摘 要:提出了一种基于不影响排气阻力及噪声,只通过改变排气尾管放置角度及其上分布的排气小孔形式的消声器。
关键词:排气尾管角度;排气小孔分布;试验方法;气流流向分布
0 引言
有现场反馈,4-5TK系列叉车配重后部经常出现被消声器喷黑的现象。为此,经现场反复试验得出:由于4-5TK系列叉车是利用配重中部大孔排气的,且消声器排气尾管上开设的小孔在排气过程中,气流与配重左上侧干涉,造成配重左上侧被排气气流喷黑。
针对上述问题,提出了如下几点改进方案:分析解决配重被喷黑现象;保持消声器安装位置和消声器筒体不动,减少排气小孔及位置下移;计算并验证减少排气小孔后对排气气流截面影响是否在可允许范围内。
1 气流分析及试验方法
如图1所示,消声器装配在车架上的专用支脚上,位于配重内部。针对配重左上侧被喷黑现象,经理论分析得出,消声器的气流是从左侧进气,经筒体消声降噪后,经后部排气尾管上的数个小孔排气的,如图2所示。由于气流排出过程中,是呈喇叭口向后排气,消声器排气尾管设计不合理,导致气流角度与配重中部大孔干涉,从而使配重喷黑。现场试验方法如下:随机挑选一台叉车,经试车后配重左上侧被喷黑。拆下消声器,依次堵上左侧2个排气小孔后,再进行试车,配重大孔左侧不再被喷黑。经现场贴纸看出,左侧没有气流,即气流与配重不干涉。
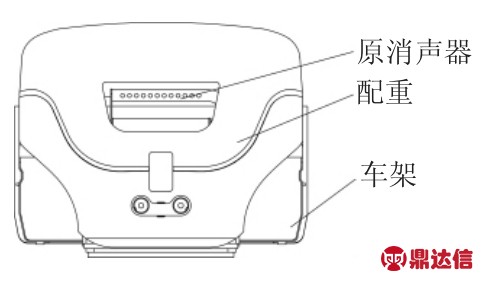
图1 原消声器装配后视示意图
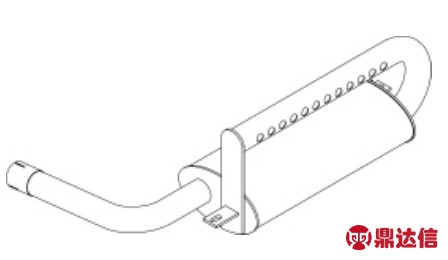
图2 原消声器外形示意图
2 实施改善
对照图2与图5可以得出,改进后排气尾管由原来的垂直放置改为倾斜放置,并且排气尾管的排气小孔位置及数量减少了。
对照图3与图6,保证消声器在车架上的支脚不动,只需要改动排气尾管放置角度,同时减少2个小孔排气,就可以得出图3和图6的区别。图3消声器排气小孔气流方向与配重大孔左侧边缘成15°夹角,而图6消声器排气小孔气流方向与配重大孔左侧边缘成35°夹角,这一夹角是排气小孔上视的左端点与配重大孔左边线相切点连线,与水平线的夹角。经试验得出,气流与配重不干涉。对照图4与图7,配重大孔上部喷黑,也是因为气流与之干涉。改进后排气气流与配重大孔上边线夹角由原来的10°改为11°。此夹角是侧视排气小孔上端点与配重大孔上边线相切点连线,与水平线夹角。此夹角经更改后经试验得出,气流与配重不干涉(上边夹角都是气流理论上与配重相应边线不干涉的夹角,经验证,上述理论可行)。
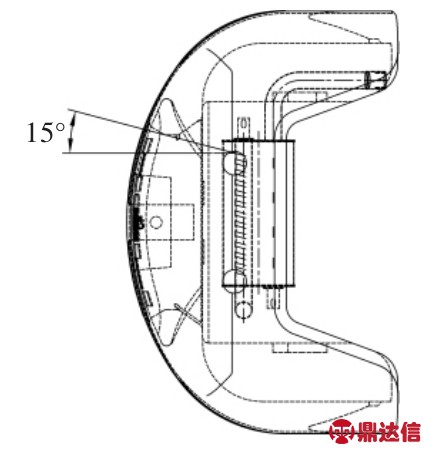
图3 原消声器排气气流上视示意图
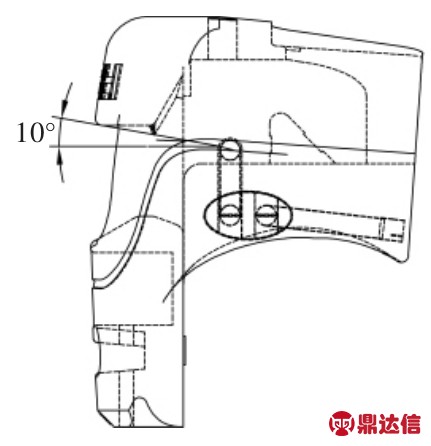
图4 原消声器排气气流侧视示意图
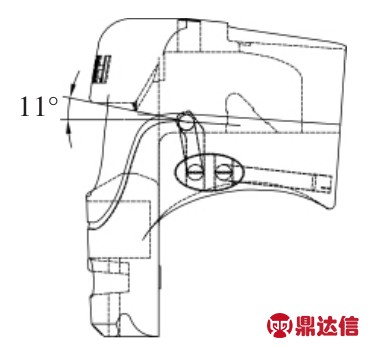
图5 新消声器外形示意图
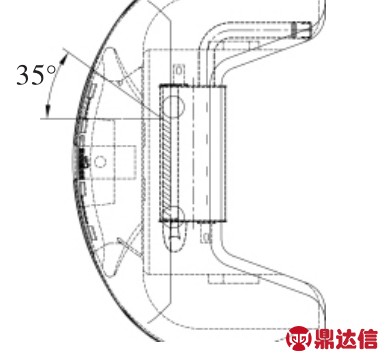
图6 新消声器排气气流上视示意图
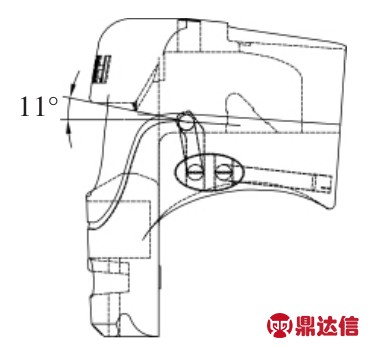
图7 新消声器排气气流侧视示意图
3 计算验证
原消声器排气尾管上布置有12个排气小孔的直径是20 mm,排气尾管是直径57 mm、壁厚1.5 mm管材,气流在排气尾管内的通流截面面积S=[3.14×(57-1.5×2)2]/4=2289.06 mm2。12个排气小孔的通流截面面积S1=12× (3.14×202)/4=3768 mm2>S。改进后消声器排气尾管上布置的10个排气小孔的直径相同,排气尾管管材截面没有改变,气流在排气尾管内的通流截面面积相同,10个排气小孔的通流截面面积S2=10×(3.14×202)/4=3140 mm2>S。由此可得出,减少2个排气小孔对排气气流影响较小。经试验验证排气阻力和噪声试验都达到预期效果。
4 结语
通过上述分析计算,再进行试车检验对比,本方法可解决消声器对配重喷黑现象,达到改善产品外观要求。