摘要:液压泵作为液压系统的能力装置、动力元件,其性能的好坏直接影响液压系统的正常工作。对液压泵气孔与气穴产生的原因进行了认真分析,并提出相应的措施来消除这类缺陷。
关键词:液压泵;气孔;气穴;改进措施
液压泵作为液压系统的能力转换装置、动力元件,其性能的好坏直接影响液压系统的工作效率。气孔和气穴是液压泵的常见故障,气孔是液压泵本身的原因引起的故障,气穴是外界因素引起的故障。通过分析产生气孔和气穴的原因,并采取相应措施,消除和预防这类缺陷。
1 气孔成因及预防措施
1.1 气孔类型及成因分析
PVBQA液压泵壳体采用铸造成型,车铸件端面3 mm,观察气孔形状特征及位置分布。气孔呈椭圆形或梨形,集中气孔呈蜂窝状,内壁光滑,靠近铸件表面,分布无规律。根据生产现状及气孔特征,判断气孔类型为侵入性气孔及少量渣气孔。侵入气体主要来源于铁液热作用下型壁内造型材料生成的气体。浇注后产生并聚集于型壁表面的砂层孔隙中的气体,因热膨胀压力猛增而向四面扩散,在铁液未凝成硬壳前,有可能侵入铁液中,也可能进入型腔或穿过砂层逸出型外。当型壁内气体的压力大于阻止气体侵入铁液的各种阻力时,气体才会侵入铁液中,即气体侵入铁液的条件为:

式中:p气为型腔表面砂层某点气体的剩余压力;
p静 为铁液的静压力 (p静=h·γ);
p腔为铁液液面上型腔内气体压力;
p阻为气体侵入铁液时因铁液表面张力而引起的附加压强 (p阻=2σ/r,r为气泡半径,取孔隙的一半,σ为铁液的表面张力)。
根据侵入性气孔的形成条件,要防止气体侵入铁液应满足的条件是:p气<p静+p阻+p腔。这可从减少铸型表面气体剩余压力p气和提高p腔、p静两方面着手。但在生产实际中,过大的p腔、p静会带来机械粘砂等其他质量问题,因此主要靠减少p气来防止气孔侵入。主要措施有减少型 (芯)砂的发气量,提高铸型的透气能力,并在较高温度下浇注,以便已侵入气体能在铁液未形成硬壳前逸出。
渣气孔是由于铁液与渣相反应生成的气孔,即:(FeO)+[C]→[Fe]+CO↑,在S含量较高时容易形成。S以FeS存在于铁液中,它与铁液中的Mn反应生成MnS,MnS溶于氧化渣并降低其熔点成液态,从而使渣中自由氧化铁能与石墨充分接触反应生成CO。要防止这类气孔必须控制铁液中的S含量,同时在熔炼和浇注过程中防止铁液氧化。
1.2 防止气孔生成的措施
1.2.1 改进型砂质量
(1)降低煤粉的加入量,减少含水量;
(2)提高新砂的补加量,并严格控制含泥量,以改善铸型的透气能力。
1.2.2 改进芯砂的质量
(1)选用更粗的新砂,含泥量控制在最低;
(2)减少黏土的加入量;
(3)适当加入一定量的木屑,以提高泥芯的透气能力。
1.2.3 改进浇注系统设计
适当增大直浇道的直径,提高浇注速度以适当增加p静;在芯头上开设一定大小的排气道,以减小p气,提高型腔的排气能力。
1.2.4 规范造型制芯过程操作
砂型紧实度要求均匀适度,起模和修型严禁过多刷水,上型应扎足够数量和深度的出气孔。泥芯必须干透,且要在冷却至室温后才能下芯合箱。合箱时封死芯头间隙,防止铁液钻入堵塞排气道口。
1.2.5 严格控制熔炼与浇注过程
妥善管理炉料,对锈蚀严重或表面油脂物多的炉料,必须经清理或处理后才能使用。用一定厚度的废钢,以防止炉内氧化。孕育剂充分预热,炉缸、前炉、浇包充分烘干。抬包浇注时应低位浇注迅速充满。浇口杯中液面高度必须大于直浇道直径,且浇注过程平稳,以防气体卷入。浇注时必须及时点火引气,铁液出炉温度确保在1 420℃以上,浇注温度在1 360℃以上。
1.2.6 控制铁液中硫含量防止渣气孔
铁液中的硫主要来自于燃料和金属炉料,因此,应选用含硫量低的铸造焦炭和低硫金属炉料,同时进行炉外脱硫,控制铁液中的硫含量少于0.1%。
1.3 改进效果
通过上述工艺改进,PVBQA泵壳体气孔缺陷由30%~40%下降到1%~2%,且没有出现其他新的铸造缺陷,废品损失显著降低。
2 气穴成因及预防措施
2.1 气穴故障原因分析
液压泵吸油系统产生气穴的主要原因是泵吸油口处压力低于气体分离压或吸入空气,依据伯努力流量连续性方程,可知液压泵吸油处压力为:
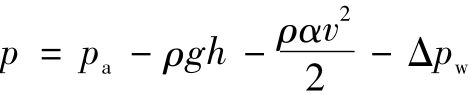
其中:p a为油箱液面压力;ρ为液体密度;g为重力加速度;h为液压泵吸油口距离油箱液面的高度;α为动能修正系数;v为液压泵吸油口处速度;Δp w为吸油管内总压力损失。
对上式分析可知,能引起p下降的变量为产生气穴故障的原因,具体如下:(1)油箱透气孔堵塞,导致油箱液面压力p a过低;(2)电动机速度高,导致液压泵吸油口液流速度v过高;(3)滤芯堵塞或滤油器精度选择过高,导致滤油器芯处压力损失过大,从而使Δp w增大;(4)油液温度低、黏度大,导致沿程阻力系数过大,从而使Δp w增大;(5)吸油管的总长度l过高或吸油管的内径d过小,导致Δp w增大;(6)管道弯折、压扁、堵塞等,导致局部阻力系数过大,从而使Δp w增大;(7)泵安装过高,导致液压泵吸油的高度h过大;(8)其他,如管道密封不严、吸油管浸入油箱面太浅等,使液压泵吸油口直接吸入空气,是液压泵产生气穴的重要原因。
2.2 预防液压泵产生气穴的措施
(1)降低管路等附件引起的压力损失。①增大吸油管直径、减小或避免吸油管道的弯曲,以降低吸油速度、减小沿程和局部压力损失。②选用合适的吸油滤油器,并要经常检查、定期清洗,避免堵塞。③尽量使液压泵吸油口低于油箱液面或把液压泵安装在低于油箱的位置,从而改善吸入条件;自吸性差的大流量泵,应加低压辅助泵供油。④避免由于油的黏度高而产生吸油不足。一方面应根据地区、季节、气温变化合理选用液压油的牌号;另一方面在低温开车运行时,应进行空车预运转,使系统温度适宜时再加载运转。
(2)防止液压泵吸空、除去油中气泡。①定期检查吸油管接头的密封状况,防止因密封不严而吸入空气。②启动机器一定要检查油箱的液面是否在合理的范围内。③设法除去油液中的气泡。如可选用性能好的液压油或在油液中加入消泡添加剂。④合理设计油箱结构。
3 结束语
分析液压泵气孔和气穴原因并提出相应的改进措施。降低气孔缺陷,能提高液压泵出厂合格率;减少气穴缺陷,能提高液压泵的工作效率。