摘要 高弹联轴器橡胶件的温度分布将影响其自身寿命和轴系运行的可靠性。结合传热学和有限元解耦理论,分析得到动态扭转载荷作用下橡胶件的温度场分布变化过程和温度变化曲线。开展动态热机械分析,根据得到的损耗因子随温度的变化关系在温度场计算中进行损耗分析迭代。利用扭转振动试验台开展了橡胶件温度分布测试试验,对比了将损耗因子作为定值和考虑损耗因子温度相关性的两种计算方法与实测数值的误差,验证了有限元数值模拟方法的有效性。研究表明,考虑损耗因子温度相关性的计算方法计算精度更高,进一步分析可得到高弹联轴器的许用扰动转矩,为联轴器以及轴系的性能监测和高弹联轴器的设计优化提供理论依据。
关键词 高弹联轴器 瞬态温度场 温度场试验 损耗因子 许用振动转矩
0 引言
高弹联轴器因其突出的位移补偿能力和对轴系扭转振动特性的调节能力在传动系统中得到广泛应用。橡胶件作为弹性元件是高弹联轴器中最重要的部件,由于其自身的阻尼特性,在实际运行中会产生大量的热功耗,这在大型高弹联轴器中尤为严重。橡胶件温度过高会影响试件性能使试件出现损伤,更是轴系运行存在隐患的表征[1-2]。由于橡胶的热传导性能低,橡胶件本体从开始启动到温度场达到平衡是一个缓慢的升温过程,通过瞬态分析能够更好的了解高弹联轴器在工作过程中的动态特性,而分析结果可反映高弹联轴器工作时的真实状态[3-4]。Clark[5]、Whicker[6]最早提出“解耦”的分析思想,该方法主要是独立求解应力应变场和温度场这两个边值问题,并通过温度迭代来涉及它们的互相影响。吴福麒[7]根据此思想,对滚动轮胎的温度场和转鼓试验进行研究,其测试结果和计算结果较一致,表明采用该方法是可行的;顾智超[8]假定每个单元生热率相同,采用Abaqus分析某款高弹性联轴器橡胶元件在不同工况下温度场的分布情况;张连凯[9]利用摩擦学、传热学、黏弹力学等理论,研究塑料合金联轴器摩擦热流密度以及黏弹性损耗生热率,获得该联轴器的稳态温度场。
前人对于橡胶材料的温度场研究已经很深入,但对于弹性联轴器橡胶件的三维瞬态温度场研究少见提及,且大多研究中没有考虑温度对橡胶材料黏弹损耗特性的影响。本文中将有限元计算与温度场试验相结合,系统研究了高弹联轴器橡胶件温度场随时间的变化过程。在此基础上分析得到不同转速下高弹联轴器的许用扰动转矩,为联轴器以及轴系的性能监测和联轴器的设计优化提供理论依据。
1 分析原理
1.1 建立模型
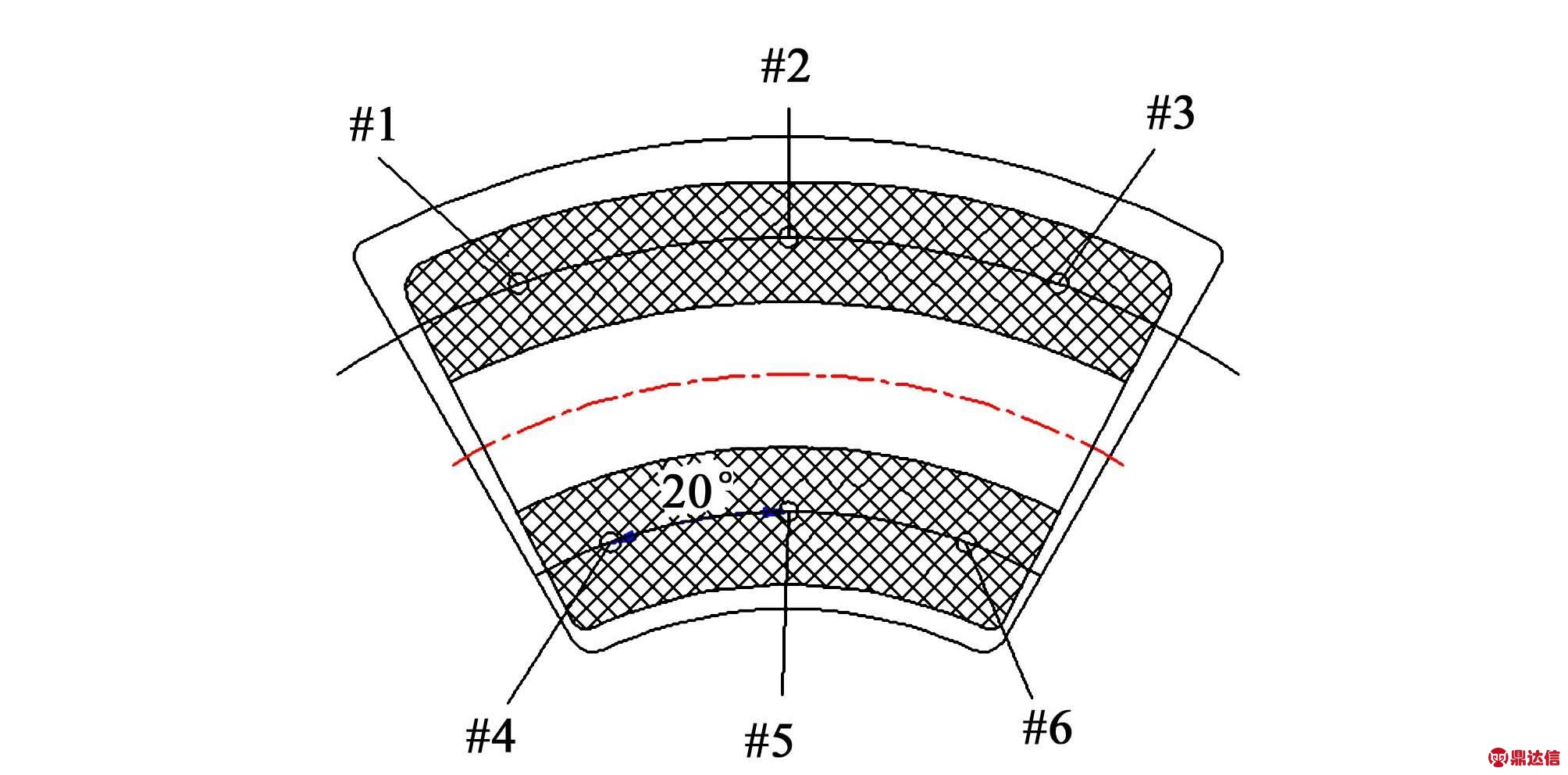
图1 高弹联轴器1/6模型
一个周期过程中各扇形橡胶块受载历程完全相同,为了提高计算效率,建模时取其中一个扇形橡胶块为研究对象。内径为280 mm,外径为560 mm,左右两端为钢制法兰,中间为弹性元件。在SolidWorks中建立三维简化模型,忽略膜片、螺栓、过度盘等结构不仅能够突出研究目标,而且节省计算量。在Hypermesh中划分网格如图1所示,网格数量为47 588,节点数量为55 425。高弹联轴器各部件的材料参数如表1所示。
表1 材料参数
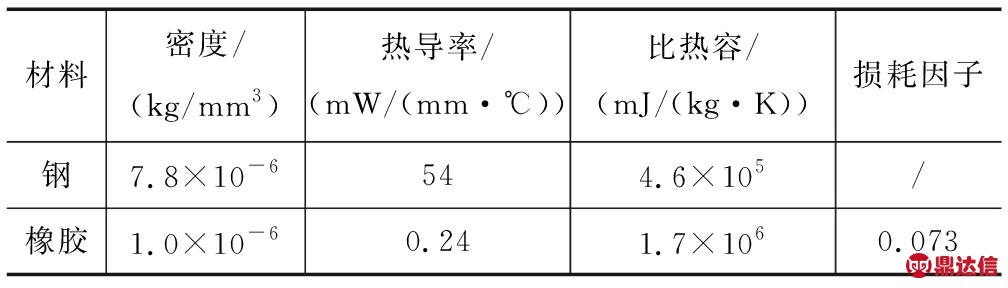
1.2 变形分析
在变形分析中,不同的材料和加载情况使用不同的本构模型计算应力应变关系,如Mooney-Rivlin模型、Yeoh模型[10]。本文中通过对橡胶材料进行单轴拉伸、双轴拉伸、平面拉伸试验,将所得试验数据利用Abaqus的材料评估功能拟合,选取Mooley-Rivlin为橡胶材料的超弹本构模型(C1=0.151,C2=0.166)。Mooney-Rivlin的应变能密度函数为
W=W(I1,I2)=C1(I1-3)+C2(I2-3)
(1)

(2)
式中,λi为主伸长比,λi=εi+1;εi为主轴方向的应变;C1和C2为材料常数;I1和I2分别为第一、第二基本不变量。
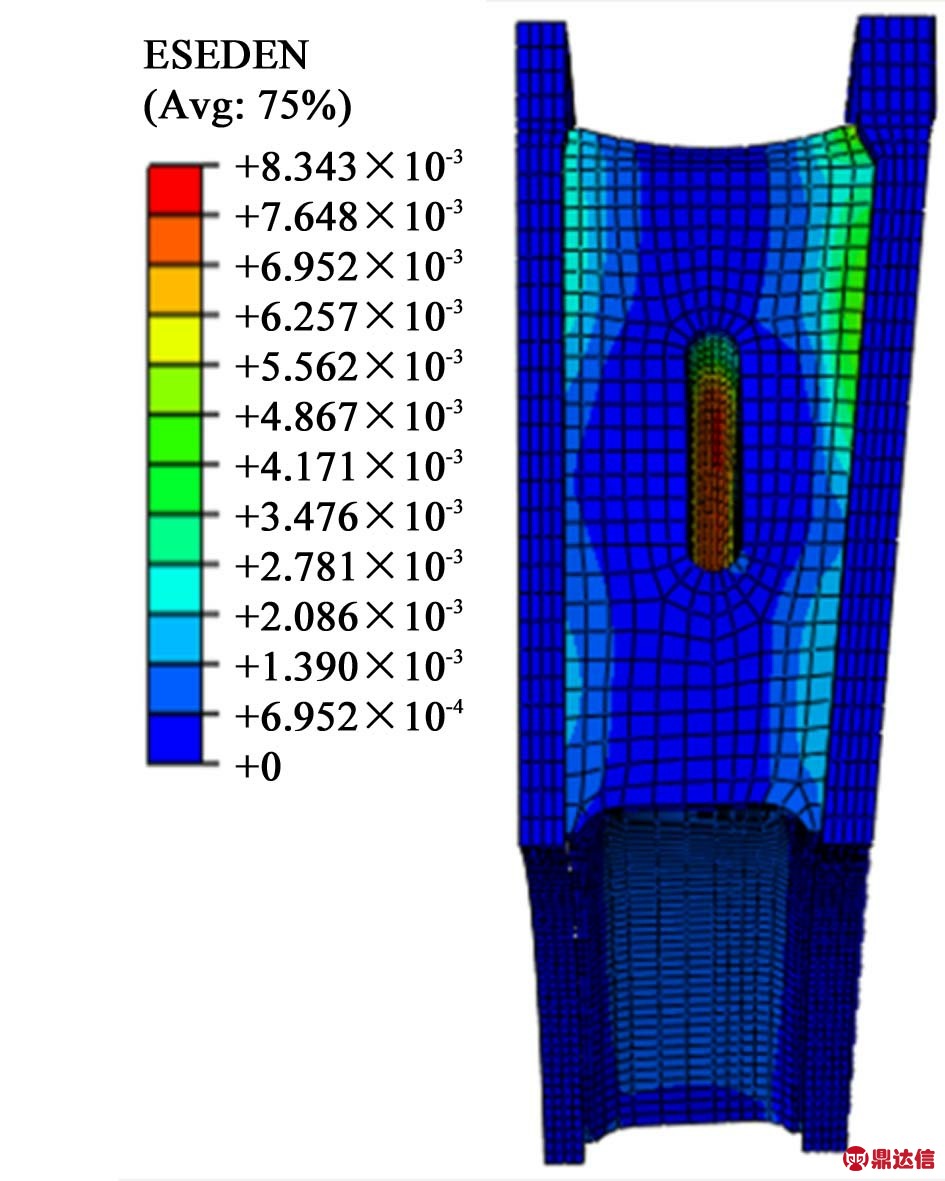
图2 单元应变能密度
在Abaqus中进行变形分析,设定联轴器在振动转矩2 kN·m、加载频率5 Hz的工况下运行,分析得到的单元应变能密度如图2所示。在大变形情况下,散热孔的上下端形状会变得尖锐,此处易产生裂纹,同时也是单元应变能密度最大的地方。这与T Pottier[11]、JRS Martinez[12]发现热源密度在裂纹尖端附近最高相符合。
1.3 损耗计算
橡胶材料的黏弹特性在力学上的表现就是应变滞后于应力,遂形成椭圆形的滞迟曲线,被封闭曲线包围的面积表示材料在承受交变的应力和应变过程中损耗的能量。这部分能量最终转变为热能,以热量的形式释放出来。
为了讨论材料的能量耗散问题,首先讨论外部作用产生的变形功。单位体积的能量为
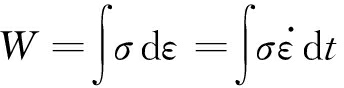
(3)
式中,σ为应力;ε为应变。
设弹性体受周期应变作用:ε(t)=ε0eiωt,则应力响应为

(4)
式中,Ε*为复弹性模量;E1为储能模量;E2为损耗模量。
损耗模量与储能模量之比为
=β=tan δ
(5)
式中,β为黏弹材料的损耗因子;δ为应变落后于应力的滞后角。
一个循环周期内单位体积的功为
W= ∮dw=∮σ(t)dε(t)=+
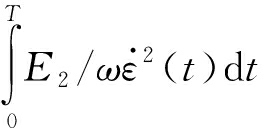
(6)
等式右边第一项表示每个循环橡胶材料的单元应变能密度,第二项表示一个振动周期中的能量损耗,可用来计算损耗生热。
阻尼材料持续经历周期性应变ε(t)=ε0cos ωt的作用,单位体积能量损耗为
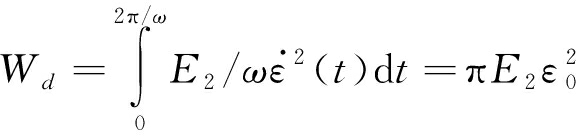
(7)
单位时间内单位体积橡胶由于机械滞后损耗转换而成的热量,用生热率来描述。满足条件

(8)
需要注意的是,这里得到的是每个单元的生热率,结合节点等效法,可计算每个节点的生热率[13]。
1.4 热传导分析
联轴器热边界条件的表征包括热导热、热对流以及热辐射三种方式。其中,导热是最主要的传热方式,而辐射换热的影响可以忽略不计。
根据傅里叶定律和能量守恒定律,三维非稳态导热微分方程的一般形式为

(9)
式中,及t分别为微元体的密度、比热容、导热率、单位体积中内热源的生热及温度。而式(9)求解的关键归结为内部热源
以及联轴器热边界条件的确定。由于橡胶块的黏弹性损耗是其主要的内热源,因此在温度场分析中只需对橡胶材料进行生热率赋值,即将式(9)中
用损耗分析得到的节点生热率代替即可。
在Hypermesh中设置单元类型为solid70,以.cdb格式输出到ANSYS中进行热分析。借助APDL语句,给每个节点赋值相应的节点生热率作为温度场分析的热载荷。
根据Mc Allen[14]旋转圆盘表面换热的试验结果来确定联轴器表面对流换热系数
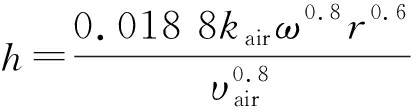
(10)
式中,kair为空气的导热系数;υair为空气的运动黏度;ω为橡胶件的旋转角速度;r为橡胶的径向坐标。
2 分析结果
2.1 高弹联轴器瞬态温度场分布
在ANASYS中进行瞬态热分析,振动转矩2 kN·m,加载频率5 Hz,环境温度25 ℃,图3的云图记录了弹性联轴器橡胶件从启动时刻开始至达到稳定工况温度场的变化过程。可以看出,在开始运行阶段,橡胶件的最高温度区域为散热孔的外圆端,即单元应变能密度最大的地方。随着时间的推移,最高温度区域逐渐向散热孔上部的橡胶件中间部位移动,6 000 s之后最高温度发生的部位基本不变。由于联轴器外圆侧承受较大转矩,橡胶件外圆面及中间散热孔与空气接触,橡胶件两侧与铁件接触,而橡胶自身的导热系数很低,导致热量在外圆侧的中间位置堆积。
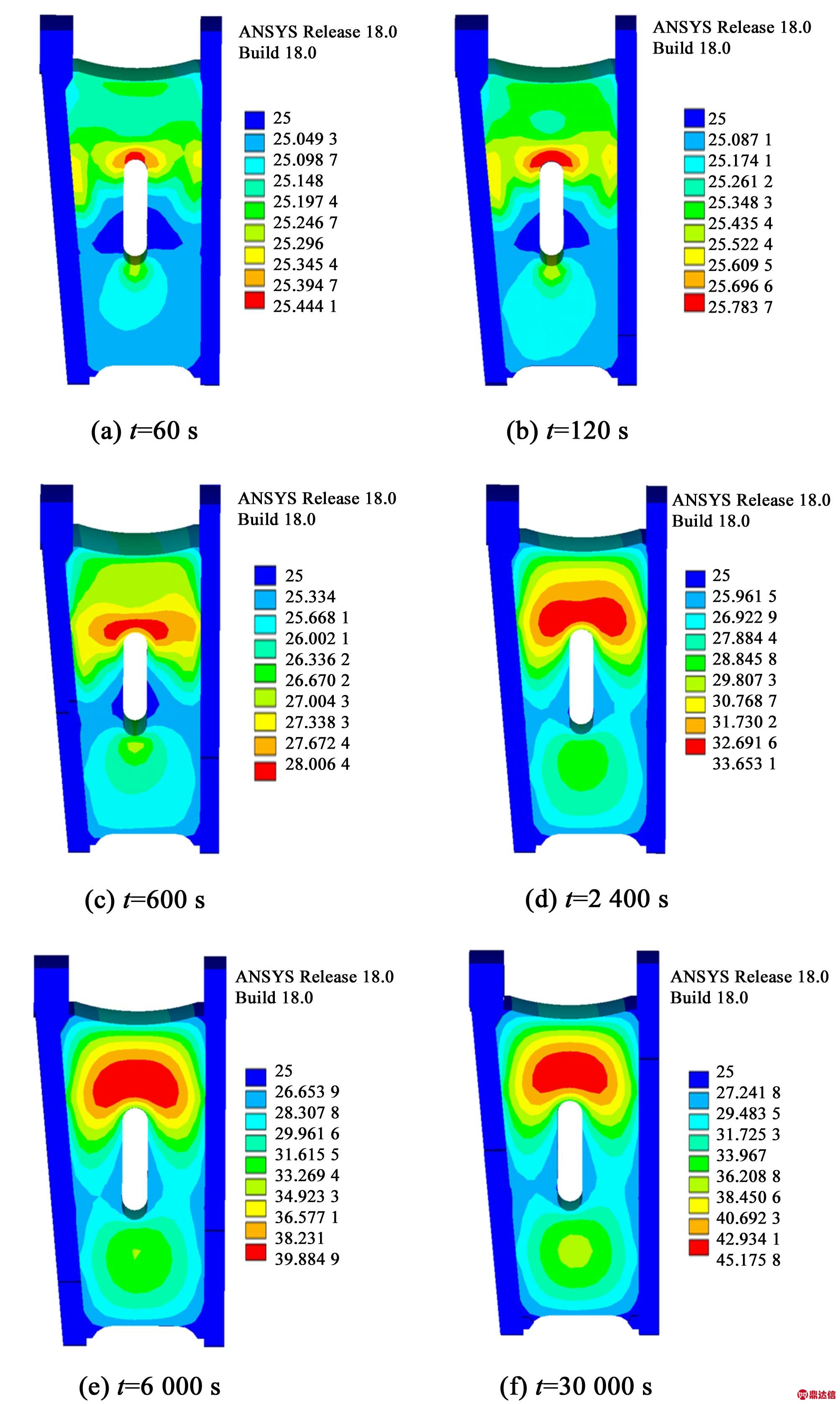
图3 温升过程中某时刻下的温度分布情况
2.2 损耗分析迭代
上文中分析得到的稳态温度场是将损耗因子作为一个常数计算得到的,这也是大多学者在温度场计算过程中采用的简化方法。而实际工况下,阻尼是随着温度的变化而变化的,即储能模量、损耗模量和损耗因子是随着温度的变化而变化的。为了能够精确地预测橡胶件的温升,须考虑橡胶材料黏弹损耗参数的温度相关性。
利用Netzsch DMA242C进行动态热机械分析,评估材料的储能模量、损耗模量和损耗因子等参数(图4)。样品尺寸为6.60 mm×1.95 mm×3.12 mm,温度范围为10~100 ℃,频率分别为1 Hz、2 Hz、5 Hz、10 Hz,振幅为30 μm,以3 ℃/min的递增速率进行温度扫频试验。研究发现在所测频率范围内频率对损耗因子影响不大,温度对损耗因子影响较大,测得的损耗因子随温度的变化曲线如图5所示。
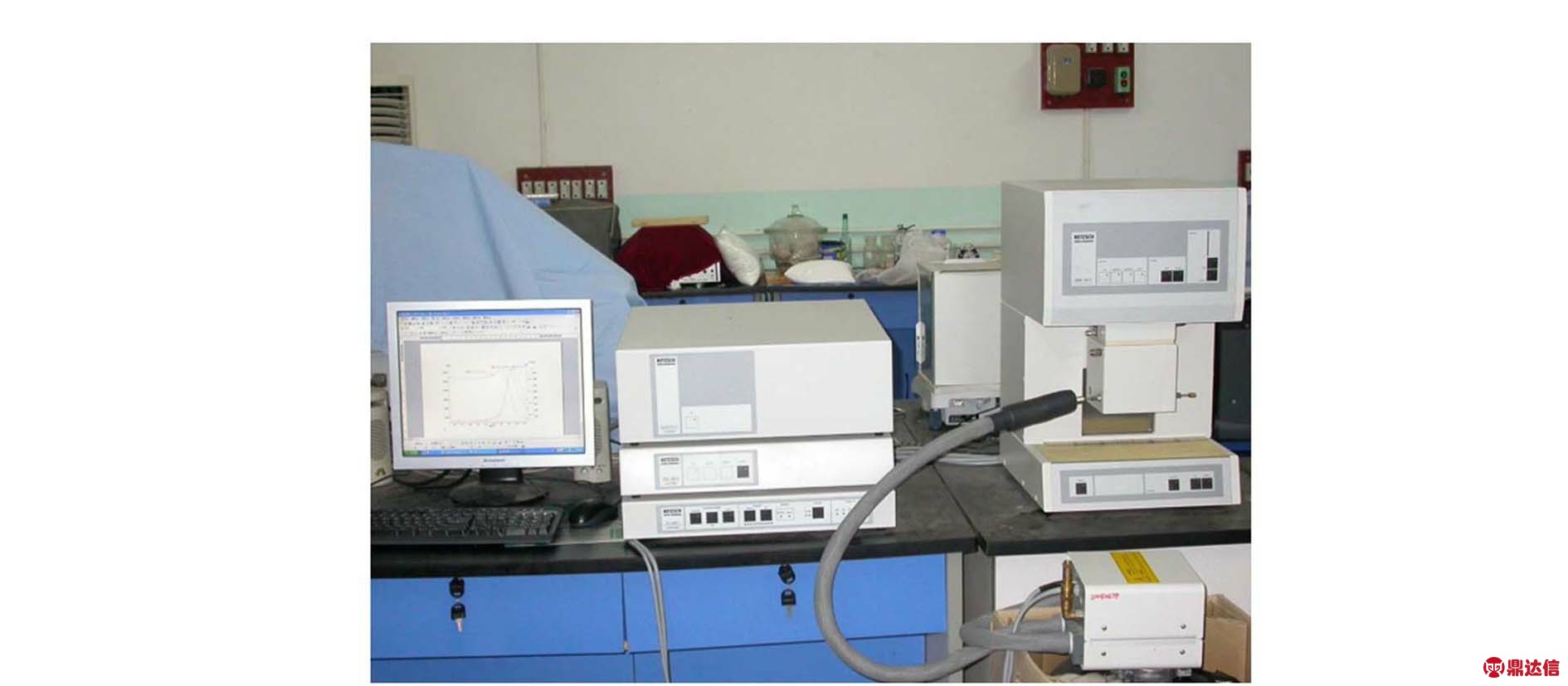
图4 动态热机械分析
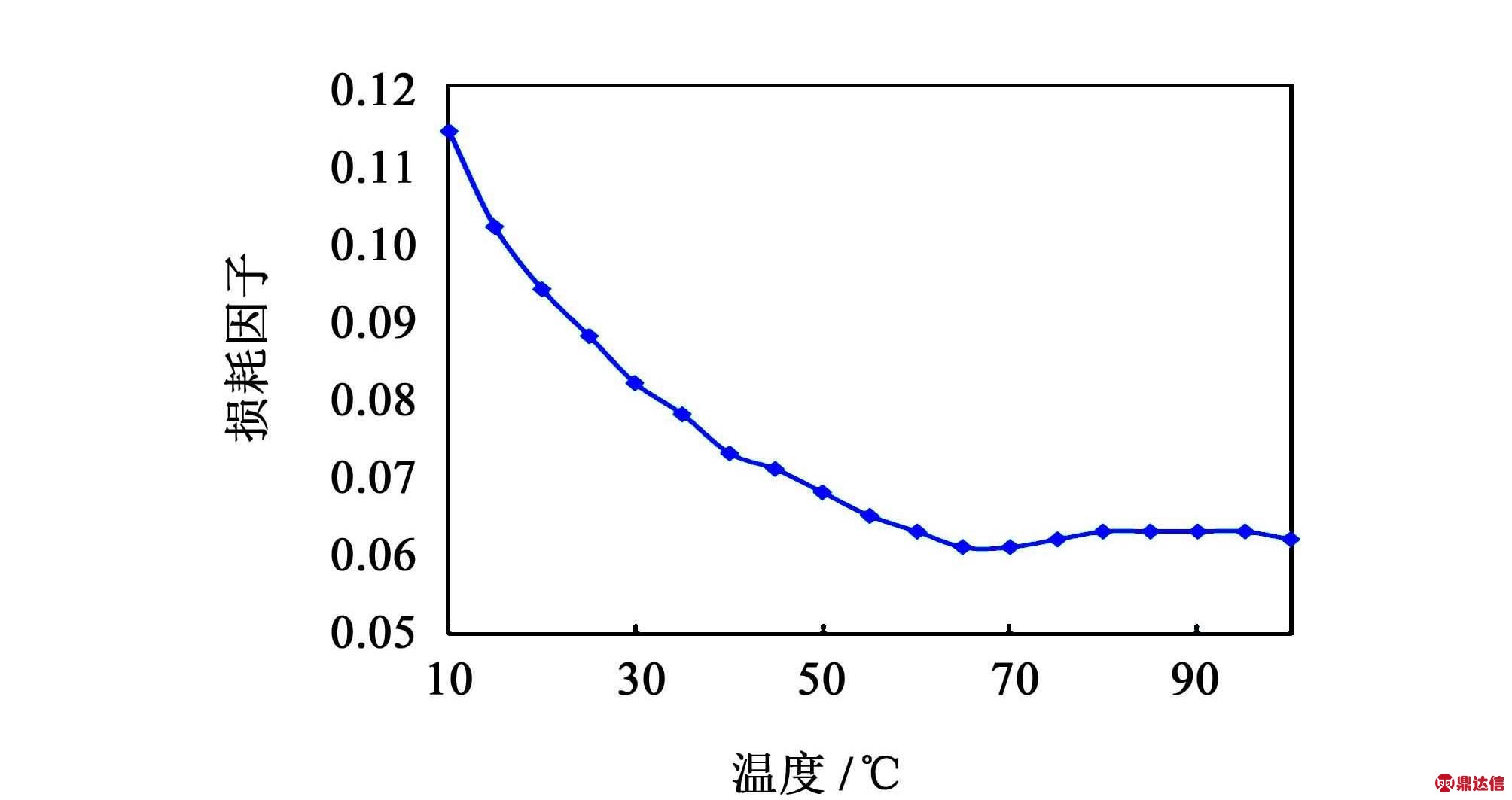
图5 损耗因子-温度曲线
基于损耗因子为定值时分析得到的温度场结果,提取各节点的温度信息,根据损耗因子-温度曲线重新计算各节点的生热率值,代入温度场仿真中进行损耗分析迭代,迭代前后温度的差值小于1 ℃即判定结果收敛。迭代前后的温度场信息将与试验结果展开对比。
3 试验与应用
3.1 试验准备
图6为高弹联轴器橡胶件轴向中间位置的剖面图,在散热孔外侧和内侧橡胶件上按图6所示位置预钻孔。在预钻孔位置分别装入直径为1 mm,测量端长度为50~57 mm的WRNK—191型铠装热电偶。其中,1、2、3为外圆侧测点,4、5、6为内圆侧测点,测点与测点之间相隔20°。
3.2 试验方案
将两件橡胶件安装到w+b 80 kN·m动态试验机上,对试验件预加载36 kN·m静态力矩,再分别施加5 Hz、10 Hz的正弦信号动态激励,施加的变动转矩幅值为4 kNm。由于橡胶件温升较慢,设定温度监控装置每隔30~40 s采集一次数据。当橡胶件各测点在60 min内温升小于1 ℃时,认定橡胶件已到达热平衡状态。试验过程记录如图7所示。
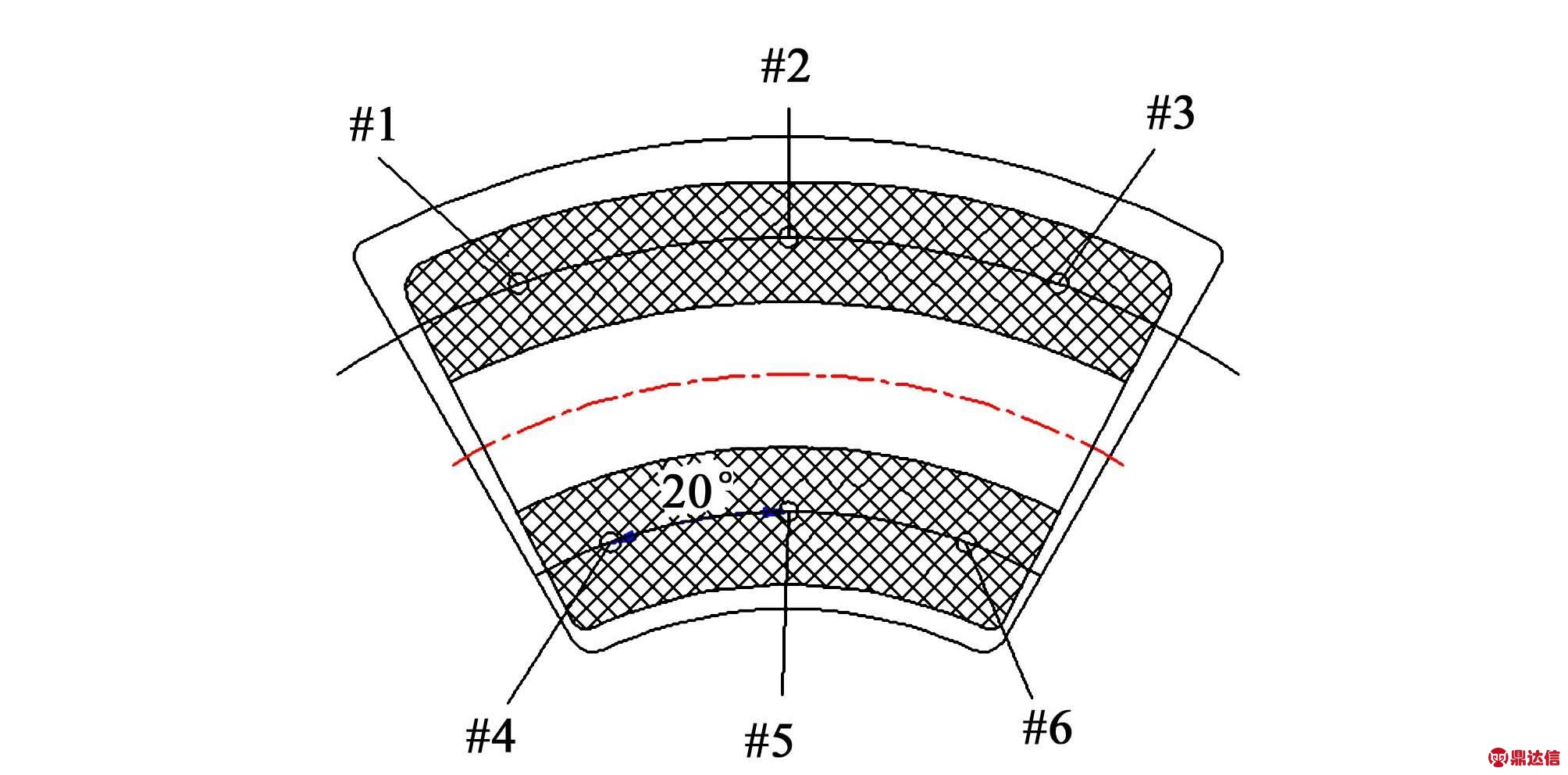
图6 橡胶件测点分布图
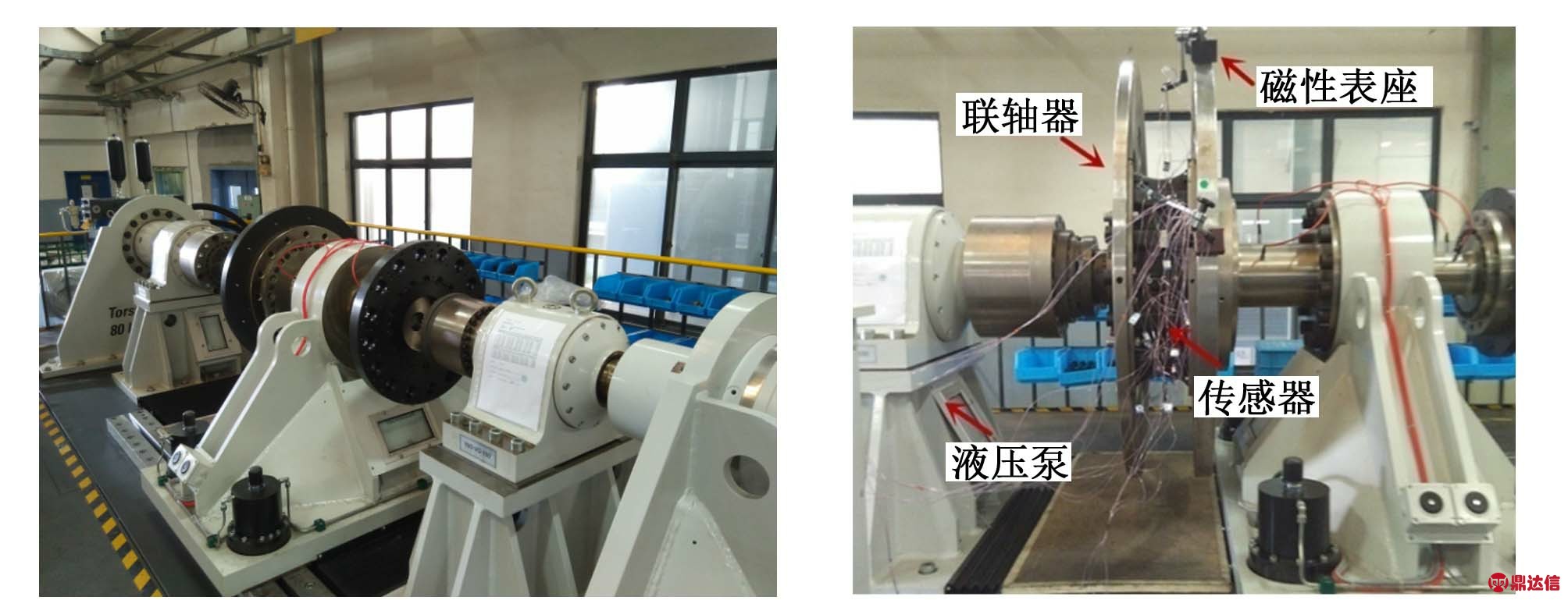
图7 橡胶件温度场试验
3.3 测试结果比较
根据热电偶在橡胶件中的位置,在有限元计算模型中找到相对应的节点,比较仿真数据和实测数据两者的误差。试验频率分别为5 Hz和10 Hz时,2号和5号测点温度随时间变化曲线如图8所示,其中,方法1是假定损耗因子为定值时的瞬态分析结果;方法2是根据图5考虑了损耗因子温度相关性的瞬态分析结果。
由图8可以发现,测点温度在前5 000 s呈近似线性升高,5 000~12 000 s 温度升高趋势放缓,12 000 s之后温升的变化率越来越小,在30 000 s之后温度基本达到稳定。从整体温升趋势来看,数值模拟的温升速率比实测温升速率快,其中,方法2的温升曲线与实测温升曲线吻合度更高。在热平衡状态下,方法1的平均误差为6.6%,方法2的平均误差为3.7%,均低于10%。由于振动转矩和扰动频率是导致温升的主要原因,可以预见,振动转矩越大或扰动频率越高的工况下,考虑损耗因子温度相关性会使计算结果更精确。综上说明,本文中采用的瞬态温度场分析方法是切实可行的。建模中忽略了辐射换热的影响,橡胶材料的导热系数和比热容会随温度的变化而变化,持续高频的振荡使传感器出现松动是误差的主要原因。
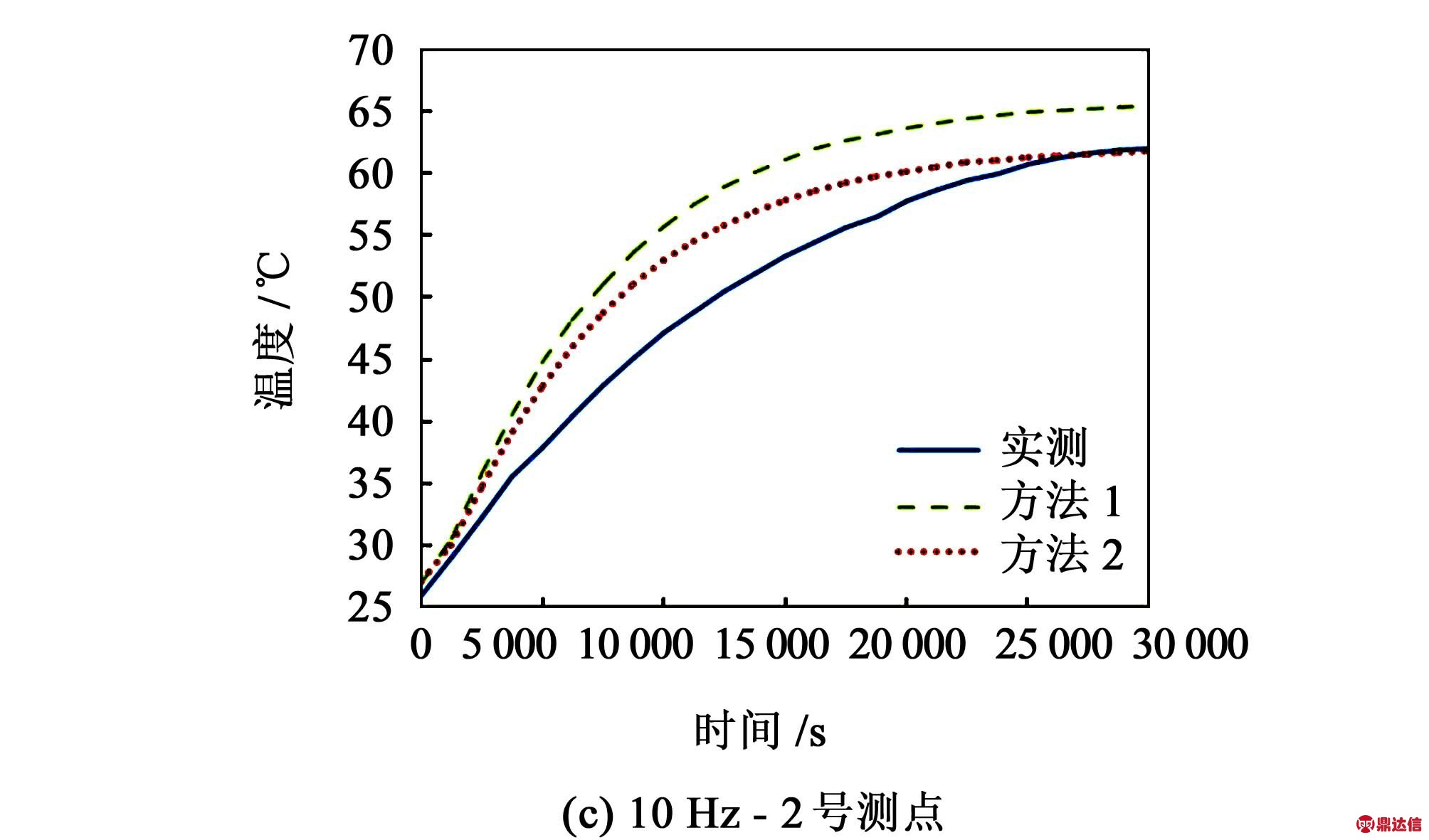
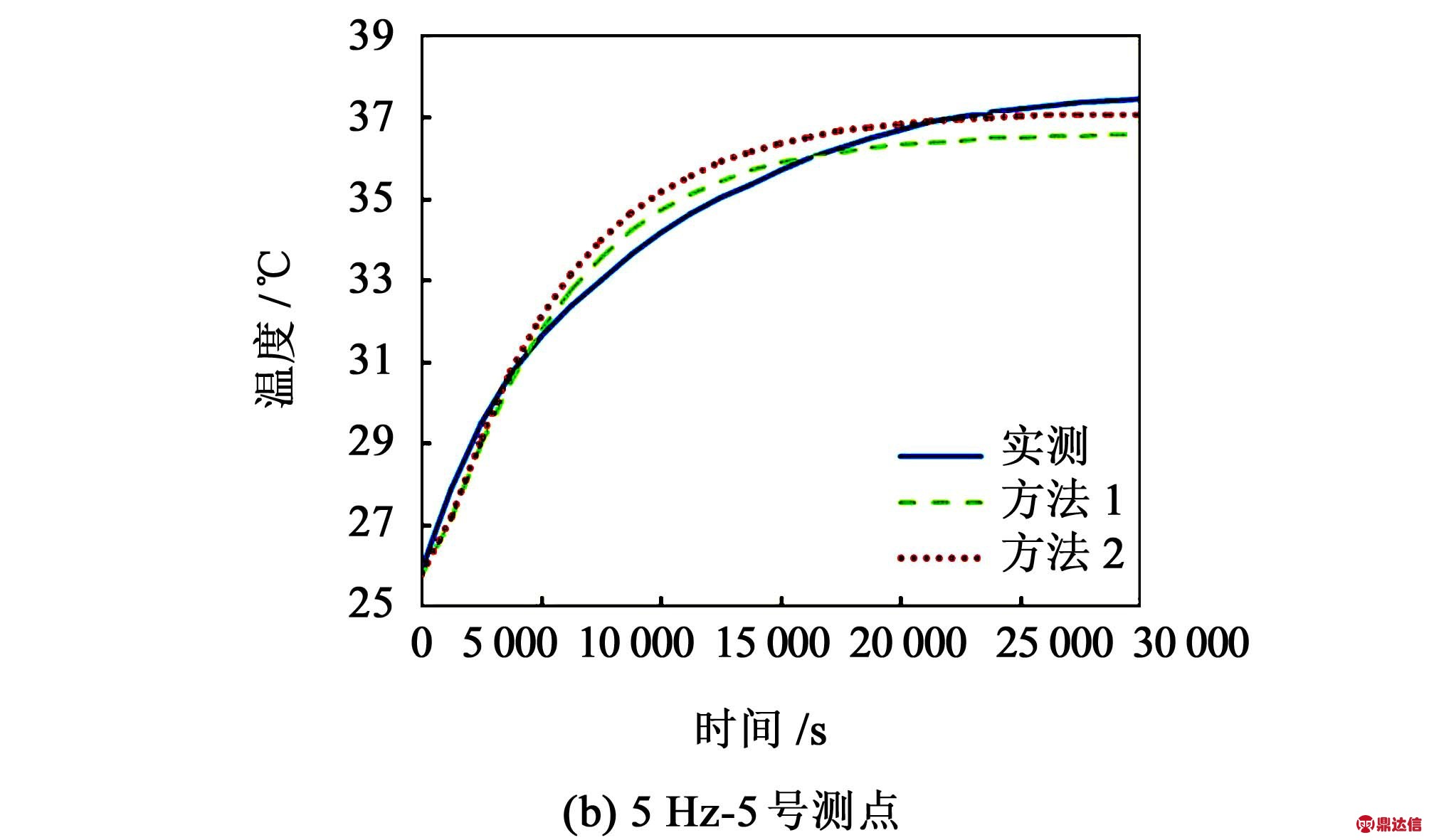
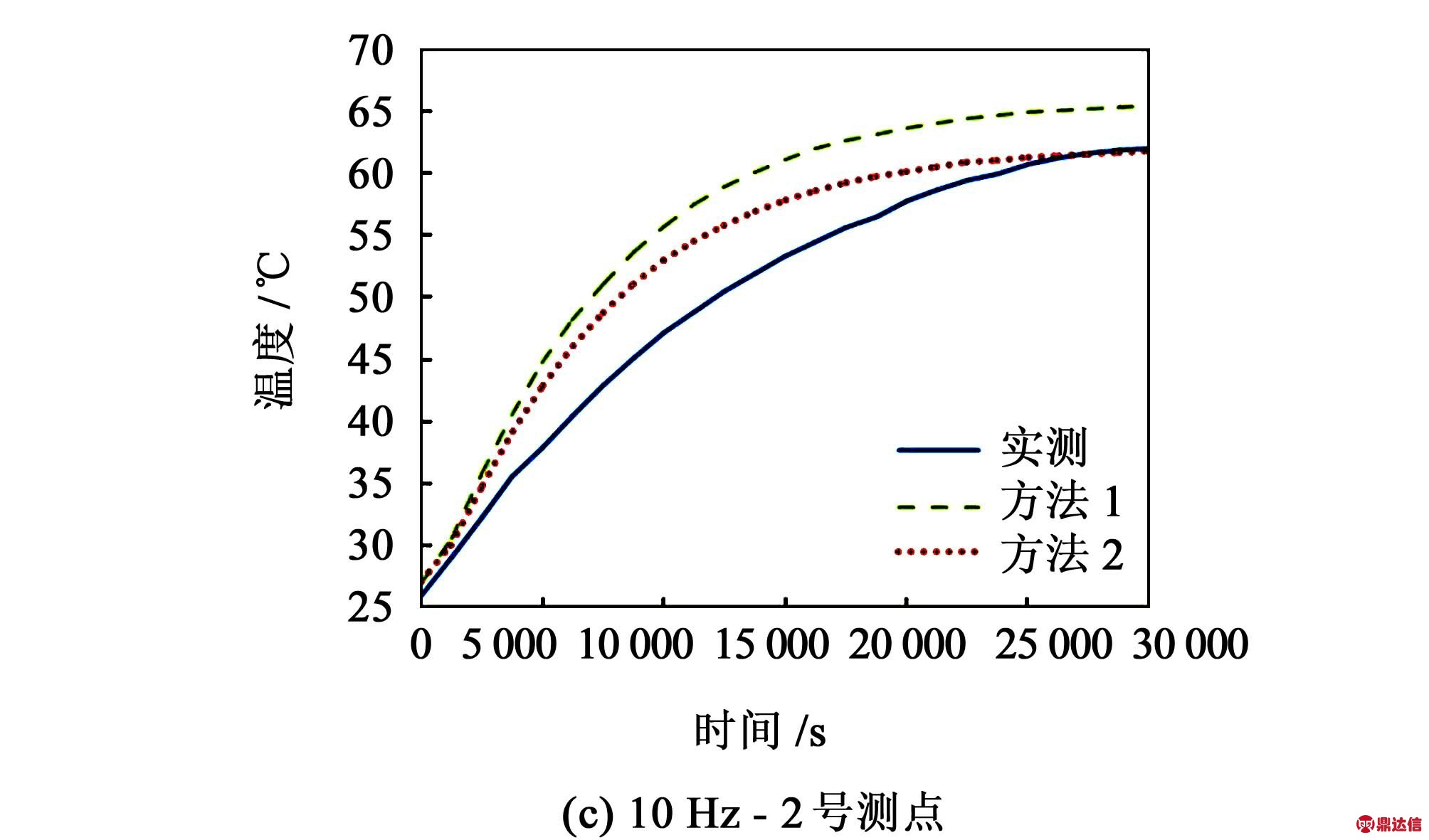
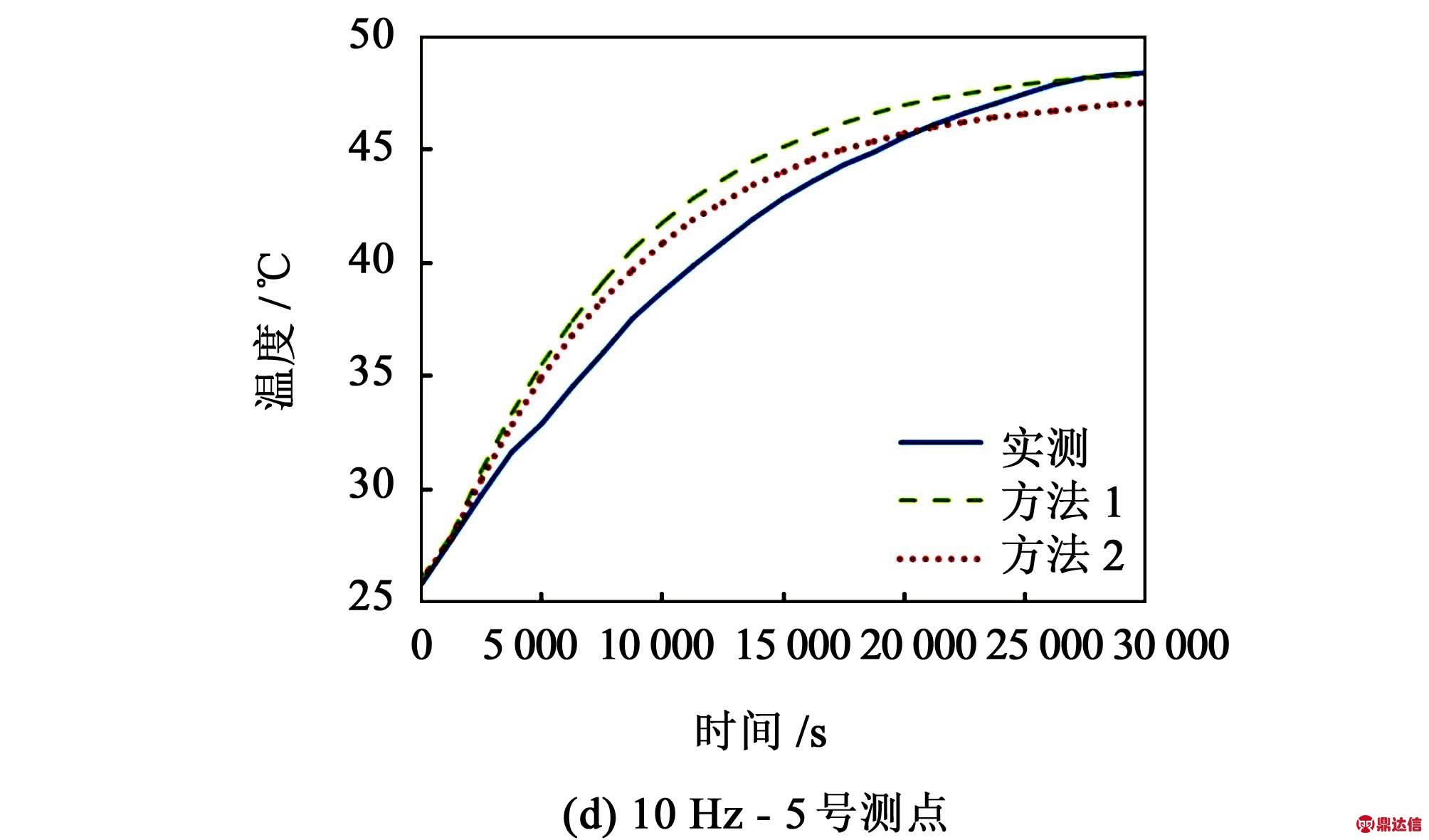
图8 测点温升曲线
3.4 不同转速下的许用振动转矩
随着转速的变化,旋转机械的工频会发生变化,当外部扰动力的频率与工频接近时会出现共振,影响轴系运行的平稳性,也会导致高弹联轴器橡胶件的温升从而出现安全隐患[15]。根据本文中建立的瞬态温度场分析方法,设定联轴器热平衡状态下最高温度达到110 ℃时的振动转矩为许用振动转矩,计算出此款高弹联轴器在不同转速下的许用振动转矩(图9)。
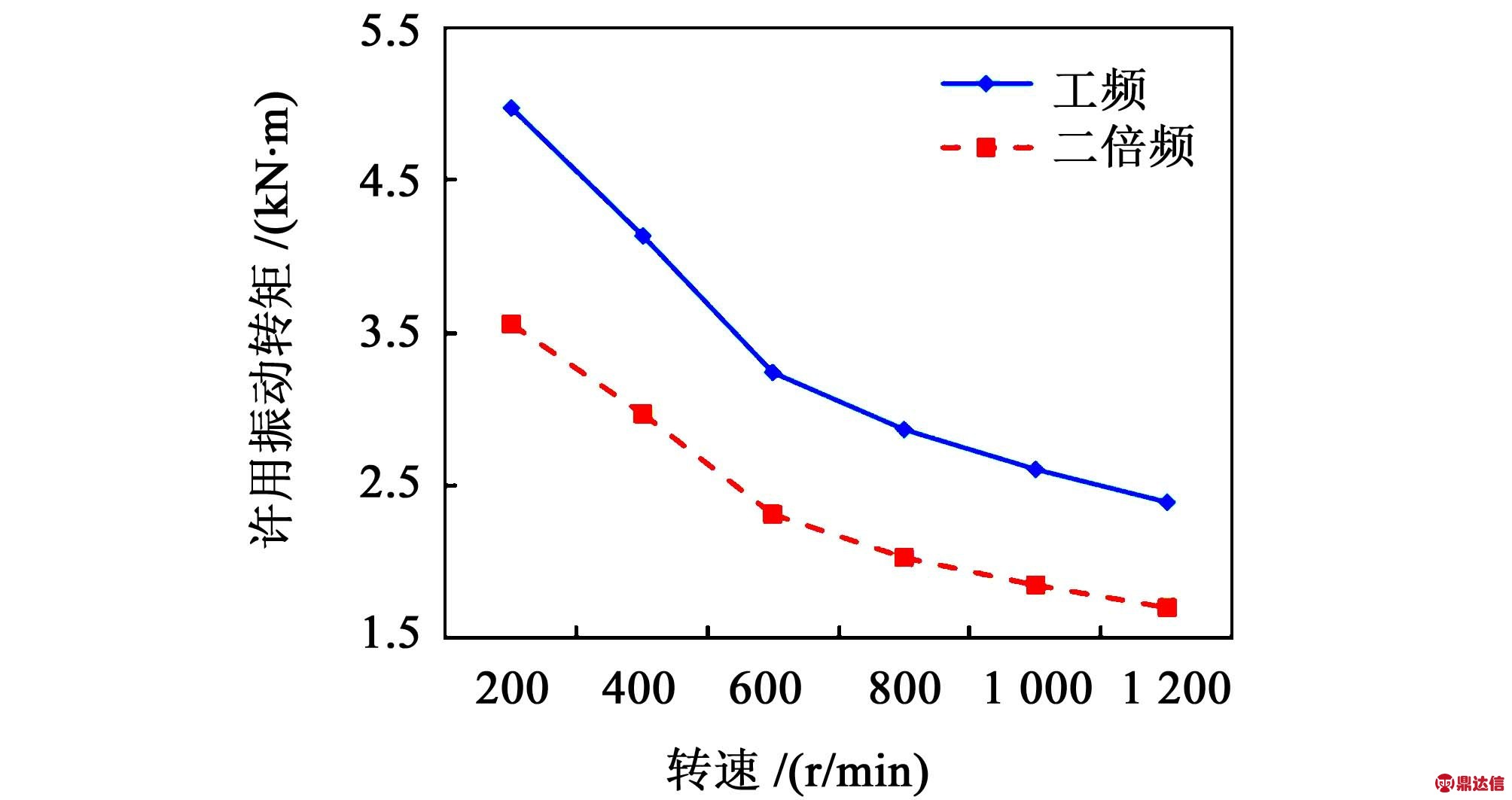
图9 不同转速下的许用振动转矩
可以看出,许用振动转矩随着转速的升高而降低,工频下的许用振动转矩比二倍频的高,两者间的许用振动转矩的差值也随着转速的增加而减小。可将此方法推向各款高弹联轴器,为高弹联轴器以及轴系的性能监测和高弹联轴器的设计优化提供理论依据。
4 结论
(1)采用试验与仿真相结合的方法分析得到,带有散热孔的高弹联轴器橡胶件的最高温度区域在开始运行阶段为散热孔的外圆端(单元应变能密度最大处),随着时间的推移,最高温度区域逐渐向散热孔外圆侧的橡胶件中间部位移动,一段时间后最高温度区域基本保持不变。
(2)建立的瞬态温度场计算方法得到的温升过程与实测温升过程基本一致。在振动转矩较大或扰动频率较高的工况下,考虑损耗因子温度相关性的温度场计算方法计算精度更高。
(3)随着转速的增加,弹性联轴器的许用振动转矩降低,工频下的许用振动转矩比倍频程的高,不同倍频程间的许用振动转矩的差值也随着转速的增加而减小。