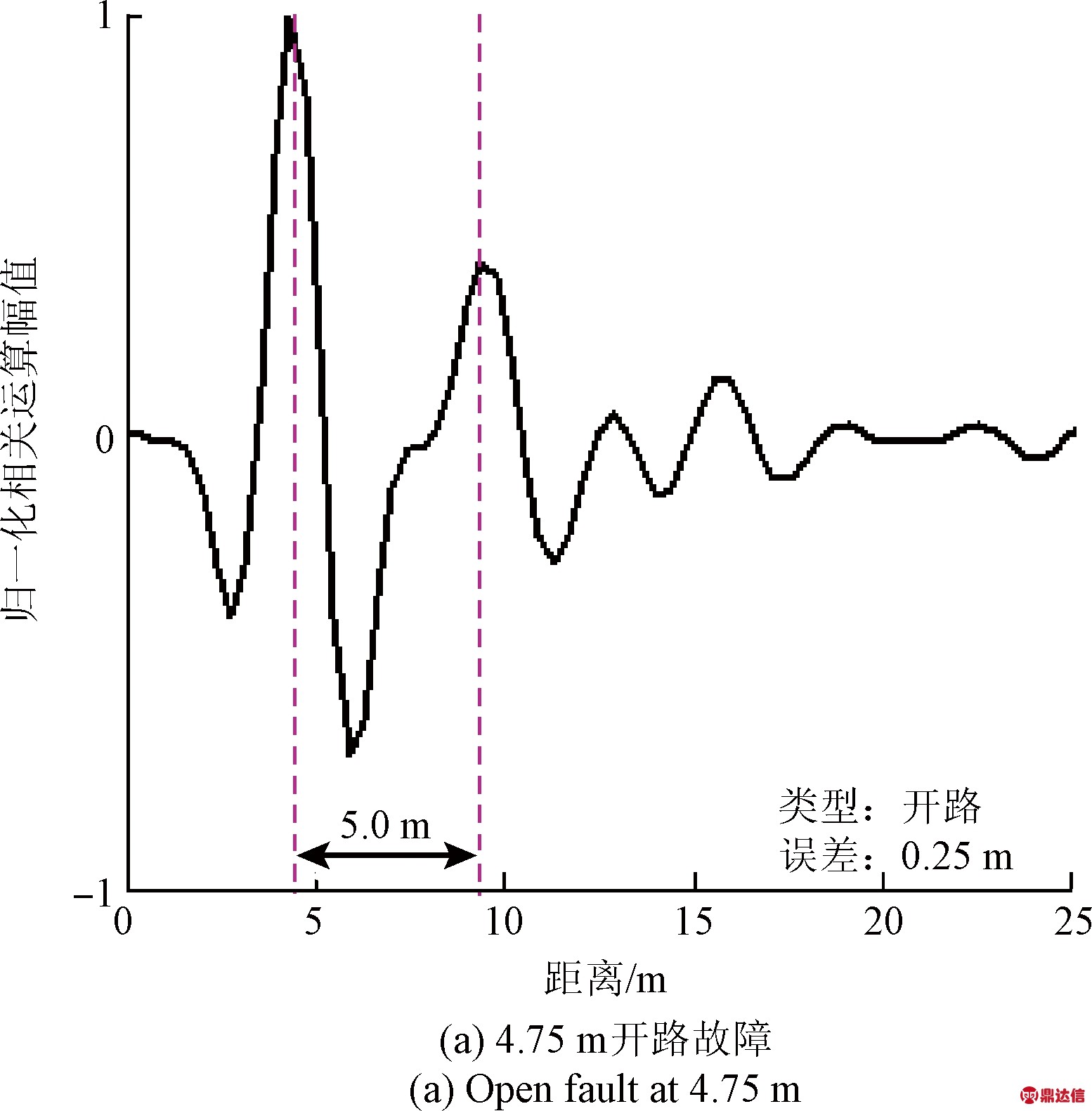
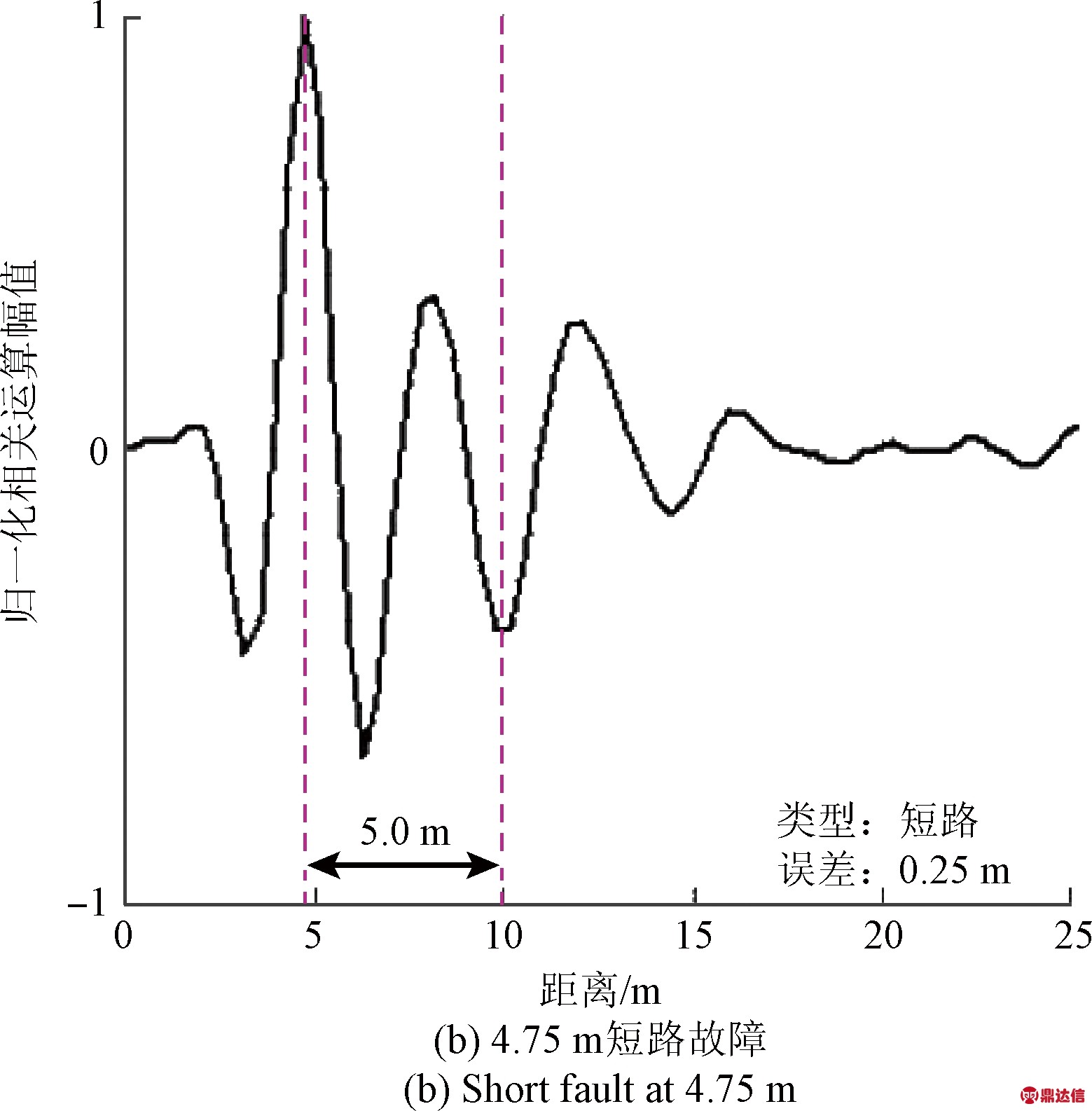
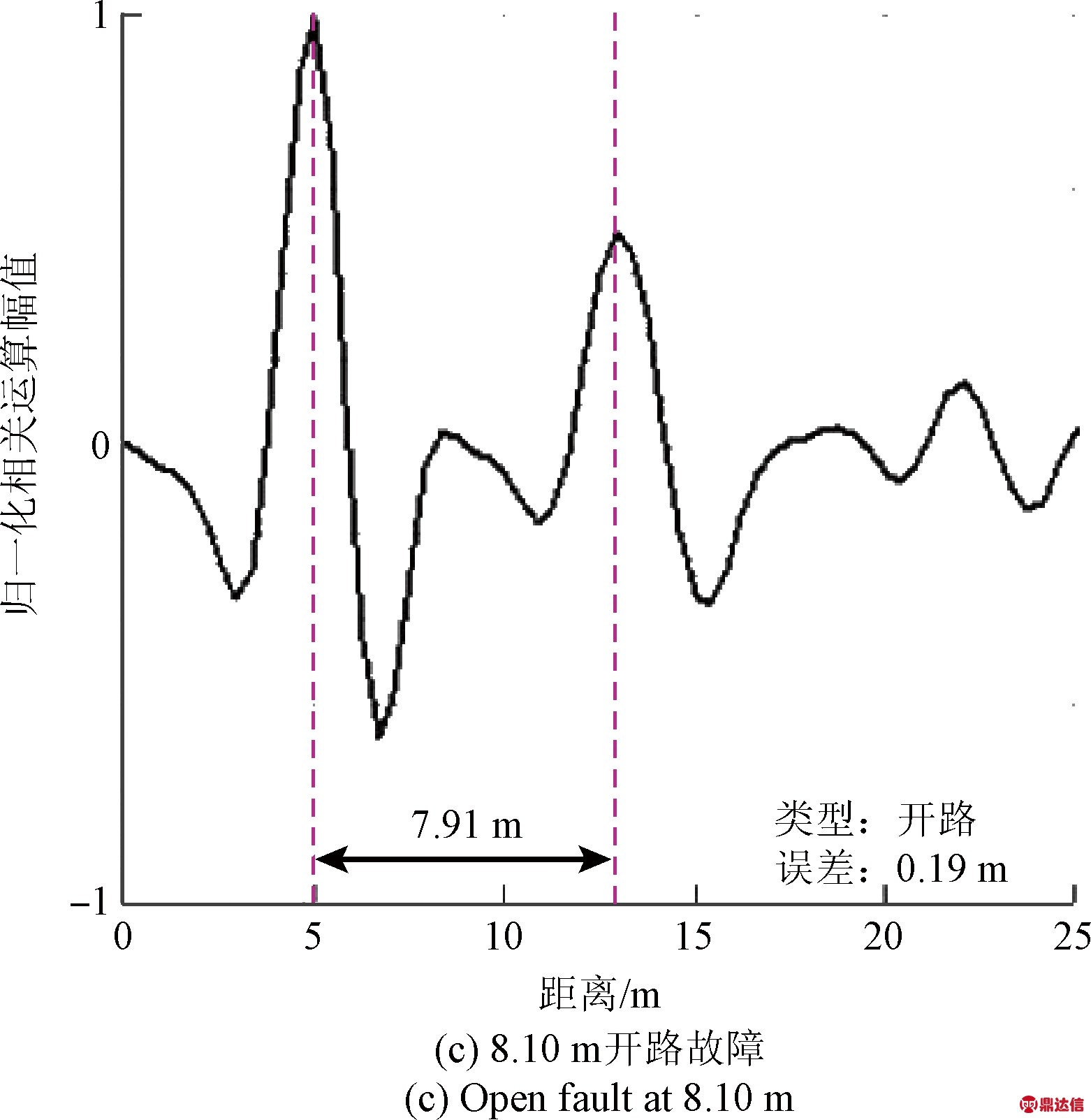
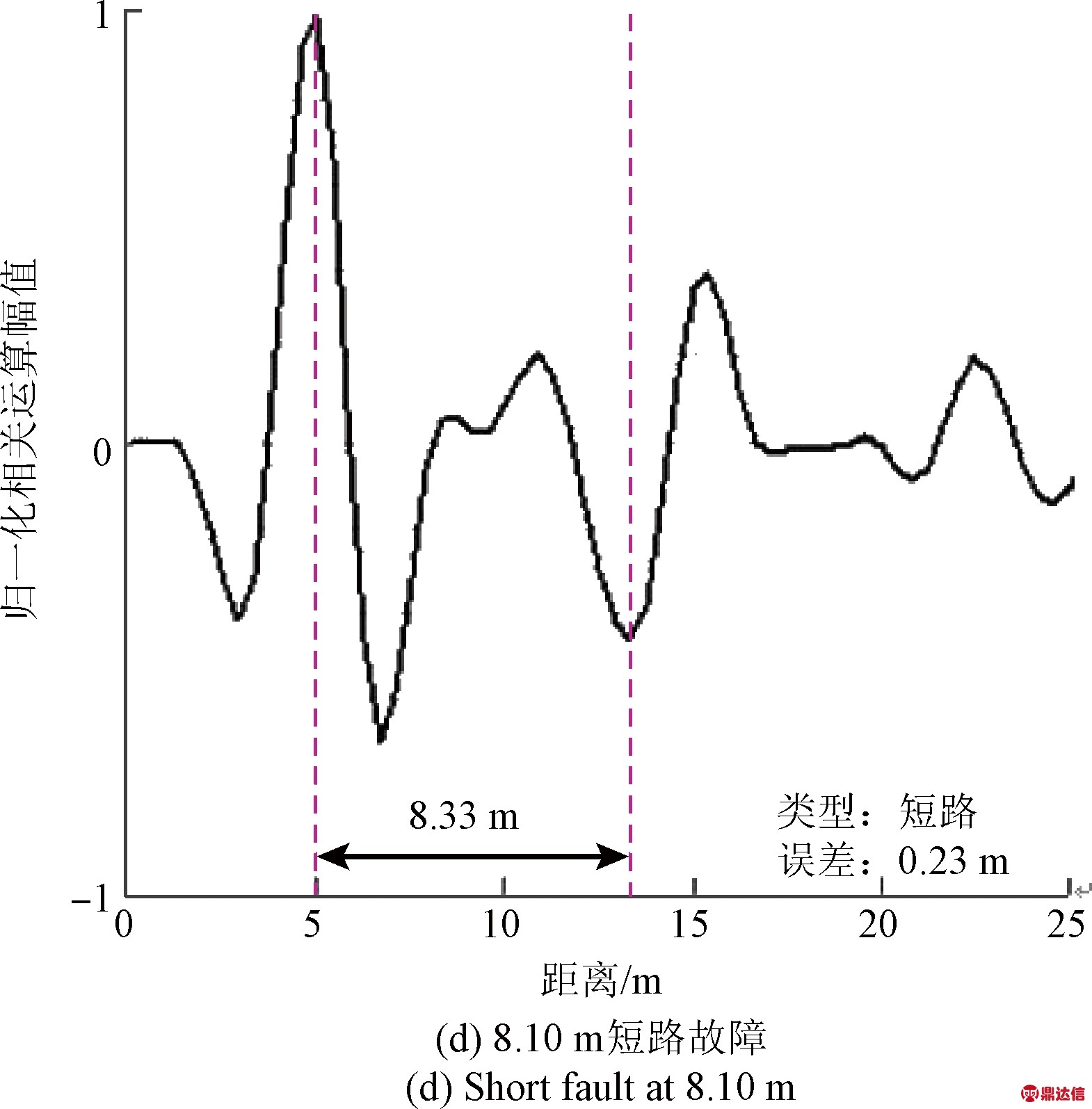
图13 感性非接触式电缆故障诊断实验验证
Fig.13 Experiment verification diagram of inductive non-contact cable fault diagnosis
根据实验波形和统计表,可以得如下结论:1)采用感性非接触式耦合能实现电缆故障的检测与定位;2)非接触式下其检测率依旧较高,最低93%,定位误差在理论误差范围内;3)非接触耦合下相关反射波头幅值在0.4~0.5,与理论推导及仿真值较为接近,此处4.75 m处反射波头幅值低于8.10 m处存在检测的偶然性,在线诊断下受一定的环境噪声影响。统计结果表明感性非接触式电缆故障在线诊断方法的可行性。
表4 故障检测统计表
Table 4 Statistical table of the detection results under different fault distance conditions
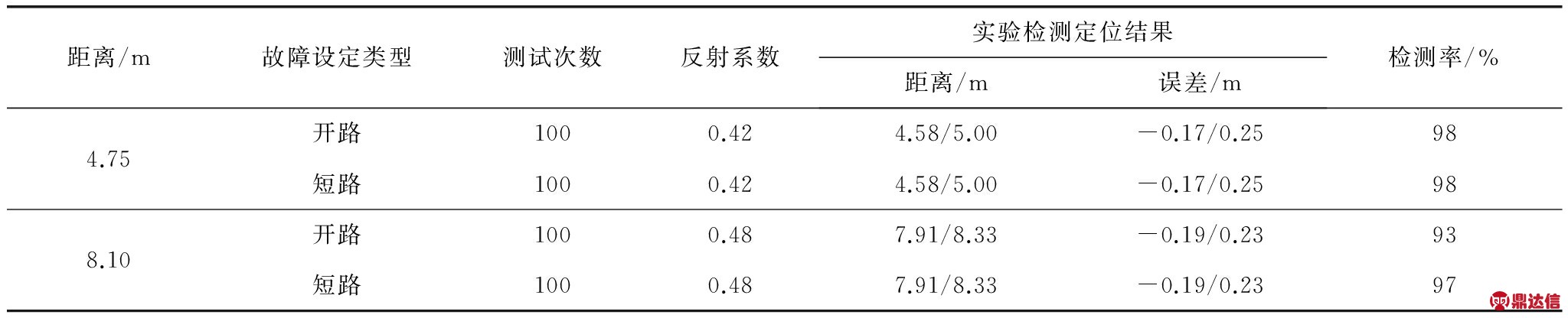
6 结 论
本文提出了采用感性耦合方法实现非接触式电缆故障在线诊断。通过理论分析、仿真和实验研究得出如下结论。
1)感性非接触耦合中耦合器互感值需大于等于一定阈值(1 μH),且需要具备良好的宽频检测信号耦合能力。在这两个条件下,根据故障点反射系数理论推导,如式(28)~(30)所示,只需保证考虑感性耦合器寄生参数值后,故障点反射系数值大于等于0.375,则依旧能够实现在线诊断,清晰明了地反应故障信息。
2)相比于容性非接触式诊断,感性非接触式耦合衰减程度小于容性(0.485>0.13),且定位误差保持在理论误差(0.42 m)范围内,检测率在93%以上,综合其非接触诊断优势,其推广应用价值更高。
由于文献[18]研究的容性非接触耦合方式基于实际加工设计的非接触电容,因此无法在同等条件下对其进行实验对比研究,且文献[18]只给出了非接触诊断实验验证波形,并没有给出具体的数据统计结果,对两种方式的详细对比研究难度较大。因此本文只在4.2及5.1小节对其衰减特性进行了理论和仿真对比,突出了感性耦合相对于容性耦合的优势。通过实验验证结果表明感性耦合方法检测率较高。当然,基于SSTDR电缆故障检测定位原理,当故障检测精度要求越来越高,检测信号频率越来越大时,感性耦合器磁饱和问题也将越来越严重,当达到一定程度时,感性耦合方法将不再适用。