摘 要:针对船用高温气体温度测试快速响应的要求,研制了高温气体热电偶温度传感器,并对该高温热电偶温度传感器的响应特性进行了测试。利用测试得到了高温气体温度传感器响应特性,基于射流冲击理论和高温热电偶的温度梯度动态特性,提出了装载舱内气垫船位置判定算法。搭建了由气源、加热器、喷口和移动式装载舱组成的试验台架,进行了高温气体条件下的热电偶温度快速响应修正算法的验证以及喷口热气100℃~200℃时不同移动速度条件下装载舱内气垫船位置判定算法验证试验。结果表明,基于射流冲击理论和高温热电偶温度梯度的动态特性判断装载舱气垫船位置的算法具有一定可行性,对装载舱环境监控设计具有一定指导意义。
关键词:高温热电偶;射流冲击;气垫船;装载舱;位置判定
0 引言
气垫船是一种利用高压空气向围裙气垫内供气,从而将船体提升,在船只底部与水面之间形成全部或部分垫升的运输工具。气垫船通过气垫的垫升,大大减少船航行时的阻力,从而实现高速航行。气垫艇是理想的近海运输装备,它的高航速和两栖性能提高运输效率,各国都进行了大量的研究和实艇试验[1]。美国十分重视气垫船的研发,研制的气垫船吨位范围较广,应用十分广泛。俄罗斯也十分重视气垫船的发展,俄罗斯有多种型号气垫船投入运营。其他国家也有自主研发的气垫船,如瑞典研制的“斯米盖”气垫船,其具有很强的机动特性和快速响应特性;加拿大、德国、法国等也进行了许多气垫船的研究与开发[2]。
大型气垫船的动力装置多采用燃气轮机,轻型燃气轮机系统相比于其他船用动力推进系统具有重量轻、结构尺寸小等优势。针对气垫船燃气轮机动力系统的性能与仿真,国内开展了一系列的研究工作。针对气垫船垫升推进控制系统建立了数学模型,开展了气垫船垫升推进控制系统仿真工作[3];针对气垫船用三轴燃气轮机推进系统,建立了三轴燃气轮机的仿真模型,并利用所建模型进行了动态性能特性的分析[4]。随着大型现代水面船舶的设计与建造,对船舶车辆库的通风系统设计提出了新要求,需采用新的通风技术来适应新的需求[5]。气垫船在水面船舶装载舱中启动时,其动力系统中的燃气轮机排气量很大,同时温度很高,对其检测并采取必要的通风冷却措施十分必要。因此,气垫船进出装载舱以及气垫船在坞舱的位置是气垫船监控中的重要参数,通过气垫船在坞舱中位置的判断,可以及时调节喷水雾系统,为气垫船动力排放降温,同时监控气垫船的运行情况。
针对气垫船行进位置的研究,MAKI 等[6]提出了一种基于声学和视觉定位的气垫船进坞方法,位置预测的成功率只有50%。AGUIAR 等[7]讨论了欠驱动气垫船的位置跟踪控制问题,开发了一种非线性Lyapunov跟踪控制器,并在加州理工学院多车无线测试台上进行了试验验证,同时给出了目标位置预测的试验结果。LI 等[8]提出了基于两个摄像机进行位置估计的方法,并成功应用于某自主水下航行器。丁福光等[9]发明了一种基于激光测距仪的气垫船进坞控制系统及控制方法,但激光测距仪价格昂贵,无法进行弯曲路径下的位置判断,同时激光测距仪可能无法应用于高温装载舱环境。为精确判断气垫船位置,从而进行喷水降温,本文提出了利用高温热电偶的响应特性和射流冲击理论进行装载舱位置判断,同时进行了试验研究,并将结果与算法模块识别出来的位置进行了对比,结果表明,本文提出的算法具有可行性,精确度较好,可以进行装载舱的位置判断。
由于测量温度高、环境恶劣、影响因素多,高温气流温度的准确测量一直很困难[10]。测量高温气流温度时,由于各种原因,测量会有误差,其中由于辐射传热引起的温度偏差称为辐射误差。在高温燃气气体中,温度热电偶的辐射误差往往较大,随着被测气体温度的增高,热电偶与周围环境的辐射换热相应增大,尤其当热电偶周围的环境处于低温时,热电偶测点对周围环境的辐射热较大,使得测量值低于气流实际温度值。在测量高温气流温度时,热电偶的辐射误差是不能忽视的误差因素。为了准确测量高温气体温度,研制了高温气体传感器,该高温气体传感器适用于装载舱高温气体环境,具有快速响应能力。
1 高温气体传感器温度修正模型
当物体内温差相差不大,可近似认为在这种非稳态导热过程中物体内的温度分布与坐标无关,仅随时间变化。因此,物体温度可用其任一点的温度表示,而将该物体的质量和热容量等视为集中在这一点,这种方法称为集总参数法。如果物体的导热系数很大或者物体的几何尺寸很小,或表面传热系数极低,则其非稳态导热都可以归结为这类问题。测量温度变化的热电偶温度传感器就是典型的实例,所以在试验之前可以使用该传热理论对温度传感器进行分析。
高温气体传感器采用热电偶形式,其测量的温度是热电偶测点与周围环境的平衡温度。为了分析热电偶测量过程产生的各种测量误差,首先需要分析热电偶测量端与周围气体环境的流动换热关系。位于气流中的热电偶测量端与气流和周围环境之间的换热如图1所示。热电偶测量端与周围环境的热交换主要以对流、辐射和导热3 种形式进行。温度是物体内平均动能的一种表现形式,由于所研究的气流速度不大,气体流动可以按照不可压流动处理,同时由于气流速度不大,气流的静温和气流的总温T*基本一致。所测气流为高温气体,高温气体传感器测点的辐射换热不可忽略,在对气流温度修正分析时必须考虑进去。设高温气体传感器测点的测量端直接测到的温度为Ti,气流的实际温度为Tj。
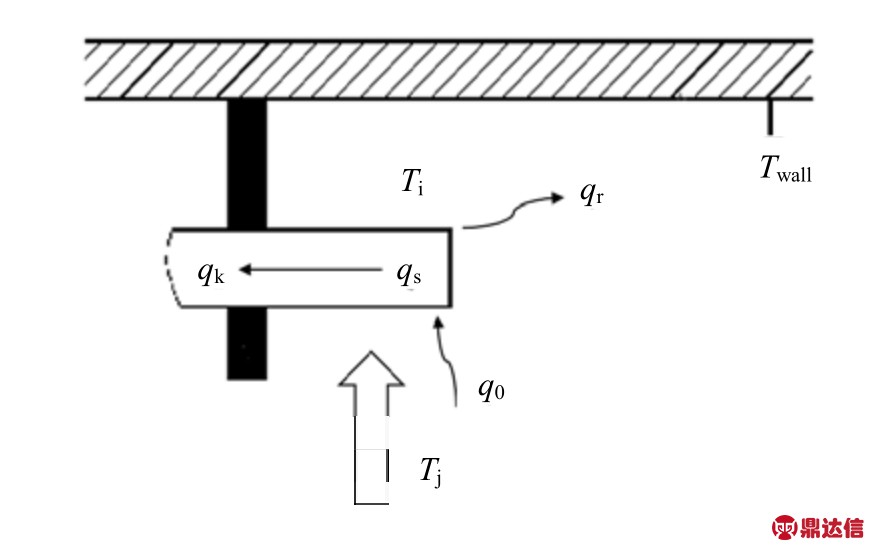
图1 热电偶测量端的热平衡图
高温气体测试热电偶头部的导热微分方程为

其中

因此得到

式中:ht 为复合传热表面传热系数,其为对流传热表面传热系数与辐射传热表面传热系数之和。

对于同时存在辐射和对流传热的综合传热问题,引入复合传热表面传热系数有助于简化计算,符合工程需求。
引入过余温度

代入式(3)可以得到

初始时刻

时间从0 到τ 积分

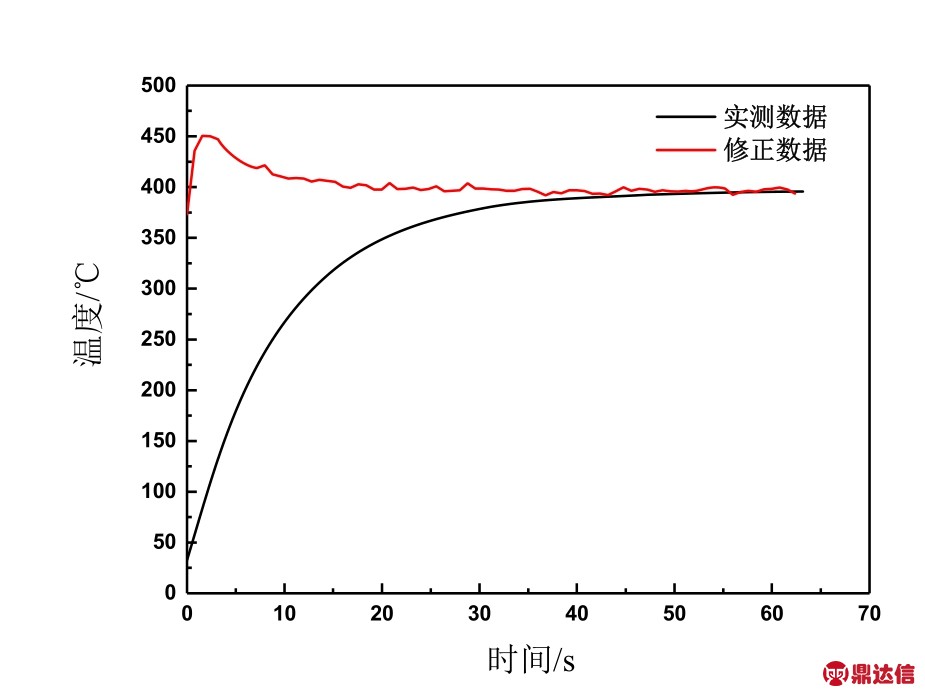
式中:T0 为初始时刻下温度传感器的测点温度;θ0为初始时刻下温度传感器的过余温度;θ 为τ 时刻下温度传感器的过余温度;V、A、ρ、c 分别为热电偶头部测点的体积、表面积、密度以及比热。
根据给定的换热情况选定准则方程,然后根据准则方程规定的定性尺寸和定性温度计算对流传热表面传热系数,再根据牛顿冷却公式计算辐射传热表面传热系数,进而计算得到复合传热表面传热系数。当复合传热表面传热系数确定后,可以根据式(10)求解出气垫船排气口的瞬态实际热气温度。
2 高温装载舱位置判别算法
2.1 射流冲击换热理论
气垫船的尾喷口对高温气体温度传感器的加热方式是射流冲击,可以将该过程简化为射流冲击平板加热问题。单个圆形喷口射流流场可以定性表示为图2所示状态,一般射流出口的流速是接近均匀的。射流离开喷口后,由于与周围静止介质之间的动量交换,使射流直径不断扩大,但是射流的中心仍然保持有一个速度均匀的核心区域。随着流体向前运动,核心区域不断缩小,最后,整个截面上的速度呈现出中间大、逐渐向边缘减小的不均匀分布。当射流抵达被冲击物体的表面后,流体向着四周沿着表面散开,形成壁面射流区。

图2 射流冲击换热流场
被冲击的壁面正对喷口的区域称为射流滞止区,与射流中心对应的点为滞止点,这里的局部换热系数最高,所以在算法中确定出对流换热最强的区域就是喷口的正对位置。
在以滞止点为圆心、半径为r 的圆内,被冲击表面的对流换热系数可以表示为下列函数形式[11]。
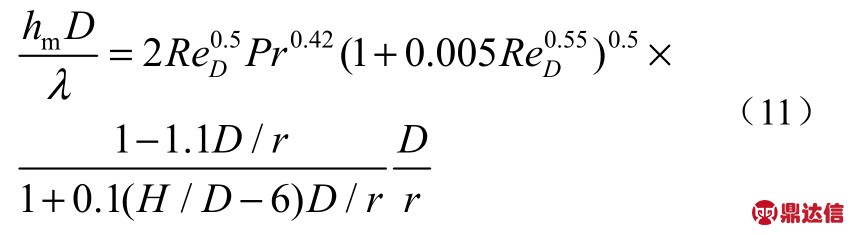
式中:hm 为射流对流换热系数;ReD 为射流喷口雷诺数;Pr 为流体普朗特数;D 为射流喷口直径;r 为射流半径;H 为射流距离。从式(11)可以得到:射流冲击对流换热系数沿射流半径方向不断减小。通过射流冲击换热理论可以确定,当高温气体温度传感器处在射流冲击滞止区时,温度传感器的上升趋势相对较高。由于传感器在工作过程中会出现不同的起点温度,如果简单地采用同一温度传感器两时刻的温度差很难判断喷口的正对位置,通过分析集中参数法传热理论式(10)可以得到

由式(12)可知:温度传感器的温度上升趋势是以过余温度的比值作为直接参考的,当两时刻过余温度比值较大时,说明传感器附近对流换热系数较高,所以可以采用两时刻下过余温度的比值作为传感器附近对流换热系数的度量,即传感器物性参数保持恒定 时,在固定时间间隔下正比于气流对流换 热系数。
由于T∞在试验前无法确定,所以使用式(13)反映传感器附近的对流换热的强弱。
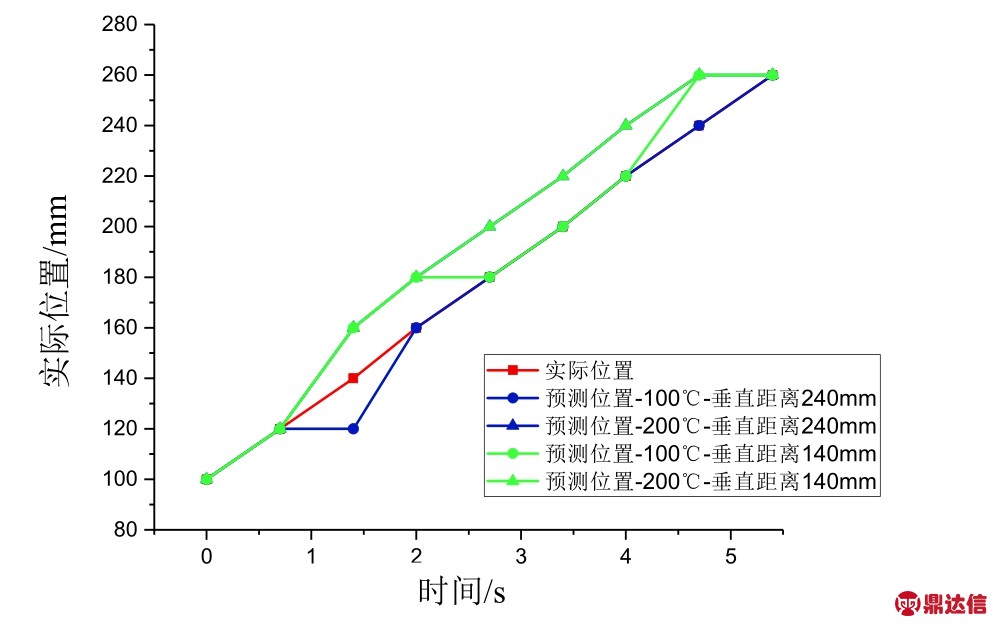
式中:T1 为当前时刻下温度传感器温度;T0 为上一时刻温度传感器温度;Tf 为计算中的参考温度,按照实际的工作状态进行调试确定。通过对比该公式所得数值,判断热气喷口位置。
2.2 气垫船位置判断算法优化
根据热电偶响应特性及射流冲击流动换热理论,可以确定气垫船位置判断算法的实现方向,但在算法具体实现过程中,还需要考虑多种实船的具体运行特性,如气垫船处在进入装载舱的过程还是离开装载舱的过程等。通过读取每一时刻下的高温热电偶温度并进行温度修正,通过热电偶温度传感器的动态响应数据进行气垫船的位置判别。在实船上,沿气垫船行进路线布置一排高温气体传感器,采用CAN 总线实时扫描高温热电偶温度值并将数据传给算法输入模块,经算法处理后得到该时刻气垫船的位置、修正后的温度以及气垫船的状态。气垫船位置判断算法主要难点为:高温气体温度传感器的温度并非如理想状态时各个温度传感器的温度都有相同的上升趋势,由于各个温度传感器初始温度不同,高温气体温度传感器温度的最高位置并非在喷口处。虽然最高点温度与气垫船的实际位置不相符,但根据射流冲击换热原理可知,热电偶温度上升趋势与气垫船的喷口位置呈现一定的单值关系,因此对每一时刻的各个温度传感器动态变化进行分析,可以在一定精度范围内判断气垫船的位置。
通过分析发现,虽然最高点温度与船的实际位置不相符,但根据对流冲击换热原理可知,温度上升趋势与船的喷口位置呈现一定的单值关系。由于判断装载舱的位置至少需要两个时刻的数据,因此初始时刻仅存储温度传感器温度值。如果温度的最高值没有明显变化,可以认为船坞内没有气垫船,气垫船的位置默认在零位或者末位。在非初始时刻,首先进行气垫船状态判定,即判断是进入还是离开船坞。判断的依据是第一个温度传感器或最后一个温度传感器的温度值有无连续上升趋势,若有,则认为装载舱开始驶入或者驶出。之所以用连续上升而非上升一次作为依据,原因在于温度传感器的温度可能出现波动,会影响判断的准确度,初始时刻的准确判断至关重要。当装载舱开始驶入或者驶出时,对上升趋势列表进行排序,取最大的前3 组进行排序,其最大值和最小值对应的位置之间的区域认为是气垫船可能存在的位置,取中间位置作为判定的结果。
当船行驶至末位/零位温度传感器位置时,并且末位/零位温度传感器的温度出现连续下降,则认为船已经驶出船坞,若船行驶至末位/零位温度传感器位置,而末位/零位温度传感器的温度没有出现连续下降,则将气垫船“固定”在末位/零位位置。
3 试验研究方案
试验的目的在于研究高温热电偶在喷口移动状态下对高温热气的响应特性以及检验气垫船位置判断算法的可靠性,着重关注射流冲击换热所产生的温度变化趋势分布。考虑试验条件限制的情况,无法采用实际尺寸进行试验,需要采用缩比模型进行试验,同时以喷口射流理论为基础进行试验方法的设计。
实际气垫船尾气排出口直径约为1 m 左右,排气口与通道顶部距离在1 m~2.5 m 之间,并与水平面成30°喷射。而在实际装载舱中,顶部墙面上安装有一排温度传感器,两传感器之间的距离在0.5 m~1.5 m之间。参考试验条件,选择1∶12.5 的缩放比例进行设计,射流孔径因此由1 m 缩小到80 mm,以模拟气垫船排气孔。同时,射流孔径改变后,其他几何尺寸也要同时加以缩比:1)射流距离;2)高温热电偶间距。
试验系统如图3所示,主要包括2 个部分:模拟尾喷口移动的驱动装置和模拟喷口的热气喷气装置。驱动装置由金属板、螺母座以及丝杆装置构成,电机转动丝杆,丝杆拖动金属板以一定的速度移动,以模拟气垫船在装载舱内的移动。喷气装置所需热气由电加热系统提供。图4为热气喷口实物图,喷口出口热气速度为10 m/s,在射流喷口处包裹了一层石英保温棉以减少热气在管路中的散热。高温气体传感器排布方式如图5所示,传感器布置间距为20 mm 和40 mm。针对3 种排布方式,分别在表1所示工况下进行试验,共计24 组。
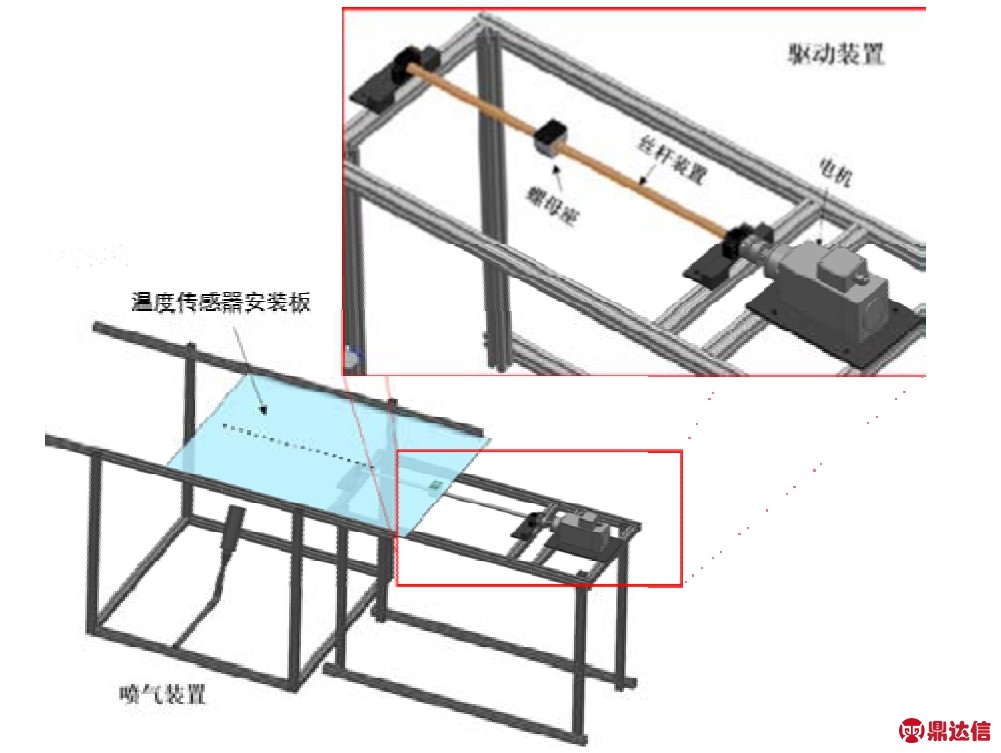
图3 气垫船位置判断模拟试验台
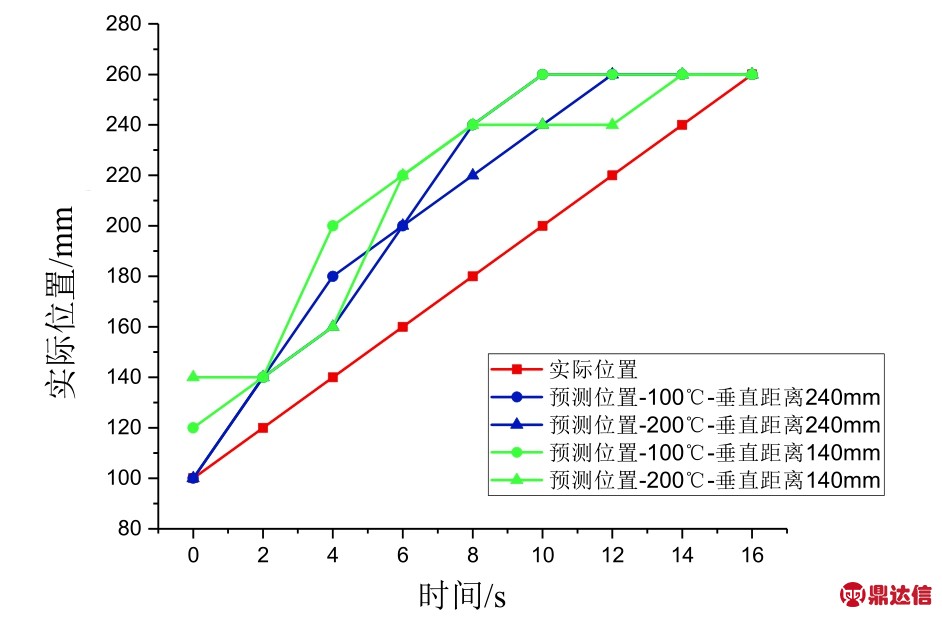
图4 模拟气垫船尾喷口的热气喷口
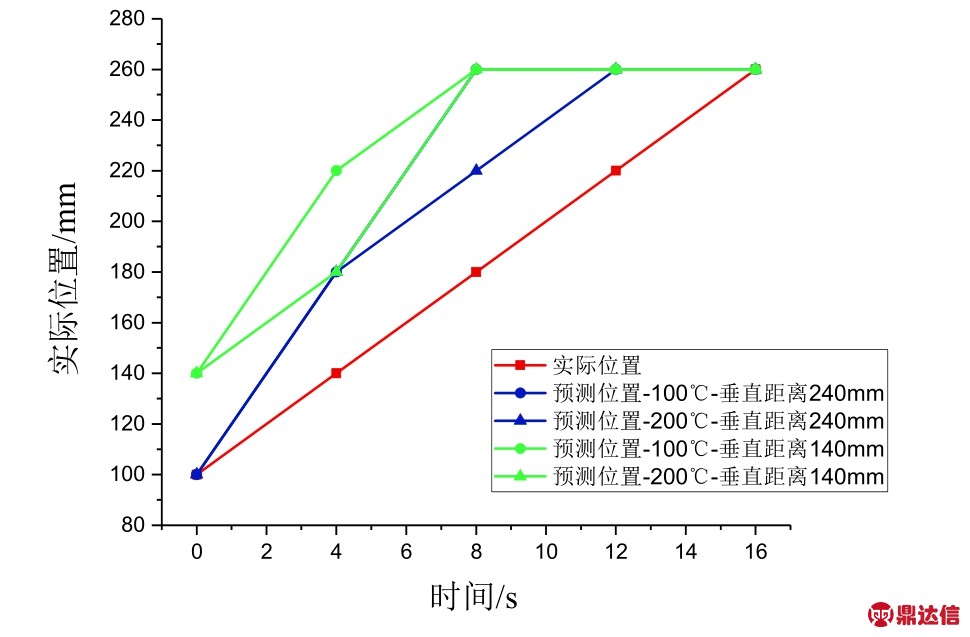
图5 高温气体温度传感器排布方式
表1 试验工况
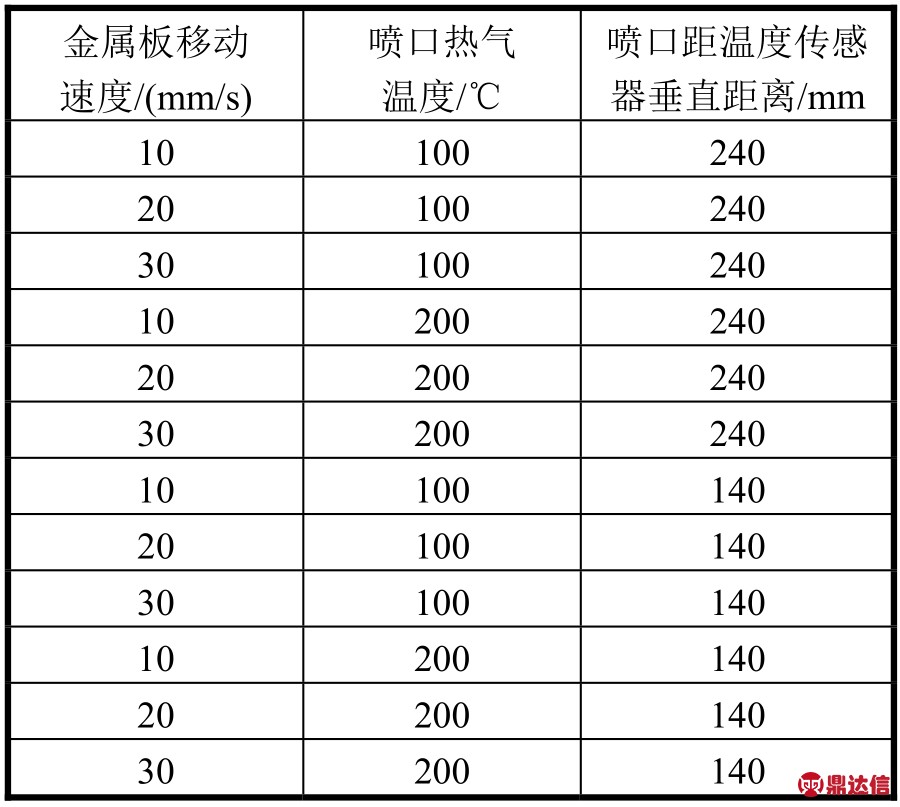
4 结果与分析
将高温热电偶埋入热气中进行动态响应测试,图6给出了试验测试热气400℃时经过温度修正算法修正之后得到的数据与原始高温热电偶实测数据之间的对比。由图6可以看出:经过修正之后,获得了快速响应的实际燃气温度,从而可以根据其动态响应特性进行气垫船位置判断。
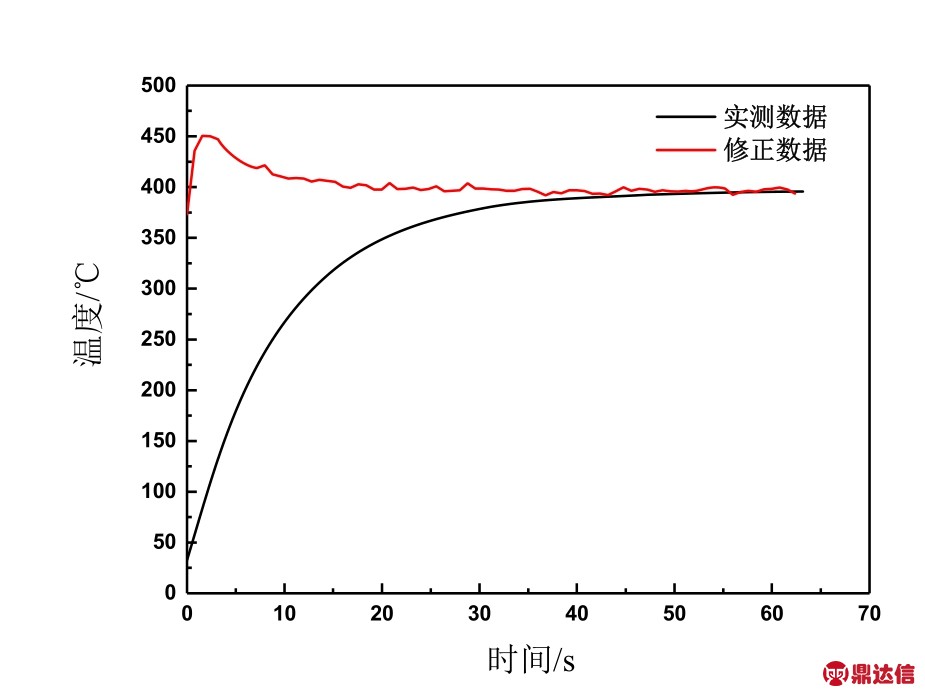
图6 400℃喷口温度下温度传感器修正图
4.1 高温热电偶间距20 mm 时位置判断试验结果
当高温热电偶间距为20 mm 时,共布置9 组高温气体热电偶。图7~图9给出了金属板移动速度分别为10 mm/s、20 mm/s 和30 mm/s 时,在不同热气温度和不同喷口距温度传感器垂直距离情况下,气垫船实际位置和算法预测位置之间的关系。预测的位置普遍超前于实际位置,当移动速度为10 mm/s、喷口距温度传感器垂直距离为240 mm、热气温度为200℃时,预测最大误差为2 个热电偶范围;当移动速度为10 mm/s时,其他3 种情况判断的最大误差均为3 个高温热电偶范围,且最大误差出现位置均在4~6 号高温热电偶处;而当移动速度增加至20 mm/s 时,最大误差依然为3 个高温热电偶范围,但此时最大误差出现的频率有所下降;当移动速度再次增加至30 mm/s 时,最大误差减少为1 个高温热电偶范围。由此可见,最大误差随着移动速度的增加而减少,原因在于判断的本质是利用高温热电偶的瞬态特性,当移动速度增加时,瞬态特性更加明显,有助于提高判断的精度。针对这12 组试验工况,预测精度最好的情况出现在移动速度为30 mm/s、温度为100℃、喷口距温度传感器垂直距离为240 mm 时,仅在3 号高温热电偶处出现1 个高温热电偶误差范围的误差。
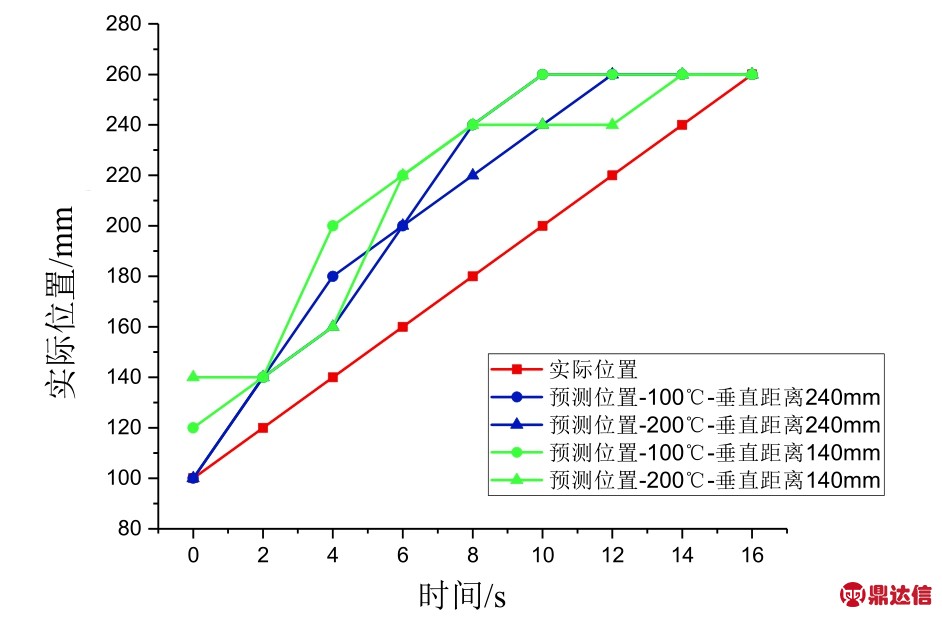
图7 热电偶间距为20 mm、金属板移动速度为 10 mm/s 时的位置判断试验结果
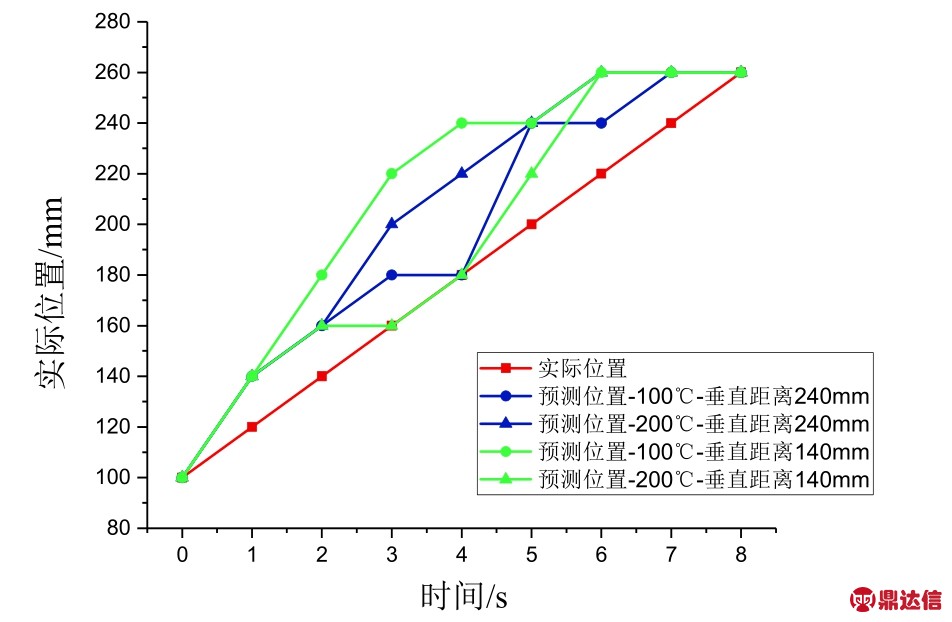
图8 热电偶间距为20 mm、金属板移动速度为 20 mm/s 时的位置判断试验结果
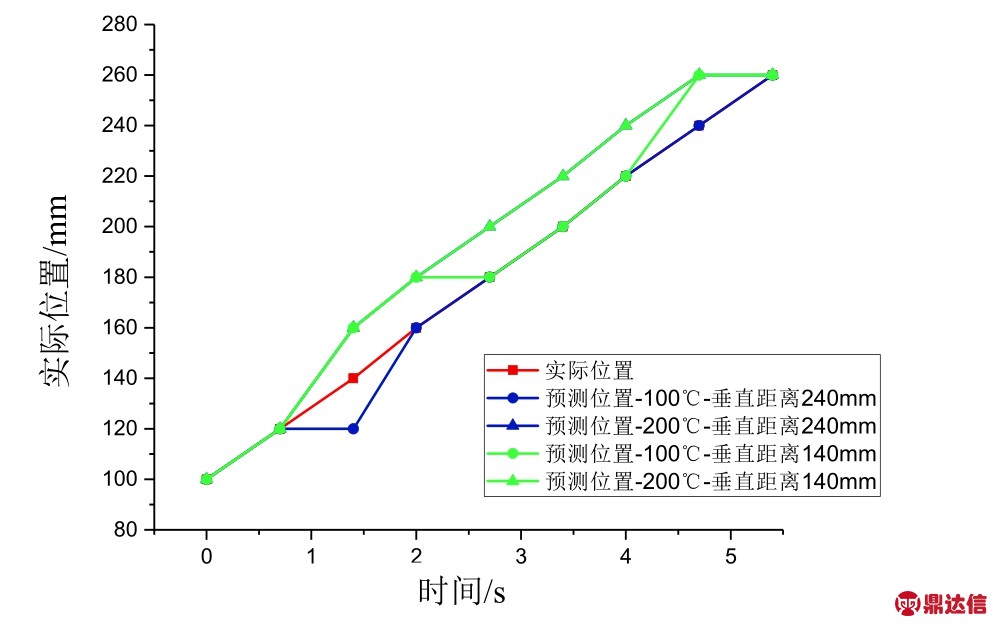
图9 热电偶间距为20 mm、金属板移动速度为 30 mm/s 时的位置判断试验结果
4.2 高温热电偶间距40 mm 时位置判断试验结果
当高温热电偶间距为40 mm,共布置5 组高温热电偶。图10~图12给出了金属板移动速度分别为 10 mm/s、20 mm/s 和30 mm/s 时,在不同热气温度和不同喷口距温度传感器垂直距离情况下,气垫船实际位置和算法预测位置之间的关系。当热气温度为100℃时,6 组试验共有5 次出现最大误差为2 个高温热电偶范围;而当热气温度为200℃时,6 组试验只有1 次试验出现最大误差为2 个高温热电偶范围,另外5 组最大误差均为1 个高温热电偶范围;不仅如此,虽然12组试验的最大误差为2 个高温热电偶范围,但由于热电偶间距增大,因此最大误差(即80 mm)仍然要比高温热电偶间距为20 mm(最大误差为60 mm)时的情况大。因此,当热电偶变少时,影响位置预测的精度。
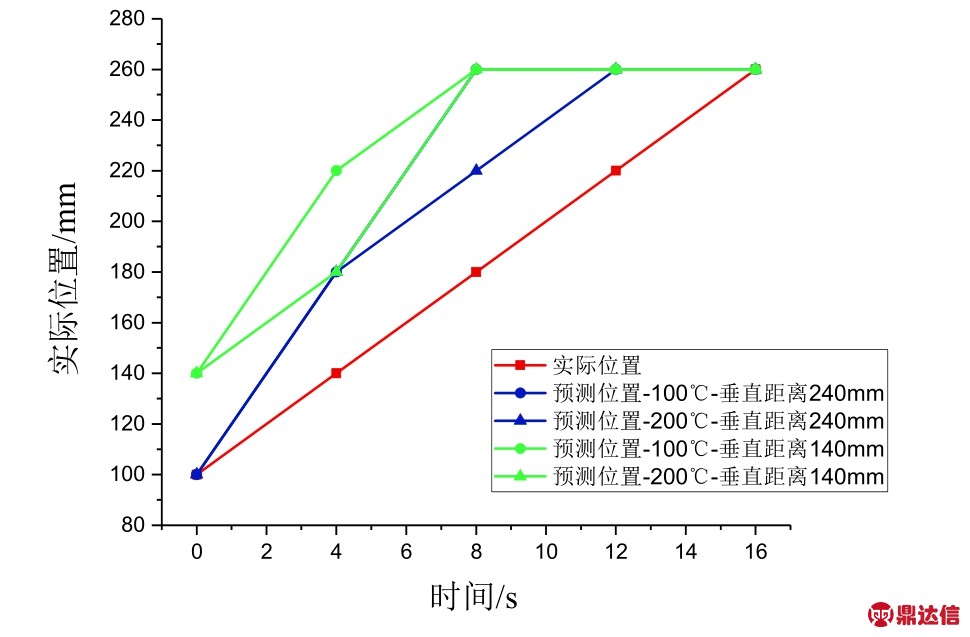
图10 热电偶间距为40 mm、金属板移动速度为 10 mm/s 时的位置判断试验结果
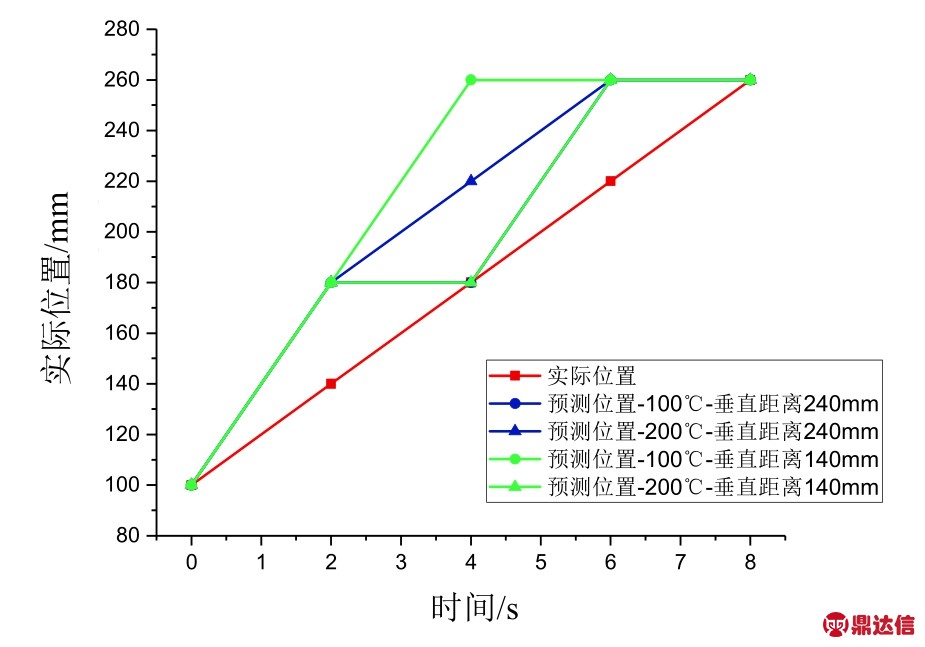
图11 热电偶间距为40 mm、金属板移动速度为 20 mm/s 时的位置判断试验结果
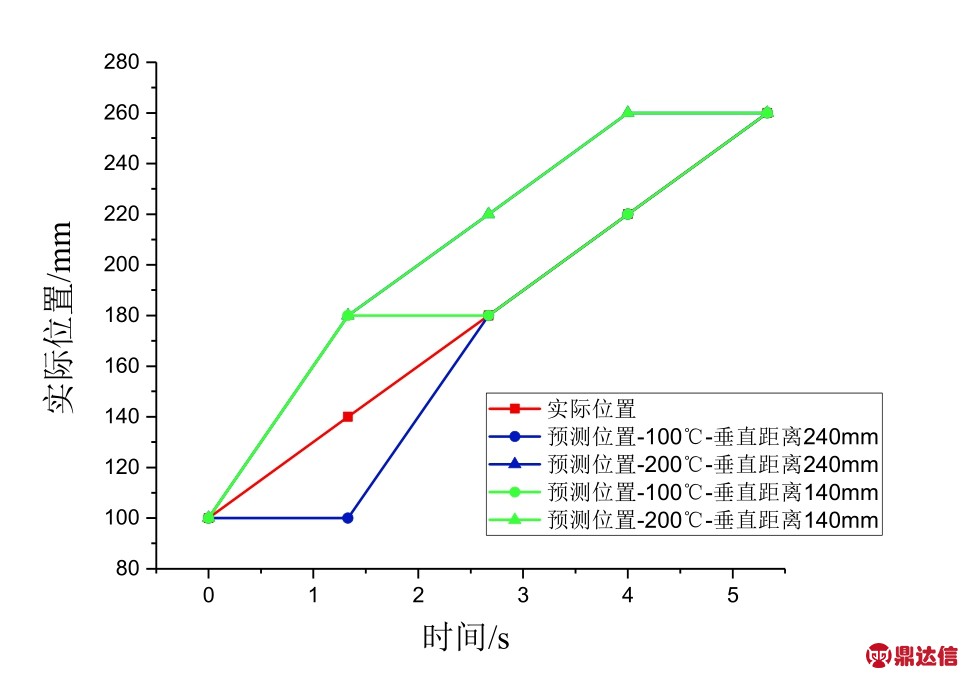
图12 热电偶间距为40 mm、金属板移动速度为 30 mm/s 时的位置判断试验结果
5 结论
本文基于温度修正和射流冲击理论,对气垫船位置判断算法进行了理论和试验研究,提出了利用高温热电偶动态特性进行位置判断的思路。通过搭建试验台,试验验证了位置判定算法的可行性,结论如下:
1)温度传感器实测燃气温度经过修正后可以获得良好的动态特性,可以将其应用于位置判断;
2)准确预测气垫船位置对保护装载舱和装载舱至关重要,基于高温热电偶的动态特性进行位置判断具有一定可行性,针对本文的设计工况,位置判定的误差在2~3 个热电偶之间;
3)气垫船移动速度、温度传感器间距、温度传感器温度采集速度和热气温度对位置预测的精度有重要影响,间距越小、燃气温度越高、温度采集速度越快,位置预测的精度越高。