摘要:为了适应高速、高精度加工目标对龙门铣床横梁部件的要求,建立了横梁的实体模型,分析了其在实际工况下的静动态特性。通过对相关尺寸的灵敏度分析,找到了影响横梁整体性能的关键因素。给出了横梁的最大变形及低阶固有频率,并在此基础上进行了多目标优化。优化结果表明,采用此方法对提高横梁的性能有很大的帮助。
关键词:ANSYS Workbench;横梁;多目标优化
0 引言
横梁部件是龙门铣床的关键部件之一,上面安装有滑枕系统,其结构连接滑枕与立柱,承受来自滑枕的切削力,是龙门铣床主要受力部件之一。随着高速、高精度先进制造技术的发展,对机床关键部件的整体性能提出了更高的要求[1-3],以往单一考虑机床静态或者动态性能的设计方法已经不能满足要求,本研究在综合考虑机床静动态特性的基础上对横梁进行了多目标优化设计,降低了横梁部件的变形,提高了其一阶固有频率,并适当的减轻了部件的质量,改善了其整体性能,提高了龙门铣床的加工精度。
1 静力学分析
1.1 三维实体模型的建立
本文的横梁模型来源于桂林某公司某型号龙门铣床,该结构比较复杂,内部是纵横交错的板筋结构,表面上有复杂孔系结构以及倒角、倒圆等,这些小特征在划分网格时会产生大量的有限元单元,加大计算机的计算时间且降低了网格质量。所以在实体建模时对原结构进行了适当的简化,本文利用ANSYS Workbench软件自带的Design Modeler模块建立了横梁的参数化模型如图1所示。
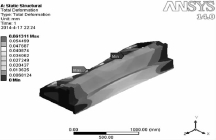
图1 横梁模型
1.2 有限元模型的建立
网格划分是进行分析的基础,划分的好坏,影响计算精度和速度ANSYS Workbench的网格划分技术有了很大提高,采用了分解与克服(Divide&Conquer)的策略,在几何体不同部分可以采用不同的划分方法[4]。结合模型特点采用四面体单元划分法来划分网格,划分后的模型如图2所示。
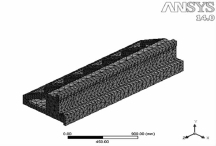
图2 有限元模型
1.3 施加载荷
载荷施加正确与否对计算结果影响很大,只有最大程度地逼近实际工况才能得到正确的结果,要考察横梁在最大载荷下的极限变形量,就要分析主轴箱所处的位置。研究表明机床在加工工件时,主轴箱处于中间位置时,横梁受到的载荷最大[5]。根据机床设计手册及厂家提供的资料,得出横梁受到来自主轴箱的扭矩为3×107N·mm。横梁自重及其上面的主轴箱的重力需考虑,重力均匀分布在横梁上,横梁与机床立柱结合面定义为固定约束。施加结果如图3所示。
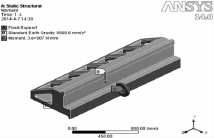
图3 载荷施加
1.4 静力计算
利用ANSYS Workbench对上述模型进行数值计算。得出横梁总变形的结果如图4所示。上述结果可以看出,横梁变形量略大,为0.07211×10-3m尤其后半部分变形最大,表明横梁整体刚度不足,分析得知:横梁壁厚度、横梁前端导轨宽度等有关尺寸对变形影响较大,可以通过优化设计改善其性能。

图4 横梁总变形
2 模态分析
2.1 模态分析基础
模态分析用于分析结构的自振频率特性,包括固有频率和振型及振型参与系数。它的好处在于可以使结构设计避免共振或以特定的频率进行振动;设计人员可以认识到结构对不同类型的载荷是如何响应的;有助于在其它动力分析中估算求解控制参数。
由经典力学理论可知,物体的动力学通用方程为:

式中,[M]是质量矩阵;[C]是阻尼矩阵;[K]是刚度矩阵;[X]是位移矢量;{F(t)}是力矢量。
对于模态分析,{F(t)} ,结构的阻尼可以忽略不计,其动力学方程为:

结构的自由振动为简谐振动,即位移为正弦函数,即:

代入上式得:

此方程的特征值为其开方ωi就是结构的自振圆频率,自振频率为:
。特征值ωi对应的特征向量{xi}为自振频率
对应的振型。
2.2 模态分析
根据上面静力学分析的有限元模型,结合机床实际安装情况把横梁与机床立柱结合面定义为固定约束。在进行模态分析时,采用ANSYS Workbench软件的Lanczos模态提取方法[6]求解。此方法适用于大型对称矩阵特征值的求解问题。横梁是一个连续体,质量和弹性连续分布的,所以应具有无穷多个自由度,也就有无穷多阶模态。研究发现,具有1000个自由度以上的振动系统,提取其前三阶振型,其精确度就可达到90%以上,若对前10阶振型进行提取,其精确程度可达到99%以上[7]。一般而言只有低阶固有频率才有可能与外界激振力接近或相等而发生共振,为了计算方便,只研究前3阶固有频率。模态分析结果如图5~图7所示。横梁前三阶固有频率及振型见表1。
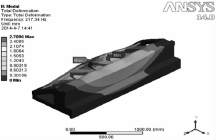
图5 一阶振型
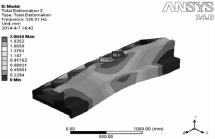
图6 二阶振型
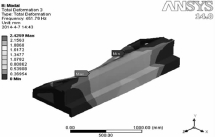
图7 三阶振型
表1 横梁模态分析前3阶的固有频率及振型
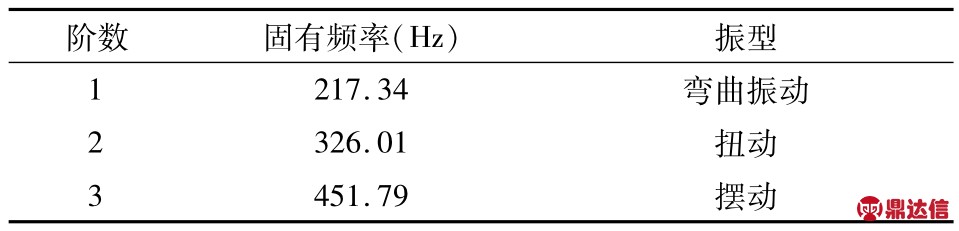
通过对前3阶振型分析,发现前2阶主要是弯曲振动和扭动,最后一阶为摆动,这说明目前横梁的壁厚使横梁动刚度不足,而横梁底板变形较小,不是主要受力部分,可以考虑优化其尺寸,以减轻横梁质量。
3 横梁多目标优化设计
3.1 灵敏度分析及优化模型的建立
由于该横梁结构复杂,相关尺寸过多,为了避免选取尺寸的盲目性,有必要对有关尺寸做灵敏度分析,从中找到影响横梁性能的关键因素,再对这些尺寸做优化设计,可以取得较理想的效果[8-10]。结合以上静动态分析结果,选择以下尺寸,尺寸的初始值及变化范围如表2所示。
表2 变量的取值范围
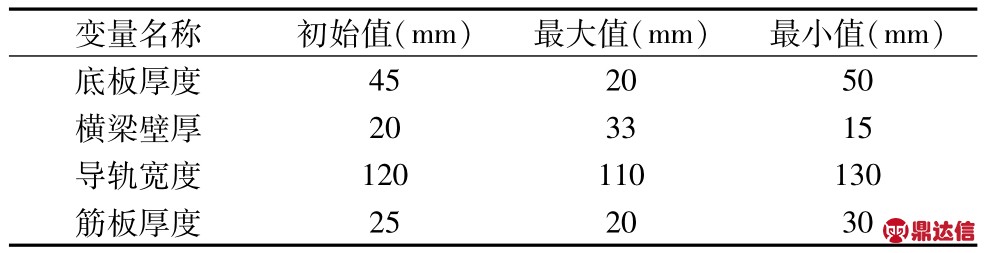
灵敏度分析结果如图8所示。
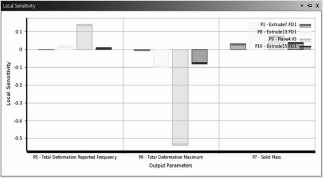
图8 各尺寸灵敏度分析结果
从图中可以看出4个尺寸中筋板厚度(p1)对三个目标函数的灵敏度都比较低,横梁壁厚(p9)对结构总变形、一阶固有频率影响最大,横梁底板厚(p8)度对结构质量影响较大,导轨宽度(p10)的灵敏度介于它们之间。
优化设计的三个基本要素是设计变量、约束条件和优化目标。设计变量为上述三个尺寸;优化目标包括横梁总变形变小,一阶固有频率提高,在满足床身整体刚度基础上总质量适当减少。综合考虑以上因素选择尺寸p8;p9;p10作为设计变量,令p8=x1,p9=x2,p10=x3优化设计数学模型如下:
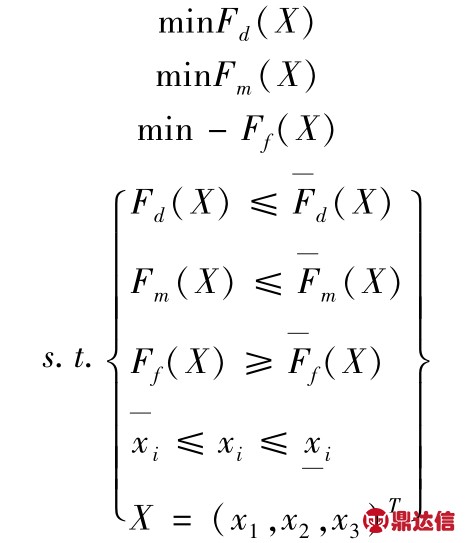
式中:Fd(X);Fm(X);Ff(X)分别为横梁的最大变形、质量、一阶固有频率,分别为优化前横梁的最大变形、质量、一阶固有频率。X为设计变量,xi为第i个设计变量,
为设计变量的上限值,
为设计变量的下限值。
3.2 优化计算结果及分析
本研究应用ANSYS Workbench的目标驱动优化及响应曲面(Response Surface)模块,从一组样本(即一定量的设计点)中得出“最佳”的设计点。有关优化计算结果如表3所示,通过上面的计算分析选A点作为优化设计点并对其尺寸进行圆整,优化前后尺寸变化见表4。
表3 优化结果

表4 化前后尺寸变化
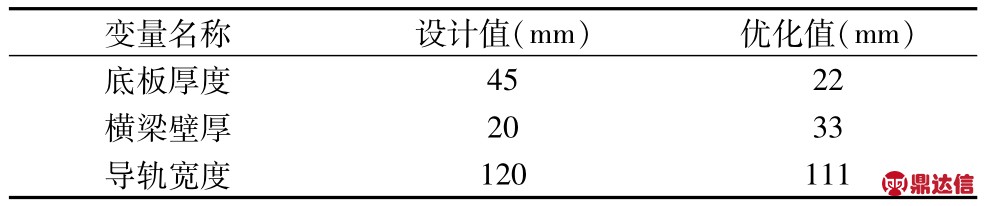
把优化后的尺寸重新生成横梁模型再次进行静态、模态分析,并将结果和原设计进行比较,如表5示。优化后横梁总变形、一阶振型如图9和图10所示。
表5 优化结果对比
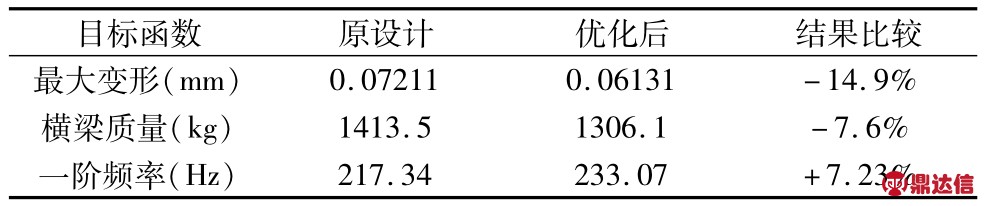
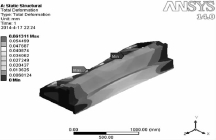
图9 优化后横梁总变形

图10 优化后横梁的一阶振型
从以上结果可以看出优化后横梁的整体性能有很大提高,最大变形有了较大的降低,质量有所减轻,达到了优化的目的。
4 结束语
通过对某型号龙门铣床的横梁结构进行静力、模态分析,得出结构的最大变形,低阶固有频率,找到了结构的薄弱环节,在此基础上对相关尺寸进行了灵敏度分析,找到影响其性能的关键尺寸,最后进行了多目标优化设计,并与优化前进行了对比分析,取得了良好的效果。文中的优化设计方法,为改进横梁结构提供了一定的理论依据,并可以推广到机床其他部件、工程机械等结构优化设计中。