摘要: 为研究多层异质复合靶板中装甲钢排布位置,对其塑性变形微观机理及受力状态的影响规律,开展了不同结构方式复合靶板抗侵彻试验。基于金属材料学理论,对复合靶板中装甲钢弹孔塑性变形微观机理进行研究,分析了装甲钢弹坑表面硬度分布及组织演变规律,利用数值模拟研究弹丸侵彻装甲钢过程力学行为与变形机理的内在联系。研究结果表明:波阻抗匹配由高至低,弹丸冲击应力波在层间界面反射形成拉伸波,产生裂纹扩展,降低弹丸侵彻阻力;绝热剪切带内部受温度以及挤压载荷影响,产生高硬度细化马氏体晶粒,抑制塑性变形向内延伸;装甲钢背板强度及刚度越高,对装甲钢塑性变形产生位错运动的阻碍作用越强,有利于提高弹丸开坑阻力。
关键词: 复合靶板; 侵彻; 塑性变形; 微观机理
0 引言
随反装甲武器毁伤效能的提高,对武器装备的机动性与防护性要求也越来越高,多层复合结构能够充分发挥不同材料优点[1-3],提高装甲防护能力,因而多层复合靶板成为防护领域研究热点之一。
研究人员在弹丸侵彻单一金属靶板组织变化与损伤分析[4-7]、高速冲击下金属力学行为及微观剪切结构差异[8-10]等方面做了大量工作。罗荣梅等[11]利用杆式穿甲弹侵彻30CrMnMo装甲靶板,发现弹孔表面产生熔化快凝层,通过扫描电子显微镜(SEM)及能谱分析对弹坑表面进行微观组织分析,研究熔化快凝层形貌特征及形成机理,利用非线性有限元分析软件LS-DYNA对弹靶作用区温度场进行了模拟。孙秀荣等[12]对采用相同尺寸柱型样、帽型样的4种不同结构金属材料进行了不同应变率下的动态压缩试验,对比了不同结构金属绝热剪切带演变过程及微观组织特征。索涛等[13]研究表明金属材料高速变形由于变形时间短,塑性功转变成的热量来不及消散,可视为绝热过程。温度升高引起热软化,侵彻结束后,剪切区域温度骤降,由此产生具有熔化再凝固特征的绝热剪切现象。对于复合靶板结构,由于材料特性各异及应力波的相互叠加效应,导致对其抗侵彻机理分析十分复杂,材料排布方式等对高速侵彻下复合靶板抗弹机理的影响规律并未掌握,尤其对于弹丸侵彻多层异质复合靶板中,装甲钢排布位置对其微观组织变化规律及抗弹性能影响机理研究还不够深入。近年来,通过宏观、细观及微观相结合成为研究材料性能的重要手段[14],因而通过细观及微观手段开展不同结构方式复合靶板中装甲钢侵彻变形机理研究具有重要意义。
针对复合靶板中装甲钢排布位置不同对其微观组织演化机理及受力环境影响规律这一研究问题,本文开展了14.5 mm穿甲弹对10 mm厚氧化铝陶瓷+6 mm厚616装甲钢+10 mm厚芳纶板和10 mm厚氧化铝陶瓷+10 mm厚芳纶板+6 mm厚616装甲钢两种结构靶板的侵彻试验研究,结合弹丸侵彻装甲钢板塑性变形特征,依据金属材料学理论,从细观及微观角度对比研究两种结构中装甲钢弹坑边缘典型区域硬度分布、组织演变规律,利用数值模拟分析了弹靶接触力学行为,为研究弹丸侵彻复合靶板的动力学特征及结构优化设计提供可靠理论依据。
1 穿甲试验
1.1 穿甲试验设计
为研究多层陶瓷复合靶板结构中装甲钢的排布位置及其支撑板材料对其塑性变形细观及微观机理的影响规律,开展了装甲钢位于芳纶板之前的10 mm厚氧化铝陶瓷+6 mm厚616装甲钢+10 mm厚芳纶板复合靶板(以下简称前置复合靶)侵彻试验研究,603装甲钢作为参照靶支撑在复合靶之后。
试验用枪为14.5 mm弹道枪,枪口到靶板距离10 m. 试验弹为14.5 mm穿甲弹,弹体简化模型如图1所示,全长65.5 mm,其中尖头长20.8 mm,锥底长10 mm,弹头直径14.9 mm,锥底下端直径11 mm. 采用红外光幕测速靶系统在距靶板3 m处对入射弹丸速度进行测试。样品在靶架上固定后,按预定着弹点垂直靶面入射,靶板固定状态如图2所示。
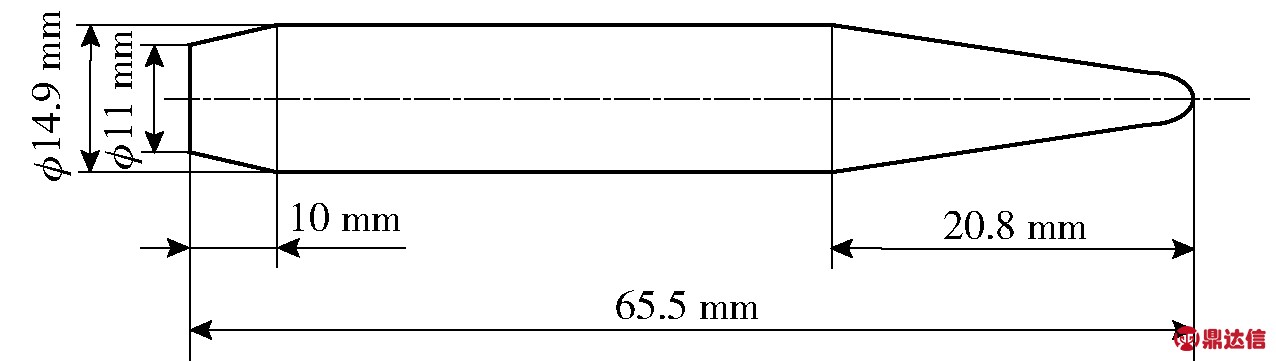
图1 14.5 mm穿甲弹弹芯尺寸
Fig.1 Core size of 14.5 mm armor piercing projectile
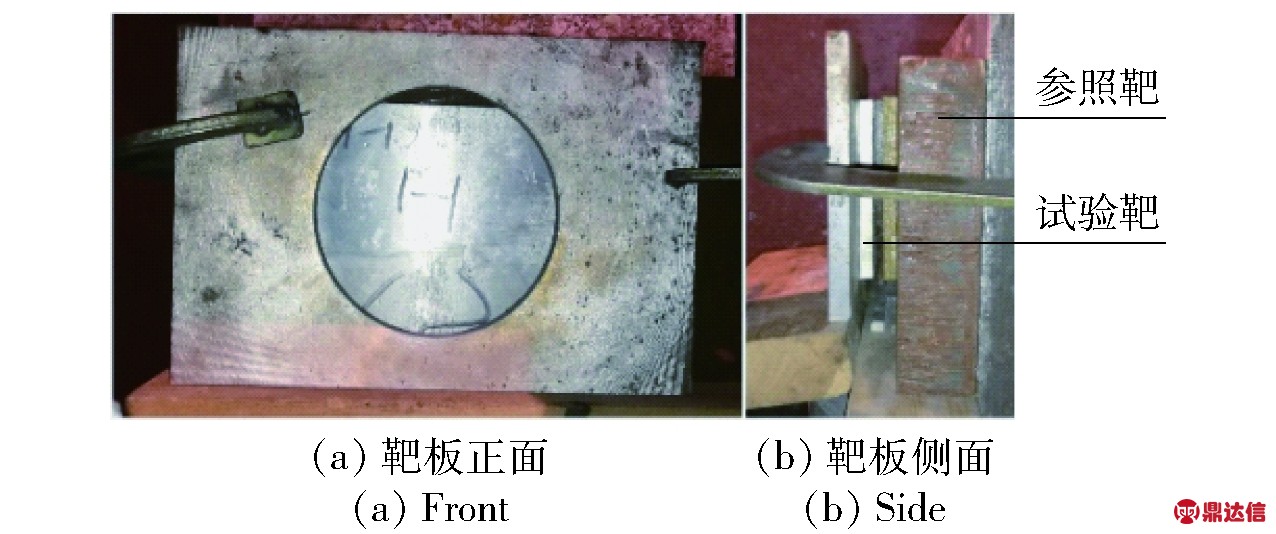
图2 靶板夹持状态
Fig.2 Clamping state of target plate
首先进行参照靶弹道试验,得出相应参考侵彻深度Pref,然后进行由试验靶板/参照靶组成的复合靶系列弹道试验,得出射弹在参照靶中剩余侵彻深度Pr及试验靶板的穿甲深度Pt,最后通过试验测得数据计算靶板防护系数f,计算公式如(1)式所示:
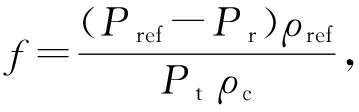
(1)
式中:ρc为复合靶板材料密度;ρref为参照靶材料密度。
1.2 试验结果及分析
试验中测得603装甲钢防护14.5 mm穿甲弹参考侵彻深度Pref=43 mm,参照靶密度ρref=7.8 g/cm3,试验靶被穿透,即Pt=26 mm,测试结果如表1所示。
表1 靶板侵彻测试结果
Tab.1 Penetration test results
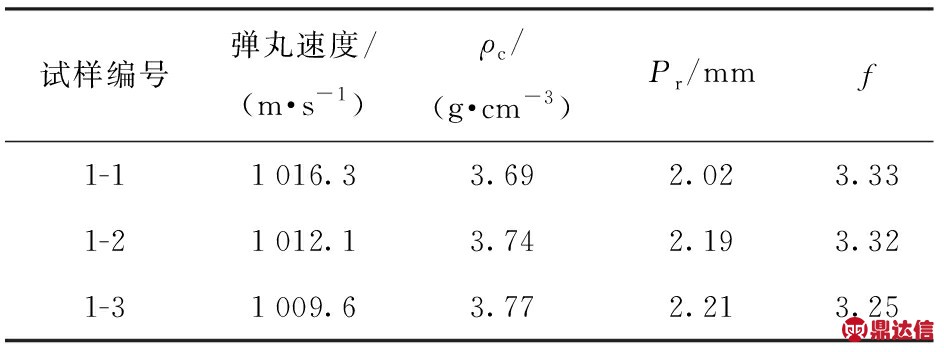
由表1可知,弹丸平均速度为1 012.7 m/s,603装甲钢平均压痕为2.14 mm,平均防护系数为3.30.
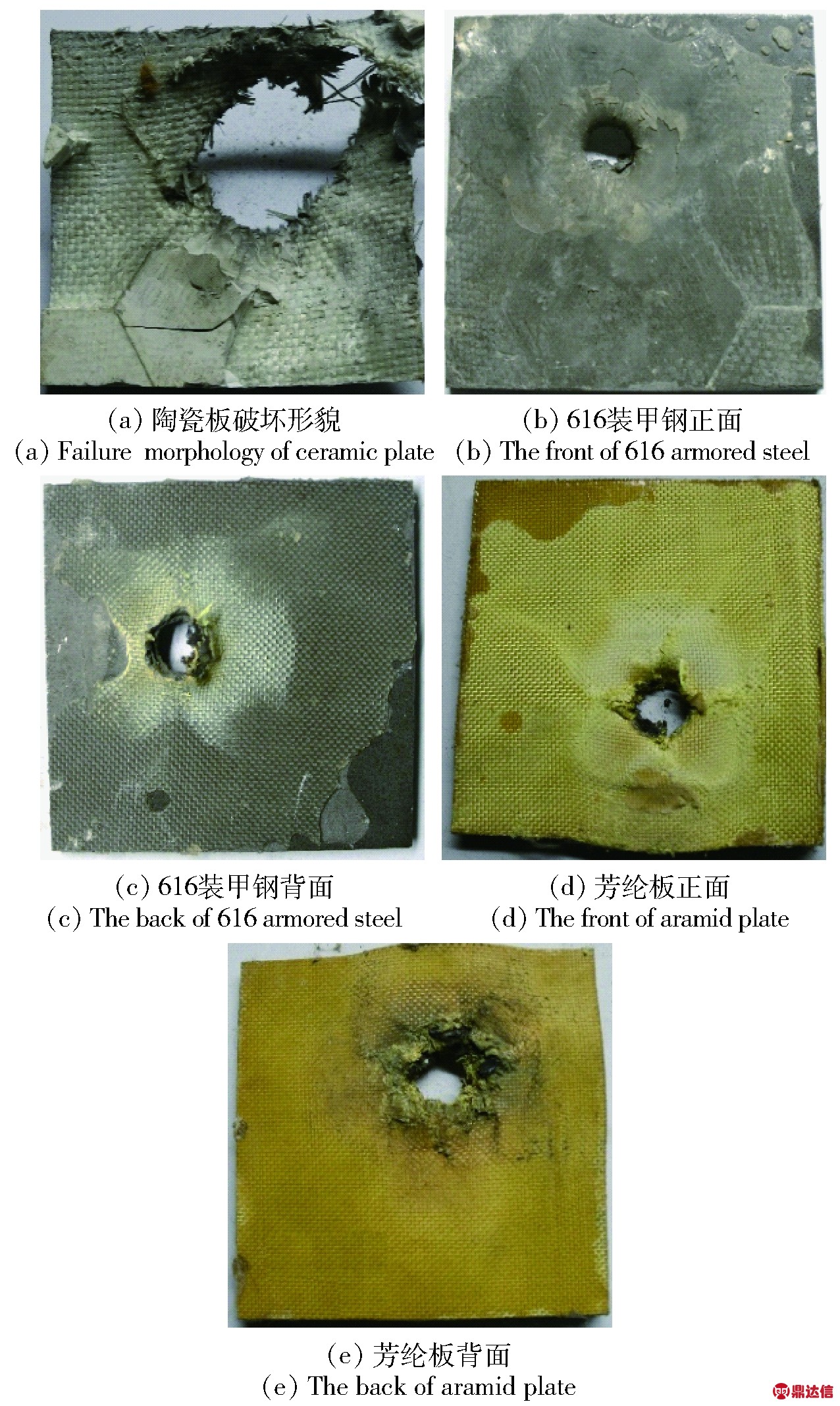
图3 复合靶板破坏形貌
Fig.3 Failure morphologies of composite target
图3所示为复合靶板破坏形貌。图3(a)所示为前置复合靶陶瓷板破坏形貌。氧化铝陶瓷、装甲钢和芳纶的波阻抗[15]分别为39 520 mg/(m2·s)、35 600 mg/(m2·s)和11 800 mg/(m2·s).陶瓷板波阻抗高于装甲钢和芳纶,陶瓷及其背板组合呈现由高到低波阻抗匹配特征,弹体冲击应力波在陶瓷背板形成反射拉伸波,陶瓷材料抗拉性能低于抗压性能,导致陶瓷面板产生崩落破坏。图3(b)、图3(c)所示为616装甲钢的宏观破坏形貌。由图3(b)、图3(c)可见:装甲钢材料在弹体压力作用下易于向最小抗力方向产生塑性流动;616装甲钢背板为芳纶,其硬度及屈服强度较低,不足以为装甲钢提供支撑,导致靶板沿侵彻方向产生塑性变形,形成延性扩孔。图3(d)、图3(e)所示为芳纶破坏形貌,从中可以看出芳纶破坏模式主要为纤维剪断失效,侵彻区以外部位几乎没有变形。
2 前置复合靶装甲钢弹孔微观组织分析
为进一步分析复合靶板结构方式对装甲钢微观损伤机理及力学行为影响规律,在复合靶616装甲钢弹孔处采用电腐蚀线切割技术取样,避免机械切割引起弹带塑性变形干扰试验结果,通过研磨、抛光以及浸蚀得到如图4(a)所示的金相试样。采用LSM700激光共聚焦显微镜对试样微观组织进行观察,弹坑边缘典型区域划分如图4(b)所示,结合数值模拟分析其弹靶界面力学行为。
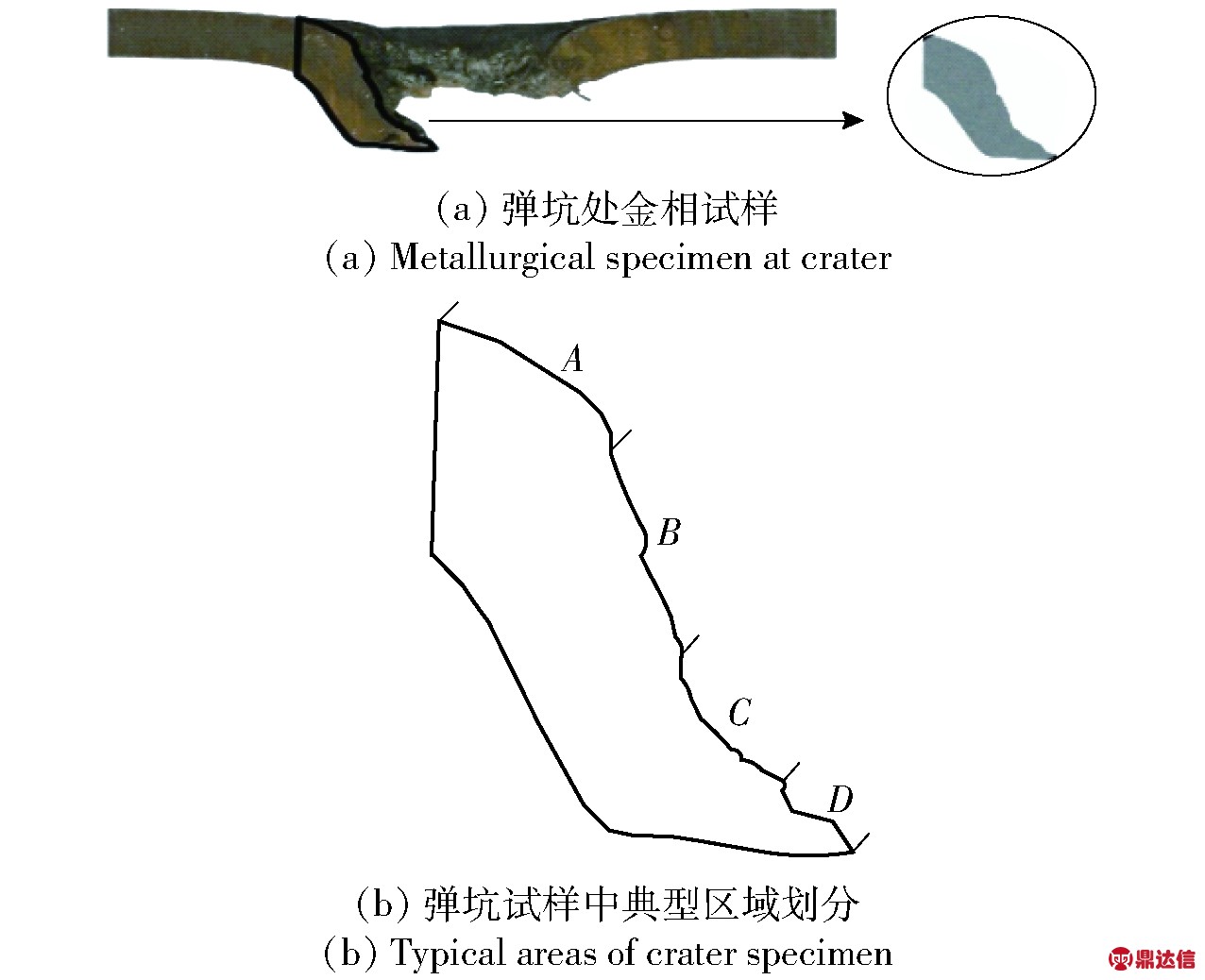
图4 金相试样
Fig.4 metallographic specimen
2.1 装甲钢原始微观组织
616装甲钢是一种低合金高强度合金钢,其最终热处理为调质或淬火加低温回火,其原始微观组织如图5(a)所示。由图5(a)可以看出内部含有大量板条状马氏体组织[8],且取向各不相同。图5(b)所示为装甲钢在高温加热和保温时表层形成的脱碳层。

图5 原始微观组织
Fig.5 Original microstructure
2.2 装甲钢弹孔金相分析
选取图4(b)沿侵彻方向A、B、C、D各区域典型微观组织形貌分别如图6(a)~图6(d)所示。
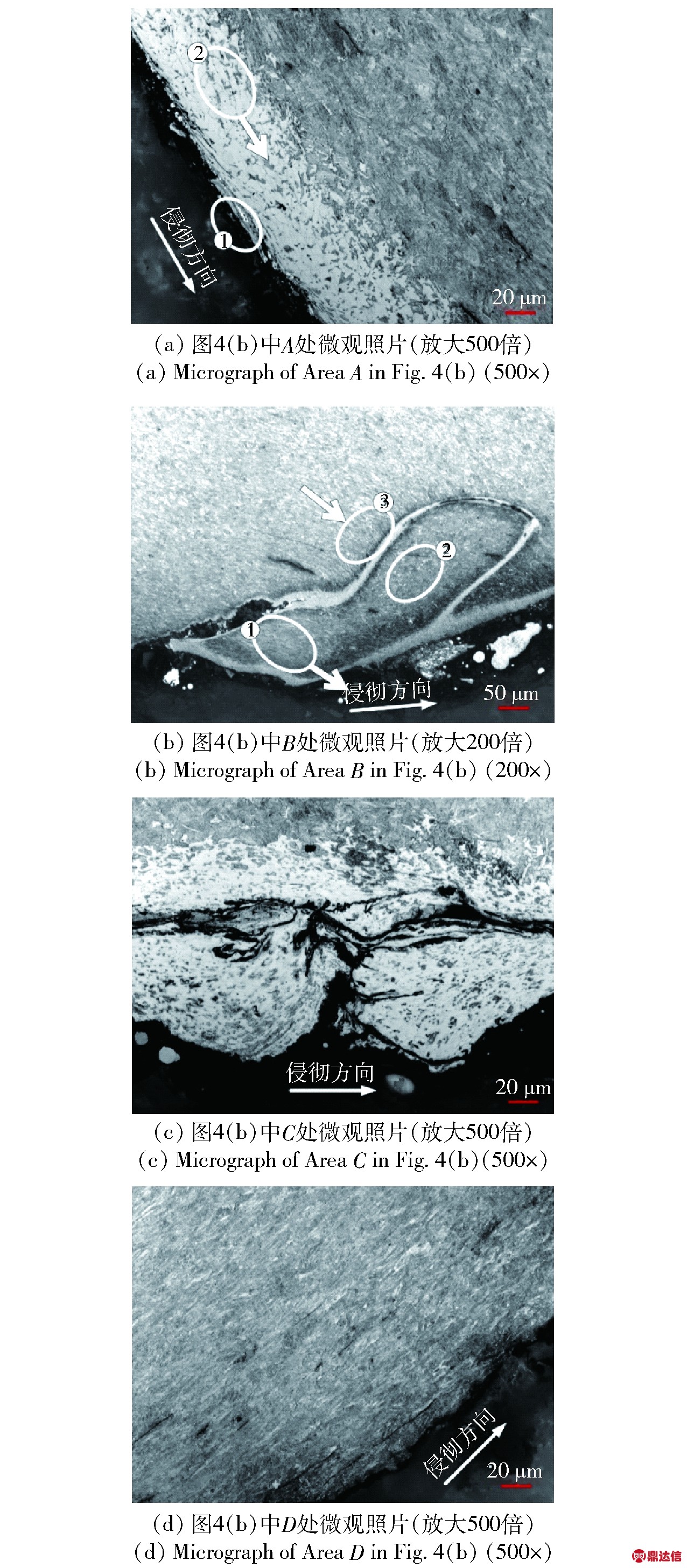
图6 前置复合靶装甲钢弹坑边缘金相显微图像
Fig.6 metallographic micrographs of armored steel crater edge in pre-composite target
图6(a)取自图4(b)中弹丸侵彻起始部位A处微观组织,对椭圆①区域边缘处进行能谱分析,元素为铅,如图7所示,表明弹靶接触表面有弹丸残留。由图6(a)可以看出,表面脱碳组织在弹丸冲击作用下产生明显的拉长变形(椭圆②区域),与弹丸侵彻方向平行,而并非剪切效应最大的45°方向,表明此阶段弹靶之间剪切作用不明显,扩孔阶段的装甲钢沿弹丸侵彻方向产生塑性变形。
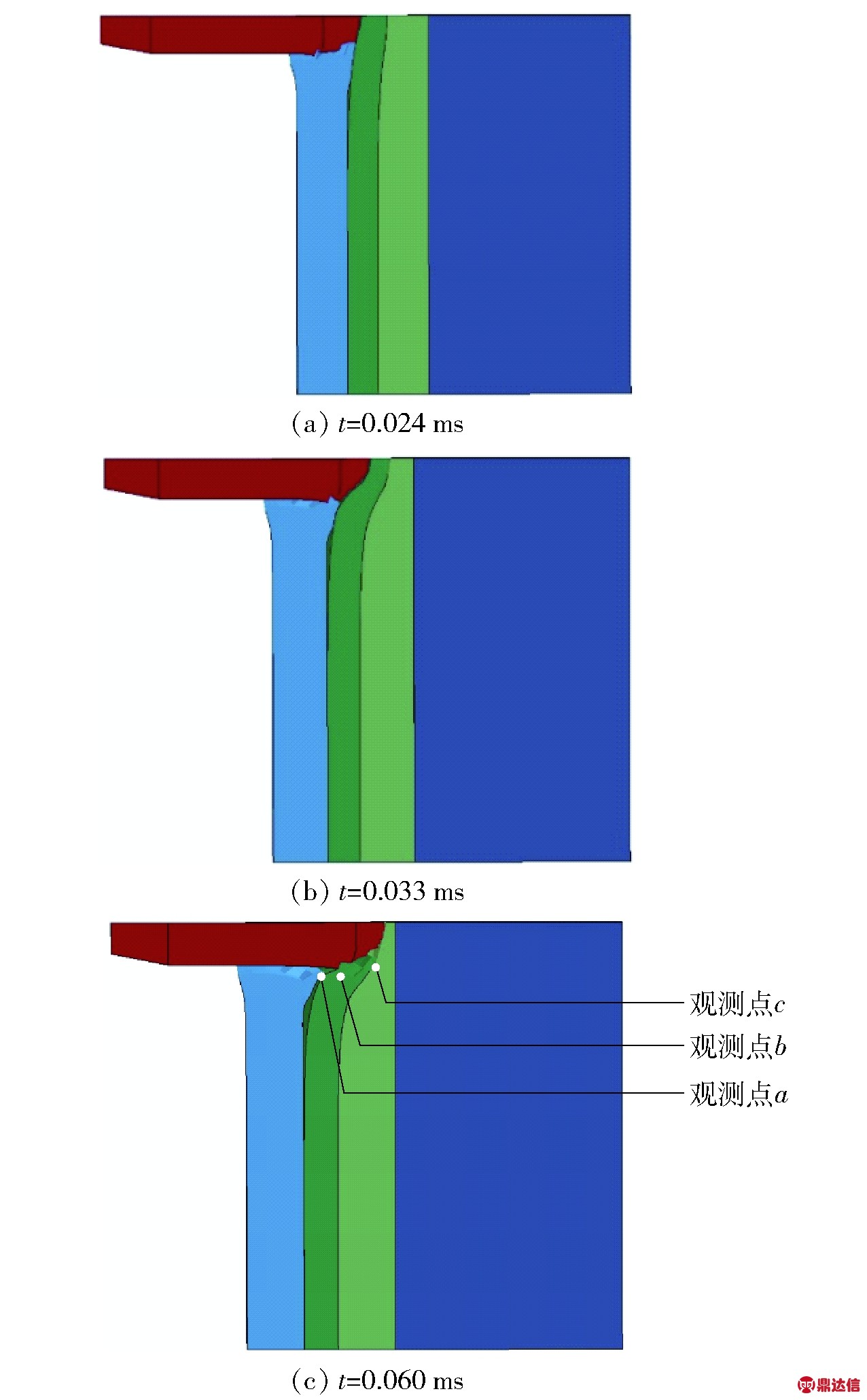
图7 能谱分析
Fig.7 Energy spectrum analysis
根据图6(b)所示微观组织观察,弹孔中间部位图4(b)中B区域产生一条闭环白色带,已有研究[16-17]表明为绝热剪切带。弹丸侵彻装甲钢过程中,材料产生高速大变形,大量塑性功转化为热量,由于变形时间很短,塑性功产生热量来不及通过热传导散失,导致在一个狭窄区域内产生绝热温升。材料热塑性变形导致塑性流动应力降低,促进塑性变形加速发展,产生更多热量,塑性变形生成热量和材料强度软化效应相互促进导致绝热剪切带的形成。如图6(b)所示,剪切带包围区域可以分为两部分:1)侵彻前端(椭圆①区域),可发现晶粒细密且晶粒拉长方向同剪切带约呈45°;2)侵彻后端(椭圆②区域)相较于侵彻前端晶粒粗大,且晶粒走向并无明显规律,由此可知在此区域内弹靶之间沿45°方向剪应力效应不明显。内侧剪切带周围晶粒出现垂直于剪切带方向的偏转伸长(椭圆③区域),说明在垂直于侵彻带方向产生侧向力作用。弹坑边缘中后部位C区域,如图6(c)所示出现大量白色晶粒夹杂黑色物质。采用Tukon 2500 Minuteman全自动显微维氏硬度计进行硬度测试,此区域晶粒硬度为299 HV,远低于原始组织中马氏体硬度440 HV,分析认为,弹丸在侵彻靶板过程中塑性变形产生热量,弹孔中间部位散热速率低于两侧位置,冷却速度慢,导致形成大量铁素体,伴随析出碳化物颗粒。在图4(b)中弹孔末端D,弹孔壁组织如图6(d)所示,研究发现在此阶段无绝热剪切带形成,晶粒沿弹丸侵彻方向拉长,在平行于侵彻方向产生了大量裂纹。绝热剪切带消失说明在此阶段弹靶接触作用减弱,塑性变形产生热量减小不足以达到绝热剪切带形成条件。
2.3 数值分析
数值模拟是弹靶侵彻常用分析手段,现有数值模拟软件还不能再现微观组织形成过程。弹丸侵彻过程中,靶板受力状态是影响塑性变形微观组织变化的重要因素,由于侵彻过程瞬间完成,弹靶之间相互作用难以现场测得,因此可利用LS-DYNA软件模拟靶板侵彻试验,获得侵彻过程中靶板受力状态,以研究弹靶界面力学行为同变形机理的内在联系。
根据实际工况,由于侵彻是轴对称的,为减小计算量,建立1/4对称模型,在对称面及周边施加约束;弹丸与靶板以及各层靶板之间均使用面- 面侵蚀接触算法;采用六面体网格,弹体头部网格密集,弹杆部位相对稀疏,靶板网格尺寸为0.5 mm.
弹体、616装甲钢及603装甲钢均采用Johnson-Cook模型和Gruneisen状态方程,芳纶材料采用Solid-Composite-Failure-Solid-Mode模型,陶瓷材料采用JH-2模型即MAT-JOHNSON-HOLMQUIST-CERAMICS模型,相应材料参数分别如表2~表4所示,主要材料参数参照文献[18-20],表中各符号均为LS-DYNA材料模型中特定参数符号。
表2 弹体、616装甲钢及603装甲钢材料模型参数
Tab.2 Material model parameters of projectile body, 616 armour steel, and 603 armour steel

注:ρ为材料密度,G为材料剪切模量,A为屈服应力常数,B为应变硬化常数,n为应变硬化指数,C为应变率相关系数,m为温度影响指数,D1、D2、D3、D4、D5为材料损伤系数,γ0为温度系数,c为应力波传播速度,S1为剪切系数。
表3 陶瓷材料模型参数
Tab.3 Material model parameters of ceramic material

注:ρ为材料密度,G为材料剪切模量,
为参照应变率,T为最大拉伸强度,pHEL为静水压力,HEL为Hugoniot弹性极限强度,A、B、C、M、N、D1、D2为材料常数,β为损失的弹性能转为静水压势能部分(0≤β≤1),K1为材料体积模量,K2、K3为材料常数。
为验证数值模型正确性,基于弹丸侵彻试验结果,对初始速度为1 012.7 m/s弹丸侵彻前置复合靶进行数值模拟,弹体模型未考虑实际弹丸表面的覆铜层和铅套。数值模拟结果表明,陶瓷复合靶板被完全穿透并在参照靶上留下3 mm穿甲深度,其总穿甲深度为29 mm,与实际总穿甲深度28.14 mm相比误差为3.05%,数值模拟结果与试验结果吻合较好。弹丸侵彻复合靶板过程中装甲钢毁伤效果如图8所示。
表4 芳纶材料模型参数
Tab.4 Material model parameters of aramid material

注:RO为材料密度,EA、EB、EC分别为横向、纵向和面内弹性模量,PRBA、PRCA、PRCB为材料泊松比,GAB、GBC、GCA为材料剪切模量,MACF表示坐标系选择方式,SBA、SCA、SCB为材料剪切失效应力,XXC、YYC、ZZC为横向、纵向和面内压缩失效应力,XXT、YYT、ZZT为横向、纵向和面内拉伸失效应力。
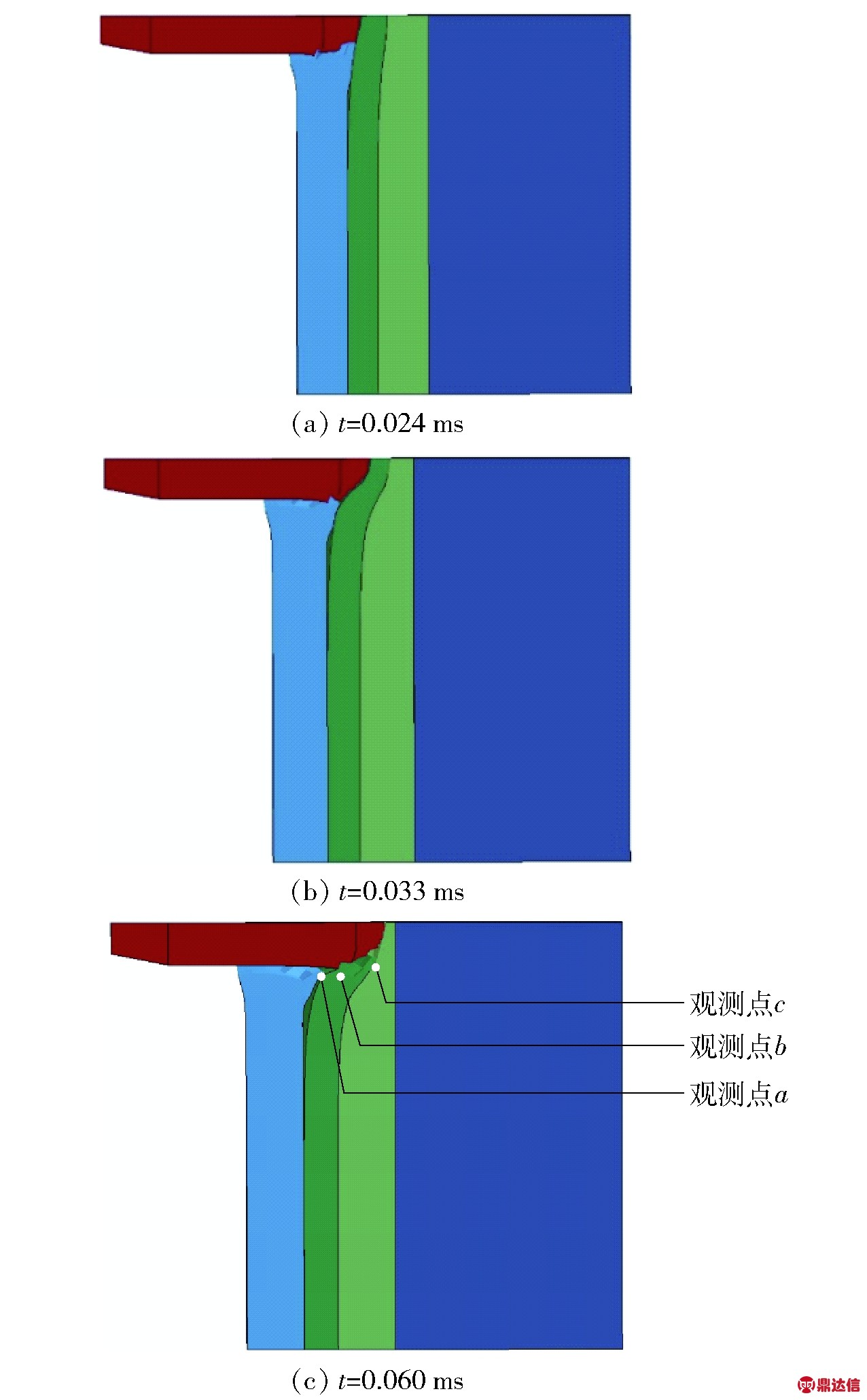
图8 数值模拟结果
Fig.8 Numerically simulated results
对616装甲钢弹孔壁处受力状态模拟结果进行分析,沿弹丸侵彻方向在装甲钢弹孔边缘设立a、b、c 3个观测点,观测点位置如图8(c)所示,以获得侵彻过程中弹靶交界面的压力变化情况(见图9)。
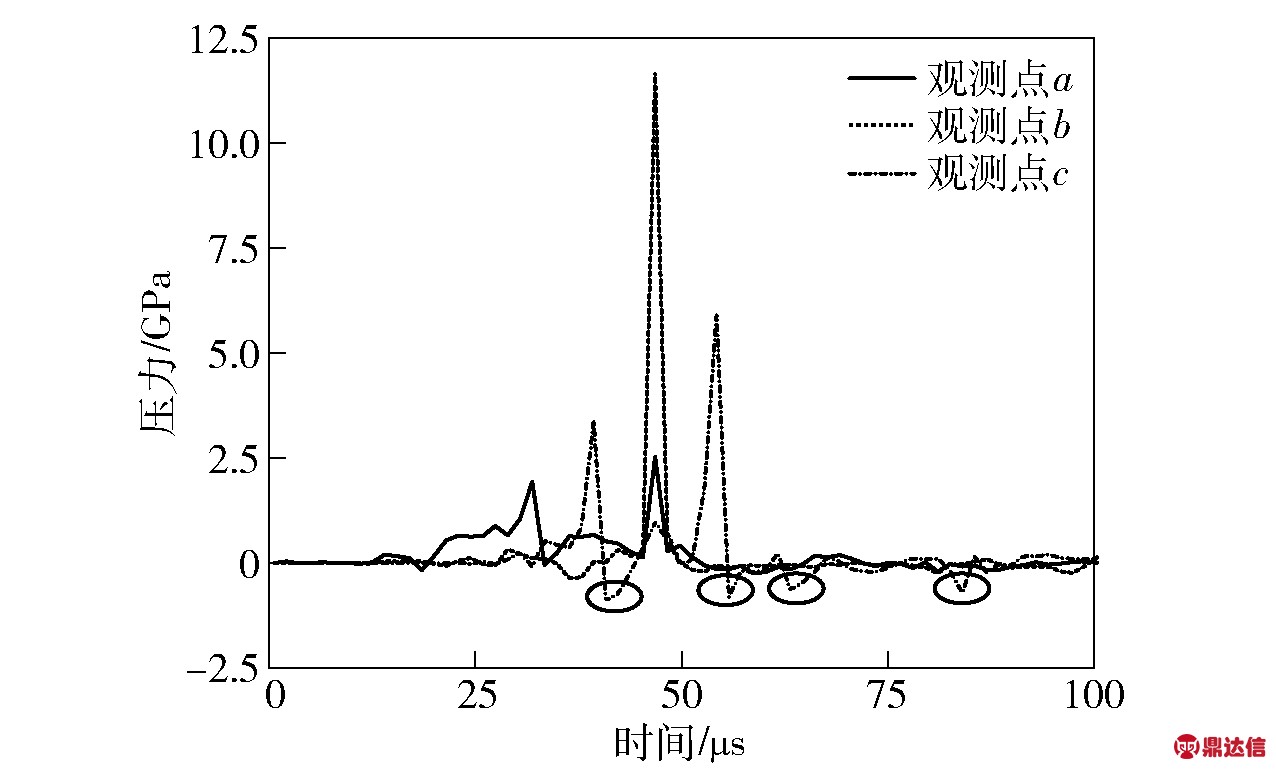
图9 616装甲钢孔壁节点压力- 时间曲线
Fig.9 Pressure-time curves at projectile holes on 616 armored steel
根据装甲钢细观及微观组织变化过程和数值仿真结果,分析如下:
1)在弹靶刚开始接触阶段,a点受力相对较小,此阶段只有惯性力和压缩力作用于弹丸上,随弹丸挤进,弹靶之间作用力出现峰值,靶板中一部分材料受弹头压缩获得与弹丸相同速度共同侵彻靶板。结合靶板变形特征,刚开始接触阶段以延性扩孔为主,弹靶接触表面脱碳组织沿侵彻方向变形,同弹靶接触初期相互作用较弱的特征符合。
2) b点相较于a点和c点压力峰值最高,在t=46 μs达到峰值,可知弹丸侵彻至中间部位,弹靶间作用力达到最大。弹丸侵彻靶板,弹靶接触表面产生塑性变形,生成大量热导致靶板材料出现热软化,热软化促进材料加速变形,二者相互促进作用导致绝热剪切带的形成。由于靶板在与侵彻方向呈45°夹角所受剪切力最大,因而绝热剪切带周围组织晶粒拉长方向同剪切带约呈45°夹角,且剪切带产生的分叉与侵彻方向也呈45°夹角。弹孔沿侵彻方向仅在中间位置产生绝热剪切包围带。分析认为前置复合靶中装甲钢的背板为芳纶材料,难以为钢板变形提供支撑,塑性变形过程中产生的位错阻碍作用较弱,产生热量不足,因而产生的绝热剪切带少。
3) c点在弹丸开始接触装甲钢板时,由于应力波的传播即产生压力作用,直至弹丸侵彻靶板背部时达到峰值,相较于弹丸侵彻中间部位,弹靶之间接触力减弱,且在弹丸侵彻过程中,产生多次卸载(图9中椭圆区域)。结合微观组织特征,分析认为装甲钢背板为芳纶材料,其波阻抗低于装甲钢,弹丸侵彻靶板产生应力波在层间界面发生反射,弹丸侵彻装甲钢出现卸载,卸载波相互作用产生局部较强拉伸应力,导致距弹孔壁一定深度范围内形成大量微裂纹,由于卸载波的出现,弹丸侵彻阻力下降,不利于装甲防护性能提高。
综上所述,616装甲钢背板支撑强度及波阻抗匹配效应对微观损伤机理具有重要影响。支撑强度不足,导致弹靶之间接触力较小,装甲钢在塑性变形过程中位错运动阻碍较小,不足以提供绝热剪切带形成条件。波阻抗匹配由高至低,导致层间界面反射拉伸应力波,产生大量微裂纹,弹丸侵彻阻力下降。上述两方面均不利于装甲防护性能提高。
3 后置复合靶装甲钢弹孔微观组织分析
为了验证装甲钢背板对其微观损伤机理的影响,将616装甲钢置于芳纶之后,603装甲钢为其提供支撑,对结构为10 mm厚氧化铝陶瓷+10 mm厚芳纶板+6 mm厚616装甲钢的复合靶板(以下简称后置复合靶)开展侵彻试验研究,测试结果如表5所示。
表5 靶板侵彻测试结果
Tab.5 Penetration test results
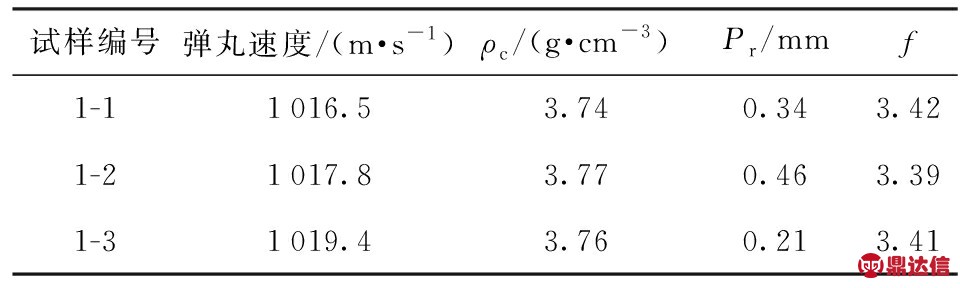
弹丸平均速度为1 017.9 m/s,后置复合靶被穿透,在背部产生裂纹孔,603装甲钢平均压痕为0.34 mm深,平均防护系数为3.41,后置复合靶防护效果明显优于前置复合靶,一定程度表明616装甲钢背板的支撑作用对其防护效果具有显著影响。图10所示为后置复合靶破坏形貌。
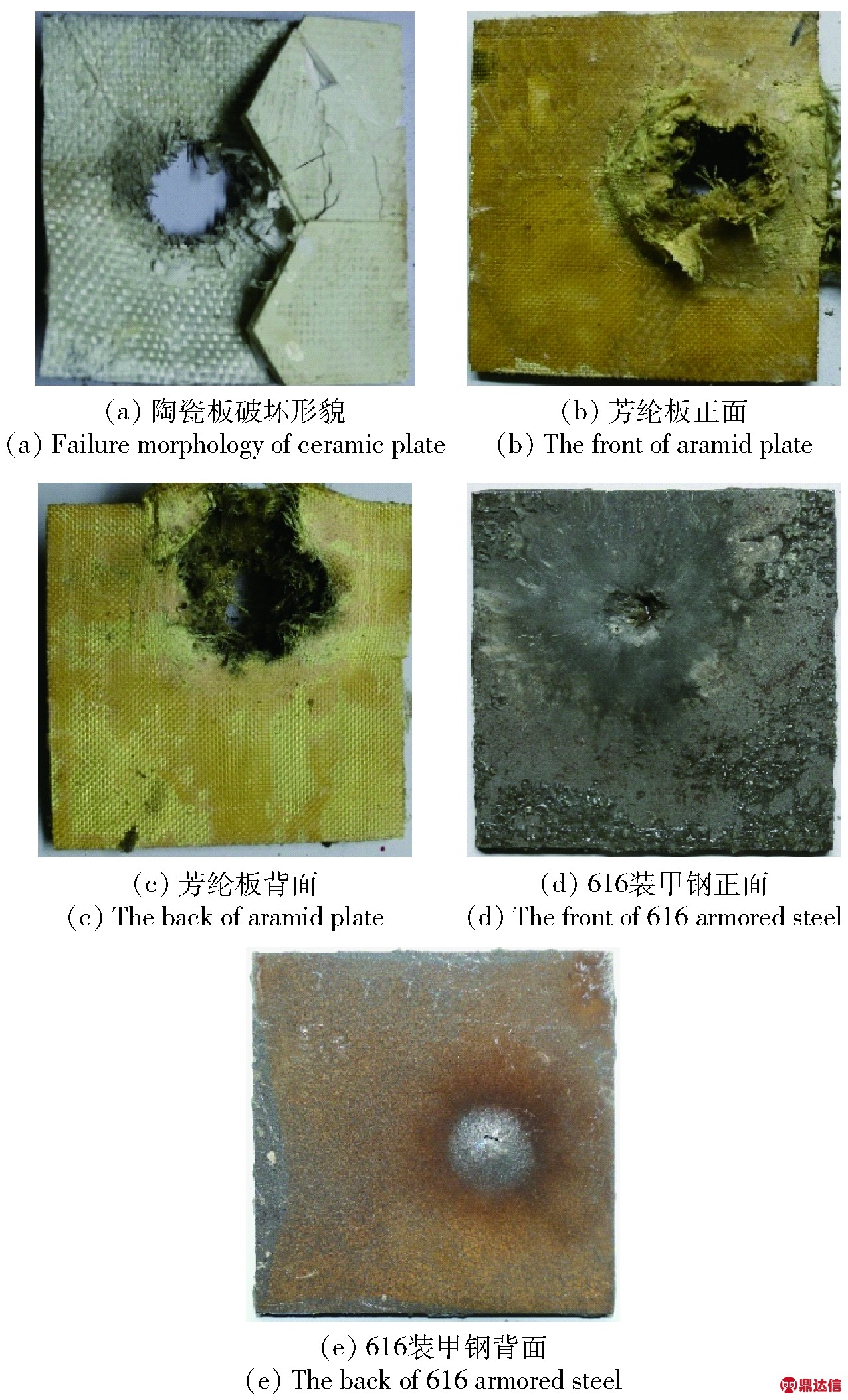
图10 复合靶破坏形貌
Fig.10 Failure morphologies of composite target
图10(a)为复合靶陶瓷板破坏形貌,破坏形式同前置复合靶基本相同,但完好程度优于前置复合靶。图10(b)和图10(c)为芳纶板破坏形貌,从中可以看出受冲击正面到冲击背面呈喇叭形放大,原因在于纤维复合材料在弹体高速撞击作用下发生压缩和剪切破坏,剪切波具有横向传播效应,因而在芳纶板背面形成喇叭形放大的变形锥。此外,后置复合靶芳纶板作为夹层,弹丸侵彻动能尚未充分消耗,侵彻过程中产生的冲击强度远高于芳纶板抗剪切、压缩强度,因而芳纶板呈现明显的纤维拉伸破坏特征。图10(d)和图10(e)为616装甲钢宏观破坏形貌,其背板为603装甲钢,在侵彻过程中提供强度支撑,对装甲钢塑性变形具有阻碍作用,616装甲钢表面产生挤凿扩孔破坏。
3.1 装甲钢弹坑金相分析
后置复合靶616装甲钢弹孔处金相试样如图11(a)所示,弹坑边缘典型区域划分如图11(b)所示。
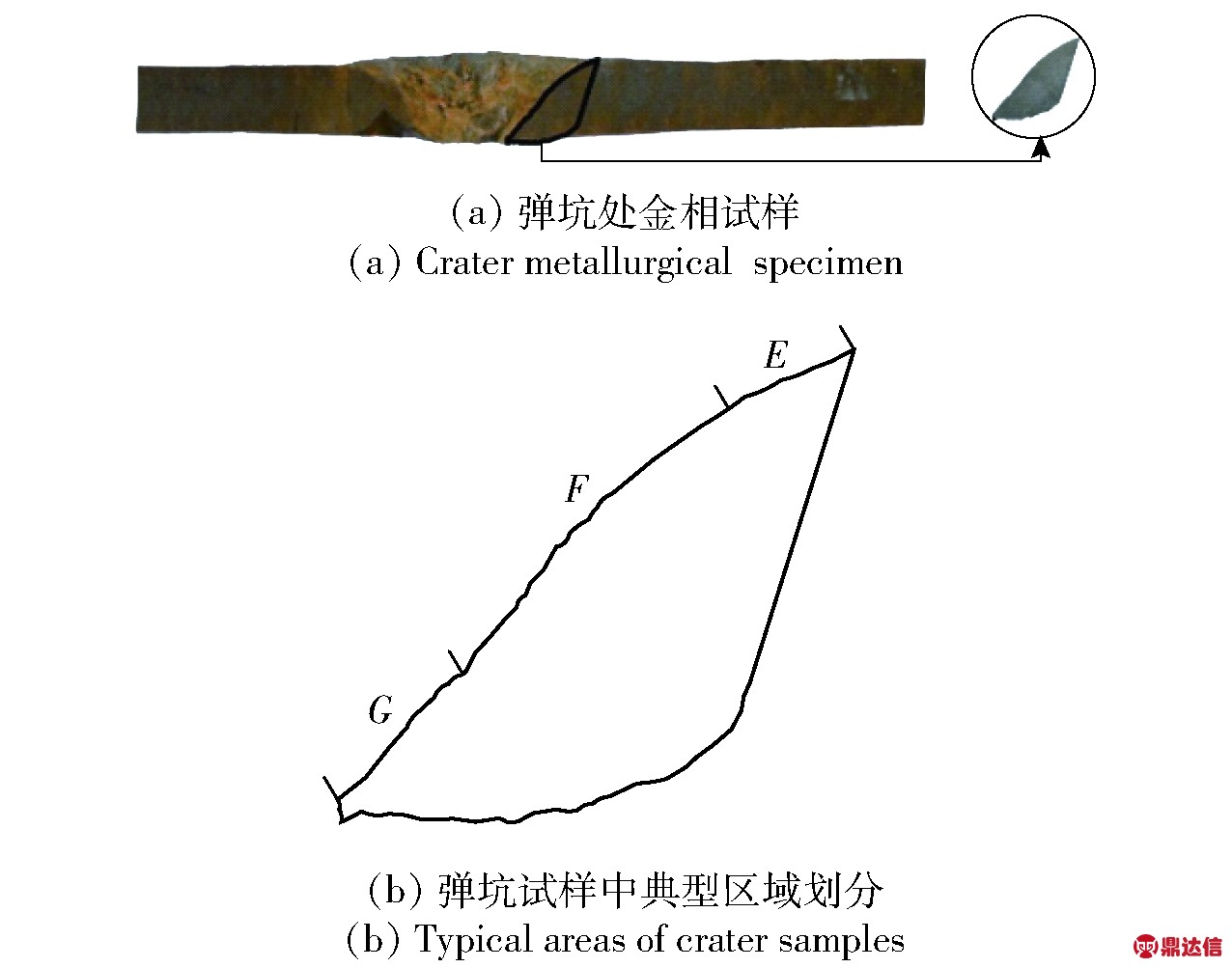
图11 金相试样
Fig.11 metallographic specimen
通过图11对其微观形貌进行分析,结果显示,同前置复合靶相比,沿弹丸侵彻方向存在大量绝热剪切带,但不同位置组织形貌由于所受弹丸侵彻载荷及由此产生的热效应不同而存在差异。沿侵彻方向各区域的典型图像如图12(a)~图12(e)所示,图中深黑色区域为镶嵌材料。
图12(a)取自后置复合靶装甲钢弹丸侵彻起始部位E,靶板表面脱碳层沿侵彻约呈45°夹角伸长。在弹坑中间部位F,如图12(b)所示沿侵彻方向绝热剪切带厚度增加,分布在20~40 μm间,并出现与侵彻方向呈45°夹角的绝热剪切带分叉(图12(c)中椭圆区域①)。图12(d)为图12(c)椭圆区域②在放大500倍下的微观组织形貌,通过图12(b)、图12(c)、图12(d)对比分析可知,随弹丸侵彻不断深入,塑性变形加剧,产生热量不断增加,由塑性变形产生的热效应及材料强度软化效应导致的绝热剪切带宽度也逐渐增加。在绝热剪切带附近区域可以观察到大量拉长晶粒,相较于原始组织,晶粒更加细密且拉长方向同弹丸侵彻方向夹角约为45°. 图12(e)取自图11(b)中弹坑底部区域G,绝热剪切带厚度仅10~20 μm且不连续,剪切带周围晶粒未出现明显沿某一方向拉长变形。
3.2 数值分析
对后置复合靶侵彻试验进行数值模拟,设定弹丸初始速度为1 017.9 m/s,数值结果表明,后置复合靶板被穿透,并在603装甲钢产生了0.5 mm深凹坑,其总穿甲深度为26.5 mm,与实际总穿甲深度26.34 mm相比误差为0.6%,可知数值模拟结果与试验结果吻合良好。弹丸侵彻后置复合靶板中装甲钢的毁伤效果如图13所示。
沿弹丸侵彻方向在装甲钢弹孔边缘设立d、e、f 3个观测点,观测点位置如图13(c)所示。获得侵彻过程中弹靶交界面的压力变化情况如图14所示。
结合后置复合靶板微观组织形貌及弹靶界面力学行为分析如下:
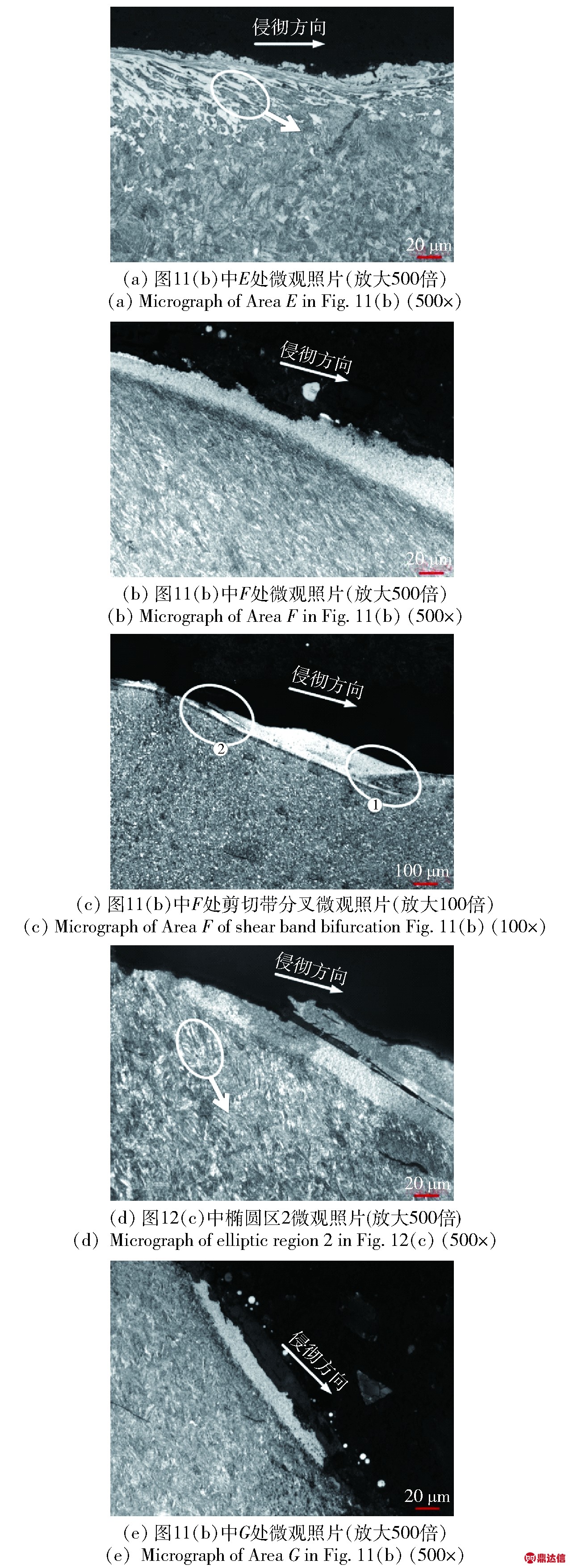
图12 后置复合靶装甲钢弹坑边缘金相显微图像
Fig.12 metallographic micrographs of armored steel crater edge in post-composite target
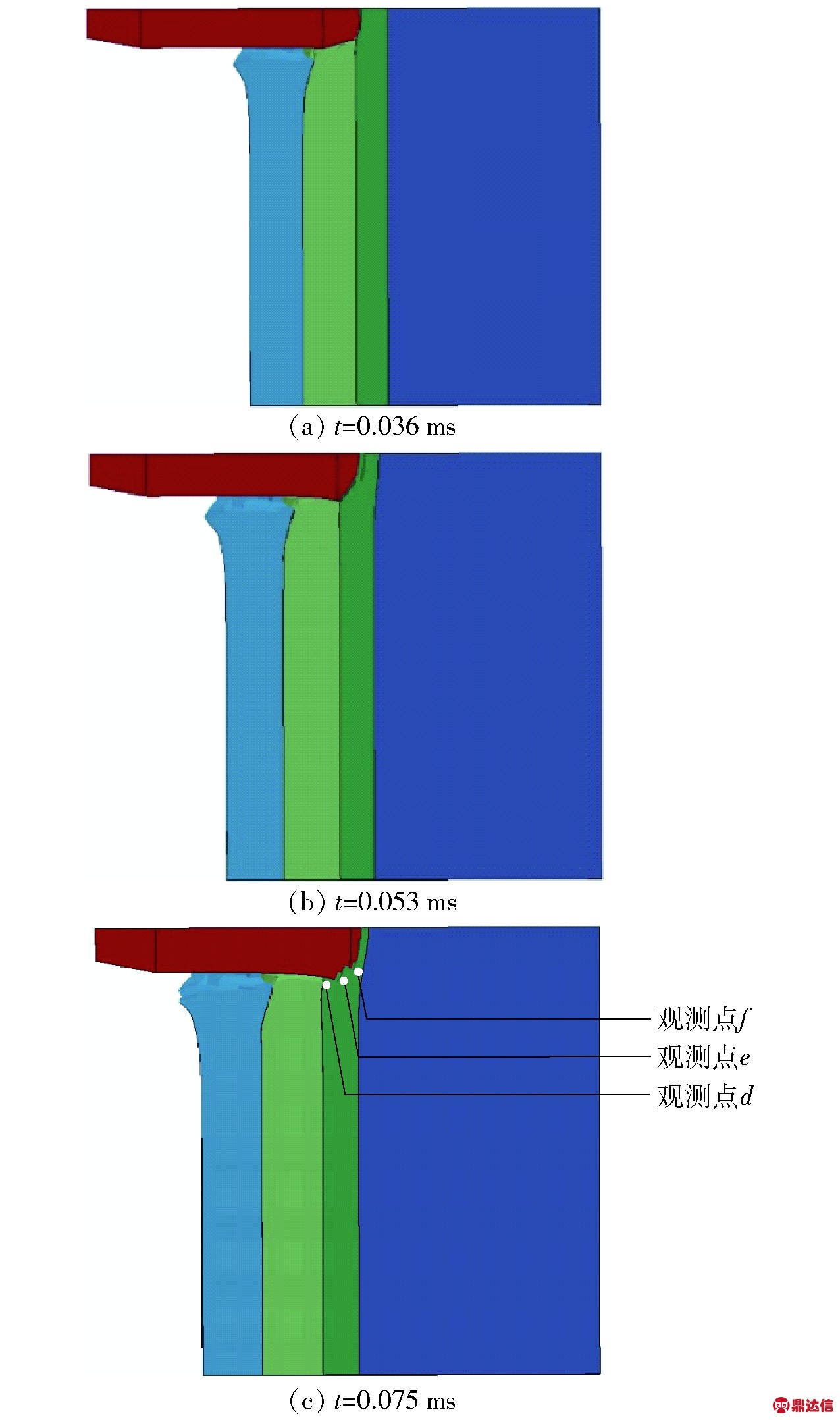
图13 数值模拟结果
Fig.13 Numerically simulated results
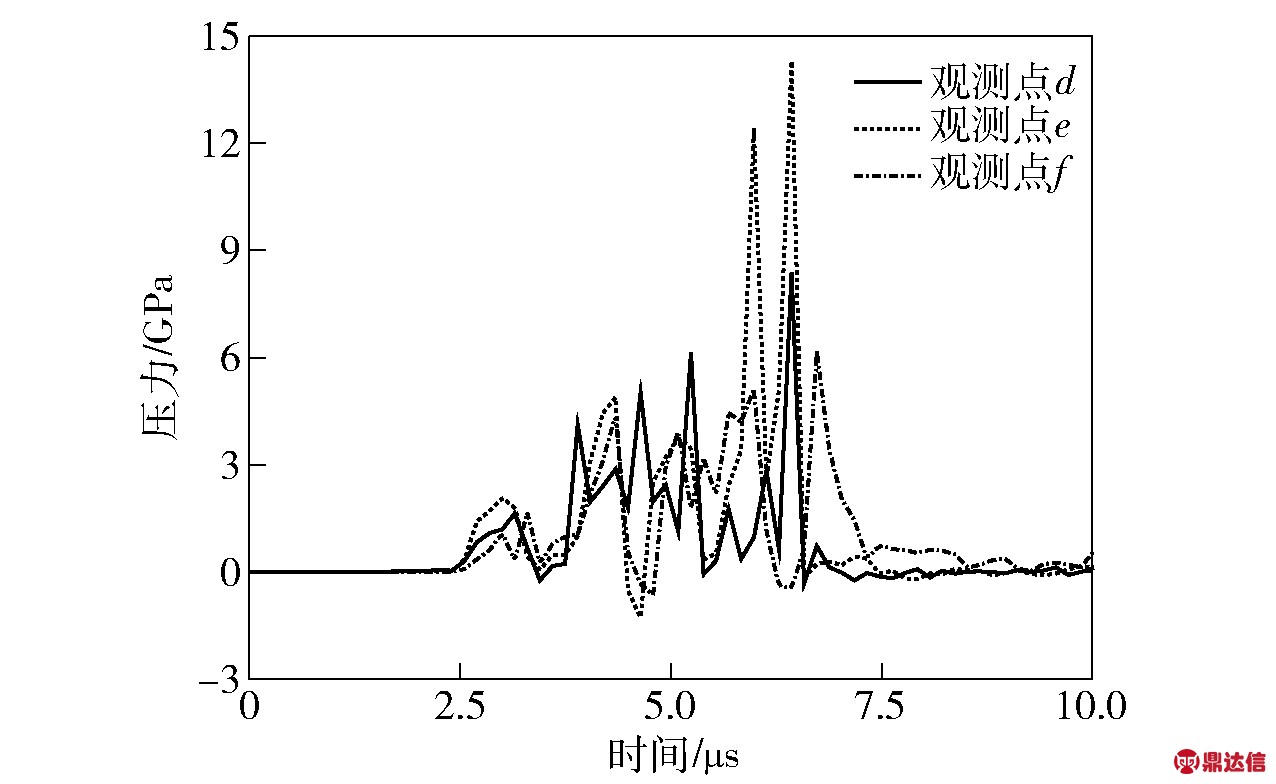
图14 616装甲钢孔壁节点压力- 时间曲线
Fig.14 Pressure-time curves at projectile holes on 616 armored steel
1)与前置复合靶相同,在弹靶刚开始接触阶段,弹靶之间作用力相对较小,装甲钢受到冲击变形不足以形成绝热剪切带,但弹丸挤进部位d点所受压力明显高于前置复合靶a点。由宏观变形可知,此阶段主要以开坑为主,在微观组织上弹靶周围组织产生同侵彻方向呈45°夹角的晶粒拉长,相较于前置复合靶剪切作用明显。
2)e点相较d点、f点受力最大,且明显高于前置复合靶b点峰值,结合微观组织,在弹坑沿侵彻方向中间部位产生大量剪切带,且随侵彻深度增加,剪切带厚度有所增加。同前置复合靶微观组织及力学行为差异表明,装甲钢背板支撑强度对其抗侵彻特性具有显著影响,绝热剪切带的形成与材料的塑性变形机理有关。钢的塑性变形以位错形式完成,位错在运动中受到第2相粒子及晶界等阻碍,形成位错塞积群,Senthil等[21]研究表明材料强度越高,越容易满足绝热剪切带形成条件。后置复合靶中,616装甲钢支撑板为603装甲钢,其具有高强度和高刚度力学特性,对616装甲钢塑性变形产生强阻碍,形成位错塞积群所需应力大。当冲击强度超过临界应力时,位错塞积崩塌,在弹坑边缘区域形成高密度位错及应力集中,位错在剪应力作用下运动,更容易达到临界条件发展成为绝热剪切带。
3)弹丸侵彻至装甲钢背部,由f点受力特点可知,相较于e点,弹靶之间接触力减弱,在微观组织中剪切带的形成出现间隔。在侵彻结束阶段,弹丸侵彻靶板能力减弱,靶板变形速度有所减缓,剪切带作为能量的一种释放方式,可以协调一定区域变形,只有在变形不协调累积到一定程度才会发生另一次绝热剪切。乔立等[22]研究表明,同裂纹相比,剪切带的形成是一种更为有效的耗散能量方式。弹丸侵彻装甲钢后期损伤形式的差异,可为靶板设计提供参考依据。
3.3 剪切带SEM分析
利用Ultra55场发射SEM对弹坑边缘微观组织形貌进行观察,如图15所示,弹坑边缘可分为弹丸残留区、绝热剪切层、变形细晶层、形变层4个区域。
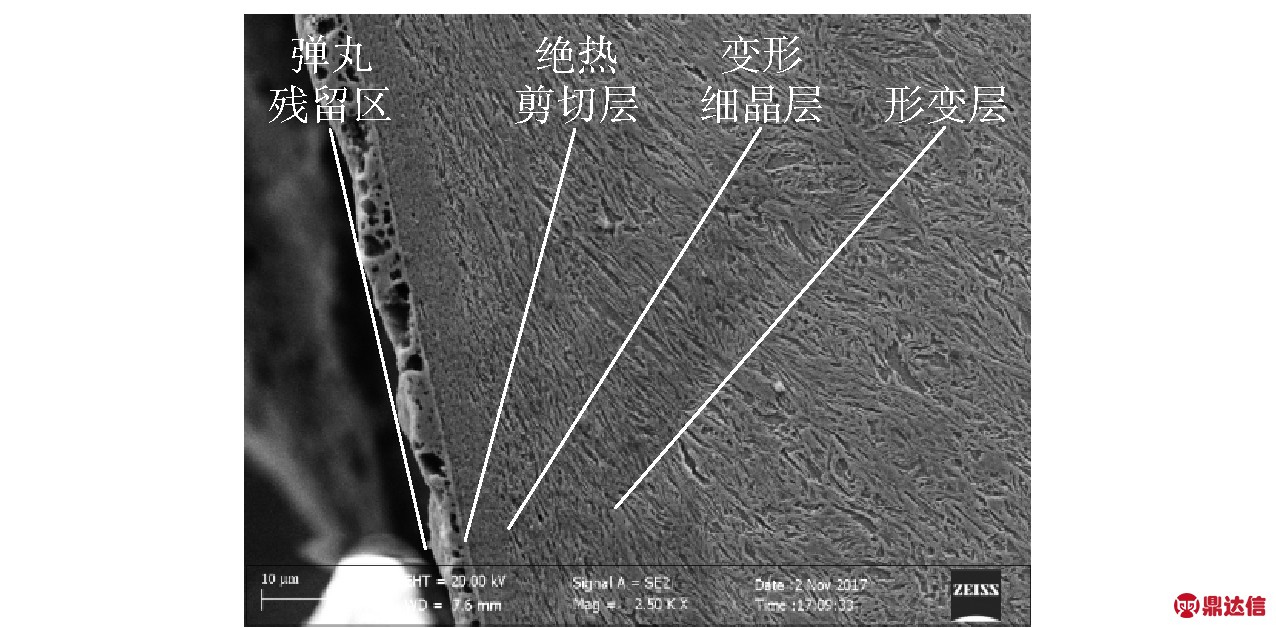
图15 绝热剪切带SEM图像(放大2 500倍)
Fig.15 SEM image of adiabatic shear bands (2 500×)
由图15可见:弹丸残留区与图6(a)中椭圆区域①相同,均为弹丸侵彻残留;绝热剪切层经硝酸酒精腐蚀后未显示组织特征;在剪切带临近变形细晶层为10~15 μm厚细化马氏体组织,晶粒取向与侵彻方向夹角约为30°,分析认为受绝热剪切温度影响,金属温度升高,原子活动能力增强,原子间结合力降低,使滑移阻力降低。在剪切力作用下,剪切带周围组织产生了塑性变形,向趋于受力方向晶面转动,使处于任意位向的晶粒调整为取向趋于一致,这种择优取向效应使剪切带周围组织表现出明显各向异性特征[23],在宏观上表现为该区域材料硬度显著提高,与测得的维氏硬度结果具有一致性。不同区域硬度测试结果表明:由绝热剪切带到变形细晶层硬度升高,变形细晶层高硬度马氏体组织有助于承受外界载荷,在一定程度上抑制塑性变形向内层延伸,提高弹丸开坑阻力;在形变层马氏体组织相较于形变细晶层晶粒粗大,且晶粒取向同侵彻方向夹角也增大,约为45°.变形细晶层和形变层晶粒取向差异主要是由于两个区域受到挤压变形程度不同影响了其方向的改变。图16所示为弹坑边缘各典型区域的维氏硬度。
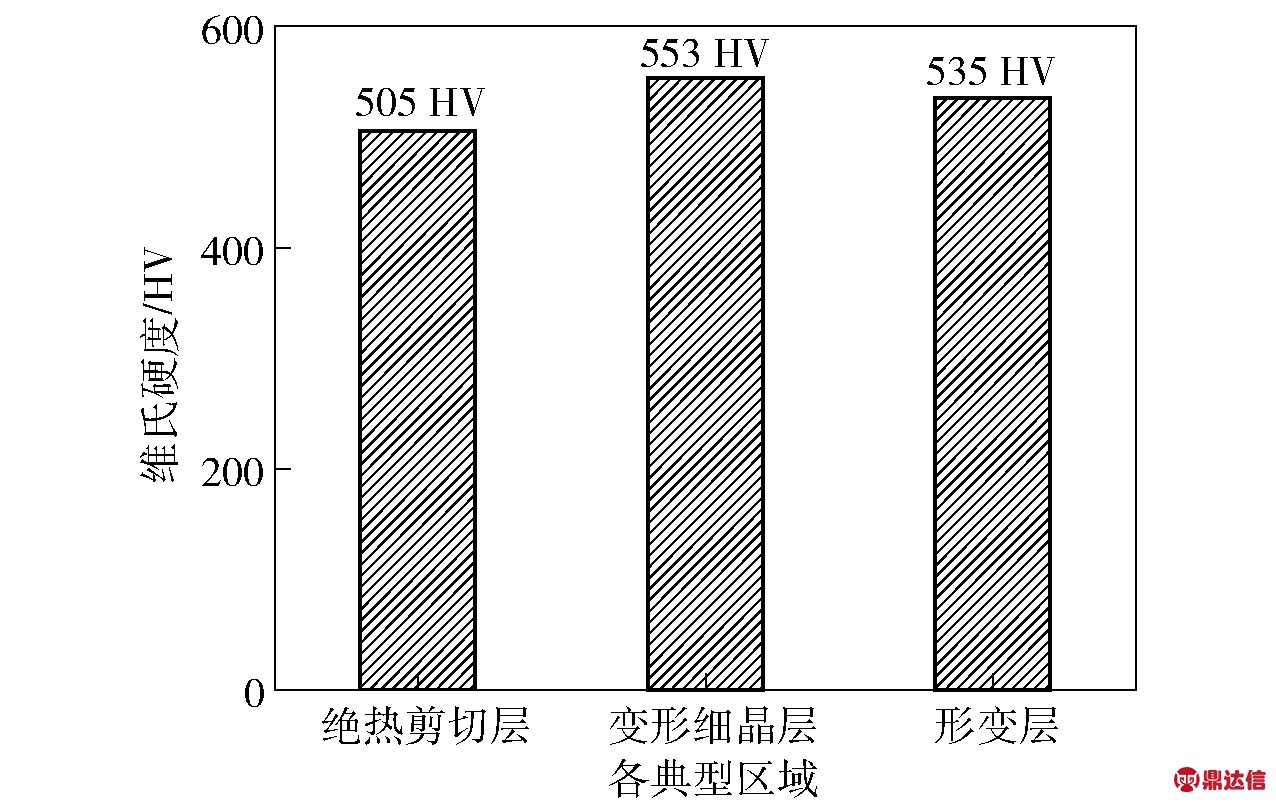
图16 弹坑边缘各典型区域的维氏硬度
Fig.16 Vickers hardness in typical regions of crater edge
上述研究表明:后置复合靶在603装甲钢支撑下,相较前置复合靶,弹靶界面接触力更高,位错运动产生塑性变形阻碍作用更强;变形细晶层高硬度马氏体组织一定程度上抑制塑性变形向内延伸,提高了弹丸开坑阻力;弹坑边缘区域形成高密度位错及应力集中,易达到临界条件发展成为绝热剪切带。
4 结论
本文通过对不同结构方式复合靶板中装甲钢弹坑组织演化规律、能谱分析及硬度分布研究,从细观和微观角度分析了其塑性变形机理,结合数值模拟弹坑边缘不同区域受力状态,得出结论如下:
1)弹丸侵彻初期,弹靶接触界面作用力小,塑性变形产生热量低,因此在侵彻初期仅出现晶粒变形,未形成绝热剪切带。随着侵彻深入,弹靶界面受力作用明显增强,接触区域由于塑性变形产生热效应及强度软化效应共同作用形成绝热剪切带,临近绝热剪切带区域组织在剪切力作用下,形成硬度较高取向一致的细密组织。在侵彻后期,弹靶之间作用力减弱,难以提供绝热剪切带的形成条件。
2)装甲钢后置复合靶防护性能优于前置复合靶,波阻抗匹配由高至低。弹丸侵彻过程产生应力波,在分层界面产生反射拉伸波,导致装甲钢背部出现卸载。卸载波之间相互作用,产生裂纹扩展,降低弹丸侵彻阻力,不利于防护性能提升。
3)616装甲钢背板支撑强度对绝热剪切带的形成具有重要影响作用,支撑板刚度越大,对616装甲钢塑性变形产生强阻碍,形成位错塞积群所需要的应力越大,当冲击强度超过临界应力时,位错塞积崩塌,在弹坑边缘区域形成高密度位错及应力集中,位错在剪应力作用下运动,更容易达到临界条件即产生失稳发展成为绝热剪切带。
4)弹丸侵彻过程中,剪切带内侧变形细晶层马氏体组织硬度高于绝热剪切带及原始马氏体组织,在一定程度上抑制塑性变形向内层延伸,有助于提高弹丸开坑阻力。
以上结论,有助于材料特性各异的多层异质复合靶板抗弹机理分析,并为抗侵彻理论模型的建立及靶板结构优化设计提供了一定理论依据。