摘要:介绍了应用于硅晶片激光标识的激光打标系统结构,并以光纤振镜式激光打标机为例,探索了不同打标工艺参数的选择对晶片激光标识效果的影响。采用单因素实验法分别研究了不同激光打标功率、打标速度和打标频率对硅片打标效果的影响,并分析了其影响其打标效果的原理。通过目检和金相显微镜对激光标识进行观察,确定了最佳的打标工艺,最终得到了优化的打标工艺即采用激光额定功率的45%,频率为25 kHz,打标速度为150 mm/s,可得到标识清楚、深浅一致、不损伤晶片特性的激光标识。
关键词:激光标识;激光功率;频率;打标速度
激光打标是利用激光的热效应烧蚀掉物体表面材料从而留下永久标记的技术,与传统的电化学、机械等标记方法相比具有无污染、高速度、高质量、灵活性大、不接触工件等优点。在工业国防科研等许多领域具有广泛的用途。目前,激光打标已经在很多领域取代传统的打标方式而成为常规的加工方式。随着激光打标技术的发展,在半导体晶片材料上制作激光标识码,实现产品的可追溯性,已成为晶片材料的基本要求。在国际上,已形成了SEMI M12、SEMI M13等与激光标识相关的工业标准。
激光打标机是集激光、光学、精密机械、电子和计算机等技术于一体的机电一体化设备。它主要由激光器、光学系统和控制器组成,其中控制器是核心部件。在激光打标方式中,现在常用的有掩模方式和扫描方式。扫描方式是用计算机控制扫描振镜,使高度聚焦的激光束在工件上移动扫描进行打标。而扫描方式又分为两种,点阵扫描方式和矢量扫描方式[1]。应用于晶片标识的激光打标机中,一般采用振镜扫描方式来实现在晶片不同位置进行标记。
1 激光打标系统结构
激光打标系统由激光器、振镜、电源控制和工控机四大部分组成。其系统组成:
(1)激光器部分:激光器为光纤激光器,功率大小可调,频率为1~500 kHz可调;
(2)振镜部分:在一系列电信号的控制下使振镜在二维进行有序摆动使激光输出点扫描出相应的图形和文字;
(3)电源控制部分:包括激光电源控制柜,声光电源控制柜;
(4)工控机用于完成扫描图形、文字的绘制、输入、生成并转换成扫描振镜能够识别的驱动信号。
2 激光打标工艺参数的影响
在硅片激光标识过程中,为了在指定位置得到标识清楚且不损伤晶片特性的激光标识,必须通过调整打标工艺参数,得到合适的加工工艺。在加工过程中,主要通过调整激光的打标功率、频率和打标速度来得到优化的加工工艺参数。为了探究最佳的工艺参数,通过调整激光功率值、频率和打标速度对晶片进行了点阵式打标的单因素实验。
2.1 打标晶片技术指标
P<100>,厚度为 525 μm。
2.2 激光打标功率的影响
在控制频率、打标速度等参数不变的情况下,使用不同的激光功率进行打标,不同激光打标功率的金相照片如图1所示。从照片中可以看出,当使用激光额定功率25%时,激光标识较浅,激光标识点与硅晶片基体形貌类似,日光灯下已难以识别;随着激光打标功率的增加,激光对晶片材料的灼烧越来越严重,相应的打标深度增加,使用45%激光额定功率进行标识的照片清晰合适;但在更高的打标功率使得激光标识已呈现模糊不清,尤其当用激光额定功率85%时,激光标识点之间区域由于功率较高,其热影响区已相互重叠。
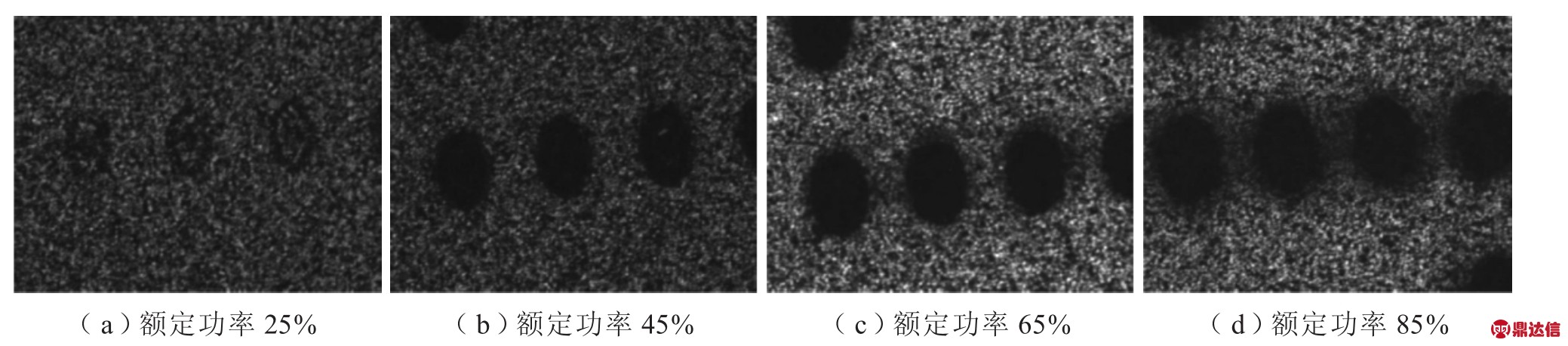
图1 不同打标功率激光标识的金相照片
2.3 激光频率的影响
在打标激光功率、打标速度等参数不变的情况下,使用不同的频率进行打标,不同频率的金相照片如图2所示。从照片中可以看出,当频率为15 kHz时,激光标识较深,但激光标识点存在亮点,表明打标深度深浅不一;当频率增加至25 kHz时,激光标识点与硅基体分辨清晰,且打标深度较深;当频率增加至50 kHz时,就出现了打标深度较浅的情况;当增加至100 kHz时,打标深度已经特别浅,在日光灯下,已难以识别。
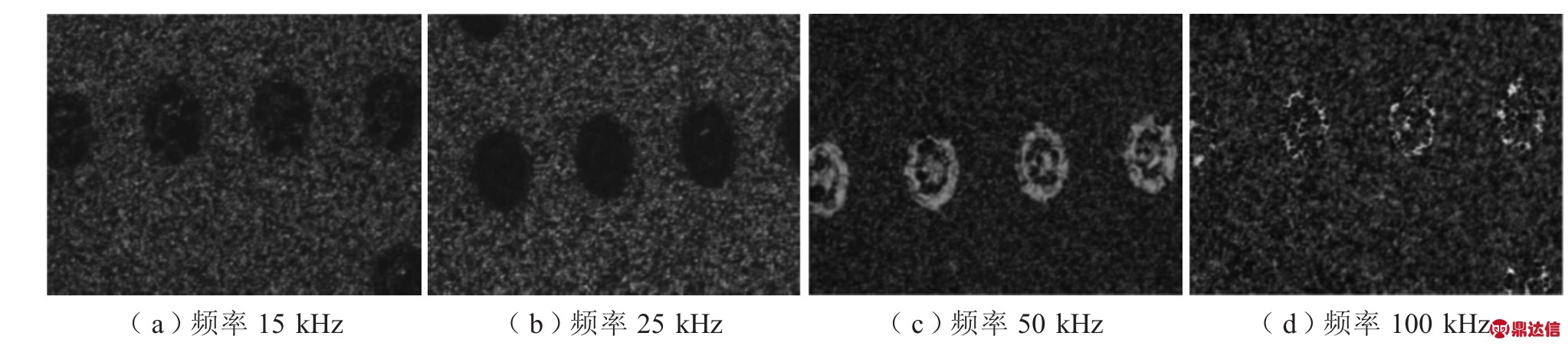
图2 不同频率激光标识的金相照片
2.4 打标速度的影响
在控制激光功率、频率等参数不变的情况下,使用不同的打标速度进行打标,不同打标速度的金相照片如图3所示。从照片中可以看出,当打标速度为30 mm/s时,激光标识较深,但激光标识点边缘轮廓不清晰;当打标速度的增加至150 mm/s时,激光标识点与硅基体分辨清晰,且打标深度较深;当打标速度增加至300 mm/s时,可以发现激光表示点出现了变形的情况;当增加至600 mm/s时,激光标识点的变形尤为严重,且出现了亮点情况,在日光灯下,表现已难以识别。
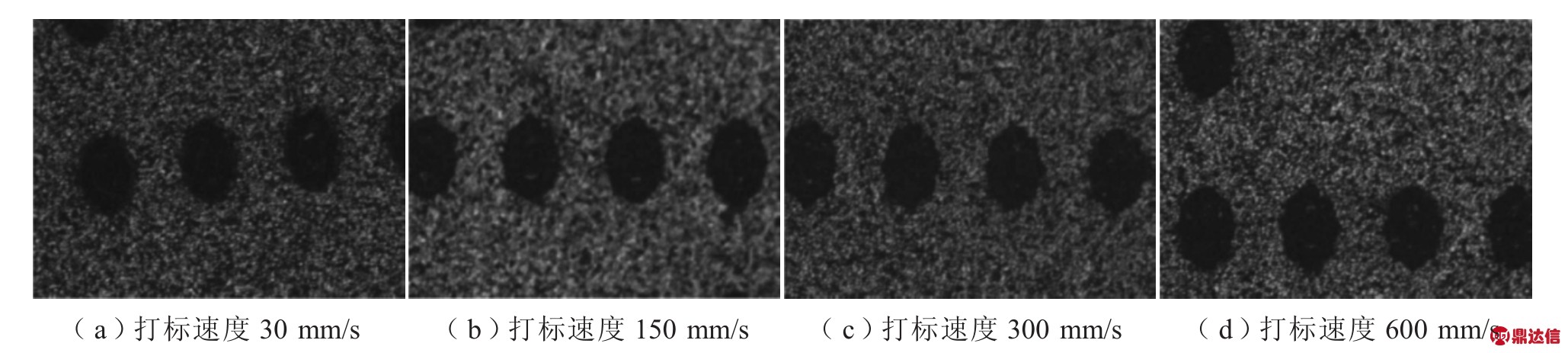
图3 不同打标速度的金相照片
通过上述3个激光标识实验,可以确定优化的打标工艺为:激光功率为45%,频率为25 kHz,打标速度为150 mm/s,在此工艺条件下,可以得到标识清晰、深浅一致、无损晶片特性的激光标识。
3 激光打标工艺参数的分析
作用在材料上的激光束因热效应使局部材料快速气化或引起材料性质的改变从而在材料上留下永久的标记,其效果主要取决于激光束作用在工件材料上的功率密度及作用时间。因此,激光打标参数对标记效果的影响主要由激光打标功率和打标速度两个因素决定。
另外,光斑大小直接影响了激光束作用在工件材料上的功率密度。光斑越小,功率密度越高。在标记对功率密度要求较高的材料时,可合理选配焦距较短的扫描镜,减小光斑尺寸,提高激光束作用在工件材料上的功率密度。
基于上述分析,我们对照激光打标试验可以发现,当功率较低时,光斑内功率密度较低。因此,在15%的激光功率下,标识较浅;而当激光功率提高时,激光打标深度相应增加;但当激光功率过高时,热影响较大,严重影响激光标识效果。
频率对激光标识的效果和激光功率的影响都有关,对功率的影响可以从峰值功率和平均功率两方面分析。当频率较低时,有高的峰值功率但平均功率过低,会出现深度不一的情况;而频率过高时,有高的平均功率但峰值功率过低,接近于连续激光输出,此时激光标识点较浅,导致难以识别。因此,上述两种情况都不太适合激光标识,频率在一定范围内时,峰值功率和平均功率均相对较高时,才是打标选用的频率值。
激光打标速率对激光标识质量的影响主要考虑的是对工件位置作用时间的长短以及在高速打标时,对标识点质量的影响。在打标速率较低时,在工件指定位置相对加工时间较长,能量高,因此会出现灼烧严重的现象;而当打标速度较快时,会导致在不该激光的区域有一些灼烧,导致标识点变形,影响标识清晰与重叠度。
要标刻出高质量的产品,不仅要考虑激光束对材料的作用,还要考虑激光束行程的均匀性及行程控制的准确性。在打标过程中可以合理地调节空走速度、重复次数、出激光延时、断激光延时、拐点延时、延时打标时间等打标参数,对机械惯性产生的影响进行校正。如果在打标速度较高时,可以适当增加延时。另外,打标图形的分辨率及扫描线密度的设置也会影响打标质量和打标速度,在打标过程中根据不同的需要作合理的设置。
4 结束语
本文介绍了激光打标系统的发展情况和结构,并通过对激光打标系统的工作原理和晶片的激光标识工艺影响进行了分析探索,确定了合适的打标工艺参数,可以得到标识清晰且不损伤晶片性能的激光标识。同时,对于激光打标的其他工艺参数的优化提供了参考,有利于激光打标时参数的选择,从而使激光打标工艺能够更好地应用于硅半导体材料标记。