[摘 要]本文以通过在导模板主体的出料端设有向下凹陷的V形槽,分析V形槽两端部的导模板主体上分别设有贯通至导模板主体下端面的辅助供料缝,加大了供料速度,提升了拉制速度,提高了生产效率,同时解决了随温度增高晶片宽度变窄的问题,利于晶体拉制时的操作,增大了控制调整范围等,适合大范围的推广和应用。
[关键词]蓝宝石;导模法;晶体生长
1.前言:
人工制备蓝宝石晶体材料目前己有很多种方法,主要有:泡生法(Kyrop olous ,简 称Ky 法)、导模法(即Edge Defined Film-fed Growth techni ques ,简称EFG 法)、热交换 法(即Heat Exchange Method,简称HE M 沾),提拉法(Czochralski ),布里奇曼法CBridgman ),坩埚下降法等。以EFG 法为例,制造方法大致如下:将氧化铝原料装入钨钼坩埚内,加热熔融,在坩埚内部放入特定的导模板,导模板开有适当宽度的孔或槽[1]。由于氧化铝与导模板之间具有浸润性,故在毛细作用下,溶液可爬升至导模板顶端,并在导模板顶部形成一层薄膜。
采用EFG 法生长蓝宝石晶片时,其核心之一就是导模板[1],导模板直接影响产品的质量和产量。导模板目前较常用的是具有单一通道的导模板,单一通道存在相应弊端,随着蓝宝石晶片使用的厚度及长度的要求越来越大,单一的供料通道的弊端愈发明显:例如:
a、由于导模板采用单一通道,在导模板的外边缘靠近发热体处温度高不容易供料,导致晶板缩角。
b、由于导模板采用单一通道,随着晶板的拉制越来越长,靠近发热体的导模板温度越来越高,造成所拉制晶体宽度不一致。
c、由于导模板采用单一通道,外侧温度高后为保证晶体厚度要求需降低拉制速度,造成生产效率降低。
鉴于此,现迫切需要设计一种新的导模板来实现晶片或晶板的持续成形,使其在拉制过程中表现形式一致,操作方便可靠等等。
本文根据了导模法生长蓝宝石晶片的导模板的研究,通过在V 形槽两端部的导模板主体上分别设有贯通至导模板主体下端面的辅助供料缝,加大了供料速度,提升了拉制速度,提高了生产效率,同时解决了随温度增高晶片宽度变窄的问题,利于晶体拉制时的操作,增大了控制调整范围等。
2.供料口设计对供料模板的影响
蓝宝石晶片生长过程中第一侧板、辅助供料缝、主供料缝和第二侧板,第一侧板与第二侧板平行且间隔设置构成长方形导模板主体,第一侧板与第二侧板之间的缝隙构成主供料缝,导模板主体分别设计不同角度的V 型槽,V 形槽两端部的导模板主体上分别设有贯通至导模板主体下端面的辅助供料缝,在导模板主体的进料端设有连接槽形成的用于导模法生长蓝宝石晶片的导模板。辅助供料缝的形状设置为V 形或波浪形或直线型或X 形,V 形辅助供料缝两边的夹角为40°~150°,辅助供料缝的开口端向外设置,与导模板主体侧边的距离为1~15mm 两端有圆弧形倒角。主缝的宽度为0.1~3mm,V 形槽两边的夹角为70°~150°.
3.增加供料缝后改善产品成型实施过程
本文结合附图1~3 导模法生长蓝宝石晶片的导模板,包括第一侧板1、辅助供料缝2、主供料缝4 和第二侧板5,第一侧板1 和第二侧板5 的形状均为长方形结构,第一侧板1 和第二侧板5 的长度、宽度和厚度均设置为一致,第一侧板1 与第二侧板5 平行、对应且间隔设置构成长方形导模板主体,第一侧板1 与第二侧板5 之间的缝隙构成主供料缝4,主供料缝4 的宽度b设置为0.1~3mm,在实际应用过程中,第一侧板1 与第二侧板5 之间设置若干个间隔块,然后第一侧板1 与第二侧板5 通过螺栓固定为一体(此结构附图中未示出);
(1),第一侧板1 与第二侧板5 的材料选用钨或钼或钨钼合金当中的任意一种;
(2),在导模板主体的出料端设有向下凹陷的V 形槽3(如图3所示),V 形槽3 两边的夹角β为70°~150°,在实际实施过程中, V 形槽3 的设置即在第一侧板1 的上端设置左侧高右侧低的斜面A,在第二侧板5 的上端设置左侧低右侧高的斜面B,由斜面A 与斜面B 构成V 形槽3;
(3),在V 形槽3 两端部的导模板主体上分别设有贯通至导模板主体下端面的辅助供料缝2,辅助供料缝2 的形状设置为V 形或波浪形或直线型或X 形,在实施实施过程中优选V 形,当辅助供料缝2 设置为V 形时,V 形辅助供料缝2 两边的夹角θ为40°~150°;同时,V 形辅助供料缝2 的开口端向外设置;辅助供料缝2 至导模板主体侧边的距离a 设置为1~15mm;
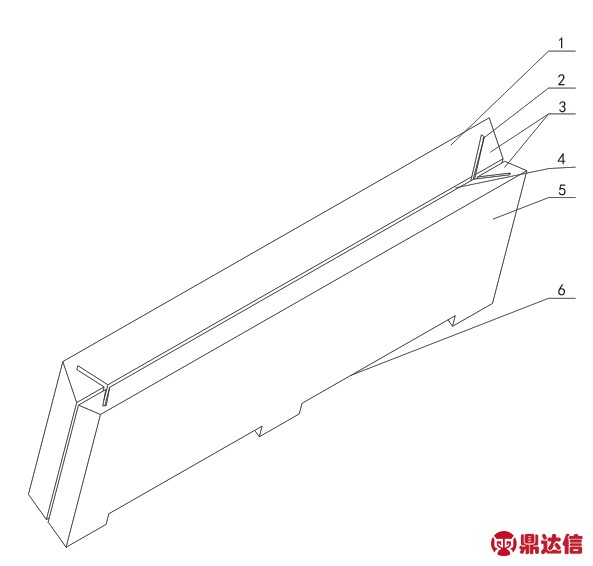
图1
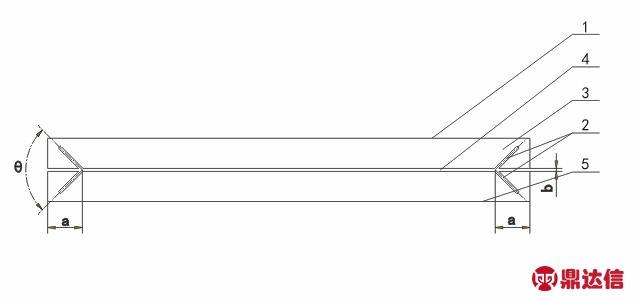
图2
(4),辅助供料缝2 的两端头分别设有圆弧形倒角;
(5),辅助供料缝2 的设置数量可以是两个或多个。
(6),在导模板主体的进料端设有连接槽6,由连接槽6 连接坩埚内的导模板固定座(此结构附图未示出)形成的用于导模法生长蓝宝石晶片的导模板。
4.实验结果
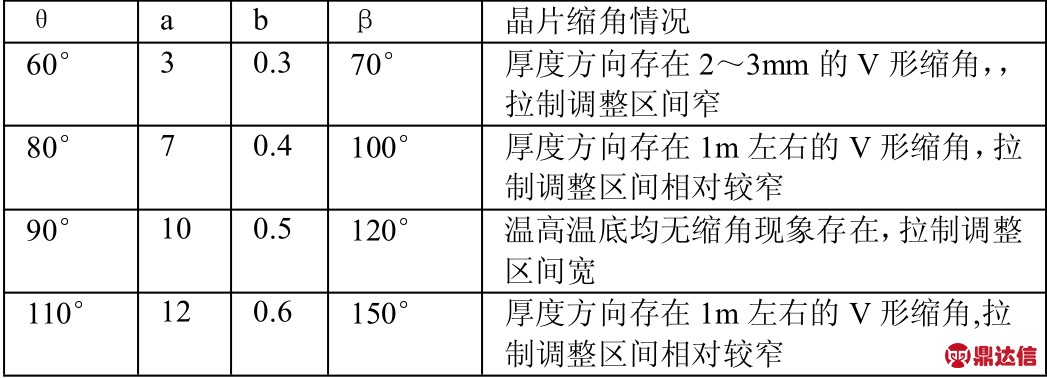
5.结论与分析
从试验的结果分析可得,增加了辅助供料缝2,加大了供料速度,提升拉制速度,提高生产效率;增加了辅助供料缝2,改变导模板局部温度,利于晶片结晶,解决晶片缩角问题,保证晶片的完整;增加了辅助供料缝2,解决了随温度增高晶片宽度变窄的问题,利于晶体拉制时的操作,增大了控制调整范围。
6.结论:
通过在导模板主体的出料端设有向下凹陷的V 形槽,在V 形槽两端部的导模板主体上分别设有贯通至导模板主体下端面的辅助供料缝,加大了供料速度,提升了拉制速度,提高了生产效率,同时解决了随温度增高晶片宽度变窄的问题,利于晶体拉制时的操作,增大了控制调整范围。等,适合大范围的推广和应用。