摘 要:通过开展预焙阳极焙烧后热极迅速上槽试验,对整个试验过程中阳极温度变化情况和对电解的影响作出了分析,研究探讨了通过加强阳极生产过程组织,充分利用阳极焙烧产生的余热,减少了换极作业对电解槽热量损失,缩短了从换极到平衡的时间,提高了电解槽的稳定性。
关键词:热阳极;换极;热量损失
1 前 言
换极操作是电解生产中的主要操作之一。残极提出、新极装入时都会对电解槽的流场、温度场产生较大的改变,由此影响了电流分布情况、电解质的流速及方向,导致换极后电解槽原先的热平衡被打破。另一方面,在换极过程中极上料落入电解槽内,影响电解质中氧化铝的浓度,导致换极后电解槽原先的物料平衡被打破。每次换极过程都会对电解槽的热平衡和物料平衡造成干扰,严重时还会引起电解槽电压波动,直接影响了电解槽的稳定性。
若是在换极前阳极就具有较高的温度,换极能实现热极上槽,对于减少电能消耗,稳定电解槽技术条件,增加铝产量都有较大的好处。在整个行业,也有相关的试验研究和报道,如通过自制的阳极预热装置,充分利用更换下高温状态残极的热量对新阳极进行提前预热,以达到加热阳极的目的[1],或者把阳极提前放在电解槽保温料上加热,或者在阳极上槽前采用电能对阳极进行预热。本试验从另外的技术思路,不需要对阳极进行提前预热,充分利用阳极焙烧后的高温余热,将焙烧后的热阳极处理后直接换极上槽试验。
为了保证阳极送到电解后处于较高的温度状态,必须减少阳极生产过程及相关环节的热量损失,缩短相关过程及环节的处理时间,尽可能让相关的处理工序去等待需要处理的产品,而不能让产品去“等待”相关工序的处理。因此要优化设计阳极出炉后的每个相关环节,统筹协调安排好相关的作业,具体优化流程如图1所示。
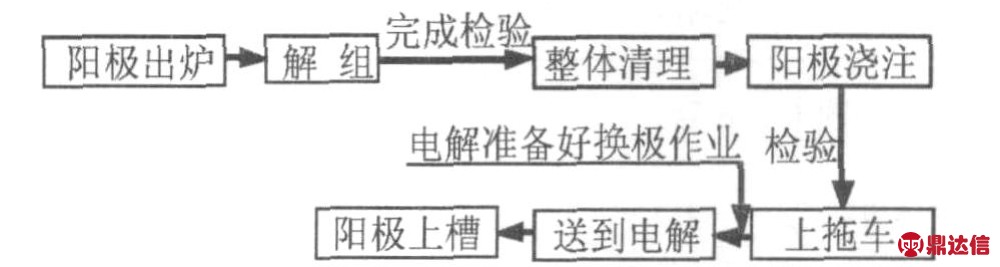
图1 优化作业流程
为了缩短流程的工时,质量检验人员及时配合做好现场的各项检验等工作,公司生产部门负责组织好试验极的运输工作,而在试验阳极运送到电解之前,做好试验槽的换极准备工作。
1.1.2 阳极温度及作业时间数据记录
为了使试验数据更加合理科学,全面了解各工序的作业时间、阳极热量损失,阳极的温度采集点分 A、B、C三点,而在每次作业完都要记录相应消耗时间,具体如下。
1.1 试验阳极的准备
1.1.1 制定合理的阳极作业流程
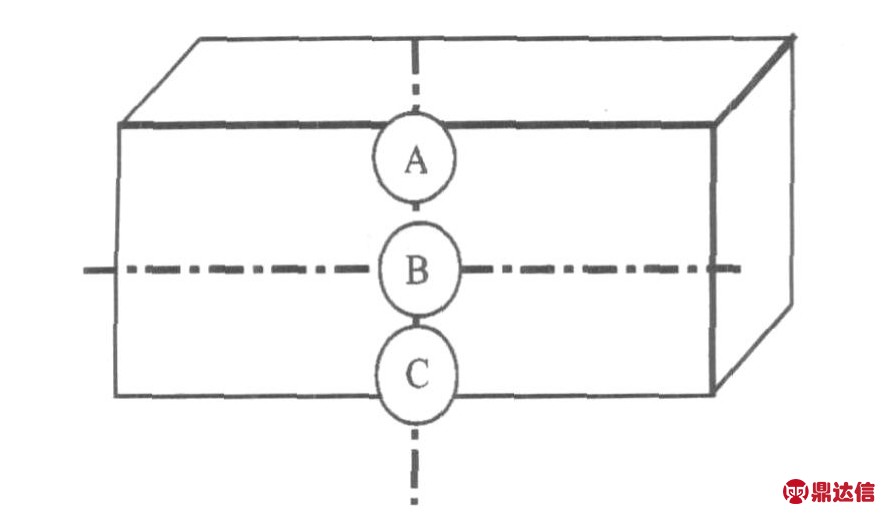
图2 阳极温度采集示意图
1.2 热阳极上槽
热极布局方式:一块热阳极与一块冷极组合进入同台槽子进行冷热极对比;另外两块热极全部进入同一台槽子进行相互对比;另再选一台槽子的普通极做整体对比。
2 试验结果分析与讨论
2.1 作业流程对阳极温度的影响
表1为阳极出炉至上槽时各工序所消耗的时间,阳极的出炉温度为 340℃,到电解上槽时温度为 247℃ (取 B点温度作为阳极的参考温度)。
表1 阳极出炉后至上槽时各工序所消耗的时间情况
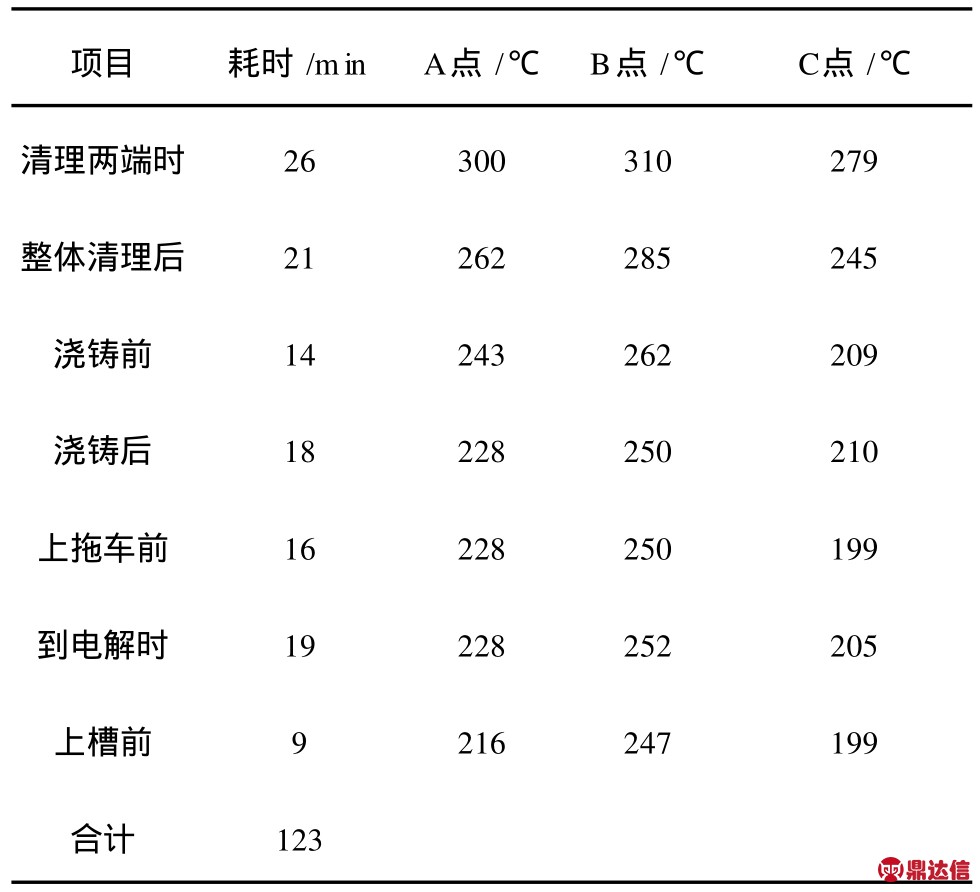
从表1中可以看出,阳极耗时最大的是阳极出炉后到阳极完全清理时,占整个工时的 38.21%,这个过程包括阳极出炉、阳极解组、阳极输送及搬运、阳极清理、阳极检验、阳极输送等作业。这个过程若通过合理的流程设计和优化,工时具有可压缩的空间。
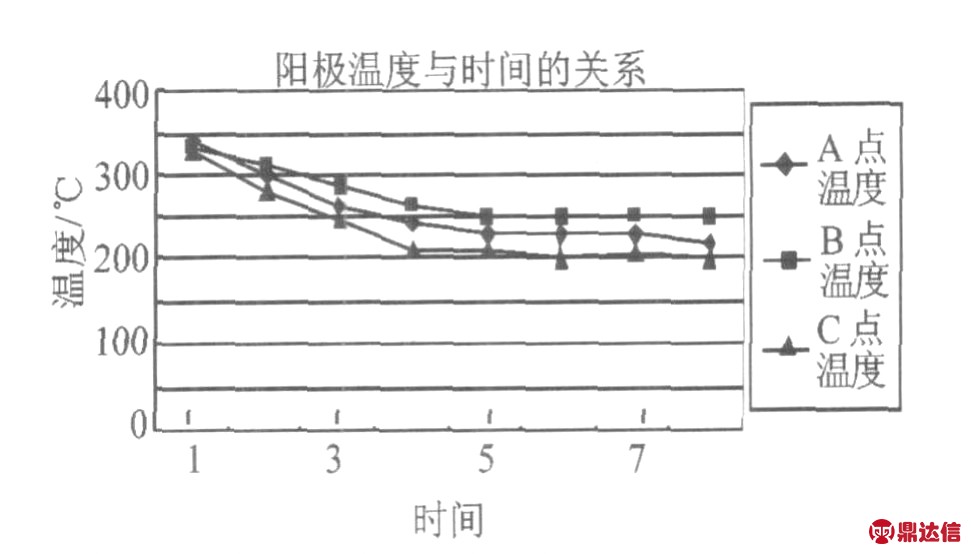
图3 阳极温度变化情况
而图3为阳极在整个作业过程中,热阳极温度随着时间的变化而变化情况,从图中可以看出:
1)由于阳极与周围的物体直接或间接接触,高温阳极热损失主要以传导热损失、对流热损失和辐射热损失等三种方式进行,阳极温度整体随着时间的变化呈某一曲线下降;但是当阳极温度下降到某一点时,出现了温度拐点,阳极温度的变化比较平缓。这主要是在阳极温度下降开始到拐点时,阳极所损失的热量主要是阳极表面的热量,随着阳极温度的下降,阳极内部的热量不断传导至阳极表面,在一定程度上补偿了表面损失的热量,因此拐点后阳极温度变化速率平缓。
2)从温度点的位置 (A点阳极上部,B点阳极中部,C点阳极下部)分布情况看,阳极中部的温度最高,阳极上部的温度次之,阳极的下部温度最低。
2.2 热阳极在电解槽中的表现
2.2.1 热阳极上槽后的导电情况
表2为热阳极与普通阳极换极后的导杆等距压降情况,图4为 113#、114#槽一冷一热阳极上槽后导电趋势情况,图5为两块热极与普通极上槽后的导电情况,从表2、图4及图5中可以看出:
1)无论那种阳极组合,在换极后的 5 h前,热阳极电流上升的速度明显高于普通阳极电流上升的速度,热极较冷极提前 4~8 h实现全电流运行。阳极上槽时,冷阳极下表面温度为室温 (约20℃),热阳极为 200℃左右,远低于电解质初晶温度 (约 935~940℃)。阳极上槽后,电解质在阳极下表面局部结晶,结晶层导致新上极电阻增大,随着阳极底掌温度升高,结晶层逐步溶解,阳极电流上升。但由于热阳极有较高的初温,结晶层较薄,溶解也较快,阳极上槽后初期,热阳极的电流上升速度大于冷阳极。
表2 热阳极与普通极换极后的导电情况
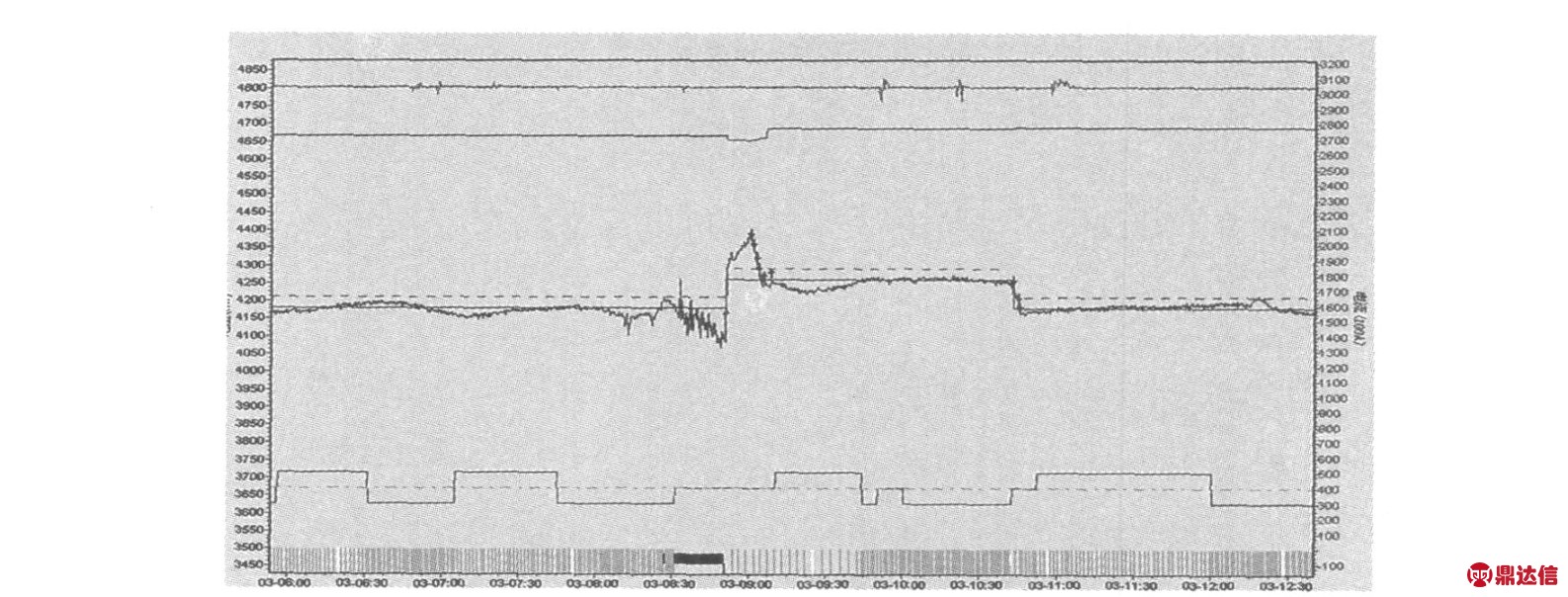
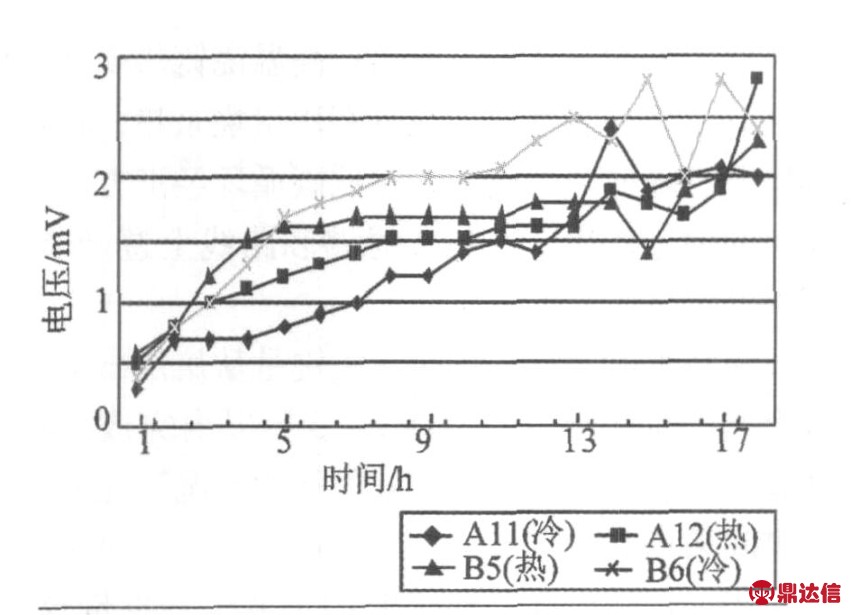
图4 113#、114#槽冷热极换极后导电趋势
2)上槽后 8 h以后,冷阳极的电流升高较快,并逐步超过热阳极。不管是同时上槽的两块一冷一热的阳极对比,还是同时上两台槽的两组冷热极数据对比,都有这一特征。这可能是热阳极提前导电,提前消耗,导致分布于热极上的电流要小。
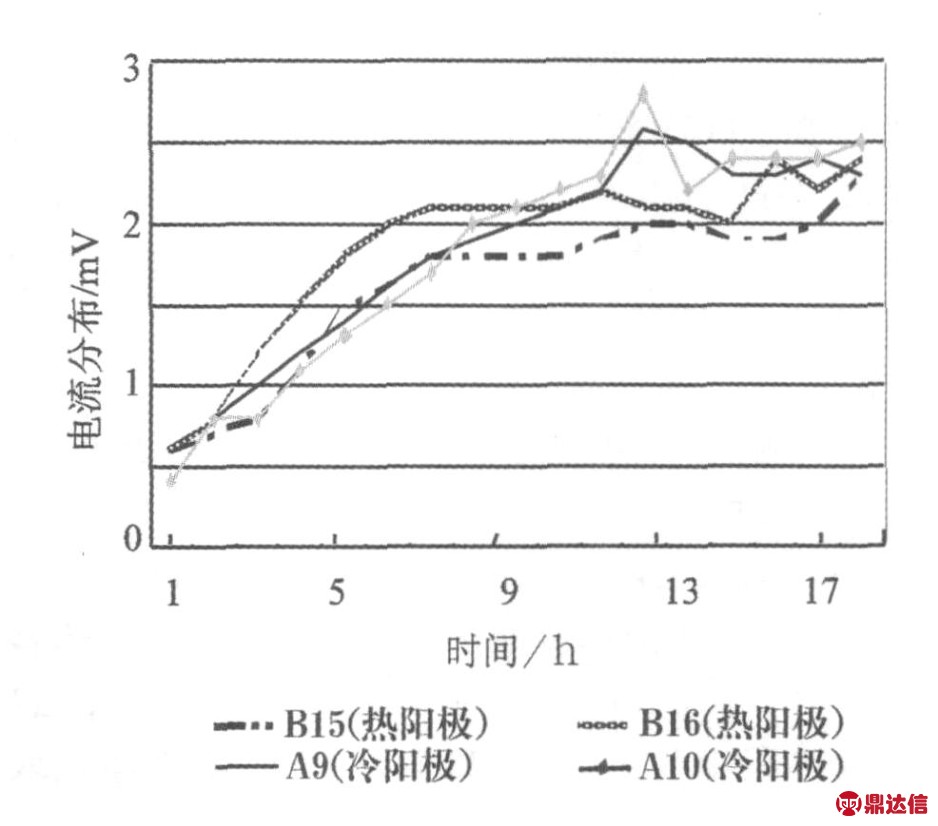
图5 115#、117#槽冷热极换极后导电趋势
2.2.2 热极上槽对电解工艺的影响
试验中分别收集了使用冷极、热极进行阳极更换作业的电压变化曲线如图6、图7所示。
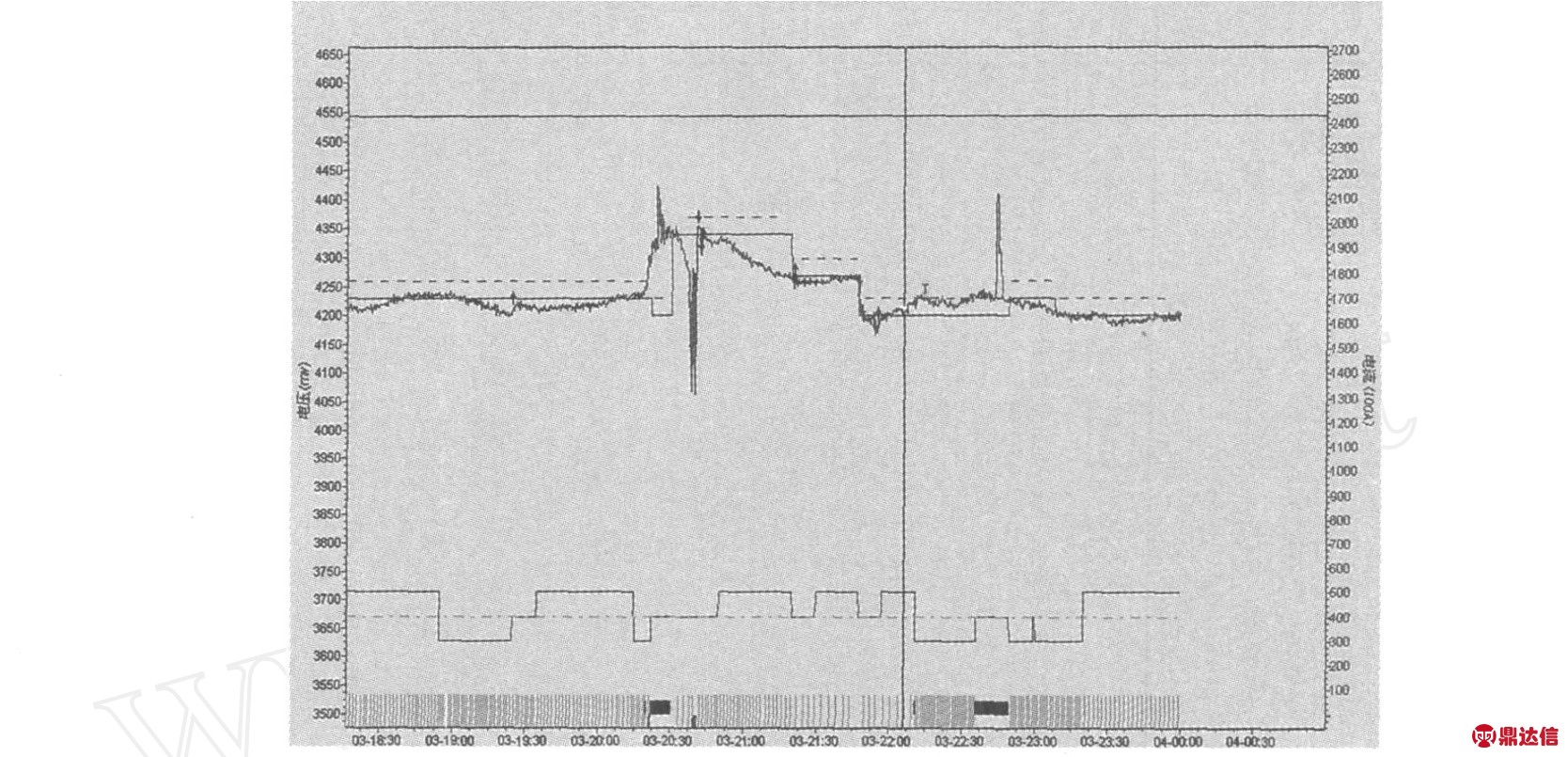
图6 117#槽冷极换极前后的槽电压情况
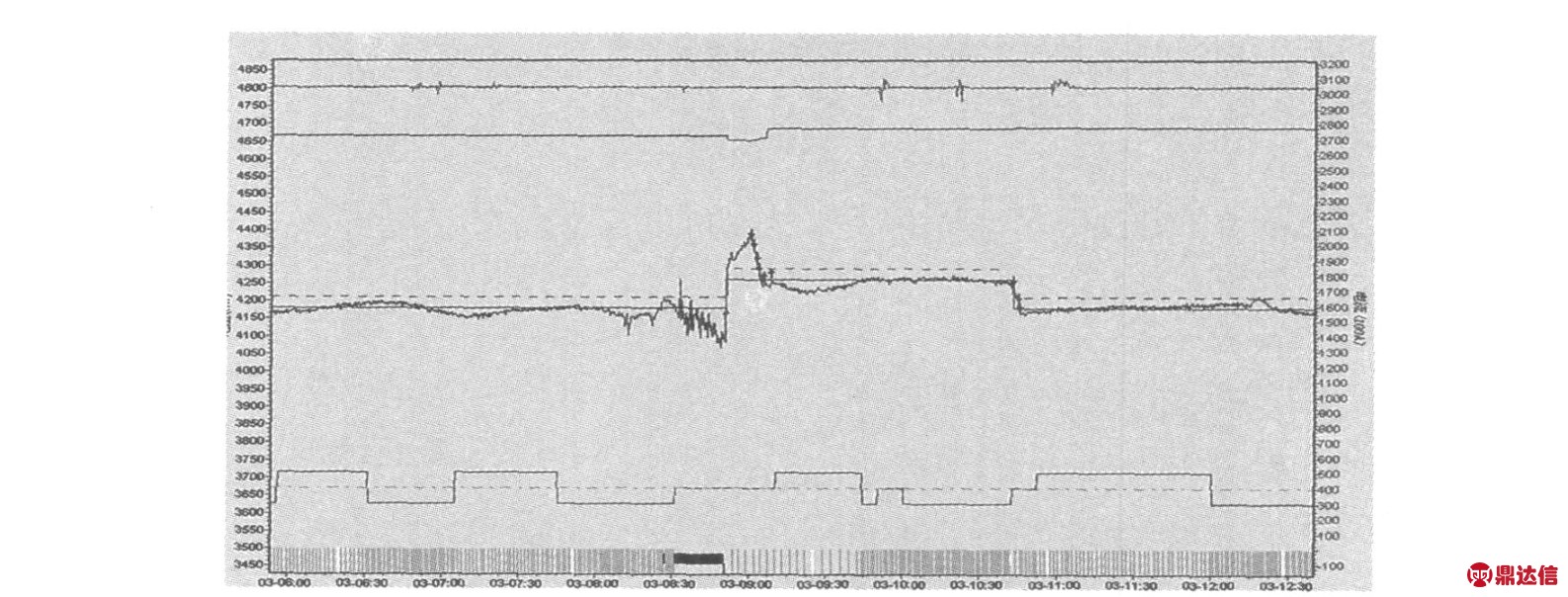
图7 115#槽热极换极前后的槽电压情况
从图6、图7中可以看出:在换极过程中,热极上槽的 115#槽比冷极上槽的 117#槽的稳定性好,换极过程中电压摆动较小,且 115#槽比 117#槽更快地恢复到了稳定的状态,缩短了从换极到平衡的时间。
2.2.3 热阳极电解能耗情况
由测量的数据可知,热阳极的温度约 250℃左右,由吸热公式可计算出一块热阳极所储热量:
Q=c.m.ΔT =2.5×105kJ=69.45 kW·h式中:Q为热阳极所储热量;C为阳极的比热容(16.88 J/mol.K);m为阳极质量 (790 kg);ΔT为冷热阳极的温差 (225 K),吨铝阳极净耗取450 kg。
将上式的结果折算成吨铝节电则为 39.5 kW·h,热极上槽后比冷阳极要少消耗电能约69.45 kW·h。
2.3 热极上槽的前景
从上面的论述可以看出,高温浇铸热阳极上槽后具有良好的表现,能充分利用焙烧余热,稳定电解槽况、降低吨铝能耗,在低碳循环经济方面具有显著的促进作用,在技术思路和路线上遵循节能、环保、经济优先的原则。
该技术能否投入应用,关键是从焙烧出炉到电解上槽的时间能否控制在 2~3 h以内完成。由于试验是在工序作业间无相互等待的情况下完成,在工序间采用平行移动方式,生产周期短,对于小批量生产可行性较强;而平时的工业生产批量较大,工序间采用顺序移动方式,生产周期长[2],过程阳极热量损失较大。
从阳极出炉后至上槽时各工序的耗时看,阳极耗时最大的是阳极出炉后到阳极完全清理时,占整个工时的 38.21%,这个过程包括阳极出炉、阳极解组、阳极输送及搬运、阳极清理、阳极检验、阳极输送等作业。这个过程若通过合理的流程设计和优化,工时具有可压缩的空间。另一方面,对于新建的铝电解企业,如果在工程的节能与环保设计理念中就能体现这一技术思想理念,把自配的炭素生产线阳极焙烧、组装工序合理统筹布局在电解厂房的两侧,简化和缩短阳极的处理流程,加之精益生产的组织方式[3],充分利用阳极焙烧余热,这将是铝电解工业技术上的一次不小进步。
3 结 语
1)热块浇铸阳极上槽后对电解槽的影响较小,显著缩短了电解槽从换极到平衡的时间。
2)热阳极温度整体随着时间的变化呈某一曲线下降;但是当阳极温度下降到某一点时,出现了温度拐点,阳极温度的变化比较平缓。
3)热块浇铸阳极上槽换极后的前 5 h,热阳极电流上升速度明显高于冷极电流上升速度;吨铝节约电耗约 39.5 kW·h。
4)焙烧热阳极上槽技术,能充分利用阳极焙烧余热,降低生产能耗,为铝工业的可持续发展提供了技术支撑。