摘要:为了探究激光焊接真空平板玻璃封接层气孔的产生机理,利用扫描电镜、自带能谱仪、X射线衍射仪和金相显微镜等手段,进行了真空平板玻璃激光侧边封接试验,研究了激光功率和焊接速率对封接层气孔的影响,分析气孔产生的原因。结果表明,真空平板玻璃封接层出现了数量较多、大小不一、相互不连通的孤立气孔,位于颗粒的交界处,主要是由焊料颗粒间的残余空气引起的;在焊接速率为2mm/s和离焦量为-2mm的条件下,过低或过高的激光功率都不利于减少封接层的气孔缺陷,激光功率为80W(能量密度为80J/mm2)时,封接层组织形貌好,封接层封接质量佳;在激光功率为80W和离焦量为-2mm的条件下,较低的焊接速率将有利于减少封接层的气孔缺陷,焊接速率为1mm/s(能量密度为160J/mm2)时,封接层组织形貌好,封接层封接质量佳。此研究可为真空平板玻璃的激光封接制造提供理论依据。
关键词:激光技术;激光焊接;真空平板玻璃;封接层;气孔
引 言
激光焊接具有能量密度高、热影响区及焊接热变形小、焊接效率高等特点,具有广泛的应用前景,被认为是21世纪最先进的焊接方法之一[1-3]。真空平板玻璃作为一种新型节能透明保温材料,具有隔热性能强、保温性能好、防结露和隔声性能优越等优点,已应用于建筑、蔬菜大棚、太阳能应用、冷冻运输等领域[4-7]。
真空平板玻璃在封接过程中封接层内部会产生不同程度的气孔,气孔的存在会使显微组织不致密,封接质量差。气孔少且分布均匀,封接层的密度和强度高;气孔多或分布不均匀,过度集中,容易造成应力集中,成为裂纹源扩展,降低平板玻璃的真空气密性、机械性能和使用寿命[8-14]。目前真空平板玻璃的封接技术有真空熔接法和激光焊接法[15]。本课题组已对真空熔接真空平板玻璃进行了系列研究[16-19],本文中将围绕真空平板玻璃激光焊接的气孔缺陷进行分析,通过研究激光功率和焊接速率对封接层气孔的影响规律,从气孔率、气孔尺寸方面阐明气孔产生的原因,探索消除气孔的工艺措施,提高真空平板玻璃的封接可靠性,旨在为真空平板玻璃激光封接制造提供理论依据。
1 实验材料与方法
1.1 实验材料
实验中选用的玻璃为20mm×20mm×4mm的普通钠钙玻璃,其主要成分见表1。
Table1 Chemical composition(mass fraction)of the common soda-lime glass

实验中所用的焊料为PbO-TiO2-SiO2-R x O y系统封接焊料,焊料的主要成分见表2。其制备工艺为:将99%纯度和平均粒度在30μm的 PbO、TiO2按70∶15的质量分数比均匀混合,然后向PbO/TiO2混合粉末中分别加入质量分数为0.10的纳米SiO2,质量分数小于0.025的CuO和质量分数小于0.025的Fe2O3配合粉末(纯度不小于99.8%,平均粒度不大于50nm),将混合粉末放入球磨机中,加入一定的松油醇作为分散剂,采用湿法球磨混合处理。具体参量为:球料质量比10∶1,转速250r/min,球磨4h,然后将其放入干燥箱中进行干燥处理,得到实验所需焊料。其粒度在1μm~25μm范围内,平均粒度为12.15μm。图1a所示为实验中所用玻璃和焊料,图1b为焊料扫描电镜(scanning electron microscope,SEM)图。
Table2 Chemical composition(mass fraction)of the sealing solder

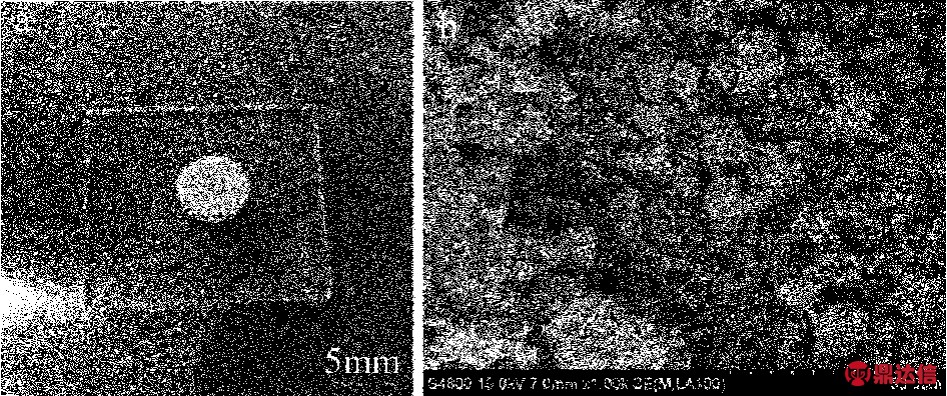
Fig.1 Experimental materials
a—glass and sealing solder b—SEM photo of the sealing solder
1.2 实验方法
焊接前,先用砂纸研磨玻璃的待焊接表面,使焊接面平整并具有一定的粗糙度,然后放在丙酮溶液中超声波清洗15min,除去表面的油渍等污垢。实验时,在一片洗净的平板玻璃上以一定间距放置支撑柱,并在玻璃四周涂覆封接焊料,然后再放另一片玻璃板,将两片玻璃板压合后在C-MAGHP4型数显加热板上预热,预热温度为220℃,预热时间为10min,然后采用YLS-2000-CT型光纤激光器在真空环境下进行激光封接,光斑直径为0.5mm。试验中采用的激光工艺参量见表3。激光输入能量是用激光能量密度去衡量的,数值计算公式为 E=P/(Dv)[20],其中 E为激光能量密度,P为激光功率,D为激光光斑直径,v为焊接速率。
Table3 Laser process parameters
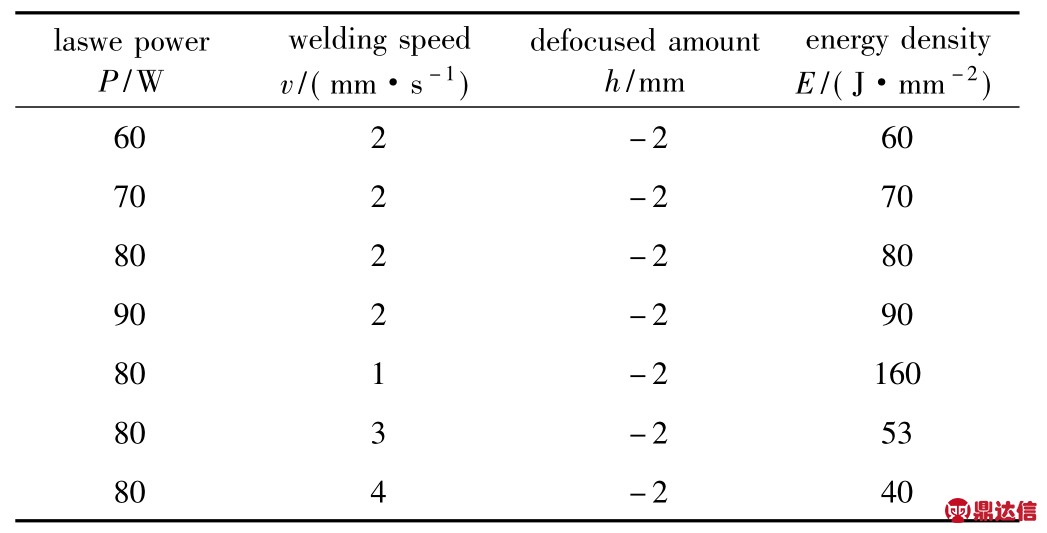
焊后在试样的两片玻璃中部沿平行于焊接方向切取横向截面,经打磨、抛光后采用Zeiss_Supra55型场发射扫描电镜及其自带能谱仪(energy duspersive spectroscopy,EDS)进行封接层的微观形貌分析和能谱测试,采用D8-Advance多晶X射线衍射仪(X-ray diffractometer,XRD)对封接层进行物相分析,采用BX41MLED型金相显微镜下观察气孔和分布特征。采用Image J软件对金相照片处理后测量计算气孔率、气孔数目及其直径尺寸d(见图2),其中气孔率p r为气孔面积A p与焊缝上表面面积A w的百分比,即p r=A p/A w×100%。图2中,d1和d2为过气孔圆心相互垂直的两条直径。
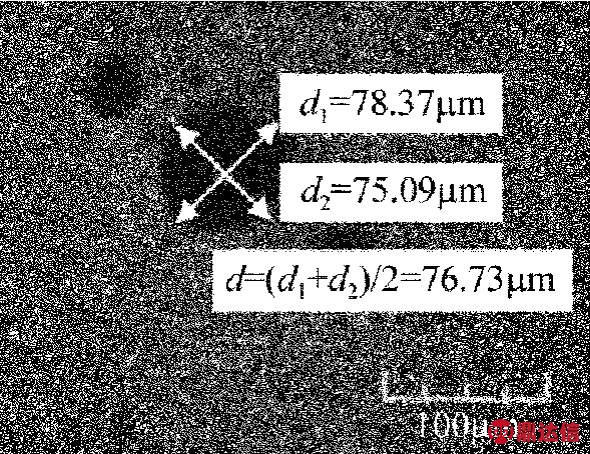
Fig.2 Calculation of the diameter of porosity
2 实验结果与分析
2.1 真空平板玻璃封边气孔来源及形成原因
气体的存在是产生气孔的先决条件,焊接时,气体的来源主要有4种形式:粉末颗粒间隙之间或基体表面的残留空气、粉末或基体含有一定量的有机物质、粉末或基体中低熔体金属化合物的挥发、粉末在熔封过程中发生化学反应产生了新的气体。为了揭示真空平板玻璃在激光封接过程中封接层的气孔成形原因,对工艺参量激光功率P=80W、焊接速率v=2mm/s、离焦量h=-2mm下的试样进行SEM分析,如图3所示。封接层中出现了数量较多,大小不一、相互不连通的孤立气孔,主要位于颗粒的交界处,在某些气孔边缘出现微小裂纹,裂纹从气孔处向熔融块状组织延伸。在真空平板玻璃封接过程中,由于焊料与玻璃基体之间存在一定的热膨胀差异,会在封接层产生一定的热应力,气孔在形成过程中也会产生一定的热涨压力,两者共同作用下会在气孔处优先产生裂纹,裂纹的产生易使一些孤立气孔连通,影响真空平板玻璃的封接质量。
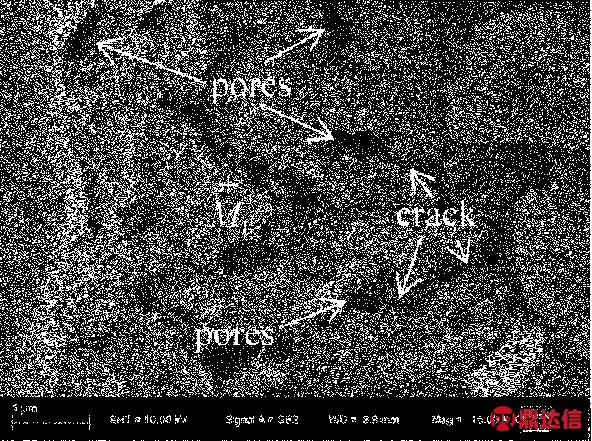
Fig.3 SEM morphology of sealing layer in P=80W,v=2mm/s,h=-2mm
图4 为图3中M1处的能谱图。从图中可以看出,封接层的主要元素为 Si,Pb,Ti,Na,O 等,在封接层中未出现有机物所含C,S等特有元素,所以可消除由有机物造成气孔的原因。焊料的主要成分为PbO,TiO2,SiO2,CuO和Fe2 O3,其均为难挥发物质,因此可以消除由焊料及其添加物挥发造成气孔的原因。
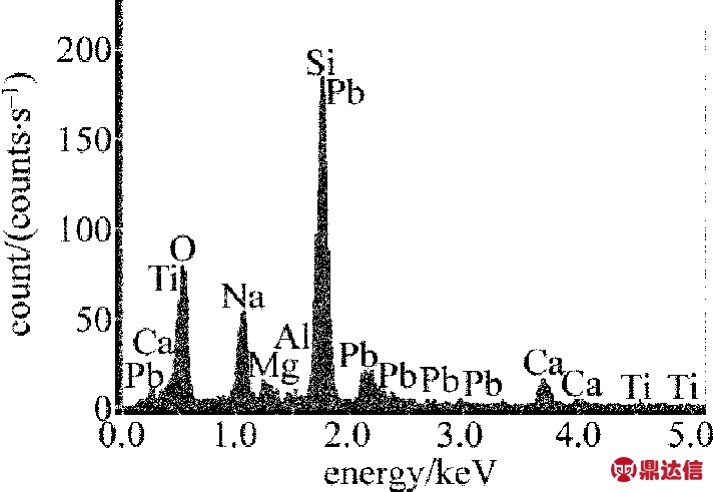
Fig.4 EDSspectrogram at point M1 in Fig.3
图5 为封接层的XRD分析结果。从图中可以看出,激光焊接过程中生成的晶相主要为PbTiO3,还有部分PbO和SiO2相,PbO和TiO2发生化学反应生成了PbTiO3,但是此过程中并不生成任何气体,因此可以消除粉末反应造成气孔的成因。综上所述,激光焊接真空平板玻璃气孔成因主要是由焊料粉末间的残留空气引起的。
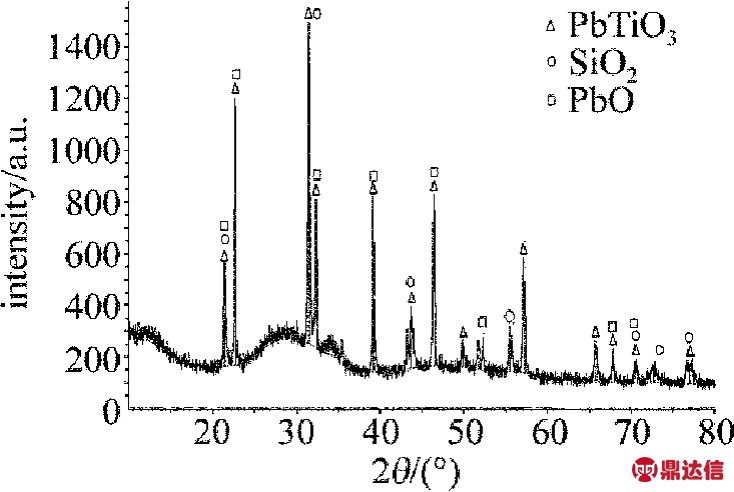
Fig.5 XRD analysis of vacuum glazing sealing layer
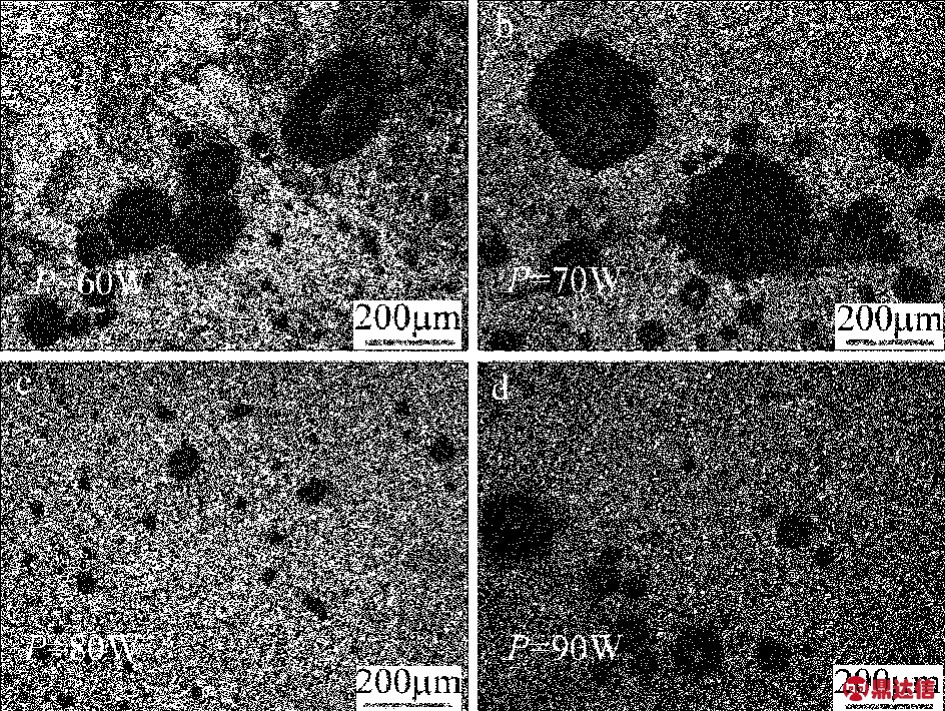
Fig.6 Pores distribution of sealing layer in laser power of 60W,70W,80W and 90W
2.2 激光功率对封接层气孔的影响
图6 为不同激光功率下封接层气孔分布图。图7为气孔率统计结果。激光功率的大小影响封接层的温度梯度、冷却速率以及焊接过程的稳定性,从而对封接层内部气孔产生不同程度的影响。从图6可见,气孔无规则的分布在封接层内部,当激光功率为60W时,气孔分布广泛,且存在较多的直径大于50μm气孔,封接层表面不平整;增大功率到70W时,仍存在较多大直径气孔,且最大直径达到289.43μm,但封接层表面平整度增加;激光功率为80W时,以直径小于50μm的气孔为多,封接层表面平整,致密度高;激光功率为90W时,小气孔数量大幅度减少,只见少量直径大于50μm的气孔,封接层表面较平整,致密度较高。由图7可知,封接层气孔率呈先降后升的变化趋势。当激光功率为70W时,封接层气孔率最大,达到20%,这主要是由于气孔直径较大造成的;当激光功率为80W时,气孔率最低,仅为4%。
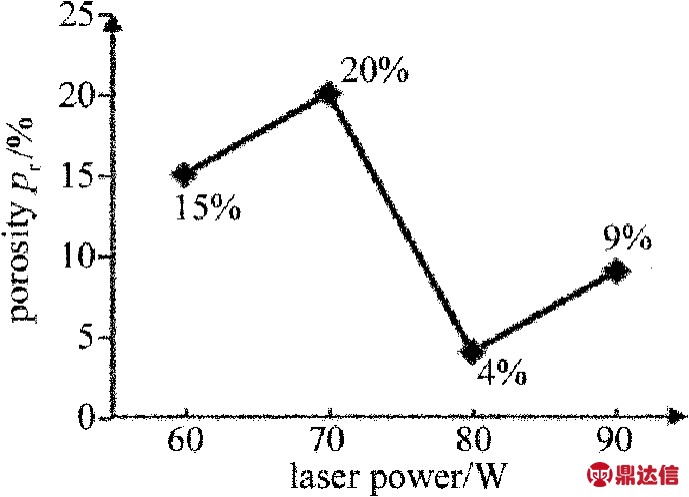
Fig.7 Variation of porosity under different laser powers
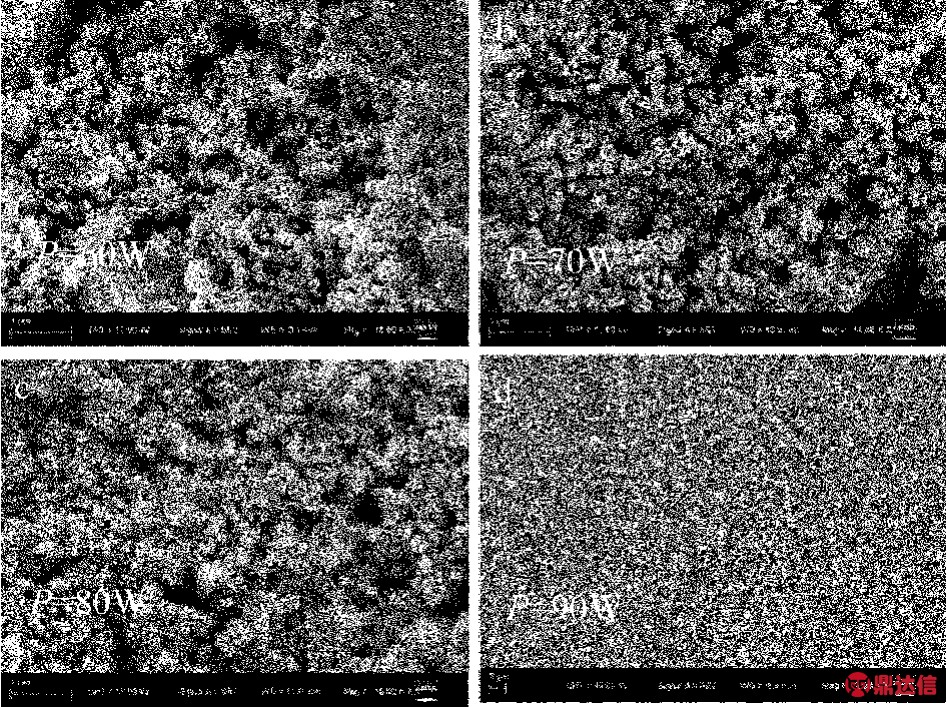
Fig.8 Micromorphology of the melting zone at different laser powers
图8 为不同激光功率下封接层熔融区微观形貌。从图中可以看出,当激光功率为60W(能量密度为60J/mm2)和70W(能量密度为70J/mm2)时,激光功率太低导致能量输入不足,焊料未完全融化,生成的液相量偏少,熔体黏度较高,不利于焊料颗粒间的残留气体溢出,所以图6中封接层内部存在较多大直径的孤立小气孔。当激光功率达到80W(能量密度为80J/mm2)时,能量输入增加使熔融金属液相量增加,焊料黏度降低,焊料颗粒间的残留气体可以溢出,所以图6中封接层气孔明显变少,同时随着激光功率的增加,熔融粉末润湿性增强,有利于粉末铺展,使得封接层表面平整度增加,提高了封接质量。当激光功率为90W(能量密度为90J/mm2)时,小气孔随着输入能量的升高而汇聚,在内外压差作用下,汇集而成的大气泡大部分从封接层溢出,只存在少部分无法溢出的气孔。可以看出,当焊接速率和离焦量一定的条件下,过低或过高的激光功率都不利于减少封接层的气孔缺陷。激光功率为80W(能量密度为80J/mm2),封接层组织形貌好,封接层封接质量佳。
2.3 焊接速率对封接层气孔的影响
通过对不同激光功率下封接层气孔分析可知,在激光功率为80W时,其封接层气孔率低,封接质量较佳,故对激光功率在80W时不同焊接速率下的真空平板玻璃封接层气孔进行分析。
图9为不同焊接速率下封接层气孔分布图。图10为气孔率统计结果。从图9和图10看出,随着焊接速率的增加,封接层气孔越来越多,相应地气孔率从0.8%逐渐增大到7.5%。焊接速率为1mm/s时,封接层部分区域出现了少量直径小于50μm的气孔,最大气孔尺寸仅为48.58μm,且封接层表面平整致密;当焊接速率为2mm/s和3mm/s时,封接层表面虽然平整致密,但是气孔数量和气孔尺寸明显增加,封接质量与焊接速率为1mm/s相比较差;焊接速率增加到4mm/s时,封接层气孔数量众多,分布广泛,大小不一,封接层表面不平整且不致密,封接质量差。
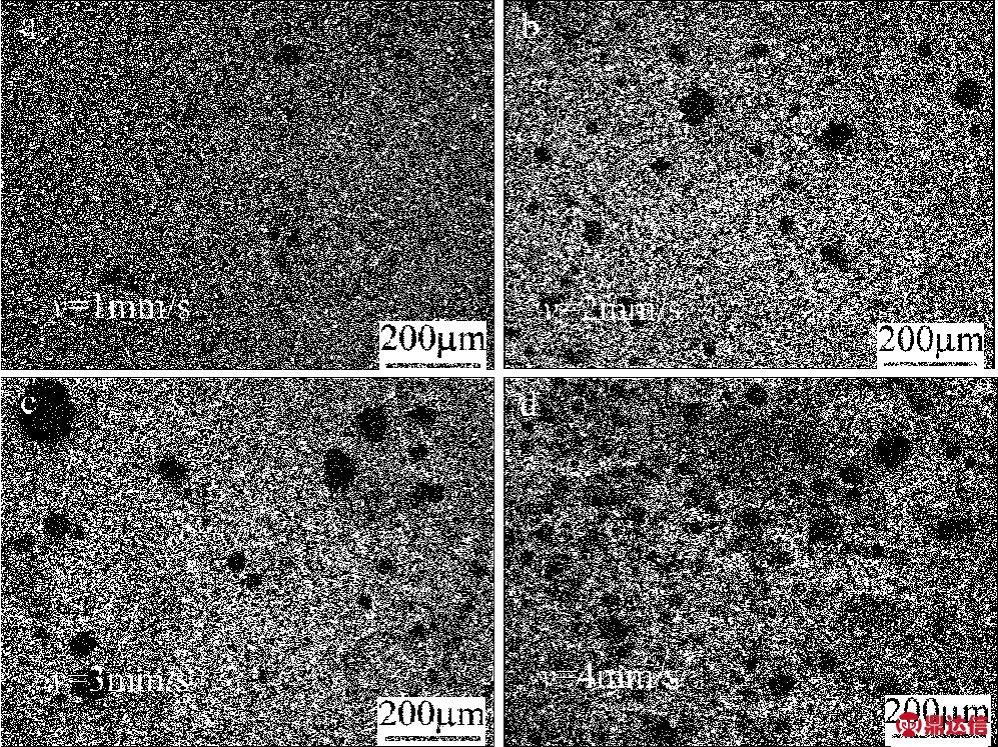
Fig.9 Pores distribution of sealing layer in welding speed of 1mm/s,2mm/s,3mm/s and 4mm/s
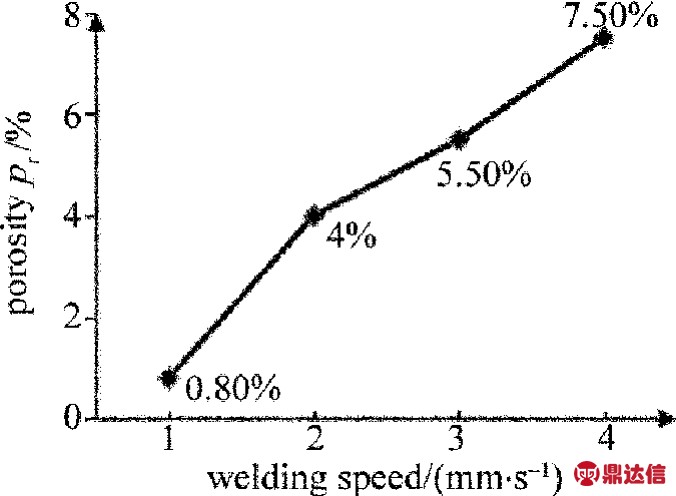
Fig.10 Variation of porosity under different welding speeds
图11 为不同焊接速率下封接层熔融区微观形貌。从图中可以看出,当焊接速率为1mm/s(能量密度为160J/mm2)时,焊料融化较彻底,熔融焊料铺展较好,焊料的黏度低,残余气体可以溢出,在焊料颗粒之间只存在极少气孔缺陷;当焊接速率逐渐增大时,焊料对激光能量的吸收越来越少,焊料出现未完全熔化,焊料黏度大,残余气体溢出困难,焊接速率达到4mm/s(能量密度为40J/mm2)时,局部区域受热不均,不能较好地形成晶粒,焊料颗粒间存在较多孔隙。可以看出,在激光功率和离焦量一定的条件下,较低的焊接速率将有利于减少封接层的气孔缺陷。焊接速率为1mm/s(能量密度为160J/mm2),封接层组织形貌好,封接层封接质量佳。
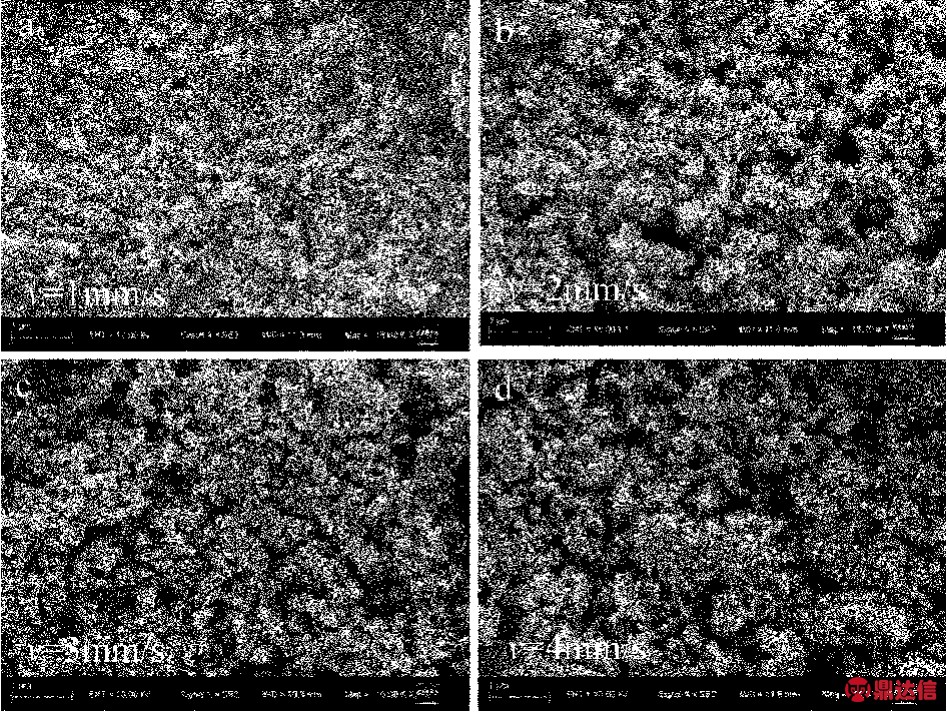
Fig.11 Micromorphology of the melting zone at different welding speeds
3 结论
通过改变激光功率与焊接速率,对气孔的分布特征及形成原因进行了分析。
(1)激光焊接真空平板玻璃的气孔主要是由焊料粉末间的残余空气引起的。
(2)在焊接速率为2mm/s和离焦量为-2mm的条件下,过低或过高的激光功率都不利于减少封接层的气孔缺陷。当激光功率为80W(能量密度为80J/mm2)时,封接层组织形貌好,封接层封接质量佳。
(3)在激光功率为80W和离焦量为-2mm的条件下,较低的焊接速率将有利于减少封接层的气孔缺陷,当焊接速率为1mm/s(能量密度为160J/mm2)时,封接层组织形貌好,封接层封接质量佳。