摘 要:研究了一种以电流变液为润滑介质的静压导轨系统静动态特性。利用液阻网络理论,在分析电场强度与电流变液黏性关系,综合考虑关联参数的基础上,建立了电流变液静压导轨系统的CFD计算数值模型。根据摄动理论,利用Fluent动网格技术,研究了在不同工作变量下电流变液静压导轨的静动态特性。研究结果表明:电场强度、负载因素与初始压力比等工作变量均会对电流变液静压导轨系统性能带来影响;电场强度增强会使系统流量减小,阻尼系数增大,但不会对系统静刚度带来影响;改变切削力载荷频率,导轨系统会出现共振现象,增强电场强度可显著提高系统动刚度,抑制共振时的最大振幅。实验结果与仿真数值一致,为电流变液静压导轨的设计应用提供了理论参考依据。
关键词:静压导轨;电流变液;电场强度;静动态特性;动网格;关联参数
液体静压导轨以其高精度、高刚度、高阻尼吸振性、低摩擦和长寿命等技术优势,在超精密加工领域获得了越来越广泛的应用。使用电流变液作为润滑介质取代液压油,是智能材料在润滑领域的重要应用,可以显著提高液体静压支承系统的性能。目前针对电流变液特性及其在润滑领域的应用方面:KO等[1]介绍了一种负电流变液的材料机理、性能及应用范围;BOUZIDANCE等[2]研究了基于电流变液的静压径向轴承因转子转动不平衡引起的惯性振动的抑制方法;AOYAMA等[3]分析了电流变液在机床工作台与轴承等关键区域的应用方案。静压支承系统主要性能参数的求解方法主要有:从雷诺方程出发,采用解析方法进行推导[4-5];使用有限差分法进行数值求解;根据摄动理论,利用CFD软件Fluent动网格技术求解刚度与阻尼系数的方法[6]。在静压支承系统静动态特性研究方面:CHEN等[7]研究了静压主轴的静动态特性;THOMAS等[8]研究了不同油腔结构参数对静压径向轴承的等效刚度与阻尼的影响情况;DU等[9]在考虑油液可压缩性与惯性效应的基础上建立了静压导轨系统的质量、刚度、阻尼等效模型;杨小高等[10]对基于固定节流的静压径向轴承进行了动态特性分析;于贺春等[11]静压气体轴承转子系统提出了流场与转子的准动态动力学特性耦合分析方法。另外导轨系统结构参数对油液温度场的影响[12]以及油液温度因素对静压支承系统性能的影响[13]也经常出现在文献之中。但是基于电流变液为润滑介质的静压导轨系统的静动态特性研究领域却鲜有报道。本文作者在分析电流变液特性与电场强度关系,并综合考虑关联参数的基础上,建立了基于关联参数的CFD计算数值模型;根据摄动理论,利用Fluent动网格技术研究了不同工作变量对静压导轨系统性能参数的影响规律;以及为在切削力载荷下提高系统动刚度并减小导轨共振振幅而选取合适的电场强度提供理论依据。
1 电流变液静压导轨系统分析建模
1.1 电流变液静压导轨系统原理
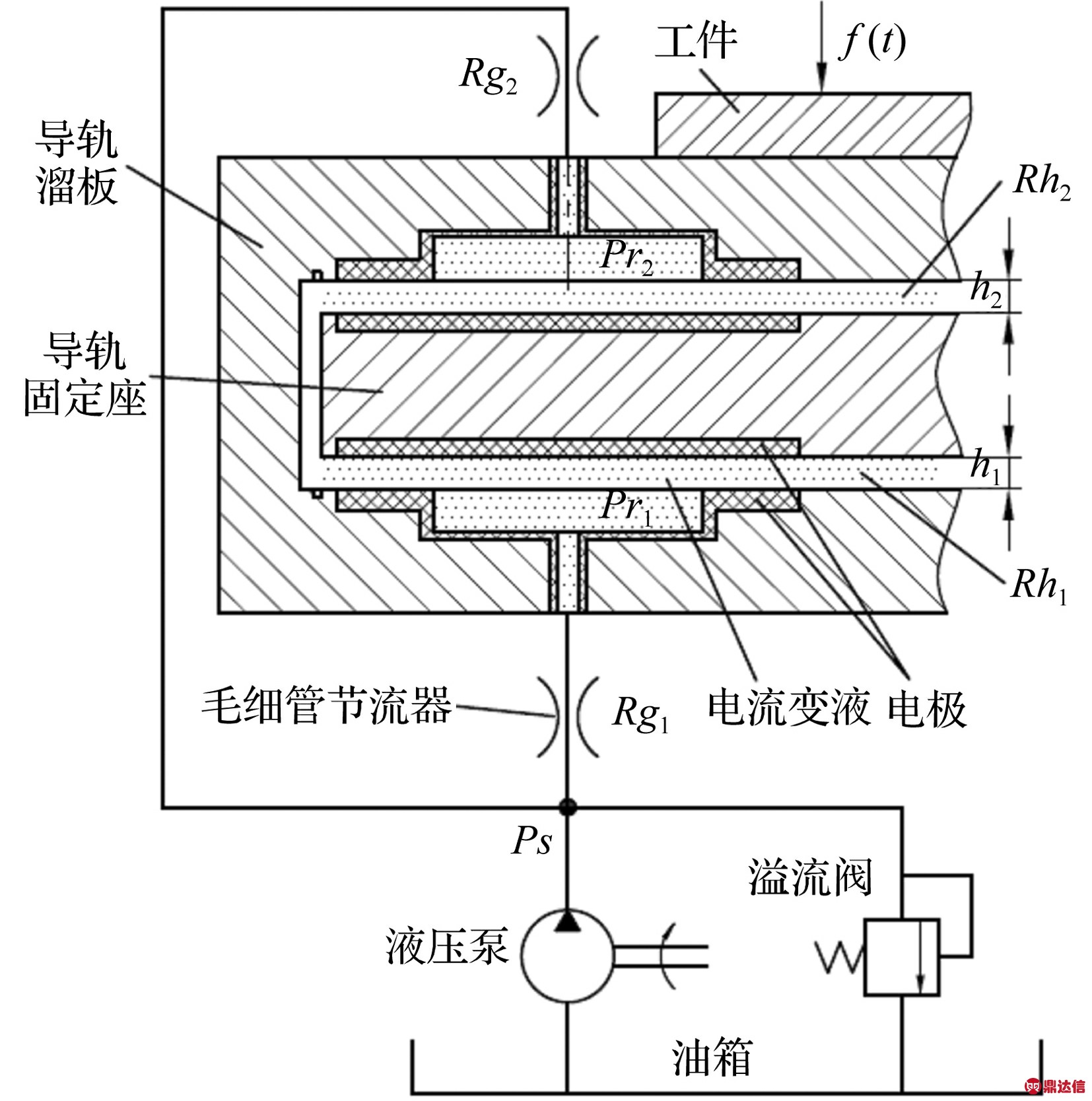
图1 电流变液静压导轨系统原理图
Fig.1 Scheme of hydrostatic guideway system based on electrorheological fluid
图1是电流变液静压导轨系统原理图。电流变液由液压泵泵出,分别经毛细管节流器进入上下油腔,在导轨溜板与固定座之间形成油膜,以抵抗溜板与工件重量和外载荷的作用。它属于毛细管节流器补偿的恒压供油闭式电流变液静压导轨。
该电流变液静压导轨上下油腔之间尺寸参数不一致,但其结构型式均为为矩形油腔,如图2所示。

图2 矩形油腔结构图
Fig.2 Structure of rectangle oil pocket
静压导轨在工作过程中受到的外载荷分为两大类:静态载荷与动态载荷。静态载荷主要分为固定重量(导轨溜板)与可变重量(工件与夹具),亦可统称为负载因素;动态载荷主要指加工过程中的切削力载荷。
F=Mg+mg+f(t)
(1)
式中:F为静压导轨总负载,N;M为导轨溜板质量,kg;m为工件与夹具质量,kg;g为重力加速度,m/s2;f(t)为切削力载荷,N。
定义负载比α为静态载荷与固定质量(导轨溜板)之比,用来定量地表征负载因素。
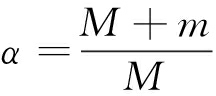
(2)
在初始设计状态,导轨在固定质量以及上下油腔作用力下保持静态平衡,由力平衡条件可知:
n(Pr0Ae2-Pr0Ae1)=Mg
(3)
Aei=(Li+li)(Bi+bi)/4
(4)
式中:Pr0为初始设计状态各油腔压力,Pa;Aei为油腔有效承载面积,m2;n为油腔对数;Li为油垫总长度,m;Bi为油垫总宽度,m;li为油腔长度,m;bi为油腔宽度,m;其中下标i为1时指下油腔及相关参数,i为2时指上油腔及相关参数,下同。
初始压力比β0是静压导轨系统重要的初始设计参数,其定义为为初始设计状态下油腔压力Pr0与供油压力Ps之比。调节Ps大小可改变β0。

(5)
在负载因素影响的任意状态,根据力平衡条件:
n(Pr2Ae2-Pr1Ae1)=αMg
(6)
值得注意的是,当α=1时,Pr1=Pr2=Pr0。此时初始设计状态下的式(3)是式(6)的特殊情况。
根据油路液阻网络理论[14],由连续性条件,液体静压导轨系统有如下关系:
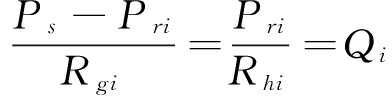
(7)
对于毛细管节流器,进油液阻Rgi表达式为:
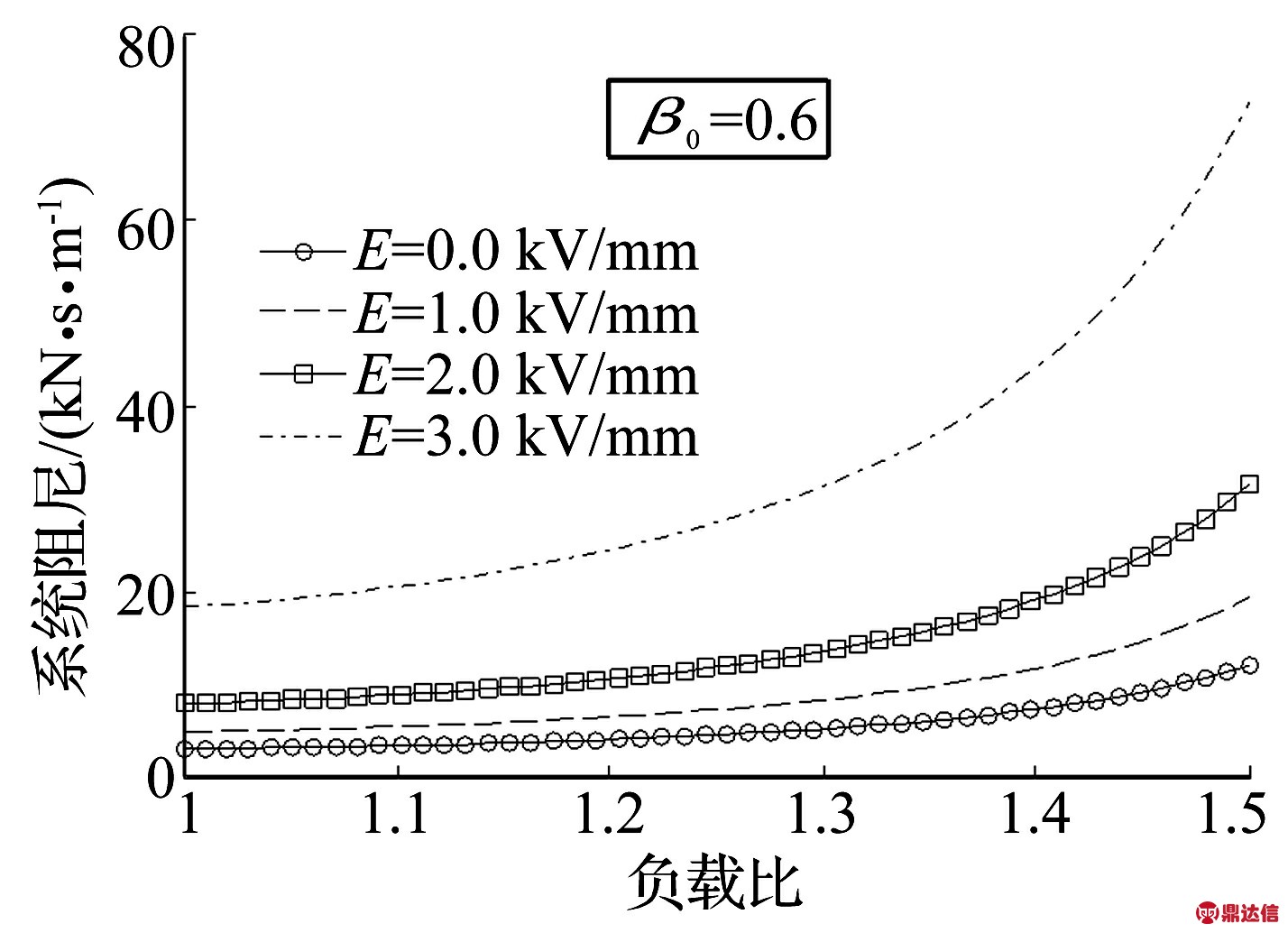
(8)
对于矩形油腔,出油液阻Rhi表达式为:

(9)

(10)
同样在初始设计状态下Δ h=0,则 h1= h2= h0。由式(5)及式(7)~式(10)可求得:
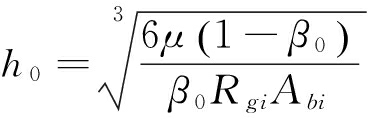
(11)
由式(7)可知,如果使初始状态下上下油膜厚度相等,须使RgiAbi=C,C为常数。所以根据初始压力比β0与C可确定初始膜厚h0。
由式(6)~式(10)可知,在负载因素下油膜厚度的变化量Δ h,又因为Δ h值较小,故略去它的高次方项。所以油膜厚度变化量Δ h可表达为:

(12)
由式(12)可知,在负载因素作用下,Δ h是负载比α的函数;且当α=1时,Δ h=0。同时在可求得任意状态下,导轨上下油膜厚度:
hi=h0-(-1)iΔ h
(13)
进一步,任意状态下导轨上下油腔压力:
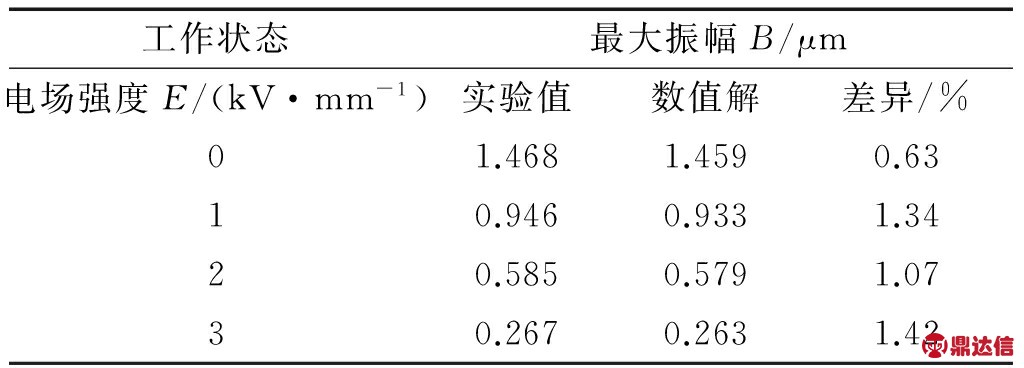
(14)
该静压导轨系统的润滑介质为电流变液,它是一种将由掺杂稀土改性的二氧化钛粉体材料溶入甲基硅油基液混合而成的悬浮颗粒溶剂[15]。由纯二氧化钛和掺杂稀土元素的二氧化钛粉体(颗粒直径φ=1 μm,导电系数 σs=10-10 S/m)在150℃干燥4 h与在150℃处理2 h的甲基硅油(介电常数εf=2.7,动力黏度 μ0=0.05 Pa·s(25℃))按颗粒/硅油体积比35%混合均匀即可得到电流变液[16]。剪切速率 在0~500 s-1内,电流变液表观黏度 μ 随外加直流电场强度E的增强而变大,其具体变化关系如图3所示。电流变液表观黏度是电场强度的函数,可记作 μ(E)。

图3 电流变液表观黏度与电场强度关系
Fig.3 Apparent viscosity versus electric field of ER fluid
由式(12)~式(14)及图3可知, hi、Pri与μ均是E、α及β0的函数,前三者构成了一组关联参数Θ。将工作变量记作Γ={E,α,β0},则关联参数Θ为:
Θ={μ, hi,Pri}=f(Γ)
(15)
关联参数Θ中的各变量不可随意组合,它们是联动变化的。可通过对Γ赋值以求得Θ,为电流变液静压导轨系统建模提供参数依据。
1.2 电流变液静压导轨系统模型
基于动网格技术的导轨性能参数计算方法是在计算流体动力学(Computational Fluid Dynamics, CFD)软件Fluent的基础上,采用自定义程序实现导轨间隙扰动功能,结合差分计算模型,计算导轨油膜性能参数的一种新方法。但该文献既未从整个系统的角度来考虑因工作变量不同所导致关联参数变化的联动效应,也未从电流变液作为特殊润滑介质的角度来研究静压支承系统的模型。
静压导轨在某一关联参数下的平衡位置受到小扰动作用(位移扰动与速度扰动)时,油膜力会发生变化。根据摄动理论,对油膜力进行一阶泰勒级数线性化处理,油膜力变化与位移扰动和速度扰动之间的关系[17]可以表达为:

(16)
式中:δW为油膜力的变化,N;KΘ为导轨系统静刚度,N/m;CΘ为导轨系统阻尼,N·s/m;δh为位移扰动,m;h为速度扰动,m/s。
这样在任一关联参数Θ下导轨系统静刚度与阻尼的计算公式为:

(17)
所以求解式(17)关键是要解决四个技术问题:其一是为电流变液选取适当的计算模型;其二是建立基于关联参数Θ的数学模型;其三是采用动网格技术施加小扰动并界定扰动范围;其四是求解计算模型得到油膜压力分布与油膜力。
1)选取电流变液计算模型。当未加电场时,电流变液为牛顿流体,可参照一般油液计算模型;施加电场后,电流变液呈现为宾汉体,其模型为:
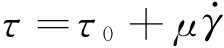
(18)
FLUENT提供了一种扩展的Herschel-Bulkley模型,它综合反映了流体中的宾汉及指数行为效应[18]:

(19)
当k=μ、λ=1且(τ0/μ0)→0时,FLUENT提供的Herschel-Bulkley模型便与文中需要的宾汉模型一致,可以用作电流变液的计算模型。该模型可在软件中材料特性的黏度栏选取。
2)关联参数Θ须运用到计算模型中去。其中油膜厚度hi决定了上下油膜流场三维模型的结构;油液黏度 μ 决定了电流变液的参数;油腔压力Pri决定了模型的压力边界条件。由于关联参数Θ是工作变量集合Γ={E,α,β0}的函数,因此不同的工作变量Γ就会导致完全不同的计算模型。关联参数Θ与计算模型的关系如图4所示。
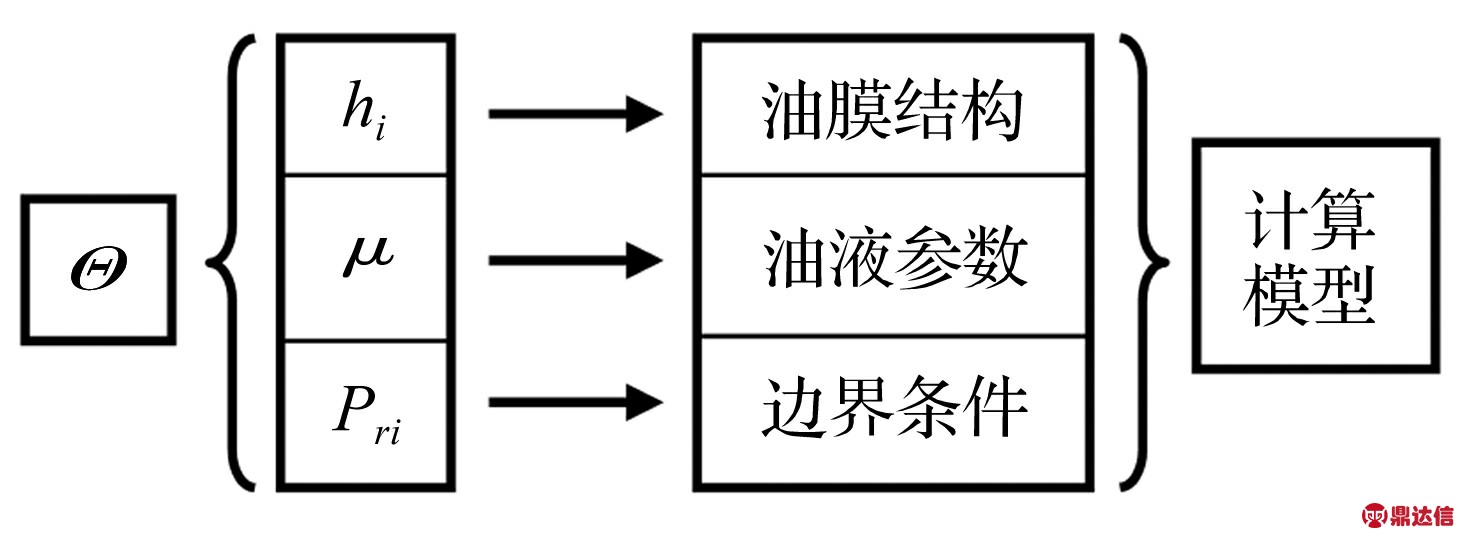
图4 关联参数与计算模型关系图
Fig.4 Relationship between correlation parameters and computational model
3)在位移扰动与速度扰动情况下,油膜几何形状随油膜发生变化,必须引入动网格技术来进行处理。此时油膜与溜板之间的边界层网格与油膜内部网格均产生变形。油膜网格运动的计算模型采用的是基于线性假设的弹性光顺Smoothing模型,其核心思想是基于胡克定律,网格线类似于弹簧,两端节点作弹性移动的网格运动方式。油膜厚度扰动程序建立在Fluent软件提供的用户自定义函数(User Define Function, UDF)的基础上,其功能通过宏DEFINE_PROFILE实现[19]:
((BOTTOMWALL_profile 2 point)
(time 0 t)
(v_z Vh Vh))
在该UDF程序中,t指的是网格运动终结时间,Vh是指油膜厚度网格运动速度。参照熊万里等提出的原则,即通过对比研究动网格瞬态计算和稳态计算在平衡点的变化,分析位移扰动与速度扰度对油膜力的影响,进而界定其取值范围:
位移扰动(求静刚度):Vh≤1 μm/s;Vh t≤0.2 μm
速度扰动(求阻尼):Vh≥0.1 mm/s;Vh t≤0.2 μm
4)在用SolidWorks建立的三维油膜模型文件x_t的基础上,采用前处理软件ICEM CFD划分网格,油膜厚度方向网格为10层。采用Fluent软件求解模型,不同电场强度及负载因素下的参数取值遵从关联参数Θ。经过迭代数值计算,得到油膜流场分布。导轨系统油膜力W可进一步求得:

(20)
式中为上下油膜压力场分布,Pa。
由上述的动网格瞬态计算最终可求得关联参数下的导轨系统静刚度KΘ与阻尼CΘ系数。另外通过稳态计算还可求得电流变液静压导轨系统总流量Q:

(21)
式中为上下油膜速度场分布,m/s。
1.3 导轨系统动态特性分析
电流变液静压导轨的油膜相当于带有阻尼的液体弹簧,故文中的导轨系统也可以简化为一个单自由度的质量—刚度—阻尼系统。假设作用在电流变液静压导轨上的载荷为波动载荷,此时考虑不同关联参数Θ下的系统振动模型为:

(22)
式中:fm为切削力幅值,N;ω为切削力频率,Hz。
式(22)是一个典型的具有黏性阻尼系统的单自由度受迫振动。如果忽略瞬态振动而仅仅研究其稳态行为,则导轨系统的动态响应方程为:
Δh(t)=Bsin(ωt-φ)
(23)
式中:B为导轨系统振动振幅,m;φ为系统位移落后于切削力的相位角,rad。
由式(23)可求得静压导轨系统的振幅放大因子:
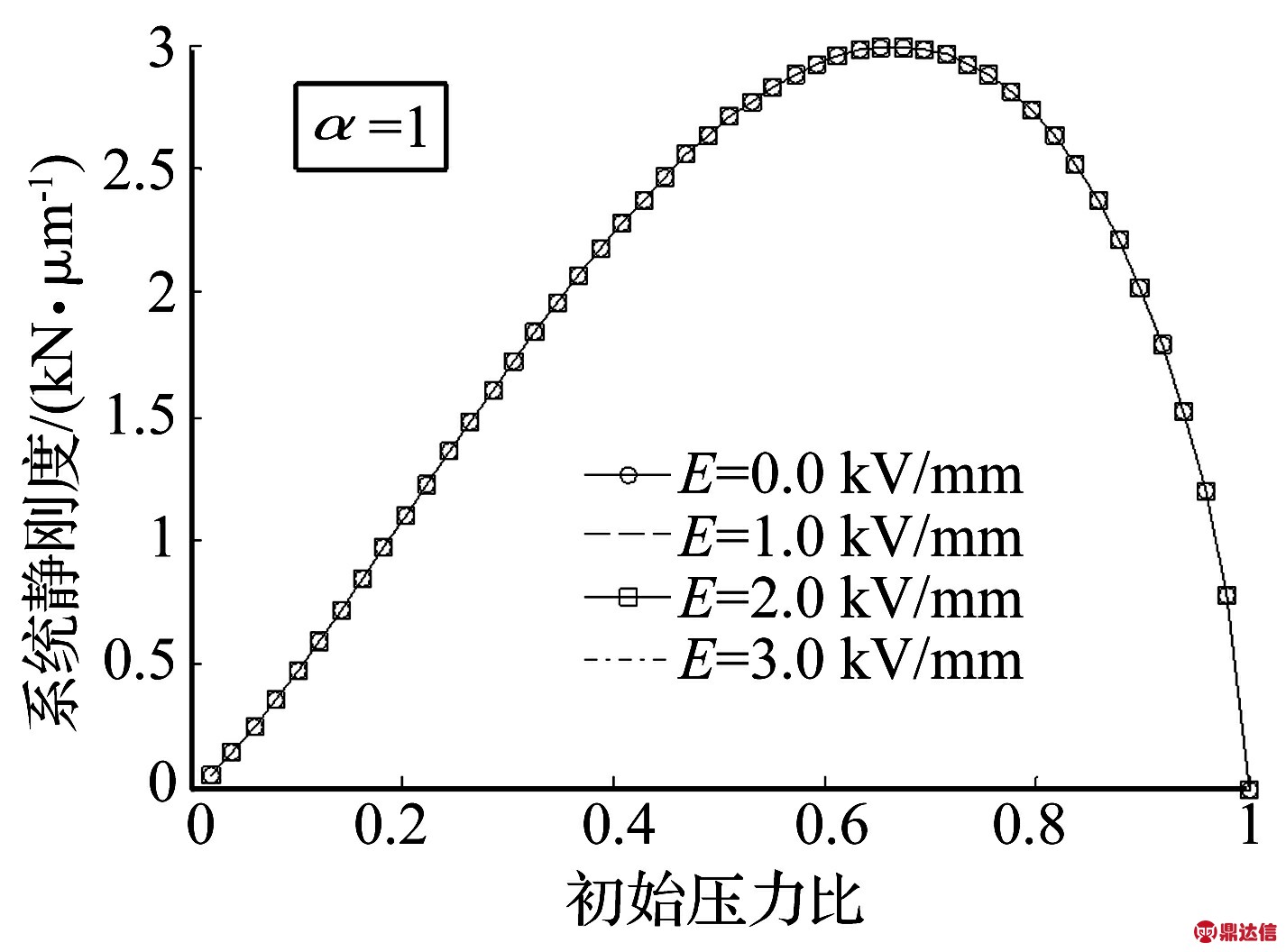
(24)
式中:Be=fm/KΘ为等效静变形,m;r=ω/ωn为频率比;为系统固有频率,rad/s;
为系统阻尼比。
导轨系统动刚度KdΘ可由其静刚度求得:

(25)
2 系统静动态特性仿真结果分析
为了定量地分析工作变量Γ (含电场强度、初始压力比及负载比)对系统性能参数的影响规律,以某精密机械研究所超精密加工系统静压导轨油垫为例进行分析。其基本参数见表1。
除了表1所列举的基本参数外,导轨系统还有一些基础参数:如供油压力Ps=2.5 MPa、导轨溜板质量M=500 kg等。另外还有前文所述的关于电流变液的特性参数等。
表1 静压导轨系统基本参数
Tab.1 Parameters of hydrostatic guideway system
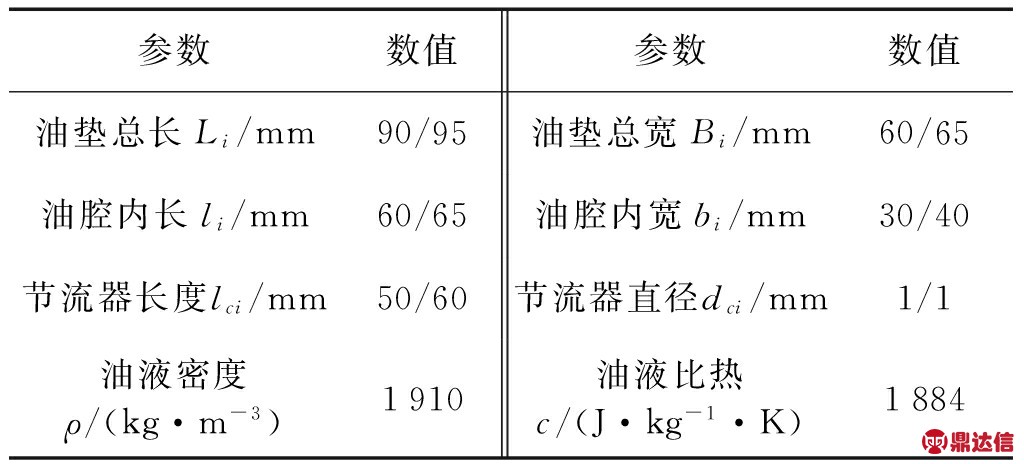
2.1 电场强度与初始压力比的影响
流量Q、油膜静刚度KΘ与阻尼CΘ是电流变液静压导轨系统的重要性能参数。本小节均是在初始设计状态(负载比α=1)下,研究不同电场强度与初始压力比对性能参数影响的。
图5为系统流量Q随电场强度E和初始压力比β0变化曲线。图中显示系统流量Q随电场强度E和初始压力比β0的增大而减小。这是由于当电场强度增大时,电流变液黏度会增加,而系统流量与黏度成反比例,变会减小。当β0=1时,系统流量Q减小为0,这是由于导轨达到了供油压力的承载极限。
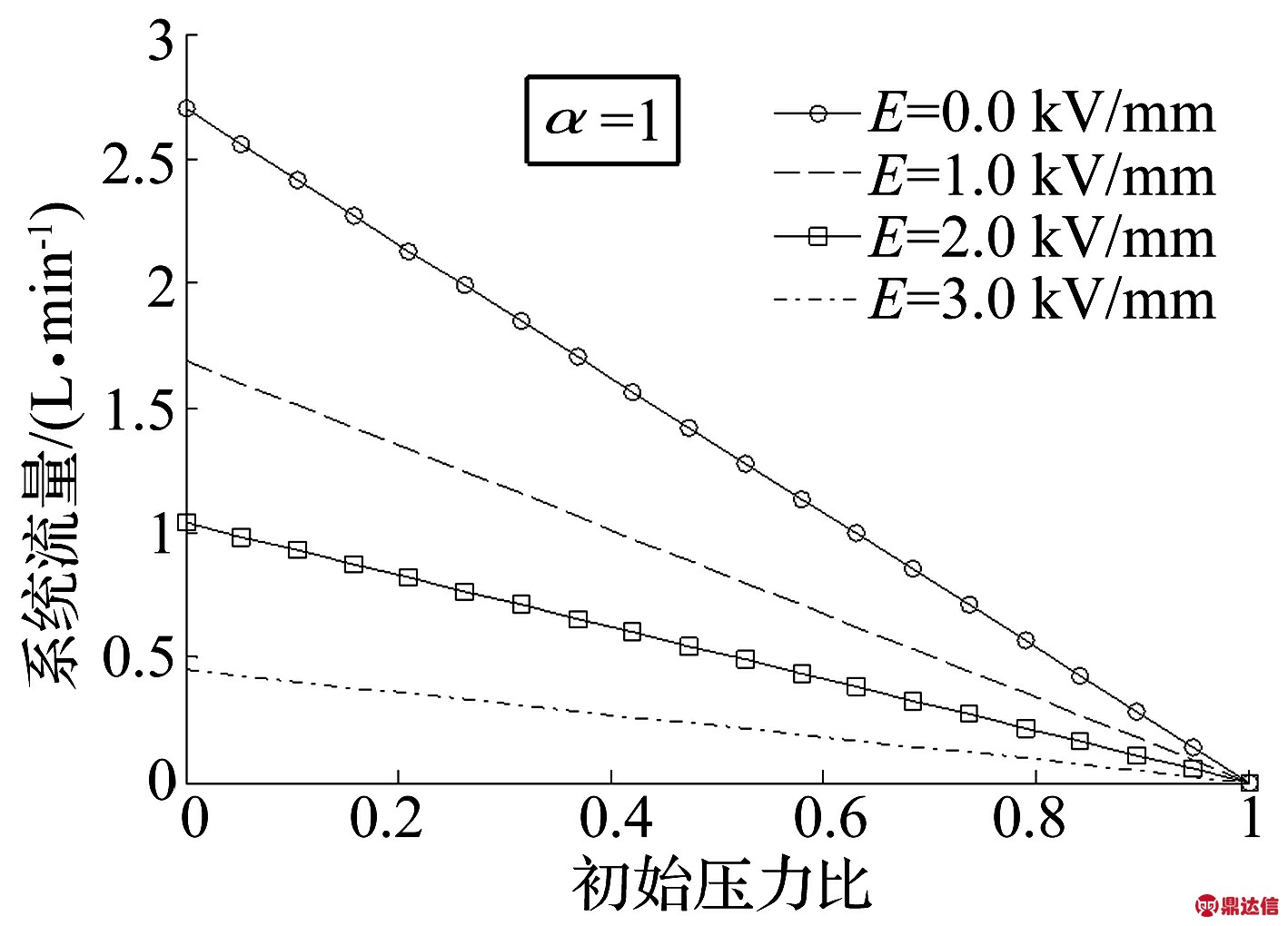
图5 系统流量随电场强度和初始压力比变化曲线
Fig.5 Flow rate versus pressure ratio for different electric fields
图6为系统静刚度K随电场强度E和初始压力比β0变化曲线。图中显示电场强度E对电流变液静压导轨系统静刚度K没有影响,因为使用毛细管补偿的导轨静刚度均与油液黏度无关,自然也与电场强度无关;静刚度K随初始压力比β0增大先变大,后减小,并且在β0=0.67处达到峰值,此时K=2 989 N/μm,这与BOUZIDANCE等分析静压轴承时得到的结论一致。
图7为系统阻尼C随电场强度E和初始压力比β0变化曲线。图中显示系统阻尼C随电场强度E和初始压力比β0的增大而增大,由于阻尼C的变化幅度较大,纵坐标采用对数坐标。初始压力比与电场强度分别通过对初始膜厚h0及电流变液黏度μ的影响来实现对系统阻尼影响的。
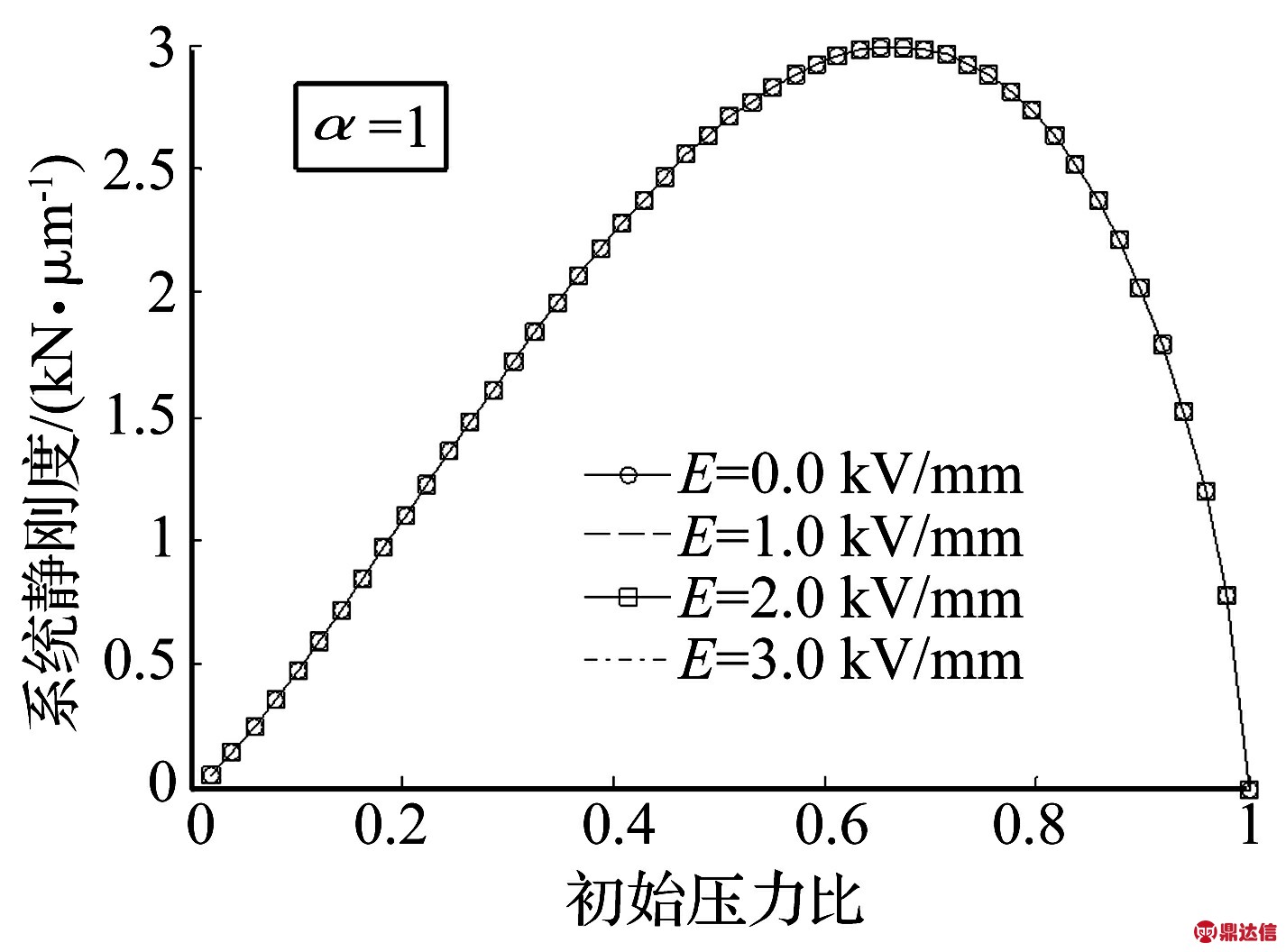
图6 系统静刚度随电场强度和初始压力比变化曲线
Fig.6 Stiffness versus pressure ratio for different electric fields
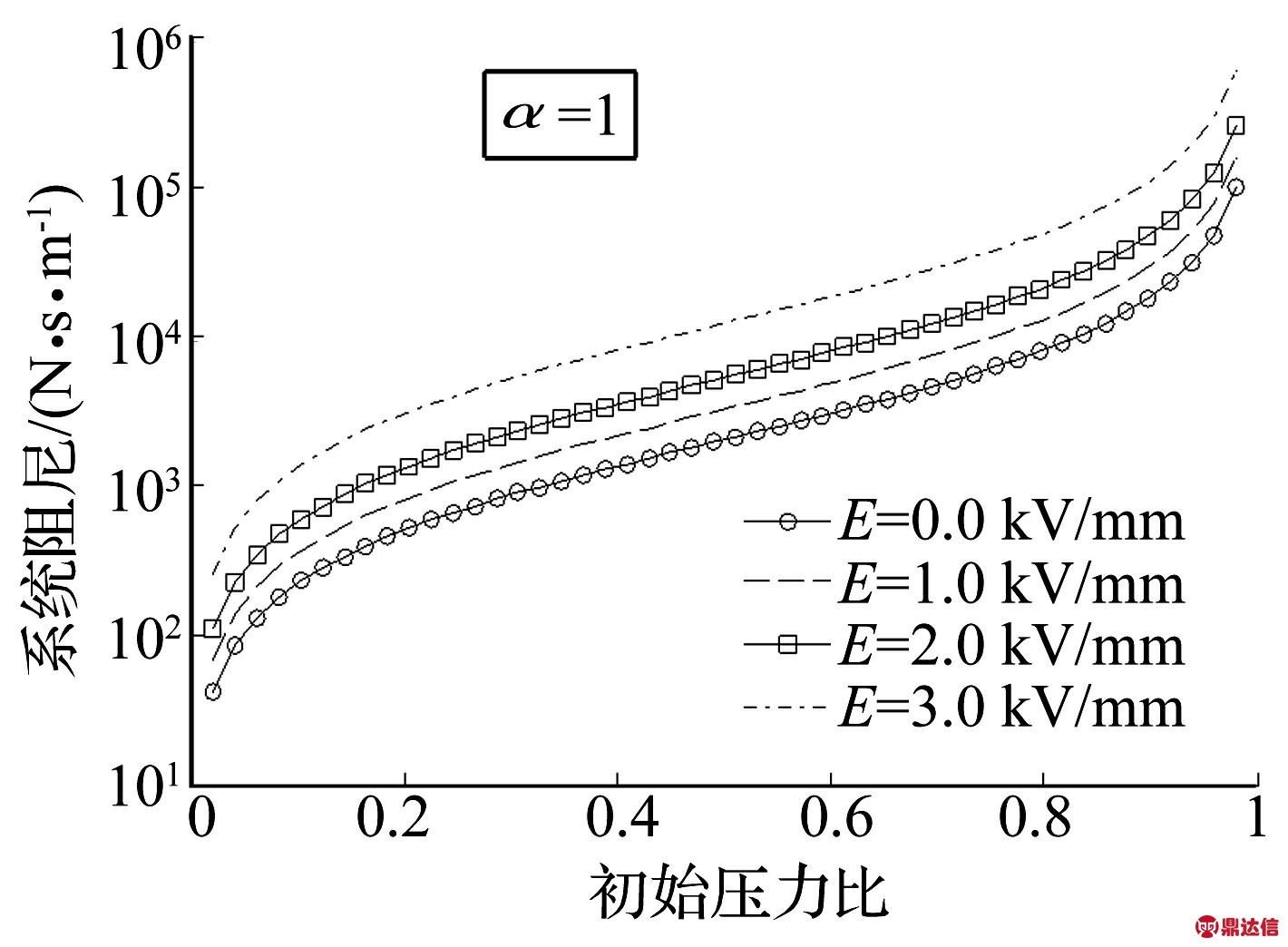
图7 系统阻尼随电场强度和初始压力比变化曲线
Fig.7 Damping versus pressure ratio for different electric fields
2.2 电场强度与负载比的影响
负载比α也会对电流变液静压导轨系统性能参数造成影响。本小节均是在初始设计状态(初始压力比β0=0.6)下,研究不同电场强度与负载比对性能参数影响的。
图8为系统静刚度K随电场强度E和负载比α变化曲线。图中显示系统静刚度K随负载比α的增大而减小,这是由于膜厚变化量Δh是负载比α的函数,而系统静刚度会随导轨偏心程度的增大而减小;所以在导轨的设计和使用阶段,应尽量降低负载比的大小,以使导轨工作在较大的系统静刚度状态之中。电场强度E依旧对系统静刚度K没有影响。
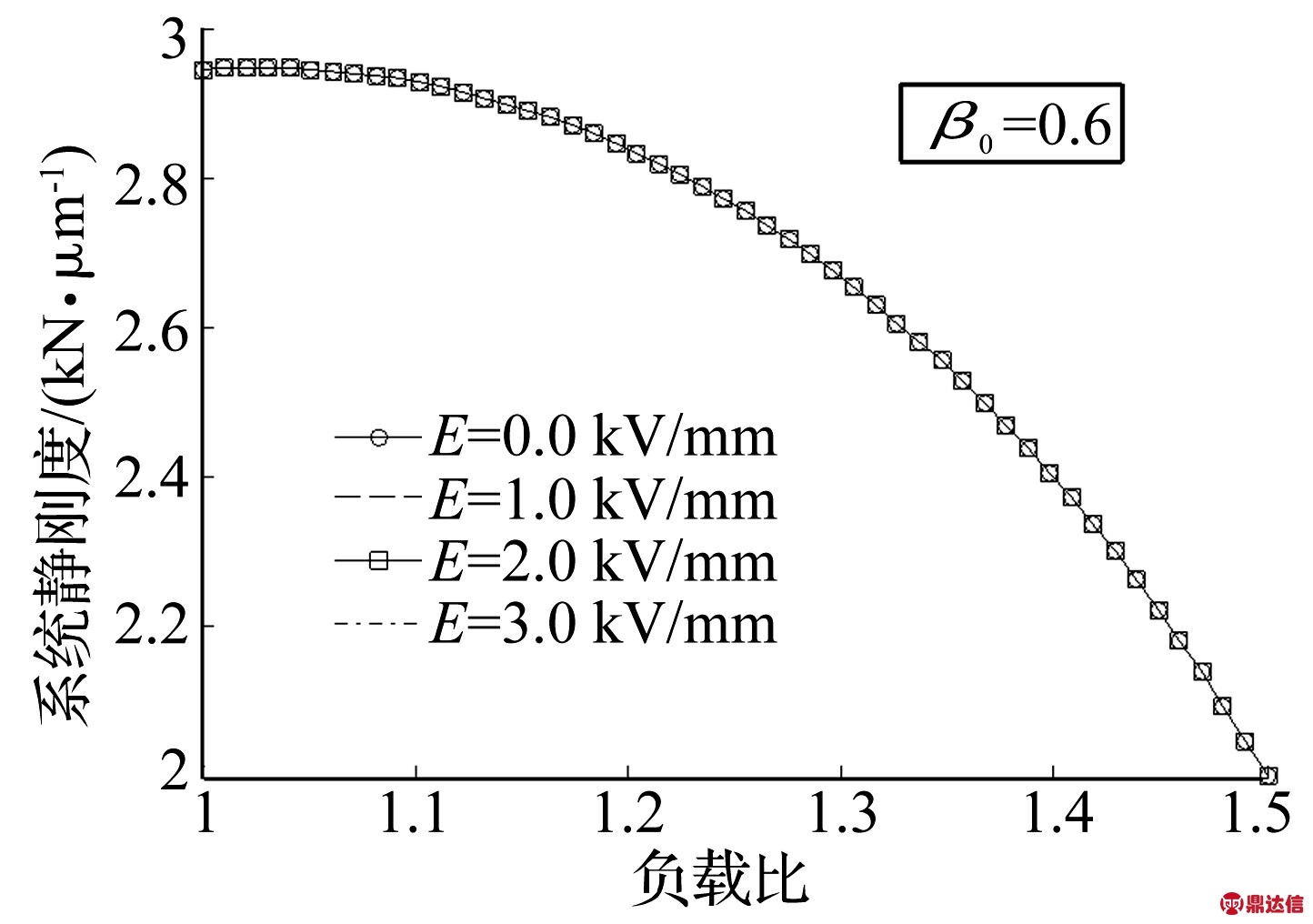
图8 系统静刚度随电场强度和负载比变化曲线
Fig.8 Stiffness versus load factor for different electric fields
图9为系统阻尼C随电场强度E和负载比α变化曲线。图中显示系统阻尼C随负载比α的增大而变大;同样由于电场强度对电流变液黏度的影响,使得系统阻尼C随电场强度E的增大而变大。
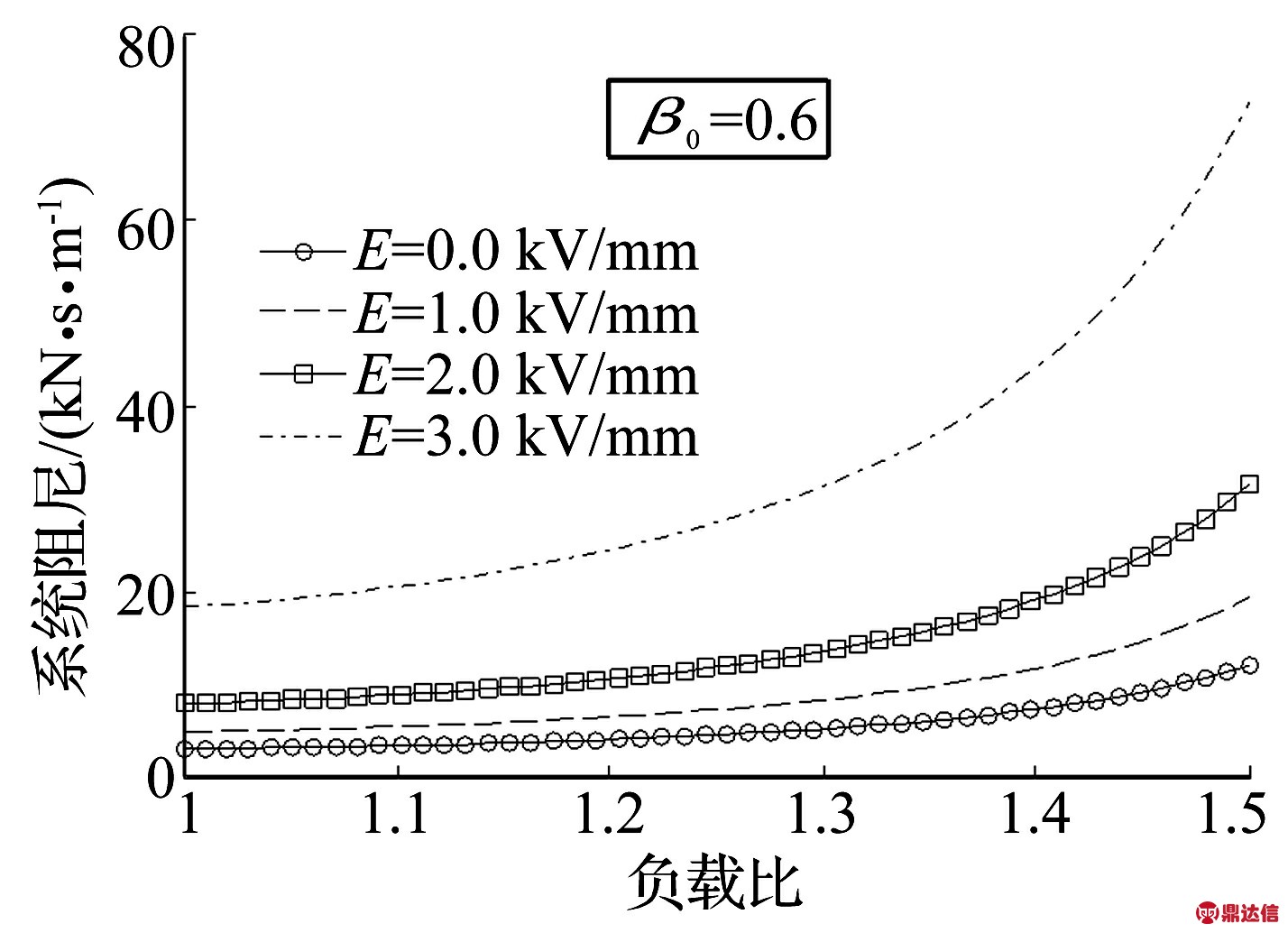
图9 系统阻尼随电场强度和负载比变化曲线
Fig.9 Damping versus load factor for different electric fields
另外由图6~图9可知,对于毛细管节流器补偿的电流变液静压导轨,电场强度E对系统静刚度K变化没有作用,而对系统阻尼C有着显著地影响。因此调节电场强度可以在不改变系统静刚度的条件下调整系统的动态特性,具有明显的优势。
2.3 电场强度对动态特性影响
从前文可知,电场强度E会对电流变液静压导轨系统动态特性带来影响。本小节均是在初始设计状态(负载比α=1、初始压力比β0=0.6)下,研究不同电场强度对系统动态特性参数影响的。
图10为系统振幅放大因子B/Be随电场强度E和切削力频率ω变化曲线。图中显示在切削力频率ω增大过程中,振幅放大因子B/Be先变大后减小,存在共振频率2 830 Hz;增加电场强度可以显著降低共振过程中的振幅幅值。
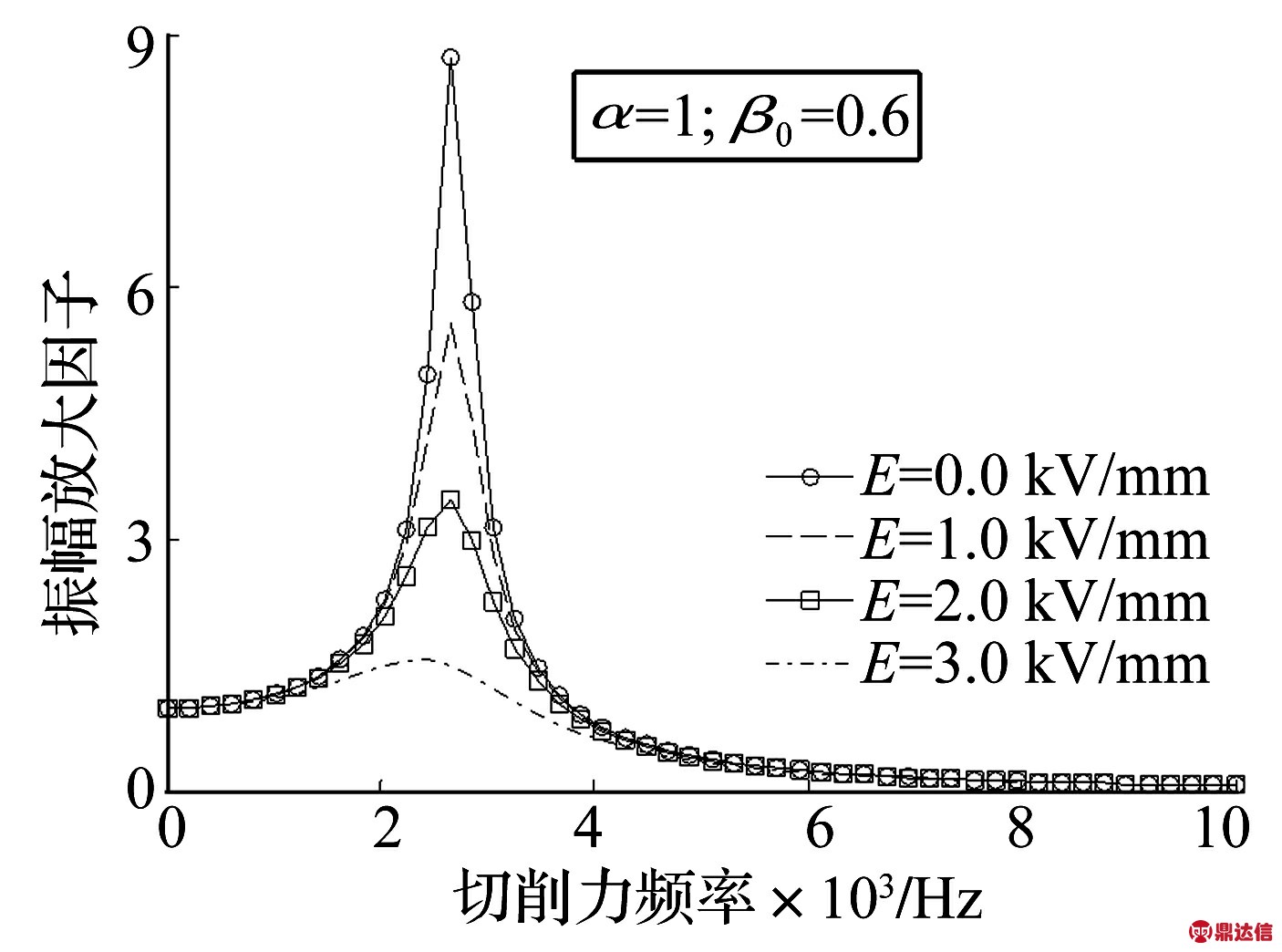
图10 振幅放大因子随电场强度和切削力频率变化曲线
Fig.10 Vibration amplitude magnification due to machining force frequency for different electric fields
图11为系统动刚度KdΘ随电场强度E和切削力频率ω变化曲线。图中显示系统动刚度KdΘ随切削频率ω的增大先变大后减小,且在共振频率附近存在着最小的动刚度数值。增大电场强度E可以显著提高共振频率附近的系统动刚度,如20倍的局部放大图Ⅰ所示。

图11 系统动刚度随电场强度和切削力频率变化曲线
Fig.11 Dynamic stiffness due to machining force frequency for different electric fields
3 实验研究
实验平台是在中国航空工业集团北京航空精密机械研究所国防科技重点预研项目——“Nanosys-300 非球面超精密加工系统”的基础上改造而成。
给导轨施加波动载荷,利用德国米依公司的非接触式位移传感器capaNCDT6300来测量导轨运动,并通过数据采集卡将数据传递到计算机中。利用HVG5000提供直流电源(电压0~5 kV/mm,电流0~10 mA)施加在电流变液静压导轨上:导轨固定座电极接负极,溜板电极接正极。另外,可以通过改变工件或夹具质量改变负载比α,调整溢流阀压力调节初始压力比β0的方式来得到导轨不同工作状态下的振动响应。
表2为电流变液静压导轨系统在不同电场强度E下,最大振幅B的实验值与数值解比较。实验中导轨系统处于初始设计状态(负载比α=1、初始压力比β0=0.6);切削力f(t)=500sin(2 830 t),切削力最大振幅为500 N,切削力频率等于共振频率大小,即2 830 Hz。从表中可以看出电流变液静压导轨系统最大振幅随电场强度的增大而减小,且数值解均能较好地与实验值相符合,差异维持在0.63%~1.42%之间。其差异是由于在导轨油膜流场数值模拟过程中忽略了油液惯性力所致。实验结果证实了文章研究方法及结果的正确性。
表2 最大振幅B的实验值与数值解比较
Tab.2 Comparison between test and computational value of vibration amplitude B
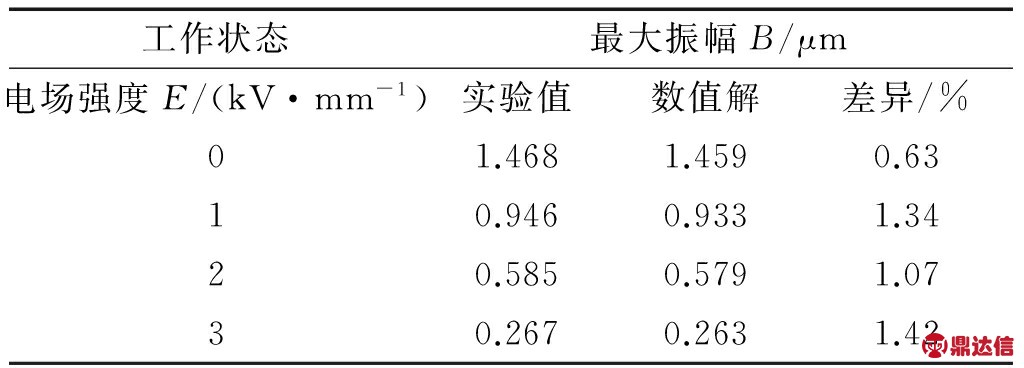
4 结 论
(1) 电场是通过改变电流变液黏度来影响静压导轨系统静动态特性的。电场强度E越大,系统流量Q就越小,而系统阻尼系数C则越大;但电场作用对静压导轨系统静刚度K没有影响。
(2)在电流变液静压导轨系统中,负载因素与初始压力比依然会对系统性能参数带来影响。负载比α越大,静刚度K就会越小,而阻尼C则会变大;初始压力比β0越大,流量Q就越小,而阻尼C会变大,系统静刚度K则会随初始压力比先大后小,出现峰值为2 989 N/μm。
(3)在切削力载荷频率ω逐渐增大的过程中,导轨系统动刚度KdΘ先减小后增大,系统振幅放大因子B/Be则先增大后减小,在共振频率2 830 Hz处存在峰值;增加电场强度E可以有效地增大系统动刚度KdΘ,减小共振振幅。
(4) 在综合考虑电场强度E对电流变液特性的影响的基础上,建立了基于关联参数的导轨系统CFD求解计算模型。研究了在不同工作变量下电流变液静压导轨的静动态特性。实验结果与仿真数值一致,为电流变液静压导轨的设计应用提供了理论参考依据,具有较好的工程应用价值。