摘要:三维多孔石墨烯及其复合材料作为一种功能材料在能量存储、光电器件、气体分离和存储、吸附和传感器等领域得到关注。模板法由于能够精确控制孔尺寸、形貌和结构得到广泛研究。综述了利用分子筛、沸石、SiO2等硬模板,胶束、乳液、嵌段共聚物等软模板以及植物、粉末冶金、原位自牺牲等非传统模板制备三维多孔石墨烯及其复合材料的方法,并分析了各种方法的优缺点及材料性能。以期为三维多孔石墨烯及其复合材料的研究提供参考。
关键词:石墨烯;模板法;复合材料;三维多孔结构
1 引 言
自从Geim[1]发现石墨烯以来,由于其独特的结构和优异的性能而备受关注。石墨烯的制备方法主要有机械剥离法[2]、水热法[3]、SiC外延生长法[4]、氧化还原法[5]、化学气相沉积(CVD)法[6]及液相沉淀法[7]等。其中,机械剥离法效率低,不易获得大尺寸石墨烯;CVD法对石墨烯沉积时工作温度较高,速率较低,对层数沉积也难以把控;化学法一般无法控制石墨烯片层间距,片层易堆叠,进而导致多层石墨烯结构中每一层生成孔隙也极为困难[8]。为了克服石墨烯易堆叠的缺点,以拓展其应用的领域,可将石墨烯组装成三维多孔结构再与其他材料进行复合,发挥多元材料的协同效应。三维多孔石墨烯比表面积显著增大,并且孔结构、表面活性、传质速率、机械性能及电化学性能均有改善,在能量储存(超级电容器[9],锂离子电池[10],燃料电池[11]等)、气体分离和储存、吸附等方面将发挥更大作用。目前,三维多孔石墨烯制备已取得一些进展,主要有水热法、模板法[12]、溶胶凝胶法、CVD法和氧化还原法等。其中,模板法由于能够精确控制孔尺寸、形貌和结构,加之操作简易、成本较低,引起了广泛的关注和研究,成为制备三维多孔石墨烯的一种重要方法[13]。
模板法是控制材料形貌和尺寸的一种制备方法,根据选用模板的特性和限域作用,主要包括硬模板法和软模板法[14]。硬模板是指所选模板的材质和结构相对较“硬”,一般为固体材料,如碳基、金属及衍生物材料或无机粒子等[15]。软模板是指模板的结构和硬度相对较“软”,即柔性的材料,一般为液体或液晶态材料,如胶束、乳液、共聚物和气泡等[16]。近年来,利用模板法结合其他的化学法如化学气相沉积法、热解法、原位聚合法、自组装法和电沉积法等制备三维多孔石墨烯及其复合材料获得了广泛的研究。
2 硬模板法
硬模板即刚性纳米结构颗粒,常用的硬模板有分子筛、沸石、SiO2及金属有机物框架等[13]。硬模板在三维多孔石墨烯时,对其结构的生长有着较强的限域作用,可以精确控制其形貌和尺寸。采用硬模板法合成的纳米材料大多需要进行后期处理,使用强酸、强碱或有机溶剂将模板去除,制备过程较为复杂,且易破坏复合材料的结构[13]。未来希望发现一些新型模板,而不需要经过酸碱刻蚀,而是直接通过热分解,或在一定反应条件下可直接升华的物质,这样既减少了洗涤的过程,又保证了样品的纯度。或是通过发现新型用于刻蚀的酸碱或其它有机溶剂,对于模板的刻蚀具有针对性,多余的溶剂对材料的结构无影响,可直接通过抽滤洗涤得到样品,这些还有待进一步研究。
2.1 分子筛
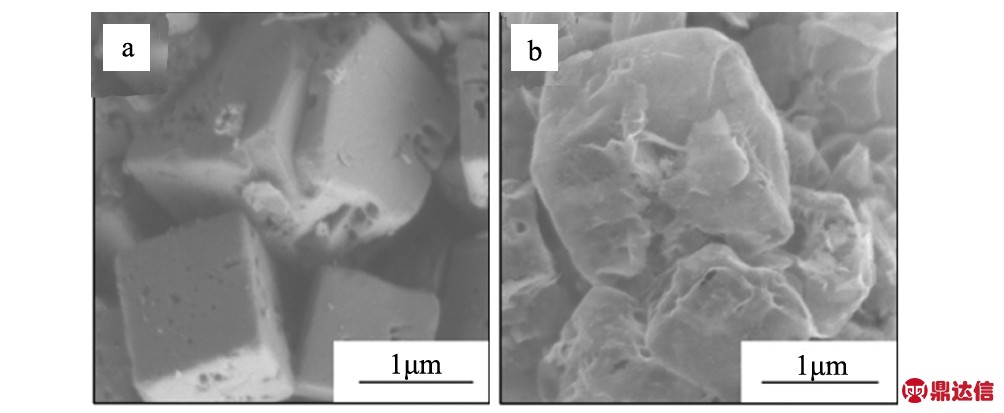
图1 SAPO-34分子筛模板和所得石墨烯材料的
SEM照片[17](a)SAPO-34;(b)纯化的HPGC
Fig.1 SEM images of SAPO-34 molecular sieve
template and the obtained graphene material[17]
(a)SAPO-34;(b)Purified HPGC
钟玲等[17]以磷酸硅铝分子筛SAPO-34作为模板,采用化学气相沉积法,甲烷为碳源,引入氨气煅烧,再经HF刻蚀,得到如图1所示,具有微孔/介孔超薄石墨烯层围成的空心多级孔石墨烯笼(HPGC),氮掺杂量为6.84at%。该法制备的HPGC精确复制了SAPO-34分子筛形态并具有超薄的特征,由于其独特的孔结构,丰富的缺陷位点以及良好的杂原子掺杂,HPGC表现出高效的双功能氧还原与氧析出反应催化活性。SAPO-34有望成为研究石墨烯在不同酸度模板上生长的多功能平台,通过调整SAPO-34的结构或利用纳米尺寸的框架,可以获得具有优化形态或与约束金属纳米颗粒(甚至单原子位点)复合的石墨烯材料。
2.2 沸 石
沸石是微孔结晶铝硅酸盐类材料,其分为200多种结构类型[18]。Kim等[19]使用β沸石合成具有大单晶形态的八面沸石(FAU),用金属盐水溶液进行离子交换。使用镧离子催化,乙烯气体作为碳源,N2和蒸汽的混合物在600 ℃下,热解可以进入直径小于1 nm的沸石孔中,形成类石墨烯碳结构。
2.3 水滑石
肖厚文[20]以富碳有机阴离子苯甲酸根为碳源,镍铝类水滑石或镁铝水滑石二维层板为模板和催化剂,通过共沉淀法实现苯甲酸根与水滑石层板的超分子自组装后,再经焙烧和“酸蚀”处理去除金属氧化物,制得石墨烯材料。所制备的石墨烯比表面积高达808.06 m2/g,在电流密度为1 A/g下比电容为195.8 F/g,且在电流密度为5 A/g时,1000次循环后比电容保持95.1%。
2.4 二氧化硅
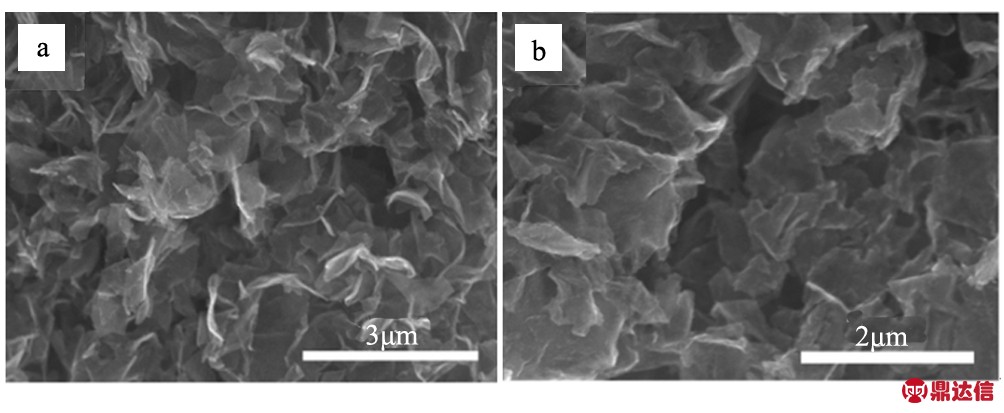
图2 G-mSiO2模板及复合材料的SEM照片[21]
(a)G-mSiO2;(b)G-mPANI
Fig.2 SEM images of G-mSiO2template and composites[21]
(a)G-mSiO2; (b)G-mPANI
Wang等[21]通过使用石墨烯-中孔二氧化硅(G-mSiO2)复合物作为模板,在超薄石墨烯纳米片杂化物上原位聚合制备中孔聚苯胺(PANI)膜(G-mPANI),得到的G-mPANI复合材料的SEM照片如图2所示,在超薄石墨烯片上具有相互连接的PANI网络,并具有介孔结构,孔径尺寸约3.5 nm和12.5 nm。G-mPANI在0.5 A/g时显示出749 F/g的比电容,具有优异的倍率性能,即使在5.0 A/g时仍保持73%。在1 mol/L H2SO4水溶液中,远高于纯PANI在0.5 A/g的315 F/g,5.0 A/g下39%的比电容保持率。G-mPANI复合材料在1000次循环后电容保持率为88%,而纯PANI为45%。
梁漫[22]以氧化石墨烯(GO)作为基底,在GO的两侧包覆SiO2,形成具有三明治结构的GO@SiO2复合纳米材料。该复合材料在pH为4时,对亚甲蓝的最大平衡吸附容量(qe)可达305.3 mg/g,吸附效率达到93%。
2.5 阳极氧化铝
Zeng等[23]采用阳极氧化铝(AAO)膜(图3a)作为刻蚀掩模,利用氧等离子体处理技术制备大面积石墨烯纳米网(GNM)(图3b)。其中聚甲基丙烯酸甲酯(PMMA)作为AAO模板和Si/SiO2晶片上的还原GO(rGO)片之间的粘附层。在氧等离子体蚀刻下,通过使用不同的AAO模板来调整GNM的周期性和均匀的孔径。结果表明由制备的GNM作为导电沟槽的场效应晶体管具有p型半导体特性,并且显示出的驱动电流几乎是单个基于石墨烯纳米带的晶体管驱动电流的100倍。
Jung等[24]使用AAO模板合成的具有有序六边形蜂窝形貌的Au纳米网状薄膜用作GNM生长的催化剂,再通过化学气相沉积在绝缘基板上直接形成石墨烯纳米网格(GNM),具有较高的电子迁移率(233.78 cm2/V·s)和电流ON/OFF比(~6.3),可作为晶体效应晶体管中的半导体沟道。因此,大面积连续半导体GNM有望在电子器件和传感器领域获得应用。
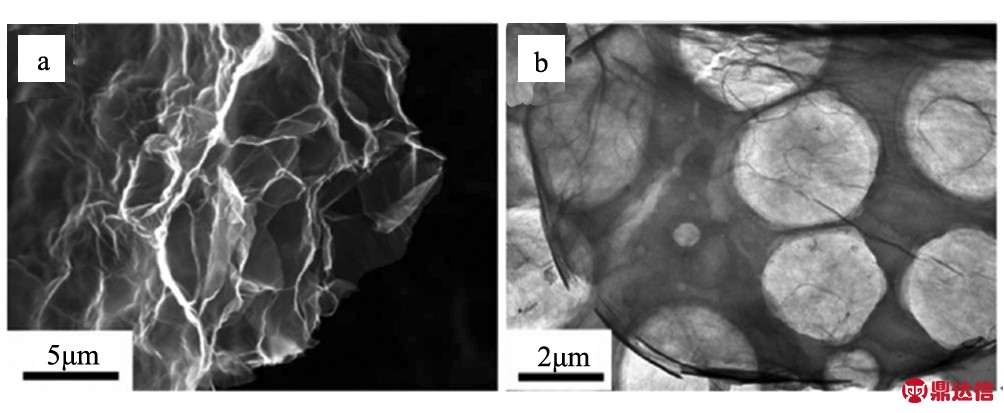
图3 (a)~80 nm孔径和~20 nm壁厚的AAO膜的
SEM照片;(b)大面积GNM的SEM照片,插图:GNM的
放大SEM照片,孔径约67 nm,颈宽约33 nm[23]
Fig.3 (a)SEM image of AAO film with pore size of about
80 nm and wall thickness of about 20 nm;(b)SEM image
of large-area GNM. Inset: magnified SEM image of GNM with
pore size of ca. 67 nm and neck width of ca. 33 nm[23]
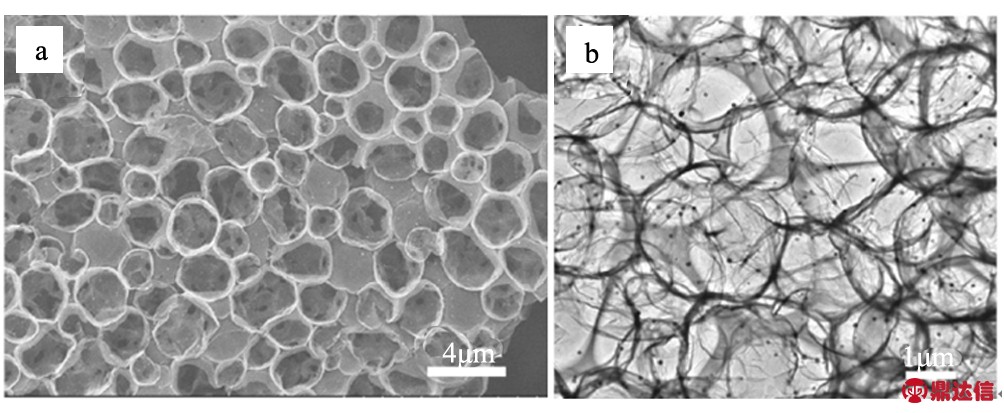
图4 DHPG电极的微观形貌[25]
(a)SEM照片;(b)TEM照片
Fig.4 Micro morphology of DHPG electrodes[25]
(a)SEM image;(b)TEM image
2.6 泡沫镍
Wang等[25]使用氧化石墨烯(GO),磺化聚苯乙烯球(S-PS)和聚乙烯吡咯烷酮(PVP)作为前驱体在泡沫Ni上制备掺杂的多级孔石墨烯(DHPG)。如图4可见,GO在S-PS的表面上沉积,并在PVP的帮助下组装成3D连续结构。此外,在前驱体的热解过程中,来自PVP的氮原子和来自S-PS的硫原子被掺杂到石墨烯中。由于泡沫Ni作为模板形成的具有多级孔结构的石墨烯电极对于离子传输是有益的,并且还提供了电极和电解质之间的足够接触面积。另外,N、S共掺杂同时提高了石墨烯在高速电化学反应过程中的电导率和电化学活性。作为锂离子电池的电极材料,在80 A/g时,它的高功率密度为116 kW/kg,能量密度高达322 Wh/kg。
2.7 氧化镁
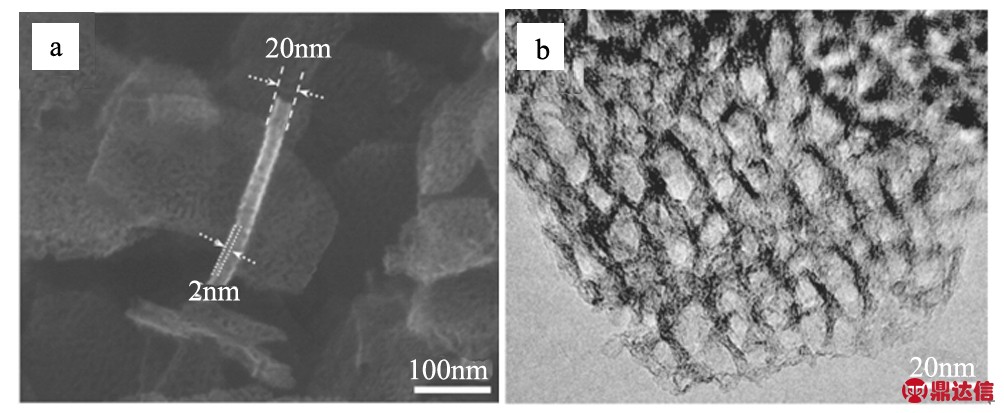
图5 (a)PPCN的SEM照片;(b)夹心形态和介
孔结构的PPCN的TEM照片[26]
Fig.5 (a)SEM image of PPCN;(b)TEM image of PPCN
with the sandwich morphology and mesoporous structure[26]
Fan等[26]采用多孔MgO作为模板,煤焦油沥青作为碳源,二者 溶于四氢呋喃(THF)溶液后,经高温碳化再用HCl洗涤去除MgO模板,得到如图5所示的大尺寸3D柱撑多孔碳纳米片(PPCN),每个碳纳米片由两个碳层及中间的碳柱构成,其中单个碳层厚度2 nm, 碳层间距10~20 nm。该多孔碳纳米片具有相互连接的开孔表面,自支撑介孔和导电网络,独特的结构不仅有效地克服了石墨烯片层的堆叠,而且纳米级孔道还有利于离子传输或扩散,进而获得优异的电化学性能。在2 mV/s时,最高比电容达到289 F/g,在200 mV/s下经10000次循环后,比电容保持94%。
2.8 纤维素纤维
Zhang等[27],使用醋酸纤维素纤维材质的香烟滤嘴(CF)作为模板,通过浸涂GO固化后高温退火,去除模板的同时还原GO,获得如图6所示排列良好的三维结构石墨烯片,石墨烯基各向异性块体材料(AGM)。该制备工艺对于有毒和不可生物降解的CF的后处理是环境友好的。获得的新型石墨烯微管结构由对齐的石墨烯片相互连接组成,在轴向和径向上的力学、电学和热学性质表现出明显的各向异性。通过在AGM中引入压缩聚合物聚二甲基硅氧烷(PDMS)进一步获得AGM/PDMS复合材料,AGM/PDMS复合材料仍保持力学、电学和热学的各向异性。
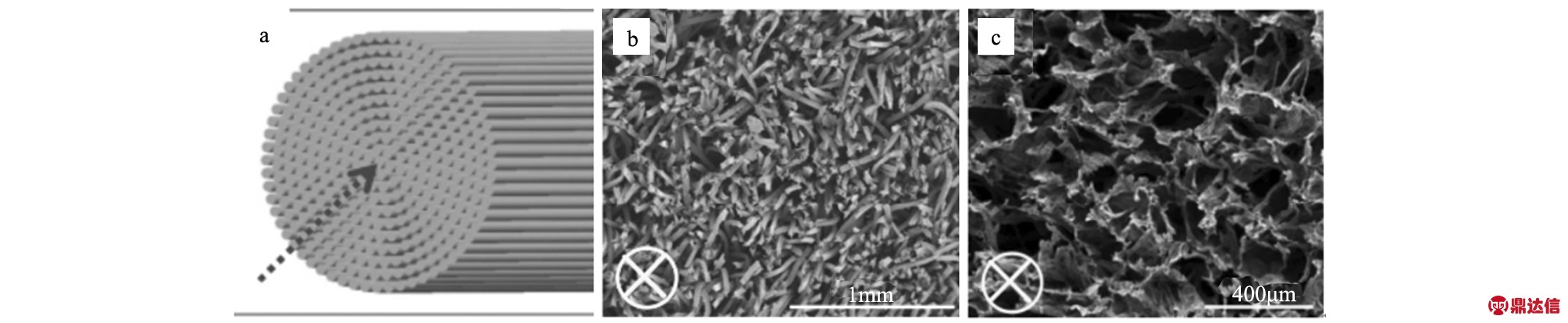
图6 (a)CF模板示意图;(b)CF/GO的SEM照片;
(c)AGM的SEM照片,其中(b)和(c)中的符号反映平行于轴线的方向[27]
Fig.6 (a)Schematic diagram of the CF template;(b)SEM image of CF/GO;
(c)SEM image of AGM, where the symbols in (b) and (c)reflect the direction parallel to the axis[27]
3 软模板法
软模板即超分子聚集体,常用的软模板主要有胶束、乳液、表面活性剂、液晶及气泡等。
3.1 胶 束
胶束指表面活性剂溶于水,当达到一定浓度时,表面活性剂分子(一般50~150个)的疏水部分相互吸引,形成的缔合体。胶束具有尺寸小,一般在1~100 nm,制备容易等特点[28],常被用来制备多孔材料。
Huang等[29],首先用肼将GO在室温下于中性水溶液中还原,以产生部分还原的GO(P-GO)悬浮液,再使用三嵌段共聚物Pluronic F127作模板,将F127水溶液与P-GO悬浮液混合,借助氢键作用自发自组装,在此期间F127胶束被包裹在P-GO纳米片之间。通过真空抽滤将自组装的P-GO /胶束复合物与悬浮液分离,最后在惰性气氛中煅烧以去除胶束同时进一步还原P-GO。该法可获得完全还原的氧化石墨烯纳米片,由图7可见,介孔石墨烯(MPG),孔径集中在25 nm左右。
3.2 乳 液
乳液模板法,即乳液聚合,指单体先借助乳化剂和机械搅拌的作用,在水中形成油水混合体系后,再加入引发剂而引发单体的聚合[30]。该法的优点是制备的石墨烯材料具有高孔隙率、低密度、大比表面积、孔径可控等,且残余单体易去除,缺点是乳化剂的加入会影响材料性能,得到的固体材料需经过凝聚、分离、洗涤等,工艺过程较为复杂,产率较低。
Zheng[31]等使用Pickering高内相乳液(HIPE)作为模板,通过阳离子表面活性剂十六烷基三甲基溴化铵(CTAB)对GO进行改性,并用作油包水(W/O)Pickering乳液的稳定剂。CTAB修饰的GO在稳定W/O Pickering HIPE方面是有效的,并且GO最低含量仅为约0.2 mg/mL(相对于油相的体积)。Pickering HIPE具有大孔结构,通过煅烧去除模板后,成功制备了三维大孔化学改性石墨烯(CMG),比表面积达到490 m2/g 。
赵鹏飞等[32]利用甲基丙烯酰氧乙烯氯化铵(DMC)改性的聚苯乙烯阳离子微球(PS+)作为模板,通过GO与 PS+之间的静电作用进行自组装,最后水合肼原位还原制备纳米石墨烯片(GNs)填充的聚苯乙烯(PS)导电复合材料中,获得极低的导电逾渗值(0.09%(体积分数))和较高的饱和导电率(25.2 S/m)。
Huang等[33]将正十六烷加入到HCl溶液经连续搅拌、超声处理以形成混浊的悬浮液,再与氧化石墨烯和蒸馏水混合,然后通过真空抽滤收集沉淀物。所得沉淀物在氩气气氛下煅烧,得到如图8所示的多孔石墨烯泡沫(PGF)。由于具有新颖的多孔结构,PGF在Li-O2电池中作为阴极催化剂时表现出优异的稳定性,并且具有高效的吸油性能。
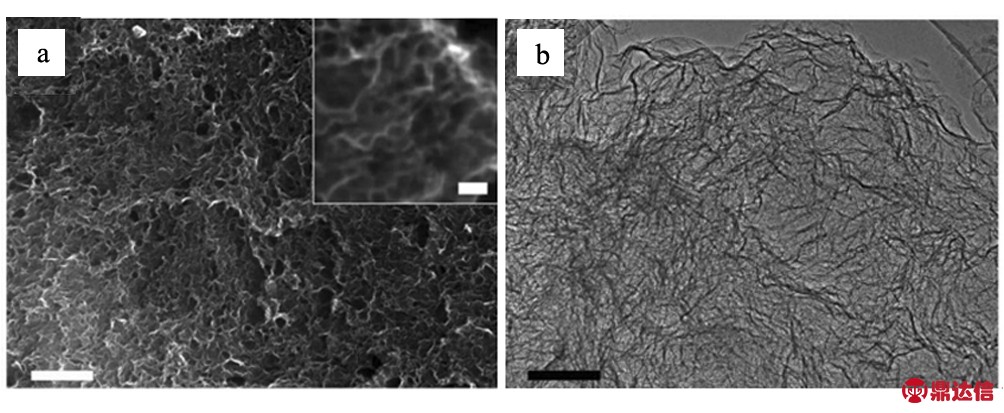
图7 MPG的形态和结构[29]
(a)SEM照片;(b)TEM照片
Fig.7 Morphology and structure of MPG[29]
(a)SEM image;(b)TEM image
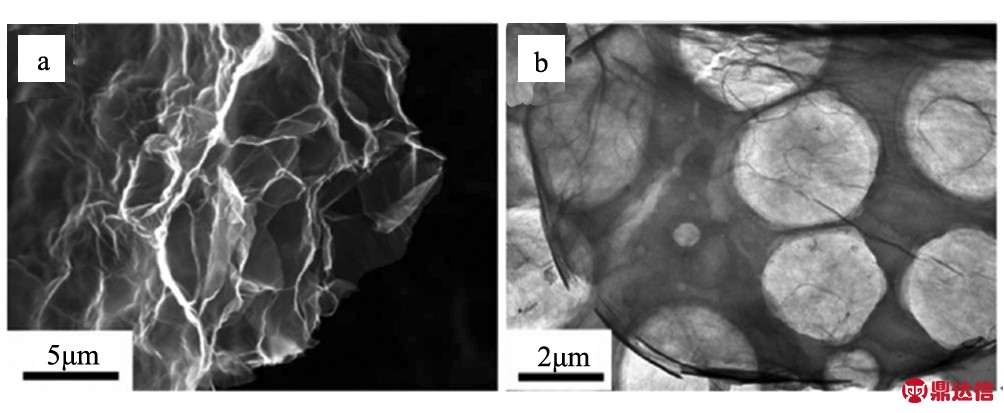
图8 多孔石墨烯泡沫(PGF)[33]
(a)SEM照片;(b)TEM照片
Fig.8 Porous graphene foam(PGF)[33]
(a)SEM image;(b)TEM image
3.3 嵌段共聚物
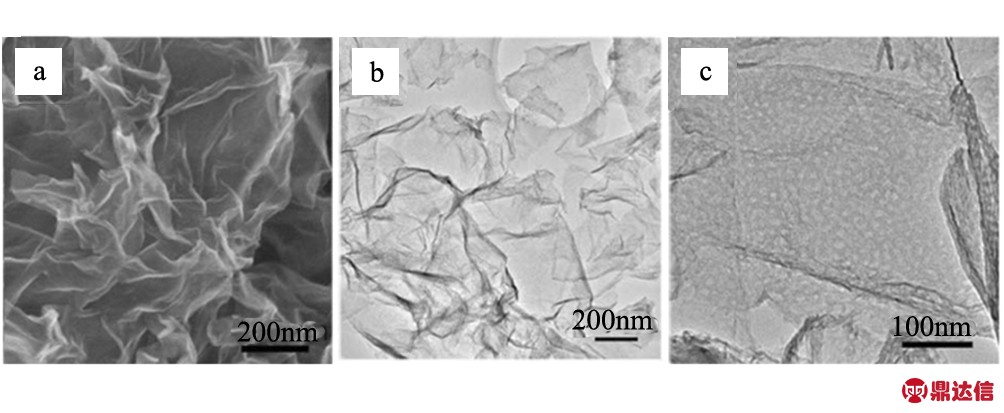
图9 介孔碳/石墨烯(MCG)复合材料[35]
(a)SEM照片;(b)TEM照片;(c)AFM照片
Fig.9 Mesoporous carbon/graphene(MCG) composites[35]
(a)SEM image;(b)TEM image;(c)AFM image
嵌段共聚物是共聚物中的一种,由两种或两种以上的单体组成。由于其微相的尺寸在5~50 nm之间,且在纳米尺度内可自组装,可被用来制备纳米材料[34],但其一般具有弱毒性。
Wang等[35]使用三嵌段共聚物Pluronic F127作为软模板制备酚醛(PF)预聚物中孔碳前驱体。将PF预聚物加入GO溶液中,超声混合后,将所得溶液转移到高压釜中并在130 ℃下加热20 h,洗涤并在40 ℃下干燥,获得用于合成介孔碳/石墨烯(MCG)复合材料的前驱体。再将前驱体在700 ℃下氩气气氛中碳化3 h同时去除共聚物模板,中孔碳和石墨烯的质量比约为1∶1,获得MCG复合材料如图9所示。MCG复合材料在电流密度为0.5 A/g时,在6 mol/L KOH电解液中表现出高达242 F/g的优异比电容,2000次循环后比电容保持95%。
3.4 气 泡
气泡模板法,通常是指利用电化学沉积过程中产生的气泡用作模板,通过控制沉积时间、沉积速率和产生气泡的速率,来控制材料的孔径大小及分布,但目前只能用来制备大孔材料。相信随着研究的不断深入,能够充分控制反应产生气泡的大小,则可用于制备介孔及微孔材料。
Yang等[36]采用电化学沉积法对GO进行沉积,在反应过程中通过减少GO在不同导电基板上的分散,并用氢气泡作为动态模板,电化学制备了三维大孔石墨烯(3D MG)电极。3D MG的形貌和孔径大小可由表面活性剂的使用和气泡产生和离开的动力学来决定。其次,通过将吡咯单体直接电聚合到3D MG网络上,构建了三维大孔石墨烯/聚吡咯(MGPPy)复合材料。受益于3D MG的良好导电性和PPy的赝电容,复合材料在1 mA/cm2的电流密度下,表现出突出的面电容为196 mF/cm2,可用于超级电容器电极。
虽然,软模板不需要强酸强碱进行刻蚀,但是由于引入了外来物种,所以很容易影响到产物的纯度和结构[13]。希望未来可以发现新型的模板剂,对于过量的模板剂,反应后可直接通过热分解,而不会影响产物的纯度,这有待工作者的进一步研究。
4 其他模板法
4.1 植物模板法
植物模板法,指利用植物的茎干、枝叶等作为模板,与其它反应物通过煅烧的方式,使其获得模板的结构。该模板成本低廉,可再生绿色环保,且具有天然多孔结构。不仅结构复杂各异,而且气孔率分布范围宽广,是制备多孔材料的良好模板,可用来制备从宏观孔到微孔、具有不同孔径分布和骨架厚度的多孔材料,是非常有前景的新型材料,未来可能会被广泛使用。但目前存在孔隙尺寸难以控制,孔隙之间连通性不好等缺点。
何凤娟等[37]利用植物膜作为模板和碳源,通过浸渍氯化锰溶液并经过两次煅烧制备了氧化锰/石墨烯复合材料。如图10所示,负载Mn2+的石墨烯呈现出褶皱片层结构,说明在N2保护下植物膜中的碳较完全地转化为片层石墨烯,且自然弯曲,无堆叠现象;在氧化锰/石墨烯复合材料中,可以明显看出MnO2颗粒生长在石墨烯薄层上,MnO2的粒径为10~40 nm,并且颗粒之间形成了尺寸不同的纳米孔。该复合材料的比电容为245 F/g,远高于市购碳粉(25~26 F/g)和植物膜锻烧制备的石墨烯(45~50 F/g)。

图10 石墨烯及复合材料的TEM照片[37](a)负载锰离子的石墨烯;(b)氧化锰/石墨烯复合材料;(c)氧化锰颗粒
Fig.10 TEM images of graphene and composite materials[37]
(a)graphene with manganese ion;(b)MnO2/graphene composites;(c)MnO2particles
4.2 粉末冶金模板法
粉末冶金指使用金属(或金属与非金属的混合物)粉末作为原料,经过成形和烧结,制备金属材料以及复合材料的工业方法[38]。粉末冶金法可以加工特殊材料及高纯材料,可批量生产。缺点是制品强度、韧性差,不能制备大型产品,且压模成本较高。
赵乃勤与Tour[39],以蔗糖作为固体碳源与金属粉末均匀分散在去离子水中,使其均匀包覆在金属粉末表面,再使用传统粉末冶金冷压法压制成型,复合块体再经过Ar/H2混合气氛保护下高温煅烧,即可一步得到原位生长的三维石墨烯泡沫。该材料具有较高的比表面积(1080 m2/g)、导电性(13.8 S/cm)、晶化度,并且具有良好的自支撑能力和结构稳定性,在水流作用下不发生破裂,并可承受超过150倍自身重量的载荷,卸载后可以实现回弹。
4.3 原位自牺牲模板法
原位自牺牲模板法,即牺牲模板法,大多采用两段加热法,在第一阶段,采用水热或煅烧的方式,合成所需要的模板和前驱体,在第二阶段,将模板通过热分解,获得孔结构与模板形貌结构类似的多孔材料。其主要优点是制备工艺简单,无任何后处理,对反应仪器设备要求较低且环境友好等[40]。其缺点是需要对温度进行严格的把控,以及在最终产物中可能会存在模板分解不完全的现象,对实验药品用量及配比要求较高。Liu等[41]采用原位自牺牲模板方法通过热解双氰胺、葡萄糖和NH4VO3的混合物合成氮化钒/氮掺杂石墨烯(VN/NGr)纳米复合材料,尺寸在2~7 nm范围内的氮化钒纳米颗粒均匀地嵌入氮掺杂石墨烯骨架中。具有高比表面积和孔体积的VN/NGr纳米复合材料,在10 mV/s时表现出高达255 F/g的比电容,并具有优异的循环稳定性(2000次循环后电容保持94%)。优异的电容性能归因于氮掺杂石墨烯的优异导电性、高比表面积、高孔体积以及氮化钒和氮掺杂石墨烯的协同效应。
4.4 冰模板法
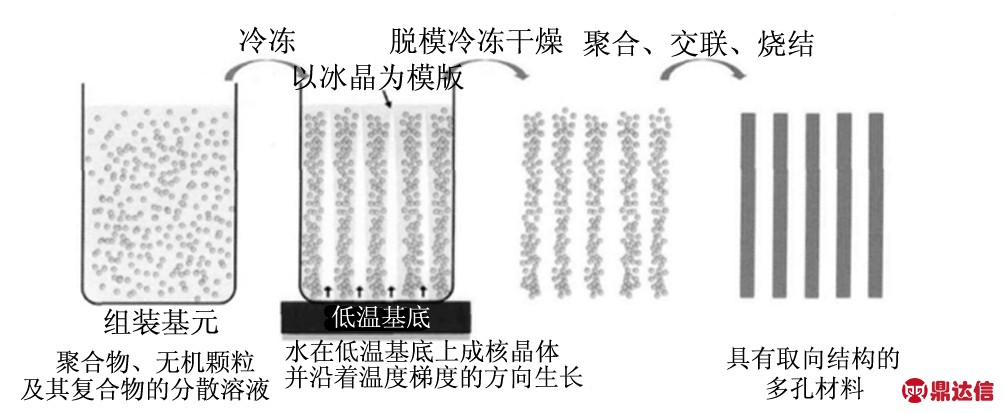
图11 冰模板法示意图[42]
Fig.11 Schematic diagram of ice template method[42]
冰模板法指利用冰冻过程中所形成的具有取向性的冰晶作为模板制备多孔材料的方法。冰模板法见图11所示,该法具有快速、易放大、环境友好的特点。与普通模板相比,冰晶作为模板更易完全去除,且实验操作更加简单。此外,通过改变反应容器的形状、分散介质的性质以及其它合成条件,还可以制成各种不同形状,例如颗粒状、块状、板状或片状的多孔材料[42],根据其制备的不同形状,会有不同的性能,未来可能会应用于很多领域,且有望成为未来制备三维多孔材料十分常用的方法。但其缺点是反应需在低温基底上持续进行,使其定向冰冻,条件较为严苛。
Sun等[43]使用冰模板法制备出了一种超轻气凝胶(Ultra-flyweight Aerogels,UFAs),密度仅为0.16 mg/cm3,约为空气密度的1/7,孔隙率高达99.9%,具有高弹性和强吸油能力。高微微等[44]同样利用冰为模板将具有不同片径的寡层GO组装成具有特定结构的3D石墨烯气凝胶,大片径GO组装的气凝胶具有更高的力学强度和抗疲劳性能。
5 结 语
石墨烯片层之间强的π-π堆叠和范德华力作用诱导石墨烯片层倾向于形成不可逆的附聚物甚至重新形成石墨,导致比表面积的显著减小,通过三维多孔结构石墨烯的构筑,并与石墨烯的固有性质相结合,是解决该问题的有效途径之一。由于模板法可以准确控制孔尺寸,且成本低、操作简单常被用来制备三维多孔石墨烯及其复合材料。近年来的研究表明,模板法在制备包括石墨烯纳米网、褶皱石墨烯、石墨烯泡沫及三维多孔石墨烯基复合材料方面取得了不错的成果。但模板法制备的三维多孔石墨烯的多孔结构和形貌高度依赖于所采用的模板,比表面积还不够理想,孔结构和孔径分布的有序性还需进一步加强,多级孔的可控构筑仍然是难点。为解决这一问题,未来的研究方向可能集中在:(1)开发新型有序阵列的模板;(2)将模板法与化学活化法相结合构造多级孔结构;(3)多种模板联用,比如硬模板与硬模板或硬模板与软模板相结合获得特定孔结构的材料;(4)探索更多三维多孔石墨烯基复合材料,以期获得性能的提升。相信随着研究的不断深入,三维多孔石墨烯及其复合材料将带来更多可观的成果。